焊接缺陷及检测方法.docx
《焊接缺陷及检测方法.docx》由会员分享,可在线阅读,更多相关《焊接缺陷及检测方法.docx(29页珍藏版)》请在冰豆网上搜索。
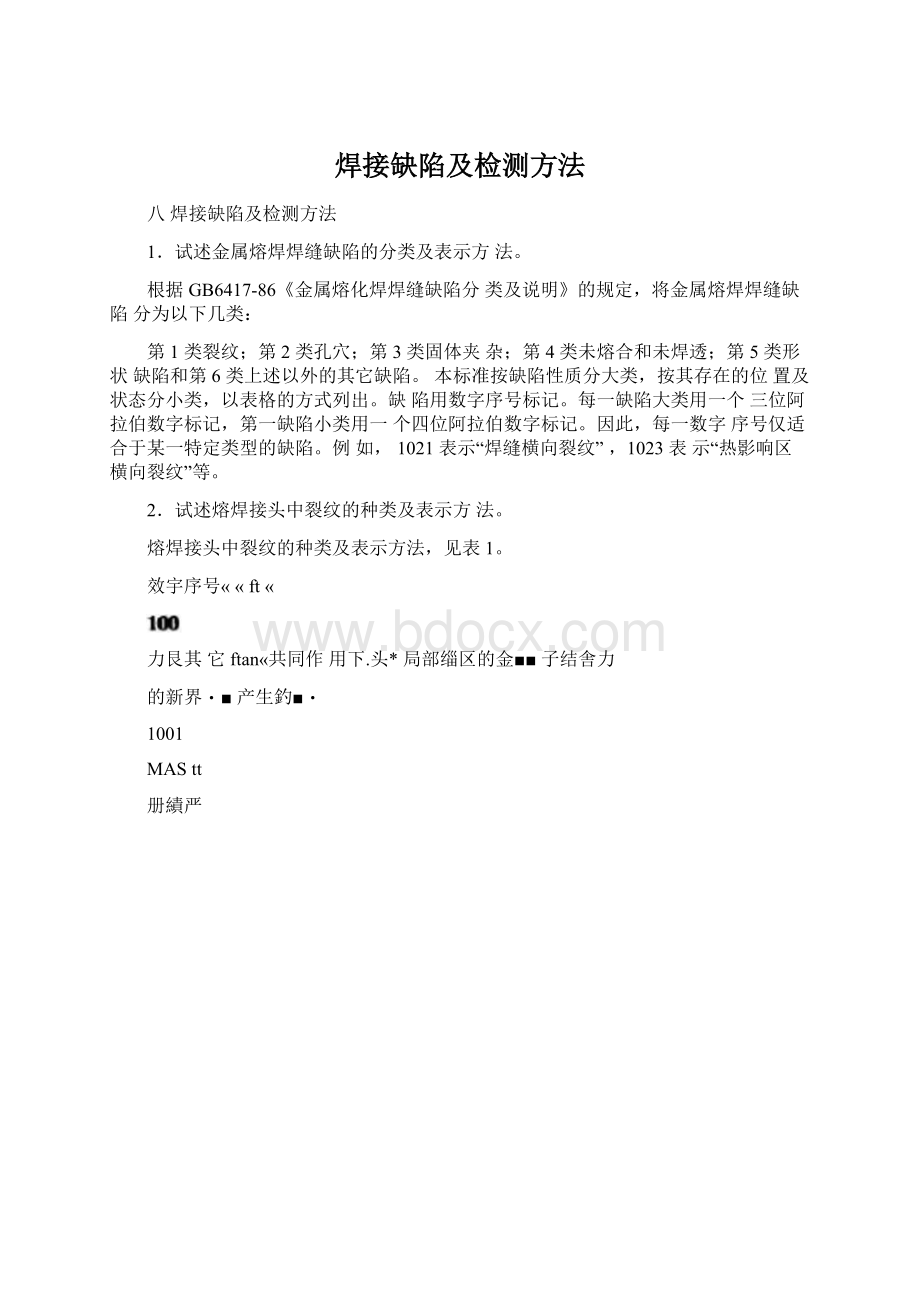
焊接缺陷及检测方法
八焊接缺陷及检测方法
1.试述金属熔焊焊缝缺陷的分类及表示方法。
根据GB6417-86《金属熔化焊焊缝缺陷分类及说明》的规定,将金属熔焊焊缝缺陷分为以下几类:
第1类裂纹;第2类孔穴;第3类固体夹杂;第4类未熔合和未焊透;第5类形状缺陷和第6类上述以外的其它缺陷。
本标准按缺陷性质分大类,按其存在的位置及状态分小类,以表格的方式列出。
缺陷用数字序号标记。
每一缺陷大类用一个三位阿拉伯数字标记,第一缺陷小类用一个四位阿拉伯数字标记。
因此,每一数字序号仅适合于某一特定类型的缺陷。
例如,1021表示“焊缝横向裂纹”,1023表示“热影响区横向裂纹”等。
2.试述熔焊接头中裂纹的种类及表示方法。
熔焊接头中裂纹的种类及表示方法,见表1。
效宇序号««ft«
力艮其它ftan«共同作用下.头*局部缁区的金■■子结舎力
的新界・■产生釣■・
1001
MAStt
册績严
1031
1033
1034
專本上崎好筑铀
找平行的裂纹•可
—炸篇金H中—令仪匕—老中
——金■中
的裂纹.巧
健位升
—堤金嵐中
—■响X中一材金属中
IWiM-公共点的敏射状辍纹•可IffitftT:
—鏗昱金M中
—佛形晌IK中―材金■中
104
1045
1046
tt
在炸t|牧1■坑处的製纹.町鹿址:
—纵向的—*向的
—星花的
Q》“m
1045
ST
'IH46('1047>
105
1051
1053
1054
岡IK製
・rnfHVi的製仪・
町儷位P:
—■金■中
―够中
——中
106
枝状裂
III墓一公共税仪
仪
淤生的一Wtt.它与的•&牧前(105)和放射状《(tt(103)不PJ.BT繼位头
1061
—催金II中
1063
——屯响区中
1064
材金JB中
1047
3.试述熔焊接头中孔穴的种类及表示方法。
熔焊接头中孔穴的种类及表示方法,见表
2。
«2孔穴的种类及隶示方法
数宇序号
名称
说明
简K
200
孔穴
201
熔池中的代池衽豪囲时,未能遑岀而残宙下来所形攻的孔穴
2011
孔
近似球形的空穴
%
2012
均布代孔
大it代孔比佼沟匀堆分布在鑒个焊■金J■中,不晏与寄状气扎(2014)
2013
集代孔
代孔*
^7^2013
2014
链状气扎
•与炸■输线平行的成申代孔
2014
2014
2015
孔
长度方向与禅S!
输找近個平行的非M形的长代孔
2016
虫膨代孔
由于代几在卿4金层中上浮而引起的管状扎穴•其位■和死状殛由豪固的形式和气孔的来操决定的.
它釘成屏堆出现并且成人字形分布
1
■
201C
11
2017
孔
的气孔
202
第孔
划化金K在豪固过程中牧第而产生的.残弼在熔核中的空穴
2021
孔
冷却过整中在那工中心形成的长形收媚孔穴.可能布残留气体,这种缺陷通倉在«fiW»宏面方向上出现
2022
徹编孔
庄显顒镇下观察到的轴孔
2023
庄下观』
4.试述熔焊接头中固体夹杂的种类及表示方法。
熔焊接头中固体夹杂的种类及表示方法,
见表3。
5.试述熔焊接头中未熔合和未焊透的种类及表示方法。
熔焊接头中未熔合和未焊透的种类及表
示方法,见表4
6.试述熔焊接头中形状缺陷的种类及表示方法。
熔焊接头中形状缺陷的种类及表示方法,
见表5。
数字序号
名称
说明
简图
5011
5012
连鏤咬边间新咬边
因焊接适成的婵趾(成焊根)处的沟權,咬边可能是连续的(5011)或间斷的(5012)
]
1
5011nth把11
IL^!
r^n
5013
编沟
由于焊縫金展的收缢.在根部焊道毎一側产生的浅的沟槽(也可见515)
<
^1eco
5013
503
凸度过大
角焊縫表面的焊
缝金属过离
504
下増
穿过单层焊建根部或从多层綁接接头穿过前道熔敷金農増落的过■炉置金H
*
^504
5041
局部下
局部圾瘡
505
焊缝形面不良
母材金属衰面与靠近焊凰处焊縫表面的切囲之间的角度a过小
&3fell
正带505
506
焊病
婵接过程中,熔化金JH流■到弊鼻之外未增化的母材上所形成的金JX瘤
506〔
r"C7~3es^2
506
507
错边
由于两个焊件没有对止而造成板的中心岐平行偲差
^<^^3-
508
角度01
曲于两个焊件粒有对正而使它们的表面不平行(或不成预定的角度)
509
下垂
由于重力作用适成的焊■金属増落
5091
5092
——焊It垂亶下垂
——字焊縫或仰
5092
nnem=i
7.试述熔焊接头中其它缺陷的种类及表示方法。
熔焊接头中其它缺陷的种类及表示方法,
见表6。
表6其它缺陷的种类及表示方法
数字序
号
名
称
说明
600
其它
缺陷
不能包括在1~5类缺陷
的其它缺陷
601
电弧
擦伤
在焊缝坡口外部引弧或打弧时产生于母材金属表面上的局部损伤
602
飞溅
熔焊过程中,熔化的金属颗粒和熔渣向周围飞散的现象。
这种飞散出的金属颗粒和熔渣习惯上也称为飞溅
6021
飞
钨溅
从钨电极过渡到母材金属表面或凝固焊缝金属表面上的钨颗粒
603
表面
不按操作规程拆除
撕裂
临时焊接的附件时产生于母材金属表面的损伤
604
磨痕
不按操作规程打磨
引起的局部表面损伤
605
凿痕
不按操作规程使用扁铲或其它工具铲凿金属而产生的局部损伤
606
打磨
过量
由于打磨引起的焊件或焊缝的不允许的减薄
607
608
位缺层错定焊陷间位
不按规定程序熔敷
的焊道
8.什么是热裂纹促使形成热裂纹的因素有
焊接过程中,焊缝和热影响区金属冷却到固相线附近的高温区间产生的焊接裂纹即热裂纹。
又称结晶裂纹。
其特征是断口呈蓝黑色,即金属在高温被氧化的颜色,裂纹总是产生在焊缝正中心或垂直于焊
缝鱼鳞波纹,焊缝表面可见的热裂纹呈不明显的锯齿状,或与焊缝波纹相垂直呈放射状分布。
个别情况下,热裂纹也可能出现在热影响区。
热裂纹主要发生在杂质含量较多的钢、单相奥氏体钢、镍基合金、铝合金、钼合金等的焊缝金属中。
促使形成热裂纹的因素有:
(1)焊缝金属的化学成分焊缝金属中
C、S、P元素较多时,促使形成热裂纹。
锰在熔池中能与硫形成MnS进入熔渣,可减少硫的有害作用,适量时可减少焊缝的热裂纹倾向。
钢中含铜量过多时,会增大焊缝热裂纹倾向。
(2)焊缝横截面形状焊缝熔宽与厚度
的比值越小,即熔宽较小、厚度较大时,容易产生热裂纹。
(3)焊接应力焊件刚性大,装配和焊接时产生较大的焊接应力,会促使形成热裂纹。
9.如何防止产生热裂纹
(1)控制焊缝金属中有害杂质的含量碳素结构钢用焊芯(丝)的含碳量均≤%,硫、磷的含量应≤%,焊接高合金钢时控制更严。
(2)预热能减小焊接熔池的冷却速
度,降低焊接应力。
随着母材含碳量或碳当量的增加,应适当增高预热温度。
奥氏体不锈钢焊缝不能采用预热的方法来防止产生热裂纹。
(3)采用碱性焊条和焊剂由于碱性焊
条和焊剂具有较强的脱硫、磷能力,因此具有较高的抗热裂能力。
(4)适当调整焊接工艺参数焊接工艺
参数直接影响焊缝的横断面形状,因此适当减小焊接电流以减少焊缝厚度,有利于提高焊缝的抗裂性能。
(5)采用收弧板焊接终了断弧时,由于弧坑冷却速度较快,常因偏析而在弧坑处形成热裂纹,即所谓的弧坑裂纹。
所以终焊时应逐渐断弧,并填满弧坑。
必要时可采用收弧板,将弧坑移至焊件外,此时即使产生弧坑裂纹,也因焊后需将收弧板割掉,并不影响结构本身。
10.什么是冷裂纹、延迟裂纹促使形成冷裂纹、延迟裂纹的因素有哪些焊接接头冷却到较低温度下(对于钢来说在Ms温度以下)时产生的焊接裂纹称为冷裂纹。
钢的焊接接头冷却到室温后并在一定时间(几小时、几天、甚至十几天)才出现的焊接冷裂纹称为延迟裂纹。
冷裂纹(包括延迟裂纹)主要发生在中碳钢、高碳钢、低合金或中合金高强钢、钛及钛合金的焊接接头中。
冷裂纹多发生在接头热影响区或熔合线上,个别情况下出现在焊缝上。
根据冷裂纹产生的部位,可将冷裂纹分为如下三种见图1。
1)焊道下裂纹在靠近堆焊焊道的热影响区内所形成的焊接冷裂纹。
其走向常与熔合线平行,但也有时垂直于熔合线。
(2)焊趾裂纹沿应力集中的焊趾处所形成的焊接冷裂纹。
其走向常与焊缝纵向平等,由焊趾的表面开始,向母材的深处延伸。
(3)焊根裂纹沿应力集中的焊缝根部
所形成的焊接冷裂纹。
其走向从焊缝根部开始,伸向热影响区或焊缝中。
形成冷裂纹的三大因素是:
钢种的淬硬倾向大、焊接接头的含氢量高和结构的焊接应力大。
特别是由氢促使形成的冷裂纹往往具有延迟的性质,常称为“氢致裂纹”。
11.如何防止产生冷裂纹
(1)控制焊缝金属的含氢量采用碱性
低氢型焊条和焊剂;严格按规定烘干焊条和焊剂;仔细清除焊接区的污物、锈、油、水。
(2)预热减慢接头的冷却速度以降低淬硬倾向。
(3)后热(消氢处理)后热是指焊接
结束或焊完一条焊缝后,将焊件或焊接区立即加热到150~250℃,并保温一段时间。
消氢处理是在300~400℃加热温度内进行。
两者均能促使氢逸出,但消氢处理效果更好。
(4)采用较大的焊接线能量减慢接头
的冷却速度。
但线能量太大时,会促使热影响区形成过热组织,所以应适当控制,不能无限制地增大。
(5)采用奥氏体不锈钢焊条因奥氏体
组织塑性好,可减少焊接应力,并能溶解较多的氢,所以可用来焊接淬硬倾向较强的低合金高强钢,避免产生冷裂纹。
12.什么是再热裂纹防止产生再热裂纹的方法有哪些焊后焊件在一定温度范围内再次加热(消除应力热处理或其它加热过程)而产生的裂纹称为再热裂纹。
再热裂纹通常发生在熔合线附近的粗晶区中,从焊趾部位开始,延向细晶区停止。
钢中Cr、Mo、V、Nb、Ti等元素会促使形成再热裂纹,其影响可用下式表示△G′=Cr+++10C-2
△G′>2时,对再热裂纹敏感;<△G′<2时,一般;△G′<时,对再热裂纹不敏感。
防止产生再热裂纹的方法:
(1)预热预热温度为200~450℃。
若焊后能及时后热,可适当降低预热温度。
例如,18MnMoNb钢焊后在180℃热处理2h,预热温度可降低至180℃。
(2)应用低强度焊缝使焊缝强度低于
母材以增高其塑性变形能力。
(3)减少焊接应力合理地安排焊接顺
序、减少余高、避免咬边及根部未焊透等缺陷以减少焊接应力。
13.什么是层状撕裂防止层状撕裂的方法有哪些焊接时,在焊接构件中沿钢板轧层形成的呈阶梯状的一种裂纹称为层状撕裂。
层状撕裂经常发生在T形接头和角接接头中,其走向与钢板表面相平行见图2,图中箭头表示接头的受力方向。
产生层状撕裂的原因是在轧制钢板中存在硫化物、氧化物和硅酸盐等低熔点非金属夹杂物,其中尤以硫化物的作用为主,在轧制过程中被延展成片状,分布在与表面平行的各层中,在垂直于厚度方向的焊接应力作用下,夹杂物首先开裂并扩展,以后这种开裂在各层之间相断发生,连成一体,造成层状撕裂的阶梯性。
防止层状撕裂的方法:
1)严格控制钢材的含硫量。
2)采用强度级别较低的焊接材料。
3)在与焊缝相连接的钢板表面堆焊几层低强度焊缝金属作为过渡层,以避免夹杂物处于高温区。
4)预热和使用低氢焊条。
14.常用的抗裂性试验方法有哪些
常用的抗裂性试验方法,见表7表7抗裂性试验方法
序号
试验方
法
产生的主要裂纹类型
也可反映的裂纹
不需特殊的试验装置
热影响
焊缝冷裂
斜Y形坡口焊
区冷裂
纹、热裂
1
2
3
4
接裂纹试验()
纹
纹或再热
压板对接
焊缝热
裂纹
(FiSCO)焊接裂
裂纹
纹试验()
热影响
搭接接头
区冷裂
热影响区
5
6
7
8
9
10
11
(CTS)焊接裂纹
纹
冷裂纹
试验()
焊缝热、
热影响区
刚性固定对接
冷裂纹
冷裂纹
试验
焊缝根
可变刚性试验
部冷、热
十字接头试验
裂纹
十字搭接裂纹
热影响
试验
区冷裂
窗形拘束对接
纹
裂纹试验
Z向窗口试验
Z向拉伸试验
H形拘束试验
焊缝横向热裂纹
层状撕裂
层状撕裂
再热裂纹
12
13
14
15
需特殊试验装置
插销试验拉伸拘束裂纹试验(TRC试验)
刚性拘束裂纹试验(RRC试验)
可调拘束高温裂纹试验
冷裂纹冷裂纹冷裂纹焊缝热裂纹
层状撕裂
16
17
间接评定方法碳当量法热影响区最高硬
冷裂纹热影响
度不地()
区冷裂
纹
15.试述防止焊缝中产生气孔的常用方法。
1)仔细清除焊件表面上的污物,手弧焊时在坡口面两侧各10mm、埋弧焊时各20mm范围内去除锈、油,应打磨至露出金属表面光泽,特别是在使用碱性焊条和埋弧焊时,更应做好清洁工作。
2)焊条和焊剂一定要严格按照规定的温度进行烘焙:
酸性焊条75~150℃;碱性焊条350~450℃;焊剂250℃,并保温1~2h。
烘焙后的焊条应放在焊条保温筒内,随用随取。
碱性焊条在露天存放4h以上时应重新烘焙,重复烘焙的次数不得超过3次。
3)不应使用过大的焊接电流。
4)采用直流电源施焊时,电源极性应为反接。
5)碱性焊条施焊时,应采用短弧焊。
6)引弧时应将焊条略作停顿,对引弧处进行预热,否则引弧处容易形成气孔。
7)采用手弧焊打底、埋弧焊盖面的工艺时,打底焊条应为碱性焊条,用酸性焊条打底极易产生气孔。
8)气体保护焊时应调节气体流量至适当值、流量太小,保护不良,易使空气侵入形成气孔。
16.试述常用无损检验方法的种类及其选择。
不损坏被检查材料或成品的性能和完整性而检测其缺陷的方法称为无损(探伤)检验。
常用的无损检验方法有超声、射线(X、γ)照相、磁粉、渗透(荧光、着色)和涡流探伤等。
其中超声探伤和射线探伤适于焊缝内部缺陷的检测;磁粉探伤和渗透探伤则用于焊缝表面质量检验。
每一种无损探伤方法均有其优点和局限性,各种方法对缺陷的检出机率既不会有100%,也不会完全相同。
因而应根据焊缝材质、结构及探伤方法的特点、验收标准等来进行选择。
不同焊缝材质探伤方法的选择见表8。
17.试述射线探伤的原理及焊接缺陷的影像特征。
射线探伤可分别采用X、γ两种射线,其探伤原理见图3。
当射线通过金属材料时,部分能量被吸收,使射线发生衰减。
如果透过金属材料的厚度不同(裂纹、气孔、未焊透等缺陷,该处发生空穴,使材料变薄)或体积质量不同(夹渣),产生的衰减也不同。
透过较厚或体积质量较大的物体时衰减大,因此射到底片上的强度就较弱,底片的感光度就较小,经过显影后得到的黑度就浅;反之,黑度就深。
根据底片上黑度深浅不同的影像,就能将缺陷清
楚地显示出来
γ射线的穿透能力比X射线强,适合于透视厚度大于50mm的焊件。
射线探伤常见焊接缺陷的影像特征见表9。
表9射线探伤焊接缺陷影像特征
缺
陷
缺陷影像
产生原
种
特征
因
类
气
多数为圆形、
1)焊条受潮
孔
椭圆形黑点,其中心处黑度较大,也有针状、柱状气孔。
其分布情况不一,有密集的,单个和链状的
2)焊接处有锈、油污等3)焊接速度太快或电弧过长4)母材坡口处存在夹层5)自动焊产生明弧现象
夹
渣
形状不规则,有点、条块等,黑度不均匀。
一般条状夹渣都与焊缝平行,或与未焊透未熔合混合出现
1)运条不当,焊接电流过小,坡口角度过小2)焊件上留有锈及焊条药皮的性能不当等
3)多层焊时,层间清渣不彻底
未
焊
透
在底片上呈现规则的,甚至直线状的黑色线条,常伴有气孔或夹渣。
在V、比V形坡口的
1)间隙太小
2)焊接电流和电压不当3)焊接速度过快4)坡口不正常等
焊缝中,根部未焊透都出现在焊缝中间,K形坡口则偏离焊缝中心
未
熔
合
坡口未熔合影像一般一侧平直另一侧有弯曲,黑度淡而均匀,时常伴有夹渣。
层间未熔合影像不规则,且不易分辨
1)坡口不够清洁
2)坡口几何尺寸不当3)焊接电流电压小4)焊条直径或种类不对
裂
纹
一般呈直线或略带锯齿状的细纹,轮廓分明,两端尖细,中部稍宽,有时呈现树枝状影像
1)母材与焊接材料成分不当2)焊接热处理不当3)应力太大或应力集中
4)焊接工艺不正确
夹钨
在底片上呈现圆形或不规
采用钨极气体保护焊时,钨极爆裂
则的亮斑点,且
或熔化的钨粒进入
轮廓清晰
焊缝金属
18.试述射线探伤的质量标准。
根据GB3323-87《钢熔化焊对接接头射线
照相和质量分级》的规定,射线探伤的质量标准分为照相质量等级和焊缝质量等级两部分。
根据采用的射源种类及其能量的高低、胶片的种类、增感方式、底片的黑度、射源与胶片间的距离等参数,照相质量等级分为A、AB和B三级,质量级别顺次增高。
即后者比前者分辨相同尺寸的缺陷时,透照的厚度大。
锅炉压力容器的缝照相质量为AB级。
焊缝质量等级共分四级,Ⅰ级焊缝内缺陷最少,质量最高;Ⅱ、Ⅲ级焊缝内的缺陷依次增多,质量逐次下降,缺陷数量超过Ⅲ级者为Ⅳ级,Ⅳ级最差。
缺陷数量的规定:
Ⅰ级焊缝内不准有裂纹、未熔合、未焊透和条状夹渣(允许有少量气孔和点状夹渣);Ⅱ、Ⅲ级焊缝内不准有裂纹、未熔合以及双面焊和加垫板的单面焊中的未焊透(允许有一定数量的气孔、条状夹渣和不加垫板单面焊中的未焊透)。
19.试述超声波探伤的原理及质量标准。
利用超声波探测材料内部缺陷的无损检验法称超声波探伤。
超声探伤的原理,是利用焊缝中的缺陷与正常组织具有不同的声阻抗(材料体积质量与声速的乘积)和声波在不同声阻抗的异质界面上,通过超声波时会产生反射现象来发现缺陷的。
探伤时由探头中的压电换能器发射脉冲超声波。
通过声耦合介质(水、油、甘油或浆糊等)传播到焊件中,遇到缺陷后产生反射波,然后再用另一个类似的探头或同一个探头接收反射的声波,经换能器转换成电信号,放大后显示在荧光屏上或打印在纸带上。
根据探头位置和声波的传播时间(荧光屏上回波位置)可求得缺陷位置;反射波的幅度可以近似地评估缺陷的大小,见图4。
质量标准:
超声波探测焊缝的方向愈多,波束垂直于缺陷平面的机率愈大,缺陷的检出率也愈高,其评定结果也愈准确。
GB11345-89《钢焊缝手工超声波探伤方法和探伤结果分级》中规定,根据对焊缝探测方向的多少,把超声波伤划分为A、B、C三个检验等级,检验的完善程度逐级升高,其中B级适合于受压容器。
焊缝质量等级分类见表10。
表中数字为允许最大波幅长度。
20.试比较射线探伤和超声探伤各自的技术特性。
射线探伤和超声探伤的技术特性比较见
表11。
表11射线探伤和超声探伤的技术特性比较
检法
测方
射线照相法探
伤
超声探伤
原
方法的原理
穿透法
脉冲反射
法
物理
能量
电磁波
弹性波
理
缺陷部位的
完好部件与缺陷部位的穿
在完好部位没有反射
表现形式
透剂量有差异。
其差异程度与这两部分的材质、射线透过的方向以及缺陷的尺寸有关。
波,而在缺陷部位发生反射波。
其反射程度与完好部位和缺陷部位的材质有关。
信息显示
射线底片
荧光屏
显示的内容
完好部位与缺陷部位的底片黑度差
缺陷反射波的位置和幅度
易于检测的缺陷方向
与射线方向
平行的方向
与超声波束垂直的方向
易于检测的缺陷形状
在射线方向上有深度的缺陷
与超声波束成垂直方向扩展的缺陷
被
铸件
◎
○
检
锻件
×
◎
物
压延
件
×
◎
焊缝
◎
○
分层
×
◎
气孔
◎
○
缺
未焊
透
○
○
陷
未熔合
○
○
裂纹
△
△
夹渣
◎
○
注:
◎-很合适;○-合适;△-有附加条件时合适;×-不合适。
21.试述磁粉探伤的原理及质量标准。
利用在强磁场中,铁磁性材料表层缺陷产生的漏磁场吸引磁粉的现象,而进行的无损检验法称为磁粉探伤。
磁粉探伤原理:
首先将被检焊缝局部充磁,焊缝中便有磁力线通过。
对于断面尺寸相同、内部材料均匀的焊缝、磁力线的分布均匀的。
当焊缝表面或内部有裂纹、
气孔、夹渣等缺陷时,磁力线将绕过磁阻较大的缺陷,产生弯曲见图5a。
此时在焊缝表面撒上磁粉,磁力线将穿过表面缺陷上的磁粉,形成“漏磁”,磁粉就被吸附在缺陷上见图5b,根据被吸附磁粉的形状、多少、厚薄程度,便可判断缺陷的大小和位置。
内部缺陷由于离焊缝表面较远,磁力线在其上不会形成漏磁,磁粉不能被吸住,无堆积现象,所以缺陷无法显
常用磁粉是四氧化三铁(Fe3O4)和三氧化二铁(Fe2O3)。
缺陷磁痕按形状可分为三种:
(1)线状缺陷磁痕其显示长度为宽度
的3倍以上。
(2)圆型缺陷磁痕除线状缺