典型零件加工工艺.docx
《典型零件加工工艺.docx》由会员分享,可在线阅读,更多相关《典型零件加工工艺.docx(24页珍藏版)》请在冰豆网上搜索。
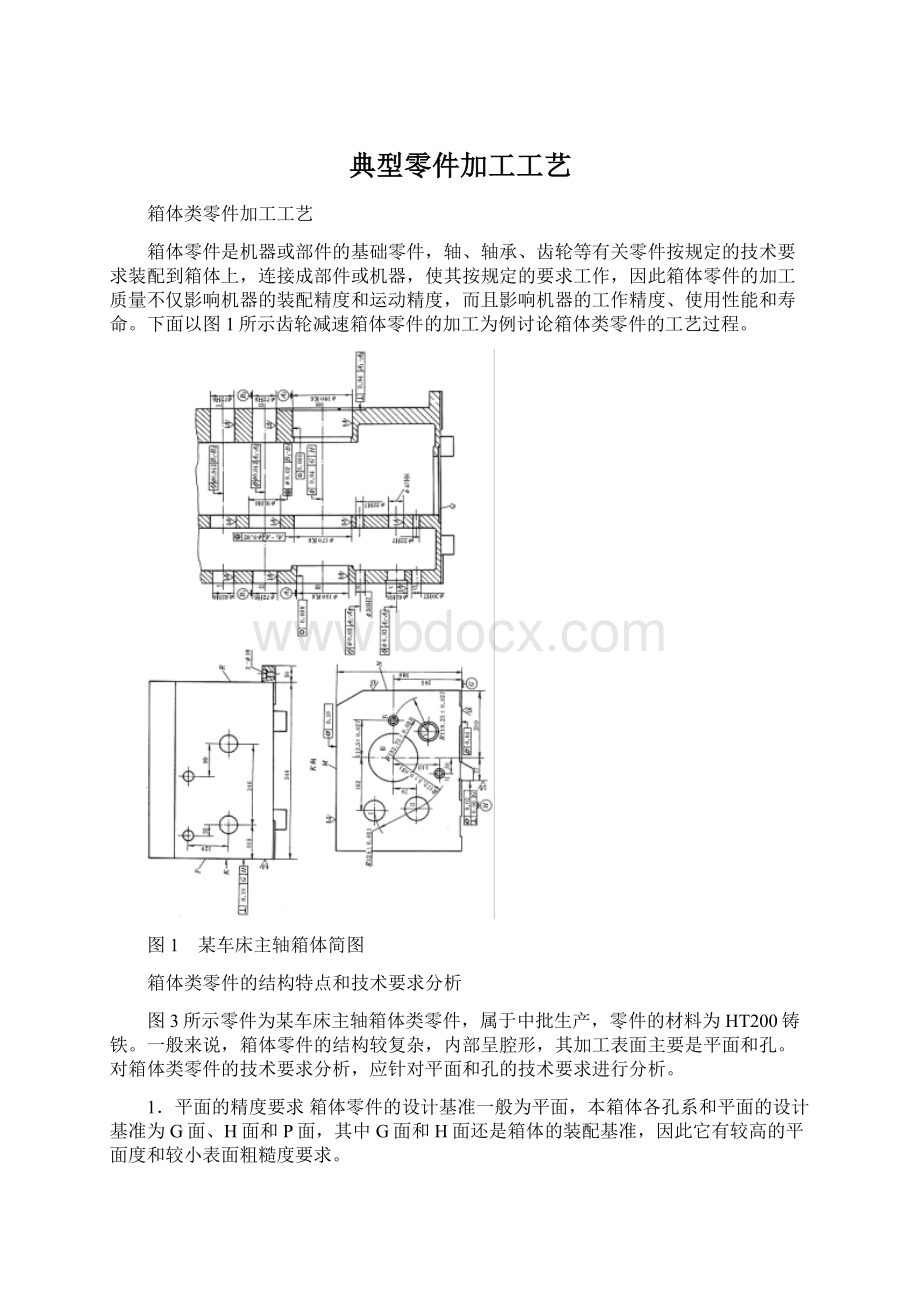
典型零件加工工艺
箱体类零件加工工艺
箱体零件是机器或部件的基础零件,轴、轴承、齿轮等有关零件按规定的技术要求装配到箱体上,连接成部件或机器,使其按规定的要求工作,因此箱体零件的加工质量不仅影响机器的装配精度和运动精度,而且影响机器的工作精度、使用性能和寿命。
下面以图1所示齿轮减速箱体零件的加工为例讨论箱体类零件的工艺过程。
图1 某车床主轴箱体简图
箱体类零件的结构特点和技术要求分析
图3所示零件为某车床主轴箱体类零件,属于中批生产,零件的材料为HT200铸铁。
一般来说,箱体零件的结构较复杂,内部呈腔形,其加工表面主要是平面和孔。
对箱体类零件的技术要求分析,应针对平面和孔的技术要求进行分析。
1.平面的精度要求箱体零件的设计基准一般为平面,本箱体各孔系和平面的设计基准为G面、H面和P面,其中G面和H面还是箱体的装配基准,因此它有较高的平面度和较小表面粗糙度要求。
2.孔系的技术要求 箱体上有孔间距和同轴度要求的一系列孔,称为孔系。
为保证箱体孔与轴承外圈配合及轴的回转精度,孔的尺寸精度为IT7,孔的几何形状误差控制在尺寸公差范围之内。
为保证齿轮啮合精度,孔轴线间的尺寸精度、孔轴线间的平行度、同一轴线上各孔的同轴度误差和孔端面对轴线的垂直度误差,均应有较高的要求。
3.孔与平面间的位置精度箱体上主要孔与箱体安装基面之间应规定平行度要求。
本箱体零件主轴孔中心线对装配基面(G、H面)的平行度误差为0.04mm。
4.表面粗糙度重要孔和主要表面的粗糙度会影响连接面的配合性质或接触刚度,本箱体零件主要孔表面粗糙度为0.8μm,装配基面表面粗糙度为1.6μm。
箱体类零件的材料及毛坯
箱体零件的材料常用铸铁,这是因为铸铁容易成形,切削性能好,价格低,且吸振性和耐磨性较好。
根据需要可选用HT150~350,常用HT200。
在单件小批量生产情况下,为缩短生产周期,可采用钢板焊接结构。
某些大负荷的箱体有时采用铸钢件。
在特定条件下,可采用铝镁合金或其它铝合金材料。
铸铁毛坯在单件小批生产时,一般采用木模手工造型,毛坯精度较低,余量大;在大批量生产时,通常采用金属模机器造型,毛坯精度较高,加工余量可适当减小。
单件小批生产直径大于50mm的孔,成批生产大于30mm的孔,一般都铸出预孔,以减少加工余量。
铝合金箱体常用压铸制造,毛坯精度很高,余量很小,一些表面不必经切削加即可使用。
箱体类零件的加工工艺过程
箱体零件的主要加工表面是孔系和装配基准面。
如何保证这些表面的加工精度和表面粗糙度,孔系之间及孔与装配基准面之间的距离尺寸精度和相互位置精度,是箱体零件加工的主要工艺问题。
箱体零件的典型加工路线为:
平面加工-孔系加工-次要面(紧固孔等)加工。
图1车床主轴箱体零件,其生产类型为中小批生产;材料为HT200;毛坯为铸件。
该箱体的加工工艺路线如表1。
表1车床主轴箱体零件的加工工艺过程
箱体类零件的加工工艺过程分析
一、主要表面的加工方法选择
箱体的主要加工表面有平面和轴承支承孔。
箱体平面的粗加工和半精加工主要采用刨削和铣削,也可采用车削。
当生产批量较大时,可采用各种组合铣床对箱体各平面进行多刀、多面同时铣削;尺寸较大的箱体,也可在多轴龙门铣床上进行组合铣削,可有效提高箱体平面加工的生产率。
箱体平面的
精加工,单件小批量生产时,除一些高精度的箱体仍需手工刮研外,一般多用精刨代替传统的手工刮研;当生产批量大而精度又较高时,多采用磨削。
为提高生产效率和平面间的位置精度,可采用专用磨床进行组合磨削等。
箱体上公差等级为IT7级精度的轴承支承孔,一般需要经过3~4次加工。
可采用扩一粗铰一精铰,或采用粗镗-半精镗一精镗的工艺方案进行加工(若未铸出预孔应先钻孔)。
以上两种工艺方案,表面粗糙度值可达Ra0.8~1.6μm。
铰的方案用于加工直径较小的孔,镗的方案用于加工直径较大的孔。
当孔的加工精度超过IT6级,表面粗糙度值Ra小于0.4μm时,还应增加一道精密加工工序,常用的方法有精细镗、滚压、珩磨、浮动镗等。
二、箱体加工定位基准的选择
1.粗基准的选择粗基准的选择对零件主要有两个方面影响,即影响零件上加工表面与不加工表面的位置和加工表面的余量分配。
为了满足上述要求,一般宜选箱体的重要孔的毛坯孔作粗基准。
本箱体零件就是宜主轴孔Ⅲ和距主轴孔较远的Ⅱ轴孔作为粗基准。
本箱体不加工面中,内壁面与加工面(轴孔)间位置关系重要,因为箱体中的大齿轮与不加工内壁间隙很小,若是加工出的轴承孔与内壁有较大的位置误差,会使大齿轮与内壁相碰。
从这一点出发,应选择内壁为粗基准,但是夹具的定位结构不易实现以内壁定位。
由于铸造时内壁和轴孔是同一个型心浇铸的,以轴孔为粗基准可同时满足上述两方的要求,因此实际生产中,一般以轴孔为粗基准。
2.精基准的选择选择精基准主要是应能保证加工精度,所以一般优先考虑基准重合原则和基准同一原则,本零件的各孔系和平面的设计基准和装配基准为为G、H面和P盖,因此可采用G、H面和P三面作精基准定位。
三、箱体加工顺序的安排
箱体机械加工顺序的安排一般应遵循以下原则:
1.先面后孔的原则箱体加工顺序的一般规律是先加工平面,后加工孔。
先加工平面,可以为孔加工提供可靠的定位基准,再以平面为精基准定位加工孔。
平面的面积大,以平面定位加工孔的夹具结构简单、可靠,反之则夹具结构复杂、定位也不可靠。
由于箱体上的孔分布在平面上,先加工平面可以去除铸件毛坯表面的凹凸不平、夹砂等缺陷,对孔加工有利,如可减小钻头的歪斜、防止刀具崩刃,同时对刀调整也方便。
2.先主后次的原则箱体上用于紧固的螺孔、小孔等可视为次要表面,因为这些次要孔往往需要依据主要表面(轴孔)定位,所以这些螺孔的加工应在轴孔加工后进行。
对于次要孔与主要孔相交的孔系,必须先完成主要孔的精加工,再加工次要孔,否则会使主要孔的精加工产生断续切削、振动,影响主要孔的加工质量。
3.孔系的数控加工
由于箱体零件具有加工表面多,加工的孔系的精度高,加工量大的特点,生产中常使用高效自动化的加工方法。
过去在大批、大量生产中,主要采用组合机床和加工自动线,现在数控加工技术,如加工中心、柔性制造系统等已逐步应用于各种不同的批量的生产中。
车床主轴箱体的孔系也可选择在卧式加工中心上加工,加工中心的自动换刀系统,使得一次装夹可完成钻、扩、铰、镗、铣、攻螺纹等加工,减少了装夹次数,实行工序集中的原则,提高了生产率。
齿轮知识介绍
齿轮简介
齿轮是能互相啮合的有齿的机械零件,它在机械传动及整个机械领域中的应用极其广泛。
现代齿轮技术已达到:
齿轮模数0.004~100毫米;齿轮直径由1毫米~150米;传递功率可达上十万千瓦;转速可达几十万转/分;最高的圆周速度达300米/秒。
齿轮在传动中的应用很早就出现了。
公元前三百多年,古希腊哲学家亚里士多德在《机械问题》中,就阐述了用青铜或铸铁齿轮传递旋转运动的问题。
中国古代发明的指南车中已应用了整套的轮系。
不过,古代的齿轮是用木料制造或用金属铸成的,只能传递轴间的回转运动,不能保证传动的平稳性,齿轮的承载能力也很小。
19世纪出现的滚齿机和插齿机,解决了大量生产高精度齿轮的问题。
1900年,普福特为滚齿机装上差动装置,能在滚齿机上加工出斜齿轮,从此滚齿机滚切齿轮得到普及,展成法加工齿轮占了压倒优势,渐开线齿轮成为应用最广的齿轮。
齿轮种类
齿轮应用广泛,种类很多。
按齿廓曲线可分为渐开线齿轮、摆线齿轮、圆弧齿轮等。
按外形可分为圆柱齿轮、锥齿轮、非圆齿轮、齿条、蜗杆-蜗轮等;
按轮齿所在的表面可分为外齿轮和内齿轮;
按齿线形状可分为直齿轮、斜齿轮、人字齿轮、曲线齿轮等。
按制造方法可分为铸造齿轮、切制齿轮、轧制齿轮、烧结齿轮等。
按齿面硬度可分为软齿面和硬齿面两种。
齿轮图示:
齿轮材料
制造齿轮常用的钢有调质钢、淬火钢、渗碳淬火钢和渗氮钢。
铸钢的强度比锻钢稍低,常用于尺寸较大的齿轮;灰铸铁的机械性能较差,可用于轻载的开式齿轮传动中;球墨铸铁可部分地代替钢制造齿轮;塑料齿轮多用于轻载和要求噪声低的地方,与其配对的齿轮一般用导热性好的钢齿轮。
齿轮加工设备
按照被加工齿轮种类不同,齿轮加工机床可分为两大类:
1.圆柱齿轮加工机床
(1)滚齿机,
(2)插齿机,(3)车齿机等。
2.锥齿轮加工机床
(1)加工直齿锥齿轮:
刨齿机、铣齿机、拉齿机。
(2)加工弧齿锥齿轮:
铣齿机。
(3)加工齿线形状为延伸渐开线:
锥齿轮铣齿机。
(4)精加工齿轮齿面:
珩齿机、剃齿机和磨齿机。
设备特点:
(1)滚齿机滚齿:
可以加工8模数以下的斜齿
(2)铣床铣齿:
可以加工直齿条
(3)插床插齿:
可以加工内齿
(4)冷打机打齿:
可以无屑加工
(5)刨齿机刨齿:
可以加工16模数大齿轮
(6)精密铸齿:
可以大批量加工廉价小齿轮
(7)磨齿机磨齿:
可以加工精密母机上的齿轮
(8)压铸机铸齿:
多数加工有色金属齿轮
(9)剃齿机:
是一种齿轮精加工用的金属切削机床
典型齿轮加工工艺
齿轮加工工艺路线
序号
工序名称
技术内容
1
下料
2
毛坯制造
锻造:
(1)自由锻造:
用于品种多,单件小批量生产
(2)模锻:
主要用于大批量生产;铸造:
用于铸铁齿轮毛坯生产
3
齿坯加工
轴类齿坯加工:
(1)铣两端面
(2)打两中心孔(3)精车颈、外圆、圆锥和端面(4)磨工艺轴颈和定位端面
盘类齿轮加工:
(1)车端面,镗内孔,粗精加工分两道工完成
(2)车端面,镗内孔,粗精加工在一次装夹中完成(3)拉内孔,车端面和外圆工艺
4
加工花键、键槽、螺纹等
根据生产规模,设备情况和精度要求,可以灵活采用多种组合方案;根据不同精度要求选择相应的加工方法,如拉、插、车、磨等。
5
齿形粗加工和半精加工
根据精度要求,从整体毛坯上切出齿槽,有时在槽侧留出适当的精加工余量。
圆柱齿轮:
成形铣削、滚齿、插齿等;
直齿圆锥齿轮:
成形铣削、精锻、粗拉齿、刨齿等
曲线齿锥齿轮:
精锻,专用粗切机铣齿等
6
齿形精加工
(热处理前)
圆柱齿轮:
滚、插、剃、挤
直齿圆锥齿轮:
刨齿、双刀盘铣齿、圆拉法拉齿
曲线齿锥齿轮:
铣齿
7
齿端倒角去毛刺
换档齿轮:
齿端按一定要求修整成一定形状
一般齿轮:
去掉齿两边锐边、毛刺
8
齿轮几何精度
检验
不要求热处理的齿轮,本工序为终检,否则为中间检验
9
热处理
根据材料不同,要求不同而异,常用:
调质、渗碳淬火、高频淬火
10
安装基准面的
精加工
轴类齿轮:
精磨各安装轴颈和定位端面,修整中心孔
盘类齿轮:
精磨内孔及定位端面
本工序多用于分度圆或分度圆锥作定位基准
11
齿形加工
(热处理后)
根据齿轮的精度要求、生产批量和尺寸形状选择加工方法
磨齿:
用于精度要求较高的圆柱、圆锥齿轮,生产效率低
王行齿:
用于降低表面粗糙度,降低噪声,生产效率很高,主要用于大批量生
产
研齿:
用于曲线齿锥齿轮,可降低表面粗糙度,降低噪声及改善接触区
12
强力喷丸
提高齿轮的弯曲疲劳强度和接触疲劳强度
13
磷化处理
为减小齿面间的摩擦,齿面最好进行磷化处理
作用:
降低摩擦系数;在高载荷下防止擦面胶合
14
清理齿面
去除齿面的毛刺、污物
15
成品齿轮的配对检验或最终检验
圆柱齿轮:
按图纸要求检验其几何精度、接触区、噪声
圆锥齿轮:
在滚动检验机上配对,检验接触区位置、大小和形状,
并检验噪声,按配对齿轮打上标记,以便成对装配使用
16
防锈和包装入库
齿轮加工工艺分析(圆柱齿轮为例)
圆柱齿轮的加工工艺程一般应包括以下内容:
齿轮毛坯加工、齿面加工、热处理工艺及齿面的的精加工。
在编制工艺过程中,常因齿轮结构、精度等级、生产批量和生产环境的不同,而采取各种不同的工艺方案。
编制齿轮加工工艺过程大致可以划分如下几个阶段:
1)齿轮毛坯的形成:
锻件、棒料或铸件;
2)粗加工:
切除较多的余量;
3)半精加工:
车、滚、插齿;
4)热处理:
调质、渗碳淬火、齿面高频感应加热淬火等
5)精加工:
精修基准、精加工齿形
1、基准的选择
对于齿轮加工基准的选择常因齿轮的结构形状不同而有所差异。
带轴齿轮主要采用顶点孔定位;对于空心轴,则在中心内孔钻出后,用两端孔口的斜面定位;孔径大时则采用锥堵。
顶点定位的精度高,且能作到基准重合和统一。
对带孔齿轮在齿面加工时常采用以下两种定位、夹紧方式。
(1)以内孔和端面定位这种定位方式是以工件内孔定位,确定定位位置,再以端面作为轴向定位基准,并对着端面夹紧。
这样可使定位基准、设计基准、装配基准和测量基准重合,定位精度高,适合于批量生产。
但对于夹具的制造精度要求较高。
(2)以外圆和端面定位当工件和加剧心轴的配合间隙较大时,采用千分表校正外圆以确定中心的位置,并以端面进行轴向定位,从另一端面夹紧。
这种定位方式因每个工件都要校正,故生产率低;同时对齿坯的内、外圆同轴要求高,而对夹具精度要求不高,故适用于单件、小批生产。
综上所述,为了减少定位误差,提高齿轮加工精度,在加工时应满足以下要求:
1)应选择基准重合、统一的定位方式;
2)内孔定位时,配合间隙应近可能减少;
3)定位端面与定位孔或外圆应在一次装夹中加工出来,以保证垂直度要求。
2、齿轮毛坯的加工
齿面加工前的齿轮毛坯加工,在整个齿轮加工过程中占有很重要的地位。
因为齿面加工和检测所用的基准必须在此阶段加工出来,同时齿坯加工所占工时的比例较大,无论从提高生产率,还是从保证齿轮的加工质量,都必须重视齿轮毛坯的加工。
在齿轮图样的技术部要求中,如果规定以分度圆选齿厚的减薄量来测定齿侧间隙时,应注意齿顶圆的精度要求,因为齿厚的检测是以齿顶圆为测量基准的。
齿顶圆精度太低,必然使测量出的齿厚无法正确反映出齿侧间隙的大小,所以,在这一加工过程中应注意以下三个问题:
1)当以齿顶圆作为测量基准时,应严格控制齿顶圆的尺寸精度;
2)保证定位端面和定位孔或外圆间的垂直度;
3)提高齿轮内孔的制造精度,减少与夹具心轴的配合间隙;
3、齿形及齿端加工
齿形加工是齿轮加工的关键,其方案的选择取决于多方面的因素,如设备条件、齿轮精度等级、表面粗糙度、硬度等。
常用的齿形加工方案在上节已有讲解,在此不再叙述。
齿轮的齿端加工有倒圆、倒尖、倒棱和去毛刺等方式。
经倒圆、倒尖后的齿轮在换档时容易进入啮合状态,减少撞击现象。
倒棱可除去齿端尖角和毛刺。
倒圆时,铣刀告诉旋转,并沿圆弧作摆动,加工完一个齿后,工件退离铣刀,经分度再快速向铣刀靠近加工下一个齿的齿端。
齿端加工必须在淬火之前进行,通常都在滚(插)齿之后,剃齿之前安排齿端加工。
4、轮加工过程中的热处理要求
在齿轮加工工艺过程中,热处理工序的位置安排十分重要,它直接影响齿轮的力学性能及切削加工性。
一般在齿轮加工中进行两种热处理工序,即毛坯热处理和齿形热处理。
轴类零件加工工艺
轴类零件是机器中的常见零件,也是重要零件,其主要功用是用于支承传动零部件(如齿轮、带轮等),并传递扭矩。
轴的基本结构是由回转体组成,其主要加工表面有内、外圆柱面、圆锥面,螺纹,花键,横向孔,沟槽等。
轴类零件的技术要求主要有以下几个方面:
(l)直径精度和几何形状精度轴上支承轴颈和配合轴颈是轴的重要表面,其直径精度通常为IT5~IT9级,形状精度(圆度、圆柱度)控制在直径公差之内,形状精度要求较高时,应在零件图样上另行规定其允许的公差。
(2)相互位置精度轴类零件中的配合轴颈(装配传动件的轴颈)对于支承轴颈的同轴度是其相互位置精度的普遍要求。
普通精度的轴,配合轴颈对支承轴颈的径向圆跳动一般为0.01~0.03mm,高精度轴为0.001~0.005mm。
此外,相互位置精度还有内外圆柱面间的同轴度,轴向定位端面与轴心线的垂直度要求等。
(3)表面粗糙度根据机器精密程度的高低,运转速度的大小,轴类零件表面粗糙度要求也不相同。
支承轴颈的表面粗糙度Ra值一般为0.16~0.63μm,配合轴颈Ra值为0.63~2.5μm。
各类机床主轴是一种典型的轴类零件,图1所示为车床主轴简图。
下面以该车床主轴加工为例,分析轴类零件的工艺过程。
图1车床主轴简图
主轴的主要技术要求分析
1.支承轴颈的技术要求 一般轴类零件的装配基准是支承轴颈,轴上的各精密表面也均以其支承轴颈为设计基准,因此轴件上支承轴颈的精度最为重要,它的精度将直接影响轴的回转精度。
由图1见本主轴有三处支承轴颈表面,(前后带锥度的A、B面为主要支承,中间为辅助支承)其圆度和同轴度(用跳动指标限制)均有较高的精度要求。
2.螺纹的技术要求 主轴螺纹用于装配螺母,该螺母是调整安装在轴颈上的滚动轴承间隙用的,如果螺母端面相对于轴颈轴线倾斜,会使轴承内圈因受力而倾斜,轴承内圈歪斜将影响主轴的回转精度。
所以主轴螺纹的牙形要正,与螺母的间隙要小。
必须控制螺母端面的跳动,使其在调整轴承间隙的微量移动中,对轴承内圈的压力方向正。
3.前端锥孔的技术要求 主轴锥孔是用于安装顶尖或工具的莫氏锥炳,锥孔的轴线必须与支承轴颈的轴线同轴,否则影响顶尖或工具锥炳的安装精度,加工时使工件产生定位误差。
4.前端短圆锥和端面的技术要求 主轴的前端圆锥和端面是安装卡盘的定位面,为保证安装卡盘的定位精度其圆锥面必须与轴颈同轴,端面必须与主轴的回转轴线垂直。
5.其它配合表面的技术要求 如对轴上与齿轮装配表面的技术要求是:
对A、B轴颈连线的圆跳动公差为0.015mm,以保证齿轮传动的平稳性,减少噪音。
上述的
(1)、
(2)项技术要求影响主轴的回转精度,而(3)、(4)项技术要求影响主轴作为装配基准时的定位精度,而第(5)项技术要求影响工作噪音,这些表面的技术要求是主轴加工的关键技术问题。
综上所述,对轴类零件,可以从回转精度、定位精度、工作噪音这三个方面分析其技术要求。
主轴的材料、毛坯和热处理
1.主轴材料和热处理的选择。
一般轴类零件常用材料为45钢,并根据需要进行正火、退火、调质、淬火等热处理以获得一定的强度、硬度、韧性和耐磨性。
对于中等精度而转速较高的轴类零件,可选用40Cr等牌号的合金结构钢,这类钢经调质和表面淬火处理,使其淬火层硬度均匀且具有较高的综合力学性能。
精度较高的轴还可使用轴承钢GCr15和弹簧钢65Mn,它们经调质和局部淬火后,具有更高的耐磨性和耐疲劳性。
在高速重载条件下工作的轴,可以选用20CrMnTi、20Mn2B、20Cr等渗碳钢,经渗碳淬火后,表面具有很高的硬度,而心部强度和冲击韧性好。
在实际应用中可以根据轴的用途选用其材料。
如车床主轴属一般轴类零件,材料选用45钢,预备热处理采用正火和调质,最后热处理采用局部高频淬火。
2.主轴的毛坯。
轴类毛坯一般使用锻件和圆钢,结构复杂的轴件(如曲轴)可使用铸件。
光轴和直径相差不大的阶梯轴一般以圆钢为主。
外圆直径相差较大的阶梯轴或重要的轴宜选用锻件毛坯,此时采用锻件毛坯可减少切削加工量,又可以改善材料的力学性能。
主轴属于重要的且直径相差大的零件,所以通常采用锻件毛坯。
主轴加工的工艺过程
一般轴类零件加工简要的典型工艺路线是:
毛坯及其热处理→轴件预加工→车削外圆→铣键槽等→最终热处理→磨削。
根据车床主轴如图1所示,其生产类型为大批生产;材料为45钢;毛坯为模锻件。
该主轴的加工工艺路线如表1。
表1车床主轴加工工艺过程
主轴加工工艺过程分析
1.定位基准的选择
在一般轴类零件加工中,最常用的定位基准是两端中心孔。
因为轴上各表面的设计基准一般都是轴的中心线,所以用中心孔定位符合基准重合原则。
同时以中心孔定位可以加工多处外圆和端面,便于在不同的工序中都使用中心孔定位,这也符合基准统一原则。
当加工表面位于轴线上时,就不能用中心孔定位,此时宜用外圆定位,例如表1中的第10序钻主轴上的通孔,就是采用以外圆定位方法,轴的一端用卡盘夹外圆,另一端用中心架架外圆,即夹一头,架一头。
作为定位基准的外圆面应为设计基准的支承轴颈,以符合基准重合原则。
如上述工艺过程中的17和23序所用的定位面。
此外,粗加工外圆时为提高工件的刚度,采取用三爪卡盘夹一端(外圆),用顶尖顶一端(中心孔)的定位方式,如上述工艺过程的6、8、9序中所用的定位方式。
由于主轴轴线上有通孔,在钻通孔后(第10序)原中心孔就不存在了,为仍能够用中心孔定位,一般常用的方法是采用锥堵或锥套心轴,即在主轴的后端加工一个1:
20锥度的工艺锥孔,在前端莫氏锥孔和后端工艺锥孔中配装带有中心孔的锥堵,如图2-a所示,这样锥堵上的中心孔就可作为工件的中心孔使用了。
使用时在工序之间不许卸换锥堵,因为锥堵的再次安装会引起定位误差。
当主轴锥孔的锥度较大时,可用锥套心轴,如图2-b所示。
图2锥堵与锥套心轴
为了保证以支承轴颈为基准的前锥孔跳动公差(控制二者的同轴度),采用互为基准的原则选择精基准,即第11、12序以外圆为基准定位车加工锥孔(配装锥堵),第16序以中心孔(通过锥堵)为基准定位粗磨外圆;第17序再一次以支承轴颈附近的外圆为基准定位磨前锥孔(配装锥堵),第21、22序,再一次以中心孔(通过锥堵)为基准定位磨外圆和支承轴颈;最后在第23序又是以轴颈为基准定位磨前锥孔。
这样在前锥孔与支承轴颈之间反复转换基准,加工对方表面,提高相互位置精度(同轴度)。
2.划分加工阶段
主轴的加工工艺过程可划分为三个阶段:
调质前的工序为粗加工阶段;调质后至表面淬火前的工序为半精加工阶段;表面淬火后的工序为精加工阶段。
表面淬火后首先磨锥孔,重新配装锥堵,以消除淬火变形对精基准的影响,通过精修基准,为精加工做好定位基准的准备。
3.热处理工序的安排
45钢经锻造后需要正火处理,以消除锻造产生的应力,改善切削性能。
粗加工阶段完成后安排调质处理,一是可以提高材料的力学性能,二是作为表面淬火的预备热处理,为表面淬火准备了良好的金相组织,确保表面淬火的质量。
对于主轴上的支承轴颈、莫氏锥孔、前短圆锥和端面,这些重要且在工作中经常摩擦的表面,为提高其耐磨性均需表面淬火处理,表面淬火安排在精加工前进行,以通过精加工去除淬火过程中产生的氧化皮,修正淬火变形。
4.安排加工顺序的几个问题
1)深孔加工应安排在调质后进行钻主轴上的通孔虽然属粗加工工序,但却宜安排在调质后进行。
因为主轴经调质后径向变形大,如先加工深孔后调质处理,会使深孔变形,而得不到修正(除非增加工序),安排调质处理后钻深孔,就避免了热处理变形对孔的形状的影响。
2)外圆表面的加工顺序对轴上的各阶梯外圆表面,应先加工大直径的外圆,后加工小直径外圆,避免加工初始就降低工件刚度。
3)铣花键和键槽等次要表面的加工安排在精车外圆之后,否则在精车外圆时产生断续切削,影响车削精度,也易损坏刀具。
主轴上的螺纹要求精度高,为保证与之配装的螺母的端面跳动公差,要求螺纹与螺母成对配车,加工后不许将螺母卸下,以避免弄混。
所以车螺纹应安排在表面淬火后进行。
4)数控车削加工数控机床的柔性好,加工适应性强,适用于中、小批生产。
本主轴加工虽然属于大批生产,但是为便于产品的更新换代,提高时生产效率,保证加工精度的稳定性,在主轴工艺过程中的第15序也可采用数控机床加工,在数控加工工序中,自动的车削各阶梯外圆并自动换刀切槽,采用工序集中方式加工,既提高了加工精度,又保证了生产的高效率。
由于是自动化加工,排除了人为错误的干扰,确保加工质量的稳定性。
取得了良好的经济效益。
同时采用数控加工设备为生产的现代化提供了基础。
在大批生产时,一些关键工序也可以采用数控机床加工。
套筒类零件的结构特点及工艺分析
套筒类零件的加工工艺根据其功用、结构形状、材料和热处理以及尺寸大小的不同而异。
就其结构形状来划分,大