第七章 压缩模与压注模.docx
《第七章 压缩模与压注模.docx》由会员分享,可在线阅读,更多相关《第七章 压缩模与压注模.docx(13页珍藏版)》请在冰豆网上搜索。
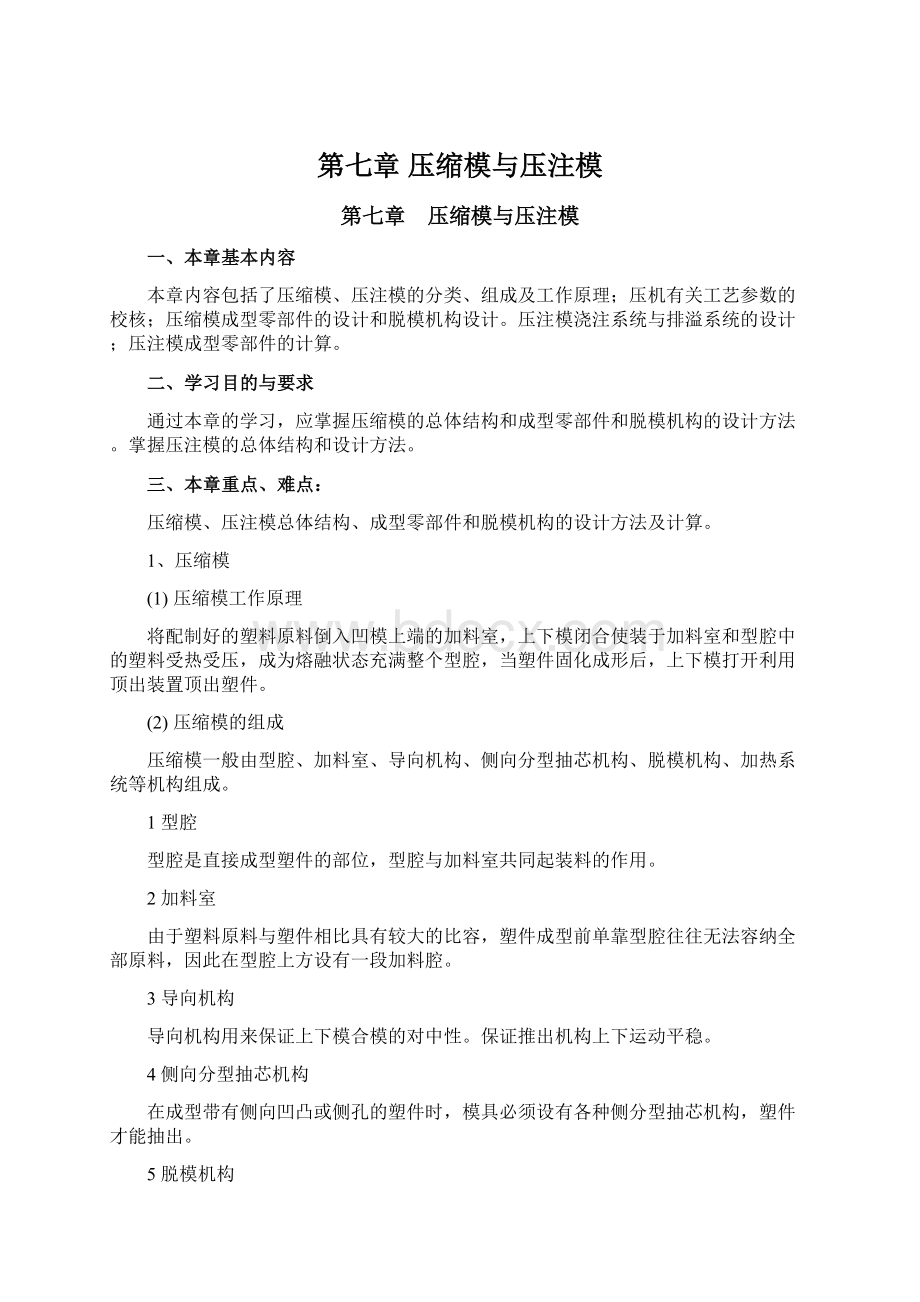
第七章压缩模与压注模
第七章 压缩模与压注模
一、本章基本内容
本章内容包括了压缩模、压注模的分类、组成及工作原理;压机有关工艺参数的校核;压缩模成型零部件的设计和脱模机构设计。
压注模浇注系统与排溢系统的设计;压注模成型零部件的计算。
二、学习目的与要求
通过本章的学习,应掌握压缩模的总体结构和成型零部件和脱模机构的设计方法。
掌握压注模的总体结构和设计方法。
三、本章重点、难点:
压缩模、压注模总体结构、成型零部件和脱模机构的设计方法及计算。
1、压缩模
(1)压缩模工作原理
将配制好的塑料原料倒入凹模上端的加料室,上下模闭合使装于加料室和型腔中的塑料受热受压,成为熔融状态充满整个型腔,当塑件固化成形后,上下模打开利用顶出装置顶出塑件。
(2)压缩模的组成
压缩模一般由型腔、加料室、导向机构、侧向分型抽芯机构、脱模机构、加热系统等机构组成。
1型腔
型腔是直接成型塑件的部位,型腔与加料室共同起装料的作用。
2加料室
由于塑料原料与塑件相比具有较大的比容,塑件成型前单靠型腔往往无法容纳全部原料,因此在型腔上方设有一段加料腔。
3导向机构
导向机构用来保证上下模合模的对中性。
保证推出机构上下运动平稳。
4侧向分型抽芯机构
在成型带有侧向凹凸或侧孔的塑件时,模具必须设有各种侧分型抽芯机构,塑件才能抽出。
5脱模机构
固定式压缩模在模具上必须有脱模机构(推出机构)。
6加热系统
热固性塑料压缩成型需花较高的温度下进行,因此模具必须加热,常见的加热方式有电加热、蒸汽加热、煤气或天然气加热等,但以电加热为普遍。
加热板圆孔中插入电加热棒。
在压缩热塑性塑料时,在型腔周围开设温度控制通道,在塑化和定型阶段,分别通入蒸汽进行加热或通入冷水进行冷却。
(3)压缩模典型结构
分为固定于压机上压板的上模和下压板的下模两大部分。
2、压缩模分类
(1)按固定方式分类
1移动式压缩模
该模具不固定在压机上面,成型后将模具移出压机,先抽出侧型芯,再取出塑件,清理加料室后,将模具重新组合好放入压机内进行下一个循环的压缩成形。
特点是模具结构简单,制造周期短,但加料、开模、取件等工序手工操作,模具易磨损,劳动强度大,模具质量不能太大。
2半固定式压缩模
半固定式压缩模如上图所示。
开合模在机内进行,一般将上模固定在压机上。
下模可沿导轨移动.用定位块定位,合模时靠导向机构定位。
也可按需要采用下模固定的形式,工作时则移出上模.用手工取件或卸模架取件。
该结构便于放嵌件和加料,用于小批量生产,减小劳动强度。
3固定式压缩模
固定式压缩模上下模都固定在压机上,开模、合模、脱模等工序均在压机内进行,生产效率高,操作简单,劳动强度小,开模振动小,模具寿命长。
但其结构复杂,成本高,且安放嵌件不方便。
适用于成形批量较大或形状较大的塑件。
(2)按加料室形式分类
1溢式压缩模
溢式压缩模又称敞开式压缩模,如下图所示。
这种模具无加料室,型腔即可加料,型腔的高度h基本上就是塑件的高度。
型腔闭合面形成水平方向的环形挤压边B,以减薄塑件飞边。
压塑时多余的塑料极易沿着挤压边溢出,使塑料具有水平方向的毛边。
模具的凸模与凹幢无配合部分,完全靠导柱定位,仅在最后闭合后凸模与凹模才完全密合。
压缩时压机的压力不能全部传给塑料。
模具闭合较快,会造成溢料量的增加,既造成原料的浪费,叉降低了塑件密度,强度不高。
溢式模具结构简单,造价低廉、耐用(凸凹模间无摩擦),塑件易取出,通常可用压缩空气吹出塑件。
对加料量的精度要求不高,加料量一般稍大于塑件质量的5%~9%,常用预压型坯进行压缩战形,适用于压缩成形厚度不大、尺寸d、且形状简单的塑件。
2不溢式压缩模
不溢式压缩模又称封闭式压缩模,如上右图所示。
这种模具有加料室,其断面形状与型腔完全相同,加料室是型腔上部的延续。
没有挤压边,但凸模与凹模有高度不大的间隙配合,一般每边间隙值约0.075mm左右,压制时多余的塑料沿着配合间隙溢出,使塑件形成垂直方向的毛边。
模具闭合后,凸模与凹模即形成完全密闭的型腔,压制时压机的压力几乎能完全传给塑料。
不溢式压缩模的特点:
a)塑件承受压力大,故密实性好,强度高。
b)不溢式压缩模由于塑料的溢出量极少.因此加料量的多少直接影响着塑件的高度尺寸,每模加料都必须准确称量,所以塑件高度尺寸不易保证,故流动性好、容易按体积计量的塑料一般不采用不溢式压缩模。
c)凸模与加料室侧壁摩擦,不可避免地会擦伤加料室侧壁,同时,加料室的截面尺寸与型腔截面相同,在顶出时带有伤痕的加料室会损伤塑件外表面。
d)不溢式压缩模必须设置推出装置,否则塑件很难取出。
e)不溢式压缩模一般不应设计成多腔模,因为加料不均衡就会造成各型腔压力不等,而引起一些制件欠压。
不溢式压缩模适用于成形形状复杂、壁薄和深形塑件,也适用于成形流动性特别小、单位比压高和比容大的塑料。
例如用它成形棉布、玻璃布或长纤维填充的塑料制件效果好,这不单目为这些塑料流动性差,要求单位压力高,而且若采用溢式压缩模成形,当布片或纤维填料进入挤压面时,不易被模具夹断而妨碍模具闭合.造成飞边增厚和塑件尺寸不准.去除困难。
而不溢式压缩模没有挤压面,所得的飞边不但极薄,而且飞边在塑件上呈垂直分布,去除比较容易,可以用平磨等方法去除。
3半溢式压缩模
又称为半封闭式压缩模,如图7.6所示。
这种模具具有加料室.但其断面尺寸大于型腔尺寸。
凸模与加料室呈间隙配合.加料室与型腔的分界处有一环形挤压面.其宽度约4—5mm。
挤压边可限制凸模的下压行程,井保证塑件的水平方向毛边很薄。
半溢式压缩模的特点:
a)模具使用寿命较长。
因加料室的断面尺寸比型腔大,故在顶出时塑件表面不受损伤.
b)塑料的加料量不必严格控制,因为多余的塑料可通过配合间隙或在凸模上开设的溢料槽排出。
c)塑件的密度和强度较高,塑件径向尺寸和高度尺寸的精度也容易保证
d)简化加工工艺。
当塑件外形复杂时,若用不溢式压塑模必造成凸模与加料室的制造困难.而采用半溢式压塑模则可将凸模与加料室周边配合而简化。
e)半溢式压缩模由于有挤压边缘,在操作时要随时注意清除落在挤压边缘上的废料,以免此处过早地损坏和破裂。
由于半溢式压缩模兼有溢式压缩模和不溢式压缩模的特点,因而被广泛用来成形流动性较好的塑料及形状比较复杂、带有小型嵌件的塑件,且各种压制场合均适用。
3、压注模
(1)压注模工作原理
压注成型的一般过程是,先闭合模具,然后将塑料加入模具加料室内,使其受热成熔融状态,在与加料室配合的压料柱塞的作用下,使熔料通过设在加料室底部的浇注系统高速挤入型腔。
塑料在型腔内继续受热受压而发生交联反应并固化成型。
然后打开模具取出塑件,清理加料室和浇注系统后进行下一次成型。
压注成型和压缩成型都是热固性塑料常用的成型方法。
压注模与压缩模的最大区别在于前者设有单独的加料室。
(2)压注模的组成
压注模由以下几部分组成:
1型腔
成型塑件的部分,由凸模、凹模、型芯等组成,分型面的形式及选择与注射模、压缩模相似。
2加料室
由加料室和压柱组成,移动式压注模的加料室和模具本体是可分离的,开模前先取下加料室,然后开模取出塑件。
固定式压注模的加料室是在上模部分,加料时可以与压柱部分定距分型。
3浇注系统
多型腔压注模的浇注系统与注射模相似,同样分为主流道、分流道和浇口,单型腔压注模一般只有主流道。
与注射模不同的是加料室底部可开设几个流道同时进入型腔。
4导向机构
一般由导柱和导柱孔(或导套)组成。
在柱塞和加料室之间,型腔分型面之间,都应设导向机构。
5侧向分型抽芯机构
压注模的侧向分型抽芯机构与压缩模和注射模基本相同。
6脱模机构
由推杆、推板、复位杆等组成,由拉钩、定距导柱、可调拉杆等组成的两次分型机构是为了加料室分型面和塑件分型面先后打开而设计的,也包括在脱模机构之内。
7加热系统
固定式压注模由压柱、上模、下模三部分组成,应分别对这三部分加热,在加料室和型腔周围分别钻有加热孔,插入电加热元件。
移动式压注模加热是利用装于压机上的上、下加热板,压注前柱塞、加料室和压注模都应放在加热板上进行加热。
(3)压注模典型结构
压注模由压柱、上模、下模三部分组成,打开上分型面A-A取出主流道凝料并清理加料室,打开下分型面B-B取出塑件和分流道凝料。
4、压注模的分类
(1)按固定方式分类
1移动式压注模
2固定式压注模
(2)按加料室形式分类
1罐式压注模
移动式罐式
移动式罐式压注模的加料室与模具本体是可以分离的。
模具闭合后放上加料室,将定量的塑料加入加料室内,利用压机的压力,通过压柱将塑化的物料高速挤入型腔,硬化定型后,开模时先从模具上取下加料室,再分别进行清理和脱出塑件,用手工或专用工具。
固定式罐式
2柱塞式压注模
柱塞式压注模没有主流道.主流道已扩大成为圆柱形的加料室,这时柱塞将物料压入型腔的力已起不到锁模的作用.因此柱塞式压注模应安装在特殊的专用压机上使用,锁模和成形需要两个液压缸来完成。
可分为下面两种形式的压注模。
上加料室柱塞式压注模
上加料室柱塞式压注模所用压机其合模液压缸(称主液压缸)在压机的下方.自下而上合模;戚形用液压缸(称辅助液压缸)在压机的上方,白上而下将物料挤人模腔。
合模加料后,当加入加料室内的塑料受热成熔融状时.压机辅助液压缸工作.柱塞将熔融物料挤人型腔,固化成形后,辅助液压缸带动柱塞上移,主液压缸带动工作台将模具下模部分下移开模,塑件与浇注系统留在下模。
顶出机构工作时,推杆将塑件从型腔中推出。
下加料室柱塞式压注模
这种模具所用压机合模液压缸(称主液压缸)在压机的上方,自上而下合模;成形用液压缸(称辅助液压缸)在压机的下方,自下而上将物料挤入模腔。
它与上加料室柱塞式压注模的主要区别在于:
它是先加料,后合模,最后压注;而上加料室柱塞式压注模是先合模,后加料.最后压注。
5、压注模成形零件设计
压注模的结构包括型腔、加料室、浇注系统、导向机构、侧抽芯机构、推出机构、加热系统等七部分,压注模的结构设计原则与注射模、压缩模基本相似。
压注模零部件的设计也与注射模、压缩模基本相似,本节只介绍压注模特有的结构零件的设计。
(1)加料室结构设计
压注模与注射模不同之处在于它有加料室。
压注成形之前塑料必须加入到加料室内,进行预热、加压。
才能压柱成形。
由于压注模的结构不同,所以加料室的形式也不相同。
固定式压注模和移动式压注模的加料室具有不同的形式,罐式和柱塞式的加料室也具有不同的形式。
加料室断面形状常见的有圆形和矩形,应由制品断面形状决定,例如圆形塑件采用圆形断面加料室。
多腔模具的加料室断面。
一般应尽可能盖住所有模具的型腔,因而常采用矩形断面。
1固定式压注模加料室
固定式压注模的加料室与上模连成一体,在加料室底部开设一个或数个流道通向型腔。
当加料室和上模分别加工在两块板上时可在通向型腔的流道内加一主流道衬套。
2移动式压注模加料室
移动式压注模加料室可单独取下.并有一定的通用性,加料室底部为一带有40—45度角的台阶,其作用在于当压柱向加料室内的塑料加压时,压力也作用在台阶上,从而将加料室紧紧地压在模具的模板上,以免塑料从加料室的底部溢出。
3柱塞式压注模加料室
柱塞式压注模加料室截面均为圆形,由于采用专用液压机,液压机上有锁模液压缸,所以加料室的截面尺寸与锁模无关,尺寸较小,高度较大。
(2)加料室尺寸计算
1罐式压注模加料室截面积
可从传热和锁模两个方面考虑。
从传热方面考虑。
加料室的加热面积取决于加料量,根据经验,未经预热的热固性塑料每克约l.4cm2的加热面积,加料室总表面积为加料室内腔投影面积的两倍与加料室装料部分侧壁面积之和。
为了简便起见,可将侧壁面积略去不计,因此,加料室截面积为所需加热面积的一半.
从锁模方面考虑。
加料室截面积应大于型腔和浇注系统在合模方向投影面积之和,否则型腔内塑料熔体的压力将顶开分型面而溢料。
根据经验,加料室截面积必须比塑件型腔与浇注系统投影面积之和大10%-25%.
2柱塞式压注模加料室截面积
其中
——压机辅助缸的额定压力;
——不同塑料所需单位挤压力;
(3)压柱结构
1罐式压注模的压柱
图7.15所示为罐式压注模几种常见的压柱结构。
图7.15a为简单的圆柱形,加工简便省料,常用于移动式压注模;
图7.15b为带凸缘的结构,承压面积大,压注平稳,移动式和固定式罐式压注模都能应用;
图7.15e为组合式结构,用于固定式模具,以便固定在压机上;
图7.15d在压柱上开环形槽,在压注时,环形槽被溢出的塑料充满并固化在其中,继续使用时起到了活塞环的作用,可以阻止塑料从间隙中溢出。
2柱塞式压注模的压柱
图7.16所示为柱塞式压注模的压柱结构。
图7.16a中,其一端带有螺纹.直接拧在液压缸的活塞杆上,图7.16b中,在柱塞上加工出环形槽以便溢出的料固化其中,起活塞环的作用。
6、浇注系统设计
(1)主流道
在压注模叶J,常见的主流道有正圆锥形的、带分流锥的、倒圆锥形的等,图7.20a所示为正圆锥形主流道,其大端与分流道相连,常用于多型腔模具,有时也设计成直接浇口的形式,用于流动性较差的塑料的单型腔模具。
主流道有6~lO度的锥度,与分流道的连接处应有半径为3mm以上的圆弧过渡。
图7.20b所示为带分流锥的主流道,它用于塑件较大或型腔距模具中心较远时以缩短浇注系统长度,减少流动阻力及节约原料的场合.分流锥的形状及尺寸按塑件尺寸及型腔分布而定。
型腔沿圆周分布时,分流锥可采用圆锥形;当型腔两排并列时,分流锥可做成矩形截面的锥形。
分流锥与流道间隙一般取l~l.5mm流道可以沿分流锥整个表面分布,也可在分流锥上开槽。
图7.20c所示为倒锥形主流道。
这种主流道大多用于固定式罐式压注模,与端面带楔形槽的压柱配合使用。
开模时,主流道连同加料室中的残余废料由压柱带出再予清理。
这种流道可用于多型腔模具,又可使其直接与塑件相连用于单型腔模具或同一塑件有几个浇口的模具:
这种主流道尤其适用于以碎布、长纤维等为填料时塑件的成形。
(2)分流道
分流道为了达到较好的传热效果,分流道(分浇道)一股都比较浅而宽,但若过浅,会使塑料受热而早期硬化,降低其流动性。
一般小型件分流道深度取2~4mm,大型件深度取4~6mm,最浅应不小于2mm。
最常采用梯形断面的分流道,其尺寸如图7.2l所示,梯形每边应有5~15度的斜角;也有半圆形分流道的。
其半径可取3~4mm。
以上两种截面加工容易、受热面积大,但隅角部容易过早交联固化。
圆形截面的分流道为最合理的截面,流动阻力小,但加工有些麻烦。
(3)浇口
浇口是浇注系统中的重要组成部分,它与型腔直接相连,其位置形状及尺寸大小直接影响熔料的流速及流态,对塑件质量、外观及浇注系统的去除都有直接影响,因此,浇口设计应根据塑料特性、塑件形状及要求和模具结构等因素来考虑。
1浇口的形式
压注模的浇口与注射模基本相同,可以参照注射模的浇口进行设计。
由于热固性塑料的流动性较差,所以设计压注模浇口时,其浇口应取较大的截面尺寸。
常见的压注模的浇口形式有圆形点浇口、侧浇口、扇形浇口、环形浇口以及轮辐式浇口等。
如图7.22所示,图7.22a、b、c、d为侧浇口,图7.22e为扇形浇口,网7.22f、g为环形浇口。
截面形状有圆形、半圆形、梯形三种形式。
图7.22a为外侧进料的侧浇口,是侧浇口中最常用的形式;
图7.22b所示的塑件外表面不允许有浇口痕迹。
所以用端面进料;
图7.22c所示的结构可保证浇口折断后,断痕不会伸出表面,不影响装配,可降低修浇口的费用;
如果塑件用碎布或长纤维做填料,侧浇口应设在附加于侧壁的凸台上.这样在去除浇口时就不会损坏塑件如图7.22d所示;对于宽度较大的塑件可用扇形浇口,如图7.22e所示。
2浇口位置选择
压注模浇口位置和数量的选择应遵循以下原则:
a)由于热固性塑料流动性较差,故浇口开设位置应有利于流动,一般浇口开设在塑件壁厚最大处,以减少流动阻力,并有助于补缩。
b)浇口的开设位置应避开塑件的重要表面,以不影响塑件的使用、外观及后加工工作量,同时应使塑料在型腔内顺序填充.否则会卷人空气形成塑件缺陷。
c)热固性塑料在型腔内的最大流动距离应尽可能限制在100mm内,对大型塑件应多开设几个浇口,减少流动距离。
d)热固性塑料在流动中会产生填料定向作用,造成塑件变形、翘曲甚至开裂,应注意浇口位置。
(4)溢料槽和排气槽
1溢料槽
成形时为防止产生熔接痕或使多余料溢出,以避免嵌件及模具配合中渗入更多塑料,有时需要在产生熔接痕的地方及其他位置开设溢料槽。
溢料槽尺寸应适当,过大则溢料多,使塑件组织疏松或缺料,过小时溢料不足,最适宜的时机应为塑料经保压一段时间后才开始将料溢出,一般溢料槽宽取3~4mm.深0.1~O.2mm,制作时宜先取薄,经试模后再修正。
2排气槽
压注成形时,由于在极短时间内需将型腔充满,不但需将型腔内气体迅速排出模外,而且需要排除由于聚合作用产生的一部分低分子(气体),因此,不能仅依靠分型面和推杆的间隙排气,还需开设排气槽。
压注成形时从排气槽中不仅逸出气体,还可能溢出少量前锋冷料,因此需要附加工序去除,但这样有利于提高排气槽附近熔接痕的强度。
排气槽的截面形状一般为矩形或梯形。
对于中小型塑件,分型面上排气槽的尺寸为深度取0.04~O.13mm,宽度取32~64mm,视塑件体积和排气槽数量而定。