机械制造装备课程设计1.docx
《机械制造装备课程设计1.docx》由会员分享,可在线阅读,更多相关《机械制造装备课程设计1.docx(34页珍藏版)》请在冰豆网上搜索。
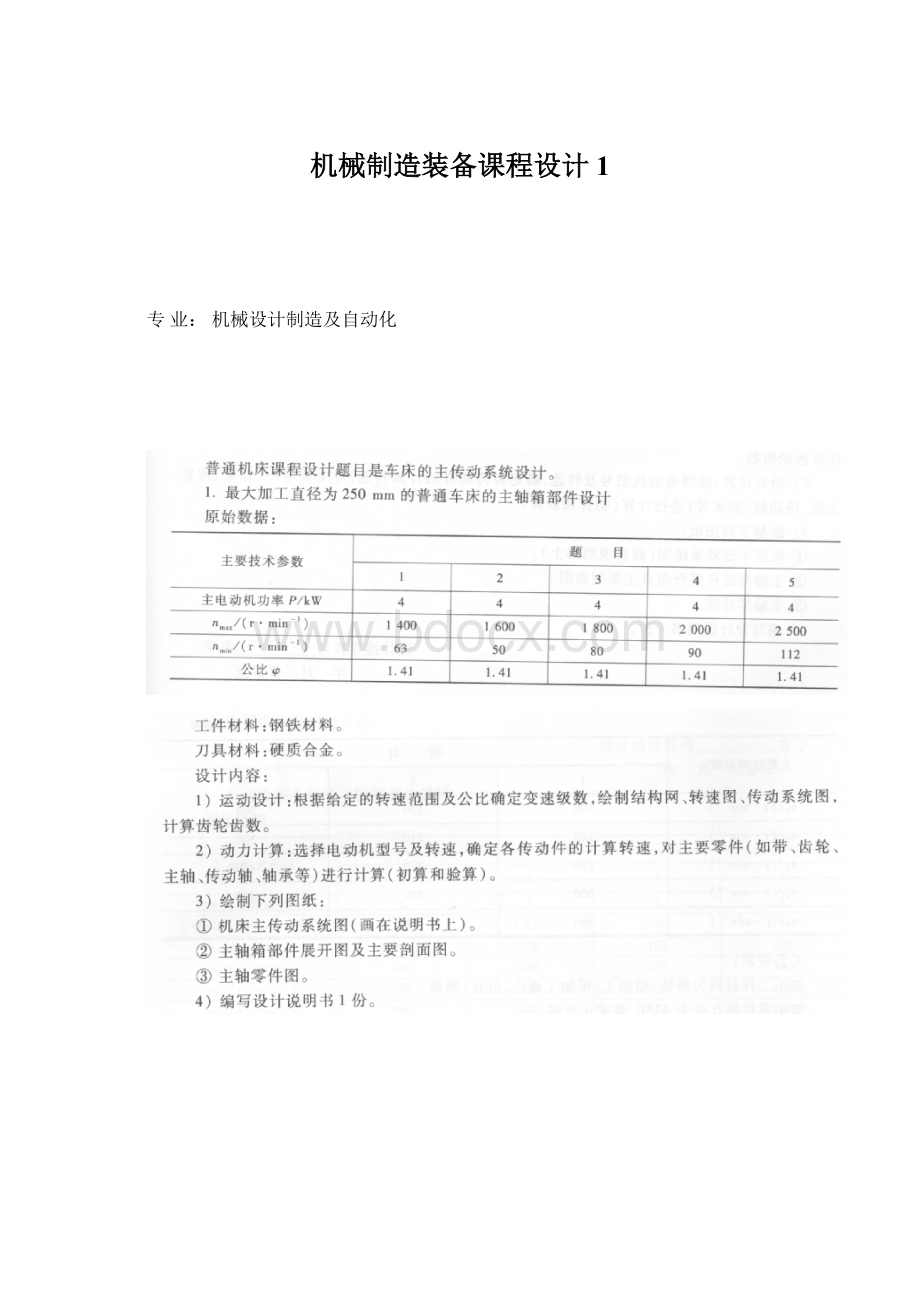
机械制造装备课程设计1
专业:
机械设计制造及自动化
湖北工业大学
机械制造装备设计
课程设计指导书
专业:
机械设计制造及自动化
第一部分机床主传动系统设计
第一章概述
一.机械制造装备课程设计的目的
机械制造装备课程设计是在学生学完《机械制造装备设计》课及其它先行课程之后进行的实践性教学环节,是学生进行设计工作的基本训练。
目的在于:
1、通过机床主传动系统的机械变速机构设计,使学生树立正确的设计思想和掌握机床设计的基本方法;
2、巩固和加深所学理论知识,扩大知识面,并运用所学理论分析和解决设计工作中的具体问题;
3、通过机械制造装备课程设计,使学生在拟订机床主传动机构、机床的构造设计、各种方案的设计、零件的计算、编写技术文件和设计思想的表达等方面,得到综合性的基本训练;
4、熟悉有关标准、手册和参考资料的运用,以培养具有初步的结构分析和结构设计计算的能力。
二、机械制造装备课程设计的内容和工作量
为满足教学要求,达到上述目的,机械制造装备课程设计的题目一般拟订为通用机床主传动系统的变速箱部件设计。
学生应在规定时间内,独立完成下列计算工作量:
1、运动设计学生根据设计任务书所给定的参数和设计要求,在明确所设计机床用途及主要技术性能的基础上,拟订结构网、转速图,确定齿轮齿数,并核算主轴转速误差,画出传动系统图。
2、动力设计根据给定电动机功率,计算主要零件的尺寸,选择材料,验算主要传动件的应力、变形以及寿命等,是否在允许的范围内。
3、机构设计将运动设计所确定的机床主传动系统(其中包括传动轴系、变速机构、主轴组件、换向、制动、操纵机构、润滑密封等)布置在展开图和截面图内,一般要完成零号图纸1张。
4、编写设计计算说明书一份。
详细的设计内容和工作量可见<<机械制造装备课程设计任务书>>和指导教师的具体布置。
三、机械制造装备课程设计的方法步骤和要求
(略,详见本指导书第二章。
)
四、学时分配、计划进度安排
本次课程设计集中安排三周。
根据设计工作程度及对学生的要求,计划进度大致安排如下:
1、理解题目,阅读指导书,拟订总体方案,进行运动设计2天
2、动力设计——主要零件的计算和初算5天
3、结构设计——绘制装配草图2天
4、验算主要零件1天
5、绘制正式装配图2天
6、整理、编写设计计算说明书2天
7、答辩
五、机械制造装备课程设计成绩考核
机械制造装备课程设计结束后,由教研室指派有关教师对学生课程设计进行全面考核,重点考核以下几个方面:
1、工作态度、设计中的表现;
2、刻苦钻研精神,独立工作能力,综合运用所学知识能力;
3、设计图纸和说明书质量;
4、答辩时回答问题情况。
综合以上情况,评定学生课程设计成绩。
成绩分优、良、中、及格、不及格五级。
第二章机械制造装备课程设计的方法步骤和要求
§2—1分析研究题目、进行运动设计
一.理解题目
学生在接受机械制造装备课程设计题目之后,应仔细阅读《机械制造装备课程设计任务书》,了解机课程设计的目的、内容、设计步骤和要求。
然后在教师指导下开展设计工作。
要理解给定的题目,对设计参数进行分析、研究;明确所设计机床的用途和主要技术性能。
二.拟订主传动系统总体结构方案
根据设计题目中所提出的要求及所设计机床的用途,主要技术性能,并参考同类型机床,拟定主传动系统总体结构方案(及其理由),大致包括:
传动形式、变速方式、换向及开停机构、制动机构、润滑装置,操纵机构的选择;变速箱的安装定位方式的选择;电机轴与第Ⅰ轴的联接方式等等.
三.运动设计
关于运动参数,已经统一给定,学生不必花费太多时间去研究,但应该明确参数中的极限转速值nmin和nmax的确定方法,变速级数Z、φ值的大小对机床性能的影响,根据给定的运动参数,完成下列工作:
1、依据给定参数(nmin、nmax、Z、φ),查表确定主轴的各级标准转速,有时要考虑混合公比。
2、列出各种结构和结构网,根据有关原则,通过分析,比较,确定其中最佳方案。
3、设计转速图,根据拟订转速图的原则,确定速比的绝对值,画出转速图。
4、确定齿轮齿数,用计算或查表法确定齿轮齿数.在确定齿数和Sz时应注意:
1)控制齿数和Sz=70~100,Szmax≤120,最小齿轮齿数Zmin≥18~20;
2)小齿轮齿根和孔壁或键槽处的壁厚a≥(1.5~2)m,或Zmin≥6.5+2T/m,
m—为齿轮模数,T—轴线到键槽的高度.
3)保证两轴承孔之间有一定的壁厚a≥2~3m,或Sz>2[(D1+D2)/2+a]/m,
D1,D2—分别为相邻两轴承外径.
4)应保证Ⅰ—Ⅱ轴间有足够的中心距,使车床:
Ⅱ轴上齿轮不碰Ⅰ轴上摩檫离合器,铣床:
不碰电磁制动器.
5)在三联滑移齿轮块中,最大齿轮齿数与其相邻大齿轮齿数之差应≥4,以保证滑动时顺利通过,不碰撞。
6)选齿数较大的一个作公用齿轮.
齿轮齿数确定后,标注在转速图中相应的传动副连线上。
5、核算主轴转速误差,齿轮齿数确定后,主轴的各级实际转速即确定,它与主轴的标准转速总会产生一定的误差,应进行核算。
误差一般不应该超过±10(φ-1)%,即应满足:
︱n实—n标︳/n标≤10(φ-1)%
一般将转速误差的核算列成如下的表格形式:
计算式
n实
n标
误差
允许值10(φ-1)%
结论
6、绘制传动系统图
1)轴,齿轮,离合器,制动器的排列位置,编号应与将要绘制的展开图相一致。
2)标写出电动机的型号、功率、转速、皮带轮直径D1、D2;皮带根数要画上;标写轴号、齿轮的齿数×模数。
3)展开图的轮廓线、传动件和执行件的画法要符合制图标准规定。
§2—2主要零件的计算与初算
初步计算主要零件的目的,是为了大致确定传动件零件的主要尺寸,如皮带轮直径,齿轮模数,传动轴直径和主轴轴径等,以便绘制主轴箱的轴系展开图。
一.皮带设计
皮带设计的已知条件是:
电机功率Nd,转速比i,电机转速nd,计算带轮直径D1、D2,皮带的型号,根数Z,压轴力Q等。
设计原则是不打滑,有足够的寿命,传递最大功率。
二.齿轮模数的初算
在计算齿轮模数和传动轴直径时需要用到其计算转速nj和传递功率Ni,因此应先将各种传动轴和有关齿轮的计算转速nj和各传动轴所传递的功率Ni确定下来,以备计算中使用。
1)只算定比、各变速组中小齿轮的模数。
2)选定标准模数,考虑种类少一些,取一种或两种。
首先确定主轴的计算转速,再根据主轴的计算转速图上查取各传动轴和各齿轮的计算转速。
各轴和齿轮传递的功率Ni=N×η总,η总—由电机到该传动件各传动副的效率相乘,但不乘入该轴承的效率。
效率值见[1]p4表5.1—5。
一般同一变速组中的齿轮取同一模数,选择负荷最重的小齿轮按简化的接触疲劳强度公式进行初算:
式中:
mj—按接触疲劳强度计算的齿轮模数,mm
Nd—驱动电机功率,Kw
nj—计算齿轮的计算转速,rpm
i—大齿轮齿数与小齿轮齿数之比,i≥1;
Z1—小齿轮齿数;
ψm—齿宽系数;ψm=Ⅰ/Ⅱ(B为齿宽,m为模数)
一般ψm=6~10;
[σj]—许用接触应力,当
45#调质(T235)[σj]=600Mpa(N/mm2)
45#整体淬火(C42)1100(N/mm2)
45#高频淬火(G54)1370(N/mm2)
40Cr调质(T265)650(N/mm2)
40Cr整体淬火(C48)1250(N/mm2)
40Cr高频淬火(G52)1370(N/mm2)
齿轮模数初算后,根据齿轮精度等级所允许的线速度(见「1」p225表5.4—52),要核算高速传动齿轮的线速度(
)是否超过允许值。
三.传动轴直径的初算
传动轴的直径可按下列扭转刚度公式进行计算:
或
式中:
d—危险断面处轴的直径,当有一个键槽时,可增大4~5%,当有两个键槽时,可增大7~10%;花键轴内径可减小7%,计算后要圆整到标准直径系列,花键轴系列标准见「1」P554表5.8—17;
Tn—该轴传递的额定扭矩,N.mm
;
Ni—该轴传递的功率,Kw
nj—该轴的计算转速,rpm
[φ]—该轴每米长度上允许的扭转角;
一般传动轴[φ]=0.5~1;
要求较高的轴0.1~0.5o
要求较低的轴1.5~2o
计算传动轴直径时,尺寸相接近的尽量取一致,以便于加工轴和孔,统一刀具和量具。
一般将计算结果列成表格形式,如:
轴号
Ni
nj
d初
d取
花键轴尺寸
备注
四.主轴轴径的确定
对通用机床的主轴尺寸参数多由结构上的需要而定,故主轴前轴颈的尺寸按下表所列的统计数据确定。
通用机床主轴前轴颈尺寸(mm)
机床
主轴的驱动功率(KW)
2.8~4
4~5.5
5.5~7.5
车床
70~90
70~105
95~130
铣床
60~90
60~90
75~100
普通车床主轴前轴颈的直径D1,后轴颈的直径D2及内孔直径d可按统计公式酌定:
D1=0.2Dmax±15(mm)
D2=(0.7~0.85)D1(mm)
d=0.1Dmax±10(mm)
式中:
Dmax—最大加工直径,(mm)
由于初步计算是在绘制装配图之前进行,零件的尺寸、形状和位置尚未确定,在绘制正式装配图过程中变化也比较大。
因此,各零件尺寸的初算,不详细计算,待装配图绘制之后,还需仔细验算。
所以,零件尺寸的初算不用花费过多时间,但齿轮模数计算一定要正确,必要时可以结合类比法确定。
§2—3结构设计—绘制部件装配草图
绘制部件装配草图的目的,是大致确定变速箱部件中各主要传动件(如齿轮、轴、轴承、离合器和箱体等)的轮廓尺寸、形状和相对尺寸等。
部件装配草图是在主要零件尺寸初算的基础上绘制的,又是作为校核验算零件尺寸的依据、草图绘制不必过分细致,但部件中各主要零件要全,尺寸要准确,布局要合理。
装配草图的设计依据是已确定的主传动系统总体结构方案;传动系统图;零件的计算与初算;参考同类型机床的装配图。
一般绘制成1:
1的展开图一张,M1:
2的截面图一张(主要用于表示轴的空间位置和部分操纵机构)。
部件装配草图的画法,可以参考同类型机床的装配图,布置齿轮的轴向位置,研究齿轮的排列方式.如果需要限制轴向尺寸,可采用公用齿轮或齿轮交替布置,或增加定比传动机构。
要注意滑移齿轮要有足够的轴向空间,保证滑移齿轮完全脱开后,才进入新的啮合。
传动轴及轴上零件的轴向定位方式要简单可靠,又要便于装拆和调整等。
根据主轴组件设计的理论知识,参考结构图册或同类型机床的结构,选择合理的主轴组件的结构,包括轴承类型、配置与调整、主轴前端结构(可参考附录3)、主轴的轴向定位方式等。
考虑问题要全面,除传动机构、变速机构外,尚须注意离合器、制动器、操纵机构和润滑密封装置等,都要统盘考虑,选择的形式、布局等要结合截面(或剖视)图,注意空间位置是否会干涉或与移动件相碰撞。
草图绘制完毕后,要请指导教师审阅。
§2—4验算主要零件
根据部件装配图所确定的零件尺寸和各零件间的相互位置关系,分析其受力状态,作用力的大小、方向和着力点位置等,对主要零件进行比较精确的验算。
为了节省时间减少重复的计算工作,可由指导教师指定验算的零件和验算内容。
但学生应明确这些零件一般都是工作情况严重、支承载荷较大。
验算时要着重掌握对问题的分析和计算的方法。
当验算结果不能满足性能要求时,可以改变零件材料、热处理方法或修改部分结构,甚至有时要改变原设计方案。
一.齿轮模数验算
一般按接触疲劳强度和弯曲疲劳强度验算,选取某轴上承受载核最大的齿轮,即同材料、同模数齿轮中齿数最少、齿宽最小的齿轮进行验算。
验算的已知条件为一对啮合的齿轮齿数Z1、Z2,模数m,齿轮传递的功率N,齿轮的精度等级(如8—8—7GB/T10095.1-2001),齿轮材料为45或40Cr,进行高频淬火G52,转速图。
1、按接触疲劳强度验算
2、按弯曲疲劳强度验算
[
]=[
式中,[
]、[
]0-分别为按接触疲劳强度和按弯曲疲劳强度计算所允许传递的最大功率,Kw;
[
]、[
]0分别为在基本条件下,按接触疲劳强度和按弯曲疲劳强度计算的Z1、、m所允许传递的功率,Kw;
[
]0-由[1]P254表5.4-80查取;
[
]0-由[1]P254表5.4-81查取。
这里基本条件是指:
(1)齿轮材料为45#钢,调质T235;
(2)非变位直齿圆柱齿轮;
(3)齿数之比i=1;
(4)
10
(5)小齿轮的计算转数n=1000rpm;
(6)加工装配精确;
(7)寿命系数
。
凡不符合上述基本条件者,在实际使用时,就要按上述两公式,通过相应的系数进行折算。
i-大齿轮与小齿轮齿数之比,
-尺宽系数
nj-该齿轮的计算转数,rpm;
K-材料的弹性模量,由[1]P259表5.4-84;
Kcj、Kcw-分别为材料的接触和弯曲性能系数,由[1]P259表5.4-84。
K1-载荷集中系数,由[1]P259表5.4-87。
K2-动载荷系数,由[1]P260表5.4-87。
Ksj、Ksw-寿命系数,决定因素较多,计算比较复杂,详见[1]P259(7)。
经计算,在此给定:
(车床)
(铣床)
-啮合角影响系数,非变位齿轮
Ksw=0.85
啮合角影响系数,非变位齿轮
;
-齿形系数,非变位外啮合直齿圆柱齿轮
;
N-齿轮实际传递的功率,Kw。
二.传动轴刚度验算
选择一根受载最重的传动轴(一般是主轴前一根传动轴,或指导教师制定),核算其装齿轮处产生的挠度y和装轴承处产生的倾角θ、为什么要进行传动轴刚度的核算?
(略,详见[1]P351:
六),验算步骤如下:
1.计算轴的平均直径,画出计算简图
机床上等径轴较少,当轴的直径相差不大时,可把轴看作等径轴,采用平均直径(各直径之和除以直径数)来进行计算,即
阶梯轴d平
花键轴d平=(d外+d内)/2
一般常将轴简化为集中载荷下的简支梁,选择该轴上转速最低,受力最大的大齿轮(被动)传入该轴,选择该轴上最小的齿轮(主动)传出,这两个齿轮处的受力为载荷点进行计算。
其受力简图为图一。
2.计算该轴传递的扭矩Tn;
式中Ni—该轴传递的功率,Kw;
nj—该轴的计算转速,rpm;
3.求作用在装齿轮处B点的力
切向力
径向力
式中,d—齿轮的分度圆直径,d=mZ;
—压力角,标准齿轮
=200;
—摩擦角,
4.求作用在装齿轮处C点的力
若传入轴、该轴、传出轴三根轴在空间位置的轴心连线夹角小于150,可以认为三轴心在同一直线上(如铣床),按照上面求B点力的方法,求出C点力即可。
若三轴心不在同一直线上(夹角大于150时)需进行坐标转换,将后一对齿轮(C点)啮合力(
、
)投影到前一个坐标(关于X、Y的坐标)之后,在进行挠度计算,车床大都属于这种情况。
如下图所示:
5.计算装齿轮处的挠度
应用[1]P255表5.8-16公式,由表5.8-17中查取轴的惯性矩I,E=2.1×100kgf/cm2=2.1×103N/mm2,在计算中要注意单位的统一,以防出现差错,力的单位用N,长度单位用mm。
另外在应用表5.8-16中公式进行计算时一定要注意计算简图中a、b、x值的相应改变。
一般将计算结果列成表格形式(表中给出所有公式):
第()轴装齿轮B、C处挠度计算
位置
坐标方向
由作用在B点的力产生的挠度
由作用在C点的力产生的挠度
各坐标迭加
合成挠度y
允许值[y]
结论
B
X
载荷点公式
XBB
任意点a段内公式
XBC
XB=XBB+XBC
yB=(XB2+YB2)0.5
表5.8-14
合格
Y
YBB
YBC
YB=YBB+YBC
C
X
任意点b段内公式
XCB
载荷点公式
XCC
XC=XCB+XCC
yC=(XC2+YC2)0.5
表5.8-14
否
Y
YCB
YCC
YC=YCB+YCC
第()轴装轴承处(A、D)的倾角计算
位置
坐标方向
由作用在B点的力产生的倾角
由作用在C点的力产生的倾角
各坐标迭加
合成倾角θ
允许值[θ]
结论
A
X
左支承公式
θXB
左支承公式
θXC
θXA=θXB+θXC
θA=(θXA2+θYA2)0.5
表5.8-14
合格
Y
θYB
θYC
θYA=θYB+θYC
D
X
右支承公式
θXB
右支承公式
θXC
θXD=θXB+θYC
θD=(θXD2+θYD2)0.5
表5.8-14
否
Y
θYB
θYC
θYD=θYB+θYC
6.计算轴承处的倾角
应用表5.8-16公式进行计算,在计算中同样应注意计算简图中a、b值相应改变。
一般将计算结果列成表格形式(表中给出所用公式见P18表格)。
三、轴承寿命验算
轴承受循环接触应力后产生疲劳剥落(龟裂),多长时间才能剥落,即寿命。
寿命是指轴承的内圈、外圈、滚动体三者中。
其一出现疲劳剥落即为到寿命,寿命以小时(h)数表示之。
应满足
Lh≥T
式中,Lh—额定寿命。
h
T—工作期限,h
T的确定机床大修期为8年,每年工作300天,按每天2班制,每班8小时,则总时数为
8×310×2×8=38000h
实际机动时间为10~50%,则
T=30000×(0.4~0.5)=15000~20000h
通常为设计方便,更换不难,取T=10000h即可
额定寿命的计算
式中,n—轴承(即轴)的计算转速,rpm;
ε—寿命指数,球轴承ε=3,滚子轴承ε=10/3;
C—额定动负荷,N,查[1]P670,十四;
P—当量动负荷,N,
P=XFr+YFa
式中,Fr—径向负荷,N,由求支反力解出;
Fa—轴向负荷,N;
X—径向系数,由[1]P584表5.9-18;
Y—轴向系数,由[1]P584表5.9-18;
轴承寿命是个统计数,大多数(90%以上)轴承的实际寿命比它的统计寿命长,如验算结果额定寿命达不到工作期限(相差不太大时),仍可使用,采用提前一、二年更换的办法亦可。
§2―5绘制正式部件装配图
根据草图验算的结果进行必要的修改,把该表示出来的零件清晰正确地绘制在正式装配图上。
绘制正式装配图时机械制造装备课程设计的重要阶段,是前阶段的工作总结,是设计思想的表达。
部件装配图包括展开图和剖面图:
一、设计部件装配图时,学生应对下列问题进行全面分析和比较
1、选用零件类型、结构、主要尺寸、材料、热处理和该零件在部件中的固定方法等。
这些零件包括:
齿轮、轴承、离合器、制动器、换向机构、润滑密封装置、各类轴、轴套和箱体等。
2、确定部件中各零件的位置、相对位置关系及主要尺寸(定位尺寸、移动件的行程极限位置尺寸、主要配合尺寸等)、联接方法、配合性质以及滚动轴承预紧及其精度选择等。
3、零件设计应尽可能遵守标准化、通用化的原则,凡是能用标准件的一定采用标准件,如螺钉、螺帽、轴承、键、垫圈、弹簧、挡圈、销钉、法兰盘等。
4、要注意变速箱部件在机床上的定位,安装方法及其加工基面;各传动轴的轴向定位及其间隙调整方法;运动件的润滑及其润滑系统设计;主轴组件的轴向定位、间隙调整、润滑方式;皮带轮的卸载装置;摩擦离合器的调整、受力分析和设计原则等。
二、绘制装配图的方法步骤
1、在画装配图之前,按部件装配草图的轮廓和结构布置,要统盘考虑全面安排,图面布局要匀称。
一般采用1:
1的比例,必要时可放大或缩小。
然后按传动轴的先后顺序,画出各轴心线的距离,以及各传动轴上的齿轮位置。
2、绘制展开图时要结合剖面图,要结合考虑操纵机构、各轴的空间位置、制动器、换向机构等。
当然操纵机构等在总布置前应确定方案,由于时间关系,在课程设计中,操纵机构根据情况由指导教师研究确定其形式,学生不必花过多的时间。
零件的位置及其相互关系,一般由装配图的“内部向外”画,同时又要考虑装配图的外观轮廓由“外向里”排列。
车床主轴箱长、宽、高尺寸比例以6:
5:
4为宜。
3、适当考虑加工工艺性,要注意部件装配工艺的可能性,特别是主轴和其它较长的传动轴。
有时就是由于零件的结构工艺性不好或零件组装时无法安装,不得不改变原设计方案。
还要注意有调整间隙的组件(如滚动轴承、摩擦离合器和制动器等)要调整方便,易损件容易更换等。
4、部件装配图的底图(或微机草图)绘制完成后,应请指导教师审核,方可加深(或出图)。
§2―6装配图的尺寸标注
由于设计时间所限,并减少重复工作,在对装配图进行尺寸标注时,可根据指导教师的要求,选择一些尺寸进行标注。
这些尺寸大体包括:
部件的外形尺寸;性能尺寸;主要联系尺寸;移动件的极限位置尺寸;主要零件间的配合尺寸等,现分别叙述如下:
一.主要尺寸标注
1、外形尺寸:
主轴箱部件长、宽、高尺寸;
2、性能尺寸:
车床主轴中心高H=D/2+(2~5);
3、主要联系尺寸:
1)车床主轴中心线和床身对称线距离一般为9~12;
2)车床中心至主轴箱前面的距离;
3)车床主轴前端锥孔按标准莫氏锥度;
4)铣床主轴中心线至横梁底面距离150;
5)铣床主轴前锥孔锥度7:
24,主轴前端外径和孔径为:
外径φ101.6h5,孔径φ57.15
外径φ88.882h5,孔径φ44.45
6)主轴或一根传动轴的轴向尺寸(成链)
4、移动件的轴向位置尺寸:
1)滑移齿轮的极限位置尺寸;
2)拨叉极限摆角(铣床)。
5、中心距尺寸:
公差按标准侧隙,由『1』P236表5.4―60。
二.主要配合尺寸的标注
1、主轴(滚动)轴承配合:
1)三支承的主轴主件——
车床:
前支承(D3182100型)外环与孔配合K6,
中间支承外环与孔J6,内环与轴径K5,
后支承外环与孔J7,内环与轴径K6
铣床:
前支承外环与孔K6,内环与轴径n6,
中间支承外环与孔K6,内环与轴径js6,
后支承外环与孔J7,内环与轴径js6.
2)双支承的主轴组件――
车床:
前支承(D3182100型)外环与孔K7,
后支承外环与孔J6,内环与轴径k5。
2、传动轴承配合:
外环与箱体孔J7,内环与轴径k6。
3、花键轴的配合(例如):
1)、滑动:
6×38H7/f7×32H12/b12×12D9/f9
2)、固定:
6×38H12/b12×12D9/f9
4、用键传递扭矩时,轴与孔的配合,如∮80H7/k6
5、滑块与拨叉的配合,如12H9/f9
三.装配图中零件的标注方法
对上述尺寸进行标注之后,应对全部基本件进行编号。
标准件、通用件和借用件,可只标注其标准代号、规格和数量,而不编排其序号和代号。
在编号、标注时应注意以下几点:
对上述尺寸进行标注之后,应对全部