砂的含泥量及泥块含量测定.docx
《砂的含泥量及泥块含量测定.docx》由会员分享,可在线阅读,更多相关《砂的含泥量及泥块含量测定.docx(23页珍藏版)》请在冰豆网上搜索。
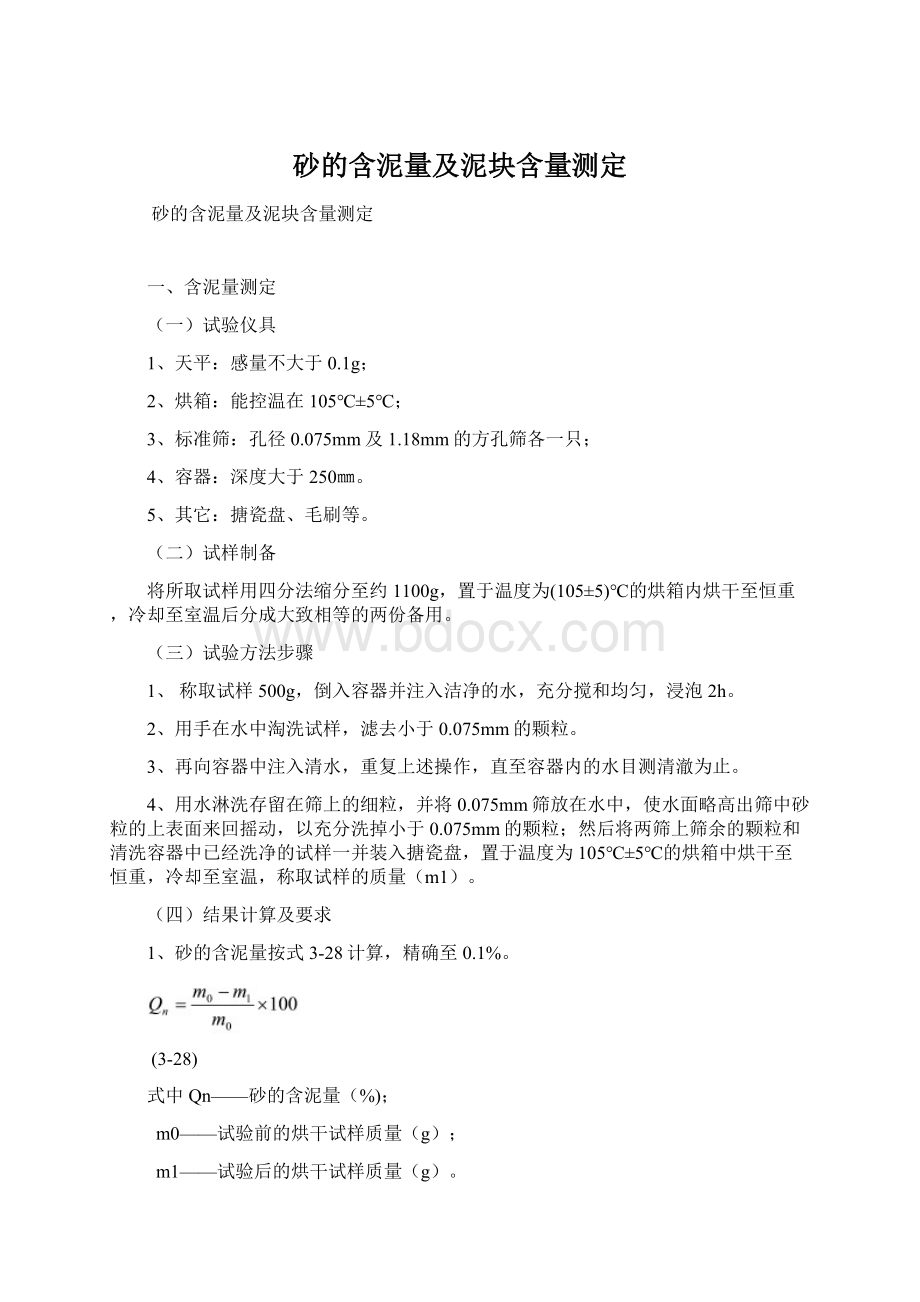
砂的含泥量及泥块含量测定
砂的含泥量及泥块含量测定
一、含泥量测定
(一)试验仪具
1、天平:
感量不大于0.1g;
2、烘箱:
能控温在105℃±5℃;
3、标准筛:
孔径0.075mm及1.18mm的方孔筛各一只;
4、容器:
深度大于250㎜。
5、其它:
搪瓷盘、毛刷等。
(二)试样制备
将所取试样用四分法缩分至约1100g,置于温度为(105±5)℃的烘箱内烘干至恒重,冷却至室温后分成大致相等的两份备用。
(三)试验方法步骤
1、称取试样500g,倒入容器并注入洁净的水,充分搅和均匀,浸泡2h。
2、用手在水中淘洗试样,滤去小于0.075mm的颗粒。
3、再向容器中注入清水,重复上述操作,直至容器内的水目测清澈为止。
4、用水淋洗存留在筛上的细粒,并将0.075mm筛放在水中,使水面略高出筛中砂粒的上表面来回摇动,以充分洗掉小于0.075mm的颗粒;然后将两筛上筛余的颗粒和清洗容器中已经洗净的试样一并装入搪瓷盘,置于温度为105℃±5℃的烘箱中烘干至恒重,冷却至室温,称取试样的质量(m1)。
(四)结果计算及要求
1、砂的含泥量按式3-28计算,精确至0.1%。
(3-28)
式中Qn——砂的含泥量(%);
m0——试验前的烘干试样质量(g);
m1——试验后的烘干试样质量(g)。
2、以两个试样试验结果的算术平均值作为测定值。
两次结果的差值超过0.5%时,应重新取样进行试验。
试验数据记录及结果处理见表3-66。
二、泥块含量测定
(一)试验仪具
1、天平:
称量1kg(感量不大于0.1g);
2、烘箱:
控温在105℃±5℃;
3、标准筛:
孔径0.6mm及1.18mm的方孔筛各一只;
4、容器:
深度大于250㎜。
5、其它:
搪瓷盘、毛刷等
(二)试样制备
将试样用四分法缩分至约5000g,并置于箱内烘干至恒重,冷却至室温,筛除小于1.18㎜的颗粒,相等的两份备用。
(三)试验方法步骤
1、称取试样200g,倒入淘洗容器中,注入洁净的水,浸泡24h,用水淘洗,直至容器内的水目测清澈为止。
2、保留下来的试样小心地从筛中取出,装入浅盘后,置于温度为105℃±5℃的烘箱中烘干至恒重,冷却至室温,称取试样的质量(m1)。
(四)结果计算及要求
1、砂的泥块含量按式3-29计算,精确至0.1%。
(3-29)
式中Qn——砂的泥块含量(%);
m0—试样在1.18㎜筛的筛余质量,单位g;
m1—试验后试样的烘干质量,单位g。
试验次数
试验前的烘干试样质量m0(g)
试验后的烘干试样质量m1(g)
砂的含泥量Qn(%)
个别值
平均值
1
2
2、以两个试样试验结果的算术平均值作为测定值,精确0.1%。
试验数据记录及结果处理见表3-67。
任务二水泥混凝土用砂石的颗粒级配试验
一、细集料的筛分析试验
(一)试验仪具与材料
1、方孔筛:
规格为0.15㎜、0.3㎜、
0.6㎜、1.18㎜、2.36㎜、4.75㎜、9.50㎜的标准筛各一只,并附有底盘和筛盖。
2、天平:
称量1Kg,感量1g。
3、烘箱:
能控温在105℃±5℃。
4、其它:
搪瓷浅盘和软硬毛刷等。
表3-68砂的公称粒径、砂筛筛孔的公称直径和方孔筛筛孔边长尺寸间关系
砂的公称粒径
砂筛筛孔的公称直径
方孔筛筛孔边长
5.0㎜
5.0㎜
4.75㎜
2.50㎜
2.50㎜
2.36㎜
1.25㎜
1.25㎜
1.18㎜
0.63㎜
0.63㎜
0.60㎜
0.315㎜
0.315㎜
0.30㎜
0.16㎜
0.16㎜
0.15㎜
0.08㎜
0.08㎜
0.075㎜
(二)试样准备
1、按模块一工作单元任务一的有关要求取样。
筛除大于9.5
的颗粒,并算出其筛余百分率。
2、将试样缩分至约1100g,置于105℃±5℃的烘箱中烘至恒重,冷却至室温后,分为大致相等的两份备用。
(三)试验步骤
1、组装标准筛。
2、准确称取烘干试样约500g,倒入套筛上,盖好筛盖。
3、取下套筛,逐个用手筛,直至每分钟的筛出量不超过试样总量的0.1%时为止,直至各号筛全部筛完为止。
4、称取各筛筛余质量,准确至1g。
试样在各号筛上的筛余量不得超过按下式3-1计算出的量
(3-30)
式中G——在一个筛上的筛余量,g。
A——筛面面积,㎜2;
D——筛孔尺寸,㎜。
(四)筛分结果有效性判断、试验数据计算和评价
1、单次筛分结果有效性判断
计算筛分后所有各筛和筛底盘上剩余量之和(
),与筛分前砂样总质量(
)相比较:
若
≥1%,单次筛分无效,需要重新取样筛分;
若
<1%,单次筛分有效,接续计算以下各筛分参数:
※分计筛余百分率(
)、
※累计筛余百分率(
)
※通过量百分率(
)
(2)计算细度摸数:
精确至0.01:
(3-31)
2、砂样平行两次有效筛分后,最终筛分结果有效性判断
(1)计算两次筛分结果的细度模数差(
),若差值小于0.2,则砂样筛分结果的细度模数取两次试验结果的算术平均值(
),精确至0.1;如两次试验的细度模数之差超过0.20时,需增加试验次数,重新取样继续筛分。
1、用计算的
平均值判断砂的粗细;按两次有效筛分在0.6㎜筛上的累计筛余百分率的平均值判断砂所属级配区;按对应级配区各筛上的通过率规定范围值,分析判断砂样是否满足规范要求。
试验数据纪录及结果评价见表3-69。
二、粗集料的筛分析试验
(一)试验仪具
1、方孔筛:
2.36㎜、4.75㎜、9.50㎜、16.0㎜、19.0㎜、26.5㎜、31.5㎜、37.5㎜、53.0㎜、63.0㎜、75.0㎜、90㎜的筛各一只,并附有筛底和筛盖。
2、天平或台秤:
称量10Kg,感量1g。
3、烘箱:
能使温度控制在105℃±5℃。
4、其它:
浅盘、铲子、毛刷等。
(二)试验准备
将从施工现场取来的试样充分拌匀,用分料器或四分法缩分至表3-70要求的试样所需量两份,烘干或风干后备用。
表3-70粗集料不同粒径下的最少取样量(Kg)
最大粒径(mm)
75.0
63.0
37.5
31.5
26.5
19.0
16.0
9.5
最少试样质量(Kg)
16.0
12.6
7.5
6.3
5.0
3.8
3.2
1.9
(三)试验步骤
1、称取规定数量的试样一份,倒入套筛(附筛底)上,然后进行筛分。
2、先手摇筛分,然后逐个用手筛分,筛至每分钟通过量小于试样总量0.1%为止。
【注】当筛余颗粒的粒径大于19.0㎜时,在筛分过程中,允许用手指拨动颗粒。
3、称取各筛上的筛余质量,准确至1g;
4、筛分结果有效性判断及筛分参数计算:
(1)单次筛分有效性判断
判断方法与细集料相同。
当单次筛分有效时,计算筛分参数分计筛余百分率、累计筛余百分率和通过量百分率。
(2)根据各号筛的累计筛余百分率,对照规范要求评定该试样的颗粒级配。
试验数据记录及结果处理见表3-71.
表3-71粗集料筛分试验记录表
筛孔尺寸(mm)
各筛存留质量(g)
分计筛余(%)
累计筛余(%)
通过率(%)
试样1
试样2
平均
63.0
53.0
37.5
…
9.5
4.75
2.36
任务三粗集料中针片状颗粒的总含量测定
一、试验仪具
1、水泥混凝土用粗集料针、片状规准仪,如图3-25、3-26所示,其尺寸应符合表3-72的要求。
图3-25针状颗粒规准仪
图3-26片状颗粒规准仪
表3-72针状和片状颗粒的总含量试验的粒级划分及其相应的规准仪孔宽或间距
公称粒级(mm)
5.00~10.0
10.0~16.0
16.0~20.0
20.0~25.0
25.0~31.5
31.5~40.0
片状规准仪上
相对应的孔宽(mm)
2.8
5.1
7.0
9.1
11.6
13.8
针状规准仪上相对应的立柱间距
17.1
30.6
42.0
54.6
69.6
82.8
2、天平和台秤:
天枰,称量2㎏,感量2g;台秤,称量20㎏,感量20g。
3、试验筛:
筛孔公称直径分别为5.0
、10.0
、20
、25
、31.5
、40
、63.0㎜和80.0㎜的方孔筛各一只,据需要选用。
4、卡尺
二、试样制备
将来样在室内风干至表面干燥,并缩分至表3-73规定的数量,称量质量为
,然后筛分成规定的粒级备用。
表3-73针状和片状颗粒的总含量试验所需的试样最小质量
最大公称粒径(mm)
10
16.0
20.0
25.0
31.5
≥40
试样最小质量(Kg)
0.3
1
2
3
5
10
三、试验步骤
1、按表所规定的粒级用规准仪逐粒对试样进行鉴定,凡颗粒长度大于针状规准仪上相应间距的,为针状颗粒;厚度小于片状规准仪上相应孔宽的,为片状颗粒。
2、公称粒径大于40㎜的可用卡尺鉴定其针片状颗粒,卡尺卡口的设定宽度应符合下列表3-74的规定。
表3-74公称粒径大于40㎜用卡尺卡口的设定宽度
公称粒径(mm)
40.0~63.0
63.0~80.0
片状颗粒的卡口宽度(mm)
18.1
27.6
针状颗粒的卡口宽度(mm)
108.6
165.6
3、称量由各粒级挑选出的针状和片状颗粒的总量
,g。
四、试验数据记录及结果处理
碎石或卵石针、片状颗粒含量按式3-32计算:
(3-32)
式中
—碎石或卵石针、片状颗粒含量。
—试样的质量,g。
—试样所含针、片状颗粒的总质量,g。
任务四粗集料的压碎值测定
一、试验仪具设备
1、压力试验机:
荷载在300KN。
2、压碎指标值测定仪,如图3-27所示。
图3-27压碎指标值测定仪
1-圆筒;2-底盘;3-加压头;4-手把;5-把手
3、天平或台秤:
称量5Kg,感量不大于5
。
4、试验筛:
孔径公称直径分别为2.5
、10
、20
各一只及筛盖和底盘。
二、制备试样
1、通过筛分取10~20
的颗粒为标准试样,并保持在气干状态下进行试验。
2、对多种岩石组成的卵石,当其公称粒径大于20.0㎜颗粒的岩石矿物成分与10.0㎜~20.0
㎜粒级有显著差异时,应将大于20.0㎜的颗粒经人工破碎后,筛取10.0㎜~20.0㎜标准粒级另外进行压碎值指标试验。
3、剔除针、片状颗粒:
用针、片状规准仪剔除试样中的针、片状颗粒,然后称取每份约3Kg的
试样3份备用。
三、试验步骤
1、装料:
取试样1份,分两层装入筒内,每装完一层试样后,在底盘下面垫放一根直径为10
的圆钢筋,将筒按住,左右交替颠击地面各25次;第二层颠实后,试样表面距离底盘的高度应控制在100
左右。
2、测定:
整平筒内试样表面,把加压头装好(注意应使加压头保持平正),放到试验机上,在160S~300s内均匀加荷至200KN,稳定5S,卸荷,取出测定筒。
5、称重:
倒出筒中的试样称其质量
,g。
6、过筛:
用公称直径为2.5
的标准方孔筛筛出被压碎的细粒,称出剩余在筛上的试样质量
,g。
四、结果计算及要求
1、碎石或砾石的压碎指标值按式3-33计算:
(3-33)
式中
——压碎值,%。
—试验用试样的总质量,g;
—试验后存留在2.5
筛上的筛余质量,g。
2、对于多种岩石组成的卵石,应对公称粒径20.0
以下和20.0
以上的标准粒级(10.0
~20.0
)分别进行检验,则其总的压碎值
按式3-34计算:
3、以三次平行试验结果的算术平均值作为压碎值指标的测定值。
试验数据记录及结果处理见表3-75。
表3-75粗集料压碎值试验记录
试验次数
试验用试样总质量
(
)
试验后在2.5mm筛上的
存留质量
(
)
压碎值
个别值
平均值
1
2
3
任务五水泥混凝土的拌制、表观密度及和易性测定
一、混凝土的拌制
(一)试验仪具设备
1、混凝土搅拌机:
容量30~100L,转速18~22r/min。
如图3-28所示。
图3-28混凝土强制式搅拌机
2、台秤:
称量50Kg,感量50g。
3、天平:
称量5Kg,感量1g。
4、其它:
拌板、抹刀、量筒、拌铲、坍落度尺子等。
(二)试验步骤
1、人工拌和
(1)称料按设计配合比将所需的材料分别称好装在各盛料器中。
(2)润湿用具将拌板和铁锹等接触混凝土拌和物的用具用湿抹布搽湿。
(3)干拌先将砂倒在拌板上,然后加入水泥,用拌铲自拌板一端翻拌至另一端,直至充分混合,颜色均匀一致。
再加入石子翻拌混合均匀为止。
(4)加水湿拌将干拌和物堆成长堆,中心扒一凹槽,将已称量好的水一半左右倒入凹槽中,仔细翻拌;然后再将拌和物堆成长堆,扒一凹槽,倒入剩余的水,翻拌至少6遍。
从加水完毕时起的拌和时间应满足表3-78的要求。
表3-78混凝土拌和物的拌和时间
拌和物体积(L)
拌和时间(min)
30
4~5
31~50
5~9
51~75
9~12
2、机械搅拌法
(1)称料按设计配合比将所需的材料分别称好装在各盛料器中,砂石集料以全干状态为准。
(2)涮膛拌制前先对混凝土搅拌机挂浆,即用按配合比要求的水泥、砂、水和少量石子,在搅拌机中涮膛,然后倒去多余砂浆。
(3)干拌将称好的石子、砂、水泥按顺序倒入搅拌机内,干拌均匀。
(4)湿拌将需用的水徐徐倒入搅拌机内一起拌和,全部加料时间不得超过2min。
(5)人工拌和将拌和物自搅拌机中卸出,倾倒在拌板上,再经人工拌和1~2min。
拌好后,根据试验要求,即可做坍落度测定或试件成型。
从开始加水时算起,全部操作须在30min内完成。
二、混凝土拌和物和易性试验
一)坍落度法
(一)主要仪器设备
1、坍落度筒、坍落度尺子、弹头捣棒、加料漏斗,见图3-29。
图3-29坍落度筒、捣棒、坍落度尺子
2、小铲、拌板、抹刀等。
(二)试验步骤
1、润湿
测定前,用湿布润湿坍落筒及其他各种拌合用具。
2、装料、插捣
混凝土拌合物分三层装入坍落度筒内,每层装入高度约为筒高的l/3。
用捣棒在每一层的横截面上沿螺旋线由边缘至中心在全面积上均匀插捣25次。
底层要插至拌板,其它两层应插透本层并至下层约20㎜~30mm。
捣棒须垂直压下(边缘部分除外),不得冲击。
插捣时应注意评定拌和物的棍度情况,评定方法详见表3-74。
3、抹平、提筒、量高
顶层插捣完毕后,用捣棒以锯和割的动作清除多余混凝土,用抹刀抹平拌合物与坍落度筒口一齐。
抹平过程须评定拌和物的含砂情况,评价方法见表3-74。
刮净筒底周围的拌和物,在5~l0S内垂直提起坍落筒。
从开始装筒到提起坍落度筒的全过程,不应超过2.5min。
用坍落度尺子立即测出筒高与坍落后的混凝土拌合物试体最高点的高度差,即为该拌和物的坍落度,精确至5
。
量取方法见图3-30。
4、坍落度试验结果确定
以两次测定结果的平均值作为测定值。
若两次结果相差20
以上须作第三次试验,第三次与前两次结果均相差20
以上时,整个试验重作。
5、粘聚性和保水性的目测评定
在测定坍落度评价混凝土流动性的同时,采取目测等办法直观评价拌合物的粘聚性和保水性。
评价办法见表3-79。
(四)和易性的调整
1、当坍落度小于设计要求时,保持水胶比不变,适当增加水胶浆用量,其增加数量可据测定值与设计值之差确定,通常每增大20㎜坍落度,需增加5%~10%的水胶浆。
2、当坍落度高于设计要求时,可在保持砂率不变的条件下,增加骨料用量。
3、当出现含砂不足,粘聚性、保水性不良时,可适当增大砂率,反之减小砂率。
当拌合物的流动性、黏聚性和保水性均满足设计要求时,混凝土拌合物的和易性评价为合格。
坍落度试验记录及结果处理见表3-80。
表3-80混凝土拌和物坍落度试验记录表
拌和15L混凝土各种材料用量
坍落度值(mm)
试验
次数
胶凝材料用量(㎏)
砂重(kg)
石子(kg)
用水量(kg)
水泥重(kg)
矿物掺合料重(㎏)
个别值
平均值
1
2
二)维勃稠度法
(一)主要仪器设备
维勃稠度仪(见图3-31)、捣棒、小铲等。
(二)试验步骤
1、把维勃稠度仪放置在坚实的操作台上,用湿布把容器、坍落度筒、喂料斗内壁及其它用具擦湿。
2、将喂料斗提到坍落度筒上方扣紧,校正容器位置,使其中心与喂料斗中心重合,然后拧紧固定螺丝。
3、把混凝土拌合物用小铲分三层经喂料斗均匀地装入筒内,装料及插捣方式同坍落度法。
图3-31维勃稠度仪
4、将圆盘、喂料斗都转离坍落度筒,小心并垂直地提起坍落度筒,
提筒时要注意不能使混凝土试体产生横向扭动。
把透明圆盘转动到混凝土圆台体顶面,放松测杆螺丝,小心地降下圆盘,使它轻轻地接触到混凝土顶面。
5、拧紧定位螺丝,并检查测杆螺丝是否完全放松,同时开启振动台和计时器,当振动到透明圆盘的底面被水泥浆布满的瞬间,关闭振动台,停止计时。
(三)试验结果确定
由计时器读出振动台振动的时间,单位为秒,S,即为该混凝土拌合物的维勃稠度值。
如维勃稠度值小于5S或大于30S,则此种混凝土所具有的稠度已超出本仪器的适用范围,不能用维勃稠度值表示。
试验记录及结果处理见表3-81.
三、混凝土拌合物毛体积密度测定
一)试验仪器
1、量筒:
2、弹头形捣棒:
同坍落度试验用捣棒。
3、磅秤:
称量100kg、感量50g。
4、振动台:
频率为(50±3)HZ,空载时的振幅应为0.5㎜±0.1㎜
5、其它:
金属直尺、镘刀、玻璃板等。
二)试验步骤
(一)容量筒容积的校正
用一块较容量筒口稍大的玻璃板,先称量出玻璃板和空筒的质量,然后向容量筒中灌入清水,灌到接近上口时一边不断加水,一边把玻璃板沿筒口徐徐推入盖严,应注意使玻璃板下不带入任何气泡。
然后擦净玻璃板面和筒壁外的水分,将容量筒连同玻璃板放在台秤上称量。
两次称量之差(以kg计)即为容量筒的容积。
(二)毛体积密度测定
1、人工振捣法测定——适用于测定坍落度不小于70
拌和物的毛体积密度测定。
(1)称筒重用湿布将量筒内外擦净,称出质量m1。
(2)装拌合物试样分三层装入量筒,每层捣实后的高度约为1/3筒高。
用捣棒从边缘到中心沿螺旋线均匀插捣,每层插捣25次,捣底层时应捣至筒底,捣上两层时须插入其下一层约20~30
。
每捣完一层,应在量筒外壁拍打10~15次,直至拌和物表面不出现气泡为止。
(3)抹平仔细用抹刀抹平坍落度筒表面,将溢至筒外壁的拌和物擦净并称其质量m2(精确至50g)。
2、机械振捣测定——适用于测定坍落度小于70mm混凝土的毛体积密度测定。
(1)称筒重用湿布将量筒内外擦净并称其质量m1。
(2)装拌合物将量筒在振动台上夹紧,一次性将拌和物装满量筒,立即开机振动,随时添加拌和物,直至拌和物表面出现浆体为止。
(3)振动、抹平从振动台上取下量筒,刮去多余混凝土,仔细用抹刀抹平表面,将溢至筒外壁的拌和物擦净,称筒及拌合物总重m2(精确至50g)。
三)结果计算及要求
1、毛体积密度按式3-35计算
(3—35)
2、以两次试验结果的算术平均值作为测定值,试样不得重复使用。
试验数据记录及结果处理见表3-82。
表3-82水泥混凝土拌合物毛体积密度试验记录
试验次数
容量筒体积
V(l)
容量筒质量
m1(Kg)
容量筒和混凝土质量m2(Kg)
混凝土质量
(m2-m1)(Kg)
混凝土拌和物密度
ρh(Kg/l)
个别值
平均值
任务六混凝土抗压强度试验
一、混凝土的取样
1、每拌制100盘且不超过100m3的同配合比混凝土,取样次数不应少于一次;
2、每一工作班拌制的同配合比混凝土,不足100盘或100m3时,取样次数不应少于一次;
3、每一次连续浇筑的同配合比混凝土超过1000m3时,每200m3取样不应少于一次;
4、对房屋建筑,每一楼层、同一配合比的混凝土,取样不应少于一次;
5、每次取样应至少留置一组标准养护试件,用于检验结构或构件施工阶段的混凝土强度。
同条件养护试件的留置组数应根据实际需要确定。
二、混凝土试件的成型和养护
一)试验仪具
1、混凝土振实台,如图3-32所示。
图3-32混凝土试件成型用振动台
2、混凝土标准试模:
如图3-33所示,为铸铁或钢制成。
可以拆卸擦洗,内部尺寸允许偏差为:
棱长不超过1
,直角则不超过0.5°。
图3-33混凝土标准立方体试模
3、其它:
拌铲、抹刀、捣棒等。
二)试验步骤
1、选择试模
根据所要测定的混凝土的技术性质,考虑集料的最大粒径,按表3-83的要求选择。
表3-83混凝土试摸选择表
试验名称
试模内部尺寸(
)
集料最大粒径(
)
抗压强度
标准尺寸
150×150×150
40
非标准尺寸
200×200×200
30
100×100×100
60
2、成型试件
混凝土标准试件的成型方式按坍落度选择,见表3-84。
表3-84拌和方式的选择
成型方式
混凝土的坍落度(单位:
mm)
机械成型
<70
人工成型
≥70
(1)机械成型
采用标准振动台成型。
试模放在振动台上夹紧,将试模内部涂一薄层矿物油脂或脱模剂,将和易性已满足要求的拌和物一次装满试模并使其稍高出模顶。
开动振动台振动至表面呈现水泥浆为止。
振动过程中随时添加混凝土拌和物使试模常满,记录振动时间(一般不超过90s)。
振动结束后,用金属直尺沿试模边缘刮去多余的混凝土,用镘刀将试件表面初次抹平,待试件收浆后(经2~4h),再次用抹刀将试件仔细抹平。
【技术提示】试件表面与试模边缘的高差不得超过0.5㎜。
(2)人工成型
将和易性满足要求的混凝土拌和物分大致相等的两层装入试模,每层插捣次数如表3-85的规定。
表3-85人工成型插捣次数
试件尺寸(mm)
每层插捣的次数
100×100×100
12
150×150×150
25
200×200×200
50
插捣时按螺旋线方向从边缘到中心均匀地插捣。
插捣底层时,捣棒到达模底,插捣上层时,捣棒插入该层底面下20㎜~30
处。
插捣时用力将捣棒压下,不得冲击,捣完最后一层时,表面若有凹陷应予以填平,抹平试件表面。
三、混凝土试件的养护
1、成型初期养护
试件成型后,用湿布覆盖表面或采取其它的保湿方法保湿,以防水分蒸发,