四分光器上盖注塑模设计.docx
《四分光器上盖注塑模设计.docx》由会员分享,可在线阅读,更多相关《四分光器上盖注塑模设计.docx(30页珍藏版)》请在冰豆网上搜索。
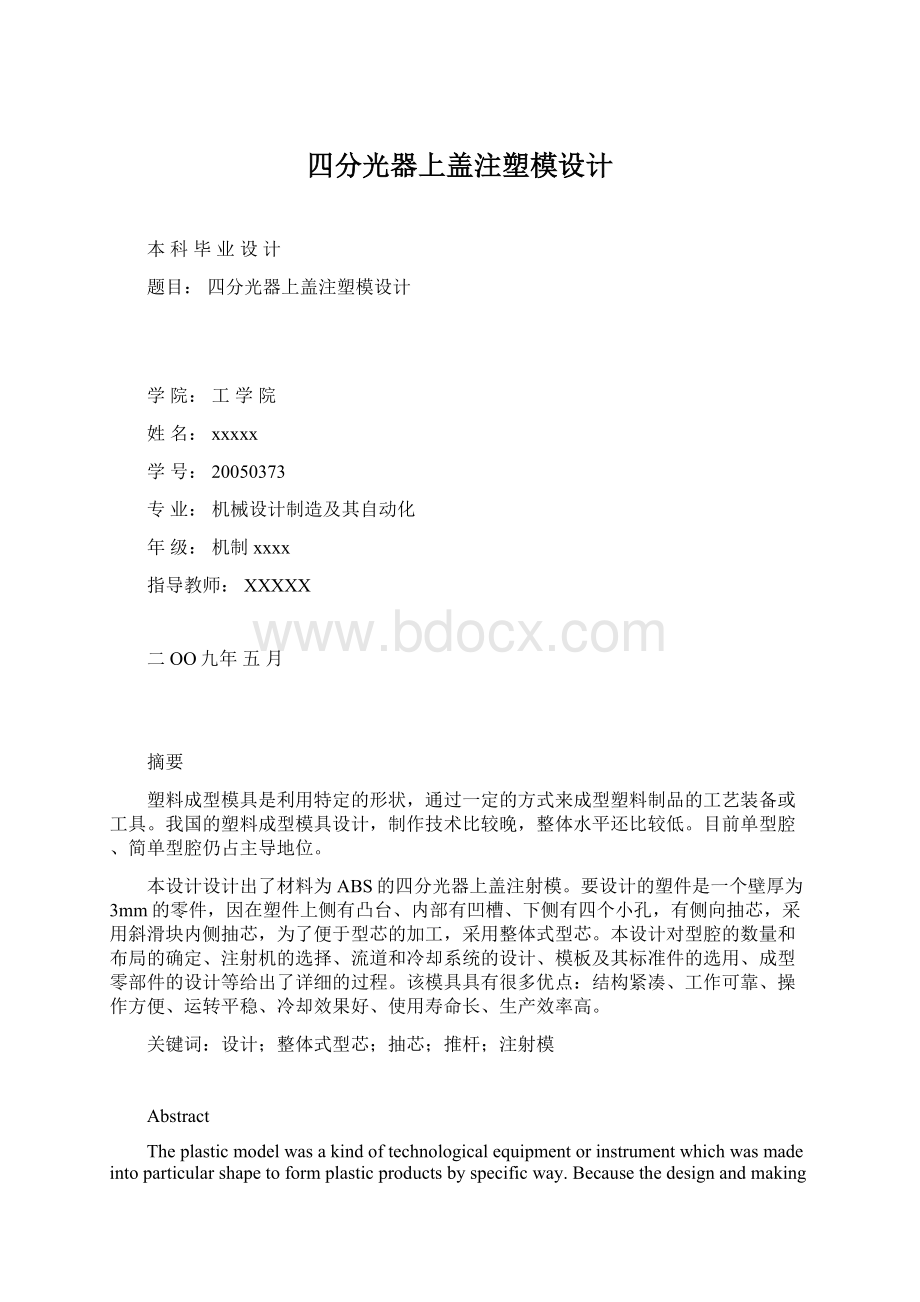
四分光器上盖注塑模设计
本科毕业设计
题目:
四分光器上盖注塑模设计
学院:
工学院
姓名:
xxxxx
学号:
20050373
专业:
机械设计制造及其自动化
年级:
机制xxxx
指导教师:
XXXXX
二OO九年五月
摘要
塑料成型模具是利用特定的形状,通过一定的方式来成型塑料制品的工艺装备或工具。
我国的塑料成型模具设计,制作技术比较晚,整体水平还比较低。
目前单型腔、简单型腔仍占主导地位。
本设计设计出了材料为ABS的四分光器上盖注射模。
要设计的塑件是一个壁厚为3mm的零件,因在塑件上侧有凸台、内部有凹槽、下侧有四个小孔,有侧向抽芯,采用斜滑块内侧抽芯,为了便于型芯的加工,采用整体式型芯。
本设计对型腔的数量和布局的确定、注射机的选择、流道和冷却系统的设计、模板及其标准件的选用、成型零部件的设计等给出了详细的过程。
该模具具有很多优点:
结构紧凑、工作可靠、操作方便、运转平稳、冷却效果好、使用寿命长、生产效率高。
关键词:
设计;整体式型芯;抽芯;推杆;注射模
Abstract
Theplasticmodelwasakindoftechnologicalequipmentorinstrumentwhichwasmadeintoparticularshapetoformplasticproductsbyspecificway.Becausethedesignandmakingofplasticdiedevelopedlatelyinourcountry,thelevelofdesigndieinourcountryisratherlowcomparedtothedevelopedcountry.Atpresentthesingleorsamplecavityoccupiesdominateposition.
ThedesignofmaterialsdesignedforABScoveraquarterofopticalinjectionmold.Mustdesignmodelsisawallthicknessisthe3mmcomponents,Becauseinmodelsaonsidetohavethelugboss,theinteriorhasthescoopchannel,thebreasthasfoureyelets,haslaterallypullsoutthecore,usestheslantingsliderodinsidetopulloutthecore,foreaseofthecoreprocessing,usestheintegraltypecore.Thedetaildeclarationfortheeveryprocesswasmainlyincludedthedeterminationofthelay-outandquantityofthecavity,thechosenoftheinjectivemachine,thedesignofthefeedinletandthecoolantsystem,theselectsofthefollowanditsstandardletter,thedesignofthesparepartfortakingshapeandsoon.Therearemanyadvantagesinthedies,suchascompact-structure,credibility-working,convenient-manipulation,steady-revolution,high-cooling-effectiveness,long-life,high-production-coefficient,andhigh-accuracy-standardandsoon.
Keywords:
Design;integraltypecore;Loosecore;Pushpole;Injectiondie
1绪论
模具是塑性成形加工方法的主要工艺装备,模具的设计与制造直接影响制件的质量以及生产效率。
20世纪发展起来并逐渐成熟的计算机辅助设计和辅助制造(CAD/CAM)技术为提高模具设计水平与制造质量和效率起到了重要作用,目前已得到广泛而深入的应用。
塑料模具是大批生产塑料制品的现代化专用成型工艺装备的总称。
塑料模具包括塑料模:
注射模、压缩模、传递模、挤出模、中空吹塑模、真空成型模等多种塑料成型模具。
在高速发展中,注射模又将其它成型模具的优点吸纳、融合和发展形成了更加完善,更加优越也更加先进的一种新型技术。
1.1模具工业在国民经济中的地位
模具是制造业的一种基本工艺装备,它的作用是控制和限制材料(固态或液态)的流动,使之形成所需要的形体。
用模具制造零件以其效率高,产品质量好,材料消耗低,生产成本低而广泛应用于制造业中。
模具工业是国民经济的基础工业,是国际上公认的关键工业。
模具生产技术水平的高低是衡量一个国家产品制造水平高低的重要标志,它在很大程度上决定着产品的质量,效益和新产品的开发能力。
振兴和发展我国的模具工业,正日益受到人们的关注。
早在1989年3月中国政府颁布的《关于当前产业政策要点的决定》中,将模具列为机械工业技术改造序列的第一位。
模具工业既是高新技术产业的一个组成部分,又是高新技术产业化的重要领域。
模具在机械,电子,轻工,汽车,纺织,航空,航天等工业领域里,日益成为使用最广泛的主要工艺装备,它承担了这些工业领域中60%~90%的产品的零件,组件和部件的生产加工。
模具制造的重要性主要体现在市场的需求上,仅以汽车,摩托车行业的模具市场为例。
汽车,摩托车行业是模具最大的市场,在工业发达的国家,这一市场占整个模具市场一半左右。
汽车工业是我国国民经济五大支柱产业之一,汽车工业重点是发展零部件,经济型轿车和重型汽车,汽车模具作为发展重点,已在汽车工业产业政策中得到了明确。
汽车基本车型不断增加,2005年将达到170种。
一个型号的汽车所需模具达几千副,价值上亿元。
为了适应市场的需求,汽车将不断换型,汽车换型时约有80%的模具需要更换。
中国摩托车产量位居世界第一,据统计,中国摩托车共有14种排量80多个车型,1000多个型号。
单辆摩托车约有零件2000种,共计5000多个,其中一半以上需要模具生产。
一个型号的摩托车生产需1000副模具,总价值为1000多万元。
其他行业,如电子及通讯,家电,建筑等,也存在巨大的模具市场。
目前世界模具市场供不应求,模具的主要出口国是美国,日本,法国,瑞士等国家。
中国模具出口数量极少,但中国模具钳工技术水平高,劳动成本低,只要配备一些先进的数控制模设备,提高模具加工质量,缩短生产周期,沟通外贸渠道,模具出口将会有很大发展。
研究和发展模具技术,提高模具技术水平,对于促进国民经济的发展有着特别重要的意义。
1.2设计内容介绍
1、四分光器的原理
四分光器作用是把入射光分为四束光,在摄影、生物技术、军事等许多领域都有重要应用。
如图1—3所示为分光器在生物技术中的应用,分光器下面的是显微镜,分光器上面的是探测器。
如果就在摄影技术中,把探测器换成摄像机,可以拍摄到绚丽的画面。
图1—3分光器的应用
其工作原理示意图、外形图和剖面图如下(图1—1,图1—2,图1—4)。
分光器是一种无源器件,它们不需要外部能量,只要有入射光即可。
一束光通过光圈1到透镜2,聚光后通过可调光圈(遮光门),再由透镜4转为平行光,平行光射到四棱镜5折射后经反光镜6反射,再通过光栅7虑光和透镜8聚光,然后通过9进入探测器或摄像机等设备。
这样就可以在9处看到四个不同的像。
1光圈;2、4、8凸透镜;3可调光圈;5棱镜;6反光镜;7光栅;9探测器
图1—1分光器工作原理示意图
图1—2分光器外形图
图1—4分光器剖面图
分光器的剖面图如下图1—4所示:
2、设计任务
本人设计的塑料件为四分光器的上盖,根据四分光器的工作原理示意图、外形图和剖面图可设计出塑件的外壳模型图,塑件图如下图1—5,图1—6所示。
塑件图1—5
塑件图1—6
1.3技术经济分析
所谓经济性就是以最小的投资获得最大的经济利益。
在产品生产过程中,经济利益是生产者首先要考虑的因素。
如何在保证产品质量,完成产品数量的情
况下,获得最大的经济利益是生产者们生产的目标。
塑料件的制造成本包括成本费、材料费、加工费(包括工人工资,车间费等)和模具费等。
产品成本受很多因素的影响,如产品的产量,材料的价格,加工的效率等。
企业要提高经济效益就要考虑很多降低成本的因素,但是在此之上的前提是一定要保证产品的质量,确保消费者的利益。
降低成本的措施包括增产和节约两个方面。
增产可以降低成本的费用,而节约更能产生直接的效果,它们都是降低成本的最重要的途径。
在此套模具中,经济问题主要出现在生产效率,模具加工费用和材料费用等等。
而实际上,平衡经济技术问题是很困难的。
例如模具的加工费用,现在越来越成为模具成本最重要的一部分。
往往,模具的材料和设计费用都比不过模具的加工费用。
本套模具考虑使用标准模架,因为标准模架本身省去了加工费用。
专业模架工厂生产的模架要比自己加工经济实惠而且精度高。
控制成型零件的加工费用便成了关键。
2塑件材料及尺寸对模具的影响
2.1塑料材料性能分析
2.1.1ABS工艺性能分析
1、使用性能:
①综合性能良好,冲击韧度、力学强度较高,且要低温下也不迅速下降。
②耐磨性、耐寒性、耐水性、耐化学性和电气性能良好。
③水、无机盐、碱、酸对ABS几乎无影响。
④尺寸稳定,易于成型和机械加工,与372有机玻璃的熔接性良好,经过调色可配成任何颜色,且可作双色成型塑件,且表面可镀铬。
2、成型性能:
①无定型塑料,其品种很多,各品种的机电性能及成型特性也各有差异,应按品种确定成型方法及成型条件。
②吸湿性强,含水量应小于0.3%,必须充分干燥,要求表面光泽的塑件应要求长时间预热干燥。
③流动性中等,溢边料0.04mm左右(流动性比聚苯乙烯、AS差,但比聚碳酸酯、聚氯乙烯好)。
④比聚苯乙烯加工困难,宜取高料温、模温(对耐热、高抗冲击和中抗冲击型树脂,料温更宜取高)。
料温对物性影响较大、料温过高易分解(分解温度为250°C左右比聚苯乙烯易分解),对要求精度较高的塑件,模温宜取50——60°C,要求光泽及耐热型料宜取60——80°C。
注射压力应比加工聚苯乙烯稍高,一般用柱塞式注塑机时料温为180——230°C,注射压力为100——140MPa,螺杆式注塑机则取160——220°C,70——100MPa为宜。
⑤易产生熔接痕,模具设计时应注意尽量减小浇注系统对斜流的阻力,模具设计时要注意浇注系统,选择好进料口位置、形式。
摧出力过大或机械加工时塑件表面呈“白色”痕迹(但在热水中加热可消失)。
⑥ABS在升温时粘度增高,塑料上的脱模斜度宜稍大,宜取1°以上。
⑦在正常的成型条件下,壁厚、熔料温度及收缩率影响极小。
3、ABS成型塑件的主要缺陷及消除措施:
主要缺陷:
缺料、气孔、飞边、出现熔接痕、塑件耐热性不高(连续工作温度为70°C左右热变形温度约为93°C)、耐气候性差(在紫外线作用下易变硬变脆)。
消除措施:
加大主流道、分流道、浇口、加大喷嘴、增大注射压力、提高模具预热温度。
2.1.2ABS主要技术指标:
表1-1热物理性能
密度(g/cm³)
1.02—1.05
比热容(J·kg-1K-1)
1255—1674
导热系数
(W·m-1·K-1×10-2)
13.8—31.2
线膨胀系数
(10-5K-1)
5.8—8.6
滞流温度(°C)
130
表1-2力学性能
屈服强度(MPa)
50
抗拉强度(MPa)
38
断裂伸长率(﹪)
35
拉伸弹性模量(GPa)
1.8
抗弯强度(MPa)
80
弯曲弹性模量(GPa)
1.4
抗压强度(MPa)
53
抗剪强度(MPa)
24
冲击韧度
(简支梁式)
无缺口
261
布氏硬度
9.7R121
缺口
11
表1-3电气性能
表面电阻率(Ω)
1.2×1013
体积电阻率(Ω·m)
6.9×1014
击穿电压(KV/mm)
\
介电常数(106Hz)
3.04
介电损耗角正切(106Hz)
0.007
耐电弧性(s)
50—85
2.1.3、ABS的注射成型工艺
1、注射成型工艺过程
(1)预烘干--→装入料斗--→预塑化--→注射装置准备注射--→注射--→保压--→冷却--→脱模--→塑件送下工序
(2)清理模具、涂脱模剂--→合模--→注射
2、ABS的注射成型工艺参数
(1)注射机:
螺杆式
(2)螺杆转速(r/min):
30——60(选30)
(3)预热和干燥:
温度(°C)80——85时间(h)2——3
(4)密度(g/cm³):
1.02——1.05(5)材料收缩率(℅):
0.3——0.8
(6)料筒温度(°C):
后段150—157中段165—180前段180—200
(7)喷嘴温度(°C):
170——180(8)模具温度(°C):
50——80
(9)注射压力(MPa):
70——100
(10)成形时间(S):
注射时间20——90高压时间0——5
冷却时间20——120总周期50——220
(11)适应注射机类型:
螺杆、柱塞均可
(12)后处理:
方法红外线灯、烘箱温度(°C)70时间(h)2——4
2.2塑件的工艺分析、确定方案
2.2.1塑件的尺寸
塑件的尺寸取决于塑料的流动性。
在一定的设备和工艺条件下,流动性好的塑料可以成型较大尺寸的塑件;反之,成型出的塑件尺寸较小。
塑件外形尺寸还受成型设备的限制。
从能源、模具制造成本和成型工艺条件出发,只要能满足塑件的使用要求,应将塑件设计得尽量紧凑、尺寸小巧一些。
2.2.2塑件的尺寸精度
影响塑件尺寸精度的因素很多,一般认为,其中的模具制造误差、塑料的收缩率的波动引起的误差以及由模具的磨损、变形、热膨胀造成的误差各占塑件尺寸误差的1/3。
实际上,对于小尺寸的塑件,模具制造误差对塑件尺寸的影响大一些;而对于大尺寸的塑件,收速率波动引起的误差则是影响塑件尺寸精度的主要因素。
在此零件中,因为塑料尺寸较小,大多数部位都采用厚度为3mm的形式,,而高度为52mm,因此影响零件尺寸精度的因素主要有是模具原因和塑料原因。
模具加工的精度,对零件尺寸影响最大,模具精度高,零件的尺寸保持就好,相反,模具精度低,模具局部尺寸就不易保持。
模具结构形式和基本结构也是模具影响塑料件尺寸精度的重要原因。
塑料件个部分之间尺寸不是很大,有的部分甚至直接相连,因此模具的型芯不适合采用分开的拼装式结构,而采用型芯的整体成型方法,这就有会反馈到模具的加工精度的问题上。
整体加工为了保证其经济性和适用性,目前大多数采用数控中心自动加工或利用电极进行电蚀加工。
两种方法中,各部分之间的配合公差和共同基准的选择,都较拼装式的型腔有了提高。
塑料的因素也是影响塑件尺寸精度的重要原因。
ABS的收缩率比较小,因此塑料的原因不是特别明显。
只要保证模具成型部分尺寸的均匀性,使塑件收缩时均匀进行,可以保证其较小的变形率。
还有几个次要原因,即和成型工艺有关的原因和和成型后时效有关的原因。
例如由于成型条件变化造成的收缩率的波动、脱模顶出时的塑料变形、弹性恢复、残余应力、残余变形引起的变化等,由于对于此零件来说,其影响不是很大,因此可以此要考虑。
在成型工艺设计中,只要保证零件顶出力均匀,在冷却适当时才进行脱模,就可以忽略此种原因产生的影响。
2.2.3脱模斜度
由于塑料冷却后,产生收缩,会使塑件紧紧包住模具型芯或模具型腔中凹进的部分,为了使塑件易于从模具中脱出,并且避免脱模时拉伤或擦伤塑件,因此,在设计塑件时必须考虑到塑件内外表面沿脱模方向均应有足够的脱模斜度。
经查表得出,ABS的拔模斜度为40′~1°30′,经思考后,模具用脱模斜度为1°
3注塑成型的准备
3.1注塑成型工艺简介
注塑成型是利用塑料的可挤压性与可模塑性,首先将松散的粒状或粉状成型物料从注塑机的料斗送入高温的机筒内加热熔融塑化,使之成为粘流状态熔体,然后在柱塞或螺杆的高压推动下,以很大的流速通过机筒前端的喷嘴注射进入温度较低的闭合模具中,经过一段时间的保压冷却以后,开启模具便可以从模腔中脱出具有一定形状和尺寸的塑料制件。
一般分为三个阶段的工作,如图3—1所示
图3-1注塑成型压力—时间曲线
(1)物料准备;成型前应对物料的外观色泽、颗粒情况,有无杂质等进行检验,并测试其热稳定性,流动性和收缩率等指标。
对于吸湿性强的塑料,应根据注射成型工艺允许的含水量进行适当的预热干燥,若有嵌件,还要知道嵌件的热膨胀系数,对模具进行适当的预热,以避免收缩应力和裂纹,有的塑料制品还需要选用脱模剂,以利于脱模。
(2)注塑过程;塑料在料筒内经过加热达到流动状态后,进入模腔内的流动可分为注射,保压,倒流和冷却四个阶段,注塑过程可以用如图所示3.1所示。
图中T0代表螺杆或柱塞开始注射熔体的时刻;当模腔充满熔体(T=T1)时,熔体压力迅速上升,达到最大值P0。
从时间T1到T2,塑料仍处于螺杆(或柱塞)的压力下,熔体会继续流入模腔内以弥补因冷却收缩而产生的空隙。
由于塑料仍在流动,而温度又在不断下降,定向分子(分子链的一端在模腔壁固化,另一端沿流动方向排列)容易被凝结,所以这一阶段是大分子定向形成的主要阶段。
这一阶段的时间越长,分子定向的程度越高。
从螺杆开始后退到结束(时间从T2到T3),由于模腔内的压力比流道内高,会发生熔体倒流,从而使模腔内的压力迅速下降。
倒流一直进行到浇口处熔体凝结时为止。
其中,塑料凝结时的压力和温度是决定塑料制件平均收缩率的重要因素。
(3)制件后处理;由于成型过程中塑料熔体在温度和压力下的变形流动非常复杂,再加上流动前塑化不均匀以及充模后冷却速度不同,制件内经常出现不均匀的结晶、取向和收缩,导致制件内产生相应的结晶、取向和收缩应力,脱模后除引起时效变形外,还会使制件的力学性能,光学性能及表观质量变坏,严重时会开裂。
故有的塑件需要进行后处理,常用的后处理方法有退火和调湿两种。
退火是为了消除或降低制件成型后的残余应力,此外,退火还可以对制件进行解除取向,并降低制件硬度和提高韧性,温度一般在塑件使用温度以上的10~20度至热变形温度以下10~20度之间;调湿处理是一种调整制件含水量的后处理工序,主要用于吸湿性很强、而且又容易氧化的聚酰胺等塑料制件.调湿处理所用的加热介质一般为沸水或醋酸钾溶液(沸点为121℃,加热温度为100~121℃,保温时间与制件厚度有关,通常取2~9小时)。
3.2注塑成型工艺条件
1)温度;注塑成型过程中需要控制的温度有料筒温度,喷嘴温度和模具温度等。
喷嘴温度通常略微低于料筒的最高温度,以防止熔料在直通式喷嘴口发生“流涎现象”;模具温度一般通过冷却系统来控制;为了保证制件有较高的形状和尺寸精度,应避免制件脱模后发生较大的翘曲变形,模具温度必须低于塑料的热变形温度。
2)压力;注射成型过程中的压力包括注射压力,保压力和背压力。
注射压力用以克服熔体从料筒向型腔流动的阻力,提供充模速度及对熔料进行压实等。
保压力的大小取决于模具对熔体的静水压力,与制件的形状,壁厚及材料有关。
对于像ABS流动性好的料,保压力应该小些,以避免产生飞边,保压力可取略低于注射压力。
背压力是指注塑机螺杆顶部的熔体在螺杆转动后退时所受到的压力,背压力除了可驱除物料中的空气,提高熔体密实程度之外,还可以使熔体内压力增大,螺杆后退速度减小,塑化时的剪切作用增强,摩擦热量增大,塑化效果提高,根据生产经验,背压的使用范围约为3.4~27.5MPA。
3)时间;完成一次注塑成型过程所需要的时间称为成型周期。
包括注射时间,保压时间,冷却时间,其他时间(开模,脱模,涂脱磨剂,安放嵌件和闭模等),在保证塑件质量的前提下尽量减小成型周期的各段时间,以提高生产率,其中,最重要的是注射时间和冷却时间,在实际生产中注射时间一般为3~5秒,保压时间一般为20~120秒,冷却时间一般为30~120秒(这三个时间都是根据塑件的质量来决定的,质量越大则相应的时间越长)。
确定成型周期的经验数值如表3-2所示。
表3-2成型周期与壁厚关系
制件壁厚/mm
成型周期/s
制件壁厚/mm
成型周期/s
0.5
10
2.5
35
1.0
15
3.0
45
1.5
22
3.5
65
2.0
28
4.0
85
3.0
34
4.5
105
3.3注塑机的选择
3.3.1注塑机简介
1956年制造出世界上第一台往复螺杆式注塑机,这是注塑成型工艺技术的一大突破,目前注塑机加工的塑料量是塑料产量的30%;注塑机的产量占整个塑料机械产量的50%.成为塑料成型设备制造业中增长最快,产量最多的机种之一.
注塑机的分类方式很多,目前尚未形成完全统一标准的分类方法.常用的说法有:
(1)按设备外形特征分类:
卧式,立式,直角式,多工位注塑机;
(2)按加工能力分类:
超小型,小型,中型,大型和超大型注塑机。
此外还有按用途分类和按合模装置的特征分类,但日常生活中用的较少。
3.3.2注塑机基本参数
注塑机的主要参数有公称注射量,注射压力,注射速度,塑化能力,锁模力,合模装置的基本尺寸,开合模速度,空循环时间等.这些参数是设计,制造,购买和使用注塑机的主要依据.
(1)公称注塑量;指在对空注射的情况下,注射螺杆或柱塞做一次最大注射行程时,注射装置所能达到的最大注射量,反映了注塑机的加工能力.
(2)注射压力;为了克服熔料流经喷嘴,浇道和型腔时的流动阻力,螺杆(或柱塞)对熔料必须施加足够的压力,我们将这种压力称为注射压力.
(3)注射速率;为了使熔料及时充满型腔,除了必须有足够的注射压力外,熔料还必须有一定的流动速率,描述这一参数的为注射速率或注射时间或注射速度.
常用的注射速率如表3-4所示。
表3-4注射量与注射时间的关系
注射量/CM
125250500100020004000600010000
注射速率/CM/S125200333570890133016002000
注射时间/S11.251.51.752.2533.755
(4)塑化能力;单位时间内所能塑化的物料量.塑化能力应与注塑机的整个成型周期配合协调,若塑化能力高而机器的空循环时间长,则不能发挥塑化装置的能力,反之则会加长成型周期.
(5)锁模力;注塑机的合模机构对模具所能施加的最大夹紧力,在此力的作用下模具不应被熔融的塑料所顶开.
(6)合模装置的基本尺寸;包括模板尺寸,拉杆空间,模板间最大开距,动模板的行程,模具最大厚度与最小厚度等.这些参数规定了机器加工制件所使用的模具尺寸