化学气相沉积技术制备粉体材料的研究进展和应用.docx
《化学气相沉积技术制备粉体材料的研究进展和应用.docx》由会员分享,可在线阅读,更多相关《化学气相沉积技术制备粉体材料的研究进展和应用.docx(8页珍藏版)》请在冰豆网上搜索。
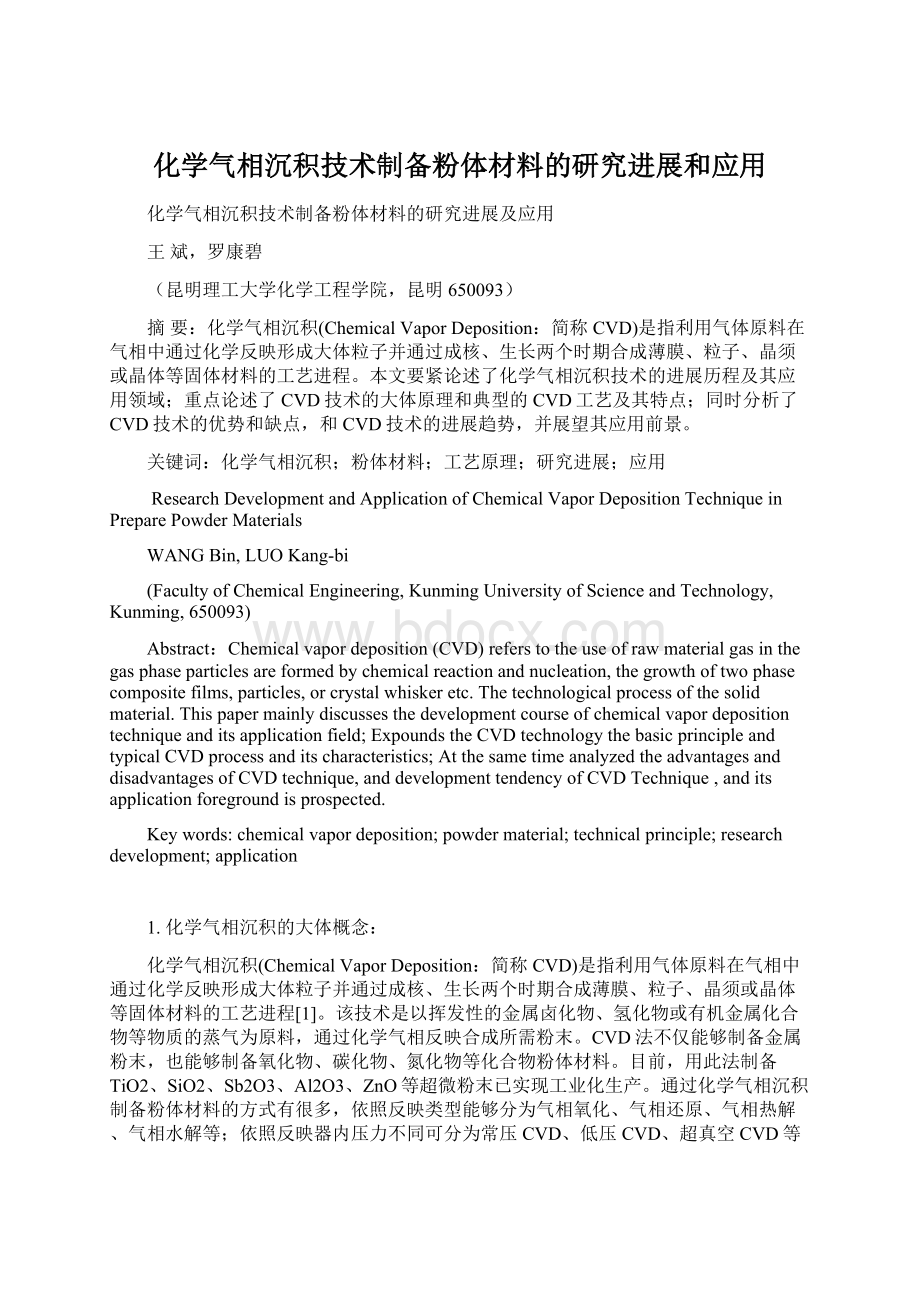
化学气相沉积技术制备粉体材料的研究进展和应用
化学气相沉积技术制备粉体材料的研究进展及应用
王斌,罗康碧
(昆明理工大学化学工程学院,昆明650093)
摘要:
化学气相沉积(ChemicalVaporDeposition:
简称CVD)是指利用气体原料在气相中通过化学反映形成大体粒子并通过成核、生长两个时期合成薄膜、粒子、晶须或晶体等固体材料的工艺进程。
本文要紧论述了化学气相沉积技术的进展历程及其应用领域;重点论述了CVD技术的大体原理和典型的CVD工艺及其特点;同时分析了CVD技术的优势和缺点,和CVD技术的进展趋势,并展望其应用前景。
关键词:
化学气相沉积;粉体材料;工艺原理;研究进展;应用
ResearchDevelopmentandApplicationofChemicalVaporDepositionTechniqueinPreparePowderMaterials
WANGBin,LUOKang-bi
(FacultyofChemicalEngineering,KunmingUniversityofScienceandTechnology,Kunming,650093)
Abstract:
Chemicalvapordeposition(CVD)referstotheuseofrawmaterialgasinthegasphaseparticlesareformedbychemicalreactionandnucleation,thegrowthoftwophasecompositefilms,particles,orcrystalwhiskeretc.Thetechnologicalprocessofthesolidmaterial.Thispapermainlydiscussesthedevelopmentcourseofchemicalvapordepositiontechniqueanditsapplicationfield;ExpoundstheCVDtechnologythebasicprincipleandtypicalCVDprocessanditscharacteristics;AtthesametimeanalyzedtheadvantagesanddisadvantagesofCVDtechnique,anddevelopmenttendencyofCVDTechnique,anditsapplicationforegroundisprospected.
Keywords:
chemicalvapordeposition;powdermaterial;technicalprinciple;researchdevelopment;application
1.化学气相沉积的大体概念:
化学气相沉积(ChemicalVaporDeposition:
简称CVD)是指利用气体原料在气相中通过化学反映形成大体粒子并通过成核、生长两个时期合成薄膜、粒子、晶须或晶体等固体材料的工艺进程[1]。
该技术是以挥发性的金属卤化物、氢化物或有机金属化合物等物质的蒸气为原料,通过化学气相反映合成所需粉末。
CVD法不仅能够制备金属粉末,也能够制备氧化物、碳化物、氮化物等化合物粉体材料。
目前,用此法制备TiO2、SiO2、Sb2O3、Al2O3、ZnO等超微粉末已实现工业化生产。
通过化学气相沉积制备粉体材料的方式有很多,依照反映类型能够分为气相氧化、气相还原、气相热解、气相水解等;依照反映器内压力不同可分为常压CVD、低压CVD、超真空CVD等;按加热方式不同可将其分为电阻CVD、等离子CVD、激光CVD、火焰CVD等[7]。
2.化学气相沉积技术的进展历程:
化学气相沉积是一种古老的“新工艺”。
说它古老,因为早在1000连年前的古代,咱们民族的先人就用气相工艺来制取用于做墨的“烟”(炭黑),这在宋朝的《墨经》和明代的《天工开物》中都有图文并茂的记载[10]。
化学气相沉积技术的研究始于19世纪末期,具有产业开发价值的典型应用是Lodyguine在1893年取得的专利:
氢气还原金属氯化物在铂丝上沉积钼、钨等难熔金属作为白炽灯丝。
尔后CVD技术被引入物质提纯进程中,采纳氯气与各类金属和金属化合物反映生成金属氯化物,再用氢气还原这种金属氯化物从而有效地实现金属分离、富集、提取与精炼[6]。
20世纪50年代初到60年代末是CVD技术研究和应用的一个顶峰期。
这一快速进展专门大程度上得益于那时材料科学学科体系的初步形成。
在这一大背景下,人们开始从材料学科的角度来看待各类冶金物理进程。
CVD技术的研究重点也从物质提纯等冶金进程转移到材料制备进程上。
为了增进CVD各个相关领域和谐进展,1960年举行了第l届CVD国际学术会议,会议主席JohnM.Blocher,Jr.建议采纳“ChemicalVaporDeposition”作为这一材料制备技术的专用术语,取得了CVD学术界的普遍认可,“CVD”被正式纳入材料科学的学科术语范围。
这期间,CVD技术在制备半导体薄膜、刀具涂层和各类耐氧化、耐侵蚀和耐热冲击涂层等上取得了普遍的工业应用。
CVD技术由此成长为材料合成化学的一个重要新领域[6]。
早在20世纪70~80年代,美国和日本的研究人员就开展了电阻CVD法制备超微粉末的研究,而且以氢气为还原剂制备出高纯度的Fe、Co、Ni、Cu、W等金属超微粉末,粉末平均粒径在100~600nm之间。
随后,在CVD法制备化合物粉末及复合粉体材料方面也进行了大量研究:
ZHUWZ等用电阻CVD法制备出10nm左右的SiC粉末,并探讨了工艺参数对粉末性能的阻碍。
YONGSH等用氢气还原FeCl3与CoCl2混合蒸气制得粒径为0.2~1.0μm的Fe-Co复合粉末。
用LCVD技术制备超微粉末的研究始于20世纪70年代,1978年美国MIT材料与能源研究所的CANNONWR和HAGGERTYJS等用CO2激光诱导化学气相反映合成了硅系超微颗粒(Si、Si3N4、SiC),使LCVD研究进入一个崭新时期。
1986年前后,美国MIT已研制成大型激光制粉装置[7]。
从20世纪70年代初至今,CVD技术在材料制备领域取得了重大成功。
CVD技术大体上经历了从无机非金属材料的制备领域进展到金属材料的制备领域,从薄膜生长技术和材料表面改性技术进展到块体材料制备技术,从传统实验技术时期进展到引入电子运算机进行材料辅助设计时期[6]。
3.化学气相沉积法的大体原理
化学气相沉积是把含有组成薄膜元素的气态反映剂或液态反映剂的蒸气及反映所需其它气体引入反映室,在衬底表面发生化学反映,并把固体产物沉积到表面生成薄膜的进程。
CVD法制粉进程要紧包括化学反映、形核、晶粒生长(表面反映和外延生长)和粒子凝并与聚结4个步骤。
在整个进程中,前3个步骤足在短时刻内完成的,后期的凝并与聚结对粉末颗粒的尺寸、结构、形貌等起决定作用[7]。
(1)化学反映
CVD的化学反映要紧可分两种:
一是通过一种或几种气体之间的反映来产生沉积,如超纯多晶硅的制备、纳米材料(二氧化钛)的制备等;另一种是通过气相中的一个组分与固态基体(有称衬底)表面之间的反映来沉积形成一层薄膜,如集成电路、碳化硅器皿和金刚石膜部件的制备等。
通过物质之问的化学反映,取得粉末产品的前驱体,并使之达到后续成核进程所需的过饱和度。
反映进程包括6个步骤:
(a)原料气体向基片表面扩散;(b)原料气体吸附到基片;(c)吸附在基片上的化学物质的表面反映;(d)析出物在表面的扩散;(e)产物从气相分离;(f)从产物析出区向块状固体的扩散。
[2]温度和反映物浓度是阻碍这一进程的要紧因素。
CVD法制粉的合成反映多数为快速的刹时反映,因此常受传递因素的操纵。
(2)粉末颗粒的形核
均匀成核是制备单分散粉体材料的基础。
依照晶核形成理论,成核率是CVD法制粉进程中的工艺重要指标。
[7]决定成核率大小的最关键因素是ΔG(形成1个新相核心时的自由能变),而关于气相一固相的转变进程,ΔG直接取决于其过饱和度P/Po(Po为T温度下的平稳蒸气压,P为实际蒸气压)。
在采纳CVD法制粉时,高过饱和度要紧通过大的温度梯度,即高温蒸发、低温冷凝来实现,但事实上形核速度并非随着过饱和度增加而无穷制地增加。
在快速冷却系统里,由于粘度明显增加,阻碍了分子的运动,从而抑制有序晶体的形成。
在选择反映体系和设计工艺参数时,有2个问题必需考虑:
1)可否气相成核。
只有过饱和度足够大的反映体系才能在气相中均匀成核而取得粉体,因此必需选择平稳常数大的反映体系。
2)临界晶核尺寸。
依照成核理论,形成的稳固核胚的临界半径为ro=2σ/(Δg)(σ为表面自由能,Δg为气、固两相的自由能之差)。
由于σ随温度的转变并非明显,故ro要紧取决于Δg,而Δg要紧取决于过饱和度,过饱和度越大,Δg越大。
过饱和度主若是靠局部降温来实现,而温度降低对σ阻碍不大。
因此,过饱和度S增大,临界核胚尺寸即临界半径减小。
在过饱和状态下,临界半径代表着稳固存在颗粒的最小尺寸。
在过饱和气态中的颗粒,当其尺寸小于临界半径时,将会消溶,相反,尺寸大于临界半径的颗粒将会继续长大。
(3)晶核生长
在通常的成核进程中,新形成的晶核表面都会吸附反映物中的原子或离子,并在颗粒表面发生相应的化学反映,通过外延生长使核表面扩张,这确实是核的表面反映与扩散机制,由此致使的外延与表面反映生长,使得晶核长大。
实际CVD制粉中,成核与生长进程很难截然分开,总有一些已生成的颗粒不断长大,而另一些新颗粒又在生成。
另一方面,晶核生长速度受温度的阻碍,温度升高,化学反映速度提高,颗粒生长速度相应增大,有利于减少颗粒各向异性生长。
(4)颗粒凝并与聚结
气相中形成的单体核、分子簇和低级粒子在布朗运动作用下发生碰撞,凝并聚结为最终颗粒,这确实是颗粒的凝并生长机制。
这种生长机制几乎在所有超微颗粒制备中都普遍存在,它是颗粒生长的主体。
2个颗粒通过碰撞能够在合成时刻内完全融合在一路,那么能够合成一个较大的致密的颗粒。
通常提高合成温度可加速融合进程,在高温时,颗粒粒度小,表面扩散系数专门大,因此以表面扩散为要紧机制的颗粒烧结并合的速度也专门大,能够使多个低级颗粒及时并合,形成大量的微小密实颗粒;一旦温度降低,将会限制颗粒问的结点生长,从而阻碍颗粒的并合,因此使得树枝状的凝聚体开始生长形成。
由于凝并碰撞生长机制的存在,致使最终颗粒的粒径较生长初期明显增大,并造成颗粒成份、结构与形态方面的诸多不同。
4.化学气相沉积的工艺进程
4.1工艺的5个大体要素[10]:
(1)气源:
能够是固态或液态的蒸发(升华)源,或气态的反映剂。
(2)热源:
制造蒸发(升华)或发生化学反映的能量条件需知足3个方面的能量需求:
系统及气源的温升、热效应、系统对环境的热损失。
(3)气氛:
能够是真空,或惰性、氧化性的。
(4)工艺参数监控系统:
主若是工作室内温度、压力及气体流量等的监控。
(5)粉体的搜集系统。
CVD装置大致由四部份组成:
原料气体和载气的供给及混合系统、反映炉、废气处置系统、操纵系统[2]。
其反映炉可分为热壁式(HotWal1)和冷壁式(ColdWall)两种,热壁式是从外部对整个反映室进行加热,这种方式可均匀对基片进行加热,但一样不可幸免向反映室内壁柝出。
冷壁式只对基板进行加热而不加热反映壁。
CVD大体工艺流程如图1所示:
4.2典型的CVD工艺[2]
(1)热灯丝CVD
热灯丝CVD是在热CVD的基础上进展起来的利用W,Ta,Mo等做灯丝材料给反映气体加热的装置。
其特点是通过热灯丝的局部高温加速反映气体的分解,增进化学反映的发生和加速产物的析出速度,而基板温度能够在1000℃以下,从而使整个腔体的温度比热CVD大为降低,与等离子CVD及激光CVD相较,设备及工艺简单,但沉积温度仍然较高,不能实现低温及室温沉积。
(2)等离子CVD(PCVD):
在高真空条件下,利用硅烷或氮气、氨气等,通过射频电场而产生辉光放电形成等离子体,以增强化学反映,从而降低沉积温度。
能够在常温到350℃条件下沉积氮化硅、氧化硅及非晶硅膜等。
在辉光放电的低温等离子体内的“电子气”的温度比一般气体分子平均温度高10~100倍,即反映气体能够接近环境温度,而这时电子能量足以使气体分子键断裂并致使化学活性粒子的产生,使本来需要在高温下进行的化学反映由于反映气体的电激活大大降低了反映温度,所产生的活化分子、原子基团之间彼此反映而最终沉积生成薄膜。
用PCVD法可调剂工艺参数方便地操纵薄膜的组成结构,从而取得均匀致密稳固性好的薄膜。
(3)微波等离子体CVD(ECRPCVD)
微波等离子体CVD是以微波作为加热源的CVD技术。
其大体原理是将用磁控管产生的微波(频率2.45GHz)用波导送入等离子体生成室。
等离子体生成室中电子在微波场的作用下产生螺旋运动,被螺旋加速的电子运动频率和微波频率一致时,产生电子回旋共振(ElectronCyclotronResonance:
ECR)和共振吸收现象。
吸收微波被加速的电子进一部和中性分子相碰撞,使分子离子化,在低温下可高产率取得稳固的、高密度的等离子体。
其大体特点如下:
1 能够在常温下取得高质量的薄膜;
2 离子的能量较低(10~20eV),对基板的损伤少;
3 能够操纵膜的组成、结构与应力;
4 不仅适用于半导体元件的制备,也适合于在高分子材料上沉积;
5 沉积速度较快。
各类CVD方式制备Si3N4的工艺参数及特点如表1所示
表1各类CVD方式制备Si3N4的工艺参数及特点
5.化学气相沉积技术的应用
用CVD技术所备的材料不仅应用于宇航工业上的特殊复合材料、原子反映堆材料、刀具材料、耐热耐磨耐侵蚀及生物医用材料等领域,而且还被应用于制备与合成各类粉体材料、块体材料、新晶体材料、陶瓷纤维及金刚石薄膜等等。
今天它作为应用于大规模集成电路技术的铁电材料、绝缘材料、磁性材料、光电子材料的薄膜的制备技术也是不可缺少的。
(1)爱惜涂层
CVD法制备的TiN、TiC、Ti(C,N)等薄膜具有很高的硬度和耐密性,在刀具切削面上仅覆l~3μm的TiN膜就能够够使其利用寿命提高3倍以上。
通过沉积取得的Al2O3、TiN等薄膜耐蚀性专门好,含有铬的非晶态的耐蚀性那么更高。
Mo和W的CVD涂层也具有优良的高温耐侵蚀性能,能够应用于涡轮叶片、火箭发动机喷嘴等设备零件上。
目前部份离子镀Al、Cu、Ti等薄膜已代替电镀制品用于航空工业零件上。
(2)微电子技术
在超大规模集成电路制作中,化学气相沉积能够用来沉积多晶硅膜、钨膜、铝膜、金属硅化物、氧化硅膜和氮化硅膜等,这些薄膜材料能够用作栅电极、多层布线的层间绝缘膜、金属布线、电阻和散热材料等。
化学气相沉积在制备这些材料层的进程中慢慢取代了如硅的高温氧化和高温扩散等旧工艺,在现代微电子技术中占主导地位。
(3)超导技术
CVD制备超导材料是美国无线电公司(RCA)在20世纪60年代发明的,用化学气相沉积生产的Nb3Sn低温超导带材涂层致密,厚度较易操纵,力学性能好,是目前烧制高场强小型磁体的最优良材料。
现已用化学气相沉积法生产出来的其它金属间化合物超导材料还有Nb3Ge、V3Ga、Nb3Ga等。
(4)太阳能利用
目前制备多晶硅薄膜电池多采纳CVD技术,包括LPCVD和PCVD工艺。
现已试制成功的硅、砷化镓同质结电池和利用Ⅱ一V族、I一Ⅵ族等半导体制成的多种异质结太阳能电池。
如SiO2/Si、GaAs/GaAlAs、CdTe/CdS等。
6.化学气相沉积技术的优势与缺点
6.1CVD技术的优势
与其他沉积方式相较,CVD技术除具有设备简单、操作保护方便、灵活性强、能够持续生产、设备本钱低、产生的颗粒纯度高、粒径散布窄等优势外,还具有以下优势:
(1)能够在大气压(常压)或低于大气压下进行沉积,低压成效更好;
(2)能够在远比材料熔点低的温度下进行材料合成;
(3)能够操纵材料的晶体结构,还能够使其沿特定的结晶方向排列;
(4)能够操纵材料的形态(粉末状、纤维状、枝状、管状、块状等);
(5)不需要烧结助剂,能够高纯度合成高密度材料;
(6)结构操纵一样能够从微米级到亚微米级,在某些条件下能够达到A级水平;
(7)能够形成多种金属、合金、陶瓷和化合物镀层。
6.2CVD技术的缺点
(1)要紧缺点是反映温度较高,沉积速度较低(一样每小时只有几μm到几百μm),难以局部沉积;
(2)参与沉积反映的气源(NH3、H2S等气体)和反映后的余气都有必然的毒性;
(3)镀层很薄,已镀金属不能再磨削加工,如何避免热处置畸变是一个专门大的难题。
7.化学气相沉积技术的进展趋势
随着工业生产要求的不断提高,CVD的工艺及设备取得不断改良,现已取得了更多新的膜层,并大大提高了膜层的性能和质量。
与此同时交叉、综合地利用复合的方式,不仅启用了各类新型的加热源,还充分运用了各类化学反映、高频电磁(脉冲、射频、微波等)及等离子体等效应来激活沉积离子,成为技术创新的重要途径。
CVD技术由于采纳等离子体、激光、电子束等辅助方式降低了反映温度,使其应用的范围加倍广漠,下一步应该朝着减少有害生成物,提高工业化生产规模的方向进展。
目前CVD工艺中经常使用的NH3、H2S等气体,或有毒性、侵蚀性,或对空气、湿度较为灵敏。
因此,寻觅更为平安、环保的生产工艺和增强尾气处置的研究在环境问题日趋突出的今天有着尤其重要的意义。
另外,利用高效稳固的催化剂增进CVD制粉进程,或与物理方式结合,在低温、高真空条件下制备粉体材料也成为以后化学气相沉积技术进展的方向。
另外,CVD反映沉积温度的更低温化,用CVD更精准地操纵材料的组成、结构、形态与性能技术的开发,厚膜涂层技术,利用残余应力提高材料强度的技术,大型持续CVD薄膜及涂层制备技术,新材料的合成技术,具有新的结构的反映器的研制,新的涂层材料及具有新的功能的材料体系的探讨等等,是尔后研究的重要课题。
结语
化学气相沉积作为一种超级有效的材料表面改性方式。
具有十分广漠的进展应用前景。
它关于提高材料的利用寿命、改善材料的性能、节省材料的用量等方面起到了重要的作用,为社会带来了显著的经济效益。
随着各个应用领域要求的不断提高,对化学气相沉积的研究也将进一步深化。
CVD技术的进展和应用也将跨上一个新的台阶。
参考文献
[1]张昭,彭少方,刘栋昌.无机精细化工工艺学[M].北京:
化学工业出版社,2005:
111-115.
[2]唐新峰,袁润章.化学气相沉积技术的研究及在无机材料制备中的应用进展(待续)[J].武汉工业大学学报,1994,16
(2):
135-139.
[3]唐新峰,袁润章.化学气相沉积技术的研究及在无机材料制备中的应用进展(续完)[J].武汉工业大学学报,1995,17
(2):
119-121.
[4]杨西,杨玉华.化学气相沉积技术的研究与应用进展[J].甘肃水利水电技术,2020,44(3):
211-213.
[5]张迎光,自雪峰.化学气相沉积技术的进展[J].科技论坛,2005,(12):
82-84.
[6]黎宪宽,陈力,蔡宏中,等.化学气相沉积技术及在难熔金属材料中的应用[J].稀有金属材料与工程,2020,39
(1):
438-443.
[7]刘志宏,张淑英,刘智勇,等.化学气相沉积制备粉体材料的原理及研究进展[J].粉末冶金材料科学与工程,2020,14(6):
359-364.
[8]王豫,水恒勇.化学气相沉积制膜技术的应用与进展[J].热处置,2001,16(4):
1-4.
[9]赵峰,杨艳丽.CVD技术的应用与进展[J].热处置,2020,24(4):
7-10.
[10]戴遐明,李庆丰.粉体的气、固相合成[J].中国粉体技术,2000,6:
15-20.
[11]胡昌义,李靖华.化学气相沉积技术与材料制备[J].稀有金属,2001,25(5):
364-368.
[12]赵薇.化学气相沉积技术在环境科学中探讨[J].硅谷,2020,19:
47.
[13]王亨瑞,雷亚民,玄真武,等.论化学气相沉积(CVD)金刚石技术最新进展[J].超硬材料工程,2020,22
(1):
22-30.
[14]李敏,李盼,王维刚.气相法制备纳米材料[J].中国粉体技术,2020,14
(2):
54-58.
[15]周生刚,竺培显,黄子良,等.气相法制备纳米粉体材料研究新进展[J].材料导报,2020,22(Z2):
100-103.
[16]汪广进,余意,程凤,等.过渡金属氮氧化物制备方式的研究进展[J].材料导报,2021,26(9):
27-31.
[17]杨林生,王君,陈长琦.硬质薄膜技术的最新进展[J].真空,2020,46(6):
35-39.