球化处理工艺.docx
《球化处理工艺.docx》由会员分享,可在线阅读,更多相关《球化处理工艺.docx(9页珍藏版)》请在冰豆网上搜索。
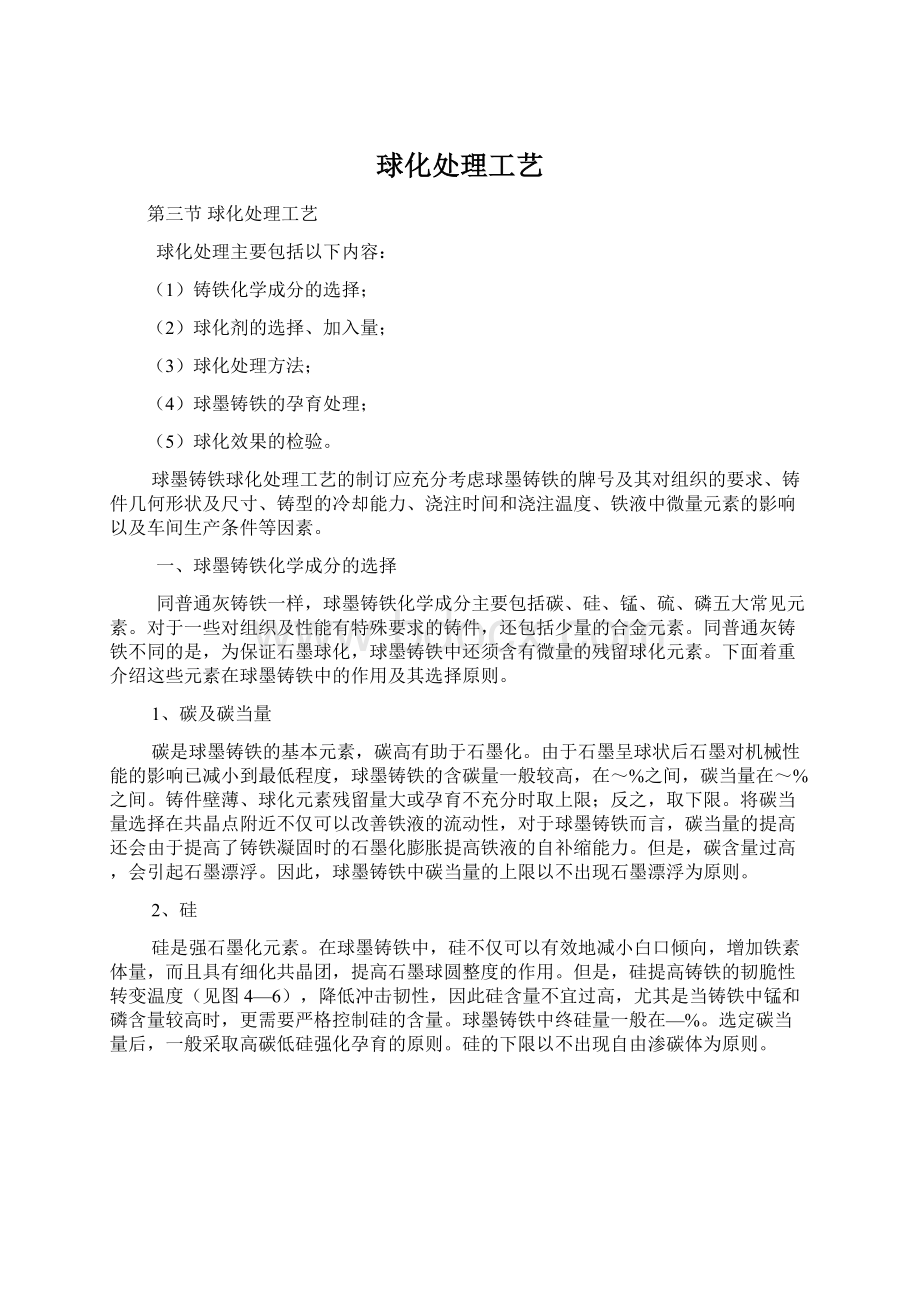
球化处理工艺
第三节球化处理工艺
球化处理主要包括以下内容:
(1)铸铁化学成分的选择;
(2)球化剂的选择、加入量;
(3)球化处理方法;
(4)球墨铸铁的孕育处理;
(5)球化效果的检验。
球墨铸铁球化处理工艺的制订应充分考虑球墨铸铁的牌号及其对组织的要求、铸件几何形状及尺寸、铸型的冷却能力、浇注时间和浇注温度、铁液中微量元素的影响以及车间生产条件等因素。
一、球墨铸铁化学成分的选择
同普通灰铸铁一样,球墨铸铁化学成分主要包括碳、硅、锰、硫、磷五大常见元素。
对于一些对组织及性能有特殊要求的铸件,还包括少量的合金元素。
同普通灰铸铁不同的是,为保证石墨球化,球墨铸铁中还须含有微量的残留球化元素。
下面着重介绍这些元素在球墨铸铁中的作用及其选择原则。
1、碳及碳当量
碳是球墨铸铁的基本元素,碳高有助于石墨化。
由于石墨呈球状后石墨对机械性能的影响已减小到最低程度,球墨铸铁的含碳量一般较高,在~%之间,碳当量在~%之间。
铸件壁薄、球化元素残留量大或孕育不充分时取上限;反之,取下限。
将碳当量选择在共晶点附近不仅可以改善铁液的流动性,对于球墨铸铁而言,碳当量的提高还会由于提高了铸铁凝固时的石墨化膨胀提高铁液的自补缩能力。
但是,碳含量过高,会引起石墨漂浮。
因此,球墨铸铁中碳当量的上限以不出现石墨漂浮为原则。
2、硅
硅是强石墨化元素。
在球墨铸铁中,硅不仅可以有效地减小白口倾向,增加铁素体量,而且具有细化共晶团,提高石墨球圆整度的作用。
但是,硅提高铸铁的韧脆性转变温度(见图4—6),降低冲击韧性,因此硅含量不宜过高,尤其是当铸铁中锰和磷含量较高时,更需要严格控制硅的含量。
球墨铸铁中终硅量一般在—%。
选定碳当量后,一般采取高碳低硅强化孕育的原则。
硅的下限以不出现自由渗碳体为原则。
图4—6硅对铁素体球墨铸铁脆性转变温度的影响
球墨铸铁中碳硅含量确定以后,可用图4—7进行检验。
如果碳硅含量在图中的阴影区,则成分设计基本合适。
如果高于最佳区域,则容易出现石墨漂浮现象。
如果低于最佳区域,则容易出现缩松缺陷和自由碳化物。
图4—7球墨铸铁中碳硅含量
3、锰
由于球墨铸铁中硫的含量已经很低,不需要过多的锰来中和硫,球墨铸铁中锰的作用就主要表现在增加珠光体的稳定性,促进形成(Fe、Mn)3C。
这些碳化物偏析于晶界,对球墨铸铁的韧性影响很大。
锰也会提高铁素体球墨铸铁的韧脆性转变温度,锰含量每增加%,脆性转变温度提高10~12℃。
因此,球墨铸铁中锰含量一般是愈低愈好,即使珠光体球墨铸铁,锰含量也不宜超过~%。
只有以提高耐磨性为目的的中锰球铁和贝氏体球铁例外。
4、磷
磷是一种有害元素。
它在铸铁中溶解度极低,当其含量小于%时,固溶于基体中,对力学性能几乎没有影响。
当含量大于%时,磷极易偏析于共晶团边界,形成二元、三元或复合磷共晶,降低铸铁的韧性。
磷提高铸铁的韧脆性转变温度,含磷量每增加%,韧脆性转变温度提高4~4.5℃。
因此,球墨铸铁中磷的含量愈低愈好,一般情况下应低于%。
对于比较重要的铸件,磷含量应低于%。
5、硫
硫是一种反球化元素,它与镁、稀土等球化元素有很强的亲合力,硫的存在会大量消耗铁液中的球化元素,形成镁和稀土的硫化物,引起夹渣、气孔等铸造缺陷。
球墨铸铁中硫的含量一般要求小于%。
6、球化元素
目前在工业上使用的球化元素主要是镁和稀土。
镁和稀土元素可以中和硫等反球化元素的作用,使石墨按球状生长。
镁和稀土的残留量应根据铁液中硫等反球化元素的含量确定。
在保证球化合格的前提下,镁和稀土的残留量应尽量低。
镁和稀土残留量过高,会增加铁液的白口倾向,并会由于它们在晶界上偏析而影响铸件的机械性能。
表4—2球墨铸铁推荐化学成分(%)
基体组织
C
Si
Mn
P
S
Mg
RE
Cu
Mo
铸态铁素体
~
~
≤
≤
≤
~
~
退火铁素体
~
~
≤
≤
≤
~
~
铸态珠光体
~
~
~
≤
≤
~
~
~
0~
表4—2给出了不同组织球墨铸铁的化学成分,供参考。
二、球化剂的选择
在选用球化剂时,应考虑以下几个因素:
(1)对铸件铸态组织的要求。
铸态铁素体球墨铸铁选用低稀土球化剂,铸态珠光体球墨铸铁选用含铜或镍的球化剂。
(2)铁液中干扰元素的含量。
如果干扰元素,诸如钛、钒、铬、锡、锑、铅、锌等含量较高,须选用稀土含量较高的球化剂。
如果干扰元素含量较低(总量小于%),可选用纯镁或镁合金球化剂。
(3)铁液含硫量。
硫含量较高时,一般采用稀土和镁含量较高的球化剂,如有条件,可进行脱硫处理。
硫含量较低时,可选用低稀土低镁的稀土硅铁镁球化剂。
(4)铸件冷却条件。
冷却速度较快的金属型铸造条件下,可选用低稀土球化剂。
冷却速度较慢的大型厚断面铸件可选用钇基重稀土球化剂。
三、球化处理方法
球化处理方法主要指球化剂的加入方法。
球化处理方法不同,球化剂被铁液吸收率不同,球化效果就大不一样。
目前常用的球化处理方法主要有冲入法、自建压力加镁法、转包法、盖包法、型内法、钟罩法、密封流动法以及型上法等。
下面简要介绍其中常用工艺方法的特点及适用范围。
1、冲入法
将球化剂破碎成小块,放入处理包底部一侧,或在处理包底部设置堤坝或凹坑,将球化剂放在堤坝内侧或凹坑内,然后在球化剂上面覆盖孕育剂、无锈铁屑、或草灰、苏打、珍珠岩集渣剂等,然后冲入1/2~2/3铁液,待铁液沸腾结束时,再冲入其余铁液。
处理完毕后加集渣剂彻底扒渣。
冲入法要求处理包的深度与内径之比在~之间,处理包要预热到600~800℃,铁液温度应高于1400℃。
冲入法的优点是设备简单,操作简单。
缺点是镁的吸收率低,一般只有30~40%,而且烟尘闪光较严重。
目前这种方法广泛应用于各种温度和含硫量的各种生产规模的球墨铸铁件生产。
2、自建压力加镁法
镁的沸点与压力呈正比,如果铁液中有6~8个大气压时,镁的沸点就会提高到1350~1400℃。
在这样的条件下加镁,就可以避免镁的沸腾。
自建压力法是在密封的条件下将装有镁的钟罩压入铁液,使镁在铁液中有控制的沸腾,从而提高镁的回收率,稳定球化质量。
自建压力加镁法要求有安全可靠的处理设备,以防止铁液喷射出来。
处理包深度与内径之比应为~2,加镁钟罩压入铁液后距包底的距离应为包深的10%。
自建压力加镁法镁的吸收率可达到70~80%,并且处理效果稳定,无镁光,无烟尘,但设备费用高,操作繁琐。
这种方法适用于大型厚断面铸件,铸态高韧性铁素体铸件以及大量生产要求控制镁量的铸件。
3、转包法
转包法原理如图图4—8所示。
反应室内装入纯镁或镁焦,转包横卧,接受铁液,然后转包立起,使铁液通过反应室的处理网孔进入反应室与镁反应。
这种方法镁的吸收率可达到60~70%,烟尘及镁光较轻,可处理含硫高达%的铁液。
其缺点是需要专门的处理设备,操作较冲入法复杂。
图4—8转包法示意图
1—反应室2—球化剂3—安全盖4—铁液入口5—处理网
4、盖包法
盖包法是在冲入法的基础上发展起来的球化处理方法。
其方法如图4—9所示,在冲入法的处理包上部安装一个中间包将其密封,处理包与中间包之间仅通过经过严格计算的浇口连接。
预先将球化剂放在处理包内,然后用中间包承接铁液,靠由中间包流入处理包的铁液使处理包处于密闭状态,从而减少反应烟尘和镁光外逸,提高镁的利用率。
4—9盖包法示意图
这种方法与冲入法比镁的吸收率高,烟尘及镁光减少,操作复杂程度和设备费用增加不多,因此可以广泛应用。
5、型内法
把球化剂放置在浇注系统中专门设计的反应室内,在浇注过程中铁液流经反应室时与球化剂发生反应进行球化处理。
为保证球化处理稳定,减少烧损,要严格计算反应室及浇注系统尺寸。
一般情况下,反应室设置于直浇道下的横浇道中,浇口杯到冒口前的系统应处于充满状态,冒口和铸件型腔保持开放。
具体尺寸可参阅有关手册。
这种方法镁吸收率高,可达70~80%,无镁光,无烟尘,无球化衰退。
其不足之处是对铁液温度、含硫量、球化剂成分、球化剂块度、反应室尺寸、浇注系统设计都有严格要求,这些因素的微小变化都会引起球化效果的变化。
此外,这种方法易产生夹渣。
这种方法适合于机械造型的大量流水生产,以及高强度高韧性球墨铸铁的生产。
四、球墨铸铁的孕育处理
由于球化剂的加入,球墨铸铁的过冷倾向增大。
为避免碳化物的析出,促进析出大量细小圆整的石墨球,往往在球化处理后需要对球墨铸铁进行孕育处理。
对于球墨铸铁的孕育处理,孕育剂一般采用硅铁。
硅铁在刚刚溶解的时候其孕育效果最好,大约在8min后出现孕育衰退现象,20~30min后孕育完全衰退。
因此,球铁的孕育以瞬时孕育效果最好。
生产实践证明,随流孕育和型内孕育效果比较理想。
但是由于操作方便,冲入孕育法(冲入法球化处理时将孕育剂覆盖在球化剂上)、倒包孕育法、浇口杯孕育法也在生产中经常使用。
图4—10为75FeSi孕育剂不同加入量、不同孕育方法时产生的不同孕育效果。
不难看出,在铸件壁厚小于40mm的情况下随流孕育效果明显优于包内孕育,只有当铸件壁厚大于45mm时,由于二者都出现严重的孕育衰退,孕育剂加入量较大的包内孕育法效果才略好。
图4—1075FeSi随流孕育与包内孕育效果比较
孕育的初期效果及其衰退速度与孕育剂中所含有的微量元素有关。
图4—11是用十种含有不同微量元素的硅铁孕育剂孕育处理球墨铸铁中石墨球数量随时间的变化情况,试棒直径为22mm。
就初期效果而言,含锶硅铁最好。
而从抗衰退能力看,Si-Mn-Ba硅铁最有效。
图4—11不同成分硅铁孕育剂孕育处理的球墨铸铁中石墨球数量与孕育处理后时间的关系
五、球化效果的检验
球化效果的检验应包括炉前铁液成分的快速分析,炉前工艺试块检验,以及金相组织和力学性能的检验。
在条件许可的情况下还可以通过测定热分析曲线测定球化率。
此外,由于石墨形态对超声波、音频的传播有影响,近年来利用超声波和音频对球墨铸铁件进行无损检测也被用于生产中。
在球铸铁的生产中,及时检验铁液化学成分是否符合要求,尤其是在球化处理前预知铁液中碳、硅及硫含量对于及时调整成分,确定球化剂和孕育剂的加入量是十分重要的。
铁液化学成分的快速检验方法请参阅本书第三章中孕育效果的检验一部分内容。
下面着重介绍球墨铸铁的炉前工艺试块检验法。
球化和孕育处理后搅拌扒渣,从金属液表面下取铁液浇入长150mm、宽25mm、高50mm的三角试样铸型中,待其冷凝至表面呈暗红色时取出,底面向下淬入水中冷却,然后将其打断,观察断口。
也可采用直径15~30mm的园棒试样。
炉前三角试样球化效果的判断方法见表4—3。
需要指出的是,只有当三角试块的尺寸与铸件厚度相近时,上述方法才比较有效。
当铸件尺寸与三角试块厚度差别较大时,可根据铸件厚度重新设计三角试块。
表4—3炉前三角试样球化效果判断
项目
球化良好
球化不良
外形
试样边缘呈较大园角
试样棱角清晰
表面缩陷
浇注位置上表面及侧面明显缩瘪
无缩陷
断口形态
断口细密如绒或呈银灰色
断口暗灰粗晶粒或银白色分布细小黑点
缩松
断口中心有缩松
无缩松
白口
断口尖角白口清晰
无白口
敲击声
音频较高
声音低哑
气味
遇水有H2S味
无味