菲林和MI资料检查规范.docx
《菲林和MI资料检查规范.docx》由会员分享,可在线阅读,更多相关《菲林和MI资料检查规范.docx(9页珍藏版)》请在冰豆网上搜索。
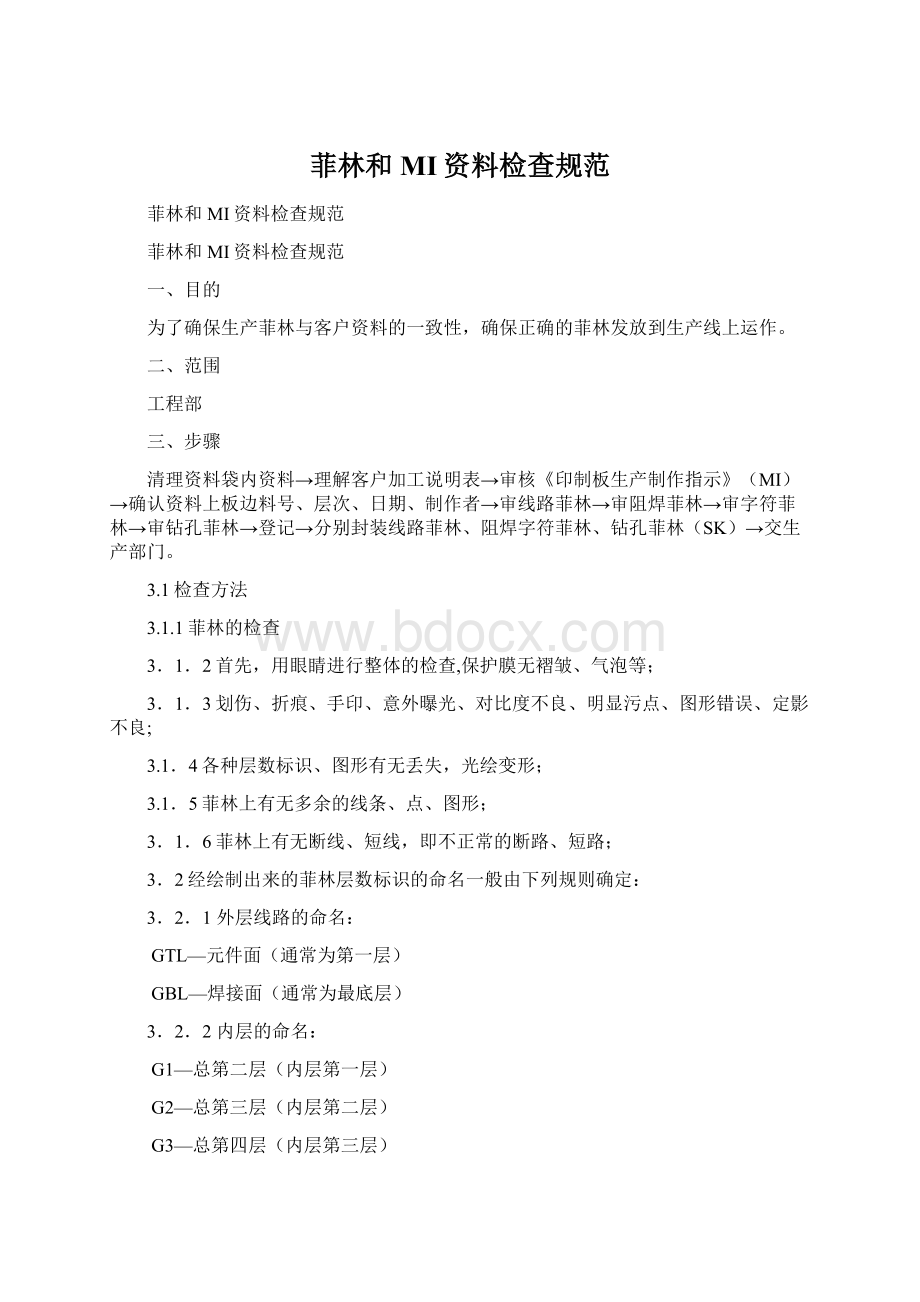
菲林和MI资料检查规范
菲林和MI资料检查规范
菲林和MI资料检查规范
一、目的
为了确保生产菲林与客户资料的一致性,确保正确的菲林发放到生产线上运作。
二、范围
工程部
三、步骤
清理资料袋内资料→理解客户加工说明表→审核《印制板生产制作指示》(MI)→确认资料上板边料号、层次、日期、制作者→审线路菲林→审阻焊菲林→审字符菲林→审钻孔菲林→登记→分别封装线路菲林、阻焊字符菲林、钻孔菲林(SK)→交生产部门。
3.1检查方法
3.1.1菲林的检查
3.1.2首先,用眼睛进行整体的检查,保护膜无褶皱、气泡等;
3.1.3划伤、折痕、手印、意外曝光、对比度不良、明显污点、图形错误、定影不良;
3.1.4各种层数标识、图形有无丢失,光绘变形;
3.1.5菲林上有无多余的线条、点、图形;
3.1.6菲林上有无断线、短线,即不正常的断路、短路;
3.2经绘制出来的菲林层数标识的命名一般由下列规则确定:
3.2.1外层线路的命名:
GTL—元件面(通常为第一层)
GBL—焊接面(通常为最底层)
3.2.2内层的命名:
G1—总第二层(内层第一层)
G2—总第三层(内层第二层)
G3—总第四层(内层第三层)
G4—总第五层(内层第四层)
3.2.3绿油层的命名:
GTS—元件面绿油层,与GTL层相对应
GBS—焊接面绿油层,与GBL层相对应
3.2.4文字层的命名:
GTO—元件面文字层,与GTS层相对应
GBO—焊接面文字层,与GBS层相对应
3.3检查药膜面方法:
线路菲林用刀轻轻地在电镀边上划一条3-5MM的痕印,若药膜要掉,那面就是药膜面,反之不是;
3.4检查黑度:
将菲林放在菲林密度仪检测黑度小于4.0即黑度不够,反之不是;
3.5.客户加工说明表
3.5.1.查看加工说明表文件名是否与提供的图纸一致。
3.5.2.查看客户加工说明表上材质,表面工艺、阻焊颜色、文字颜色、标记添加及一些特殊注明事项
3.5.3.是否有特殊注明事项超出我司加工能力而处理资料时没有注意到的。
3.6.光绘指示:
a.检查标识:
指示中“X”表示镜像,“N”阴片(负片);
b.单面板检查标准为:
GBL不镜像绘阴片(负片);
c.双面孔化板菲林绘制检查标准为GTL镜像,GBL不镜像;GTL、GBL、绘阳片(正片);
d.普通多层板内层检查标准G1为正绘阴片(负片),G2为反绘阴片(负片),G3为正绘阴片(负片),G4为反绘阴片(负片),以此类推;普通多层板外层检查标准同双面孔化板一样;
e.原始资料的绘制与工程菲林刚好相反,方便核对原装。
f.阻焊菲林标准为GTS镜像,GBS不镜像;字符菲林标准为GTO不镜像,GBO镜像。
3.7.开料审核
a.利用率(82%)等于拼板开料尺寸乘以每张大料能裁料张数除以大料的面积。
b.特殊排板应在生产制作指示上标明;
c.批量板(3平米)有无提供拼板方式和开料示意图;
d.板材材质和板材厚度、基铜厚度等。
3.8.钻孔审核
a.单面板、普双板、非金属化孔、孔径公差±0.05。
b.双面孔化板、多层板、孔径公差±0.08;
c.特殊要求公差是否与客户要求一致。
a.如有按键或金手指如无特殊情况,阻焊需开窗。
如MARK点、散热片开窗;
b.金手指处,阻焊挡点必须开窗到外型线以外1MM,防止金手指卡槽边有阻焊。
且工作边上添加6MM阻焊挡点,用作镀金夹点。
c.检查客户加工说明表上的阻焊颜色与生产制作指示填写是否一致;
d.
e.非金属化孔;电镀后,蚀刻前铣/钻;沉铜前铣阻焊菲林上加挡点。
f.成型铣内部图形,阻焊菲林上不加挡点,只加5MIL边框线。
g.除黑色阻焊外,所有阻焊菲林上加5MIL边框线。
h.将阻焊层对应线路层检查贴片及器件焊盘有无开窗,阻焊开窗大小是否符合,是否还有特殊阻焊亮锡,及时与CAM制作人员沟通。
i.用阻焊菲林对照线路菲林,检查开窗大小,是否有开窗太大以至露线或露铜
j.所有黑阻焊,阻焊图上不加外形边框线,若需开槽,要在阻焊图上将开槽线亮出来
k.不上阻焊与要上阻焊合拼的,不上阻焊那种文件的阻焊图必须加挡点且铺出外形边框外1mm;
l对于要画沉头孔的板子,在需要画的那面阻焊图上加上沉头孔大小的挡点,以便于操作员区分避免画反;
m.(顾客无特殊要求)阻焊桥未补偿时:
10mil以下阻焊桥开窗,10-20mil阻焊桥不补偿;
n.钻孔图(SK)对照阻焊菲林,检查有无多亮、少亮阻焊。
o.特殊单位亮阻焊的,如康特的阻焊开槽
p.客户要求过孔阻焊,确认阻焊菲林是否正确;孔径12mil阻焊菲林上加5至8mil挡点,孔径12mil以上阻焊菲林上加12mil挡点。
过孔塞孔、BGA塞孔阻焊菲林上不加挡点,孔径小于12MIL,阻焊图上不加挡点。
3.11.文字审核
a.检查客户加工说明表上的字符颜色与生产制作指示填写是否一致;
b.检查顶层字符是否有“反字”,检查底层字符是否有“正字”。
c.将字符菲林对相应的阻焊菲林,看是否有特殊字符标识而没有阻焊挡点的,及重要字符是否有在阻焊上被卡掉的;
d.文字菲林对阻焊菲林,确认文字和文字框是否在板内,若在外型线上或V-CUT线上时须移开,防止成型后文字残缺。
e.如有字符上大锡面(或金面),则应尽量移动字符而不切削字符。
对于顾客允许字符上锡面(或金面)时,工艺流程为“热风整平(沉金)-字符”,在生产制作指示上体现出来。
f.元器件编号和元器件代码同时存在同一器件时,应立即向CAM制作人员反馈并落实其软件版本(如R10和100K同时存在)。
g.文字不能入孔(单面板也不例外);无阻焊菲林可用钻孔图(SK)菲林拍对字符菲林。
h.沉金工艺板,除中光的做先沉金后印字外,其余按喷锡工艺作业。
3.12.标记
a.UL标志
标记
双面孔化板
单面板
b.顾客无特殊要求(指定加于某层、某位置的),标记加在字符层的空白处且阻焊区,不能加在元件字符框内,不得出边框外;不得于数钻、数铣内。
且应不覆盖顾客原设计在线路层或阻焊层的字符、图形,标志应清晰可辨;在添加时,需注意标记方向与板内大多数字符方向保持一致;如有下列情况可不加公司标记(需见客户沟通确认单):
1、制作通知单中或顾客文件要求不加标记;
2、字符层无空余位置时;
3、大小缩至最小比例仍不够空位加入时。
c.板符合《UL产品制作及检验要求》方可添加UL标记。
d.添加UL标记同时必须加上我司厂标和94V-0,尽量将标识加在板边或不显眼的地方,不要与客户的标识加在一起。
3.13.电镀审核
a.35UM基铜板做镀金工艺,有无工艺部门确认。
b.生产制作指示有无按要求填写电流、受镀面积、时间、镍厚、金厚、焊盘面积、消耗金盐量、成品铜厚等。
c.计算方式:
一铜面积,长乘以宽乘以两面;一铜电流:
面积乘以2.5A
3.14.“拼板”工艺
a.SMT加工能力:
MAI:
330X250MIN:
50X50MM。
b.拼板有无满足SMT要求,板边有无马克点、有无模具测试孔。
c.有表贴面必须有马克点的存在。
3.15邮票孔
a.顾客无特殊要求,邮票孔按照孔径1.0mm,孔中心间距1.3mm,1个连接处4个邮票孔进行制作。
如为顾客设计邮票孔,应满足以下条件:
1、0.20mm≤邮票孔孔壁间距≤0.4mm,常规按0.25mm间距设计。
2、每个桥连上邮票孔数量至少需要3个。
3、所有图形板拼板邮票孔按照孔径0.6mm,孔中心间距1.1mm,1个连接处3个邮票孔进行制作。
如不满足上述条件需反馈顾客进行更改,顾客另有要求的除外。
3.16.客户带样件或带图纸抄板审核
a.客户带样件抄板的,用我司菲林资料拍对样件,线路无漏抄、抄变;阻焊无漏亮、多亮现象;文字无漏抄、抄错;焊盘误差±0.1MM;钻孔图(SK)对照样件无明显抄大抄小现象。
b.带图纸抄板的查看图纸是否清晰,线路无漏抄、抄变;阻焊无漏亮、多亮现象;文字无漏抄、抄错;
3.17.拼片加工审核
a.查看袋内工程更改(ECN)更改内容和生产制作指示修改记录和菲林上修改标识;
b.旧菲林拍对新菲林查看是否有加粗线、移线、削焊盘、削铜皮,漏焊盘、多焊盘、文件拼变等问题。
3.18高频材料
a.除我司RO4350双面材料,所有高频板(自带)和多层盲孔板沉铜流程:
沉铜→背光检测→预镀。
b.所有F4B-2材料:
除29所必须收铜外,其它单位不收铜,且将背面大面积铜皮填充,超过成型边框线,“RF”开头的材料,也不收铜。
c.客户要求加工我司F4B-2材料喷锡且上阻焊工艺的,有无与客户沟通达到我司工艺要求。
d.高频材料有无按基铜厚度进行补偿。
f.所有F4B-2材料钻孔后先用整孔剂整孔后刷板沉铜。
3.19.多层板审核
a.多层板内层要挖掉的地方,做文件时内层铜箔不卡掉,但要收铜;目的是减少压合时产生气泡的因素;
b.多层板一面大面积,一面细线路,且开槽交货,在线路面的开槽工艺边上铺铜箔,目的是避免板翘曲;
c.普通多层板内层不要独立挡点,盲孔板:
内层线路上盲孔挡点不去除。
d.F4B-2系列多层板,钻孔后整孔,且钻孔时F4B-2材料必须在最上面。
e.盲孔板叠层注意考虑所加PP厚度、铜箔厚度、镀层厚度;
f.用干膜加工的内层,菲林挡点铺出开料尺寸1.5~2MM。
如图2:
g.所有多层板在区分孔下方加编号。
如图2:
如图2
h、常规多层板开料厚度及PP添加方式:
四层板成品板厚(mm)
芯板(Core)厚度(mm)
PP添加厚度(mm)
2.0
1.2
0.395
2.0
1.0
0.46
1.6
1.0
0.285
1.2
0.6
0.285
1.0
0.4
0.285
0.8
0.4
0.22
0.4
0.2
0.11
六层板成品板厚(mm)
芯板(Core)厚度(mm)
PP添加厚度(mm)
1.6
0.4
1-2层和5-6层加PP0.285,3-4层加PP0.22
2.0
0.6
1-2层和5-6层加PP0.28,3-4层加PP0.22
1.8
0.4
1-2层和5-6层加PP0.28,3-4层加PP0.395
八层板成品板厚(mm)
芯板(Core)厚度(mm)
PP添加厚度(mm)
1.6
0.2
1-2层和7-8层加PP0.285,3-4、5-6层加PP0.22
2.0
0.4
每层之间PP添加0.22
3.20.极化片审核
a.采用干膜加工线路,所有单面板加工作边。
b.文字层加客户文件名和厂标与日期,且成型前印文字方便检验组区分板。
c.检验时采用二次元测量线宽、线距、角度、起始点等,并标注打印。
d.外协化银和镀厚金的板边工艺线必须全部连接在工作边上,增强电镀致密性。
3.21.菲林上的一些状态位置,如下
3.22.第二遍从头到尾一项项核对检查。
3.23.首先再次核对公司内部编号和客户文件名、板材类型、钻孔放大系数、表面工艺、阻焊颜色、文字颜色、标记添加及一些特殊注明事项,以防遗漏;
3.24.发现文件有异常,应立即向CAM制作人员反馈并落实其结果,直至文件合格;
3.25.若客户要求生产的PCB板,严重超出我公司的制程能力,有没有召集工艺、质管各部门的相关人员进行评审表的签写,确定特殊工艺参数后再开始生产。
3.26.将《印制板生产制作指示》和钻孔表盖上受控章进行受控;
3.27.将菲林检查结果记录在《工程资料检验一览表》上。
3.28.菲林封装
3.29.1.用胶膜将菲林封好,且在封装上贴小标签注明单位、文件名,交生产部门
3.29.2.将正确的资料交生产部门,若应急用或出现返工,返修资料不齐须在联络单上注明清楚。
3.30.相应记录有《工程部资料检验一览表》。
编制:
审核:
批准:
生效日期: