砂型铸造作业指导书.docx
《砂型铸造作业指导书.docx》由会员分享,可在线阅读,更多相关《砂型铸造作业指导书.docx(12页珍藏版)》请在冰豆网上搜索。
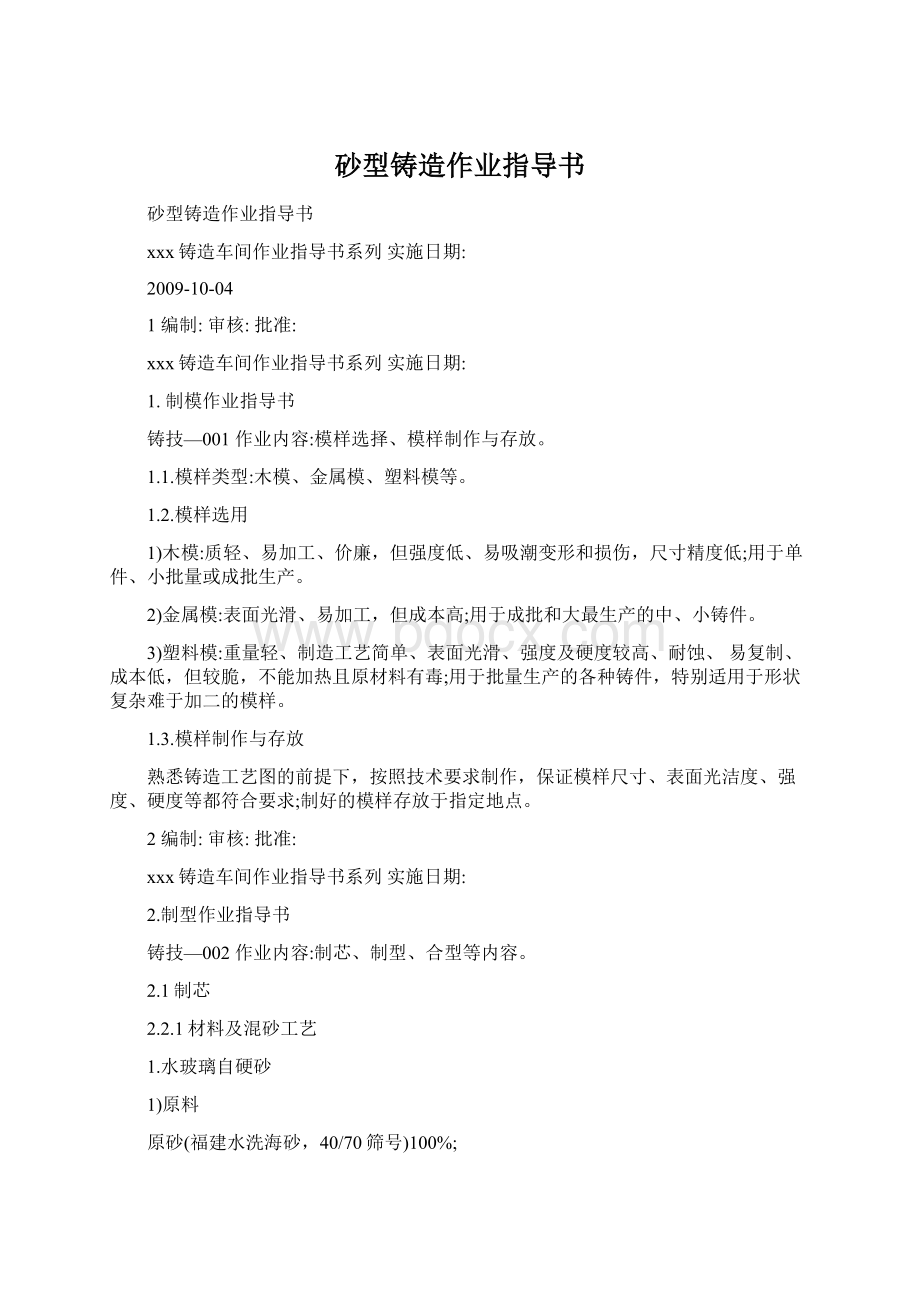
砂型铸造作业指导书
砂型铸造作业指导书
xxx铸造车间作业指导书系列实施日期:
2009-10-04
1编制:
审核:
批准:
xxx铸造车间作业指导书系列实施日期:
1.制模作业指导书
铸技—001作业内容:
模样选择、模样制作与存放。
1.1.模样类型:
木模、金属模、塑料模等。
1.2.模样选用
1)木模:
质轻、易加工、价廉,但强度低、易吸潮变形和损伤,尺寸精度低;用于单件、小批量或成批生产。
2)金属模:
表面光滑、易加工,但成本高;用于成批和大最生产的中、小铸件。
3)塑料模:
重量轻、制造工艺简单、表面光滑、强度及硬度较高、耐蚀、易复制、成本低,但较脆,不能加热且原材料有毒;用于批量生产的各种铸件,特别适用于形状复杂难于加二的模样。
1.3.模样制作与存放
熟悉铸造工艺图的前提下,按照技术要求制作,保证模样尺寸、表面光洁度、强度、硬度等都符合要求;制好的模样存放于指定地点。
2编制:
审核:
批准:
xxx铸造车间作业指导书系列实施日期:
2.制型作业指导书
铸技—002作业内容:
制芯、制型、合型等内容。
2.1制芯
2.2.1材料及混砂工艺
1.水玻璃自硬砂
1)原料
原砂(福建水洗海砂,40/70筛号)100%;
水玻璃2.8%;
有机酯0.28%。
2)混砂工艺:
原砂+有机酯,水玻璃,混砂速度快、混合均匀。
2.树脂砂
1)原料
新砂(SC40-70目,含泥及微粉量<1.5%,含水量<0.2%)100%;
呋喃树脂1-2%;
固化剂加入量为呋喃树脂的30%左右;
2)混制工艺:
原砂+固化剂(匀混60秒)?
树脂(匀混35-40秒),随混随用。
3)将型芯清理时的残砂及时拉走。
2.2.2制芯
1.制芯方法:
手工制芯:
刮板造芯,机器造芯:
震实式、挤压式、壳芯式、
自硬砂流水线。
2.型芯制作步骤
1)型砂与芯骨组装好放入芯盒内。
2)确定型芯气道:
对型芯应设置排气道;型芯排气道应与铸型排气口相通。
3.要求:
型芯含水量、强度、透气性符合工艺要求。
2.2制型
1.3.1材料及混砂工艺
3编制:
审核:
批准:
xxx铸造车间作业指导书系列实施日期:
1.水玻璃砂自硬砂
1)原料
原砂(福建水洗海砂,40/70筛号)100%;
水玻璃2.8%;
有机酯0.28%。
2)混砂工艺:
原砂+有机酯,水玻璃,混砂要求速度快,混合均匀。
2.树脂砂
1)原料
新砂(SC40-70目,含泥及微粉量<1.5%,含水量<0.2%)100%;
呋喃树脂1-2%;
固化剂加入量为呋喃树脂的30%左右;
2)混制工艺:
砂+固化剂(匀混60秒)树脂(匀混35-40秒),随混随用。
3)将铸型清理时的砂及时拉走。
1.3.2铸型制作
1(制作方法:
低压造型、中压造型、高压造型、冲击造型、手工造型等。
2.制作过程:
1)根据铸件结构确定分模面和组模结构;
2)根据铸件材质和结构确定缩水;
3)根据工装和模具特点确定分型面;
4)根据铸造工艺图确定浇注系统、冒口、冷铁结构和位置。
3.要求:
铸型含水量、透气性、强度符合工艺要求。
2.3合型
1.4.1准备工作
1.检查铸型制作状态;
2.检查型芯制作状态;
1.4.2合型内容及方法
1(型芯装配常用方法
4编制:
审核:
批准:
xxx铸造车间作业指导书系列实施日期:
1)各类型芯均考虑铸型内的定位;
2)型芯装配应按序进行。
2(下型芯时检查芯头或其他定位物与铸型相对应部位配合状态。
3.合型前检查铸型内无浮砂或其他残存物。
4.合型时检查砂箱定位装置是否良好。
5.合型后正确安装浇口杯。
5编制:
审核:
批准:
xxx铸造车间作业指导书系列实施日期:
3.熔炼作业指导书
铸技—003作业内容:
材料准备、熔炼操作、熔炼工艺。
3.1.材料准备
1.原料
根据产品要求确定合适的原料,一般要确定原料的具体化学成分。
2.炉料
炉料应清洁、无污染、尺寸合适,根据铸件成分计算各原料的重量比。
3(造渣剂
1)碎玻璃:
采用无色干燥碎玻璃。
2)石英砂:
采用10,20目干燥石英砂。
3)石灰:
采用无氧化块度在20mm左右石灰。
4)萤石:
采用干燥块度在20mm左右萤石
4.集渣剂
1)珍珠岩粉:
应保持干燥。
2)稻草灰:
炉前采用热稻草灰。
3.2熔炼操作
1.熔炼操作由炉长统一指挥。
2.熔炼工检查炉料备料情况。
3.熔炼工检查熔炼炉及其电器情况。
4.熔炼工检查浇包烘烤和工具准备情况。
炉长监督各岗位人员认真做好工作。
5.
6.熔炼过程中若出现异常情况,应紧急处理,并停炉检查。
7.保证出钢温度、成分符合工艺要求。
8.做好熔炼原始数据记录。
3.3熔炼工艺
1.按实际入炉的炉料过磅计重,误差不超过20Kg.2.按照顺序加料,易熔料加在炉底,大小料搭配,尽可能提高炉料密度。
3.选择适当供、配电制度,合理供电,节约能源。
6编制:
审核:
批准:
xxx铸造车间作业指导书系列实施日期:
4.按照工艺和材质要求做好造渣、除渣、脱氧、去气等有利提高冶金质量的
操作。
5.降低送电功率,并保温几分钟,测量温度、调整温度。
7编制:
审核:
批准:
xxx铸造车间作业指导书系列实施日期:
4.浇注作业指导书
铸技术—004作业内容:
浇注操作、浇注工艺。
4.1浇注操作
1.由炉长统一指挥;
2.检查浇包烘烤情况,结合当班生产任务,确定浇包数量;
3.根据工艺要求选择正确浇注温度。
4.浇注过程,配合协调,不耽搁时间。
5.准备挡渣设备、严格挡渣。
6.浇注完毕,清理浇嘴,将残留钢液回炉,然后翻转浇包至原位置。
7.做好浇注原始数据记录。
4.2浇注工艺
1.浇注前确定浇注高度;
2.浇注过程保证浇口杯程充满状态,防止杂物进入型腔,并做好除渣措施;3.浇注后,清理未浇注的金属液;根据工艺要求保证铸件保温时间。
8编制:
审核:
批准:
xxx铸造车间作业指导书系列实施日期:
5.清理作业指导书
铸技—005作业内容:
落砂,落芯,切割浇冒口,打磨浇冒口余根,抛丸处理,焊补、矫正。
5.1清理方法
1(常用打断浇冒口方法:
1)冷清除法:
(1)锤击敲断法;
(2)机械切割法;
(3)机械折断法。
2)热清除法:
(1)氧炔焰切割;
(2)电弧切割;
(3)离子切割。
3)其它方法:
(1)导电切割;
(2)新型的超声波切割;
(3)水砂流切割。
2(打磨:
可通过打磨对铸件做更进一步处理。
常用打磨浇口余根工具:
手工砂轮机、固定式砂带机和角向磨光机。
3(抛丸处理:
铸件上的锈皮和附着物可以使用喷、抛丸处理。
一般选择钢
0.8mm。
清理效率取决于弹丸的喷射速度和单位时间喷射到铸件丸直径为0.4,
表面的弹丸量。
4.铸件焊补与矫正
铸件的缺陷不可避免,可以采用焊补的方法使铸件满足技术要求。
1)修补质量必须进行严格检验:
(1)检验焊补前缺陷处是否清理干净;
(2)待焊表面是否清洁;
(3)焊接角度是否合理。
9编制:
审核:
批准:
xxx铸造车间作业指导书系列实施日期:
2)采用焊补工具:
铸造缺陷修补冷焊机、金属缺陷修复机。
10编制:
审核:
批准:
xxx铸造车间作业指导书系列实施日期:
6.热处理作业指导书
铸技—006
作业内容:
工艺要求(碳钢件的热处理、低合金钢铸件热处理、高锰钢铸件的热处理、耐热钢铸件的热处理),操作过程。
6.1工艺要求
6.1.1碳钢件的热处理工艺
1)退火:
加热到AC3以下20-30?
,保持一定时间,随炉缓慢冷却至620?
出炉。
2)正火:
加热到AC3以上30-50?
,保持一段时间,空冷。
复杂铸件可作正火后回火,一般铸件不用回火。
3)调质处理:
含碳量为0.35-0.45%,在温度850-830?
淬火处理,在温度为300-640?
回火处理。
6.1.2低合金钢铸件的热处理工艺
加热到AC3+(30-50?
),根据合金种类在适合的温度下回火回火处理后,采用快冷。
6.1.3高锰钢铸件的热处理工艺
1)加热速度
高锰钢从常温加热到600?
这段时间,钢的韧性最低,容易开裂,这段时间要严格控制加热速度。
壁厚小于25mm的薄壁件为70?
/h加热速度;25-50mm的中等壁厚铸件可用50?
/h的加热速度;厚后壁铸件采用30-50?
/h的加热速度。
?
以上可以选100-150?
的加热速度。
待温度升高到600
2)加热温度和保温时间
一般加热温度控制在1050—1100?
,随含碳量提高,加热温度也应提高;保温时间主要根据铸件的壁厚来确定。
3)淬火
开炉到入水的时间越短越好,保证铸件入水温度不低于1000?
,淬火池中水温不高于50?
。
6.1.4耐热钢铸件的热处理工艺
11编制:
审核:
批准:
xxx铸造车间作业指导书系列实施日期:
耐热铸钢工作环境在600?
以下,热处理主要采用正火和调质处理。
马氏体耐热铸钢Cr%=9%-13%,热处理的方法采用正火+回火;其中Cr%=13%应在300?
或600?
-800?
回火,以免在480?
变脆。
铁素体耐热必须快速通过400-550?
的脆性区。
6.2操作过程
6.2.1准备工作
1.穿戴好规定的劳保用品。
2.检查设备情况(各个仪表指示是否正常,记录仪与温度显示是否相符,记录仪的时间指示是否准确,超温报警温度与工艺温度是否匹配,三相电流表的指示是否稳定匹配,电器声音是否正常,热电偶是否完好,天车运行是否正常,冷却风扇是否正常,炉门钢丝绳是否紧固可靠,使用工具是否齐全),确认无误后,方可接班。
3.装好记录纸,根据待处理件的工艺,将仪表调至设定温度,调好对应时间,并调整合适的超温报警温度。
4将待热处理件(材质、规格、数量)与跟踪单、炉号报表对照核实无误后,根据铸件特征及工艺规定确定采用的热处理炉和装炉方式。
6.2.2操作过程
1.温度升到工艺要求温度后,断开电源,打开炉门,开出台车,台车完全离开炉体后,立即关闭炉门。
吊装装件,防工件磕碰,装炉时动作要稳,以防工件磕碰和炉体损坏。
装炉操作应稳步迅速进行,尽量减少热损失。
2.装完炉后,再一次检查工件是否放稳,工件是否在有效加热区,工件距炉壁间距离是否合适,无异常情况立即关闭炉门。
炉门不严或有漏气现象,用保温棉封好,送电升温。
至规定温度后保温,应经常检查电流表是否正常,记录仪指示是否准确,有无超温或其它异常现象,并将所处理产品相关内容写在记录纸对应位置上。
常规的内容包括:
产品名称、规格、材质;熔炼炉号或炉次号;数量,操作者,热处理炉次。
3.保温到时后,断开电源,撤开保温棉,打开炉门,迅速将铸件分散到已调整好的规定冷却装置中,动作要迅速平稳,防止碰坏炉内热电偶,避免铸件在高温时造成磕碰。
然后立即将准备好的下一炉铸件装入炉中,关门升温进行热处理。
12编制:
审核:
批准:
xxx铸造车间作业指导书系列实施日期:
4.散落在地上的或其它原因造成不符合工艺温度的热处理件,务必重新热处
理。
一般情况下,重新热处理次数不超过两次。
5.自检合格后摆放好,填好跟踪单,并做好明显标记。
6.一个班次工作结束时,给下一班次备好工件,调好设备工作状态,检查设
备情况,按规定进行日常保养,做好原始记录。
13编制:
审核:
批准:
xxx铸造车间作业指导书系列实施日期:
7.缺陷认定及防止方法
铸技—0077.1冷隔、浇不足
1.缺陷特征
冷隔:
铸件上有未完全融合的缝隙,其交接边缘是圆滑的。
浇不足:
铸件局部未充满,铸件缺肉,末端呈圆弧状。
2.产生原因
由于浇注温度低或者浇注速度慢,金属液产生的阻力过大,产生浇不足、冷隔情况。
3.防止措施
1)提高浇注温度或者浇注速度。
2)提高压头高度。
3)设计合理浇注系统,使金属液能快速、平稳的充满型腔。
7.2气孔
1.缺陷特征
由气体形成的光滑孔眼、凹穴及分散性微气孔;分布于铸件表面或接近表面处。
主要有气泡形成的皮下气孔、侵入性气孔和析出性气孔。
2.产生原因
1)皮下气孔:
(1)合金熔炼不当,脱氧不良。
(2)浇注过程中,铁液氧化产生气体。
)侵入性气孔2
铸型和型芯产生的气体侵入到金属液后未能逸出导致气孔。
3)析出性气孔
主要是熔炼过程中金属液吸收的气体,在凝固过程中未能全部析出而产生的气孔。
3.防止措施
1)皮下气孔
(1)适当提高浇注温度,严格控制各种添加剂含量,尽可能缩短浇注时间。
14编制:
审核:
批准:
xxx铸造车间作业指导书系列实施日期:
(2)防止铁液氧化,严格控制进风量。
(3)尽量降低型砂水分。
(4)提高浇注速度。
2)侵入性气孔
(1)严格控制型砂和砂芯中的发气物质含量。
型砂中含水量不能过高,型
芯要保证烘干。
隔天使用的型芯需要回炉烘干。
(2)改善砂型、型芯透气性。
(3)在适当位置扎排气孔。
(4)适当提高浇注温度。
3)析出性气孔
(1)限制含气量多的炉料使用。
(2)铁槽、出铁口、过桥、浇包要烘干。
(3)各种添加剂需要在烘干情况下才能使用。
7.3砂眼、渣孔
1.缺陷特征
砂眼:
缺陷处内部或表面充塞着型砂的小孔。
渣孔:
形状不规则,内部是渣或者夹渣物。
2.产生原因
1)砂眼
(1)砂型紧实率较低。
(2)型腔中含有浮砂。
(3)金属液对型壁冲刷作用较大。
2)渣孔
(1)金属液不纯净、
(2)金属液在浇注过程中产生氧化。
(3)扒渣、挡渣效果不当。
3.防止措施
1)砂眼
(1)提高砂型紧实度。
15编制:
审核:
批准:
xxx铸造车间作业指导书系列实施日期:
(2)造型时对浮砂彻底清除。
(3)合理设计浇注系统,减轻铁液对型壁冲刷作用。
2)渣孔
(1)提高金属液温度,放置静止一段时间,利于熔渣上浮。
(2)尽量减少金属液氧化。
(3)增加过滤网,提高挡渣能力。
7.4缩孔、缩松
1.缺陷特征
的厚断面、热解、或者轴心等最后凝固的地方形成表面粗糙的孔洞。
在铸件
2.产生原因
金属液凝固过程时产生的液态收缩和凝固收缩远大于固态收缩,并且最后凝固位置得不到金属液的补缩所形成的。
3.防治措施
1)根据工艺正确选择金属液成分。
2)适当降低金属液浇注温度。
3)合理设计浇注系统,必要时配用冒口和冷铁。
7.5粘砂
1.缺陷特征
铸件表面粘结着一层很难清理的造型材料。
2.产生原因
高温金属液渗入到砂粒间隙中间。
金属氧化与造型材料粘合在一起形成。
3.防止措施
1)选择耐火度高的砂粒;型砂中SiO含量高于92%。
2
2)砂型紧实度要高。
3)适当降低浇注温度和提高浇注速度。
7.6裂纹
1.缺陷特征
铸件表面有直线或者曲线的裂纹。
热裂:
不规则曲线,断口表面呈黑色,有较深氧化色。
冷裂:
裂口较直,表面呈金属光泽,比较干净。
16编制:
审核:
批准:
xxx铸造车间作业指导书系列实施日期:
2.产生原因
冷却凝固收缩时受到阻碍产生较大应力,应力大于金属强度时,产生了裂
纹。
3.防止措施
1)严格控制金属液中化学成分,尤其是硫的含量。
2)调节系统中金属液冷却速度。
采用加冷铁的方式。
3)铸件浇注完后,不易开箱太早,最好低于600度。
4)设计铸件时,采用加强肋或者反变形法,减少铸件应力作用。
7.7变形
1.缺陷特征
长的铸件容易产生变形。
2.产生原因
1)铸件壁厚不均匀。
2)金属液冷却凝固时产生应力。
3.防止措施
1)铸件壁厚设计的尽量均匀,适当增加加工余量。
2)模具设计成反向变形,以抵消变形。
3)铸件进行应力退火。
4)开箱时间不易过早。
17编制:
审核:
批准: