壳体零件注塑模具课程设计说明书.docx
《壳体零件注塑模具课程设计说明书.docx》由会员分享,可在线阅读,更多相关《壳体零件注塑模具课程设计说明书.docx(13页珍藏版)》请在冰豆网上搜索。
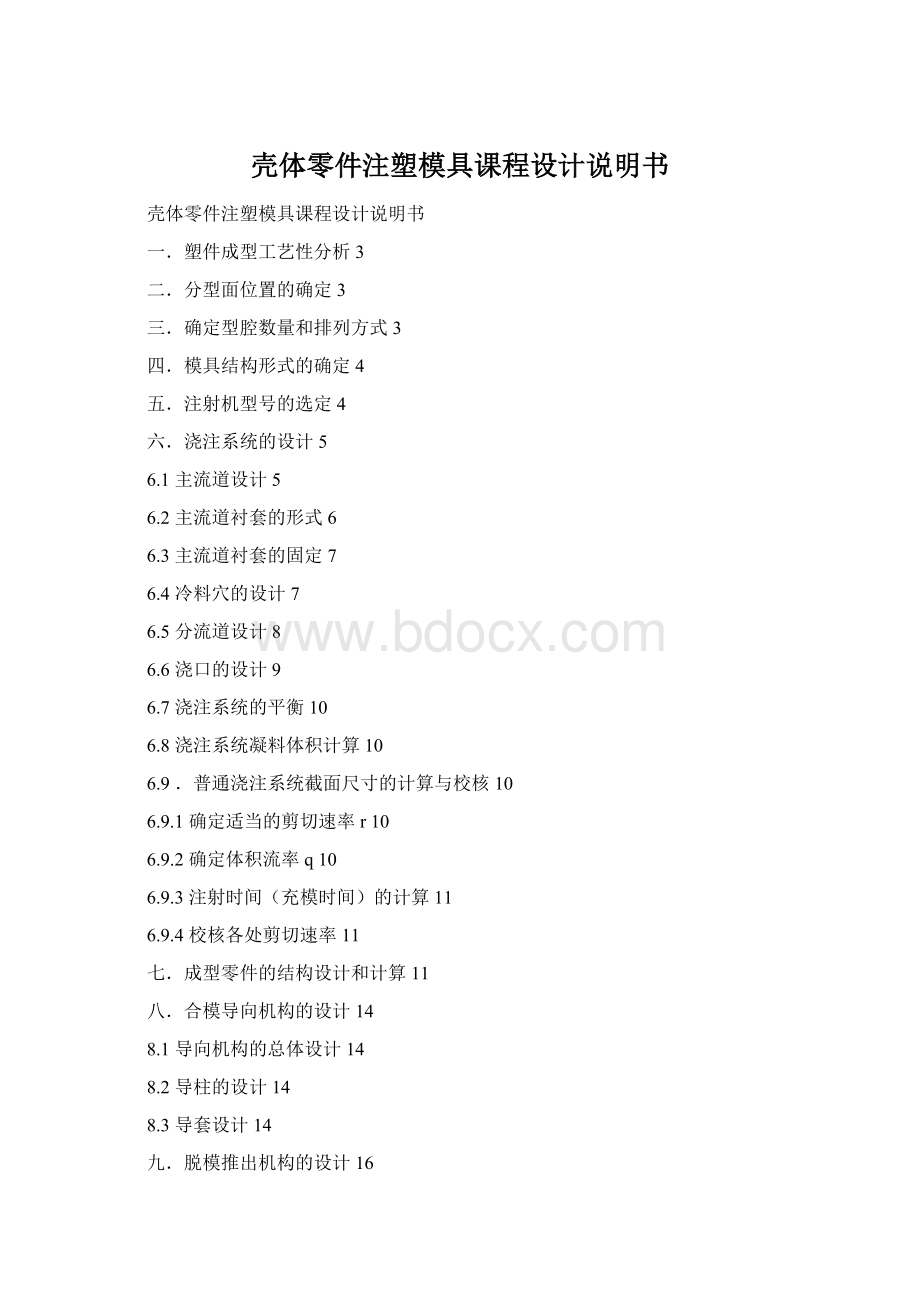
壳体零件注塑模具课程设计说明书
壳体零件注塑模具课程设计说明书
一.塑件成型工艺性分析 3
二.分型面位置的确定 3
三.确定型腔数量和排列方式 3
四.模具结构形式的确定 4
五.注射机型号的选定 4
六.浇注系统的设计 5
6.1主流道设计 5
6.2主流道衬套的形式 6
6.3主流道衬套的固定 7
6.4冷料穴的设计 7
6.5分流道设计 8
6.6浇口的设计 9
6.7浇注系统的平衡 10
6.8浇注系统凝料体积计算 10
6.9.普通浇注系统截面尺寸的计算与校核 10
6.9.1确定适当的剪切速率r 10
6.9.2确定体积流率q 10
6.9.3注射时间(充模时间)的计算 11
6.9.4校核各处剪切速率 11
七.成型零件的结构设计和计算 11
八.合模导向机构的设计 14
8.1导向机构的总体设计 14
8.2导柱的设计 14
8.3导套设计 14
九.脱模推出机构的设计 16
十.湿度调节系统设计 17
总 结 19
参考文献 20
一.塑件成型工艺性分析
该塑件是一壳体,塑件壁属厚壁塑件,生产批量大,材料选PS,考虑到主流道应尽可能短,一般小于60mm,过长则会影响熔体的顺利充型,因此采用下列数据:
二.分型面位置的确定
根据塑件结构形式分型面应选在I上,如下图:
三.确定型腔数量和排列方式
1.该塑件精度要求不高,批量大,可以采用一模多腔,考虑到模具的制造费用和设备的运转费用,定为一模四腔。
2.型腔排列方式的确定如下图:
四.模具结构形式的确定
从上面的分析中可知本模具采用一模四腔,双列直排,推件板推出,流道采用平衡式,浇口采用侧浇口,动模部分需要一块型芯,固定板,支撑板。
五.注射机型号的选定
1.通过分析,塑件为26.5g,,1.05
V=25.2,流道凝料的质量
2.塑件和流道凝料在分型面上的投影面积,可用0.35nA来进行估算,所以
n=1.354A=25920mm
式中
查表2-2<塑料模具设计指导>
取
3.选择注射机
根据每一生产周期的注射量和锁模力的计算值可选用SZ-250/1250
理论注射量270 锁模力1250
螺杆直径 45 拉杆内间距415415
注射压力160 移模行程360
注射速率110 最大模厚
塑化能力18.9 最小模厚150
螺杆转速 定位孔直径160
喷嘴半径15 锁模方式双曲肘
4、注射机有关参数的校核
型腔数校核合格。
式中,K—-注塑机最大注射量的利用系数一般取0.8
m—注射机的额定塑化量(10.5g/s)
T—成型周期取30s
1)注射压力校核
——注射压力的安全系数,一般取K=1.25-1.4
,中等壁厚件
2)锁模力校核
。
而F=1250KN
K--锁模力安全系数,一般取K=1.1-1.2
其他安装尺寸的校核要待模架的选定,结构尺寸确定后才可进行。
六.浇注系统的设计
6.1主流道设计
1)主流道尺寸设计
根据所选注射机,则主流道小端尺寸为
d=注射机喷嘴尺寸+(0.5-1)
=4
2)主流道球面半径为
SR=喷嘴球面半径+(1-2)=16mm
3)球面配合高度
h=3mm-5mm,取h=3mm
4)主流道长度,尽量小于60,由标准模架结合该模具的结构,取
L=25+20=45mm
5)主流道大端直径
D=d+2Ltana=6.54mm(半锥角a为,取a=)取D=6.5mm
6)浇口套总长
=25+20+h+2=50
6.2主流道衬套的形式
主流道小端入口处与注射机喷嘴反复接触属易损性,对材料要求严格,因而模具主流道部分常设计可拆卸更换的主流道衬套形式即浇口套,以便常用碳素工具如T8A,T10A等,热处理硬度为50HRC-55HRC,如图示
由于该模具主流道较长,定位圈和衬套设计成分体式较宜,其定位圈结构尺寸如下图
6.3主流道衬套的固定
主流道衬套的固定形式如下图
6.4冷料穴的设计
1)主流道冷料穴的设计
开模时应将主流道中的凝料拉出,所以冷料穴直径稍大于主流道大端直径,采用
Z形头冷料穴,很容易将主流道凝料拉离定模,如图所示
1:
定模座板 2:
冷料穴 3:
动模板 4:
推杆
主流道凝料体积
=809mm=0.8mm
主流道剪切速率校核
有经验公式v=3.3q/
主流道剪切速率偏小主要是注射量小,喷嘴尺寸偏大,使主流道尺寸偏大所致。
6.5分流道设计
1)分流道布置形式
分流道布置有多种形式,但是需要循两方面原则;一方面排列紧凑,缩小模具版面尺寸;另一方面流程尽量短,锁模力力求平衡。
应采用平衡时分流道。
如图:
2)分流道长度
第一级分流道
第二级分流道
3)分流道的形式。
截面尺寸以及凝料体积
为了便于加工及凝料脱模,分流道大多设置在分型面上。
工程设计中常用梯形截面,加工工艺好,且塑料熔体的热量散失。
流动阻力均不大,一般采用下面的经验公式可确定其截面尺寸,即B=0.2654
式中,B---梯形大底边的宽度
m---塑件的质量,为26.5g
根据《塑料模具设计手册》表4-9,取B=4
H=2/3B=2.67mm, 取H=3mm
从理论上1.2,1.3分流道可以1.1截面小1/10,但为了刀具的统一和加工方便,在分型面上的分流道采用一样的截面。
4)分流道的表面粗糙度
由于分流道中与模具接触的外层塑料迅速冷却,只有中心部位的塑料熔体的流动状态较理想,因此分流道的内表面粗糙度Ra并不要求很低,一般取0.63um---1.6um,这样表面并不光滑,有助于增大塑料熔体的外层流动阻力,避免熔体表面滑移,使中心层具有较高的剪切速率。
此处Ra=0.8um。
5)凝料体积
分流道长度 L=(50+82+12)2=136mm
分流道截面面积
凝料体积
6)分流道剪切速率校核
采用经验公式r=3.3q/
式中q=v/t=425.28=101.12
6.6浇口的设计
浇口截面积通常为分流道截面积的0.07--0.09倍,浇口截面积形状多为矩形和圆形两种,浇口长度为0.5--2mm。
浇口具体尺寸一般根据经验确定,取其下限值,然后在试模时逐渐修正。
(1)浇口类型及位置确定
该模具是中小型塑件的多型腔模具,设置侧浇口比较合适,侧浇口开设在垂直分型面上,从型腔(塑件)外侧面进料,侧浇口是典型的矩形截面浇口,能很方便的调整充模时的剪切速率和浇口封闭时间,因而又被称为标准浇口。
这类浇口加工容易,修正方便,并且可以根据塑件的形状特征灵活地选择进料位置,因此它是广泛使用的一种浇口形式,普遍使用于中小型的多型腔模具。
(2)浇口结构尺寸的经验公式
侧浇口深度和宽度经验计算:
经验公式为 h=nt=1mm w=2.3
式中,h——侧浇口深度(mm)
W——浇口宽度(mm)
A——塑件外表面积;
T——塑件厚度(约为3mm)
n——塑料系数,查表得n=0.6
6.7浇注系统的平衡
对于该模具,从主流道到各个型腔的分流道的长度相等,形状及截面尺寸对应相同,各个浇口也相同,浇注是平衡的。
6.8浇注系统凝料体积计算
(1)主流道与主流道冷料井凝料体积
6.9.普通浇注系统截面尺寸的计算与校核
6.9.1确定适当的剪切速率r
根据经验浇注系统各段的r取以下值,所成型塑件质量较好。
1)主流道
2)分流道
3)点浇口
4)其他浇口
6.9.2确定体积流率q
1)主流道体积流率
因塑件小,即使是一模四腔的模具结构,所需注射塑料熔体的体积也还是比较小的,而主流道尺寸并不小,因此主流道体积流率并不大,取代入得:
2)浇口体积流率q
侧(矩形)浇口用适当的剪切速率代入得:
6.9.3注射时间(充模时间)的计算
1)模具充模时间
式中
2)单个型腔的充模时间
3)注射时间
根据经验公式求得注射时间
6.9.4校核各处剪切速率
1)浇口剪切速率
2)分流道剪切速率
由经验公式
七.成型零件的结构设计和计算
塑料模具型腔在成型过程中受到塑料熔体的高压作用应具有足够的强度和刚度,如果型腔侧壁和底版厚度过小,可能因强度不够而产生塑性变形甚至破坏,也可能因刚度不足而产生挠曲变形,导致溢14料飞边,降低塑件尺寸精度并影响顺利脱模。
1.模部分的型芯
为了便于加工设置一个定模型芯,它的配合可以采用过盈配合。
2.成型零件钢材的选用
零件是大批量生产,成型零件所选用钢材耐磨性和抗疲劳性能应该良好,机械加工性能和抛光性能也应该良好,因此构成型腔的嵌入式凹模钢材选用SMI
3.成型零件工作尺寸的计算
塑件尺寸公差按SJ1372—78标准中的6级精度选取
1).型腔径向尺寸
Lm1=[(1+s)Ls1-x△]=[(1+s)80-0.58×0.70]=80.28
Lm2=[(1+s)Ls2-x△]=[1.0035×60-0.58×0.7] =59.79
式中,S——塑件平均收缩率S=(0.006+0.008)=0.0035
X——修正系数(取0.58)
Δ——塑件公差值(查塑件公差表取0.70)
——制造公差,(取Δ/5)参考《塑料模具设计手册》P49型腔深度尺寸Hm=[(1+s)h-xΔ]0+δ=24.7
式中,h——塑件厚度最大尺寸(取25)
x——修正系数(取0.56)
Δ——塑件公差值(取0.40)参考《塑料模具设计手册》P47型芯高度尺寸
hm=[(1+s)H+xΔ]0-δ2=3.130-0.04
式中,h——塑件厚度最小尺寸(取3)
X——修正系数(取0.58)
Δ——塑件公差值(查塑件公差表取0.20)
模架的确定和标准件的选用
模架尺寸确定后,对模具有关零件要进行必要的强度或刚度的计算,以校核所选模架是否适当,尤其对大型模具,模架选用A4型。
由前面型腔的布局以及相互的位置尺寸,再根据成型零件尺寸结合标准模架,选用模架尺寸为250mm×315mm的标准模架,可符合要求。
模具上所有的螺钉尽量采用内六角螺钉,模具外表尽量不要有突出部分,模具外表面应光洁,加涂防锈油。
两模板之间应用分模间隙,即在装配,调试,维修过程中,可以方便地分开两块模板。
1.定模座板(315mm×315mm,厚25mm)材料为45钢.通过4个M10的内角圆柱螺钉与定模板连接定位圈通过4个M6的内六角圆柱螺钉与其连接,定模座板与浇口套为H8/f8配合。
2.定模板(凸模固定板)(250mm×315mm,厚20mm)固定板应有一定的厚度,并有足够的强度,一般用45钢或Q235A制成,最好用调质230HB—270HB。
其上的导套孔与导套一端采用H7/k6配合,另一端采用H7/e7,定模板与浇口套采用H8/m6配合,定模板与圆筒型芯为H7/m6配合。
3.支撑板(180mm×250mm,厚度40mm)支撑板应具备较高的平行度和硬度。
4.垫块(40mm×315mm,厚50mm)
1.)主要作用在动模座板与支撑板之间形成推出机构的动作空间,或是调节模具的总厚度,以适应注射机的模具安装厚度要求。
2.)结构形式可以是平行垫块或拐角垫块,该模具采用平行垫块。
3.)垫块材料垫块材料为Q235A,也可用HT200,球墨铸铁等,该模具垫块采用Q235A制造。
4.)垫块的高度h校核.
H=h1+h2+h3+s+δ=0+16+12.5+18+3.5=50mm
式中,h1————推板厚度,为16mm
h2————推杆固定板厚度,为12.5mm
h3————推出行程,为18mm
δ———推出行程富余量,一般为2mm—6mm,取3.5mm
5.)动模座板(315mm×315mm,厚25mm)
材料为45钢,注射机顶杆孔为mm,其上的推板导柱孔与导柱采用H7/m6配合。
6.)推板(118mm×315mm,厚16mm)
材料为45钢,其上的推板导套孔和推导套采用H7/k6配合,用4个,M6的内六角圆柱螺钉与推杆固定板固定。
7.)推杆固定板(118mm×315mm。
厚12.5mm)
材料为45钢,其上的推板导套孔与推板导套采用H7/f6配合。
8.)脱模板
八.合模导向机构的设计
8.1导向机构的总体设计
1.)导向零件应合理地均匀分布在模具的周围或靠近边缘的部分。
2.)该模具采用4根导柱,其分布为等直径导柱不对称装置
3.)该模具导柱安装在支撑板和模套上,导套安装在定模固定板上。
4.)为了保证分型面很好的接触,采用在导套的孔口倒角。
5.)在合模时,应保证到向零件首先接触。
6.)动定模板采用合并加工时,可确保同轴度要求。
8.2导柱的设计
该模具采用带头导柱,不加油槽,如下图示
导柱的长度必须比凸模端面高度高出,6mm—8mm.
1.)为使导柱能顺利地进入导向孔,导柱的端部常做成锥形或球形的先导部分.
2.)导柱的直径应根据模具尺寸来确定,应保证具有足够的抗弯强度,该导柱直径由标准模架可知为φmm.
3.)导柱的安装形式,导柱固定部分与模架按H7/f6配合,导柱的滑动部分按H7/f7或H8f7的间隙配合.
4.)导柱工作部分的表面粗糙度为Ra=0.4mm
5.)导柱应具有坚硬耐磨的表面,坚韧而不易折断的内芯.多采用低碳钢经渗碳淬火处理或碳素工具钢T8A.T10A,经淬火处理,硬度为50HRC以上或45钢经调质表面淬火,低温回火,硬度为50HRC以上.
8.3导套设计
导套与安装在另一半模上的导柱相配合,用一确定运动定模的相对位置,保证模具运动导柱相配合,用以确定运动定模的相对位置,保证模具运动导向精度的圆套形零件.导套常用的结构形式有两种:
直导套(GB/T41692.2---1984(带头导套(GB/T4169.3—1984).
1.)结构形式,采用带头导套(Ⅰ型)如图所示
2.)导套的端面应倒角,导柱孔最好做成面孔,利于排出孔内剩余空气.
3.)导套孔的滑动部分按H8/f7或H7/f7的间隙配合,表面粗糙度为0.4mm.导套外径与模板一端采用H7/k6配合;另一端采用H7/e7配合入模板.
4.)导套材料可用,淬火钢或青铜合金等耐磨材料制造该模具中采用T8A.
8.4推板导柱与导套设计
推板导柱除了起导向作用外,还支撑着支撑板,从而改善了支撑板的受力情况,大大提高了支撑板的刚性,该模具设置了4套推板导柱与导套,它们之间采用H8/f7配合其形状与尺寸配合如图所示
九.脱模推出机构的设计
注射成型每一循环中,塑件必须准确无误地从模具的凹模中型芯上脱出,完成脱出塑件的装置称为脱模机构也常推出机构
1.塑件推出的基本方式
1.)推杆推出
推杆推出是一种基本的,也是一种常用的塑件推出方式常用的推杆形式有圆形,矩形,阶梯形.
2.)推件板推出
对于轮廓封闭且周长较长的塑件,采用推件推出结构.推件板推出部分的形状根据塑件形状而定.
3.)气压推出
对于大型深型塑件,经常采用或&助气压推出方式本模具,考虑到塑件轮廓封闭且周长较长故采用推板推出.
脱模力的计算
脱模力是指将塑件从型芯上脱出时所需克服的阻力它是设计脱模机构上午重要依据之一.
F阻=f(-.sinα)=f.-f.sinα
式中,————摩擦阻力(N)
f————摩擦系数,一般取f=0.15—1.0(取f=0.3)
———塑件收缩对型芯产生的正压力即包紧力(N)
————脱模
α——脱模斜率,一般为1°——2°(取α=1°)
根据受力图可列平衡方程式
+sinα=.cosα
由于α,一般很小,式中(f.sinα项之值可以忽略。
=f.cosα-sinα=(f.cosα-sinα)PA
=PA
式中,P——塑件对型芯产生的单位正压力(包紧力),一般为P=8——12MPa薄件取小值,厚件取大值,(P=10MPa)
A——塑件包紧型芯侧面积(mm)
A=2274=1628mm
=AP=162810=16280N
=(f.cosα-sinα)=162800.2=3256N
由于塑件有孔不需要计算,真空吸引阻力
=n(+)=43256=13024N
推杆的尺寸计算,圆形推杆的直径可由欧拉公式简化得,d=k(*****
式中,d——推杆直径(mm)
L——推杆长度(mm)
——塑件的脱模力(N)
E——推杆材料的弹性模量(MPa)
n——推杆数量
k——安全系数,取k=1.5
推杆直径确定后,还应进行强度校核
十.湿度调节系统设计
1.加热系统
由于该套模具的模温要求在80°以下,又是中小型模具,所以无需设置加热装置。
2.冷却系统
一般注射到模具内的塑料温度为200℃左右,塑件固化后,从模具型腔中取出时其温度在60℃以下。
热塑性塑料在注射成型后,必须对模具进行有效的冷却,使熔融塑料的热量尽快地传给模具,23以使塑料可靠冷却定型并迅速脱模。
因为PS黏度低流动性好,因为成型工艺要求模温都不太高,所以常用温水对模具进行冷却。
PS的成型温度和模具温度分别260℃—280℃,32℃—65℃用常温水对模具进行冷却。
1.)冷却介质
冷却介质有冷却水和压缩空气,但用冷却水较多,因为水的热容量大,传热系数大,成本低,用水冷却即在模具型腔周围或内部开设冷却水道
2.)冷却系统的简略计算如果忽略模具因空气对流,热辐射以及与注射机接触所散发的热量,不考虑模具金属材料的热阻,可对模具冷却系统进行初步和简略计算。
1.)求塑件在固化时每小时释放的热量Q查《塑料制品成型与模具设计》表4——25PS单位质量放出的热量Q=2.8102KJ/kg——3.5102KJ/kg取,Q1=3.5102KJ/kg故Q=Q1W0.2153.510260=4275KJ/h
式中,W—单位时间(每分钟)内注入模具中的塑料质量(KJ/h)
该模具每分钟注射2次
所以,W=2102.51.05=0.215kg/min
2.)求冷却水的体积流量]
qv=W/P(-)=215.25×3.5×102/[4.187×103×(25-20)]=3.59×10-3m3/min
式中,e——冷却水的密度,为1X103kg/m3
c1——冷却水的比热容,为4.187kj/kg.℃
——冷却水出口温度,取25℃
——冷却水入口温度,取20℃
3.)求冷却管道直径查《塑料制品成型及模具设计》表4-27,取f=6.84(水温为25℃)
取d=8mm
求冷却管道总传热面积A
由公式得,A=60W/h△=60×0.215×3.5×102/h×[65-(25+20)/2]=22.4×10-3m2
式中,△Q——模具温度与冷却水温之间的平均温度差(℃)
模具温度取65℃
4.)计算凹模上座设冷却管总长度(mm)由于传热面积A=πdL
所以:
L=A/πd=22.4×10-3(3.14×8×10-6)=0.887m25
5.)求凹模所需冷却水管根数
n=L/B(B为模具的宽度)
=0.887/0.315=2.8≈3孔
总 结
通过本次课程设计的练习,我对以前的知识有了更深的了解。
在完成设计任务的同时,对设计方法、实验验证、文献资料的查阅、各种设计规范和设计标准的运用以及文档的撰写等方面的能力要求,需要得到全面的训练与提高。
在课程设计的过程中,有很多不够了解的问题,感谢同学们和老师的帮忙解答,这次课程设计,为我以后的学习和工作提供了很多有益的经验。