基于PAC的流量控制系统设计.docx
《基于PAC的流量控制系统设计.docx》由会员分享,可在线阅读,更多相关《基于PAC的流量控制系统设计.docx(37页珍藏版)》请在冰豆网上搜索。
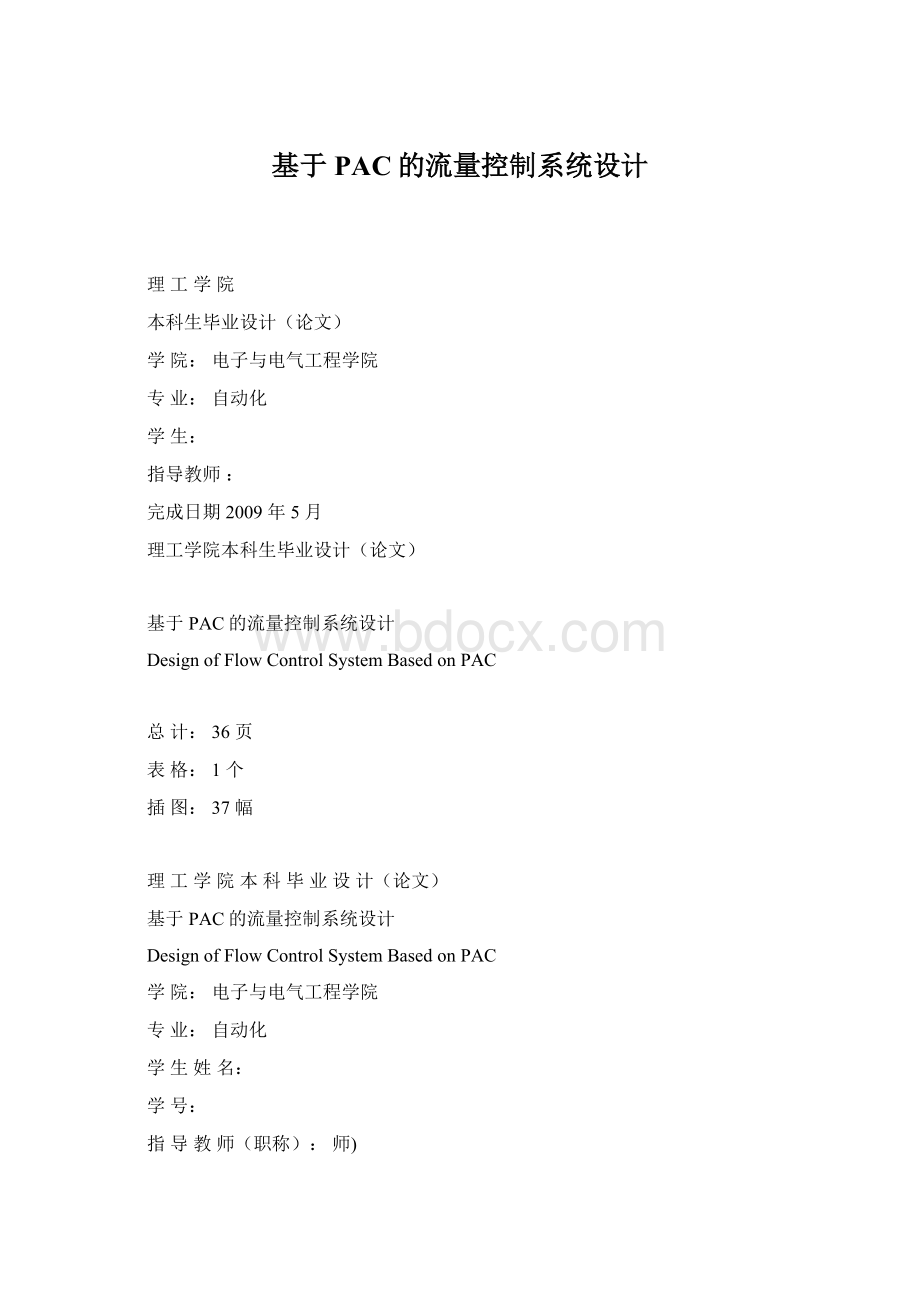
基于PAC的流量控制系统设计
理工学院
本科生毕业设计(论文)
学院:
电子与电气工程学院
专业:
自动化
学生:
指导教师:
完成日期2009年5月
理工学院本科生毕业设计(论文)
基于PAC的流量控制系统设计
DesignofFlowControlSystemBasedonPAC
总计:
36页
表格:
1个
插图:
37幅
理工学院本科毕业设计(论文)
基于PAC的流量控制系统设计
DesignofFlowControlSystemBasedonPAC
学院:
电子与电气工程学院
专业:
自动化
学生姓名:
学号:
指导教师(职称):
师)
评阅教师:
完成日期:
理工学院
NanyangInstituteofTechnology
基于PAC的流量控制系统设计
[摘要]本文基于PACSystemsRX3i控制器,以ProficyMachineEdition软件为开发平台,在iFIX上做组态监控的基础上,主要完成对流量控制系统设计。
本设计采用流量传感器采集并反馈流量信号给PID控制器,PID控制器控制变频器的输出频率,从而调节水泵转速实现对流量的控制。
通过对流量控制系统软件的编程和相关硬件调试,系统实现了预定的流量控制。
运行结果表明流量控制的精度达到了设计要求。
[关键词]流量控制;组态监控;程序设计;PID算法
DesignofFlowControlSystemBasedonPAC
Abstract:
ThisarticleisbasedonPACSystemsRX3icontrollerandusestheProficyMachineEditionsoftwareasadevelopmentplatform,configuresmonitoringoniFIX,mainlyaccomplishthedesignofflowcontrolsystem.ThisdesignusesaflowsensortocollectandfeedbacktheflowratetoPIDcontroller.PIDcontrolleradjustsoutputoffrequencyconverter,theflowisincontrolthroughadjustingspeedofwaterpumpaccordingtofrequency.Bydesigningflowcontrolsystemsoftwareanddebugginghardware,thesystemrealizesthedesiredflowcontrol.Testingresultsshowthattheaccuracyofflowcontrolreachesthedesignrequirement.
KeyWords:
Flowcontrol;configurationmonitoring;programdesign;PIDalgorithm
1引言
本章首先阐明了本文的研究目的与意义,其次论述了过程控制的发展历程、PAC的优点,最后叙述了流量控制的发展及国内外研究现状及主要工作。
1.1研究目的和意义
流量是过程控制中主要的控制参数,随着生产水平和科学技术的不断发展,流量控制系统在钢铁、石油、化工、食品饮料等各行各业的应用越来越广泛,但现代工业过程控制系统对设备和被控系统的安全性、可靠性和有效性的要求也越来越高。
这时PAC的出现解决了这一问题,PAC是新一代的可编程控制器,它比现有的PLC具有更强大的处理速度和通信速度,以及编程能力。
PAC提供了开放的工业标准,扩展的域功能,通用的开发平台,以及其他高级功能,确保了现代工业生产过程高效、安全的进行,保证并提高产品质量。
无论是现在还是将来,PAC都将在生产自动化领域扮演一个极其重要的角色。
本设计中采用GE先进的PACSystemsRX3i对流量系统进行控制,通过流量传感器采集并反馈信号给PID控制器,PID控制器控制变频器输出频率,从而调节水泵转速实现对流量的控制。
采用PAC控制将会使系统的安全性、可靠性和有效性得到进一步的提升。
1.2过程控制的发展
随着瓦特蒸汽机的发明和使用,人类的工业水平得到了快速发展,将人们从繁重的劳动中解脱出来,大大的提高了生产力和劳动效率。
随着工业进一步的快速发展和科技水平的提高,工业自动化成了势在必行的发展趋势。
工业自动化是机器设备或生产过程在不需要人工直接干预的情况下,按预期的目标实现测量、操纵等信息处理和过程控制的统称。
工业自动化的实现是建立在自动控制系统的基础上的。
而作为自动控制系统的核心—控制器,随着科技的发展和工业的高要求也在不断的更新。
在现代工业控制中,过程控制技术是一历史较为久远的分支。
在本世纪30年代就已有应用。
过程控制技术发展至今天,在控制方式上经历了从人工控制到自动控制两个发展时期。
在自动控制时期内,过程控制系统又经历了三个发展阶段,它们是:
分散控制阶段,集中控制阶段和集散控制阶段[1]。
从过程控制采用的理论与技术手段来看,可以粗略地把它划为三个阶段:
开始到70年代为第一阶段,70年代至90年代初为第二阶段,90年代初为第三阶段开始。
其中70年代既是古典控制应用发展的鼎盛时期,又是现代控制应用发展的初期,90年代初既是现代控制应用发展的繁荣时期,又是高级控制发展的初期。
第一阶段是初级阶段,包括人工控制,以古典控制理论为主要基础,采用常规气动、液动和电动仪表,对生产过程中的温度、流量、液位和压力进行控制,在诸多控制系统中,以单回路结构、PID策略为主,同时针对不同的对象与要求,创造了一些专门的控制系统,如:
使物料按比例配制的比值控制,克服大滞后的Smith预估器,克服干扰的前馈控制和串级控制等等,这个阶段的主要任务是稳定系统,实现定值控制。
这与当时生产水平是相适应的。
第二阶段是发展阶段,以现代控制理论为主要基础,以微型计算机和高档仪表为工具,对较复杂的工业过程进行控制。
这个阶段的建模理论、在线辨识和实时控制已突破前期的形式,继而涌现出了大量的先进控制系统和高级控制策略,如克服对象特性时变和环境干扰等不确定影响的自适应控制,消除因模型失配而产生不良影响的预测控制等。
这个阶段的主要任务是克服干扰和模型变化,满足复杂的工艺要求,提高控制质量。
1975年,世界上第一台分散控制系统在美国Honeywell公司问世,从而揭开了过程控制崭新的一页。
分散控制系统也叫集散控制系统,它综合了计算机技术、控制技术、通信技术和显示技术,采用多层分级的结构形式,按总体分散、管理集中的原则,完成对工业过程的操作、监视、控制。
由于采用了分散的结构和冗余等技术,使系统的可靠性极高,再加上硬件方面的开放式框架和软件方面的模块化形式,使得它组态、扩展极为方便,还有众多的控制算法(几十至上百种)、较好的人机界面和故障检测报告功能。
经过20多年的发展,它已日臻完善,在众多的控制系统中,显示出出类拔萃的风范,因此,可以毫不夸张地说,分散控制系统是过程控制发展史上的一个里程碑。
第三阶段是高级阶段,目前正在来到。
PAC是一种新型的可编程自动化控制器,它满足控制引擎集中,涵盖PLC用户的多种需要,以及制造业厂商对信息的需求。
与PLC相比更具有开放的体系结构和优秀的互操作性、灵活性;与PC相比又具有更高的稳定性和更好的实时性,因此能更好地满足现代工业自动化的要求。
是目前工业自动化领域研究的热点之一。
流量是过程控制中主要的控制参数之一,由于液体本身的属性及控制机构的摩擦、噪声等的影响,控制对象具有一定纯滞后和容量滞后的特点,流量输出的过程缓慢,呈现非线性,经常采用PID控制器来实现对流量的控制和调节[2]。
即使在美国、日本等工业发达国家,PID控制的使用率仍达90%,PID控制技术在国外经历了数十年的发展,从模拟PID控制发展到数字PID控制,技术不断完善与成熟。
尤其近十多年来,随着微处理技术的发展,国外对智能控制的理论研究和应用研究十分活跃,智能控制技术发展迅速,如专家控制、自适应控制、模糊控制等,现已成为工业过程控制的重要组成部分。
智能控制与常规PID控制相结合,形成所谓智能PID控制,这种新型的控制方式已引起人们的普遍关注和极大兴趣,并已得到较为广泛的应用。
流量控制系统在国内各行各业的应用虽然已经十分广泛,随着生产水平和科学技术的不断发展,现代控制系统的规模日趋大型化,复杂化[3]。
对生产过程运行在线监控,及时准确的把握生产运行状况,已成为目前过程控制领域的一个研究热点。
但从国内生产的流量控制器来讲,总体发展水平仍然不高,同国外的日本、美国、德国等先进国家相比仍然有着较大的差距。
1.3本文主要工作
论文主要完成的工作有:
(1)首先是流量计的选择,在条件允许的情况下,选择合适的流量计以确保精度。
(2)完成PAC与计算机、水箱、控制台之间的硬件连线。
(3)PID是过程控制中最基本、最常用、最重要的控制算法。
在PLC和组态软件中一般都有PID指令或模块,但是算法程序不公开,这使使用者对算法的正确使用产生障碍。
所以全面了解PID算法并完成编程和调试是非常重要的。
(4)在ProficyMachineEdition软件中完成对流量控制的编程。
(5)利用iFIX组态进行实时监控并做出监控画面,生成曲线图。
2控制系统硬件设计
2.1控制方案
本设计中用到电动机、变频器、流量传感器、两个水箱、PAC、阀门等硬件。
其流量控制管道仪表流程图如图1所示。
在实验台中流量控制分为2种控制方案,一种是工频磁力泵和电动调节阀的控制方案,另外一种是变频磁力泵和电磁阀的控制方案。
当然也可以两种方案一起使用,但是他们的基本原理都是一样的,考虑到实际问题我选择了第二种的控制方案,且没有用到电磁阀,所以它是一个变频调速过程。
PAC模拟量输入模块将流量传感器检测到的流量信号作为反馈信号,并与给定量比较,经过PID控制器运算后输出调节变频器从而达到控制流量的目的。
控制方框图如图2所示。
图1流量控制管道仪表流程图
图2控制方框图
启动电源之前,先把手动阀1、2打开是为了工作时管道畅通。
启动电源,在ProficyMachineEdition软件中下载连接程序无误后,摁下启动按钮,设置一个流量值,通过PAC的数字量输出模块保持工作指示灯亮,使变频器上电且启动,通过流量传感器采集流量值反馈给PAC中的PID控制器,对偏差进行运算输出一个数值传送到变频器,从而带动电机旋转,水从B水箱经流量传感器到达A水箱并被指示仪表显示出来。
采集到的流量值在设定值之间浮动,多次调试后达到最佳值。
实验完毕后,摁下停止按钮,并关闭电源。
其系统结构图如图3所示。
图3系统结构图
流量控制系统管道仪表的组成:
(1)磁力泵:
磁力泵(磁力驱动泵)主要由泵头、磁力传动器(磁缸)、电动机、
连接底板等几部分零件组成。
磁力泵磁力传动器是有内、外转子及不导磁的隔离套等组成[4]。
当电动机带动外转子旋转时,磁场能穿透空气隙和非磁性物质,带动与叶轮相连的内磁转子作同步旋转,实现动力的无接触同步传递,将容易泄露的动密封结构转化为零泄漏的静密封结构。
磁力泵从B水箱到A水箱抽送水,是整个系统的动力单元。
(2)变频器:
变频器发送频率到磁力泵,从而带动并控制磁力泵的转速。
(3)电磁继电器:
电磁继电器一般由铁芯、线圈、衔铁、触点簧片等组成的。
只要在线圈两端加上一定的电压,线圈中就会流过一定的电流,从而产生电磁效应,衔铁就会在电磁力吸引的作用下克服返回弹簧的拉力吸向铁芯,从而带动衔铁的动触点与静触点(常开触点)吸合。
当线圈断电后,电磁的吸力也随之消失,衔铁就会在弹簧的反作用力下返回原来的位置,使动触点与原来的静触点(常闭触点)释放。
这样吸合、释放,从而达到了在电路中的导通、切断的目的。
它主要是控制变频器的通断、指示灯的明灭。
(4)流量传感器:
采集瞬时的流量值反馈给控制器,控制器运算调节变频器从而控制流量的大小。
(5)流量指示仪表:
用以显示通过的瞬时流量值。
(6)水箱。
(7)阀门。
2.2流量的检测方法
流量的检测方法繁多。
根据流量的定义,流量的测量主要有以下4大类测量方法:
(1)差压流量测量法:
利用流体流过通道中阻力件时产生的压力差与流量之间的确定关系求得流量即是利用压力能与动能的转换和守恒原理而测量流量的。
(2)容积式流量测量法:
利用标准容积的容器,接连不断的对流动介质进行测量从而直接确定流量。
(3)流体振动式测量法:
流体在流动过程中遇到某种阻碍后在它的下游会产生一系列自激振荡的旋涡,测量流量旋涡的振动频率就可推算出流量值。
(4)流速式流量测量法:
通过测量管道截面上流体平均流速来测量流量。
本设计中用到的SMC流量计的检测方式是卡曼涡街式,即利用流体流过障碍物时产生稳定的漩涡,通过测量其漩涡产生的频率而实现流量计量的[5]。
卡曼涡街是流体横向流过圆柱体时,在圆柱体背面的两侧交替产生旋涡,且在脱离后形成旋涡尾流的现象。
产生旋涡的原因是流体受阻后动能和压力能相互转换,且压强沿圆柱体周边向及边界层的厚度方向发生变化,边界层外部流体的较大压强作用迫使边界层内部压强较小的质点向相反方向流动,从而使边界层增厚,形成旋涡,然后从圆柱体表面脱离,旋涡随着流速增大被拉长后消失。
当一侧旋涡长大脱离时,另一侧的旋涡正在形成并长大,这样交替形成两行旋涡尾流,形似“涡街”。
本设计中用到的SMCFLOWSWITCHPF2W520-03-2属于流体振动式测量法的范畴。
SMCFLOWSWITCHPF2W520-03-2是水用数字式流量开关,检测方式是卡曼涡街式,流量和设定流量量程为2~16L/min,最小单位为0.1L/min,显示单位分别为瞬间流量和累计流量。
它是将检测到的流量信号传送给PAC,显示部分用的是PF2W300,流量计和显示部分外形如图4所示。
其具体参数如表1所示,流量传感器三视图如附录中图1所示。
表1SMC流量计参数表
型号
PF2W520-03-2
测定流体
水
检测方式
卡曼涡街式
流量和设定流量范围
2~16L/min
设定最小单位
0.1L/min
显示单位
瞬时流量
L/min,gal(US)/min
积算流量
L,gal(US)
使用压力范围
0~1MPa
耐压
1.5MPa
累积流量范围
0~999999L
使用温度范围
0~50℃不结露
线性
±5%F.S.以下
精度
±3%F.S.以下
温度特性
±5%F.S.以下(0~50℃)
输出规格
27:
NPN开路选择30V80mA两输出
工作指示灯
ON灯亮OUT1:
绿色OUT2:
红色
响应时间
1秒
响应时间延迟
变量可调,窗口固定显示:
3位数
电源电压
DC12~24V(波动±10%以下)
工作电流
70mA以下
耐电压
外部端子和外壳间AC1000V1分钟
绝缘电阻
外部端子和外壳间2MΩ(DC500V)
抗噪音
1000Vp—p,脉冲宽度:
1μs,持续1ns
抗振动
10~500Hz振幅1.5mm,加速度98m/s2,X,Y,Z每个方向的较低频率,各两个小时
抗冲击
490m/s2,X,Y,Z方向,各三次
质量
520g(含软线)
防护等级
IP65
显示部分用输出
脉冲输出N通道开漏显示部分PF2W300用输出。
(参考规格:
最大负载电流10mA,最大施加电压30v)
模拟输出
电压输出1﹀5V
直线性:
±5%F.S.以下;许用负载阻抗:
100KΩ以上
电流输出4﹀20mA
直线性:
±5%F.S.以下;许用负载阻抗:
300Ω以下(DC12V)﹑600Ω以下(DC24V)
图4流量计的外形图
2.3控制器的选型
PACSystemsRX3i控制器是创新的可编程控制器,是中、高端过程和离散控制应用的新一代控制器。
它具备单一的控制引擎和通用的编程环境,并具有多种网络连接模块,使其能灵活、方便地构成功能强大的网络构架。
它的基本模块由背板(机架)、电源、CPU、开关量输入/输出模块、模拟量输入/输出模块、特殊模块等组成[6]。
其PAC硬件图如图5所示。
图5PAC硬件图
2.3.1电源模块
PACSystemsRX3i的电源模块像I/O一样简单地插在背板上,并且能与任何标准型号的RX3iCPU协同工作。
每个电源模块都具有自动电压适应功能,用户无需跳线选择不同的输入电压。
电源模块具有限流功能,发生短路时,电源模块会自动关断来避免零件损坏。
RX3i电源模块与CPU性能紧密结合能实现单机控制、故障安全和容错。
RX3i的电源模块的输入电压可以有100~240VAC、125VDC、24VDC或12VDC等备选。
本设计中用到的是IC695PSD040,该模块的输入电压范围是18~39VDC,提供40W的输出功率。
当电源模块发生内部故障时将会有指示,CPU可以检测到电源丢失会记录相应的错误代码。
该模块上4个LED灯指示该模块的工作状态,指示如下:
电源(绿色/琥珀黄):
当LED为绿色时,意味着电源模块在给背板供电。
当LED为琥珀黄时,意味着电源已加到电源模块上,但是电源模块上的开关是关着的。
P/S故障(红色):
当LED亮起时,意味着电源模块存在故障并且不能提供足够的电压给背板。
温度过高(琥珀黄):
当LED亮起,意味着电源模块接近或者超过了最高工作温度。
过载(琥珀黄):
当LED亮起,意味着电源模块至少有一个输出接近或者超过最大输出功率。
2.3.2CPU模块
本设计中用到的PACSystemsRX3i高性能的CPU是基于最新技术的具有高速运算和高速数据吞吐的处理器,在多种标准的编程语言下能处理高达32KI/O。
RX3i支持多种IEC语言和C语言,使得用户编程更加灵活。
RX3i广泛的诊断机制和带电插拔能力增加了机器周期运行时间,减少停机时间,用户能存储大量的数据,减少外围硬件花费。
C695CPU315是一个1Ghz的中央处理器,带有两个内置串行端口。
仅限通用背板使用PCI总线。
它能够支持多种语言,包括:
(1)继电器梯形图语言;
(2)指令表语言;(3)C编程语言;(4)功能块图;(5)OpenProcess;(6)用户定义的功能块;(7)结构化文本;(8)SFC。
CPU模块上有7个诊断用的LED,分别显示:
CPUOK、运行、输出允许、输入/输出强制、电池、系统故障、COM1和COM2端口激活状态。
2.3.3I/O模块
GEIP自动化提供一系列模块能支持不同的电压范围和类型、最大允许电流、隔离与响应时间等,以满足用户应用的需要。
本设计用到的I/O模块分为开关量输入/出模块和模拟量输入/出模块分别对应的是IC694MDL660、IC694MDL754、IC695ALG600、IC695ALG704。
数字量输入模块提供PLC和数字量信号(如接近开关、按钮、开关等)之间的连接接口。
IC694MDL660具有24VDC正/负逻辑32点输入,需要高密接线板。
数字量输出模块提供PLC和诸如接触器、继电器、BCD显示器和指示灯这样的外部输出设备之间的接口。
IC694MDL754有32点输出。
如:
Q00007是本设计中变频器上电的物理地址,Q00008是变频器启动的物理地址。
模拟量输入模块是将输入电流或电压转变成内在的数字数据,向PLCCPU提供所得的数字数据。
IC695ALG600是通用型模拟输入模块,提供8路通用输入通道和两路冷端补偿输入通道,输入端分成2个相同的组,每组4个通道。
如:
AI0001是本设计中采集流量的物理地址。
模拟量输出模块提供易于使用、用于控制过程的信号。
IC695ALG704有4个模拟量输出通道,由外部提供24V电源,具有快速的模拟量输出速度。
如:
AQ0007是模拟量输出模块输出给变频器控制频率大小的物理地址。
2.3.4以太网接口模块
以太网通信模块为IC695ETM001模块,用来连接PAC系统RX3i控制器至以太网。
通过它RX3i控制器也可以与其他PAC系统和90系列、VersaMax控制器进行通信。
以太网接口模块提供与其他PLC,运行主机通信工具包(或编程器软件的主机)和运行TCP/IP版本编程软件的计算机连接。
这些通信在一个4层TCP/IP上使用GESRTP和EGD协议。
以太网接口模块有两个自适应的10BaseT/100BaseTXRJ-45屏蔽双绞线以太网端口,用来连接10BaseT或者100BaseTXIEEE802.3网络中的任意一个。
这个接口能够自动检测速度,双工模式(半双工或全双工)和与之连接的电缆(直行或者交叉),而不需要外界的干涉。
以太网模块上有7个指示灯,简要说明如下:
(1)EthernetOK指示灯:
指示该模块是否能执行正常工作。
(2)LANOK指示灯:
指示是否连接以太网络。
(3)LogEmpty指示灯:
在正常运行状态下呈亮状态,如果有事件被记录,指示灯呈“熄灭”状态。
(4)2个以太网激活指示灯(LINK):
指示网络连接状况和激活状态。
(5)2个以太网速度指示灯(100Mbps):
指示网络数据传输速度(10Mb/sec(熄灭)或者100Mb/sec(亮))。
2.3.5IC695ALG600的参数设置
举例设置一下PAC硬件中IC695ALG600模块,它提供8路模拟输入通道和2个冷端温度补偿通道,输入端分成2个相同的组,每组4个通道,具有A/D转换功能。
在设置时,先选择用到的通道。
然后在选择的通道中进行设置,有好多类型如:
RTD、Voltage/Current、Disabled等。
本设计选用的是Voltage/Current,输入信号是电流信号。
在Range中设置电流的范围4mA到20mA。
在ChannelValueFormat中选择32位。
设置如图6所示。
图6IC695ALG600设置
2.4变频器
本设计中用到的变频器是SIEMENS的MicroMaster440。
MicroMaster440是全新一代可以广泛应用的多功能标准变频器。
它是专门针对与通常相比需要更加广泛的功能和更高动态响应的应用而设计的。
这些高级矢量控制系统可确保一致的高驱动性能,即使发生突然负载变化时也是如此。
由于具有快速响应输入和定位减速斜坡,因此,甚至在不使用编码器的情况下也可以移动至目标位置。
该变频器带有一个集成制动斩波器,即使在制动和短减速斜坡期间,也能以突出的精度工作。
它采用高性能的矢量控制技术,提供低速且高转矩输出和良好的动态特性,同时具备超强的过载能力,以满足广泛的应用场合。
其外形如图7所示。
图7变频器
主要特征:
支持200V-240V±10%,单相/三相,交流,0.12KW-45KW;支持380V-480V±10%,三相交流,0.37-250KW;采用矢量控制方式,可构成闭环矢量控制,闭环转矩控制;具有高过载能力,内置制动单元。
本设计用到的变频器范围为0到50Hz。
在操作方面也是比较简单的,但是在调试操作之前要阅读《MICROMASTER440使用大全》。
操作面板按键功能介绍图如图8所示:
图8按键功能介绍图
3iFIX监控设计
3.1iFIX软件简介
iFIX是全球最领先的HMI/SCADA自动化监控组态软件