炼钢材料设备.docx
《炼钢材料设备.docx》由会员分享,可在线阅读,更多相关《炼钢材料设备.docx(38页珍藏版)》请在冰豆网上搜索。
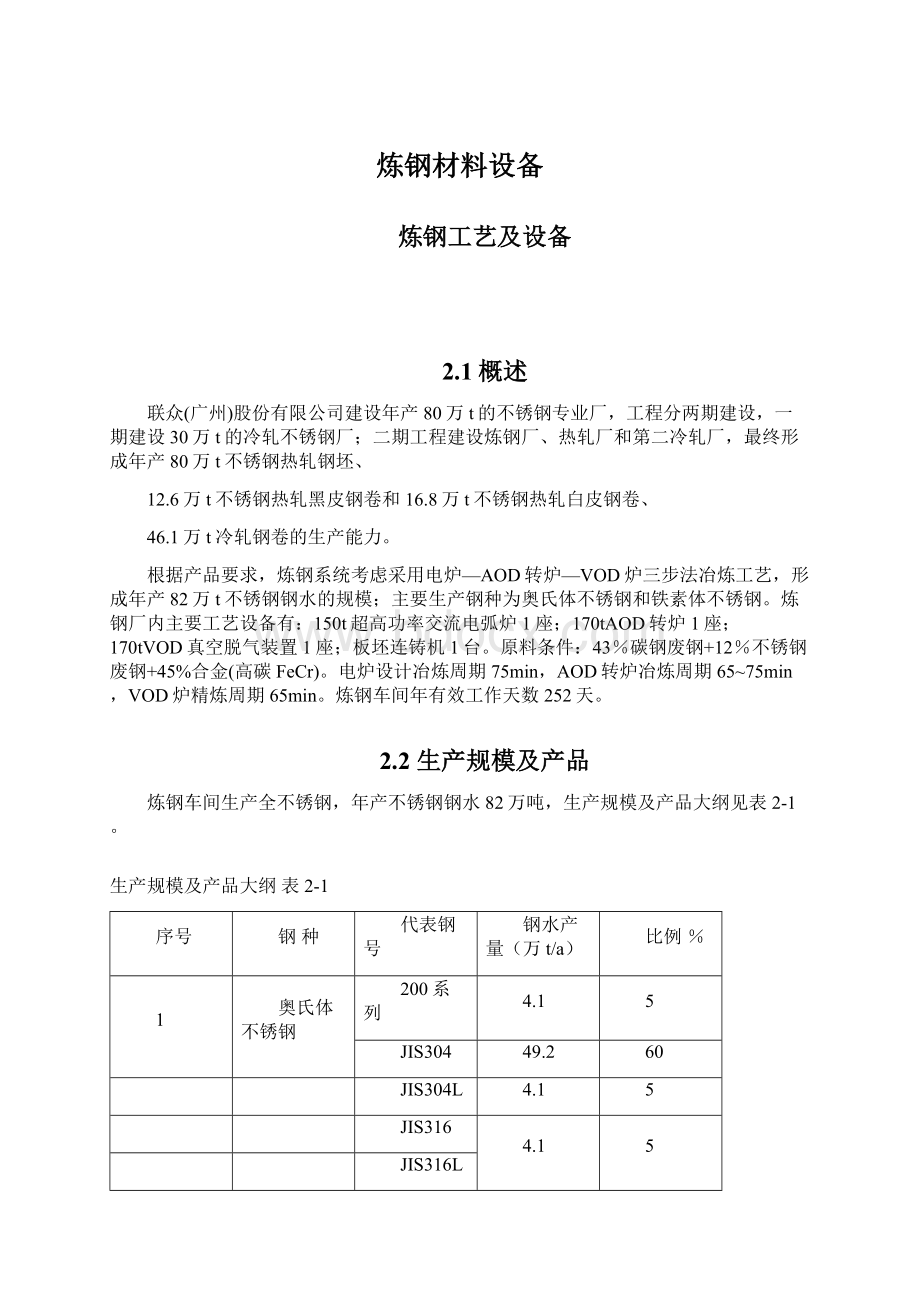
炼钢材料设备
炼钢工艺及设备
2.1概述
联众(广州)股份有限公司建设年产80万t的不锈钢专业厂,工程分两期建设,一期建设30万t的冷轧不锈钢厂;二期工程建设炼钢厂、热轧厂和第二冷轧厂,最终形成年产80万t不锈钢热轧钢坯、
12.6万t不锈钢热轧黑皮钢卷和16.8万t不锈钢热轧白皮钢卷、
46.1万t冷轧钢卷的生产能力。
根据产品要求,炼钢系统考虑采用电炉—AOD转炉—VOD炉三步法冶炼工艺,形成年产82万t不锈钢钢水的规模;主要生产钢种为奥氏体不锈钢和铁素体不锈钢。
炼钢厂内主要工艺设备有:
150t超高功率交流电弧炉1座;170tAOD转炉1座;170tVOD真空脱气装置1座;板坯连铸机1台。
原料条件:
43%碳钢废钢+12%不锈钢废钢+45%合金(高碳FeCr)。
电炉设计冶炼周期75min,AOD转炉冶炼周期65~75min,VOD炉精炼周期65min。
炼钢车间年有效工作天数252天。
2.2生产规模及产品
炼钢车间生产全不锈钢,年产不锈钢钢水82万吨,生产规模及产品大纲见表2-1。
生产规模及产品大纲表2-1
序号
钢种
代表钢号
钢水产量(万t/a)
比例%
1
奥氏体不锈钢
200系列
4.1
5
JIS304
49.2
60
JIS304L
4.1
5
JIS316
4.1
5
JIS316L
2
铁素体不锈钢
400系列
20.5
25
合计
100
代表钢种化学成分表表2-2
代表钢号
[C]
(%)
[Si]
(%)
[Mn]
(%)
[P]
(%)
[S]
(%)
[N]
(%)
[Cr]
(%)
[Ni]
(%)
[Mo]
(%)
[Ti]
(%)
304
0.035-0.055
0.5-0.6
1.0-1.3
≤0.03
≤0.01
≤0.06
18.05-18.3
8.03-8.15
304L
0.015-0.25
0.35-0.55
1.3-1.5
≤0.03
≤0.01
0.035-0.055
18.05-18.3
8.03-8.15
316L
≤0.025
0.55-0.7
0.7-0.9
≤0.03
≤0.004
0.025
16.1-16.3
10.05-10.15
2.05-2.25
409
≤0.015
0.4-0.6
≤0.5
≤0.035
≤0.004
≤0.012
11.1-11.3
≤0.3
7x(C+N)
430
0.035-0.05
0.25-0.4
0.45-0.55
≤0.03
≤0.008
0.035-0.055
16.1-16.3
≤0.2
2.3炼钢工艺确定及主要设备
2.3.1不锈钢冶炼工艺
目前世界上不锈钢的冶炼有三种方法,即一步法,二步法,三步法。
一步法:
即电炉一步冶炼不锈钢。
由于一步法对原料要求苛刻(需返回不锈钢废钢、低碳铬铁和金属铬),生产中原材料、能源介质消耗高,成本高,冶炼周期长,生产率低,产品品种少,质量差,炉衬寿命短,耐火材料消耗高,因此目前很少采用此法生产不锈钢。
二步法:
1965年和1968年,VOD和AOD精炼装置相继产生,它们对不锈钢生产工艺的变革起了决定性的作用。
前者是真空吹氧脱碳,后者是用氩气和氮气稀释气体来脱碳。
将这两种精炼设施的任何一种与电炉相配合,这就形成了不锈钢的二步法生产工艺。
采用电炉与VOD二步法炼钢工艺生产不锈钢具有如下优点:
1)VOD炉不仅可以生产不锈钢的所有品种,包括C+N≤150ppm的低碳低氮不锈钢,而且钢水含氮含氢量低,钢水质量较好;
2)VOD炉氧气耗量(10Nm3/t钢)、氩气耗量(0.3Nm3/t钢)、还原硅铁耗量(4kg/t钢)较少;
3)VOD炉设备投资少,仅5800万元,且对厂房适应性也较好;
4)VOD炉不需设置庞大的除尘系统、炉渣运输及处理系统。
其缺点:
1)由于VOD要求初炼钢水含C<0.6%左右,要求电炉出钢C在0.6%以下,因此需要采用高价中低碳FeCr以及20%不锈钢废钢进行配料,增加操作成本;
2)由于脱C速度较慢,精炼时间长(80-120分钟),生产率低;
3)电炉+VOD炉结合综合生产成本较高。
目前该法仅用于生产少量不锈钢,采用VOD炉生产不锈钢的厂家的产量约占不锈钢总产量的5.8%左右。
因此VOD炉比较适合小规模多品种的兼容厂的不锈钢生产。
采用电炉+AOD的二步法工艺生产不锈钢具有如下优点:
1)AOD生产工艺对原材料要求较低,电炉出钢含C可达到2%左右,因此可以采用廉价的高碳FeCr和20%不锈钢废钢作为原料,降低了操作成本;
2)AOD法可以一步将钢水中的碳脱到0.01%,且不锈钢中95%的品种都可以生产;
3)不锈钢生产周期较短,灵活性较好;
4)生产系统设备总投资较VOD贵,但比三步法少5800万元;
5)AOD炉生产一步成钢,人员少、设备少,所以综合成本较低。
其缺点:
1)由于侧吹风口的耐材熔损较快,炉衬使用寿命短(仅130-200炉);
2)还原硅铁消耗大(14kg/t钢);
3)目前还不能生产超低C、超低N不锈钢,且钢种含气量较高;
4)氩气耗量大(12-20Nm3/t钢);
目前世界上88%不锈钢采用二步法生产,其中76%不锈钢是通过AOD炉生产。
因此它比较适合大型不锈钢专业厂使用。
三步法:
即电炉+复吹转炉+VOD三步冶炼不锈钢。
其特点是电炉作为熔化设备,只负责向转炉提供含Cr、Ni的半成品钢水;复吹转炉主要任务是吹氧快速脱碳,以达到最大地回收Cr的目的;VOD真空吹氧负责进一步脱碳、脱气和成份微调。
三步法与传统的二步法电炉+AOD相比,有如下优点:
1)氩气消耗量低(0.6~2.0Nm3/t);
2)还原硅铁消耗低(8~10Kg/t);
3)复吹转炉炉衬寿命高(约900~1500炉,最高2000炉);
4)精炼周期短(60~70分),生产率高,易于连铸配合实现全连浇;
5)生产品种多(可以冶炼所有不锈钢产品);
6)钢水气体含量低,[N]=40-70ppm、[H]≤2ppm;
7)生产成本低,据国外比较三步法生产不锈钢比二步法节约9美元/t坯,据上钢三厂比较,节约160元/t坯。
因此三步法比较适合氩气供应比较短缺的地区,且生产低C、低N不锈钢比例较大的专业厂采用。
综合比较,考虑到新建钢厂100%生产不锈钢,生产规模大,生产品种多,且联众公司在三步法生产不锈钢的管理和生产实践上有着丰富的经验,因此设计采用电炉+AOD转炉+VOD的三步法不锈钢冶炼工艺。
2.3.3熔剂及铁合金加料系统工艺方案
由于冶炼不锈钢电炉、转炉及钢包炉需要散料较多,采用垂直皮带机系统集中供料。
EAF、AOD、钢包精炼炉分别采用3组高位料仓,熔剂及铁合金加料系统经垂直皮带机集中上料、分散供料给各高位料仓,再经过转运皮带机分别给电炉、炉后钢包及LF、VOD系统。
EAF高位料仓表表2-3
料仓序号
物料
料仓容积(m3)
堆比重(t/m3)
储存料重(t)
备注
1
活性石灰
100
1
100
2
Ni
100
3.5
350
3
FeCr(HC)
70
4
280
4
白云石
100
16
160
5
活性石灰
70
1
70
6
FeSi
25
2.6
65
7
FeCr(LC)
25
3
75
8
萤石
25
1.6
40
9
FeMo
70
4.7
329
10
备用
70
AOD高位料仓表表2-4
料仓序号
物料
料仓容积(m3)
堆比重(t/m3)
储存料重(t)
备注
1
FeCr(HC)
100
4
400
2
FeMo
25
4.7
117.5
3
白云石
25
16
40
4
萤石
25
1.6
40
5
Ni
50
3.5
175
6
废钢
70
2
140
7
FeNi(HC)
100
4
400
8
FeNi(HC)
70
4
400
9
FeNi(LC)
50
4
280
10
FeCrSi(LC)
50
3
75
11
FeCr(HC)
100
4
400
12
MgO
25
1
25
13
Al
25
1.5
37.5
14
FeSi
100
2.6
72.5
15
FeMn(HC)
50
3.6
180
16
SiMn(MC)
50
3.4
170
17
白云石
150
1.6
240
18
活性石灰
150
1
150
19
活性石灰
150
1
150
20
活性石灰
150
1
150
VOD/LF高位料仓表表2-5
料仓序号
物料
料仓容积(m3)
堆比重(t/m3)
储存料重(t)
备注
1
FeMo
25
4.7
117.5
2
Ni
25
3.5
87.5
3
FeMn(LC)
25
3.7
92.5
4
FeMn(HC)
25
3.6
90
5
FeCr(LC)
25
3
75
6
FeCr(HC)
25
4
100
7
MnSi(LC)
25
3.5
87.5
8
Al
25
1.5
37.5
9
FeSi
50
2.6
130
10
FeSi
50
2.6
130
11
活性石灰
100
1
100
12
白云石
25
1.6
40
13
备用
25
14
备用
25
15
萤石
25
1.6
40
16
活性石灰
100
1
100
2.3.4电炉转炉出渣
电炉、转炉出渣及扒渣站出渣均采用渣罐车出渣。
先将电炉、转炉渣流入18m3渣罐内,然后采用抱罐车运至翻渣间,经冷却回收后再运到渣场处理或直接运往渣场。
连铸钢包铸余渣采用回炉方式,这样电炉既可以利用铸余渣提前进行脱P、S,减少渣料消耗,进行综合利用,还可以减少铸余渣的运输。
电炉、转炉除尘后的烟尘也可以加入到电炉进行综合利用。
2.3.5电炉转炉修砌
目前炼钢车间电炉修砌方式可以采用离线修砌(活炉座)也可以采用在线修砌(死炉座)。
为了提高车间作业率,我们采用离线修炉工艺。
与一般转炉相比较来说,因为AOD精炼转炉炉衬寿命很短,只有几百炉,而且车间主要生产工艺设备均是一对一的关系,为了保证车间年产量,提高车间作业率,采用离线修理可以满足要求。
2.3.6电炉转炉除尘
近代电炉普遍都采用电炉四孔+密闭罩+屋顶罩三位一体的联合除尘方式,达到降低噪音和有效收集烟尘目的,经过布袋系统除尘后,气体含尘量小于10mg/Nm3,噪音下降至85分贝以下。
因此决定电炉除尘采用电炉四孔+密闭罩+屋顶罩的联合除尘方式,以满足现代化钢厂严格的环保治理要求。
转炉采用一次+二次烟气排烟系统,除尘采用干法除尘。
2.3.7主要设计特点和新技术的采用
为了保证该炼钢车间的现代化水平,确保把炼钢车间建成一个优质、高产、高效、低耗的车间,本设计将采用如下新工艺、新设备、新技术。
1)电炉采用超高功率电炉;
2)电炉采用辅助能源及炉内二次燃烧技术,以达到最佳能源利用;
3)电炉炉门外配置自耗式碳氧枪,在冶炼不锈钢时插入钢液中造泡沫渣,实现埋弧冶炼;
4)电炉采用水冷炉壁和水冷炉盖等技术;
5)采用出钢槽钢渣混出工艺,提高Cr的回收率;
6)采用导电横臂技术和短网系统三相平衡布置的技术;
7)在电炉出钢线附近设有在线钢包烘烤器,可做到“红包”出钢,降低出钢温度;
8)电炉出钢钢包车设有电子称量装置和钢包氩气搅拌系统;
9)电炉、出钢钢包、转炉、LF、VOD炉采用机械化、自动化加渣料及铁合金,进一步提高炼钢效率;
10)电炉采用四孔+密闭罩+屋顶罩相结合的除尘方式,转炉四周采用防烟室和炉前、炉后大门将转炉封闭起来的捕捉二次烟尘,满足现代化炼钢厂对环保的严格要求;
11)转炉采用顶侧复合吹炼工艺,侧部供气采用微机控制,氮氩自动切换;
12)转炉氧枪升降传动采用变频调速;
13)转炉倾动采用变频调速,转炉倾动机构采用四点啮合的全悬挂型式,炉口、炉帽、托圈、耳轴采用水冷,炉腹部分采用风冷;
14)转炉炉前、炉后门及周围挡板采用无水冷型防护结构,节约能源;
15)转炉设钢包在线快速烘烤器,红包出钢。
在线快速烘烤器和其它烘烤器均采用高效蓄热燃烧系统,可节约能源50%;
16)转炉在线连续测温技术。
17)钢包下渣检测及自动关闭钢包滑动水口系统.;
18)炼钢车间配备有光谱分析等快速分析设备,满足电炉炼钢的快节奏和质量控制的要求;
19)炼钢车间将配置三级自动化控制及管理系统,对炼钢生产全过程进行自动监测和控制,实现典型钢种最佳化操作;
20)炼钢车间主要冶炼设备均引进国外先进的技术设备,在保证技术先进性和可靠性前题下,尽量节约基建投资,采用最合理的工艺布置,使炼钢车间在工艺和技术上达到目前世界先进水平。
2.4生产工艺路线及金属平衡
2.4.1生产工艺路线
1)200系列、304、400系列等不锈钢:
43%碳钢废钢+12%不锈钢废钢+45%合金→电炉→AOD转炉→LF钢包精炼炉→连铸机
2)304L、316、316L等不锈钢
43%碳钢废钢+12%不锈钢废钢+45%合金→电炉→AOD转炉→VOD真空处理→LF钢包精炼炉→连铸机
2.4.2金属平衡
金属平衡见图2-1。
铁合金
不锈钢废钢
碳钢废钢
396305
106436
410335
384210
超高功率交流电弧炉
150t×1
264082
12095
711709
20000
AOD转炉
170t×1
139673
3290
3290
LF炉
170t×1
VOD炉
170t×1
738000
82000
板坯连铸机
800000
金属平衡图2-1(单位:
t/年)
2.5炼钢车间原材料、能源介质消耗及质量要求
原材料、能源介质消耗及质量要求见表2-3。
原材料、能源介质消耗及质量要求表2-6
序号
名称
单位
年消耗量
质量要求
备注
一
主要原材料消耗
1
碳钢废钢
万t
40.84
体积密度>0.6t/m3,断面<500x500mm,长度<1000mm,重量<1t,S<0.04%,P<0.04%
2
不锈钢废钢
万t
10.64
体积密度>0.5t/m3,断面<500x500mm,长度<1500mm,重量<1t,S<0.03%,P<0.035%
3
铁合金
万t
41.03
按国家标准供应,粒度30-50mm
4
石灰
万t
83.64
按国家标准供应,粒度30-50mm
5
萤石
万t
0.57
按国家标准供应,粒度30-50mm
6
生白云石
万t
1.07
按国家标准供应,粒度30-50mm
7
碳粉
万t
0.82
成份C<85%,S<1%,灰分<12%,粒度<1.0mm
8
电极
万t
0.28
按国家标准供应
9
线卷
万t
0.13
按国家标准供应
10
料罐及工具
万t
0.16
按国家标准供应
11
保温剂
万t
0.49
按国家标准供应
12
镁砂
万t
9.84
按国家标准供应
13
铬碳砖
万t
6.48
按国家标准供应
14
镁砖
万t
1.64
按国家标准供应
15
高铝砖
万t
9.84
按国家标准供应
16
粘土砖
万t
3.28
按国家标准供应
17
耐火粉
万t
0.82
按国家标准供应
二
主要动力介质消耗
1
电炉冶炼电耗
x106kwh
410
35KV,380V,220V
2
其它电耗
x106kwh
41
35KV,380V,220V
3
氧气
x106Nm3
53.3
压力2.0MPa,纯度99.6%,含水量<0.5kg/min
4
氩气
x106Nm3t
11.48
压力>02.0MPa
5
氮气
x106Nm3
16.4
压力>2.0MPa
6
压缩空气
x106Nm3
29.52
压力0.4-1.0MPa,干燥,无油
7
工业净环水量
x106m3
45.1
压力0.7MPa
8
蒸汽
x106kg
82
压力1.3MPa,温度210℃,蒸汽干度≥97%
9
LPG
x106GJ
0.42
热值≥40128kJ/Nm3
2.6炼钢车间主要冶炼设备性能
2.6.1电炉及其辅助设备技术性能
150t电炉主要技术性能表表2-7
序号
名称
单位
技术参数
1
电炉公称容量
tx座数
150x1
2
电炉型式
AC出钢槽式
3
平均出钢量
t
150
4
最大出钢量
t
160
5
电炉炉壳直径
mm
8000
6
炉门至操作平台高度
mm
700
7
电炉容积
m3
170
8
熔池容积
m3
24
9
熔池深度
mm
950
11
电炉倾动方式
单缸倾动,双缸锁紧
12
电炉倾动角度
度
+40(出钢),-10(出渣)
13
电炉倾动速度
度/s
0.5-3.5
14
炉盖提升旋转型式
液压顶缸式,连身式炉盖,与电极可分开旋转
9
炉盖提升行程
mm
500
10
炉盖提升、下降速度
mm/s
30
11
电极直径
mm
Φ710
12
电极极心圆直径
mm
1350-1500
13
电极提升行程
mm
5300
14
电极提升速度
自动
mm/min
120-250
手动
mm/min
120-300
应急快速提升
mm/min
400
15
炉盖旋转速度
度/s
4
16
炉盖旋转角度
度
72
17
炉盖提升时间
s
12
18
炉盖旋转时间
s
18
19
电炉变压器额定容量
MVA
155
20
变压器一次电压
KV
35
21
变压器二次电压
V
735~1327
22
最大电极电流
kA
78
23
冷却水系统
冷却水总流量
m3/h
1953
冷却水进水压力
MPa
0.6
冷却水进水温度
℃
45
冷却水回水温升
℃
15-32
24
液压系统
电极调节方式
电液调节
循环泵台数
台
2用1备
循环泵额定流量
L/min
220
电极夹持器额定压力
MPa
25
油箱容积
L
5000
25
主要辅助设备配置
炉门氧枪及喷粉系统
自耗式碳氧枪技术参数表表2-8
序号
名称
单位
技术参数
1
旋转、倾动、摆动型式
电动
2
氧枪数量
支
2
3
喷粉枪
支
1
4
氧气流量
Nm3/h
2x3000
5
供氧压力
MPa
1
喷FeSi与喷C枪参数表表2-9
序号
名称
单位
技术参数
1
FeSi与C粉最大颗粒
mm
<3
2
喷FeSi氮气耗量
Nm3/h
900
3
喷C粉压缩空气气耗量
Nm3/h
900
4
储仓个数
个
2
5
储仓容积
m3
25
6
额定喷粉能力
kg/min
150
石灰喷吹系统参数表表2-10
序号
名称
单位
技术参数
1
石灰粉颗粒
mm
3~12
2
石灰堆密度
t/m3
1.0-1.2
3
耗量
kg/t钢水
15
喷罐容积
m3
2.5
4
压缩空气
个
2
压力
MPa
0.6
喷吹耗量
Nm3/h
300-1500
硫化耗量
Nm3/h
100
5
储仓容积
m3
50
6
额定喷粉能力
kg/min
50-252
2.6.2170tAOD炉及其辅助设备技术性能
170tAOD转炉主要技术性能表表2-11
序号
名称
单位
技术参数
1
转炉公称容量
tx座数
170x1
2
最大出钢量
t
180
3
风口数量
个
8
4
风口布置位置
水平布置在炉壁
5
新炉容积
m3
102
6
转炉主要尺寸
转炉高度
mm
9110
炉身直径
mm
6117
炉口直径(耐材内径)
mm
1950
7
转炉倾动速度
rpm
Max.1.2
8
事故驱动
事故驱动方式
气动马达
气源
氮气
压力
MPa
Max.1.8
流量
Nm3/min
30
事故倾动速度
rpm
0.15
倾动180°时蓄能器容积
m3
10
9
旋转接头
驱动侧旋转接头个数x直径
个xmm
1xΦ100
非驱动侧旋转接头个数x直径
个xmm
8xΦ25
压力
MPa
2.5
顶吹氧枪主要技术性能表表2-12
序号
名称
单位
技术参数
1
长度
mm
15000
2
直径
mm
~220
3
喷嘴型式
3孔
4
氧气额定流速
Nm3/min
250
5
氮气、氩气额定流速
Nm3/min
70
6
氧气压力
MPa
1.2
7
冷却水流量
m3/h
100
8
冷却水压力
MPa
0.8
9
氧枪提升行程
mm
11000
10
氧枪最大提升速度
m/min
20
11
氧枪最小提升速度
m/min
5
12
氧枪事故提升
事故驱动方式
气动马达
气源
氮气
压力
MPa
Max.1.8
流量
m/min
5
事故提升速度
rpm
0.15
风口主要技术性能表表2-13
序号
名称
单位
技术参数
1
型式
双管式
2
数量
个
8
3
内径
mm
16
4
总气体流量
Nm3/min
180
5
氮气、氩气额定流速
Nm3/mi