润滑剂地总结大集合.docx
《润滑剂地总结大集合.docx》由会员分享,可在线阅读,更多相关《润滑剂地总结大集合.docx(19页珍藏版)》请在冰豆网上搜索。
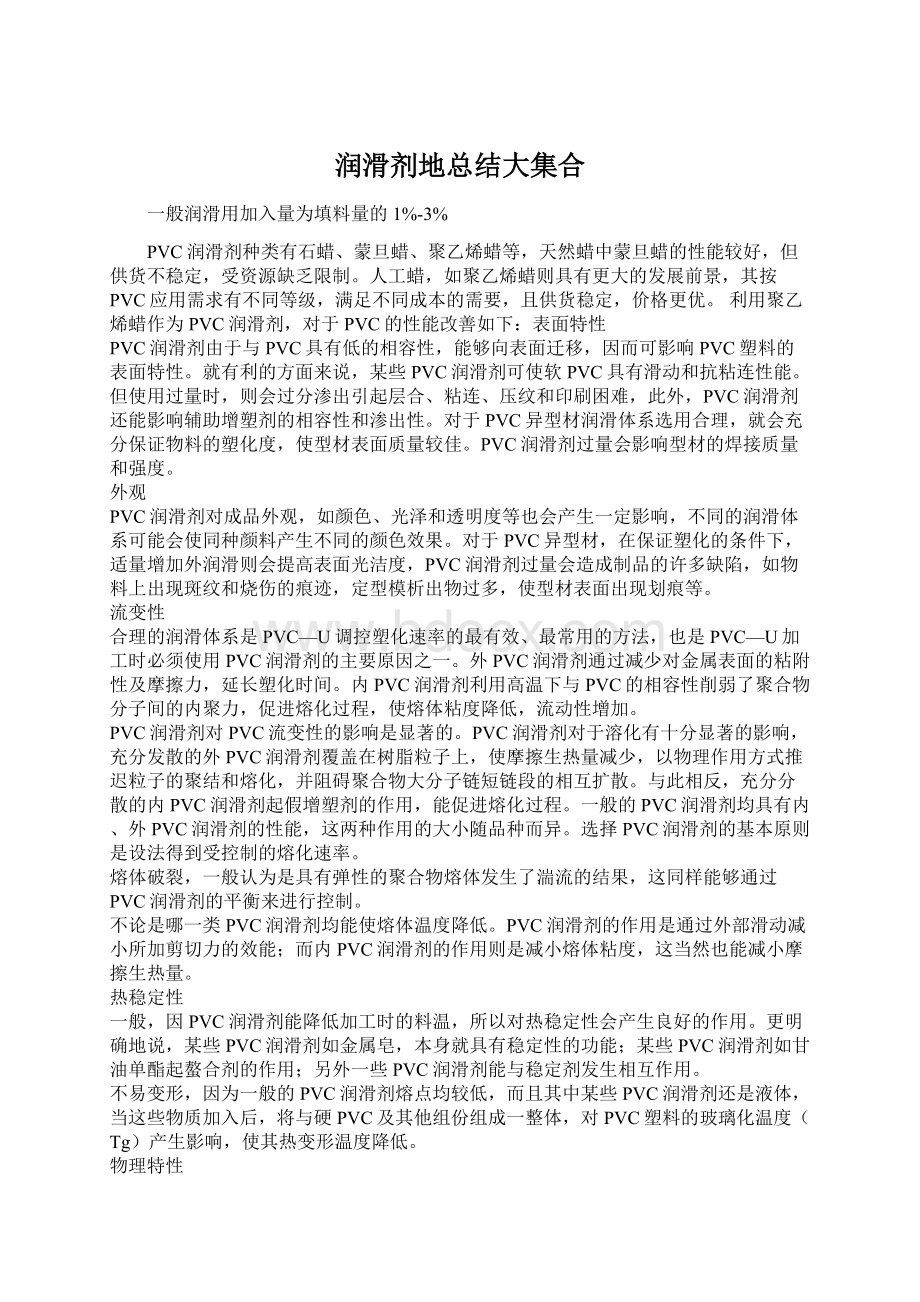
润滑剂地总结大集合
一般润滑用加入量为填料量的1%-3%
PVC润滑剂种类有石蜡、蒙旦蜡、聚乙烯蜡等,天然蜡中蒙旦蜡的性能较好,但供货不稳定,受资源缺乏限制。
人工蜡,如聚乙烯蜡则具有更大的发展前景,其按PVC应用需求有不同等级,满足不同成本的需要,且供货稳定,价格更优。
利用聚乙烯蜡作为PVC润滑剂,对于PVC的性能改善如下:
表面特性
PVC润滑剂由于与PVC具有低的相容性,能够向表面迁移,因而可影响PVC塑料的表面特性。
就有利的方面来说,某些PVC润滑剂可使软PVC具有滑动和抗粘连性能。
但使用过量时,则会过分渗出引起层合、粘连、压纹和印刷困难,此外,PVC润滑剂还能影响辅助增塑剂的相容性和渗出性。
对于PVC异型材润滑体系选用合理,就会充分保证物料的塑化度,使型材表面质量较佳。
PVC润滑剂过量会影响型材的焊接质量和强度。
外观
PVC润滑剂对成品外观,如颜色、光泽和透明度等也会产生一定影响,不同的润滑体系可能会使同种颜料产生不同的颜色效果。
对于PVC异型材,在保证塑化的条件下,适量增加外润滑则会提高表面光洁度,PVC润滑剂过量会造成制品的许多缺陷,如物料上出现斑纹和烧伤的痕迹,定型模析出物过多,使型材表面出现划痕等。
流变性
合理的润滑体系是PVC—U调控塑化速率的最有效、最常用的方法,也是PVC—U加工时必须使用PVC润滑剂的主要原因之一。
外PVC润滑剂通过减少对金属表面的粘附性及摩擦力,延长塑化时间。
内PVC润滑剂利用高温下与PVC的相容性削弱了聚合物分子间的内聚力,促进熔化过程,使熔体粘度降低,流动性增加。
PVC润滑剂对PVC流变性的影响是显著的。
PVC润滑剂对于溶化有十分显著的影响,充分发散的外PVC润滑剂覆盖在树脂粒子上,使摩擦生热量减少,以物理作用方式推迟粒子的聚结和熔化,并阻碍聚合物大分子链短链段的相互扩散。
与此相反,充分分散的内PVC润滑剂起假增塑剂的作用,能促进熔化过程。
一般的PVC润滑剂均具有内、外PVC润滑剂的性能,这两种作用的大小随品种而异。
选择PVC润滑剂的基本原则是设法得到受控制的熔化速率。
熔体破裂,一般认为是具有弹性的聚合物熔体发生了湍流的结果,这同样能够通过PVC润滑剂的平衡来进行控制。
不论是哪一类PVC润滑剂均能使熔体温度降低。
PVC润滑剂的作用是通过外部滑动减小所加剪切力的效能;而内PVC润滑剂的作用则是减小熔体粘度,这当然也能减小摩擦生热量。
热稳定性
一般,因PVC润滑剂能降低加工时的料温,所以对热稳定性会产生良好的作用。
更明确地说,某些PVC润滑剂如金属皂,本身就具有稳定性的功能;某些PVC润滑剂如甘油单酯起螯合剂的作用;另外一些PVC润滑剂能与稳定剂发生相互作用。
不易变形,因为一般的PVC润滑剂熔点均较低,而且其中某些PVC润滑剂还是液体,当这些物质加入后,将与硬PVC及其他组份组成一整体,对PVC塑料的玻璃化温度(Tg)产生影响,使其热变形温度降低。
物理特性
PVC润滑剂能影响PVC强力高速混合时的压实程度及最终的表观密度和凝胶化程度。
在用双螺杆挤出时尤其如此。
因为其挤出量与干混料的表观密度成正比,同时部分凝胶化的粒料在挤出中熔化所需的能量较少,所以挤出量较高。
力学性能
PVC润滑剂能影响拉伸强度、伸长率和冲击强度等力学性能。
PVC润滑剂对型材力学性能的影响主要体现在型材的焊角强度和耐低温冲击性能。
PVC润滑剂对制品低温冲击的影响,主要是通过对制品塑化效果的影响反映出来。
塑化程度越好,低温冲击强度越高。
在充分保证物料塑化的前提下,随PVC润滑剂用量的增加,焊角强度有减小的趋势。
大量实验表明,外PVC润滑剂过量时焊角强度较差,且具有较好的耐低温落锤冲击强度。
反之,外PVC润滑剂不足时,焊角强度较好而耐低温落锤冲击强度较差。
电性能
一般说,PVC润滑剂的极性或离子性越强则性能越差,而且温度越高,差别变得越大。
除体积电阻率和与此相关的导线绝缘电阻以外,表面电阻率也会受PVC润滑剂的影响。
极性较大的PVC润滑剂可减小表面电阻率且能造成一定的抗静电效果。
在聚乙烯蜡的选择方面,不能一味考虑价格,要从性价比方面着手,对于高等级的PVC应用需要使用进口的聚乙烯蜡,推荐型号719聚乙烯蜡,氧化度高,适用于PVC异型材、PVC热稳定剂上
硬聚氯乙烯加工中润滑剂的作用
1、内、外润滑平衡的多样性P1:
?
Q&>
IqKmIG?
事实上不同类型的加工设备,如挤出(又分单、双螺杆)、注塑、压延,均要求有不同的润滑平衡。
严格地讲,同类设备,不同生产厂家的产品,甚至同一个设备新的与旧的对润滑平衡均有不同的要求。
不同类型的产品,如管、膜、片以及型材,也有各自不同的润滑平衡。
例如,生产异型材、挤出片材、注塑制品、中空制品、吹塑膜及高透明制品均要有较高的塑化程度,较高的流动性,因而要求较高的塑化速率,所以内润滑剂要多一些;而对于管材的生产而言,它的塑化程度以60%~70%为宜[8,9],因而要求塑化速率低一些,外润滑剂应相对多一点;对于压延工艺,为了熔融的PVC易于剥离压延辊,外润滑剂亦应多一些;而注塑工艺则要尽可能少用外润滑剂,尽可能地减少外润滑对熔接痕强度下降的影响。
pN_rE58"|D
!
2"hY 2、实验室中如何评价内、外润滑平衡(sq`2
J,vItUtP= 2、1内、外润滑剂用量均不足/RWg~k
HycA"sln 其特点是塑化扭矩较大,熔体粘附性较严重,有可能提前热分解。
MypK&E2Sr
9^1y
nAr 2、2内、外润滑剂用量均过量*WS{;iD 其特点是析出较严重,制品力学性能下降(如试样较脆),二次加工性能较差,但其他实验数据均与内、外润滑平衡时相似。
:
+M\U/:
MX_|RTjF 2、3内润滑剂较少,外润滑剂较多:
I#`/R&X
GOTP(e 其特点是塑化时间较长,塑化扭矩较大,有可能出现析出现象(外润滑剂过量)。
FvPFa_?
-5]/nvlU 2、4内润滑剂较多,外润滑剂较少ZMJ+5b,zz
HEK@[UU 其特点:
塑化时间较短,有较重的粘附现象,有可能热稳定性变差。
总之外润滑剂用量不足则有粘附现象,塑化时间短;过量则力学性能下降,有可能有析出现象。
内润滑剂用量不足,则塑化扭矩较大,塑化时间较长;过量则塑化时间较短,塑化扭矩较小,热稳定性有可能变差。
Ren_
Q,x[qK/}B 2、5关于从流变仪得到数据的分析\&q4\0
&Dw/=; 熔体的流动性与粘度成反比,粘度又与扭矩成正比。
所以,熔体流动性越好,扭矩越低。
在扭矩流变仪的结果中给出三种扭矩值,即最小扭矩,最大扭矩(塑化扭矩)及平衡扭矩。
笔者认为,塑化扭矩是评价润滑剂改善PVC树脂流动性的最重要指标。
当然,最小扭矩及平衡扭矩也有一定的参考意义,但它们均与塑化扭矩有很好的对应关系,一般塑化扭矩大,最小扭矩及平衡扭矩也较大,反之亦然。
笔者还认为,塑化扭矩对实际加工设备转动装置能量消耗的影响远大于平衡扭矩的影响。
原因有二:
①在一般接近实用硬PVC配方中均有ACR加工助剂,在这种情况下,不同的润滑体系的塑化扭矩值的变化较大,而平衡扭矩值变化却很不显著[8];②由于多种原因(如尽量避免热分解,提高生产率等),加工者希望熔融物料在平衡扭矩所对应的时间尽可能地短一些,即达到预期塑化程度后,塑料熔体尽早离开加工设备。
虽然塑化扭矩只是一个峰值,但整个塑化峰所对应的时间的积分面积(能量消耗)却远大于平衡扭矩所对应的时间的积分面积(能量消耗)。
事实亦证明:
塑化扭矩只大百分之几,因它积分面很大,所以消耗的能量亦很大,加工设备因不堪重负,而有可能“报警”[10]。
3"-X;*HV%Y
对于塑化峰的峰值(塑化扭矩,塑化时间)常见于报道中,但对塑化峰的形状(即半峰宽度及半坡斜率)却少见评论,事实上,半峰宽度及后半坡斜率亦是润滑体系影响树脂熔化特性一个重要标志。
UfWi*hA
相对而言,能耗较少,较充分地利用了摩擦热,进一步促进了树脂塑化,减少树脂在设备中停留时间,有利树脂的热稳定化,并为进一步提高生产效率提供了可能性。
;y?
dFn@~H
+2k04P)mU 3润滑剂的选择u
v"d*#^
1U*~F=4 前已述及内、外润滑剂平衡的多样性以及“相容度”影响润滑剂的作用和属性。
这些均给配方工作者在选择和应用润滑剂时带来诸多不便。
因为选择润滑剂既没有“理论”指导,也没有带有普遍意义的规律可供参考。
虽然如此,仍然有一些经验可供参考。
FQTs
m#B^q|, 3.1选择润滑剂的一般原则TpSf
7PiCm( 如前所述,要合理兼顾PVC树脂的流动性、防粘性及塑化速率。
也就是一定要使内、外润滑作用平衡,达到能经济、连续生产的目的。
'\UhNO
XNuS7N 研究与实践表明:
并不是100%塑化的制品质量最好,力学性能最高[8,9]。
另外,出于多种原因的考虑,不同的制品对塑化程度均有不同的要求。
不完全塑化,不仅质量好,产量高,能耗低,并且可以降低热稳定剂用量,有利于降低成本,提高产量。
在充分考虑热稳定剂及其他助剂等因素对润滑剂影响的前提下,通过调整内、外润滑剂品种与数量可以调控塑化速率,增加树脂流动性及改善粘附性。
SG%iA
Ulj]C7B 3.2选择润滑体系的一般实验程序@Yf6_EX
R7J_;5d0
(1)标准样+Pn1x2aO.L
"/^&;A`P 用一个加工性能好,品质优良的同一类设备生产同一类产品的高速搅拌料,用扭矩流变仪做实验。
测试其塑化时间,塑化时扭矩及塑化峰宽度和峰后坡斜率。
然后调整内、外润滑剂品种及数量,使其与标准样尽量接近。
^bF.o
$zXWQE,8
(2)首先通过改变内润滑剂品种及用量来改变PVC熔体流动性即熔体粘度(塑化扭矩值)。
ow5s*XFgi
Jy^>}o (3)在基本调整好熔体粘度(塑化扭矩值)的前提下,通过改变外润滑剂的品种与数量调整塑化时间(即塑化速率)。
当然,增减外润滑剂的数量或改变其品种时,对塑化峰值亦有所影响。
Xh/Lrm
BP&V.p%Z7 (4)防粘性
t;Xm"
v2?
>nM,#F 在熔体的流动性、塑化时间(速率)基本满意以后,应考察防粘附性是否足够,如果防粘性仍然不足,可适当按比例增加内、外润滑剂的用量。
如果感觉防粘性已经可以(不粘流变仪混合头的转子),这表明润滑剂总量有可能过量(这是高水平的润滑平衡),可适当减少一些内、外润滑剂的用量,直至有轻微的发粘为止。
在此基础上适当补加一些内、外润滑剂使它不发粘,这是较低水平的润滑平衡,也是较接近实际应用水平的润滑平衡。
高水平的润滑平均虽然可以改善PVC体系的热稳定性、降低热稳定剂用量、减少配方成本,但外润滑剂的析出现象有可能较严重,对连续产不利。
同时,有可能使停机率增加、生产率下降、废品率上升,增大了生产成本,并带来诸多操作不便,甚至会影响二次加工性能。
29C9?
os
\)z(
0 (5)放大实验11P6W,?
~L9C,'h#> 把上述初步确定的配方在生产中进行放大试验,发现有何不足处,再有针对性调整体系,如此反复几次即可设计出一组较满意的润滑平衡体系,达到经济、连续生产优质产品的目的。
=`CKK}
*P)xH+'| 如果没有标准配方,可以向热稳定剂或润滑剂的生产商索要参考配方,按参考配方试生产一次,找出存在问题,并按参考配方做Brabender流变实验,参照流变实验结果按上述试验程序进行改进,或用便宜的产品对原参考配方中润滑剂进行取代。
fb[gJ+1=
P&4rH 3.3实验数据对实际生产的影响u->pnA~Pb
?
&Y下面列举了三个配方的实验结果及在生产中情况,以供参考[7]。
qv[C05O~
]vZQSNy; 1#配方是山东某厂用平行双螺杆正常生产管材的混合料测得数据。
2#配方是外国某生产热稳定剂公司推荐配方,据称在美国已经广泛地用于锥形双螺杆挤出有机锡热稳定剂的管材,但是在平行双螺杆挤出时,只能在远低于正常转速时才能生产出合格管材,主机转速稍一提高,即会因主机扭矩太大而自动报警,不能正常生产。
分析一下上面的实验数据:
2#配方较1#配方塑化时间短了12s,即短了414%的时间;虽然2#配方的塑化扭矩只比1#配方大了2%。
但在用于实际生产时差别却非常之大。
Bo0#n*?
"
3#配方是笔者在2#配方基础上改进的配方,塑化时间3#比1#延长20s,延长7%;塑化扭矩3#比1#小013N·m,小了018%。
结果3#配方可以正常地使用平行双螺杆挤出合格管材。
Bu!
q3
;
PoSBIyw
4评价单独润滑剂的标准及实验设备6*sYA%%U
En#O8Ju 评价润滑体系的标准前文已提及,要合理地兼顾熔体流动性,防粘附性及塑化速率。
但在有些情况下,即使达到上述标准也不能满足现代化大生产的要求,不能经济地、连续生产优质产品。
如注塑制品还要求有很好的脱模性,在模具中既要形成一层润滑薄膜,同时在熔体表面又不能有与树脂完全不相容的润滑薄膜存在,否则就影响熔体熔合线处的力学强度。
因此评价某种润滑剂的优劣不能仅仅以其润滑作用的强弱为标准,优良的润滑剂还应具有如下的一些性能。
;!
0%w1@
z8G!
;+a 4.1润滑剂还应具有的其他性能#Fx:
O+vPi
RgbEB
w 4.1.1对塑料性能无不良影响I8N[2Yy@
Q3FkaS/y?
如对光、热稳定性、力学性能、电性能、透明性、毒性及二次加工性能均无不良影响。
3;RTKs&~3
8n7gp!
z 4.1.2优良的光、热稳定性及化学稳定性(?
8uC
Xcu(~"d4 如果热稳定性低或化学稳定性差,在加工时有可能分解成其他物质,可能影响润滑体系平衡而给加工带来不便。
兼有良好润滑作用的热稳定剂———金属皂,它们在参与热稳定化反应以后生成金属氯化物及硬脂酸,这两种物质在PVC中的相容度与原来的硬脂酸盐差异较大,其润滑性差异亦很大,有可能造成内、外润滑失衡。
P]6G2a#
/!
L}VCL19IM
bo#@m]/J 润滑剂加入总量一般不超过2.5phr,所以要求它必须有良好的分散性。
分散性除与润滑剂的内聚力、相容度有关外,也与熔点有关,如果熔点高于加工温度,相容性又差,润滑剂很难均匀地分散在PVC树脂中。
熔点最好在115℃以下,这样在高速搅拌时即已熔化,使其更均匀地分散在PVC树脂中。
aTIF?
:
pD4u
DL~Z[e 4.1.4低挥发性6[1)7ufXU
FrSsSkg 一般熔点越高挥发性越小。
硬脂酸及石蜡价格便宜,润滑作用强;石蜡的熔点随品种而异,在选用时应选高熔点石蜡,用量亦不宜太多,否则因其挥发而破坏中、后期润滑平衡,甚至影响连续开车时间。
E<}
n^%NI
Xvcw
[QhgU 4.1.5与其他助剂的协同效应eADM`}:
!
TMO| 一些多羟基部分酯化物的内润滑剂,可以络合不稳定氯原子,从而有一定辅助热稳定剂作用,同时也能起到防雾滴及抗静电作用;作为热稳定剂的金属皂类,只要使用得当,也可以起很好的润滑作用。
?
u3>b;P0r
FbNNIDK[` 4.1.6有较好的质量价格比%#{n{8}n{B
}M<,O;dy 事无万全,一个润滑剂要完全达到上述各项要求几乎是不可能的,也没有必要。
只要能满足特定的设备及工艺要求,正常生产即可。
例如异型材一般不要求透明度、电性能等特性。
因此,就无需选用具备这些性能的品种。
ow|gOm{,h
"0\`p` 4.2使用润滑剂的操作弹性
|vP?
Fuv
=L|GZB?
f 好的润滑剂不仅具有润滑作用强及上述的一些性能外,还应有较宽的操作弹性。
如配料比的微小差异、工艺条件的变动(温度的波动、压力增减等),尤其是为了提高产出率而提高挤出速度等情况时,生产者希望润滑体系仍然处于平衡状态,保证更经济地高速连续化产。
yTdBlZ
fzTbcq*
4.3选择润滑剂时所需的实验YUB{\s
K0d_Mg)
(1)双辊混炼机实验&)@FVmO`a
B?
iHXqp}>y 称取100gPVC树脂,按设计配方加入待考察的润滑剂及其他助剂,并把粉料基本混均匀,在双辊温度达到180±2℃时,启动双辊把粉料倒入双辊间,并开始掐秒表计时,测定其抱辊时间,观察粘辊情况。
9N%bXbZQ
*P@x7r)0@
(2)扭矩塑化仪(Brabender)实验试验在相同实验条件下考察配方中不同润滑剂的润滑特性,测试其塑化时间、塑化扭矩及半峰宽度。
转速低或设定温度低时,塑化时间较长,塑化扭矩较低,半峰较宽;转速高或温度高时其结果与上述情况相反。
=_~]32!
7
[;z^gK (3)析出实验@+pm#0
Lr>d3W9 在待测配方中加入一些颜色较深的颜料(例如红色颜料),在双辊混炼机上混炼5~7min,然后用加有30phrDOP及4phrTiO2的软片清洗双辊。
比较软片上红色程度,确定析出程度。
HXgPk
l`
));p#
Fa
润滑及改善pvc制品光亮度的原因
1。
单体蜡 PEwax 提高填料等熔体物料的分散效果,在后期是可以成膜,有着比较不错的脱模效果,如楼上杜站长所述,EBS比较特殊,他可以提高制品的光亮度的同时,有着不错的分散效果,只是国产的EBS质量较差。
在色母粒行业等他们用EBS和PE蜡搭配使用,生产的色母粒颜色光亮度好
2。
氧化聚乙烯蜡类润滑,提高熔体的塑化能力,使得熔体的塑化效果更好,从内因上改善制品的塑化,使得制品光亮度比较好,显示出物料本来的光亮度,遮盖由于填料等造成的光亮度下降。
光亮剂是增加亮度的,润滑剂是增加加工流动性。
PVC-U的润滑平衡
大量的研究与实践表明:
PVC-U的塑化程度在65%左右时,其各项力学性能最好,这就要求在加工PVC-U时必须掌握适当的塑化程度,内润滑剂在降低塑化扭矩的同时能促进塑化(缩短塑化时间),而外润滑剂在改善PVC-U的流动性的同时又能延迟塑化。
因而在设计PVC-U配方时,调整内、外润滑剂的比例及加入总量,就能调控PVC-U的塑化速率(塑化时间),而调控塑化速率则是内、外润滑作用平衡的重要研究内容。
但是,由于塑料润滑作用的多变性及润滑平衡的多样性,至今在国内尚未见到关于润滑平衡方面的专论文章,笔者就塑料润滑作用平衡(以下简称润滑平衡)提出一些观点,供广大读者参考。
1润滑平衡的设计
润滑平衡的设计是PVC-U配方设计的最乡键的一环。
1.1润滑剂及润滑作用目前尚没有真正意义的理论及规律
对―般PVC-U配方设计而言,笔者认为配方设计的难点及主要内容是内、外润滑剂种类的选择及它们的比例和加入总量的设计。
润滑剂加入总量应适宜,而内、外润滑剂的比例更重要,尽管总量足够,但如果比例失调,也不合连续地生产出合格产品。
然而对于PVC-U加工过程至关重要的润滑体系,在目前还没有可称为理论的理论,甚至连可以有效地指导配方实验的规律也没有。
唯一的所谓规律是借鉴普通化学中“相似相溶”规律,也就是润滑剂的极性与PVC树脂的极性越相似,其相容性越奸,因而其内润滑作用也越好;反之外润滑作用较强,但是这个规律对于配方设计的指导性亦很有限。
因为判断润滑剂的极性的根据是润滑剂的化学结构,即润滑剂分子中含有的羟基、酯基、羧基、酰胺基以及醚基、酮基等极性官能团的种类、数量及其与长链烷基的比例。
由于润滑剂化学结构复杂、多样,以及相邻官能团的相互影响,使得对润滑剂的极性大小的判断更为困难,这就造成了单凭润滑剂的极性来推断润滑剂的润滑作用与润滑剂实际上所起的润滑作用之间的差异性远远超出人们的想象。
1.2润滑作用的多变性
问题的复杂性还不仅如此,更为重要的是润滑剂与树脂的相容性(即润滑作用)还受其他条件的影响,尤其是其他润滑剂与增塑剂等助剂的影响更为显著,这种改变甚至可使内润滑剂变成外润滑剂,也就是说,同一种润滑剂的润滑作用会随着添加量的不同,随着配方中其他助剂组成的不同,随着加工条件的不同而改变。
1.3内、外润滑平衡的多样性
事实上,不同类型的加工设备如双螺杆及单螺杆挤出、注塑、压延等设备,均要求各自不同的润滑平衡。
严格地讲,同类设备、不同生产厂家的产品,甚至同一台设备,旧的与新的设备,对润滑平衡均有不同的要求。
不同类型的产品,如管材、片材、膜以及异型材,要有各自不同的润滑平衡。
如断面复杂的异型材、挤出片材、注塑制品、中空制品、吹塑膜及高透明制品均要求有较高的塑化程度,更好的熔体流动性,因而要求内、外润滑剂,尤其是内润滑剂的加入量要多一些,而管材则对熔体黏度及流动性要求相对不太高,塑化程度以60%~70%为宜,因而外润滑剂相对可以比内润滑剂的用稍多。
但是注塑制品则要求尽可能少用非极性外润滑剂,以便尽可能减少外润滑剂对熔接痕强度的影响。
上述内容均说明了润滑平衡的多样性。
这就造成润滑作用理论的研究较为困难,在实际配方设计时,也极大地增加了润滑剂配方设计的难度。
笔者认为,对于一般PVC-U而言,配方设计的关键是内、外润滑剂种类、比例及加入总量的设计,就是润滑平衡的设计。
2润滑平衡的研究方法
对于润滑平衡的设计来讲,既不精楚内、外润滑剂在配方中实际的润滑作用强度,又不知其他润滑剂及其他助剂对其润滑作用影响的具体情况。
最简单的方法,是用只问最后结果,不管其作用机理如何的宏观概括研究方法,即只考虑因素(内、外润滑剂和其他助剂)对最终结果(润滑平衡)的贡献的研究法,也就是不管内、外润滑剂及其他助剂之间如何相互作用及其影响程度的大小,只看它们对润滑平衡最终结果的综合影响的方法。
3润滑平衡的定义及其定量表述
内、外润滑剂品种适当,内、外润滑剂比例与加入总量适当,达到适当的塑化速率及熔体粘度(扭矩流变曲线上适当的塑化时间及塑化扭矩)。
也就是能保证特定的加工设备及工艺经济地、连续地生产出合格塑料制品的润滑体系,即为内、外润滑平衡体系。
3.1适当的塑化时间
润滑平衡既不是个固定值,又因缺乏润滑作用的基础数据,所以造成定量表述润滑平衡很困难。
因此,只能用对比类推法对润滑平衡进行研究。
也就是首先研究已经确认是润滑平衡的体系,把它在塑料加工设备上的塑化情况与它在扭矩流变曲线上表现出的塑化情况进行对比。
结果发现:
润滑平衡体系在扭矩流变曲线上的塑化时间对应于挤出机2/3左右的位置,也就是对应挤出机塑化段将结束、均化段将开始的位置。
如果不是润滑平衡体系,其塑化时间对应于挤出机的位置将有所改变。
塑化时间对应挤出机的位置小于2/3时期,则过度塑化,对于PVC-U而言有可能热分解,物料发黄;塑化时间对应挤出机的位置大于2/3时,则塑化度不够,制品较糙、发脆。
由上述分析可得出结论:
可以用扭矩流变曲线上的塑化时间作为定量判断润滑体系是否处于平衡