滚动轴承减摩设计.docx
《滚动轴承减摩设计.docx》由会员分享,可在线阅读,更多相关《滚动轴承减摩设计.docx(16页珍藏版)》请在冰豆网上搜索。
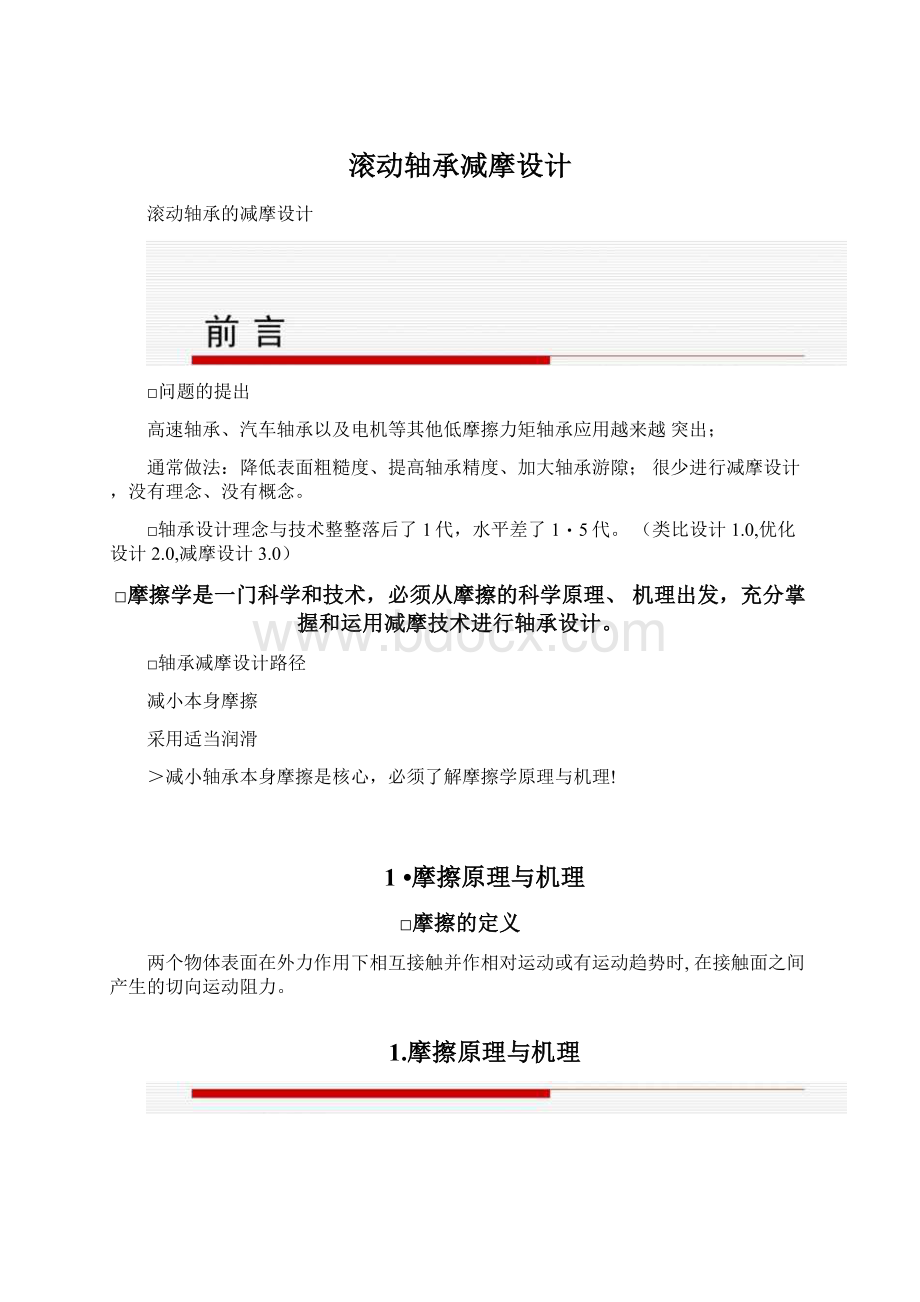
滚动轴承减摩设计
滚动轴承的减摩设计
□问题的提出
高速轴承、汽车轴承以及电机等其他低摩擦力矩轴承应用越来越突出;
通常做法:
降低表面粗糙度、提高轴承精度、加大轴承游隙;很少进行减摩设计,没有理念、没有概念。
□轴承设计理念与技术整整落后了1代,水平差了1・5代。
(类比设计1.0,优化设计2.0,减摩设计3.0)
□摩擦学是一门科学和技术,必须从摩擦的科学原理、机理出发,充分掌握和运用减摩技术进行轴承设计。
□轴承减摩设计路径
减小本身摩擦
采用适当润滑
>减小轴承本身摩擦是核心,必须了解摩擦学原理与机理!
1•摩擦原理与机理
□摩擦的定义
两个物体表面在外力作用下相互接触并作相对运动或有运动趋势时,在接触面之间产生的切向运动阻力。
1.摩擦原理与机理
□摩擦分类
(1)按摩擦副运动状态可分为
静摩擦:
两物体表面产生接触,有相对运动趋势但尚未产生相对运动
时的摩擦。
(2)按相对运动的位移特征可分为
滑动摩擦:
两接触物体接触点具有不同速度和(或)方向时的摩擦。
自旋摩擦:
两接触物体环绕其接触点处的公法线相对旋转时的摩擦。
1.摩擦原理与机理
□摩擦分类
(3)按表面润滑状态可分为
「摩擦:
两表面之间即无润滑剂又无湿气的摩擦。
流体摩擦:
以流体层隔开相对运动表面时的摩擦,即由流体的粘性
阻力或流变阻力引起的摩擦。
混合摩擦:
半干摩擦和半流体摩擦的统称。
1.摩擦原理与机理
□滚动轴承是由滑动轴承演变而来的
□滑动摩擦复习
>机械互锁(啮合)理论
>分子吸引(引力)理论
>机械分子理论
>粘着理论(犁沟效应)
1•摩擦原理与机理
□达芬奇1509年第一个系统地研究了滑动摩擦学
通过实验研究指岀:
一切物体刚要开始运动时,便产生摩擦阻力;
光滑表面间的摩擦力大小约为其重量的1/4;摩擦力与法向力成止比。
1■摩擦学原理与机理
□古典摩擦学定律(阿蒙顿■库仑定律,1785年):
(1)摩擦力方向与接触表面相对运动速度方向相反,大小与法向载荷成正比,即F=fWo
(2)摩擦系数与表面名义接触面积无关。
(3)静摩擦系数大于动摩擦系数。
(4)摩擦系数的大小取决于材料性质,与滑动速度和载荷大小无关。
上述经典摩擦定律并非基本的物理定律,只是从实验结果中总结得出的规律,尽管己有很多实验结果显示其并不完全正确。
但是至今还没有发现或总结出更好的摩擦定律,因此在工程实际问题中依然被近似地应用。
1.摩擦学原理与机理
□修正摩擦定律
古典摩擦定律长期作为工程应用的指导法则使用。
但根据近代的研究,发现多数内
容不完全正确,必须进行修正:
(1)摩擦力与名义接触面枳无关,与真实接触而枳有关。
当两者接近时,即法向压力很高时,摩擦力与法向压力成非线性关系,摩擦力增加很快。
(2)有一定屈服极限的材料(如金属),其摩擦力才与名义接触面积无关,粘弹性材
料的摩擦力与接触面积有关。
(3)粘弹性材料的静摩擦系数不大于动摩擦系数。
(4)精确测量表明,摩擦力与滑动速度有关。
一般,速度对金属的摩擦力的影响不像
对粘弹性显著的弹性体的摩擦力那样明显。
一般认为,f=F/Wk,k=2/3〜/。
1.摩擦学原理与机理
□塑性公式
式中巾——塑性指数(无量纲);
E——综合弹性模量(N/cm2):
H材料布氏硬度(N/cm2);
览微凸体高度均方根值(um);
R——微凸体曲率半径(um)o
由公式可看出,增大材料的硬度和微凸体的峰顶曲率半径,减小微凸体高度都可以使塑性指数减小。
在实际生产中利用抛光、研磨、磨合或其他特殊加工方法来降低表面粗糙度,增大微凸体曲率半径,都可降低塑性指数,使摩擦表而呈弹性接触状态,以达到减少摩擦磨损的目的。
1.摩擦学原理与机理
□修正粘着理论
6二软表面膜的剪切强度极限
示—硬基体材料受压屈服极限
具有软材料表面膜的摩擦副滑动时,粘着结点的剪切发生在膜内,其剪切强度较低。
又由于表面膜很薄,实际接触面积由硬基体材料的抗压屈服极限来决定,实际接触面积又不大,所以薄而软的表面膜可以降低摩擦系数。
在工程应用中,在钢制零件上涂镀软金属等,就是应用这一机理。
2.滚动摩擦机理
□滚动摩擦定义
两接触物体接触点的速度大小和方向均相同时的摩擦。
点接触或线接触的两物体在接触处的速度大小和方向均相同(纯滚动)时的阻力。
一个物体(滚动体)在另一个物体的表面(可以是平面或曲面)上滚动时遇到的阻力。
在力矩作用下沿接触表面滚动时摩擦。
2.滚动摩擦机理
□滚动运动形式
齐种滚动运动都可以视为以下三种基本滚动形式的组合:
(1)自由滚动
无切向摩擦力和不发生切向滑动的滚动称为自由滚动或纯滚动,这是最简单的滚动形式。
(2)具有牵引力的滚动
在接触区内同时受到法向载荷和切向牵引力的作用,例如摩擦轮、铁路车辆的牵引车轮等。
(3)伴随滑动的滚动
当两个滚动体的几何形状造成接触面上的切向速度不相等时,滚动中必
将伴随滑动,例如深沟球球轴承屮球与沟道Z间的滚动。
滚动摩擦机理与滑动摩擦有显著不同
除非接触面存在很大的滑动,滚动摩擦通常不存在犁沟效应,粘
着结点的剪切阻力也不是滚动摩擦的主要原因。
硕质材料滚动时的阻力很小,滚动摩擦系数比滑动摩擦系数低2个数量级以上。
滚动摩擦机理可概括为以下4种:
(1)微观滑移
(2)弹性滞后
(3)塑性变形
(4)粘附效应
>滚动摩擦是由上述多种机理组合叠加的复杂过程。
>接触应力不大时主要以弹性滞后为主,应力较大时主要以塑性变形为主。
(1)微观滑移
当两个弹性模量不同的物体接触而发生滚动时,由丁•接触表面产生不相等的切向位移,会有微观滑移出现。
用以传递机械能的滚动接触表面有切向牵引力作用,也将产生较大的微观滑移。
由于几何形状使得接触面上两表面齐点的切向速度不同时,将导致更大的微观滑移。
微观滑移所产生的摩擦阻力占滚动摩擦的较大部分,其机理与滑动摩擦相同。
微观滑移是滚动过程中普遍存在的现彖。
(2)塑性变形
在滚动过程中,当表而接触应力达到一定值时,首先在距表面一定深度处
产生塑性变形,随着载荷增加塑性变形区域扩大。
塑性变形消耗的能量表现为滚动摩擦阻力,可以根据弹塑性力学计算。
如:
球体沿平而口由滚动时,由于球体运动前方的材料塑性变形所产生的滚动摩擦阻力尸町表达为
二二二「二;二二二二二二二Foc
:
R
式中,W为法向载荷;R为球体半径。
(3)弹性滞后
滚动过程中产生弹性变形需要一左能量,而弹性变形能的主要部分在接触
消除后得到回复,其中小部分消耗于材料的弹性滞后现彖。
低速滚动时的弹性滞后损失小
高速滚动时的弹性滞后相对较大
(4)粘附效应
滚动表而相互紧压形成的粘着结点在滚动中将沿垂直接触而的方向分离。
因为结点分离是受拉力作用,没有结点面积扩大现彖,所以粘着力很小。
通常由粘着效应引起的阻力只占滚动摩擦阻力的很小部分。
2.滚动摩擦机理
□滚动摩擦系数
(1)滚动摩擦系数
当滚动体沿平面滚动时,由于接触区的变形使得以接触点O,为中心的接触压力分布不对称,因而支承面的反力产生偏移。
此反力对丁•接触点的力矩称为滚动摩擦力矩。
滚动摩擦系数定义为滚动摩擦力矩与法向载荷之比,即
FR
W
>滚动摩擦系数与滑动摩擦系数不同,它是有量纲的量,常用单位为mmo
2.滚动摩擦机理
□滚动摩擦系数
(2)滚动阻力系数
滚动体滚过角度为©滚过的距离为R0而驱动力作功为
滚动阻力系数定义为滚动驱动力在单位距离所作的功与法向载荷之比,
2.滚动摩擦机理
□滚动摩擦定律
滚动阻力系数是库仑于1785年用实验方法得出滚动摩擦定律:
DupuitT1837年提出了修正公式,通常称为Dupuit定律:
上述滚动摩擦定律未涉及到摩擦机理,系实验所得,因而叮近似地应用于工程计算。
3.滚动轴承的摩擦特性
□滚动轴承本身就属于“减摩”轴承
滚动轴承的“减摩”特性是相对于滑动轴承而言。
滚动轴承的摩擦因子“一般为0.01-0.001,滑动轴承为0.1~0.01。
滚动轴承的摩擦因子比滑动轴承低1~2个数量级。
3.滚动轴承的摩擦特性
□不同类型轴承的摩擦系数比较
摩擦系数//
3.滚动轴承的摩擦特性
□不同类型轴承的极限转速比较
3.滚动轴承的摩擦特性
□滚动轴承摩擦类型
轴承的摩擦按其产生机理可以分为以下4种类型:
(1)纯滚动摩擦;
(2)滚动接触表面上的差动、自旋和陀螺等滑动摩擦:
(3)滑动接触部位的滑动摩擦(包括滚动体与保持架兜孔之间的滑动;
保持架与套圈引导面Z间的滑动;滚子端面与套圈挡边之间的滑动;密封轴承中密封件与套圈之间的滑动等等);
(4)润滑剂的黏性阻滞摩擦。
M=Ml+Mv=(Md+Ms)+Mv
Ml——与载荷有关的轴承摩擦力距,又称为载荷项摩擦力距,Nnmi:
Mj—与载荷无关的轴承摩擦力距,又称为速度项摩擦力距,Nmm。
□滚动轴承的摩擦系数计算
M
“=——厂代具有工程思想。
同时
|包含了各种影响因素。
p——轴承当量载荷,n;V2>
d轴承内径,nuno
3・滚动轴承的摩擦特性
□球轴承的差动滑动
以深沟球轴承的差动滑动摩擦力矩的经验计算公式为例:
式中,D/ni轴承节圆直径,mm;
Dw球直径,nun;
m——球与内圈沟道接触形成的滑动摩擦力矩,Nmm;n?
——球与外圈沟道接触形成的滑动摩擦力矩,Nmm。
可以得知,通过减小轴承节圆直径和增大球直径均可以减小轴承摩擦力矩。
其他类型轴承也同此理。
4.
轴承减摩设计案例_
德国FAG的电机用新一代C系列深沟球轴承
□N8K的家电用GR系列深沟球轴承
用于家用空调、吸尘器和电扇
/摩擦力矩降低40〜50%:
/使用寿命提高50%以上;
/噪声水平更低或相当。
□JTEKT的LFT-III第三代超低摩擦力矩圆锥滚子轴承
□NTN汽车传动系用轴承
NTN开发出纯电动和混合动力汽车电机及减速器轴承。
电机要求轻量化,
而减小体积则转矩也会降低,因此需要增加转速,以确保输出功率。
但轴承转速过高,保持架在离心力的作用下会变形,或者流入轴承内部润滑油的搅拌阻力导致温度上升。
因此开发采用“适用高速的低摩擦力矩树脂保持架”o保持架采用两片,可互相抑制离心力造成的各自变形,最大dn值达1.2X106,相当于d=40的轴承转速^30000r/min。
保持架侧而设计成防护罩形状,限制流入的油量,大大降低搅拌阻力。
摩擦力矩损失降低了50%。
□NSK的混合动力车低摩擦力矩轴承
NSK开发出了摩擦损失比以往降低50〜65%的“混合动力车专用
低摩擦扭矩球轴承”,用于丰田的新款“普锐斯”o
钢球数量从标准设计的22〜23个大幅减少到16个。
除加大径向游隙之外,还优化了钢球直径、沟道尺寸,从而降低滚动摩擦的损失。
保持架采用尼龙46制造,以减轻钢球与保持架之间的滑动摩擦。
另外,还消除了旋转方向的凹凸形状,从而降低了搅拌损失。
单个保持架上的摩擦力矩降低了30〜40%,轴承整体的摩擦力矩降低了50〜
65%o
4.轴承减摩设计案例——密封
□NTN的低摩擦密封深沟球轴承
Type,codeno.
Shieldedtype
Sealedtype
Construction
NorxontacttypeZZ
Non-contacttypeLLB
ContacttypeLLU
•Metalshieldplateisaffixedtooutsiderin^:
innernngincorporatesaV-grooveandlabyrinthclearance
•Outerringincorporatessyntheticrubbermoldedtoasteelplate:
sealedgeisalignedwithV-^roovealcxiginnerrirvgsurfacewithlabyrinthctearance.
•Outerringinoocporatessyntheticrubbermoldedtoasteelplate;sealedgecontactsV-groovealonginnerringsurface.
•BasicconstructionthesameasLUtype,butspeciallydesignedliponedgeofsealpreventspenetrationbyforeignmatter;lowTorqueconstruction.
Torque
Duetproofing
Waterproofing
Highspeedcapacity
Low
Verygood
Sameasopentype
Dopenddonlubricant
Ratherhigh
Excellent
Verygood
Liltedbycontact$eals
251C-110C
□NTN的深沟球轴承冲压保持架
4.轴承减摩设计案例保持架
□SKF采用PA46塑料保持架减摩
SKF在新一代深沟球轴承中采用PA46+GF30作为标准保持架,摩擦能耗降低30%。
工程塑料保持架PA46+GF30具有耐疲劳、耐摩擦、耐磨损、低扭矩、低噪声、耐腐蚀、长寿命等显著优点,而且比金属保持架成本平均降低60%。
汽午交流发电机、空调压缩机、变速箱轴承中开始推广应用。
□微型汽车驱动桥半轴轴承的减摩设计《轴承》2014N94
仅考虑弹性滞后引起的摩擦力矩堆和接触椭圆上差动滑动引起的摩擦力矩Md
设计结果比较
轴承内部结构参叢
I
Cr
Dy
Z
D庆
f.
(N)
(N.nim)
优化前
13.494
8
59.6
0.515
0.525
28065
5.9282
优化后
13.501
&184
5753
0.515
0.541
27494
5.3019
取值
13.494
8
0.515
(0?
540)
27109
<53582)
4.轴承减摩设计案例——国内
□微型汽车驱动桥半轴轴承的减摩设计《轴承》2014N94
摩擦力矩测试结果比较
轴承状态
平均摩擦力矩(N•]
mm)
1
2
3
4
5
优化前
轴承自身
2.35
2.36
2.38
2.41
2.41
装密封件
29.12
29.09
29.06
29.19
29.10
优化后
轴承自身
1.52
1.54
1.57
1.57
1.60
装密封件
28.28
28.25
28.33
2&3
2&29
结束语
□众多案例表明“减摩型”结构已悄然成为轴承产品最显著的发展方向,特别是在电动汽车、高效能电机与家电(吸尘器、洗衣机)等领域的应用更为突出。
□减摩设计已成为新一代轴承设计准则,是“现在时”和“现在将来进行时”,加强型设计已成为常规设计,必须导入新的设计理念。
□如同“加强型”(长寿命)设计具有成熟的额定载荷与额定寿命理论做指导一样,减摩型设计也具有相对成熟的摩擦学理论为基础。
因此掌握理论在减摩设计中特别重要,具有事半功倍的作用。
(低噪声设计理论不足)。
□摩擦学既是理论科学,又是实验科学。
通过测试等手段将理论无解的复杂因素耦合影响得岀简单答案,是轴承减摩设计的另一途径。
谢谢!