RPS定位系统要点.docx
《RPS定位系统要点.docx》由会员分享,可在线阅读,更多相关《RPS定位系统要点.docx(22页珍藏版)》请在冰豆网上搜索。
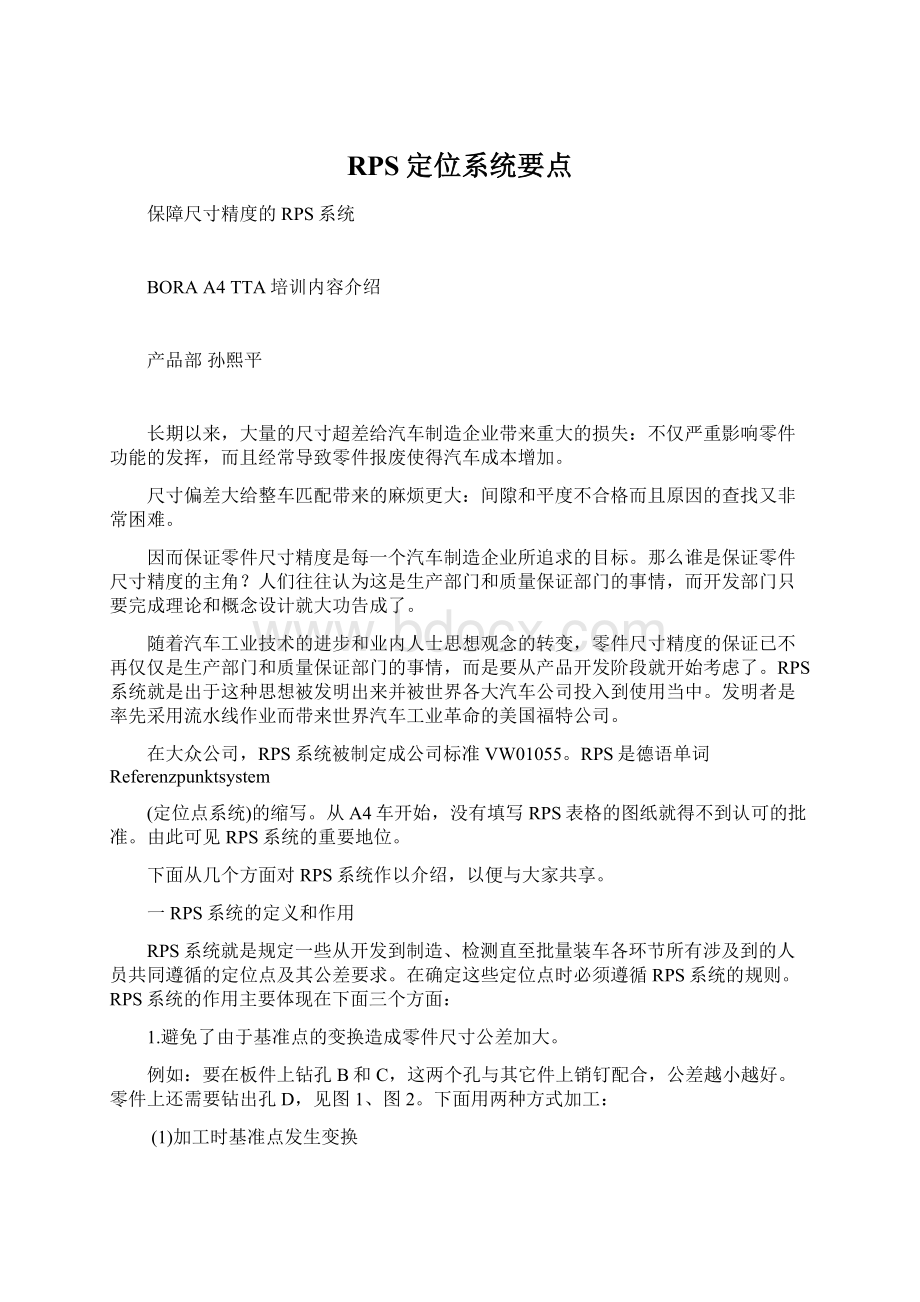
RPS定位系统要点
保障尺寸精度的RPS系统
BORAA4TTA培训内容介绍
产品部孙熙平
长期以来,大量的尺寸超差给汽车制造企业带来重大的损失:
不仅严重影响零件功能的发挥,而且经常导致零件报废使得汽车成本增加。
尺寸偏差大给整车匹配带来的麻烦更大:
间隙和平度不合格而且原因的查找又非常困难。
因而保证零件尺寸精度是每一个汽车制造企业所追求的目标。
那么谁是保证零件尺寸精度的主角?
人们往往认为这是生产部门和质量保证部门的事情,而开发部门只要完成理论和概念设计就大功告成了。
随着汽车工业技术的进步和业内人士思想观念的转变,零件尺寸精度的保证已不再仅仅是生产部门和质量保证部门的事情,而是要从产品开发阶段就开始考虑了。
RPS系统就是出于这种思想被发明出来并被世界各大汽车公司投入到使用当中。
发明者是率先采用流水线作业而带来世界汽车工业革命的美国福特公司。
在大众公司,RPS系统被制定成公司标准VW01055。
RPS是德语单词Referenzpunktsystem
(定位点系统)的缩写。
从A4车开始,没有填写RPS表格的图纸就得不到认可的批准。
由此可见RPS系统的重要地位。
下面从几个方面对RPS系统作以介绍,以便与大家共享。
一RPS系统的定义和作用
RPS系统就是规定一些从开发到制造、检测直至批量装车各环节所有涉及到的人员共同遵循的定位点及其公差要求。
在确定这些定位点时必须遵循RPS系统的规则。
RPS系统的作用主要体现在下面三个方面:
1.避免了由于基准点的变换造成零件尺寸公差加大。
例如:
要在板件上钻孔B和C,这两个孔与其它件上销钉配合,公差越小越好。
零件上还需要钻出孔D,见图1、图2。
下面用两种方式加工:
(1)加工时基准点发生变换
步骤1用孔A定位钻出孔B和孔D
公差A…B=+/-0.1
A…D=+/-0.1
步骤2用孔D定位钻孔C(这时基准由孔A变为孔D)
公差D…C=+/-0.1
孔B、孔C距离公差结果
A…B=+/-0.1
A…D=+/-0.1
D…C=+/-0.1
B…C=+/-0.3
(2)加工时基准不变化
步骤1用孔A定位钻出孔B
和孔D
公差A…B=+/-0.1
图1加工时基准点发生变换
A…D=+/-0.1
步骤2板件仍以孔A定位钻孔C
(基准没有变化)
公差A…C=+/-0.1
孔B、孔C距离公差结果
A…B=+/-0.1
A…C=+/-0.1
B…C=+/-0.2
图2加工时基准不变化
比较两种情况可以看出,加工孔C时
基准不变比基准变换造成的公差减小了+/-0.1mm
上面例子给我们的提示是:
为避免基准变换,必须事先规定好在制造和测量过程中的基准点。
不允许各部门自作主张随意找基准点进行工作。
2.避免了模板的使用。
模板的使用有很大的局限性,并且增加了加工时间。
规定工装用RPS点调准,那么加工就变成是直接的了,模板不再作为辅助定位工具,参见图3。
用RPS点作定位点
图3加工时不用模板
3.RPS点是模具、工装、检具的定位点。
为了实现统一的定位技术规则,必须保证
∙模具
∙工装
∙检测工具
都按照RPS点来制造。
这一点是RPS系统最重要的作用。
二RPS系统的五大规则
为了使RPS系统在实际当中发挥作用,必须遵守下面五条规则:
∙3-2-1规则
∙坐标平行规则
∙统一性规则
∙尺寸标注规则
∙RPS尺寸图
1.3-2-1规则
一个刚体的平行移动和转动共有6个自由度。
限制其6个自由度,刚体才能保持平衡。
按照3-2-1规则,保持刚体平衡状态需要6个定位点,如图4所示:
图4刚体的6个自由度
3个旋转自由度
其中3个定位点在Z方向
2个定位点在Y方向
1个定位点在X方向
3-2-1规则由此得来。
这些点就是
RPS系统的定位点,称为RPS点。
对于没有孔的零件,6个RPS点是
3个平移自由度
必须的。
而有孔的零件往往将孔设定
为RPS点。
一个圆孔可以限定2个自由
度,如图5所示。
图中给出的RPS点限
定了3个自由度,因此本例子中只有
定位点
4个RPS点。
这个圆孔限定了X,Y方向的平移
这个平面作为Z方向的1个定位点,和孔定义为一个RPS点
图5带孔零件RPS点限定的自由度
这个平面作为Z方向的1个定位点,和孔被定义为一个RPS点
大众公司标准VW01055对RPS点的标注给出了规定,见图6。
孔定位点标记字母
带有序号的RPS点名称
孔限位方向
平面定位点标记字母
平面定位方向
图6RPS点的标注
对定位方式标记字母的含义说明如下:
H,h=孔/销定位
F,f=平面/棱边/球面/顶点定位
T,t=理论点
大写字母表示主RPS点的定位方式,小写字母表示附加定位点的定位方式。
小写字母x,y,z表示RPS点的限位方向。
但是对于大的刚度不足的零件,在保障了3-2-1规则的前提下,还需要
附加的定位点来保证零件的平衡状态,如图7所示。
图7大的刚度不足零件需要附加定位点
图中RPS5fz是附加定位点,它的命名与主RPS点相似,但定位方式用小写
字母表示。
3-2-1规则适用于任何形状的零件。
但是任何规则都有例外,下面三种情
况与3-2-1规则相悖:
例1:
球体只需要3个定位点即达到平衡,如图8所示。
例2:
旋转体需要5个定位点即达到平衡,如图9所示。
例3:
铰接零件平衡需要的定位点多于6个,必须有附加的定位才能达到平衡
状态,如图10所示。
图8球体只需要3个定位点
图10铰接零件需要的定位点多于6个
图9旋转体需要5个定位点
图10铰接零件需要的定位点多于6个
2.坐标平行规则
在测量和加工时,零件的放置必须保证能够获得精确的结果。
下面通过
两种定位系统的对比来分析坐标平行规则的重要性。
图11所示为两种定位系统。
图11两种定位系统
定位系统2
图11两种定位系统
将合格的零件放到两种定位系统中,似乎看不出有什么不同,见图12:
图12将合格的零件放到两种定位系统中
定位系统2
定位系统1
当零件出现了制造公差,如图13所示,2个零件在X方向存在偏差--它们比合格零件做短了。
图13零件在X方向存在偏差
图13零件在X方向存在偏差
将这两个零件分别放到两个定位系统中进行测量,如图14所示:
图14将X方向存在偏差的零件放到两个定位系统中测量
可以看出倾斜放置导致测量结果不正确。
这里出现了Z方向的测量偏差。
其实零件在Z方向是正确的。
同时还可以看出测量得到的X方向的偏差也是不
正确的。
倾斜放置造成的测量结果会导致这样一些严重后果:
∙尺寸合格的零件会被错误地当成废品
∙模具根据错误的测量结果在X,Z方向上进行修改,其实Z方向并没有错误
∙工装被不正确地调整了
∙通过上述做法导致后来生产的产品都是废品
因此下面结论的正确性是不言而喻的:
为了获得准确的结果,定位点应当是平行于坐标轴的。
这里所说平行于坐标轴是指定位平面与坐标系的坐标轴平行。
这些定位点通常被定义为RPS点。
不过在有些零件上是找不到与坐标轴平行的平面做RPS点的,如图15,
这时在不影响功能的基础上应当设计出平行于坐标轴的平面作为RPS点,
如图16所示。
图15零件上没有与Z轴平行的平面做定位点
在零件上压出与坐标轴平行的平面
图16压出与坐标轴平行的平面
3.统一性规则
RPS系统的主旨是通过避免基准转变来保证制造工艺过程的可靠性和可
重复利用的精确性。
RPS系统的统一性规则要求从产品开发阶段直到批量生产,RPS点的使用
贯彻始终。
当然不是所有的RPS点都一直使用下去,那样的话在总成零件上
就会有许多点是重复的。
下面从纵梁到地板总成的焊接流程来看RPS点按统一性原则的运用。
图17是总成焊接前各零件RPS点的分布情况。
图17焊接前RPS点分布情况
图18是第一道焊接工序后RPS点重新确定的情况。
可以看到地板总成上有3
个RPS点是沿用合成前零件上已有的:
总成上的RPS1点是单件左纵梁上的RPS1点,总
成上的RPS3点是单件前地板上的RPS3点,总成上的RPS4点是单件右纵梁上的RPS点。
图中各RPS点是完全遵循地板总成的功能要求确定下来的:
地板有固定前端
图18第一到焊接工序后RPS点重新确定的情况
框架、座椅、踏板、后轴、付车架以及与侧围连接的功能。
图18第一道焊接工序后RPS点重新确定的情况
图19是地板总成焊接完成后RPS点再一次重新确定的情况。
可以看到总成上的RPS1、
RPS2、RPS3、RPS4以及附加RPS点RPS7、RPS8都是从前一步延续使用的,只不过是重新排序。
图19地板总成焊接完成后RPS点再一次确定的情况
RPS系统的统一性规则还要求所有工艺流程中的输送装置原则上都要使用
RPS点作为支点,如图20所示。
图20输送装置使用RPS点作为支点
4.尺寸标注规则
在图纸中尺寸一般是从整车坐标线引出和标注的,往往不标注实际尺寸。
这种标注方式会造成推算尺寸公差的增大,如图21所示。
在零件图纸中画出整车坐标是有意义的--这可以确定零件在整车中的位置,这是零件设计过程中重要的基础。
可是对于零件的制造和测量,采用整车坐标会带来很多困难。
RPS系统要求建立起零件自身的坐标系--零件坐标系,并以此作为基础。
零件坐标系是以整车坐标系为基础建立起来的,有下面两种建立方式:
∙通过在整车坐标系中平移建立,这是通常的情况
∙通过在整车坐标系中旋转建立,这是特殊的情况
图22描述了通过在整车坐标系中平移建立零件坐标系的情形。
图21从整车坐标线引出尺寸线
尺寸AB的公差是+/-0.4,
因为点A和点B从坐标线引出的尺
寸都有+/-0.2的公差
图22在整车坐标系中平移建立零件坐标系
图23则描述了通过在整车坐标系中旋转建立零件坐标系的情况。
基准点
图23通过在整车坐标系旋转建立零件坐标系
(1)通过平移建立零件坐标系的尺寸标注规则
按照零件特性选择三个与整车坐标轴平行的平面并求其交点,
这个交点定义为RPS系统的基准点。
基准点相对于整车坐标没有公差,
零件尺寸以基准点为起点标注。
尺寸标注必须符合零件功能
要求,对于重要尺寸要给出直接
尺寸。
例如安装在翼子板上的
转向灯罩的装配要求准确的孔
距,如图24,不仅尺寸要准确,
尺寸公差也要满足功能的要求。
两个固定孔在翼子板上的位置
并不很重要(转向灯在翼子板
上位置公差在1mm时是不易被察
觉的),因此它们的位置公差
可以较大而对功能没有影响。
图24翼子板上转向灯固定孔尺寸标注
在零件坐标系中一个点相对于基准点的距离称为名义尺寸。
名义尺寸可以通过减法算出绝对值。
例如:
基准点在整车坐标系中的坐标为X=400Y=-65Z=100
定位点RPS3Fz整车坐标为X=550Y=-95Z=100
如图25所示
零件坐标系
移动
基准点
整车坐标系
起点
图25名义尺寸举例
那么RPS3Fz的名义尺寸计算结果如下:
基准点坐标RPS3点坐标名义尺寸
X=400-550=150
Y=-65--95=30
Z=100-100=0
因为名义尺寸是绝对值,所以都是正值。
在大众公司产品图中,在确定为RPS点的部位画出网格框并引出箭头线标出名称,如图26所示,同时在图中列出RPS表格。
RPS表格已被规定为图纸内容的重要组成部分。
RPS表格的形式及各栏目意义如表一所示。
(2)通过旋转建立的零件坐标系规则
有些零件按照平移建立零件坐标系是不合理的,而必须进行一次或多次的旋转才与其拔模方向相一致,如图23所示。
对于旋转建立的零件坐标系,在RPS表格中需要填入旋转角,如表二所示。
在图纸中RPS点的定位方向用a,b,c值来表示,如图26所示。
其中:
RPS1HabFc(主定位点)
…
RPS7fc(附加支撑点)
对于多次旋转的情况,应在图中说明旋转角度和旋转顺序。
在RPS表格
旋转栏中注明“见图纸”字样。
图26旋转建立零件坐标系图纸标注的例子
对表格做以下几点说明:
a.在公差栏内可以看到,零件基准点的公差设置为0。
各主RPS点在限位方向上的公差也设置为0。
但对于附加支撑点的限位方向允许有公差。
b.第一个RPS点占两行位置,是因为这一点是由孔和面复合而成,在这里孔、面分开填写。
c.在公差栏内第一行Y向公差格中填入小横线,这是为了避免因空格而被视为未注公差。
d.最后两行中,a1是定义出的功能点。
a-b为2个功能点之间的距离,对于功能点要给出形位公差,理论尺寸要加上方框。
说明:
绕X,Y,Z轴的转角用正值(逆时针方向)或负值(顺时针方向)填入表中
5RPS尺寸图
RPS尺寸图是在图纸完成之前的一种工作用图,供同步工程小组确定RPS点填写和讨论使用,并作为开发工作的指导性文件。
RPS尺寸图有固定的格式,见图27。
图27RPS尺寸图
三RPS系统制定过程
在组织机构方面,RPS系统是由同步工程小组确定的。
同步工程小组由下面各部门的专业人员组成:
∙开发部门
∙质量保证部门
∙生产部门
∙规划部门
∙协作厂家
早在产品开发阶段,各部门的专业人员就在同步工程小组内在达成共识的前提下确定零件的RPS系统。
这是因为在后续制造中如果再进行产品更改,就会造成更高费用的发生。
统一的RPS系统使用规则可以使查找错误、分析错误变得即快捷又清晰。
另外,依据RPS系统方法制定出目标清晰的措施能够有效地控制住高费用的更改过程。
RPS系统制定过程可以分为下面六个步骤:
1功能研究
2公差研究
3RPS系统确定
4尺寸图确定
5公差计算
6产品图纸
以付司机气囊为例将各阶段说明如下。
1功能研究阶段
首先研究零件与周围各零件的关系,在此基础上进一步研究零件的功
能。
在研究零件功能时,要按照重要程度把各功能排序。
例如付司机气囊
盖板(见图28)的功能按重要程度做如下排序:
间隙和平度
气囊单元释放
螺栓紧固方式
将间隙和平度放在第一位,是因为对于用户来说第一感觉是外观形象。
这种排序思想并不是没有道理的。
X,Y,Z向存在公差
气囊盖板在仪表板切口上的机构元件
中出风口的机构元件
图28付司机气囊盖板功能研究
2公差研究阶段
在这一阶段要考虑的问题是,公差会造成哪些对功能不利的影响?
在上面的例子中,公差会造成盖板四周边缘与仪表板开口匹配不好。
3RPS系统确定阶段
RPS系统的确定必须符合零件功能重要性的排序结果和公差目标。
在本例中将间隙和平度排在气囊盖板功能重要性的第一位,那么很自然地将RPS点定义在外表面上,如图29所示。
4尺寸图确定阶段
由同步工程小组确定的RPS点需要填入RPS尺寸图中。
它是同步工程小组工作用图,在产品图纸完成之前它是有约束力的指导性文件。
5公差计算阶段
在做公差计算时,应当充分利用RPS系统原理来保障设计意图的实现。
公差计算要回答下面两个问题:
--总的公差达到多少?
--它能够保障零件的功能吗?
另外,公差计算应当包含算术值和统计值两种结果。
6产品图纸阶段
在此阶段,将RPS尺寸图进一步扩充内容--把RPS点的名义尺寸和公差填加进
去。
只有在确定出RPS点之后,才能给出图纸的认可。
至此,RPS系统的制定过程全部结束。
图29RPS点定义在外表面上
结束语
RPS系统对于我公司还是一个很新的技术,尽管从AudiA6开始大家已经接触到并且也有了一定的应用。
但是进一步提高对它的重视程度,进一步利用这门新技术提高我们的产品质量,特别是能否将这一技术引入到我公司自主开发的产品上来,是值得大家思考的课题。
2001-4-12