纤维缠绕工艺及设备最新进展.docx
《纤维缠绕工艺及设备最新进展.docx》由会员分享,可在线阅读,更多相关《纤维缠绕工艺及设备最新进展.docx(12页珍藏版)》请在冰豆网上搜索。
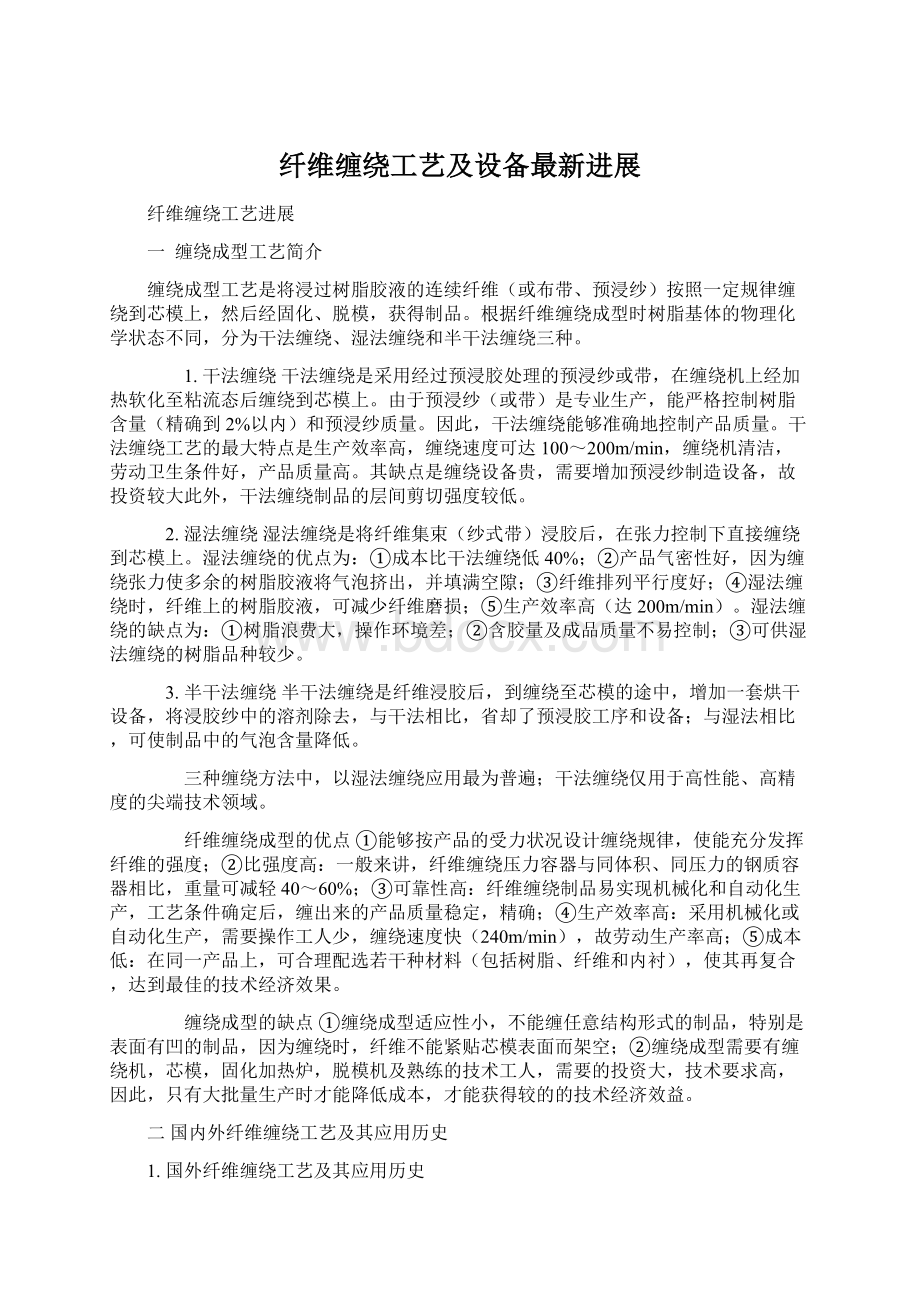
纤维缠绕工艺及设备最新进展
纤维缠绕工艺进展
一缠绕成型工艺简介
缠绕成型工艺是将浸过树脂胶液的连续纤维(或布带、预浸纱)按照一定规律缠绕到芯模上,然后经固化、脱模,获得制品。
根据纤维缠绕成型时树脂基体的物理化学状态不同,分为干法缠绕、湿法缠绕和半干法缠绕三种。
1.干法缠绕干法缠绕是采用经过预浸胶处理的预浸纱或带,在缠绕机上经加热软化至粘流态后缠绕到芯模上。
由于预浸纱(或带)是专业生产,能严格控制树脂含量(精确到2%以内)和预浸纱质量。
因此,干法缠绕能够准确地控制产品质量。
干法缠绕工艺的最大特点是生产效率高,缠绕速度可达100~200m/min,缠绕机清洁,劳动卫生条件好,产品质量高。
其缺点是缠绕设备贵,需要增加预浸纱制造设备,故投资较大此外,干法缠绕制品的层间剪切强度较低。
2.湿法缠绕湿法缠绕是将纤维集束(纱式带)浸胶后,在张力控制下直接缠绕到芯模上。
湿法缠绕的优点为:
①成本比干法缠绕低40%;②产品气密性好,因为缠绕张力使多余的树脂胶液将气泡挤出,并填满空隙;③纤维排列平行度好;④湿法缠绕时,纤维上的树脂胶液,可减少纤维磨损;⑤生产效率高(达200m/min)。
湿法缠绕的缺点为:
①树脂浪费大,操作环境差;②含胶量及成品质量不易控制;③可供湿法缠绕的树脂品种较少。
3.半干法缠绕半干法缠绕是纤维浸胶后,到缠绕至芯模的途中,增加一套烘干设备,将浸胶纱中的溶剂除去,与干法相比,省却了预浸胶工序和设备;与湿法相比,可使制品中的气泡含量降低。
三种缠绕方法中,以湿法缠绕应用最为普遍;干法缠绕仅用于高性能、高精度的尖端技术领域。
纤维缠绕成型的优点①能够按产品的受力状况设计缠绕规律,使能充分发挥纤维的强度;②比强度高:
一般来讲,纤维缠绕压力容器与同体积、同压力的钢质容器相比,重量可减轻40~60%;③可靠性高:
纤维缠绕制品易实现机械化和自动化生产,工艺条件确定后,缠出来的产品质量稳定,精确;④生产效率高:
采用机械化或自动化生产,需要操作工人少,缠绕速度快(240m/min),故劳动生产率高;⑤成本低:
在同一产品上,可合理配选若干种材料(包括树脂、纤维和内衬),使其再复合,达到最佳的技术经济效果。
缠绕成型的缺点①缠绕成型适应性小,不能缠任意结构形式的制品,特别是表面有凹的制品,因为缠绕时,纤维不能紧贴芯模表面而架空;②缠绕成型需要有缠绕机,芯模,固化加热炉,脱模机及熟练的技术工人,需要的投资大,技术要求高,因此,只有大批量生产时才能降低成本,才能获得较的的技术经济效益。
二国内外纤维缠绕工艺及其应用历史
1.国外纤维缠绕工艺及其应用历史
20世纪40年代中期,国际上正式提出了纤维缠绕技术的概念。
纤维缠绕制品的最早应用是1945年制成的玻璃钢环,用于原子弹工程。
1946年,纤维缠绕成型工艺在美国取得专利,1947年美国Kellog公司成功地制成世界上第一台缠绕机,随后缠绕了第一台火箭发动机壳体,直径5英寸,长5英尺。
60年代初期,出现第一代机械式纤维缠绕机,其控制系统是由皮带、齿轮、滑轮和链条等组成的机械系统。
美国宇航局和空军材料研究室用纤维缠绕工艺研制成功“北极星”导弹发动机壳体,在质量减轻1/2、射程提高一倍多的情况下,成本仅为钛合金的1/10,从而奠定了纤维缠绕在制造尖端军用产品(火箭和导弹)中的重要地位。
1973年Entec公司开发了第一台微处理器控制的纤维缠绕机。
1976年第一个商业化标准的缠绕机型号McCleanAnderson60型投放市场。
20世纪60-70年代是纤维缠绕技术飞速发展的阶段,在这一时期,纤维缠绕用的纤维仍然是以玻璃纤维为主导。
但是,随着新纤维的不断问世,纤维缠绕的应用领域也拓宽了,已从军事部门扩展到化工、污水处理、石油及风能系统等重要的民用部门,商用纤维缠绕机也开始在市场上销售,美国的多家公司都在生产各种高压管、污水管等,并缠绕出巨大体积的复合材料产品,如直径8m、38m长的风机叶片和直径10m、容积1000m3的巨型储罐等。
20世纪80~90年代,更多的计算机技术投入到缠绕机的开发当中,新一代微机控制纤维缠绕机开始研制。
英国的Pultrex有限公司采用通用数控系统成功开发了四轴联动纤维数控缠绕机。
当时,每台缠绕机的硬件部分都必须包括计算机和运动控制卡,机床的速度控制得到了极大改善,计算机控制系统能够更精确地跟踪机床的位置和速度并对其进行实时控制。
与此同时,很多公司开始探索用计算机设计缠绕模式,即纤维缠绕CAD技术开始出现。
用计算机辅助设计缠绕模式,大大简化了缠绕模式的设计,从而减少了产品的开发和工艺设计周期。
同时,为了提高生产效率,人产设计开发了多转轴缠绕机,即1台缠绕机同时缠绕多个部件或1台缠绕机上装有多个出纱装置同时缠绕一个部件。
这一时期,纤维缠绕仍然以航空和国防为主,但在民用领域进一步扩展,如水力工程中用于制造各种压力管道、压力容器等。
在此期间,第一台计算机控制的纤维缠绕机问世,使缠绕精度更高、形状更复杂的产品成为可能。
进入20世纪90年代,纤维缠绕技术发展速度明显加快,进入新的高速发展阶段,商用领域进一步扩展到汽车、救生设备、运动器材等,多轴缠绕机已出现并得到发展。
进入21世纪,缠绕机的功能更加完善,各种类型的缠绕机广泛应用于航空航天、军工和民用工业等领域。
纤维缠绕设备的开发速度明显加快,同时提高劳动生产率已被置于首要地位,多主轴、多运动轴联动缠绕机逐渐成为标准。
为了解决异型件的缠绕成型,研制出了计算机控制的六轴联动纤维缠绕机,解决了基本异型件的缠绕成型问题,结束了用手糊、半手糊方式生产常用管道配件——弯管和三通管的历史。
更多运动轴缠绕机的引入使得缠绕形状更为复杂的产品成为可能,目前国际上已有七轴甚至多达十一轴的计算机控制纤维缠绕机。
但由于高性能和大型的缠绕机可用于航空航天等军工部门,国外对我国一直限制出口。
对于中小型缠绕机虽然通过一些渠道可以出口,但价格昂贵,如可缠绕φ1.6m、长度6m压力容器的四轴联动卧式数控缠绕机价格要在40万欧元以上。
国外知名的缠绕机制造商主要有美国的ENTEC公司、McCleanAnderson公司和德国的BSD公司等。
除硬件外,目前国外的纤维缠绕CAD/CAM软件也已经发展到很高的水平。
CAD/CAM软件不仅具有完善的回转体纤维缠绕轨迹设计功能,还具有异型件纤维缠绕轨迹设计功能。
对于各种常见异型件,已经开发出完善的CAD/CAM软件进行芯模设计、线型规划以及后置处理,可以根据具体的数控系统生成相应的控制代码。
如比利时MATERIAL公司的CADWIND和英国CrescentConsultantsLtd的CADFIL,其中CADWIND历时12年研制成功,该CAD/CAM系统受到用户的广泛欢迎,经多年实践,开发了多个版本,其最高版本价格约为4万欧元。
2.我国纤维缠绕工艺及其应用历史
我国对纤维缠绕工艺的研究开始于1958年,其出发点是为“两弹一星”国防建设服务。
60年代初我国开始了纤维缠绕技术的研究。
随着微机和自动化技术的发展,目前国内大部分纤维缠绕设备实现了微机控制,中低档的两轴、三轴微机控制纤维缠绕机制造技术和缠绕工艺已经成熟,并在管道、储罐以及各种压力容器的缠绕成型方面发挥了重要作用。
缠绕理论方面1965年我国完全掌握了缠绕规律和缠绕速比计算方法,实现了螺旋缠绕排线机械化。
1971年起开始研究异型件缠绕,提出了异型件截面的“相当圆假设”原理,解决了异型件截面纤维缠绕的近似计算问题。
1987年提出了网格结构纤维缠绕计算原理,这项新技术的实现,不仅解决了某卫星的关键技术,而且标志着我国纤维缠绕技术进入了一个新的发展阶段。
1996~1998年,一类新的非测地线---拟测地线路径算法被提出,它主要用于回转体的纤维缠绕稳定轨迹设计。
哈尔滨工业大学结合缠绕设备的研制,所开发的缠绕软件Windsoft也愈趋完善,通过不断改进,现已经推出了第3个版本,逐渐成为一套比较成熟的纤维缠绕CAD/CAM软件。
三纤维缠绕设备的创新和发展
纤维缠绕技术是树脂基复合材料制造技术之一,是将连续纤维或布带,预浸纱经过浸胶后,按照一定的方式缠绕到芯模上,然后在一定温度下固化,制成一定形状制品。
纤维缠绕技术经半个多世纪的发展已经完善成熟。
原材料生产已成为一个工业体系;缠绕设备从小到生产几毫米直径的杆件设备大到生产直径二十几米的化工储罐的现场缠绕机;从两轴缠绕机到十几轴的多功能缠绕机。
产品广泛应用于航天、航空、国防和民用工业等领域。
随着纤维缠绕复合材料的高速发展和广泛应用,要求纤维缠绕既具有更高的精度,更高的生产率和更大的柔性,与此相适应,纤维缠绕设备得到极大的发展,并且一些辅助系统也得到了长足的进步。
1.芯模
美国MagnumVenusPlastech(MVP)公司开发的折叠悬臂式芯模可以大大提高生产效率,因为固化后部件易于移走。
这种芯模最适合长度2英寸以上,25英寸以下的部件,可折叠的悬臂梁芯模不需要使用多个芯模,就可以将生产时间缩短50%。
MVP缠绕系统的另一个特点是双芯模驱动设备,缠绕机缠绕架两侧都装有芯模驱动装置,这使缠绕机以更连续的模式进行生产,缠绕在一侧进行的同时,另一侧可以进行维修,移除或准备缠绕状态。
缠绕完成时,缠绕架和铺放头可以旋转180度,将材料输送到相对的一侧进行缠绕。
这种系统的优势在于生产效率的提高和时间的缩短。
该设备无需停机装上或取下芯模,可一直连续缠绕。
MVP双芯模驱动设备
2.高精度树脂浸胶槽
德国BSD公司开发出一种高精度树脂浸胶槽。
它是专为多芯轴缠绕机开发的。
这些单独的收紧臂能抓紧松散的纤维。
特别是在转动区域,可用作纤维断裂传感器。
通常,我们可以利用这个高质量的浸胶槽调整工艺,以减少树脂用量,提高纤维浸润效果。
高精度树脂浸胶槽
3.新型挂线环系统
德国IBK公司开发一种新型挂线环系统,在低缠绕角下改进纤维缠绕,挂线环减少了材料损耗和缠绕时间,挂线针连接成带状并根据芯模直径切割成所需长度。
缠绕前挂线针插入芯模,然后在制品固化后拆下。
新型挂线环系统
4.树脂和纤维控制系统
MVP公司开发了一种能在缠绕过程中控制树脂和纤维使用的系统。
这种系统可以计算正在使用的树脂和纤维用量。
操作者可实时在树脂槽中调整以获取树脂和纤维的合适比例。
另外,在缠绕结束后树脂最终用量能被记录下来。
5.机器人缠绕系统
MFTech公司开发了Pitbull和FOX两个版本的机器人系统。
Pitbull采用机器人传送纤维,将纤维缠绕到固定的旋转芯模上。
现在Pitbull版本可以同时进行五个部件的缠绕。
Pitbull能以2m/秒的速度运送150kg的原料。
FOX系统能够带动芯模,使其旋转,将芯模移到固定的送料系统,FOX可以承受10kg重量,FOX适合压力容器的缠绕而Pitbull适合管道结构件缠绕。
6.径向移动臂和模块化虹吸预浸单元
径向移动臂和模块化虹吸预浸单元的绕丝嘴的引入,极大地改进了湿法缠绕技术。
这种概念以更高效、更经济的方式进行批量生产。
6.1径向移动臂和绕丝嘴
当缠绕压力容器时,有必要减少循环次数。
这可以通过圆周方向几个固定位置上预浸纤维的模拟丝嘴获得。
如果自由纤维长度(丝嘴和芯模之间的距离)要保持连续性,那么绕丝嘴需在径向移动。
在缠绕过程中,必须减少丝嘴轴向运动以便减小缠绕机安装长度。
以前的绕丝嘴不是径向运动的。
GmbH已经开发出这样一种氢气压力容器湿法缠绕的延伸装置,在圆周方向安装八个绕丝嘴(如图4)每个臂相应地浸渍并铺放碳纤维粗纱。
这个系统在相同的工艺速度下输送材料是传统缠绕机的三倍,MaterialS.A的CADWIND软件使其可以自动产生满足绕丝嘴运行的缠绕路径。
绕丝嘴
下图表示的是缠绕过程中的多绕丝嘴缠绕系统。
绕丝头的操控直接与GmbH缠绕机的CNC控制直接相连,并在此处接收位置数据。
程序,可视化都在WindowsPC机上。
使用改进的CADWIND软件程序根据所要求的铺层产生缠绕的路径。
多绕丝嘴缠绕系统
粗纱准确的铺层尤其在封头区域要通过可旋转的绕丝嘴来实现。
这种特别的结构在缠绕圆柱筒壁时保持粗纱宽度一致和充分的树脂浸渍。
6.2模块化虹吸预浸单元
分布在芯模圆周方向上的粗纱预浸和供应是一个难题。
由于商业上的预浸单元对这种工艺有一定的限制而且这种工艺还要求批产,所以开发了一种新的预浸方法。
粗纱通过一个完全封闭的虹吸式预浸单元并由精确剂量的树脂浸润。
另外,减少了苯乙烯(不饱和聚酯树脂)挥发所带来的污染。
粗纱通过绕丝嘴活动臂直接到容器表面并由旋转的导丝头准确地铺放。
耐用性试验证明了这种批产预浸方法的适用性。
预浸单元八小时工作无任何故障,并且粗纱进料管无任何磨损,也无任何纤维破裂。
模块化虹吸预浸单元
使用虹吸式预浸单元绕丝头,成功缠绕了若干压力容器,经检测缠绕层质量符合标准。
例如,孔隙率含量与标准缠绕技术制造的产品孔隙率相似。
除了预浸技术,显著影响空隙率的其它因素包括绕丝嘴本身和是否使用刮胶刀。
检验工作压力为200bar的缠绕容器,爆破压力超过750bar。
模块化虹吸预浸单元缠绕头的发展是湿法缠绕技术的巨大进步。
这种方法的主要优势是极大地提高了铺层率。
对于相同的铺层质量,由绕丝头控制的大量粗纱能够极大地减少芯模完全浸润所要求的时间。
不断改变缠绕线型和减少粗纱交叉点,产生了其他积极效果。
纤维性能的优化利用进一步减轻了重量,缠绕过程中绕丝嘴的径向移动有助于极大地减少支架系统的长度,这不仅减少了循环次数,而且减少了缠绕设备的安装空间。
7.软件和自动化
纤维缠绕的自动化部分归功于有效的控制软件。
控制软件的改进极大地促进了缠绕机和缠绕技术的进步。
布鲁塞尔Materials公司开发的CADWIND2006的新特点包括实时模拟缠绕程序和所有轴上缠绕头的移动。
这种模拟有助于调整铺放头的运动,从而避免铺放头与芯模间可能的接触碰撞,而且还缩短了增加开发时间和成本的多次试验周期,加快了简单和复杂部件的生产速度。
CADWIND2006后处理单元采用一种新算法简化了在部件任一点上夹紧芯模和缠绕启动的过程。
CNCTechnics公司对低成本多功能控制系统软件JOKAM作了改进,并开辟了另外两个应用领域:
一是数控加砂两轴缠绕机,并与芯模的尺寸和旋转相关联,另一种应用是四轴缠绕机生产压缩天然气储罐(CNG)和氢储罐。
加砂和树脂供给这样的数控功能都是自动化生产的特征,可以使整体工艺更快更准确。
四.纤维缠绕发展方向
1. 纤维缠绕工艺的发展方向
随着复合材料相关技术的发展,纤维缠绕工艺呈现出多工艺复合化、热塑性树脂缠绕逐渐增多以及新型固化技术不断应用的发展趋势。
(1)拉挤成型、带铺放、带缠绕及纤维编织、压缩模塑等工艺与传统缠绕工艺相结合,提高了缠绕工艺的适应性。
纤维缠绕技术有一个明显的局限,就是沿制品轴向铺设纯纵向,即0 度纤维(纤维与简体母线夹角为0度较为困难,限制了它在某些结构类管状制品制造中的应用。
将纤维缠绕与带铺放工艺、拉挤工艺结合起来可解决这一问题。
纤维铺放技术集传统缠绕技术与带铺放技术于一身,可进行任意角度缠绕,也可任意增减纤维,还可在凹形表面缠绕,克服了传统缠绕工艺的不足;缠绕一拉挤工艺制造的薄壁管改善了力学性能,已用于汽车司机驾驶室框架一弱;缠绕与注射模塑结合制造的自润滑多面滑动轴承具有卓越的摩擦学行为;纤维缠绕预制件与RTM技术相结合扩大了纤维缠绕工艺的应用范围。
(2)热固性树脂缠绕向热塑性树脂缠绕方向发展。
据统计,从1994年以来,热塑性复合材料是同期热固性复合材料增长的2倍。
该高速增长可以用热塑性复合材料良好的机械性能、高的耐温性、良好的介电常数和良好的可循环性来解释,尤其是它的可回收、可重复利用和不污染环境的特性适应了当今材料环保的发展方向。
欧美一些国家已有一些产品用于航空航天和民用,如美国用CF/PEEK缠绕制件作飞机水平安定面,德国用CF/FA缠绕管件制造超轻质自行车等。
国外已有杜邦公司、帝国化学公司、BASF公司和德国凯瑟斯路登大学等多家大公司和科研机构对热塑性树脂缠绕工艺进行了研究和生产实践。
国内有北京航空材料研究院先进复合材料国防科技重点实
验室等少数机构对热塑性预浸带进行了缠绕实验,并对制品性能进行了初步分析。
可以说国内这种工艺还处在逐步开发的阶段。
发展空间较大。
(3)新型固化技术及在线固化监测技术。
红外加热、微波加热、火焰加热、电子束固化等技术可缩短固化周期,减少残余应力,提高复合材料力学、物理性能,降低成本。
法国航空航天公司已对固体火箭发动机纤维缠绕壳体的电子束固化技术进行了成功演示,其综合性能优于常规的加热固化复合材料。
此外,超声技术以及光纤传感技术等都被用于在线固化监测。
2.纤维缠绕机械的发展方向
随着纤维缠绕复合材料的高速发展和广泛应用,要求纤维缠绕机械具有更高的精度、更高的生产率和更大的柔性。
缠绕机正向着高自动化,高集成化,高产量的方向发展,纤维缠绕机配备精密引力控制系统,以提高缠绕精度;多轴缠绕机越来越得到广泛的应用,使复杂形状产品的制造成为可能。
另外,机器人用于纤维缠绕使其自由度更多、运动更灵活。
缠绕机械的发展极大地促进了纤维缠绕技术进步。
(1)纤维缠绕机开始配备精密张力控制系统,以提高缠绕精度。
在缠绕过程中,缠绕张力与制品的强度、疲劳性有着密切的关系,对缠绕制品的性能影响很大。
哈尔滨工业大学正对微机数控纤维缠绕机精密张力控制系统进行研究,法国则开发出一种用于粗纱的精密缠绕系统。
(2)多轴缠绕机得到应用。
多轴缠绕机既能提高生产率,也使得缠绕形状更为复杂的产品成为可能。
EnTec公司缠绕透平机叶片的计算机控制缠绕机有11个轴;在美国华盛顿州塔科马市建立的复合材料研究开发中心的多轴数控缠绕机可生产长度达4mm的缠绕件,可进行多筒纤维缠绕、树脂自动分配,质量自动控制等,该中心正在研究开发飞轮组件,包括飞轮转子、飞轮外壳等。
(3)与工艺复合化发展方向相适应,缠绕机上也增加了一些辅助装置,如带铺放头、加热和压辊装置、切断装置等。
目前已有许多公司出售热固性和热塑性纤维铺放机,并已成功用于自行车架、机翼梁、小型船身、锥壳及飞机进气口通道等部件的制造。
(4)机器人与缠绕机相结合。
机器人用于纤维缠绕具有自由度多、运动灵活、工艺范围宽等优点,尤其适合缠绕小型复杂构件,包括轴不对称和双凹面部件。
美、欧及加拿大正在研究开发机器人纤维缠绕机,如比利时Leuven天主教大学用一台PUMA-762机器人与两轴数控缠绕机联接,缠绕了多种零件;加拿大OTTAWA大学也用机器人成功缠绕了T型管;德国AACHEN工业大学建成了一个复合材料柔性制造单元,己成功生产出机床主轴、飞机机身等零件;Northop’SVenturaDivision也正在用机器人缠绕导管组件。
另外,CAD、CAM和仿真技术在纤维缠绕工艺和纤维缠绕设备中的应用日益增多,国内外已有一些实用化的软件问世。
CAD、CAM与传统缠绕工艺的结合,有助于缩短产品设计周期、减少废品率、提高制品的质量,能提高自动化水平及生产柔性。
但与传统CAD/CAM技术相比,纤维缠绕CAD/CAM技术的研究才刚刚起步,研究成果有限,远未达到成熟地步。
五.纤维缠绕成型工艺的应用
1.国外纤维缠绕成型工艺的应用
目前,纤维缠绕技术已广泛应用于固体火箭发动机壳体、固体火箭发动机烧蚀衬套、火箭发射筒鱼雷食品舱、飞机机头雷达罩、天线杆、点火器、波导管、连接裙、航天飞机的机械臂,发动机机匣、燃料贮箱、发动机短舱、飞机副油箱导弹、鱼雷发射管、机枪枪架、火箭发射筒等航空航天领域。
C/CFRP是用来制造洲际弹道导弹的鼻锥、发动机喷管和壳体的最好选材,且已实用化。
MK是美国核武库中最为先进的机动洲际弹道导弹。
它的长度为21.3 m,直径2.3 m,发射质量39.5 t。
它不仅鼻锥和喷管喉衬采用了C/CFRP,而且储运发射筒(箱)也采用了芳纶(凯芙拉纤维,KF)的缠绕复合材料。
发射筒长24 m,质量约8.2 t。
KF的优点是质量轻,比强度高,韧性非常好。
固体发动机的喷管是一换能器。
它将壳体内装的推进剂经燃烧转变为热能,再经喷管转变为动能,从而产生推力以推动火箭或导弹克服地球引力向上飞行。
推进剂燃烧时产生的高温高压和高能粒子通过收敛扩散从喷管以3.0~4.5马赫的超音速喷出,喷管承受3 500℃高温、5~15 MPa的压力和高能粒子的冲刷,要求喷管材料需经受这一恶劣环境而不烧损。
特别是喷管喉衬的工作环境最为苛刻,但要求经烧蚀、冲刷而尺寸稳定;否则,喉径尺寸变大,临界截面也随之变化,喷射压力下降,推力也降,最终会导致推重比(发动机推力与起飞质量之比)下降,发射失败。
当前,制造大型火箭或导弹的喷管材料是用 C/CFRP,且已实用化。
固体发动机壳体的轻量化、复合化是提高其性能的有效途径。
固体发动机壳体的制造大多采用缠绕( FW)工艺,所用碳纤维为高强中模型。
目前,CFRP广泛用于战略导弹和发动机壳体,发动机性能得到显著提高。
国外有很多直升机部件采用长丝缠绕工艺方法,这其中有美国贝尔公司的AH—IG夹层结构尾斜梁、B—206垂尾、OH—58的平尾管梁与蒙皮及硬壳式式尾梁;与此同时美国西科斯基公司用缠绕工艺方法研制了S—76的尾梁、水平安定面和斜梁(即ACAP)计划;法国宇航公司也研制了缠绕成形的复合材料尾梁替代海豚直升机铝合金面板的夹层结构尾梁。
国外缠绕工艺方法还用到LHX计划、EH101起落架部件和操纵系统拉杆及传动系统的传动轴。
随着缠绕技术的不断发展,其应用已逐步扩大到某些机体结构,如全复合材料小型飞机“星舟”号的原型机机身。
当前直升机上可采用缠绕成形的部件除机身和尾梁外有:
翼面结构,如桨叶、平尾、垂尾、桨叶根部、旋翼轴、起落架零件(横管、摇臂和缓冲支柱外筒等)、操纵杆件、传动轴等旋转体部件。
1.座舱骨架
早期的座舱骨架一般由铝合金梯形管通过组成,各在定位型架上成型。
随着复合材料的应用和发展,现代直升机为了减小结构重量系数,降低成本等目的而采用复合材料整体设计和制造技术。
座舱骨架由于其截面形状多为四边形和多边形。
因此选用复合材料制造时,一般采取预浸料铺放或缠绕的方法制造。
同样,采用长丝缠绕制造也是可行的,而且有其特有的优势。
制造时可将其分为若干段管梁进行缠绕,然后通过胶接加铆(螺)接的方法装配而成。
2.机身中段
机身中段结构是直升机的主承力构件,其结构形状为近似四边形或多边形,适宜采用缠绕工艺方法制造。
但此处协调关系多,开口我,受力复杂,且为直升机的主承力部分,采用缠绕技术进行设计和制造有一定困难,需精心设计,可作为缠绕技术在直升机上的一个发展方向。
据资料介绍,战术运输直升机NH—90的机身是用缠绕工艺方法制成,其机身是菱形横截面,宽度约2米多,如此庞大的机身结构缠绕方法制造成功,在国际上是首例,是复合材料设计和新工艺成功的一个创举。
3.尾梁
直升机尾梁结构多为截面形状为圆形、长圆形四边形、多边形的锥体,因而非常适合采用复合材料纤维缠绕整体成型的工艺方法制造。
美国西科斯基公司ACAP计划设计的S—76全复合材料机身结构,其尾梁就采用了长纤维(石墨纤维/环氧树脂)缠绕成形。
4.水平安定面、斜梁等翼面结构
水平安定面及斜梁若采用长纤维缠绕成形后,则可以采取以下两种方法:
仅受力盒段采用缠绕技术制造
先计算好翼面结构两端翼形截面的周向长度,由于其为直母线结构,因而可将其先制成圆形或长圆形锥(柱)体结构,再通过上下对合模对其整形、固化制成最终形状。
5.起落架零部件
普通起落架一般选用金属材料制造,重量代价相当大。
若采用复合材料制造,着重效果十分明显。
特别是起落架零部件多为旋转体结构,如横管、摇臂、减震支柱的外筒等,这为起落架零部件采用缠绕成形技术提