超高强度汽车钢板氢致延迟断裂敏感性测试及评价规范.docx
《超高强度汽车钢板氢致延迟断裂敏感性测试及评价规范.docx》由会员分享,可在线阅读,更多相关《超高强度汽车钢板氢致延迟断裂敏感性测试及评价规范.docx(15页珍藏版)》请在冰豆网上搜索。
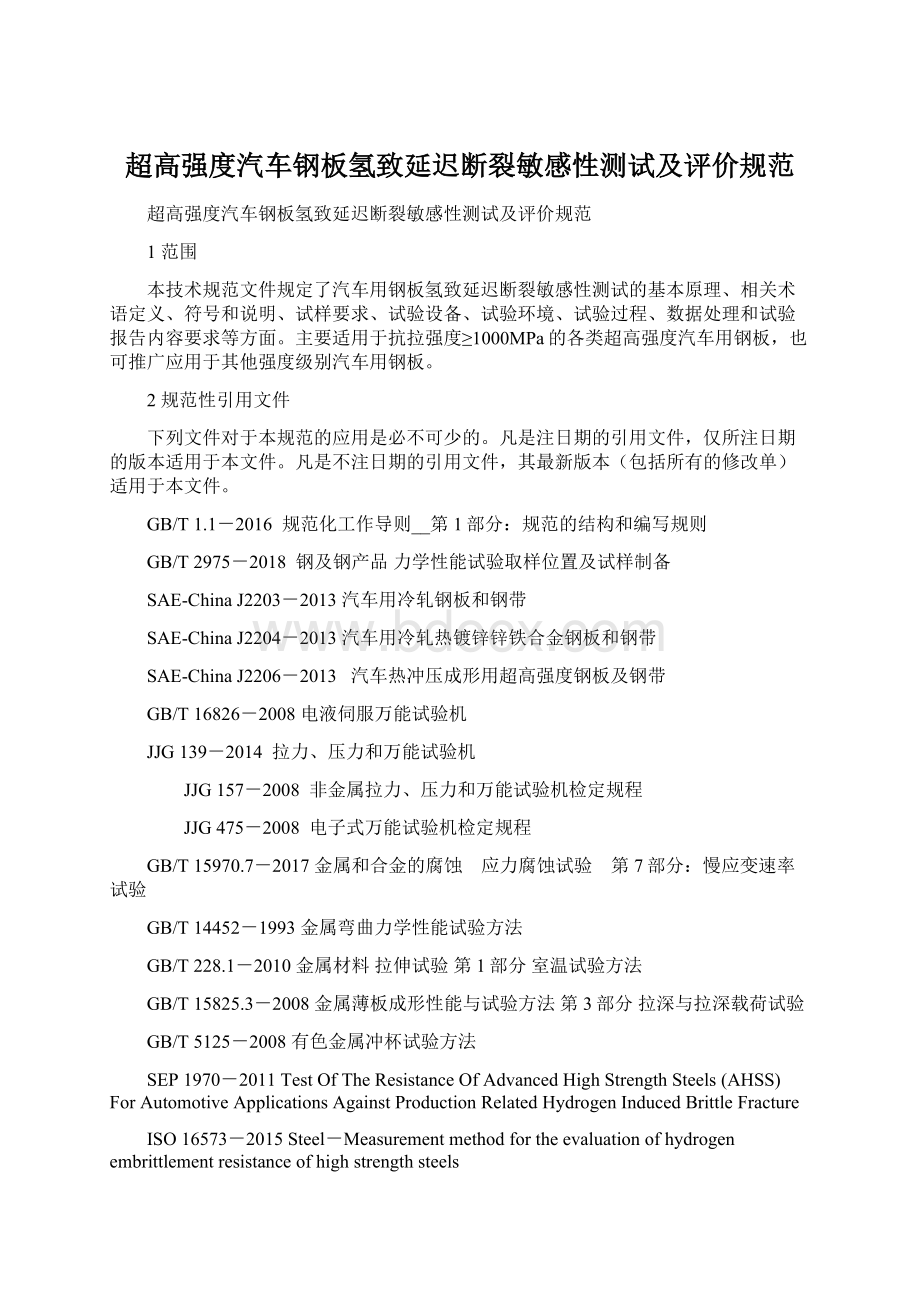
超高强度汽车钢板氢致延迟断裂敏感性测试及评价规范
超高强度汽车钢板氢致延迟断裂敏感性测试及评价规范
1范围
本技术规范文件规定了汽车用钢板氢致延迟断裂敏感性测试的基本原理、相关术语定义、符号和说明、试样要求、试验设备、试验环境、试验过程、数据处理和试验报告内容要求等方面。
主要适用于抗拉强度≥1000MPa的各类超高强度汽车用钢板,也可推广应用于其他强度级别汽车用钢板。
2规范性引用文件
下列文件对于本规范的应用是必不可少的。
凡是注日期的引用文件,仅所注日期的版本适用于本文件。
凡是不注日期的引用文件,其最新版本(包括所有的修改单)适用于本文件。
GB/T1.1-2016规范化工作导则__第1部分:
规范的结构和编写规则
GB/T2975-2018钢及钢产品力学性能试验取样位置及试样制备
SAE-ChinaJ2203-2013汽车用冷轧钢板和钢带
SAE-ChinaJ2204-2013汽车用冷轧热镀锌锌铁合金钢板和钢带
SAE-ChinaJ2206-2013汽车热冲压成形用超高强度钢板及钢带
GB/T16826-2008电液伺服万能试验机
JJG139-2014拉力、压力和万能试验机
JJG157-2008非金属拉力、压力和万能试验机检定规程
JJG475-2008电子式万能试验机检定规程
GB/T15970.7-2017金属和合金的腐蚀 应力腐蚀试验 第7部分:
慢应变速率试验
GB/T14452-1993金属弯曲力学性能试验方法
GB/T228.1-2010金属材料拉伸试验第1部分室温试验方法
GB/T15825.3-2008金属薄板成形性能与试验方法第3部分拉深与拉深载荷试验
GB/T5125-2008有色金属冲杯试验方法
SEP1970-2011TestOfTheResistanceOfAdvancedHighStrengthSteels(AHSS)ForAutomotiveApplicationsAgainstProductionRelatedHydrogenInducedBrittleFracture
ISO16573-2015Steel-Measurementmethodfortheevaluationofhydrogenembrittlementresistanceofhighstrengthsteels
JB/T6261-1992电阻应变仪技术条件
GB/T13992-2010金属粘贴式电阻应变计
GB/T8170-2008数值修约规则与极限数值的表示和判定
3试验原理
本规范通过U型弯梁延迟断裂试验法和冲杯延迟断裂试验法,评估钢板在平面应变状态(贴近零件成形及碰撞等服役工况)及模拟腐蚀环境下发生氢致延迟断裂的可能性。
通过慢应变速率拉伸试验法、预充氢拉伸试验法、恒载荷延迟断裂试验法获取钢种的氢脆指数,临界断裂应力等指标,从不同角度实现对钢板氢致延迟断裂敏感性的定量表征,并可作为不同钢板氢致延迟断裂敏感性对比的依据,从而为国内汽车用钢生产和应用的企业提供一套简便、可靠、成本较低的超高强度钢板氢致延迟断裂敏感性测试评价方法,满足超高强度汽车钢板的应用需求。
1)针对冷成形超高强度汽车钢板,考虑其零件实际制造工艺特性,在来料状态下即可进行氢致延迟断裂敏感性的测评;
2)针对热成形超高强度汽车钢板,考虑其零件制造工艺特性,统一在淬火态条件下进行材料的氢致延迟断裂敏感性测评;
3)针对超高强度钢车身零件,可根据零件外观及其加工工艺特性,选取零件上应力集中的部位进行取样,对零件取样不再进行任何预处理,直接进行零件级别的氢致延迟断裂敏感性测评。
4术语定义
4.1氢致延迟断裂(HIC):
是材料在低于抗拉强度应力载荷和酸性环境双重作用下发生的滞后断裂行为。
4.2充氢:
采用一定技术手段,使材料基体富含氢元素的过程。
4.3充氢电流密度:
充氢过程中单位时间内通过试样表面单位面积的电量大小,单位:
mA/cm2。
4.4标称抗拉强度:
由牌号或其生产厂家提供的材料理论抗拉强度下限值(Ultimatetensilestrength,UTS),单位:
MPa。
4.5U型弯梁延迟断裂试验法:
试验前先将钢板按照一定尺寸规格切割,处理成规范试样,将试样放在特制模具中,利用专用加载设备进行U型弯曲成形,直至弯曲角度达到既定要求,采用工装紧固,放置在含氢介质中进行静置处理。
采用断裂试样占总试样的百分比、试样的断裂应力-断裂时间曲线等,作为评价或对比不同钢板氢致延迟断裂敏感性的依据。
4.6冲杯延迟断裂试验法:
试验前先将钢板按照一定尺寸规格切割,处理成规范试样,在专用成形试验机上压延成具有不同高度值的杯形试样,再将试样放置在含氢介质条件下进行静置处理,采用断裂试样占总试样的百分比、断裂应力-断裂时间曲线、试样裂纹数量等作为评价或对比不同钢板氢致延迟断裂敏感性的依据。
4.7慢应变速率拉伸试验法(SSRT):
试验前先将钢板按照一定尺寸规格切割,处理成规范试样,将试样置于含氢溶液中,利用专用设备进行电化学充氢处理,同步利用力学性能加载设备,对试样在低应变速率10-7/s~10-3/s条件下进行拉伸试验,获取断裂应力及塑性参量,并与未充氢试样的拉伸力学性能进行对比,求出氢脆指数,作为评价或对比不同钢板氢致延迟断裂敏感性的依据。
4.8预充氢拉伸试验法:
试验前先将钢板按照一定尺寸规格切割,处理成规范试样,将试样置于含氢溶液中,利用专用设备进行电化学预充氢处理,对充氢后材料,利用专用加载设备进行准静态拉伸试验,获得相应的断裂应力和塑性参量,并与未充氢试样的拉伸力学性能进行对比,求出氢脆指数,作为评价或对比不同钢种氢致延迟断裂敏感性的依据。
4.9恒载荷延迟断裂试验法:
试验前先将钢板按照一定尺寸规格切割,处理成规范试样,将试样置于含氢溶液中,利用专用设备进行电化学充氢处理,同步(也可在试样预充氢后)采用具有恒应力输出功能的专用试验设备或夹具,对材料施加恒定应力载荷,直至试样发生断裂结束,获得相应的断裂应力-断裂时间的变化曲线,求出临界断裂应力,作为评价或对比不同钢板氢致延迟断裂敏感性的依据。
4.10氢脆指数EH:
预充氢或同步充氢条件下,试样在准静态拉伸过程中的断裂应力(σ1)及其断面收缩率(Z1)相比于未充氢试样在准静态拉伸条件下的断裂应力(σ0)及其断面收缩率(Z0)的变化率,单位:
%。
其值越大则材料的氢脆敏感性越弱。
4.11临界断裂应力σHIC:
试样在含氢介质及恒应力作用下,在规定时间范围内不发生氢致延迟断裂所对应的最大应力值。
其值越大则材料的氢脆敏感性越弱。
5试样要求
1)尺寸规格:
①U型弯梁延迟断裂试验试样推荐尺寸规格如图1。
(a)一般试验试样(I型)
(b)一般试验试样(II型)
(c)加速试验试样(SEP1970)
图1U型弯梁延迟断裂试验试样尺寸规格(mm)
②慢应变速率拉伸、恒载荷延迟断裂、预充氢拉伸三种试验的试样尺寸规格若无特殊需求,均推荐参照GB/T228.1规定执行,根据板厚确定尺寸规格。
③冲杯延迟断裂试样尺寸规格推荐参照GB/T15825.3,采用圆片状试样,其直径选用Φ85mm、Φ90mm、Φ95mm三种规格之一。
若受来料尺寸规格限制,也可参照GB/T5125,推荐选用Φ52mm、Φ55mm、Φ60mm三种规格之一。
④针对零件取样,对其外观、尺寸规格在本规范中不做硬性规定,可通过试验双方协商,结合零件结构、工艺及服役工况等综合因素进行确定。
2)试样状态:
试样可通过在零件产品或板料上取样获得,针对板材来料的交货状态及零件的加工工艺不做硬性规定。
应尽量保证来料与测试试样的状态相一致,若不一致则应在报告中注明来料及试样状态。
针对冷成形板料,其相关技术要求推荐参照SAE-ChinaJ2203或SAE-ChinaJ2204要求执行;针对热成形板料,其相关技术要求推荐参照SAE-ChinaJ2206要求执行;若来料为零件,则本规范中无硬性规定。
3)取样方法:
针对板材来料(冲杯延迟断裂试验除外),若无特殊需求,应确保取样长度方向与板材的轧向平行,若需按其他方向取样,应在试验报告中进行注明。
此外,取样应避开来料表面所有可见裂纹等缺陷的区域。
针对试样的尺寸及形状精度,若为冷及热成形钢板料取样,参照本规范对应的各种试验方法要求执行(U型弯梁延迟断裂试验试样加工精度推荐参照GB/T14452执行);若为在零件上取样,对试样形状及其尺寸精度由试验双方协商确定。
4)针对试样加工,推荐采用线切割或激光切割,采用其他加工方式应确保不对试样组织性能构成显著影响。
5)完成试样加工后应对试样进行边缘去除毛刺、45º倒角等处理,倒角宽度推荐≤0.5mm,对于边缘存在可见裂纹的试样应视为废品样。
6)针对一批待检试样应尽量在同一零件或同一批次板材上获取,若在不同零件或不同批次板材上取样,应在报告中体现批次信息。
7)针对制备好的试样,应尽量在一周以内进行试验,针对一周以内无法开展试验的试样,应将其置于可防止氢渗透的密闭环境中(推荐置于≤-30℃的液氮环境中)进行保存。
8)试样其余的取样和加工制备要求均参照GB/T2975执行。
9)针对试样的结构、尺寸规格、取样方式等若有其他特殊需求,可由试验双方协商而定,并在报告中注明。
6试验环境
若无特殊要求,针对U型弯梁延迟断裂试验、冲杯延迟断裂试验、慢应变速率拉伸试验、预充氢拉伸试验及恒载荷延迟断裂试验,均在室温和常压环境条件下完成。
若有特殊需求,也可在其他设特定温度或压力环境条件下进行试验,但应在报告中注明试验条件。
7试验设备(工装)
1)U型弯梁延迟断裂试验:
若无特殊要求,推荐采用满足弯曲加载功能需求的特制工装完成弯曲应力加载,推荐加载工装结构见附录C;利用工装对试样进行预弯曲时,推荐在工装与试样间增加非金属垫片,以降低二者接触部位的应力值(见附录C)。
2)冲杯延迟断裂试验:
若无特殊要求,推荐采用专用成形试验机,其应满足GB/T15825.3或GB/T5125中对试验设备的相关要求。
3)慢应变速率拉伸试验:
若无特殊要求,推荐在常规电液伺服材料试验机或其他可满足慢应变速率加载要求的设备上进行,若采用电液伺服材料试验机其应满足GB/T16826、GB/T15970.7等相关设备要求。
若采用其他类型设备也应满足GB/T15970.7要求。
4)预充氢拉伸试验:
若无特殊要求,推荐在常规电液伺服材料试验机或其他可满足准静态加载功能要求的试验设备上进行,若采用电液伺服材料试验机其应满足GB/T16826规范中的技术要求,若采用其他设备则其应满足GB/T228.1中对设备的相关要求。
5)恒载荷延迟断裂试验:
若无特殊要求,推荐在具有恒定应力输出功能的专用电液伺服材料性能试验机上进行,除加载应力需求外,其还应满足GB/T16826规范中的其他技术要求。
若采用其他具备同等功能的加载设备(含工装,如采用螺钉旋拧或悬挂砝码等方式对试样施加恒应力),应满足对应试验规范对设备(工装)的要求。
6)针对上述2)~5)项中所涉试验设备精度均应满足至少达到1级水平要求(试验力示值相对误差≤±1%),且应定期参照JJG139、JJG157、JJG475等要求进行精度校核。
7)针对上述3)~5)项试验,可根据试样的结构及其尺寸规格、加载设备的试样夹持接口结构及其尺寸规格,设计专用夹具实现对试样的可靠夹持,其结构尺寸在本规范内不做硬性要求。
8)U型弯梁延迟断裂试验和冲杯延迟断裂试验中的应变量可采用接触式(如应变检测仪+应变片)或非接触式测量设备(如非接触式光学测量系统,DIC)。
采用接触式设备进行检测时,应变仪及应变片应分别确保满足JB/T6261及GBT13992技术要求;采用非接触式设备检测时,应确保其满足生产厂家企业产品技术要求。
9)针对U型弯梁延迟断裂试验,利用工装对试样进行预弯曲时,推荐在工装与试样间增加非金属垫片,以降低工装与试样接触部位的应力值(附录C)。
8试验过程
1)U型弯梁延迟断裂试验:
1.试样准备:
试验前需清除试样表面的油污、锈迹、氧化皮等,脱碳层或各类镀层可由试验双方协商确定保留或去除,若保留则应在试验报告中记录表面脱碳层或镀层厚度值。
2.试样装夹:
采用材料性能试验机或专用弯曲工装夹具,对图1结构试样进行预弯曲加载。
针对图1(a)结构试样,其装夹流程为将试样置于夹具中部,通过旋拧夹具两端螺母,推动夹具上的滑块向中部移动,使试样片发生弯曲变形,直至样品的弯曲跨距大小达到既定指标值,实现弯曲应力加载(如图3);针对图1(b)~(c)结构试样,装夹流程为将试样置于特制模具中,利用力学加载试验机对试样进行弯曲,然后采用螺杆及螺母等配件紧固试样,实现弯曲应力加载(图4)。
图3预弯曲过程示例(I型)图4预弯曲过程示例(II型)
3.应变测量:
弯曲过程中可采用应变测试仪(图5(a))实时检测试样最小弯曲半径部位的应变量;为提高应变测量的量程和准确度,推荐采用DIC进行弯曲应变测试。
利用该方法代替传统的引伸计或应变片等方法,不仅能更加精确地对局部微小区域内的应变值进行实时测量,且能有效避免环境因素对测量过程的干扰(如腐蚀介质对应变片等检测器件的损坏),还能解决应变量过大时应变片易脱落的问题。
若采用DIC方式测试弯曲应变(图5(b)),相关操作流程及要求按DIC厂商要求执行。
(a)应变片测量
(b)非接触式应变测量(DIC)
图5预弯曲过程中的接触式/非接触式应变测量示例
4.应力标定:
选取同材质试样参照GB/T228.1技术要求,进行准静态拉伸试验,获得相应的工程应力应变曲线数据,在应力应变数据对中找到每个弯曲试样实测应变量对应的应力值,近似作为试样最小弯曲半径部位的应力值,用于标定氢致延迟断裂的临界应力值。
5.应力范围设定:
推荐材料抗拉强度的为0.3~0.9倍作为弯曲应力的选取范围。
相同弯曲应力的试样为一组,推荐每个应力条件下重复试样≥2件,试验组数≥5。
6.浸泡试验:
推荐选用0.1mol/LHCL水溶液作为材料氢致延迟断裂敏感性评价的环境介质。
若仅作材料性能对比试验,也可选用0.5mol/LHCL水溶液或采用图1(c)试样尺寸规格做加速试验。
若有特殊需求也可选其他含氢介质,介质类别推荐参照ISO16573标准要求选取。
为保证试验结果可靠性,试验过程中应定期检测溶液PH值,实时进行溶液更新,保证溶液浓度稳定。
将预弯曲后的试样置于上述相关含氢介质中进行静置处理。
从试样静置于含氢介质中起,实时监测试样表面裂纹产生情况并进行记录(检查试样表面裂纹时用毛刷刷掉覆盖在试样表面的腐蚀产物,然后用放大镜观察是否有裂纹并做记录,量化裂纹大小:
如肉眼观察到的头发粗细的裂纹)。
记录发生开裂试样对应的时间及加载应力值(图6),并绘制关系曲线。
图6试验后开裂试样外观示例
7.结果记录:
若选用0.1mol/LHCL水溶液,推荐300小时为浸泡上限时间,若在此时间段内试样不发生开裂,则认定试样合格;若希望延长静置时间进行验证则推荐采用700小时和1000小时两个时间评价点,建议试样最长静置时间不宜超过1000小时。
若在指定静置时间范围内出现试样开裂,则记录下断裂试样对应的弯曲应力值及静置时间,并绘制关系曲线。
若选用加速试验工况(0.5mol/LHCL水溶液)或其他处理介质,则静置时间范围的选取由试验双方协商后确定;酸性溶液浸泡过程中,试样观察时间间隔不大于2小时,推荐采用具备持续录像及存储功能的视频监控设备对试样进行不间断观测,以实现对试样开裂时间点的精确记录。
2)冲杯延迟断裂试验:
1.试样准备:
试验前清除试样表面的油污、锈迹、氧化皮等,试样表面若存在脱碳层或镀层,由试验双方协商确定保留或去除,若保留则应在试验报告中记录表面脱碳层或镀层厚度值。
2.试样装夹:
将试样置于成形试验机上进行冲杯成形处理,试验过程参照GB/T15825.3或GB/T5125规范要求执行(图7)。
凸模压入深度设定不做硬性规定,最大压入深度的选取应以确保试样不发生开裂为原则。
压入深度一致的试样为一组,推荐每组试样数≥2件,试验组数≥5。
图7冲杯试验示例
3.应力标定:
定义为冲杯加载后,杯形件各部位残余应力中的最大值。
可采用专用设备或仿真法,检测试样的残余应力分布,获取最大残余应力值作为试样的加载应力。
若采用应变值作为评价变量,则可采用压入深度作为表征参量,或采用非接触应变测量系统的测试结果。
4.浸泡试验:
推荐参照U型弯梁浸泡试验方法执行。
5.结果记录:
推荐参照U型弯梁浸泡试验方法执行。
3)慢应变速率拉伸延迟断裂试验:
1.试样准备:
试验前需清除试样表面的油污、锈迹、氧化皮等,脱碳层或各类镀层可由试验双方协商确定保留或去除,若保留则应在试验报告中记录表面脱碳层或镀层厚度值。
2.参照GB/T228.1规范要求,进行不少于3件准静态拉伸试验,试验后获取每件试样的断裂应力(σ0)及断面收缩率(Z0),并取平均值。
3.电化学充氢处理:
电化学充氢过程如图8。
推荐充氢溶液可选用0.2mol/LNaOH水溶液(若有特殊需求,可参照ISO16573标准要求选取其他溶液。
);推荐充氢电流密度应≤2.0mA/cm2、充氢电极为Pt电极。
充氢时间可根据试验方产品技术需求或参照行业经验确定,也可利用试验机专门配备(或外接)的氢浓度测试仪器(如TDS氢热分析仪)实时监测氢含量变化,推荐时间不宜超过48小时(若有特殊需求,也可延长充氢时间,但最长不超过72小时)。
每个充氢电流密度参数条件下试样的重复数量不少于3件。
若作为对比试验,充氢电流密度值的设定数量应≥2。
图8电化学充氢处理
4.慢应变速率加载:
在充氢过程中,应同步将试样置于试验机上进行慢应变速率拉伸试验。
加载应变速率设定范围为10-7~10-3/s,推荐取10-5/s~10-4/s中间速率范围,由系统自动采集并显示加载过程中的应力变化,若材料出现断裂则试验结束。
每个充氢电流密度参数条件下试样的重复数量不少于3件。
5.结果记录:
记录每件试样的断裂应力(σ1)及断后收缩率值(Z1),并取平均值,进而求出试样的氢脆指数EH。
4)预充氢拉伸试验:
1.试样准备:
试验前需清除试样表面的油污、锈迹、氧化皮等,脱碳层或各类镀层可由试验双方协商确定保留或去除,若保留则应在试验报告中记录表面脱碳层或镀层厚度值。
2.拉伸试验:
参照GB/T228.1规范要求,进行不少于3件准静态拉伸试验,试验后记录每件试样的断裂应力(σ0)及断面收缩率(Z0),并取平均值。
3.预电化学充氢处理:
同慢应变速率拉伸延迟断裂试验的充氢方法(图8)。
4.充氢后拉伸试验:
将预充氢后的试样立即置于拉伸试验机上,参照GB/T228.1要求进行准静态拉伸试验。
5.结果记录:
记录下每件试样的断裂应力值(σ1)及断后收缩率值(Z1),并取平均值,进而求出试样的氢脆指数EH。
5)恒载荷延迟断裂试验:
1.试样准备:
试验前需清除试样表面的油污、锈迹、氧化皮等,脱碳层或各类镀层可由试验双方协商确定保留或去除,若保留则应在试验报告中记录表面脱碳层或镀层厚度值。
2.恒应力加载:
利用专用恒载荷拉伸试验机或者其他方式(如螺钉旋拧或配备砝码加载)对试样施加恒定的应力(图9),推荐应力范围为抗拉强度的0.3~0.9倍。
相同加载应力的试样为一组,推荐每个应力条件下重复试样≥2件,在各充氢电流密度条件下的应力水平数≥5。
3.充氢处理:
同慢应变速率拉伸延迟断裂试验的充氢方法(图8)。
图9充氢过程
4.结果记录:
记录不同充氢电流密度参数条件下每组试样出现断裂失效样所对应的加载应力值及断裂时间值,取100小时(或200小时)充氢条件下重复3件均未出现断裂失效的最大加载应力为临界断裂应力σHIC。
备注:
可根据实际需求,在本技术规范中可选取5种试验方法中的任意一种或几种进行试验。
其中若为模拟评估板料在接近实际服役工况下的抗氢致延迟断裂性能,则推荐选用U型弯梁延迟断裂试验法,该方法也可作为钢板供需双方在钢板供货技术协议中指定的基本质量测评方法之一;若重点关注零件成形工艺对其氢致延迟断裂敏感性影响,侧重于为产品研发、生产等提供指导依据,则可选用冲杯延迟断裂试验法;若仅作为钢板氢致延迟断裂性能对比试验,推荐采用慢应变速率拉伸试验、恒载荷延迟断裂试验和预充氢拉伸试验法。
此外,针对其他强度级别的钢板,若需开展氢致延迟断裂性能测评,也可参照本规范流程及相关要求执行。
9数据处理
上述试验结束后,除可直接得出的结果数据外,针对各关键结果参数数据的确定方式如下:
1.氢脆指数EH,可由下式
(1)或式
(2)计算确定:
(1)
(2)
式中各字母代表的物理量。
2.临界断裂应力σHIC:
以恒应力试验过程中发生断裂的时间为横坐标,相同充氢电流密度条件下,不同断裂时间点所对应的应力值为纵坐标,断裂应力-时间曲线(附录A)上100小时(或200小时)试样不发生断裂对应最大应力即为σHIC。
10试验报告
本试验结束后应在报告中提供以下内容:
1.试样基本信息;
2.试验环境条件;
3.试验设备型号,关键参数及外观照片(含工装);
4.试验过程参数(力学参数、电化学充氢参数、含氢介质类别等);
5.试验步骤及过程要求;
6.试验结果(氢脆指数,临界断裂应力,断裂时间等);
7.试验前后试样外观照片;
8.其他。
附录A
(资料性附录)
图1氢脆指数表征示例
图2临界断裂应力表征示例
附录B
(资料性附录)
来料状态确认及处理要求的补充说明
当前汽车车身用钢板材从成形工艺角度,可分为冷成形及热成形两类,由于两者间的制造工艺模式的显著差异性,在进行氢致延迟断裂敏感性测量时,应区别对待。
针对冷成形和热成形板料及其零件的处理方式和要求具体如下:
1)冷成形板料取样:
一般冷成形零件制造过程中,基体仅受成形力的作用,不会发生本质性的变化(如强烈相变),由于试验过程中也将引入外应力,因此无需对冷成形零件板料进行试验前预处理。
2)热成形板料取样:
由于实际的热成形零件基体为淬火态,因此本规范推荐热成形板料应为淬火态。
若试验委托方无法提供淬火态板材,则可经试验双方协商,由委托方提供相应的热成形工艺处理条件,并由试验承担方负责完成淬火板制备。
若试验委托方无法提供热成形条件,则推荐统一按照930℃保温5min热处理规范对板料进行淬火处理。
淬火处理必须采用固体平板模具淬火法,淬火质量以确保板材基体为近全淬火马氏体组织或满足试验委托方或相关热成形零件厂商性能技术要求等为基准
3)零件取样:
零件上取样可直接用于氢致延迟断裂敏感性测试。
由于实际成形后零件各部位的性能有所差异,且各自的服役要求也可能不同,因此取样部位应由试验委托方根据己方零件使用需求提出,由试验双方协商确定。
4)表面镀层:
原则上应将其看作是材料本身不可分割的一部分,因此试验时应予以保留,但试验前应注明镀层厚度值,以便于对试验结果的准确分析。
附录C
(资料性附录)
U型弯梁延迟断裂试验夹具外观示例
(a)弯曲加载夹具(I型)
(b)弯曲加载夹具(II型)
图1典型U型弯梁延迟断裂试验加载夹具结构外观示例