第2章节 塑料注射模设计要点.docx
《第2章节 塑料注射模设计要点.docx》由会员分享,可在线阅读,更多相关《第2章节 塑料注射模设计要点.docx(42页珍藏版)》请在冰豆网上搜索。
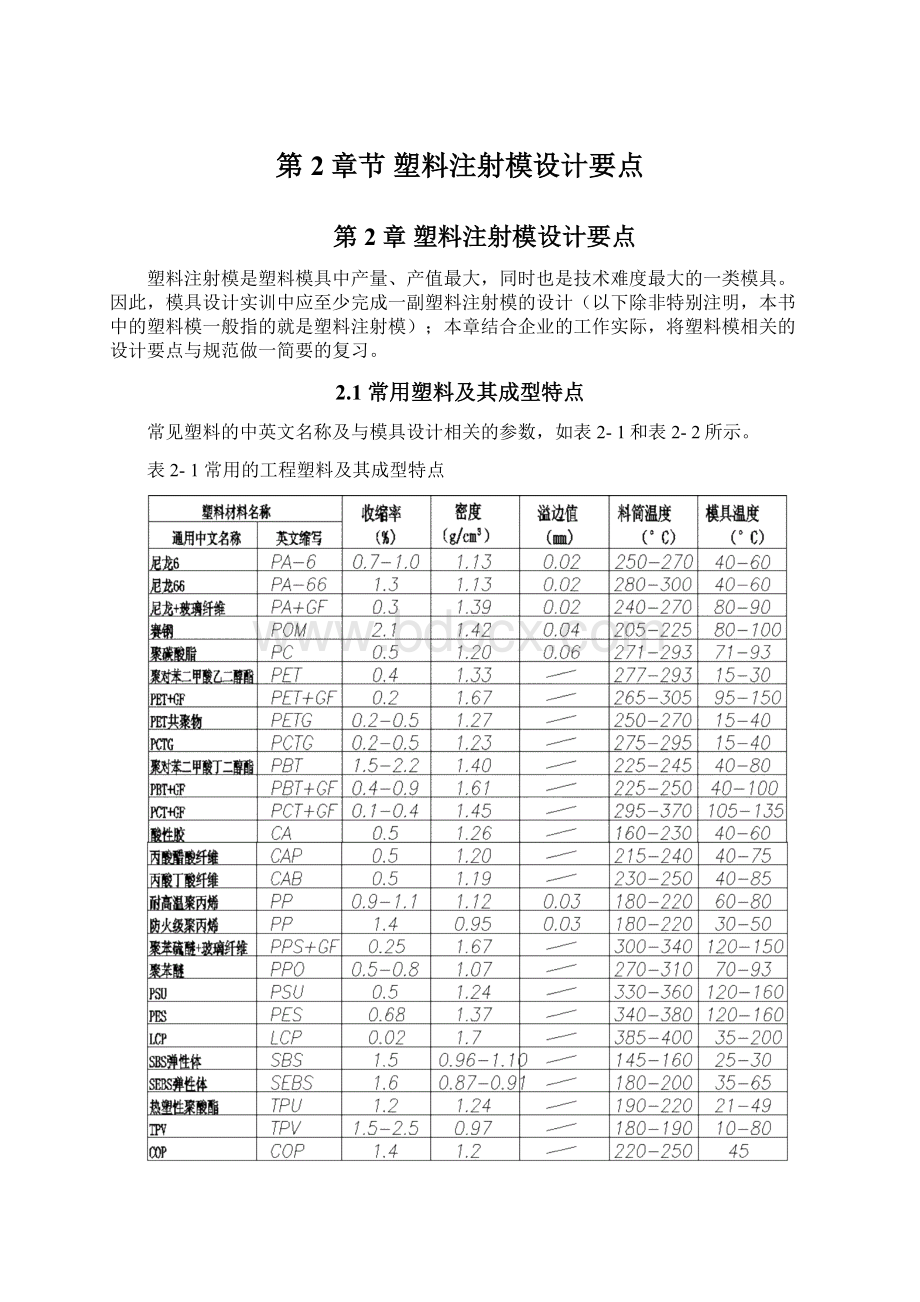
第2章节塑料注射模设计要点
第2章塑料注射模设计要点
塑料注射模是塑料模具中产量、产值最大,同时也是技术难度最大的一类模具。
因此,模具设计实训中应至少完成一副塑料注射模的设计(以下除非特别注明,本书中的塑料模一般指的就是塑料注射模);本章结合企业的工作实际,将塑料模相关的设计要点与规范做一简要的复习。
2.1常用塑料及其成型特点
常见塑料的中英文名称及与模具设计相关的参数,如表2-1和表2-2所示。
表2-1常用的工程塑料及其成型特点
表2-2常用的通用塑料及其成型特点
2.2塑料注射模的基本组成
一般情况下,对于塑料模具而言,主要有二类,一类为二板模,俗称大水口模;另一类为三板模,俗称细水口模。
不管是二板模,还是三板模,塑料模具一般由以下几个部分组成。
1、模架:
模架构成了塑料模具最基本的框架部分。
模架一般可从专业模架厂商处直接采购。
2、塑料模具的核心部分——型腔和型芯:
主型腔和主型芯俗称模仁或内模,是模具里面最重要的组成部分。
设计工作的大部分时间的也花费在模仁的设计上。
不过,相对有些比较简单的模具,它没有模仁部分,产品直接在模板上面成形,特别是早期的塑料模具大都如此,这种结构已经逐步淘汰。
3、塑料模具附助零件:
如定位环、浇口套、推杆(也称顶杆或顶针)、拉料杆(俗称抓料销)、支撑柱、顶出板导柱导套、支撑钉(俗称垃圾钉)等。
如果是三板模,往往还要设置专门的顺序开模控制机构。
4、塑料模具的附助系统:
一般的塑料模具有以下三个系统:
浇注系统、顶出系统、冷却系统。
有时,因为所运用的塑料材料需加热的温度很高,所以,有的模具还会存在一个加热系统。
5、当塑料制品侧向有孔或卡勾的时候,模具还必须设置一个或多个处理这些孔、卡脱模的机构,如滑块、斜推杆杆、油压缸等等。
这种处理的机构称之为侧向分型与抽芯机构。
2.3标准模架
为了在缩短模具的设计与制造时间,模具制造企业的往往将工作的重点放在模仁的设计与加工上,而作为基础构建的模架往往采用专业厂家的标准模架。
标准模架又称标准模座或者标准模胚,它由专业的厂家进行生产,模具的设计人员根据模具的需求可以直接从模架厂商定购回来。
目前的标准模架一般可分类为二板式模架和三板式模架。
二板式模架俗称大水口模架,主要适用于采用侧向浇口的模具;三板模俗称细水口模架,比较适合于采用点浇口的某。
根据模架的具体功能和结构,这两类模架又各自细分为若干个不同的样式。
2.3.1二板式模架
二板模标准模架的组成如图2-1所示,它一般它由以下几个部分组成:
1、模板:
上下固定板、公母模板、上下顶出板、模脚等。
某些情况下,公母模侧还会有一块承板。
2、连接螺钉:
S1--连接上固定板与母模板,一般4-6个;S2--连接下固定板与公模板,它穿过了模脚,与其是间隙配合,一般是4-6个,它的大小和到模具中心线之间的位置跟S1一致,只有其螺钉的长度不一样。
S7--连接上下顶出板,分布在顶出板的四个角上,一般是4个。
S8--连接下固定板与模脚,一般为4-6个。
3、辅助零件:
导柱与导套,一般是4组。
为了防止模具在安装时装反,四组导柱导套中靠近基准的一套向模具中心线向上偏了2mm,并在相对应的位置标刻有“OFFSET”的字样,该值不管模具大小,每套模具都一样。
回位销——即复位杆,一般有4个,分布在顶出板四个角上。
4、其它部分:
吊环孔——由于模具一般都较重,为了方便模具的安装和搬运,往往在模具上加工出吊环孔以安装吊环。
根据上述特点,用户在订购二板式标准模架时,只需要决定以下几个尺寸即可:
(1)模具的长×宽;
(2)A板、B板的厚度(即公母模板的高);
(3)模脚的高度;
据此,订购模架时只需标记出模架的型号和上述3组参数即可,如SC1530A60B70C90,其表示的意思如下:
SC——模架类型代号,代表的是大水口(二板式)系列的C类型;
1530——模具的宽为150mm,长为300mm;
A60——A板的厚度60mm,B70——B板的厚度为70mm;C90——C板的高度为90mm。
而各个连接螺钉、吊环孔、导柱导套、回位销等的位置、大小、数量,用户一般不能更改。
图2-1典型二板式标准模架
2.3.2三板式模架
三板模标准模架的组成部分如图2-2所示,其与二板模标准模架的许多地方是相同的,一般也由以下几个部分组成:
1、模板:
上下固定板、A板和B板、上下顶出板、模脚等。
有时,B板下方还会有一块承板。
此外,它多了一块不可缺少的板——脱浇板,俗称剥料板。
2、连接螺钉:
S1——连接下固定板与公模板,它穿过了模脚,一般是4-6个。
S3——连接上下顶出板,分布在顶出板的四个角上,一般是4个。
S2——连接下固定板与模脚,一般为4-6个。
这里要特别注意的是:
上固定板与剥料板、母模板之间没有螺钉进行连,它依靠导柱B进行定位和导向,因为剥料板需要运动。
3、辅助零件:
导柱与导套,三板式模架有二种导柱导套,导柱导套A和导柱导套B,总共8套。
同样,为了防止模具在安装时装反,8套导柱导套中靠近基准的二套向模具中心线向上偏了2mm,并标记有“OFFSET”的字样。
4、其它部分与二板式模架相同。
用户在订购三板式标准模架时,除决定模具的长、宽以及A板、B板、C板的厚度外,还应决定导柱B(大拉杆)的长度。
图2-2典型三板式标准模架
2.4浇注系统
2.4.1喷嘴与浇口套的关系
注射机喷嘴与模具浇口套的关系应满足图2-3所示的关系。
图2-3喷嘴与浇口套的关系
2.4.2定位环
定位环的常见形式有A型和B型两种,当喷嘴直接作用于产品胶位面时,为防止浇口套因受注射压力的作用而变形,可采取特殊形式的定位环,如图2-4所示。
(a)A型定位环(b)B型定位环
(c)特殊形式定位环
图2-4定位环的形式与规格
2.4.3浇口套
浇口套的形式如图2-5所示。
当主流道长度大于80mm时,可用延伸浇口套以缩短流道长度.;而锥度浇口套用于当主流道高度大于80时代替延伸浇口套,主要用于细水口和简化细水口模具。
(a)A型浇口套(b)B型浇口套
(c)锥形浇口套(d)延伸浇口套
(d)倾斜浇口套
图2-5浇口套的形式与规格
2.4.4流道
1.流道的截面形式
塑料模常用的流道类型有圆形流道、半圆形流道和梯形流道。
其断面形状及尺寸大小应根据塑件的成型体积、塑件壁厚、形状和所用塑料的工艺特性、注射速率、分流道长度等因素来确定。
(1)圆形流道
如图2-6所示,圆形流道的直径d一般在4~12mm范围内变动,对流动性很好的聚丙烯、尼龙等塑料,当分流道很短时,其直径可小到2mm;对流动性很差的聚碳酸酯、聚砜等,直径可达12mm,对多数塑料来说,分流道直径在5~6mm以下时,对流动性影响较大,但直径在8mm以上时,再增大其直径,对流道性的影响却不大。
图2-6圆形流道
(2)梯形流道
如图2-7所示,梯形流道的断面尺寸高度为h=2/3w,梯形斜角单边常取5°和10°,底部半径r=1.5mm,分流道宽度w常在4~12mm范围内变动。
图2-7梯形流道
2.4.5浇口
1、浇口的设计原则
(1)浇口应设置在产品胶位厚壁处,使塑料从厚壁流向薄壁处,以减少压力的损失。
(2)浇口应设置在制品最容易清除的地方,且尽量不要影响外观。
(3)浇口位置和塑料流入方向,应使塑料流入型腔时,能沿型腔平行方向均匀地流入,并有利于型腔的排气,如图2-8所示。
图2-8浇口位置应使熔体沿
(4)浇口位置设置应尽量避免熔接痕、流痕产生于制品的重要部位。
如图2-9所示。
图2-9浇口位置
(5)一模多腔时,浇口的尺寸应根据浇口与主流道的距离和制品的大小来开设。
(6)浇口的设置应避免塑料直接冲击薄弱的型芯、镶件、行位等,防止工件变形。
如图2-10所示。
图2-10浇口位置
(7)浇口的设置还应考虑制品在横方向和纵方向不同的收缩。
2、浇口的类型与应用
(1)直接浇口
直接浇口进胶适用于一模一穴,根据客户确定而浇口不影响产品外观且成型深腔的大型塑料制品,不宜成型平薄形塑件和容易变形的塑件。
如图2-11所示,D值取8~12之间,对于平薄形塑件和容易变形的塑件D值最大取2S,L值一般不超过150,遇到特殊结构再加长.
图2-11直接浇口
(2)侧浇口
如图2-12所示,侧浇口也称标准浇口,标准浇口形状简单,加工方便,适合于除聚碳酸脂(PC)外的所有塑料材料。
其缺点是易产生流痕,不适合薄板形的透明制品,同时也不适合于细而长的桶形制品。
图2-12侧浇口
(3)搭接式浇口
如图2-13所示,搭接浇口适合于外观面不允许有浇口痕迹的所有塑料制品.可减少标准浇口所产生的流痕。
其缺点是浇口不易切除,材料是PVC、PU制品不宜采用。
图2-13搭接浇口
(4)潜伏式浇口
如图2-14所示,潜伏式浇口可以自动切断浇口,适合自动化生产。
但由于流道弯折过度、压力损失过大,建议PC、PMMA、SAN料制品不宜采用。
(a)潜定模(b)潜动模
(b)潜顶杆
图2-14潜伏式浇口
(5)薄形浇口
如图2-15所示,薄形浇口主要适用于大形的平板产品,使产品不易产生变形、流痕、气泡等现象。
其缺点是浇口不易剪除。
图2-15薄形浇口
(6)扇形浇口
如图2-16所示,扇形浇口主要适用于平板形制品及浅的壳形或盒形制品.这种浇口进入型腔速度均匀,可降低塑件的内应力和带入空气的可能性,去除浇口方便。
图2-16扇形浇口
(7)环形浇口
如图2-17所示,环形浇口适用于粘性塑料管形制品来避免熔接痕及减缓压力
图2-17环形浇口
(8)牛角形潜伏浇口和圆弧形潜伏浇口
在制品表面不允许留有任何浇口痕迹,又不能做普通潜伏浇口的情况下,选择如图2-18所示的牛角形潜伏浇口或如图2-19所示的圆弧形潜伏浇口。
牛角形潜伏浇口要采用镶件式加工。
图2-18牛角形潜伏浇口
图2-19圆弧形潜伏浇口
(9)点浇口
如图2-20所示,点浇口可应用于各种形式的制品,浇口附近的残余应力小,能自行拉断浇口,可实现自动化生产,对于较大的制品可多点进浇。
但注射压力损失大,多数要采用三板模结构,模具结构较复杂,成形周期较大。
图2-20点浇口
2.4.6冷料井
原则上,所有流道要留冷料井。
常用的冷料井结构与尺寸如图2-21所示。
图2-21冷料井
2.4.7流道凝料拉杆
为保证开模时流道凝料留在定模,应设置流道凝料拉杆;常用的流道凝料拉杆的结构如图2-22所示。
图2-22流道凝料拉杆
2.5内模
直接参与成型制品形状的零件,一般称为主型芯、主型腔,俗称内模或模仁,是决定制品质量的关键部件。
1.内模尺寸
(1)一般情况下的内模的尺寸
一般情况下,可按图2-23所示的数据决定内模的长、宽和高。
图2-23内模尺寸
上表提供的数据为制品形状正常的情况下实用,如制品有下面所述的情形,可不按此数据设计。
(2)当产品有下列情况出现时,产品到内模边的距离可适当减小。
1当产品存在有大面积的碰穿位,如所示。
图2-24产品中间部位存在大面积碰穿
2当产品整体比较平坦,只有局部有小面积凸台。
图2-25产品整体平坦
3当产品的截面形状大部分为圆弧,直身面较小
图2-26产品的截面形状大部分为圆弧
(3)当产品有下列情况出现时,产品到内模边的距离应适当增加.
①深腔形制品,制品的长、宽尺寸明显大于高度方向的尺寸,且高度的尺寸达到150mm以上。
图2-27深腔型制品
②深桶形制品对于深桶型制品,也应考虑定模采用原身留的形式并尽可能的做原身止口,矩形的深桶件应比圆形的深桶件留厚些。
图2-28深桶形制品
2.内模螺钉的排布
内模与模板的固定一般通过螺钉连接,连接螺钉的排布如表2-3所示。
表2-3内模螺钉
3.内模分型面及插穿位
(1)分型面
分型面往往被称为P/L面,是制品沿垂直于开模方向最大外形线所处的面。
确定P/L面应注意以下几点:
1P/L面应沿产品的外形拉伸,尽量避免线或点封胶。
图2-29避免尖角的分型面
2产品有较严格有外观要求,动模部分的胶位应比定模稍做小0.2~0.3mm.。
图2-30动模部分的胶位应比定模稍做小0.2~0.3mm。
3若产品没有平面,必须设计平面方便加工制造。
图2-31增加平面以方便加工
4原则上内模的封胶位最小在5mm以上。
对于大面积的P/L面,留15~20mm,封胶即可,其它部分避空。
图2-32内模的封胶位
(2)插穿位
一般情况下,内模的插穿斜度应在2°以上,最好3~5°,对于表面积超过2500mm的插穿面需要加开油槽,对于细小的,单独凸起的插穿位应设计镶件,便于更换。
内模插穿方法的选用如图2-33所示。
图2-33穿插方式的选用
4.内模的镶拼结构
(1)内模镶拼的原因
内模需要镶拼结构的原因主要有下列几点;
1整体加工困难(EDM或抛光困难),如图2-34所示;
2排气不良,塑料充填困难;
3互换性,当一套模具需要生产产品的多种型号时,可使用互换镶件达到目的.
4强度弱,易损坏的部位。
图2-34需要镶拼的地方
⑤前动模局部细小的突起,基于节约成本的考虑。
图2-35镶件
图2-36单独突起
(2)内膜镶拼的注意事项
①内模镶拼时,防止尖角的产生,如图2-37所示。
图2-37防止尖角
②内模镶件必须设计碰数平面,以方便后续加工。
如图2-38所示。
图2-38垂直面
(3)内模镶拼的形式
①通孔式(优先选用),结构如图2-39所示。
图2-39通孔式
②盲孔式当内模上的镶件尺寸T过长时,或内模水道必须通过镶件处时,镶件需镶盲孔。
T1封胶位尺寸最低不能小于5mm,镶件用螺钉定位。
图2-40盲孔镶件
(4)镶件的定位方式
①挂台定位(常用),如图2-41所示。
图2-41挂台定位
②销钉定位,适用于长、宽小于10x10的薄形镶件,如图2-42所示。
图2-42销钉定位
2.6冷却系统
塑料模具中常用的冷却方式一般就是以下几种:
(1)用水冷却模具,这种方式最常见,运用最多。
(2)用油冷却模具,不常见。
(3)用压缩空气冷却模具。
(4)自然冷却。
对于特简单的模具,注塑完毕之后,依据空气中与模具的温差来冷却。
冷却水道的形式一般有直通式、阶梯式、鸭舌片式和盘旋式等,分别如图2-43~46所示。
图2-43直通式水路
图2-44阶梯式水路
图2-45鸭舌片式(挡板式)水路
图2-46螺旋式水路
2.7斜导柱侧向抽芯机构
2.7.1斜导柱侧向抽芯机构的组成
侧向抽芯机构,俗称行位机构,是为了解决制品侧孔、倒勾等影响制品脱模问题而发展的模具机构,典型的侧向抽芯机构是斜导柱——滑块抽芯机构,其基本原理是将模具开闭的垂直运动,转向成水平运动。
斜导柱侧向抽芯机构的基本组成如图2-47所示。
图2-47斜导柱—滑块抽芯机构的组成
2.7.2滑块的基本参数
图2-48滑块的基本参数
2.7.3滑块设计的注意事项
(a)(b)
(c)(d)
(e)(f)
(g)
图2-49滑块设计的注意事项
2.7.4斜导柱的规格
图2-50斜导柱的规格
2.7.5斜导柱的安装
图2-51斜导柱的安装
2.7.6滑块的锁紧方式
由于制品在成型机注射时产生很大的压力,为防止滑块与活动芯在受到压力而位移,从而会影响成品的尺寸及外观(如跑毛边),因此滑块应采用锁紧定位,通常称此机构为止动块或后跟块。
常见的锁紧方式如表2-4所示。
表2-4滑块的锁紧方式
2.7.7滑块的定位方式
滑块在开模过程中要运动一定距离,因此,要使滑块能够安全回位,必须给滑块安装定位装置,且定位装置必须灵活可靠,保证滑块在原位不动,但特殊情况下可不采用定位装置,如左右侧跑滑块,但为了安全起见,仍然要装定位装置。
常见的定位方式如表2-5所示。
表2-5滑块的定位方式
2.7.8滑块与小型芯的连接
滑块头部小型芯的连接方式由成品决定,不同的成品对滑块小型芯的连接方式可能不同,具体小型芯的连接方式大致如表2-6所示。
表2-6滑块与小型芯的连接
2.8顶出机构
2.8.1顶出机构的基本要求
顶出机构也称推出机构或脱模机构,目的是成型后将制品从模具上顺利脱出。
常用的顶出机构可分为顶杆顶出、顶管顶出、斜顶杆顶出、推板顶出、气动顶出、油缸顶出等多种形式。
不管那种顶出方式,其机构应满足一下基本要求:
(1)尽量使塑料制品留在后模上,这是因为要利用注塑机顶出装置来顶出制品,必须在开模过程中保证制品留在后模上,这样模具的顶出机构较为简单。
如果因为制品的关系,产品不能留在后模上时,才由前模复杂的顶出机构顶出制品。
(2)为保证产品不变形不损坏,为此,必须分析产品在型腔各部位附着力的关系,以便选择适当的顶出方式及顶出部位。
(3)由于制品包紧型芯,因此脱模力应尽可能靠近型芯,同时也要布置在刚度、强度最大的部位,作用面积应可以能大些,以免损坏制品。
(4)结构可靠,即顶出机构应工作可靠,运动灵活并具有足够的强度和刚度。
2.8.2顶杆与顶管顶出机构
如图2-52所示,顶杆顶出时应注意以下几点:
(1)顶杆优先排布在骨位附近或脱模力较大的地方。
(2)水路与顶杆的间隔距离不能小于3.5MM。
(3)当顶杆与支撑柱较近时,以顶杆杯头不穿顶杆板孔为原则。
(4)顶杆应尽量排布在较平的位置,避免设在R角,尖角,太大的斜面及靠胶位边太近的地方。
(5)顶杆设在曲面上时杯头均需添加防转。
(6)顶杆要排布均匀,当产品顶出面有适当的位置及无特殊外观要求时,优先选用大顶杆。
(7)在十字架形或较深的骨位上,在不产生缩水和影响产品的情况下,可加胶做成如(图C)的方式。
(8)顶杆到胶位的最近避空为20MM~30mm。
(9)一套模具中尽量用较少规格的顶杆,以便于加工。
(10)尺寸大的产品收缩量很大,顶杆不可太靠边,以避免产品套在顶杆上,取产品困难。
图2-52顶杆顶出注意事项
而当采用直径小于2.5mm的顶杆时,应注意图2-53所示的问题。
图2-53小顶杆的设置
当采用扁顶杆时,应注意图2-54所示的问题。
图2-54扁顶杆顶出
采用顶管顶出时,则需注意图2-55所示的问题。
图2-55顶管顶出
2.8.3斜顶杆顶出机构
斜顶杆,也称斜推杆,简称斜顶;其机构与滑块机构的基本原理都是将模具开模时垂直方向的运动换为水平方向的运动,其最大的不同在于其动作的驱动力来源不同:
斜顶杆主要靠顶针板运动而动作﹐并非像滑块是靠动、定模的开闭的运动而动作,因此斜顶杆的设计与推板的行程有关系,这就是斜顶杆设计与滑块设计最大的不同点。
斜顶杆结构的组成如图2-56所示。
图2-56斜顶杆机构的组成
设计斜顶杆时,斜顶杆的行程应按图2-57所示的内容进行。
图2-57斜顶杆的行程
斜顶杆的导滑方式应按图2-58所示进行。
图2-58斜顶杆的导滑
当斜顶杆采用镶拼结构式,应注意图2-59所示的问题。
图2-59斜顶杆的镶拼结构
2.9模具的装配图
一般而言,一副完整的模具装配图应包括下列内容:
(1)图框和标题栏
一般情况下,不同的公司都有自已独特的图框和标题栏,它反映了公司的名称、设计者、设计的日期、图纸名称、编号等等。
(2)一组视图
一般情况下,塑料模具装配图有四个主要的视图,它们分别为:
动模侧视图、定模侧视图、正剖视图和侧剖视图。
正、侧剖视图可以理解为模具完全装配之后的剖视图,而动模侧视图是把定模侧所有的东西拿掉之后,垂直看下来所得到的视图,它仅仅只看到动模侧的东西。
定模侧视图,则是把属于动模侧的所有东西绕基准右侧旋转180°之后、垂直看下来所得到的视图,也仅仅只看到定模侧的东西。
值得注意的是,在动、定模侧视图上都有一个基准符号,动模侧基准符号为“
”,母模侧基准符号为“
”。
此外,不管是动侧视图,还是定模侧视图,垂直看下去的对象都是各侧的所有零件完全装配下的视图。
有时,当模具比较复杂,还会追加一些附助视图来进行补充,如浇口的放大视图、塑件产品的立体示意图等。
(3)标注必要的尺寸和技术要求
装配图应包括各零件的装配关系,必要的尺寸(如外形尺寸,定位圈尺寸、安装尺寸、极限尺寸等),零件编号及明细表,技术要求等。
技术要求包含如下内容:
对模具某些结构的性能要求,如对脱模机构、抽芯机构的装配要求;对模具装配工艺的要求;模具的使用说明;防氧化处理;模具编号、刻字、油封及保管等要求;有关试模及检验方面的要求等。
(4)明细表
原则上,装配图的明细表应将该套模具的所有零件编上号码、定义名称、规格、数量等等等,以方便采购、生产和验收。