精品完整版计算流体动力学和动态耦合热力学中英文资料外文翻译文献.docx
《精品完整版计算流体动力学和动态耦合热力学中英文资料外文翻译文献.docx》由会员分享,可在线阅读,更多相关《精品完整版计算流体动力学和动态耦合热力学中英文资料外文翻译文献.docx(24页珍藏版)》请在冰豆网上搜索。
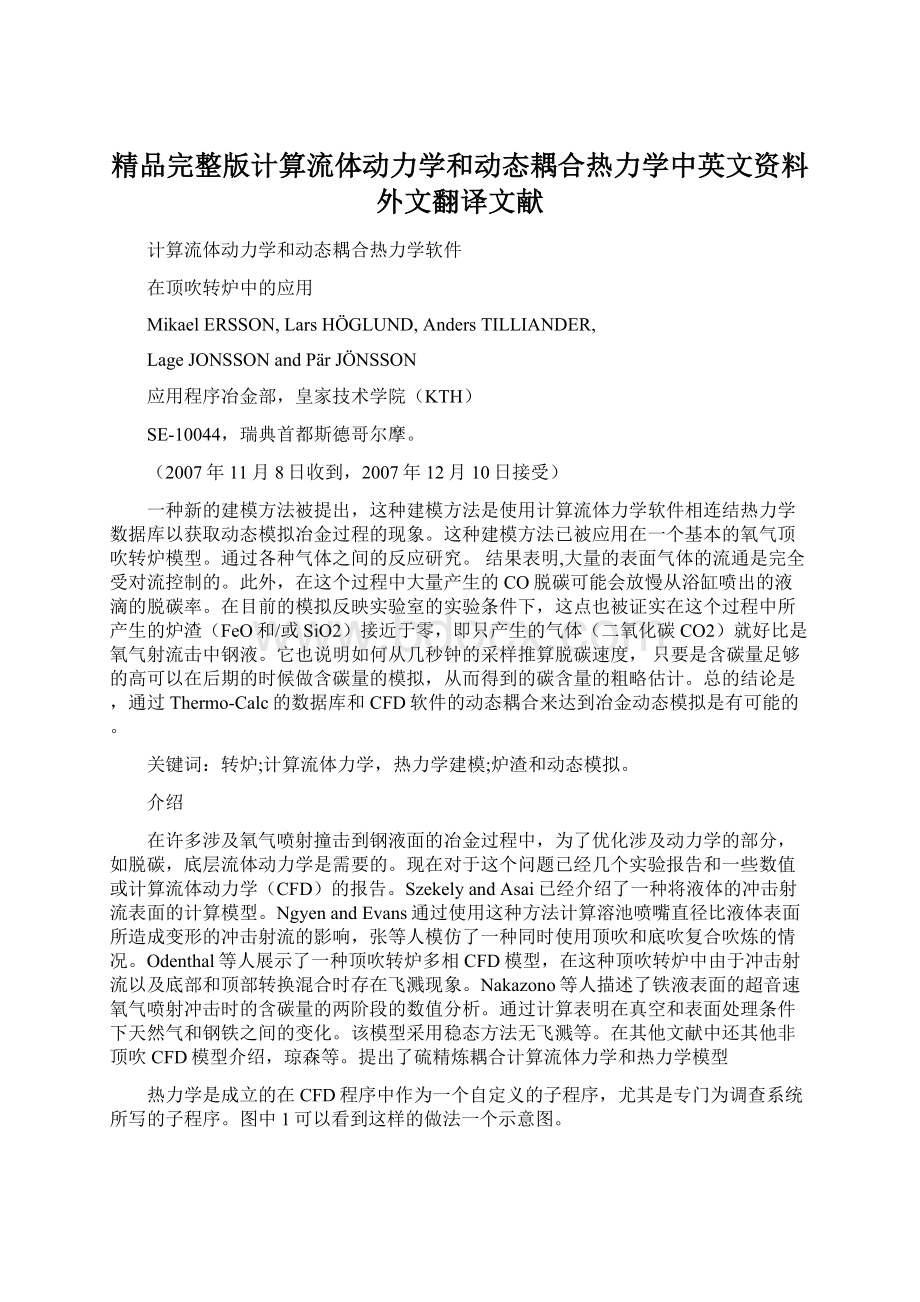
精品完整版计算流体动力学和动态耦合热力学中英文资料外文翻译文献
计算流体动力学和动态耦合热力学软件
在顶吹转炉中的应用
MikaelERSSON,LarsHÖGLUND,AndersTILLIANDER,
LageJONSSONandPärJÖNSSON
应用程序冶金部,皇家技术学院(KTH)
SE-10044,瑞典首都斯德哥尔摩。
(2007年11月8日收到,2007年12月10日接受)
一种新的建模方法被提出,这种建模方法是使用计算流体力学软件相连结热力学数据库以获取动态模拟冶金过程的现象。
这种建模方法已被应用在一个基本的氧气顶吹转炉模型。
通过各种气体之间的反应研究。
结果表明,大量的表面气体的流通是完全受对流控制的。
此外,在这个过程中大量产生的CO脱碳可能会放慢从浴缸喷出的液滴的脱碳率。
在目前的模拟反映实验室的实验条件下,这点也被证实在这个过程中所产生的炉渣(FeO和/或SiO2)接近于零,即只产生的气体(二氧化碳CO2)就好比是氧气射流击中钢液。
它也说明如何从几秒钟的采样推算脱碳速度,只要是含碳量足够的高可以在后期的时候做含碳量的模拟,从而得到的碳含量的粗略估计。
总的结论是,通过Thermo-Calc的数据库和CFD软件的动态耦合来达到冶金动态模拟是有可能的。
关键词:
转炉;计算流体力学,热力学建模;炉渣和动态模拟。
介绍
在许多涉及氧气喷射撞击到钢液面的冶金过程中,为了优化涉及动力学的部分,如脱碳,底层流体动力学是需要的。
现在对于这个问题已经几个实验报告和一些数值或计算流体动力学(CFD)的报告。
SzekelyandAsai已经介绍了一种将液体的冲击射流表面的计算模型。
NgyenandEvans通过使用这种方法计算溶池喷嘴直径比液体表面所造成变形的冲击射流的影响,张等人模仿了一种同时使用顶吹和底吹复合吹炼的情况。
Odenthal等人展示了一种顶吹转炉多相CFD模型,在这种顶吹转炉中由于冲击射流以及底部和顶部转换混合时存在飞溅现象。
Nakazono等人描述了铁液表面的超音速氧气喷射冲击时的含碳量的两阶段的数值分析。
通过计算表明在真空和表面处理条件下天然气和钢铁之间的变化。
该模型采用稳态方法无飞溅等。
在其他文献中还其他非顶吹CFD模型介绍,琼森等。
提出了硫精炼耦合计算流体力学和热力学模型
热力学是成立的在CFD程序中作为一个自定义的子程序,尤其是专门为调查系统所写的子程序。
图中1可以看到这样的做法一个示意图。
图1。
合并计算流体力学和热力学建模与数值模型方法的示意图。
由文献(14)
最近包含顶吹系统CFD模型已经出现并和实验数据进行比较,这里提出,这个模型是包括气/液/渣的流体体积(VOF)等反应扩展的一个多相流模型,这个模型适用于顶吹系统。
这个模型以及各个阶段的扩展已经获得批准使用这一方法所建的装备使得终于有一个可以说明基本的顶吹转炉模型结果。
2。
数值模型
目前的建模方法如图2所示。
图2。
合并数值模型方法的示意图
为了解决新的研究可以轻易的合并到这个模型的问题建立了以模块化的方式,这也意味着,当从一个系统变到另一个系统是只需要一个很小的重编程程序,只要是热力学数据在目前的热力学数据库中是存在的以及不超过CFD软件的运算能力。
这个模拟过程已经在包含6个节点的集群的LinuxPC上执行。
现实生活中的模拟时间是和运算系统的数量相关的,所以没有固定和典型的模拟时间;它可能会在一小时和10天的实时变化亦或是10秒的时间。
在图3中可以看出其物理域和数值域的原理。
图3。
顶吹转炉示意图。
a)物理域b)数值域。
所涉及的边界条件为入口速度,出口压力,无滑墙壁和对称轴。
所有的墙壁都用标准壁面函数表示,合理的k–e模型已使用在所有的例子中。
域的宽度为0.075米,高度是0.13米。
最开始,1500°C的15.6公斤距顶枪0.01米以上的钢熔液用来试验,大量的气体从入口吹入相当于25升/分钟的纯体积流量氧气。
用于模拟的表1中的各种参数可以看出和表2中的初始浓度的不同。
表1.不同阶段密度和扩散系数
表2.初始浓度
2.1。
差价
ANSYS软件同时也被使用,这是一个为计算求解流体体积、质量的有限元分析软件,这样动量守恒方程中所涉及的质量、体积都得到了解决。
根据湍流模型同时使用了一些额外的守恒方程作为补充,例如湍流动能守恒,k,和动荡能量耗散,e,都是用标准的k-e模型,下面的公式用来计算任何形式的
这里r是密度,u是指速度矢量,当基于雷诺兹平均使用湍流模型,G是扩散系数,正如从表3中看到的一样方程
(1)和表3描述了质量、动量、湍流动能,动荡能量耗散、能量、物质和体积分数。
表3守恒方程参数
2.2热计算
为了获得准确描述了热力学特征,软件Thermo-Calc被使用使用。
这是一个通用的软件方案的多组分的相平衡计算。
它使用一种技术,它允许非常灵活的设置条件的平衡状态,从而适用过程模拟。
问题的解决方法是以下。
第一,质量和热量含量分别计算每个阶段。
然后,总质量和热量的内容是总结。
该系统是氢原子核装备中的。
最后,程序将计算各阶段温度,新的成分和含量。
能与热力学的软件应用程序编程接口使用TQ操作。
这个接口是一个接口Thermo-Calc中可用的软件包,使其能要推广实施不同系统(例如组件和元素,该系统由),而无需更改代码。
2.3.耦合和假设
其目在于CFD-package和Thermo-Calc数据库软件两个软件的耦合,是创建一个通用的计算模型,包括化学反应冶金系统。
在下面的文本描述的耦合。
主要的假设是局部均衡、每个时间步可以到达每个计算单元的过程中,。
软件之间的接口CFD-package和热力学数据库分别被编码在C和FORTRAN。
2.4.多相考虑
所有的散装阶段的建模为不可压缩;有统一的密度,见表1。
与一个精化的模型应该有可能使用一个理想气体定律假设对气态和一些温度对钢密度模型的依赖。
简要地说明一些细节的功能假设一摩尔的氧和碳反应形成的融化2摩尔的一氧化碳。
在计算单元在考虑将会有一个扩张的气相到约两倍于原体积。
这反过来将很可能意味着气体向外扩张的计算单元。
如果再加上CFD,扩张将发生在以下步骤中,作为额外的气体质量被添加到细胞源项。
经过计算细胞已经达到平衡它也将会有一个特定的温度平衡温度。
3.结论
3.1.基本顶级吹转炉
在图5显示气体射流向量的情况,正如水落在钢铁溶液中所显示的那样。
这是看到射流失去其轴向冲击就好像其滴落在刚溶液表面。
从射流中来的低流量给出了一个相对较小的渗透率在钢铁溶液中。
图6说明了流场的钢铁浴引起碰撞射流。
目前的最高速度的射流冲击的钢液面和面积。
流体措施阻止了渗透区向墙壁,然后进入到钢液中。
一个大型的循环,循环中形成的冲击流(即轴和墙之间)和几个小的循环回路。
应该指出的是,在更大的循环级速度是非常小的。
这是由于低流量来自高层的射击流。
更高的流率呈现较大的渗透和较强的循环。
图5.在气体速度矢量。
矢量有固定长度;他们是由色彩反映速度级(m/s)。
图6.速度向量在钢液中的变现,矢量有固定长度;他们速度级有色彩反映
图7展示了碳在1、2、3和5s时在钢液里的浓度。
首先气体的射流量应该注意,只有在相当狭窄的范围内才能看到的结果。
这是故意为了使少量浓度的差异在一定范围内可见。
同时可以看到图7(a),碳浓度
梯度存在于一个小区域接近自由面面积以及在一个更大的地区的右边的渗透区当仔细观察图7时。
7(a)-7(d),它的变化就会更明显,规模更大的向炉壁发展混合,且随着时间变得更大。
从图之间可以看到碳浓度在不断地减小。
从7(a)-7(d)看来,钢液实在表面混合运动(参见图6),随后由于循环模式出现在中下部出现,而且呈现紊流的混合。
碳浓度高的钢的深度只有几毫米的渗透区;然而真正的大梯度出现在一个更薄的地区靠近自由表面。
渐渐地,随着流场的发展,再循环趋向炉壁。
图7a.钢中碳的质量分数.1s模拟时间
图7b.钢中碳的质量分数.2s模拟时间
图7c.钢中碳的质量分数.3s模拟时间
图7d.钢中碳的质量分数.5s模拟时间
图8.CO的质量分数5s模拟时间。
图8展示了在气相中CO气体浓度呈现的规律。
射流所覆盖的钢液的表面几乎完全充满氧气所以几乎没有CO的存在,除了一个薄层旁边的钢液表面。
CO气体数量则会变得更明显的逐渐减少距离炉壁附近。
4.结论
一个新的建模方法,提出了采用CFD软件已经耦合热力学数据库(Thermo-Calc)使用自定义子例程获得动态模拟冶金过程的现象。
gas-steel之间的反应,gas-slag,steel-slag和gas-steel-slag一直被认为在一个基本的模型顶吹转炉。
最后的结论是,它可能是一个动态的耦合Thermo-Calc数据库和CFD软件进行动态模拟的冶金过程如顶吹转炉。
具体的结论来自高层的吹转炉模拟包括:
(1)紊流扩散的气体中不可忽视的要考虑射流冲击面积的影响。
(2)大量一氧化碳脱碳期间可能会减慢钢液中钢的脱碳速度。
(3)可以使用脱碳速度的推断,对一个几秒钟的仿真,得到的粗略估计碳含量在随后阶段过程中只要碳含量相对较高(比较下一点)。
(4)对当前系统来说,大约3%碳在钢的初始的渣中。
FeO或二氧化硅了接近于零即只要气体(COCO2)在钢液中的含量足够的多。
找出浓度的结合,流动速率和温度下,呈现最高效脱碳,未来会有更进一步的参数研究。
确认
这个工作是由瑞典财政支持战略研究基金会(SSF)和瑞典钢铁行业通过热力学计算中心(CCT)进行的。
参考文献
1)E.T.Turkdogan:
Chem.Eng.Sci.,21(1966),1133.
2)N.A.Molloy:
J.IronSteelInst.,(1970),Oct.,943.
3)T.KumagaiandM.Iguchi:
ISIJInt.,41(2001),S52.
4)A.Nordquist,N.Kumbhat,L.JonssonandP.Jönsson:
SteelRes.Int.,2(2006),82.
5)B.BanksandD.V.Chandrasekhara:
J.FluidMechanics,15(1963),13.
6)A.ChatterjeeandA.V.Bradshaw:
TheInteractionBetweenGasJetsandLiquids,IncludingMoltenMetals,314.
7)M.Ersson,A.Tilliander,M.Iguchi,L.JonssonandP.Jönsson:
ISIJint.,46(2006),No.8,1137.
8)J.SzekelyandS.Asai:
Metall.Trans,5(1974),464.
9)A.NguyenandG.Evans:
3rdInt.Conf.onCFDintheMineralsandProcessIndustriesCSIRO,Melbourne,Australia,(2003),71.
10)J.-Y.Zhang,S.-S.Du,S.-K.Wei:
IronmakingSteelmaking,12(1985),249.
11)H.-J.Odenthal,U.FalkenreckandJ.Schlüter:
EuropeanConf.onComputationalFluidDynamics,theNetherlands,(2006).
12)D.Nakazono,K.-I.Abe,M.NishidaandK.Kurita:
ISIJInt.,44(2004),91.
13)M.Ersson,A.Tilliander,andP.Jönsson:
Proc.SohnInt.SympAdvancedProcessingofMetalsandMaterials,ed.byF.KongoliandR.G.Reddy,TMS,Sandiego,USA,Aug27–31,(2006),p.271.
14)L.Jonsson,D.SichenandP.Jönsson:
ISIJInt.,38(1998),260.
15)L.Jonsson:
PhDThesis,Dept.ofMetallurgy,KTH,Sweden,(1998).
16)L.Jonsson,P.Jönsson,S.SeetharamanandD.Sichen:
Proc.of6thJapan–NordicCountriesSteelSymp.,ISIJ,Tokyo,(2000),77.
17)C.W.HirtandB.D.Nichols:
Comput.Physics,39(1981),201.
18)B.E.LaunderandD.B.Spalding:
Comp.Meth.Appl.Mech.Eng.,3(1974),269.
19)FluentUser’sManual,(2007).
20)T.-H.Shih,W.W.Liou,A.Shabbir,Z.YangandJ.Zhu:
ComputersFluids,24(1995),227.
21)J.-O.Andersson,T.Helander,L.Höglund,P.Shi,andB.Sundman:
Calphad,26(2002),273.
22)A.Nordquist,A.TillianderandP.Jönsson:
Proc.5thEuropeanOxygenSteelmakingconf.,Aachen,Germany,(2006),519.
DynamicCouplingofComputationalFluidDynamicsandThermodynamicsSoftware:
AppliedonaTopBlownConverter
MikaelERSSON,LarsHÖGLUND,AndersTILLIANDER,LageJONSSONandPärJÖNSSON
DivisionofAppliedProcessMetallurgy,RoyalInstituteofTechnology(KTH),SE-10044Stockholm,Sweden.(ReceivedonNovember8,2007;acceptedonDecember10,2007)Anovelmodelingapproachispresentedwhereacomputationalfluiddynamicssoftwareiscoupledtothermodynamicdatabasestoobtaindynamicsimulationsofmetallurgicalprocessphenomena.Themodelingapproachhasbeenusedonafundamentalmodelofatop-blownconverter.Reactionsbetweengas–steel,gas–slag,steel–slagandgas–steel–slaghavebeenconsidered.Theresultsshowthatthemasstransportinthesurfaceareaistotallycontrolledbyconvection.Also,thatalargeamountofCOproducedduringthedecarburizationmightslowdowntherateofdecarburizationindropletsejectedfromthebath.Forthepresentsimulationconditionsreflectinglaboratoryexperiments,itwasalsoseenthattheamountofslag(FeOand/orSiO2)createdisclosetozero,i.e.onlygas(CO_CO2)iscreatedastheoxygenjethitsthesteelbath.Itwasalsoillustratedhowanextrapolationofthedecarburizationrate,sampledfromafewsecondsofsimulation,couldbedonetogetaroughestimateofthecarboncontentatalaterstageintheprocessaslongasthecarboncontentisrelativelyhigh.TheoverallconclusionisthatitispossibletomakeadynamiccouplingoftheThermo-CalcdatabasesandaCFDsoftwaretomakedynamicsimulationsofmetallurgicalprocessessuchasatop-blownconverter.
KEYWORDS:
BOF;CFD;thermodynamics;modeling;slaganddynamicsimulations.
1.Introduction
Inmanymetallurgicalprocessesinvolvinganoxygen-jetimpingingontoasteelbathsurface,agoodunderstandingoftheunderlyingfluiddynamicsisdesirableinordertooptimizetheinvolvedkineticssuchasdecarburization.Therehavebeenseveralexperimentalreportsonthesubjectforinstance1–7)andalsosomenumericalorComputationalFluidDynamics(CFD)reports.8–13)SzekelyandAsai8)presentedacomputationalmodelofajetimpingingontoaliquidsurface.NgyenandEvansinvestigatedtheeffectthenozzle-to-pooldiameterratiohadonthedeformationoftheliquidsurfacecausedbyanimpingingjet,usingacomputationalmodel.9)Zhangetal.modeledacombinedblowncasewhereatopjetaswellasasubmergedjetwasemployed.10)Odenthaletal.showedamultiphaseCFDmodelofatopblownconverterwheresplashingphenomenaduetotheimpingingjetwasinvestigatedaswellasthemixingtimeintheconverterduetobottomandtopblowing.11)Nakazonoetal.describedatwo-phasenumericalanalysisofasupersonicO2-jetimpingingonaliquidironsurfacecontainingcarbon.12)Thecalculationswereperformedundervacuumandaddressedsurfacechemistrybetweenthegas-andthesteel-phase.Themodelusedasteadystateapproachwithouttreatmentofsplashing,ripplesetc.TherearealsoothernontopblowingCFDmodelspresentedintheliteraturethataddresschemicalreactionsinmetallurgicalsystems,seeforinstance.14,15)Jonssonetal.presentedacoupledCFDandthermodynamicsmodelofsulfurrefininginagas-stirredladle.14)ThethermodynamicswasincorporatedintheCFDprogramasacustomsubroutinespecificallywrittenfortheinvestigatedsystem.AschematicofsuchanapproachcanbeseeninFig.1.RecentlyaCFDmodelconsistingofatopblownsystemhasbeenpresentedandcomparedtoexperimentaldata.13)Hereanextensiontothismodelispresentedwhichincludesreactionsi.e.agas/liquid/slagVolumeofFluid(VOF)17)multiphasemodel,foratopblownsystem.Reactionsbetweenallphaseshavebeenallowedaswellasexpansion/contractionassociatedwiththecreationordestructionofphasesinthecomputationalcells.Themethodolo