基于plc的加工中心刀库换刀控制系统设计.docx
《基于plc的加工中心刀库换刀控制系统设计.docx》由会员分享,可在线阅读,更多相关《基于plc的加工中心刀库换刀控制系统设计.docx(55页珍藏版)》请在冰豆网上搜索。
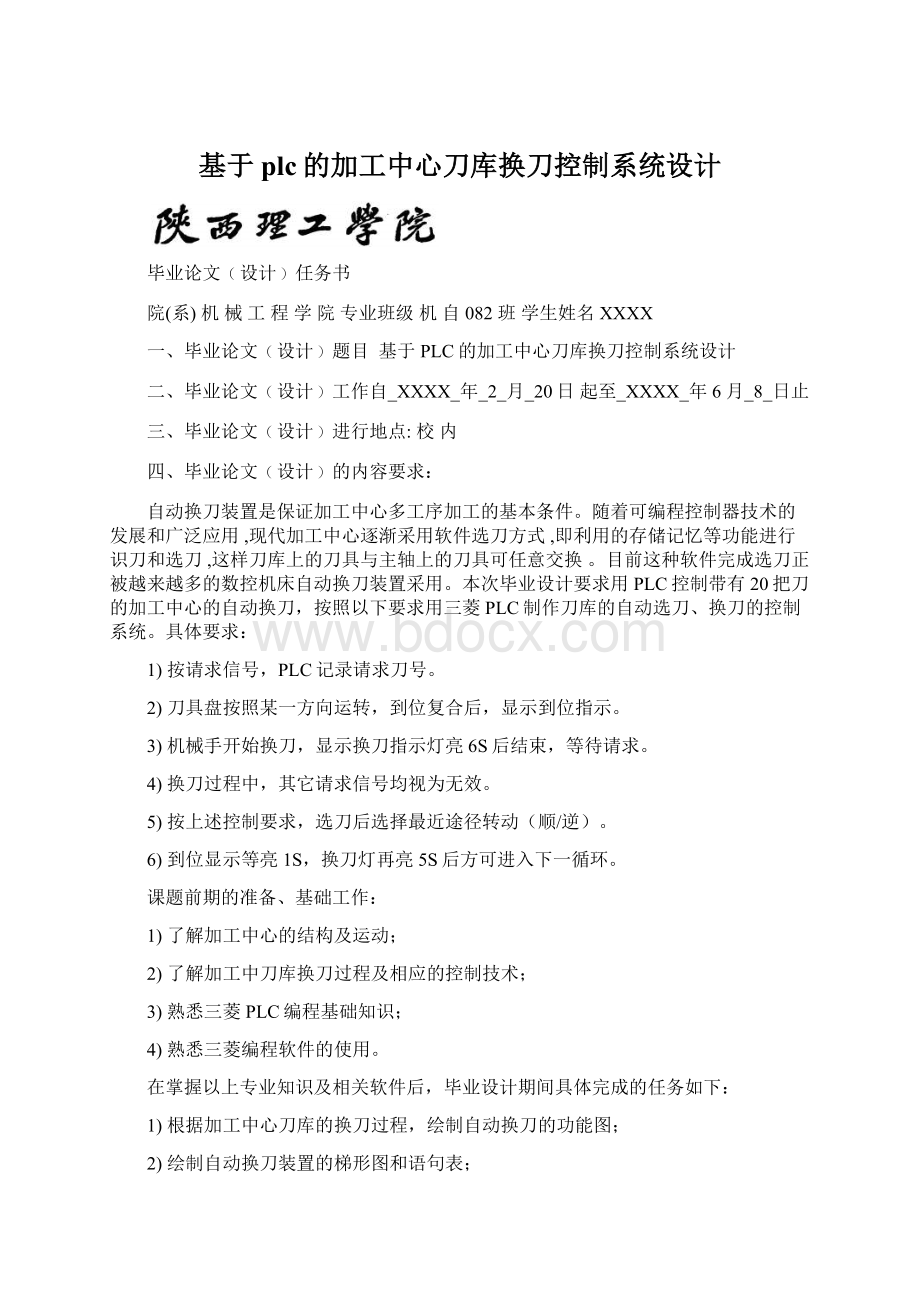
基于plc的加工中心刀库换刀控制系统设计
毕业论文﹙设计﹚任务书
院(系)机械工程学院专业班级机自082班学生姓名XXXX
一、毕业论文﹙设计﹚题目基于PLC的加工中心刀库换刀控制系统设计
二、毕业论文﹙设计﹚工作自_XXXX_年_2_月_20日起至_XXXX_年6月_8_日止
三、毕业论文﹙设计﹚进行地点:
校内
四、毕业论文﹙设计﹚的内容要求:
自动换刀装置是保证加工中心多工序加工的基本条件。
随着可编程控制器技术的发展和广泛应用,现代加工中心逐渐采用软件选刀方式,即利用的存储记忆等功能进行识刀和选刀,这样刀库上的刀具与主轴上的刀具可任意交换。
目前这种软件完成选刀正被越来越多的数控机床自动换刀装置采用。
本次毕业设计要求用PLC控制带有20把刀的加工中心的自动换刀,按照以下要求用三菱PLC制作刀库的自动选刀、换刀的控制系统。
具体要求:
1)按请求信号,PLC记录请求刀号。
2)刀具盘按照某一方向运转,到位复合后,显示到位指示。
3)机械手开始换刀,显示换刀指示灯亮6S后结束,等待请求。
4)换刀过程中,其它请求信号均视为无效。
5)按上述控制要求,选刀后选择最近途径转动(顺/逆)。
6)到位显示等亮1S,换刀灯再亮5S后方可进入下一循环。
课题前期的准备、基础工作:
1)了解加工中心的结构及运动;
2)了解加工中刀库换刀过程及相应的控制技术;
3)熟悉三菱PLC编程基础知识;
4)熟悉三菱编程软件的使用。
在掌握以上专业知识及相关软件后,毕业设计期间具体完成的任务如下:
1)根据加工中心刀库的换刀过程,绘制自动换刀的功能图;
2)绘制自动换刀装置的梯形图和语句表;
3)根据提供的元器件,搭建自动换刀装置的控制面板;
4)整理并编写设计计算说明书一份,要求条理清楚、论述有据。
指导教师XX系(教研室)XX
系(教研室)主任签名XX批准日期XX
接受论文(设计)任务开始执行日期XX学生签名XXX
基于PLC的加工中心刀库换刀控制系统设计
[摘要]本设计的题目是基于PLC加工中心刀库换刀控制系统的设计。
通过分析刀库的自动换刀的过程,使刀库在加工中心上能配合换刀机械手的需要——能在数控程序的控制下灵活的实现换刀过程每次换新刀只需输入相应换刀号信号即可。
在分析控制要求的基础上,设计出相应控制程序。
控制程序包含:
建立当前刀具库映像、记录请求刀具号、转盘转动方向判断并确定转盘正反转、发出脉冲控制刀盘转动、到位灯及换刀指示灯显示等部分,程序结构性好、可读性强、运行效率高,能很好地满足实用要求。
[关键词]加工中心,刀库换刀,PLC
BasedonthePLCMachiningCenterToolChangeControlSystemDesign
(ShaanxiInstituteofMechanicalEngineeringCollegeofmechanicalengineeringandautomationprofessionalmachinefromclass082,ShaanxiHanzhoung723003)
Teacher:
[Abstract]thisdesigntopicisbasedonthePLCmachiningcentertoolchangecontrolsystemdesign.Throughtheanalysisoftheknifeoftheautomatictoolchangingprocess,sothatthecutterinmachiningcentercanbematchedwiththetoolchangingmanipulatorneeds--inNCprogramunderthecontrolofflexibleimplementationtoolchangingprocesseverytimenewknifeonlyneedstoinputthecorrespondingtoolchangesignalcanbe.Theanalysisandcontrolonthebasisoftherequirements,designsthecorrespondingcontrolprocedure.Thecontrolprogramincludes:
establishthelibraryimage,recordingrequesttoolnumber,therotationoftheturntabledirectionjudgmentandtodeterminetheturntableisreversed,tosendpulsestocontrolthecutterdisctorotateinplace,lightsandtoolchangeindicatordisplayparts,goodprogramstructure,readabilityisstrong,operationefficiencyishigh,whichcanmeetthepracticalrequirements.
[Keywords]MC,changingtool,PLC
引言
进入21世纪,我国机床制造业既面临着提升机械制造业水平的需求而引发的良机,也遭遇到加入WTO(世界贸易组织)后激烈的市场竞争压力。
从技术层面上来讲,加速推进数控技术将是解决机床制造业持续发展的一个关键。
装备制造业的技术水平和现代化程度决定着整个国民经济的水平和现代化程度。
当今世界各国制造业广泛采用数控技术,以提高制造能力和水平,提高对动态多变市场的适应能力和竞争能力。
此外,世界上各工业发达国家还将数控技术及数控装备列为国家的战略物资,不仅采取重大措施来发展自己的数控技术及其产业,而且在“高精尖”数控关键技术和装备方面对我国实行限制政策。
数控技术是用数字信息对机械运动和工作过程进行控制的技术是现代化工业生产中的一门新型的发展十分迅速的高技术,数控装备是以数控技术为代表的新技术对传统制造业和新兴制造业的渗透形成机电一体化产品。
其及技术范围所覆盖的范围有,机械制造技术,微电子技术,信息处理,加工,传输技术,自动控制技术,伺服驱动技术,检测监控技术,传感技术,软件技术等。
在提高生产率,减低成本保证加工质量及改善工人劳动强度等方面,都有突出的优点,特别是在适应机械产品迅速更新换代,小批量,多品种生产方面,各类数控装备是实现制造技术的关键。
数控加工中心是目前世界上产量最高、应用最广泛的数控机床之一。
它的综合加工能力较强,工件一次装夹后能完成较多的加工内容,加工精度较高,就中等加工难度的批量工件,其效率是普通设备的5~10倍,特别是它能完成许多普通设备不能完成的加工,对形状较复杂,精度要求高的单件加工或中小批量多品种生产更为适用。
数控加工中心是一种功能较全的数控加工机床。
它把铣削、镗削、钻削、攻螺纹和切削螺纹等功能集中在一台设备上,使其具有多种工艺手段。
加工中心设置有刀库,刀库中存放着不同数量的各种刀具或检具,在加工过程中由程序自动选用和更换。
这是它与数控铣床、数控镗床的主要区别。
特别是对于必需采用工装和专机设备来保证产品质量和效率的工件,采用加工中心加工,可以省去工装和专机。
这会为新产品的研制和改型换代节省大量的时间和费用,从而使企业具有较强的竞争能力。
数控加工中心是一种带有刀库并能自动更换刀具,对工件能够在一定的范围内进行多种加工操作的数控机床。
在加工中心上加工零件的特点是:
被加工零件经过一次装夹后,数控系统能控制机床按不同的工序自动选择和更换刀具;自动改变机床主轴转速、进给量和刀具相对工件的运动轨迹及其它辅助功能,连续地对工件各加工面自动地进行钻孔、锪孔、铰孔、镗孔、攻螺纹、铣削等多工序加工。
由于加工中心能集中地、自动地完成多种工序,避免了人为的操作误差、减少了工件装夹、测量和机床的调整时间及工件周转、搬运和存放时间,大大提高了加工效率和加工精度,所以具有良好的经济效益。
加工中心按主轴在空间的位置可分为立式加工中心与卧式加工中心。
加工中心是目前世界上产量最高,应用最广泛的数控机床之一,他是适应省力,省时和节能的时代要求而迅速发展起来的自动换刀机床,是综合了机械技术,电子技术等等的高技术产品。
加工中心综合能力较强,工件经一次装夹后能完成较多的加工内容其效率是普通机床的五到十倍特别是它能完成许多普通设备不能完成的加工,对新装复杂的,精度要求高的单件产品或小批量多品种生产更适用。
加工中心不仅提高了共建的加工质量,而且是数控机床中生产率和自动化程度最高的综合性机床。
加工中心(MachiningCenter)简称MC,是由机械设备与数控系统组成的使用于加工复杂形状工件的高效率自动化机床。
加工中心又叫电脑锣。
加工中心备有刀库,具有自动换刀功能,对工件一次装夹后进行多工序加工的数控机床。
加工中心是高度机电一体化的产品,工件装夹后,数控系统能控制机床按不同工序自动选择、更换刀具,自动对刀、自动改变主轴转速、进给量等,可连续完成钻、镗、铣、铰、攻丝等多种工序。
因而大大减少了工件装夹时间,测量和机床调整等辅助工序时间,对加工形状比较复杂,精度要求较高,品种更换频繁的零件具有良好的经济效果。
加工中心的由来
加工中心最初是从数控铣床发展而来的。
与数控铣床相同的是,加工中心同样是由计算机数控系统(CNC)、伺服系统、机械本体、液压系统等各部分组成。
但加工中心又不等同于数控铣床,加工中心与数控铣床的最大区别在于加工中心具有自动交换刀具的功能,通过在刀库安装不同用途的刀具,可在一次装夹中通过自动换刀装置改变主轴上的加工刀具,实现钻、镗、铰、攻螺纹、切槽等多种加工功能。
加工中心的分类
一、加工中心按加工工序可分分镗铣与车铣两大类。
(1)镗铣
(2)车铣
二、按控制轴数可分为:
(1)三轴加工中心
(2)四轴加工中心
(3)五轴加工中心。
三、以主轴与工作台相对位置分类,分为卧式、立式和万能加工中心。
(1)卧式加工中心:
是指主轴轴线与工作台平行设置的加工中心,主要适用于加工箱体类零件。
(2)立式加工中心:
(VerticalMachiningCenter)是指主轴轴线与工作台垂直设置的加工中心,主要适用于加工板
类、盘类、模具及小型壳体类复杂零件。
(3)万能加工中心(又称多轴联动型加工中心):
是指通过加工主轴轴线与工作台回转轴线的角度可控制联动变化,完成复杂
空间曲面加工的加工中心。
适用于具有复杂空间曲面的叶轮转子、模具、刃具等工件的加工。
多工序集中加工的形式扩展到了其他类型数控机床,例如车削中心,它是在数控车床上配置多个自动换刀装置,能控制三个以上的坐标,除车削外,主轴可以停转或分度,而由刀具旋转进行铣削、钻削、铰孔和攻丝等工序,适于加工复杂的旋转体零件。
加工中心按主轴的布置方式分为立式和卧式两类。
卧式加工中心一般具有分度转台或数控转台,可加工工件的各个侧面;也可作多个坐标的联合运动,以便加工复杂的空间曲面。
立式加工中心一般不带转台,仅作顶面加工。
此外,还有带立、卧两个主轴的复合式加工中心,和主轴能调整成卧轴或立轴的立卧可调式加工中心,它们能对工件进行五个面的加工。
加工中心的自动换刀装置由存放刀具的刀库和换刀机构组成。
刀库种类很多,常见的有盘式和链式两类。
链式刀库存放刀具的容量较大。
换刀机构在机床主轴与刀库之间交换刀具,常见的为机械手;也有不带机械手而由主轴直接与刀库交换刀具的,称无臂式换刀装置。
加工中心的发展史
第一台加工中心是1958年由美国卡尼-特雷克公司首先研制成功的。
它在数控卧式镗铣床的基础上增加了自动换刀装置,从而实现了工件一次装夹后即可进行铣削、钻削、镗削、铰削和攻丝等多种工序的集中加工。
二十世纪70年代以来,加工中心得到迅速发展,出现了可换主轴箱加工中心,它备有多个可以自动更换的装有刀具的多轴主轴箱,能对工件同时进行多孔加工。
加工中心定期检查项目
1)主轴在额定最高转速下运转轴承状态测振仪
2)设备水平检测水平仪
3)X/Y/X轴相互垂直度检测方箱/角尺
4)X/Y/Z轴重复定位精度检测激光干涉仪(视设备品牌可以自动补偿)
5)X/Y/Z轴累计误差检测激光干涉仪(视设备品牌可以自动补偿)
6)主轴300mm径向跳动检测
7)主轴与工作台面的垂直度检测
8)X/Y/Z轴滚珠丝杠轴承状态检测、
9)X/Y/Z轴丝杠状态检测
在数控加工中心,目前的编程方法通常有两种:
①简单轮廓——直线、圆弧组成的轮廓,直接用数控系统的G代码编程。
②复杂轮廓——三维曲面轮廓,在计算机中用自动编程软件(CAD/CAM)画出三维图形,根据曲面类型设定各种相应的参数,自动生成数控加工程序。
以上两种编程方法基本上能满足数控加工的要求。
但加工函数方程曲线轮廓时就很困难,因为早期的铣床数控系统不具备函数运算功能,直接用G代码不能编制出函数方程曲线的加工程序,(版本较低的)CAD/CAM软件通常也不具备直接由方程输入图形的功能。
所以切削函数方程曲线轮廓,目前通常使用的方法是:
根据图纸要求,算出曲线上各点的坐标,再根据算出的坐标值用直线或圆弧指令代码编制程序,手工输入系统进行加工。
本设计是某数控加工中心的换刀控制系统,实现基于PLC的自动换刀控制,刀具库由二十种刀具、换刀转盘和取放刀机械手组成。
该刀具库SB1~SB10按钮控制选择二十种刀具,由霍尔元件构成的行程开关ST1~ST20进行刀具到位限位,机械手进行换取刀具。
1PLC在加工中心中的应用
随着我国新型工业化的进程,数控加工中心等机床在机械制造业中的应用范围和水平有了很大的提高,特别是箱体类零件和复杂曲面零件非常适合在加工中心上完成多工序加工。
加工中心是目前世界上产量最高、应用最为广泛的一种数控机床,加工中心综合机床为了能在工件一次装夹中完成多种工序的加工,以缩短辅助时间,减少多次安装工件所引起的误差,必须带有ATC(自动换刀)装置,因此加工中心的加工能力和效率比普通的数控铣床有了很大的提高。
自动换刀系统的性能将直接影响机床的换刀效率和机床的加工性能。
由于加工中心是一种高技术含量的机电一体化产品,自动换刀装置的控制系统本身及相关机械结构的复杂,因此在实际的生产维护、维修过程中,需要技术人员具备较高的机电复合知识和技能。
1.1数控加工中心组成结构及工作过程
本例数控机床有输入、输出装置、可编程控制器、伺服系统、检测反馈装置和机床主机等组成。
如下图1.1所示:
图1.1数控机床组成机构图
输入装置可将不同加工信息传递给计计算机。
在数控机床产生的初期,输入装置为穿孔纸带,现已趋于淘汰;目前,使用键盘、磁盘等,大大方便了信息输入工作。
输出指输出内部工作参数(含机床正常、理想工作状态下的原始参数,故障诊断参数等),一般在机床刚工作状态需输出这些参数做记录保存,带工作一段时间后,再将输出与原始资料做比较、对照,可帮助判断机床工作是否维持正常。
数控装置只数控机床的核心与主导,完成所有加工数据的处理、计算工作,最终实现数控机床个功能的指挥工作。
它包含为计算机的电路,各种借口电路、CRT显示器等硬件及相应软件。
可编程控制器对主轴单元实现控制,将程序中的转速指令进行处理而控制主轴转速;管理刀库,进行自动刀具交换、选刀方式、刀具累计使用次数、刀具剩余寿命及道具刃磨次数等管理;控制主轴正反转和停止、准停、切削液开关、卡盘夹紧松开、机械手取送刀等动作;还对机床外部开关(行程开关、压力开关、温控开关等)进行控制;对输出信号(刀库、机械手、回转工作台等)进行控制。
检测反馈装置由检测元件和相应的电路组成,主要是检测速度和位移,并将信息反馈与数控装置,实现闭环控制以保证数控机床加工精度。
数控机床的工作过程如下图1.2所示
图1.2数控机床的工作过程
数控加工的准备过程比较复杂,内容多,含对零件的结构认识、工艺分析、工艺方案的制定、加工程序的编制、选用工装及使用方法等。
机床的调整主要包括刀具命名、调入刀库、工件安装、对刀、测量刀位、机床各部件状态等多项工作内容。
程序调试主要是对程序本身的逻辑问题及其设计合理性进行检查和调整。
试切成功后方可对零件进行正式加工,并对加工后的零件进行结果检测。
前三步均为待机时间,为提高工作效率,希望待机时间越短越好,越有利于机床合理使用。
该项指标直接影响对机床利用率的评价即(机床实动率)。
1.2数控机床中PLC和NC的关系
PLC用于通用设备的自动控制,称为可编程控制器。
PLC用于数控机床的外围辅助电气的控制,称为可编程序机床控制器。
因此,在很多数控系统中将其称之为PMC(programmablemachinetoolcontroller)。
控制系统有两大部分,一是NC、二是PLC,这两者在数控机床所起的作用范围是不相同的。
可以这样来划分NC和PLC的作用范围
数控系统有两大部分,一是NC、二是PLC,这两者在数控机床所起的作用范围是不相同的。
1、实现刀具相对于工件各坐标轴几何运动规律的数字控制。
这个任务是由NC来完成;2、机床辅助设备的控制是由PLC来完成。
它是在数控机床运行过程中,根据CNC内部标志以及机床的各控制开关、检测元件、运行部件的状态,按照程序设定的控制逻辑对诸如刀库运动、换刀机构、冷却液等的运行进行控制。
相对于PLC,机床和NC就是外部。
编PLC程序要用到NC给PLC的信号和PLC给NC的信号是为了PLC与NC之间的信息交换。
可编程控制器(PLC)与数控系统(NC)以及数控机床(MT)之间的信息交换有以下信号:
相对于PLC,机床和NC就是外部。
PLC与机床以及NC之间的信息交换,对于PLC的功能发挥,是非常重要的。
PLC与外部的信息交换,通常有四个部分:
(1)机床侧至PLC:
机床侧的开关量信号通过I/O单元接口输入到PLC中,除极少数信号外,绝大多数信号的含义及所配置的输入地址,均可由PLC程序编制者或者是程序使用者自行定义。
数控机床生产厂家可以方便的根据机床的功能和配置,对PLC程序和地址分配进行修改。
(2)PLC至机床:
PLC的控制信号通过PLC的输出接口送到机床侧,所有输出信号的含义和输出地址也是由PLC程序编制者或者是使用者自行定义。
(3)NC至PLC:
CNC至PLC:
CNC送至PLC的信息可由CNC直接送入PLC的寄存器中,所有CNC送至PLC的信号含义和地址(开关量地址或寄存器地址)均由CNC厂家确定,PLC编程者只可使用不可改变和增删。
如数控指令的M、S、T功能,通过CNC译码后直接送入PLC相应的寄存器中。
(4)PLC至CNC:
PLC送至CNC的信息也由开关量信号或寄存器完成,所有PLC送至CNC的信号地址与含义由CNC厂家确定,PLC编程者只可使用,不可改变和增删。
PLC在数控机床中的控制功能:
(1)操作面板的控制。
操作面板分为系统操作面板和机床操作面板。
系统操作面板的控制信号先是进入NC,然后由NC送到PLC,控制数控机床的运行。
机床操作面板控制信号,直接进入PLC,控制机床的运行。
(2)机床外部开关输入信号。
将机床侧的开关信号输入到送入PLC,进行逻辑运算。
这些开关信号,包括很多检测元件信号(如:
行程开关、接近开关、模式选择开关等等)(3)输出信号控制:
PLC输出信号经外围控制电路中的继电器、接触器、电磁阀等输出给控制对象。
(4)功能实现。
系统送出T指令给PLC,经过译码,在数据表内检索,找到T代码指定的刀号,并与主轴刀号进行比较。
如果不符,发出换刀指令,刀具换刀,换刀完成后,系统发出完成信号。
(5)M功能实现。
系统送出M指令给PLC,经过译码,输出控制信号,控制主轴正反转和启动停止等等。
M指令完成,系统发出完成信号。
A、实现刀具相对于工件各坐标轴几何运动规律的数字控制。
这个任务是由NC来完成;
B、机床辅助设备的控制是由PLC来完成。
它是在数控机床运行过程中,根据CNC内部标志以及机床的各控制开关、检测元件、运行部件的状态,按照程序设定的控制逻辑对诸如刀库运动、换刀机构、冷却液等的运行进行控制。
在数控机床中这两种控制任务,是密不可分的,它们按照上面的原则进行了分工,同时也按照一定的方式进行连接。
NC和PLC的接口方式遵循国际标准“ISSO4336-1981(E)机床数字控制-数控装置和数控机床电气设备之间的接口规范”的规定,接口分为四种类型:
a、与驱动命令有关的连接电路;
b、数控装置与测量系统和测量传感器间的连接电路;
c、电源及保护电路;
d、通断信号及代码信号连接电路;
从接口分类的标准来看,第一类、第二类连接电路传送的是数控装置与伺服单元、伺服电机、位置检测以及数据检测装置之间的控制信息。
第三类是由数控机床强电电路中的电源控制控制电路构成。
通常由电源变压器、控制变压器、各种断路器、保护开关、继电器、接触器等构成。
为其他电机、电磁阀、电磁铁等执行元件供电。
这些相对于数控系统来讲,属于强电回路。
这些强电回路是不能够和控制系统的弱电回路直接相连接的,只能够通过中间继电器等电子元器件转换成直流低压下工作的开关信号,才能够成为PLC或继电器逻辑控制电路的可接受的电信号。
反之,PLC或继电器逻辑控制来的控制信号,也必须经过中间继电器或转换电路变成能连接到强电线路的信号,再由强电回路驱动执行元件工作。
第四类信号是数控装置向外部传送的输入输出控制信号。
1.3PLC在数控机床中的应用
1.3.1PLC在数控机床中的应用形式
PLC在数控机床中应用,通常有两种形式:
一种称为内装式;一种称为独立式。
内装式PLC也称集成式PLC,采用这种方式的数控系统,在设计之初就将NC和PLC结合起来考虑,NC和PLC之间的信号传递是在内部总线的基础上进行的,因而有较高的较高交换速度和较宽的信息通道。
它们可以共用一个CPU也可以是单独的CPU这种结构从软硬件整体上考虑,PLC和NC之间没有多余的导线连接,增加了系统的可靠性,而且NC和PLC之间易实现许多高级功能。
PLC中的信息也能通过CNC的显示器显示,这种方式对于系统的使用具有较大的优势。
高档次的数控系统一般都采用这种形式的PLC。
独立式PLC也称外装式PLC,它独立于NC装置,具有独立完成控制功能的PLC。
在采用这种应用方式式,可根据用户自己的的特点,选用不同专业PLC厂商的产品,并且可以更为方便的对控制规模进行调整。
1.3.2PLC与数控系统及数控机床间的信息交换
相对于PLC,机床和NC就是外部。
PLC与机床以及NC之间的信息交换,对于PLC的功能发挥,是非常重要的。
PLC与外部的信息交换,通常有四个部分:
(1)机床侧至PLC:
机床侧的开关量信号通过I/O单元接口输入到PLC中,除极少数信号外,绝大多数信号的含义及所配置的输入地址,均可由PLC程序编制者或者是程序使用者自行定义。
数控机床生产厂家可以方便的根据机床的功能和配置,对PLC程序和地址分配进行修改。
(2)PLC至机床:
PLC的控制信号通过PLC的输出接口送到机床侧,所有输出信号的含义和输出地址也是由PLC程序编制者或者是使用者自