造气岗位培训教材模板.docx
《造气岗位培训教材模板.docx》由会员分享,可在线阅读,更多相关《造气岗位培训教材模板.docx(14页珍藏版)》请在冰豆网上搜索。
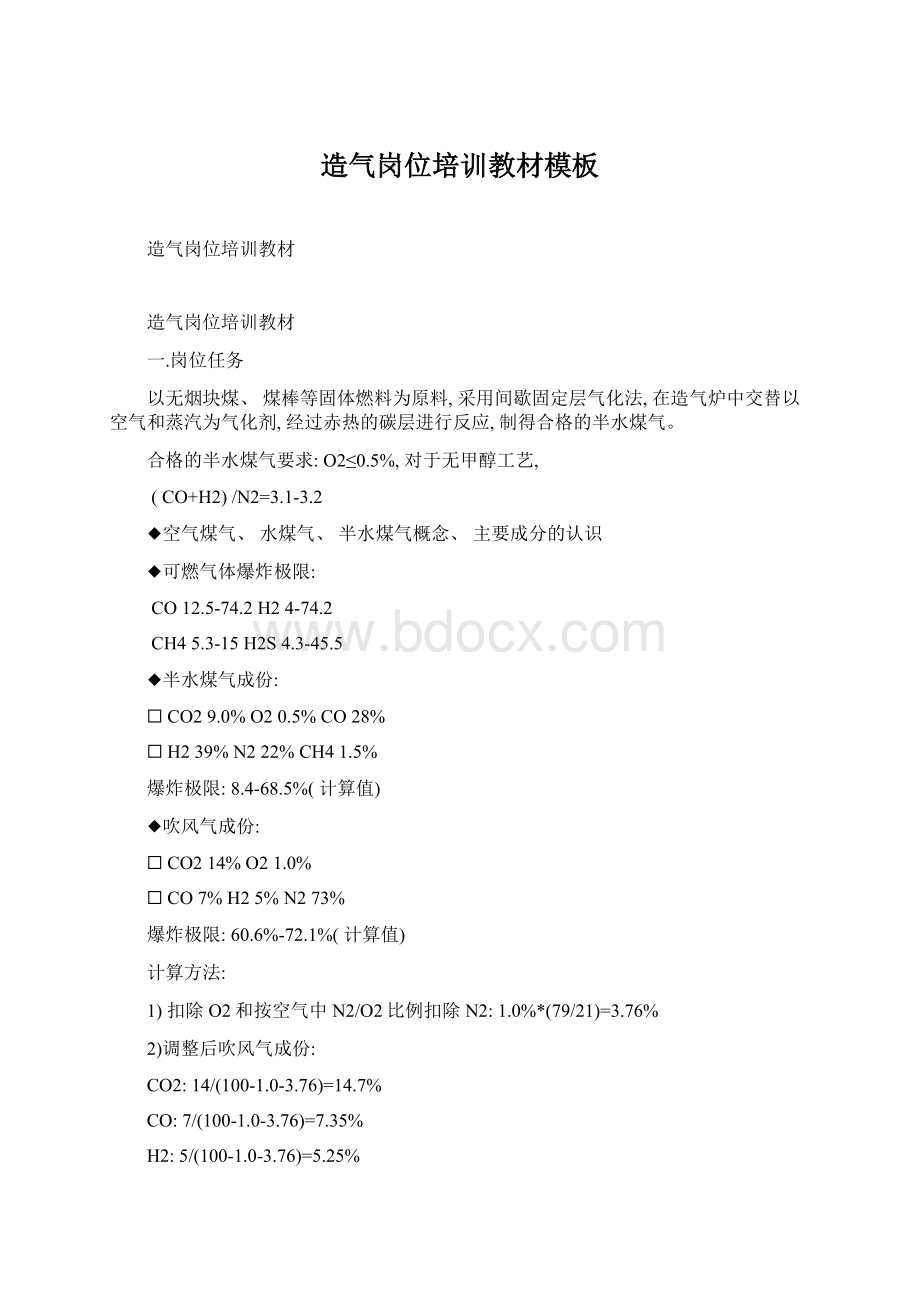
造气岗位培训教材模板
造气岗位培训教材
造气岗位培训教材
一.岗位任务
以无烟块煤、煤棒等固体燃料为原料,采用间歇固定层气化法,在造气炉中交替以空气和蒸汽为气化剂,经过赤热的碳层进行反应,制得合格的半水煤气。
合格的半水煤气要求:
O2≤0.5%,对于无甲醇工艺,
(CO+H2)/N2=3.1-3.2
◆空气煤气、水煤气、半水煤气概念、主要成分的认识
◆可燃气体爆炸极限:
CO12.5-74.2H24-74.2
CH45.3-15H2S4.3-45.5
◆半水煤气成份:
☐CO29.0%O20.5%CO28%
☐H239%N222%CH41.5%
爆炸极限:
8.4-68.5%(计算值)
◆吹风气成份:
☐CO214%O21.0%
☐CO7%H25%N273%
爆炸极限:
60.6%-72.1%(计算值)
计算方法:
1)扣除O2和按空气中N2/O2比例扣除N2:
1.0%*(79/21)=3.76%
2)调整后吹风气成份:
CO2:
14/(100-1.0-3.76)=14.7%
CO:
7/(100-1.0-3.76)=7.35%
H2:
5/(100-1.0-3.76)=5.25%
N2:
(73-3.76)/(100-1.0-3.76)=72.7%
3)惰气和可燃气进行组合:
CO+CO2=22.5%CO2/CO=2
H2+N2=77.95%N2/H2=13.8
4)查表:
CO+CO2爆炸极限为:
49%-60%
H2+N2爆炸极限为:
65%-76.5%
5)计算吹风气爆炸极限:
下限:
100/{(22.05/49)+(77.95/65)}=60.6%
上限:
100/{(22.05/60)+(77.95/76.5)}=72.1%
◆可燃气体和惰气混合后其比率(惰/燃)在下列情况下不爆炸:
N2/H2>16.5N2/CO>4.1N2/CH4>6
CO2/H2>10.2CO2/CO>2.2CO2/CH4>3.3
◆对氧指标控制的认识:
(1)半水煤气
在爆炸极限内氧含量对应值:
下限:
(100%-8.4%)*21%=19.24%
上限:
(100%-68.5%)*21%=6.6%
上述仅是理论计算,生产中为确保安全,当半水煤气中氧含量上升至2%时,必须进行紧急停车。
(2)吹风气
在爆炸极限内氧含量对应值:
下限:
(100%-60.6%)*21%=8.3%
上限:
(100%-72.1%)*21%=5.8%
经计算:
当吹风气中CO+H2<10%,O2<1.0%时,其惰气与可燃气比率在爆炸范围之外,为确保安全,用吹风气作惰气置换时一般控制CO+H2<8%,O2<0.5%。
需要指出:
浓度极限的存在并不意味着达不到这个界限时,气体就不会燃烧,实际上,把浓度小于下限的可燃物加热(用外热)到高温后,将它们点着也能燃尽。
在浓度极限之内和之外燃烧的根本区别,在于前者的火焰在其中能够自行传播发生爆炸,而后者不能。
二、生产原理:
1.气化过程主要反应式:
造气炉内固体燃料的气化过程,实际上主要是碳与氧的反应和碳与蒸汽的反应,这两个反应为固体燃料的气化反应。
A以空气为气化剂的反应
C+O2=CO2+401.9KJ/mol
2C+O2=2CO+118.5KJ/mol
C+CO2=2CO-164.96KJ/mol
2CO+O2=2CO2+31.5KJ/mol
以空气为气化剂的目的是提高炉温为蒸汽转化制煤气创造条件,为抑制CO的还原反应,提高碳的利用率,可采用提高气流速度,减少接触时间。
B以蒸汽为气化剂的反应
C+H2O(g)=CO+H2-122.67KJ/mol
C+2H2O(g)=CO2+2H2-80.4KJ/mol
C+CO2=2CO-164.96KJ/mol
CO+H2O(g)=CO2+2H2+42.3KJ/mol
C+2H2=CH4+83.3KJ/mol
CO+3H2=CH4+H2O+206KJ/mol
CO2+4H2=CH4+2H2O+163.7KJ/mol
◆以蒸汽为气化剂的主要目的是为了得到氢和一氧化碳,可采取提高反应温度,并增加反应接触时间,使二氧化碳充分还原成一氧化碳,提高有效成份。
◆由式(9)、(10)、(11)知,存在甲烷生成反应,是在煤气炉中的还原层次要层内进行。
可是在高温状态下,甲烷反应受到抑制。
半水煤气中的甲烷气含量主要是由于燃料中挥发物含量不同所致。
2.固定层气化对固体燃料质量的要求:
A块煤气化要求:
项目
技术要求
粒度
大块50-100mm
中块25-50mm
小块13-25mm
水份
<6%
挥发份
≤10%
灰分
一级<16%
二级<16-20%
三级<20-24%
固定碳
一级>75%
二级70-75%
三级65-70%
硫
一级≤0.5%
二级0.51-1.0%
三级1.01-2%
灰熔融性
一级>1350℃、二级1300-1350℃、三级1250-1300℃
热稳定性
>70%
B燃料的化学性质:
(1)水份:
水份高,蒸发吸热,造成炉温下降,燃料消耗增加,产气下降。
(2)挥发份:
挥发份含量高,制出的半水煤气中甲烷和焦油含量高。
(3)灰份熔点:
主要用于固态排渣锅炉和气化炉设计并指导实际操作,能定性说明灰的熔化温度范围。
当灰份过高时,在气化过程中由于部分碳表面为灰份覆盖,减少气化剂与碳表面的接触面积,降低了燃料反应活性,灰渣残碳高。
◆灰份:
煤中有许多矿物质组成,经高温灼烧后,剩下的残留物就叫灰份。
◆灰份主要是硅、铝、铁、钙、镁等元素的氧化物和盐类。
当加热到一定温度时,这些混合物开始部分熔化,温度升高,熔化量增加。
◆煤灰熔化时三个特性温度:
开始变形温度、软化温度、流动温度。
◆根据灰熔点高低,分为四种:
易熔:
<1160℃
中等熔融:
1160-1350℃
难熔:
1350-1500℃
不熔:
>1500℃
(4)硫份
◆根据煤中硫含量的不同,煤可分为低硫煤(1.5-2.5%)、多硫煤(2.6-4.0%)、高硫煤(>4%)。
◆煤中硫根据存在状态可分为无机硫和有机硫两大类,无机硫以黄铁矿、白铁矿(分子式FeS)和硫酸盐的形式存在。
以黄铁矿和白铁矿形式存在的硫又称为硫化物硫。
有机硫主要是硫醚、梳醇、噻砏类硫化物。
◆煤中硫份在气化过程中转化为含硫气体,不但对设备管道有腐蚀作用,而且会使催化剂中毒。
(5)化学活性:
是指燃料与气化剂中氧、蒸汽或二氧化碳反应的能力。
(6)燃料的成渣性能:
是指燃料在气化时是否易于烧结成渣。
易于成渣的燃料在受高温时,容易软化熔融而生成迷渣块,使排灰和气化剂均匀分布困难,炉况恶化。
一般认为,在灰份中的Fe2O3、CaO、FeO含量越多,越易结渣,含Al2O3和SiO2越多,则熔点较高,不易结渣。
固定层气化炉要求燃料有较高的灰熔点。
C燃料的物理性质:
(1)机械强度
(2)热稳定性:
指燃料在受高温后粉碎的程度。
(3)粘结性:
指煤在高温下干馏粘结的性能。
粘结性大的原料煤,在气化中相互点结,生成焦拱,破坏透气性,恶化炉况。
(4)燃料粒度
.煤气发生炉内燃料的分布情况
炉内燃料层气化过程中大致分五个层区:
干燥层(150~200毫米):
依靠气体的显热来蒸发料燃料中的水份。
干馏层(300~400毫米):
燃料依靠热气体换热分解,放出挥发份。
还原层(350~450毫米):
主要进行二氧化碳还原成一氧化碳,或水蒸汽分解为氢。
氧化层(200~300毫米):
碳被气化剂中的氧氧化成二氧化碳及一氧化碳并放出热量。
灰渣层(100~200毫米):
分配气化剂并防止炉篦受高温影响,借灰渣显热来预热气化剂。
自由空间:
起聚积煤气作用和减少煤粉带出。
4.生产工艺条件的选择和工艺指标
A工艺条件
(1)气化层温度:
◆气化反应在高温下进行,气化层温度越高,产气和气质越好。
◆发生炉中气化层的最高温度不能超过原料的灰熔点,应根据原料性质控制,否则在气化层产生结渣使气化剂分布不均,产气和气质下降,严重时结疤,炉况恶化。
◆气化层实际温度一般很难直接测得,操作中主要根据探火棒控测炉内料层及炉顶、炉底温度变化和半水煤气组成变化来进行判断。
一般半水煤气中二氧化碳控制在8%-12%,炉顶温度350-400℃,炉底温度200-250℃。
2)吹风时间和入炉风量
在吹风和制气中,制气吸热和吹风放热必须达到平衡,由入炉空气总量决定煤气炉生产负荷。
调节入炉空气总量方法有两种:
一是调节吹风速度大小,二是调节吹风时间长短。
在稳定碳层的前提下,一般采取”强风短吹”,可减少吹风气中二氧化碳的生成量,降低热量损失,碳的消耗,可延长制气时间,有利于提高炉生产能力。
正常操作下,炉带出物应小于4%。
每生产1Nm3半水煤气,约耗入炉风量0.95-1.05m3空气。
(3)吹制气时间和蒸汽用量
在吹风时间和入炉总风量确定的基础上,蒸汽用量的大小将取决于炉温,不要使炉温波动过大。
合适的蒸汽用量将使上、下吹制气平均蒸汽分解率达到50%,下吹蒸汽用量约为上吹的1.1-1.5倍。
(4)碳层高度:
高碳层有利于炉内燃料层的分区相对稳定,储存较多热量,维持较高的气化层温度和使用大风量的操作条件,碳层高度一般控制在1.8-2.2米。
(5)循环时间:
一般以120-150秒为宜。
(6)生产强度
适宜的生产强度应根据原料煤性质确定,根据生产负荷调节,一般为800-900m3半水煤气/(m2·h·台)
B操作条件的选择
a上、下制气操作
b吹风和回收操作
◆在决定循环百分比分配时,应该保持”吹风+回收”为定值。
当入炉总风量确定后,切勿随意变动。
◆发气量好及氢氮比较高时,可增加回收并应减少吹风,但回收时,入炉的风量要比吹风时入炉的风量为少,此时总的入炉风量略有降低,可防止炉温继续升高。
◆当炉温低,发气量差以及氢氮比较低时,可减少或不做加回收,而相应改做吹风。
此时总的入炉风量略有增加,能够提高炉温。
用这种调节气体成分的方法,有利于减少炉温的波动。
c加碳和出灰操作
◆加碳和出灰是保持煤气发生炉物料平衡的手段,正确的加碳和出灰应以稳定碳层和维持炉内燃烧层良好的造气性为原则。
◆块度均匀,灰熔点高的原料,因为造气性良好而又不易结疤,能够采取高碳层操作;块度不均匀的燃料,因为造气性差而又容易结疤,碳层可适当降低些。
d操作指标
1).压力
(1)蒸汽缓冲罐减压前蒸汽压力:
0.2-1.2MPa
(2)蒸汽缓冲罐减压后蒸汽压力:
0.05--0.08MPa
(3)废锅、夹套汽包蒸汽压力:
≤0.2MPa
(4)废锅、夹套汽包加水压力:
≥0.4MPa
(5)油泵油压:
4.0—6.0MPa
2).温度
(1)炉顶温度:
≤400℃
(2)炉底温度:
≤300℃
(3)夹套温度:
≤135℃
(4)气柜进口温度:
≤50℃
(5)气柜出口冷却塔煤气温度:
夏天≤35℃,冬天≤30℃
3).循环百分比(总循环时间:
150秒)
吹风:
29秒上吹:
33秒(加氮:
24秒)
下吹:
75秒二次上吹:
5秒
吹净:
8秒
4).液位
(1)夹套汽包液位:
1/2—2/3
(2)油泵油位:
1/2—2/3
(3)洗气塔冷却塔设置U型水封,防跑气,防液封。
5).成分
(1)半水煤气O2≤0.5%,O2≥1.5%紧急停车
CO2≤10%CO+H2≥65%(根据导入氢循环氢调节)
(2)导入氢:
72—75%(根据循环氢确定)
6).气柜高度
(1)控制指标:
30%--75%
(2)高限:
80%(4000M3),停炉
低限:
≤30%(1500M3),减量
≤10%(500M3),紧急停车
7).风机电流:
按铭牌规定值(1#—3#风机电流100A)
5.工艺流程
1)造气微机系统油压流程
经过滤油机严格过滤后的液压油,依次经油箱加油口过滤网进入油箱,经油泵进油管过滤器后,由齿轮油泵升压,升压后经单向阀、调节阀及出口截止阀后,至泵站出口压力油总管,压力油至蓄能器和各阀门油缸有杆腔,经过滤器到达电磁阀换向站,各油缸无杆腔管线引至各对应的电磁阀,电磁阀接受微机送来的电信号,经过电磁阀动作来改变无杆腔的油压实现油缸的动作,以此完成煤气炉生产的阀门动作的需要,实现煤气炉生产,电磁阀换向站的回油总管至油冷却器降温后返回油箱循环使用,油泵出口油量一路至溢流阀,经过调节溢流阀的先导阀,调节油泵站的出口压力,经过溢流阀多余的液压油经过油冷却器后返回油箱。
2)气体流程
向煤气发生炉内交替通入空气和蒸汽,与炉内灼热的炭进行气化反应,吹风阶段生成的吹风气根据要求送三气岗位回收热量或直接过烟囱放空,并根据需要回收一注部分入气柜,用以调节循环氢,煤气炉出来的煤气经显热回收,洗气塔冷却和除尘后,在气柜中混合为半水煤气,然后去脱硫。
上述制气过程应在微机集成油压系统控制下,往复循进行,每一个循环一般分六个阶段,其流程如下:
(一)吹风阶段
空气由鼓风机来→自炉底鼓风箱入炉→旋风除尘器→上行煤气阀、烟道阀(或三气阀)→烟囱放空(或三气岗位)
(二)回收阶段
空气由鼓风机来→自炉底鼓风箱入炉→经旋风除尘器→上行煤气阀→煤气总阀→煤气总管→显热回收→洗气塔→气柜
(三)上吹(加氮)气阶段
蒸汽(加氮空气)→自炉底入煤气炉→旋风除尘器→上行阀、总煤气阀→煤气总管→显热回收→洗气塔→气柜
(四)下吹制气阶段
蒸汽→自炉上部入煤气炉→下行阀→总煤气阀→显热回收→洗气塔→气柜
(五)二次上吹气阶段
蒸汽→炉底入炉→旋风除尘器→上行煤气阀→煤气总阀→显热回收→洗气塔→气柜
(六)空气吹净阶段
鼓风机鼓空气→炉底入炉→旋风除尘器→上行阀煤气总阀显热回收→洗气塔→气柜
序号
设备名称
型号
技术性能
数量
厂家
1
造气风机
D400-2500
(1)
400m3/min2500mmH2O
1
焦作风机厂
D500-2600
(2)
500m3/min
2600mmH2O
1
焦作风机厂
D500-11-12(3)
500m3/min
2300mmH2O
1
上海鼓风机厂
2
造气电机
Y355L1—2
(1)
280kW2980R380V
1
长沙电机厂
JK134-2
(2)
350kW2970R6000V
1
长沙电机厂
JK133-2(3)
290kW2950R6000V
1
䦋㌌㏒㧀낈ᖺ琰茞ᓀ㵂Ü
3
液压侍服机构
HX-PC-900
滤油机电机Y132M-47.5kW
䦋㌌㏒㧀낈ᖺ琰茞ᓀ㵂Ü
成都华西化工研究所
4
造气炉配减速机
JZQ350-IV-2E
中心距350
输入转速1000ri=23.34
5
温县通用机械厂
5
气柜出口冷却塔循环泵
ISNO-80-160
电机Y160M2-2
100m3/hH=32m
15kW2900R
各3
新乡水泵厂
杭州电机厂
7.工艺计算
A煤气化过程计算
煤的气化反应是一个很复杂的过程,而且原料的种类、性质和气化方法将会对反应产生影响,完全根据理论进行计算是很困难的。
当前大致有三种方法:
Ⅰ以实测的煤气成份为依据进行计算;Ⅱ综合计算法;Ⅲ根据反应平衡进行计算。
下面以实测的煤气成份为依据进行计算,其结果如下:
(1)每100kg燃料用于制水煤气70kg,用于制吹风气30kg.
(2)吹风气产量:
132m3/100kg燃料,炉渣产量:
21.67kg/100kg燃料。
吹风空气量:
180m3/100kg燃料
(3)蒸汽耗量:
130.8kg/100kg燃料
(4)半水煤气产量:
210.1m3/100kg燃料
(5)吨氨消耗定额:
吨氨耗半水煤气按3300m3
◇吨氨耗原料煤:
3300/210.1*100=1570kg/tNH3
◇吨氨耗蒸汽:
130.8/210.1*3300=2054kg/tNH3
◇蒸汽分解率:
(3300*38.92%)/22.4*18/2054=50.24%
(6)影响煤耗因素分析
1)蒸汽用量
蒸汽分解率提高至60%可减少蒸汽用量:
(3300*38.92%)/22.4*18*(100/60)-2054=333.9kg/tNH3
可减少热量损失:
333.9*(3112.21-2914.01)=66178.98kg/tNH3
吨氨降低煤耗2.7kg/tNH3
2)原料煤含碳影响
含碳量增加1%,吨氨减少原料耗量:
1570*(1/67)=23.4kg/tNH3
3)炉渣残碳影响
残碳下降1%,减少煤耗
21.67*(1570/100)*1%/67%=5.1kg/tNH3
4)原料煤水份影响
水份下降1%,可减少热量带出
1570*1%*(3112.21-125.69)=46888.36kg/tNH3
减少煤耗:
46888.36/24150.3=2kg/tNH3
5)半水煤气消耗影响
吨氨耗半水煤气下降100m3,可减少原料煤消耗
100/210.1*100=47.6kg/tNH3
当前我公司半水煤气单耗在3200m3/tNH3。
结论:
煤棒水份下降1%,含碳上升1%,在炉况稳定下,一般会使吨氨耗煤下降30kg以上。
吨氨耗半水煤气下降100m3,原料煤消耗下降47.6kg。
经过计算:
煤棒含碳达65-68%,含水份≤9%,炉渣残碳≤16%,烟道灰≤4%时,炉况稳定,热量损失少,吨氨耗棒可降至1450kg/tNH3
B循环氢和补充氢的确定
(1)补充氢:
氨反应式:
3H2+N2=2NH3H2/N2=3
合成补充气中CH4一般为2%左右
则:
H2=(100%-2%)*3/4=73.5%
补充氢应控制在73-75%范围内。
(2)循环氢:
合成塔前循环气中氨含量为2.5%(除氨后作其它成份分析),CH4含量为20%(包括Ar)
H2/N2=3计算,则循环氢为
(100%-20%)*3/4=60%
循环氢应根据合成塔负荷(压力)和系统甲烷确定。
氢氮比一般控制在2.2-2.8之间。
C半水煤气成份对产氨的影响
(1)甲烷
◇补充气甲烷1%,合成塔后放空气中甲烷15%和25%,合成吨氨弛放量为110m3和190m3。
合成补充气消耗分别为2760m3/tNH3和2850m3/tNH3
◇补充气甲烷由1%上升至2%时,合成吨氨弛放量将成倍增加,消耗补充气增加125Nm3/tNH3
(2)CO+H2/N2的影响
CO+H2/N2发生变化,反应出合成补充气中氢氮比的变化。
当补充气中氢氮比持续失调,会使循环氢走高和走低,导致合成超压和放空。
(3)CO2含量影响
在一入压力:
290mmHg,一入温度18ºC时,煤气中CO2上升1%,有效气下降按1%计算,少产氨
2160273101.33+38.6-2.064
12*24*------*-------*-------------------*98%*1%
3300273+18101.33
=288*0.00818=2.36吨氨/日,合0.157方氨/时
三气岗位生产工艺
一、岗位任务
在经氨洗后合成弛放气引燃、助燃的作用下,把水煤气岗位来的吹风气引入立式燃烧炉完全燃烧,产生高温烟气,顺序经过高压余热锅炉、热管式省煤器、低温空气预热器,进水沫除尘器除尘,再由引风机引出经由烟囱放空,利用高温烟气的热量来产生高压蒸汽,预热三气所需的二次空气和锅炉用脱盐水,减压后入水煤气岗位缓冲罐,从而达到充分利用热量和保护环境的目的。
二、工作原理
在合成弛放气引燃、助燃的作用下,把吹风气引入立式燃烧炉,配以适量的空气,使其完全燃烧,形成高温烟气,依次经过蒸汽过热器、高压余热锅炉、空气及脱盐水预热器,以辐射、对流、传导的综合传热方式,把热量传递给各冷热载体(水和空气),后经水沫除尘器除尘降温后由引风机抽出经烟囱放空,达到生产高温过热蒸汽,同时过热三气所需二次空气和锅炉用水的目的。
主要化学反应方程式有:
2CO+O2=2CO2+Q放
2H2+O2=2H2O+Q放
CH4+2O2=CO2+2H2O+Q放
三、工艺流程简述
1、蒸汽流程:
高压余热锅炉所产蒸汽从锅炉主汽阀出来后,并入高压蒸汽管网,进入高压分汽缸。
送造气水煤气岗位缓冲罐,供制半水煤气用。
2、气体流程:
合成来弛放气经甲烷气缓冲罐、甲烷气自调减压稳压并除水后,经甲烷气水封桶、气水分离器进燃烧炉,配以适当预热空气,使甲烷气燃烧,达到引燃吹风气的目的,造气来吹风气分两股与适量预热空气混合后进入燃烧炉,在甲烷气引燃、助燃作用下完全燃烧,形成高温烟气,依次经过,高压余热锅炉,热管式省煤器、低温空气预热器、水沫除尘器,然后经过引风机抽出经由烟囱放空。
3、脱盐水流程:
20T锅炉供水来的脱盐水经脱盐水预热器,出来后的脱盐水进高压余热锅炉用于副产蒸汽。
四、工艺指标
蒸汽压力≤1.3MPa
液位1/2—2/3
炉温700—1000℃
甲烷气缓冲罐压力≤0.4MPa
炉水PH9—12
引风机电流80A
鼓风机电流90A
五、主要设备一览表
序号
设备名称
规格与型号
数量(台)
1
燃烧炉
φ7000/φ6100×2×14
1
2
余热锅炉
Q92/920—35—3.83/450
1
3
热管式省煤器
F=160m2
1
4
低温空气预热器
F=260m2
䦋㌌㏒㧀낈ᖺ琰茞ᓀ㵂Ü
5
水沫除尘器(麻石)
φ3600/φ3100×1
1
6
甲烷气水封
φ1020×1800×10
1
7
甲烷气水分
φ1020×1800×10
1
8
引风机
Y4—73—12No16D对应电机(Y315L2—6)流量119330m3/h、全压2200Pa、功率132kw、转速960r/min
1
9
鼓风机
9—26No11.2D、对应电机(Y315M—4)流量42221m3/h全压6382Pa功率132kw、转速1450r/min
2