箱体零件加工工艺.docx
《箱体零件加工工艺.docx》由会员分享,可在线阅读,更多相关《箱体零件加工工艺.docx(15页珍藏版)》请在冰豆网上搜索。
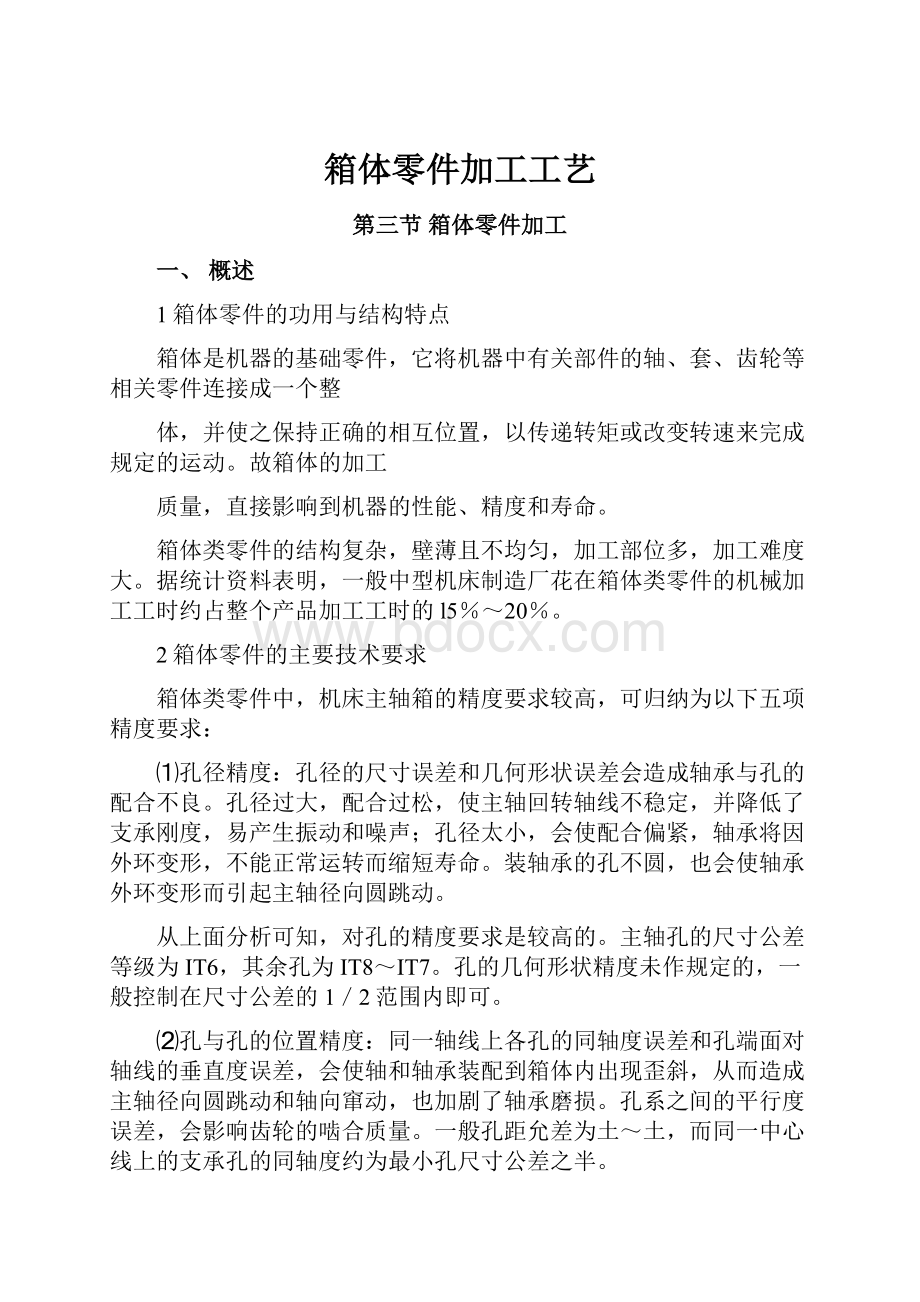
箱体零件加工工艺
第三节箱体零件加工
一、概述
1箱体零件的功用与结构特点
箱体是机器的基础零件,它将机器中有关部件的轴、套、齿轮等相关零件连接成一个整
体,并使之保持正确的相互位置,以传递转矩或改变转速来完成规定的运动。
故箱体的加工
质量,直接影响到机器的性能、精度和寿命。
箱体类零件的结构复杂,壁薄且不均匀,加工部位多,加工难度大。
据统计资料表明,一般中型机床制造厂花在箱体类零件的机械加工工时约占整个产品加工工时的l5%~20%。
2箱体零件的主要技术要求
箱体类零件中,机床主轴箱的精度要求较高,可归纳为以下五项精度要求:
⑴孔径精度:
孔径的尺寸误差和几何形状误差会造成轴承与孔的配合不良。
孔径过大,配合过松,使主轴回转轴线不稳定,并降低了支承刚度,易产生振动和噪声;孔径太小,会使配合偏紧,轴承将因外环变形,不能正常运转而缩短寿命。
装轴承的孔不圆,也会使轴承外环变形而引起主轴径向圆跳动。
从上面分析可知,对孔的精度要求是较高的。
主轴孔的尺寸公差等级为IT6,其余孔为IT8~IT7。
孔的几何形状精度未作规定的,一般控制在尺寸公差的1/2范围内即可。
⑵孔与孔的位置精度:
同一轴线上各孔的同轴度误差和孔端面对轴线的垂直度误差,会使轴和轴承装配到箱体内出现歪斜,从而造成主轴径向圆跳动和轴向窜动,也加剧了轴承磨损。
孔系之间的平行度误差,会影响齿轮的啮合质量。
一般孔距允差为土~土,而同一中心线上的支承孔的同轴度约为最小孔尺寸公差之半。
⑶孔和平面的位置精度:
主要孔对主轴箱安装基面的平行度,决定了主轴与床身导轨的相互位置关系。
这项精度是在总装时通过刮研来达到的。
为了减少刮研工作量,一般规定在垂直和水平两个方向上,只允许主轴前端向上和向前偏。
⑷主要平面的精度:
装配基面的平面度影响主轴箱与床身连接时的接触刚度,加工过程中作为定位基面则会影响主要孔的加工精度。
因此规定了底面和导向面必须平直,为了保证箱盖的密封性,防止工作时润滑油泄出,还规定了顶面的平面度要求,当大批量生产将其顶面用作定位基面时,对它的平面度要求还要提高。
⑸表面粗糙度:
一般主轴孔的表面粗糙度为μm,其它各纵向孔的表面粗糙度为μm;孔的内端面的表面粗糙度为μm,装配基准面和定位基准面的表面粗糙度为~μm,其它平面的表面粗糙度为Ra10~μm。
3箱体零件的材料及毛坯
箱体零件材料常选用各种牌号的灰铸铁,因为灰铸铁具有较好的耐磨性、铸造性和可切
削性,而且吸振性好,成本又低。
某些负荷较大的箱体采用铸钢件。
也有某些简易箱体为了缩短毛坯制造的周期而采用钢板焊接结构的。
二、箱体结构工艺性
箱体机械加工的结构工艺性对实现优质、高产、低成本具有重要的意义。
1、基本孔
箱体的基本孔,可分为通孔、阶梯孔、盲孔、交叉孔等几类。
通孔工艺性最好,通孔内又以孔长L与孔径D之比L/D<=1~的短圆柱孔工艺性为最好;L/D>5的孔,称为深孔,若深度精度要求较高、表面粗糙度值较小时,加工就很困难。
阶梯孔的工艺性与“孔径比”有关。
孔径相差越小则工艺性越好;孔径相差越大,且其
中最小的孔径又很小,则工艺性越差。
相贯通的交叉孔的工艺性也较差。
盲孔的工艺性最差,因为在精镗或精铰盲孔时,要用手动送进,或采用特殊工具送进。
此外,盲孔的内端面的加工也特别困难,故应尽量避免。
2、同轴孔
同一轴线上孔径大小向一个方向递减(如CA6140的主轴孔),可使镗孔时,镗杆从一端伸人,逐个加工或同时加工同轴线上的几个孔,以保证较高的同轴度和生产率。
单件小批生产时一般采用这种分布形式。
同轴线上的孔的直径大小从两边向中间递减(如C620-1,CA6140主轴箱轴孔等),可使刀杆从两边进入,这样不仅缩短了镗杆长度,提高了镗杆的刚性,而且为双面同时加工创造了条件。
所以大批量生产的箱体,常采用此种孔径分布形式。
同轴线上孔的直径的分布形式,应尽量避免中间隔壁上的孔径大于外壁的孔径。
因为加工这种孔时,要将刀杆伸进箱体后装刀、对刀,结构工艺性差。
3、装配基面
为便于加工、装配和检验,箱体的装配基面尺寸应尽量大,形状应尽量简单。
4、凸台
箱体外壁上的凸台应尽可能在一个平面上。
以便可以在一次走刀中加工出来。
而无须调整刀具的位置,使加工简单方便。
5、紧固孔和螺孔
箱体上的紧固孔和螺孔的尺寸规格应尽量一致,以减少刀具数量和换刀次数。
此外,为保证箱体有足够的动刚度与抗振性,应酌情合理使用肋板、肋条,加大圆角半径,收小箱口,加厚主轴前轴承口厚度。
三、箱体机械加工工艺过程及工艺分析
在拟定箱体零件机械加工工艺规程时,有一些基本原则应该遵循。
1先面后孔
先加工平面,后加工孔是箱体加工的一般规律。
平面面积大,用其定位稳定可靠;支承孔大多分布在箱体外壁平面上,先加工外壁平面可切去铸件表面的凹凸不平及夹砂等缺陷,这样可减少钻头引偏,防止刀具崩刃等,对孔加工有利。
2粗精分开、先粗后精
箱体的结构形状复杂,主要平面及孔系加工精度高,一般应将粗、精加工工序分阶段进行,先进行粗加工,后进行精加工。
3基准的选择
箱体零件的粗基准一般都用它上面的重要孔和另一个相距较远的孔作粗基准,以保证孔加工时余量均匀。
精基准选择一般采用基准统一的方案,常以箱体零件的装配基准或专门加工的—面两孔为定位基准,使整个加工工艺过程基准统一,夹具结构类似,基准不重合误差降至最小甚至为零(当基准重合时)。
4工序集中,先主后次
箱体零件上相互位置要求较高的孔系和平面,一般尽量集中在同一工序中加工,以保证其相互位置要求和减少装夹次数。
紧固螺纹孔、油孔等次要工序的安排,一般在平面和支承孔等主要加工表面精加工之后再进行加工。
四、箱体平面的加工方法
箱体平面加工的常用方法有刨、铣和磨三种。
刨削和铣削常用作平面的粗加工和半精加工,而磨削则用作平面的精加工。
刨削加工的特点是:
刀具结构简单,机床调整方便,通用性好。
在龙门刨床上可以利用几个刀架,在工件的一次安装中完成几个表面的加工,能比较经济地保证这些表面间的相互位置精度要求。
精刨还可代替刮研来精加工箱体平面。
精刮时采用宽直刃精刨刀,在经过拉修和调整的刨床上,以较低的切削速度(一般为4~12m/min),在工件表面上切去一层很薄的金属(一般为7~0.lmm)。
精刨后的表面粗糙度值可达0.63~2.51mm,平面度可达0.002mm/m。
因为宽刃精刨的进给量很大(5-25mm/双行程),生产率较高。
铣削生产率高于刨削,在中批以上生产中多用铣削加工平面。
当加工尺寸较大的箱体平面时,常在多轴龙门铣床上,用几把铣刀同时加工各有关平面,以保证平面间的相互位置精度并提高生产率。
近年来端铣刀在结构、制造精度、刀具材料和所用机床等方面都有很大进展。
如不重磨刃端铣刀的齿数少,平行切削刃的宽度大,每齿进给量af可达数毫米。
平面磨削的加工质量比刨削和铣削都高,而且还可以加工淬硬零件。
磨削平面的粗糙度R。
可达0.32~1.25mm。
生产批量较大时,箱体的平面常用磨削来精加工。
为了提高生产率和保证平面间的相互位置精度,工厂还常采用组合磨削来精加工平面。
五、箱体孔系的加工方法
箱体上若干有相互位置精度要求的孔的组合,称为孔系。
孔系可分为平行孔系、同轴孔
图5-12孔系分类
a)平行孔系b)同轴孔系c)交叉孔系
系和交叉孔系(图5-12)。
孔系加工是箱体加工的关键,根据箱体加工批量的不同和孔系精度要求的不同,孔系加工所用的方法也是不同的,现分别予以讨论。
1平行孔系的加工
图5-14样板找正法镗孔
1-样板2-百分表
下面主要介绍如何保证平行孔系孔距精度的方法。
图5-13用心轴和块规找正
a)第一工位b)第二工位
1—心轴2—镗床主轴3—块规4—塞尺5—镗床工作台
⑴找正法
找正法是在通用机床(镗床、铣床)上利用辅助工具来找正所要加工孔的正确位置的加工方法。
这种找正法加工效率低,一般只适于单件小批生产。
找正时除根据划线用试镗方法外,有时借用心轴量块或用样板找正,以提高找正精度。
图5-13所示为心轴和量块找正法。
镗第一排孔时将心轴插入主轴孔内(或直接利用镗床主轴),然后根据孔和定位基准的距离组合一定尺寸的块规来校正主轴位置,校正时用塞尺测定块与心轴之间的间隙,以避免块规与心轴直接接触而损伤块规(图5-13a)。
镗第二排孔时,分别在机床主轴和已加工孔中插入心轴,采用同样的方法来校正主轴轴线的位置,以保证孔心距的精度(图5-13b)。
这种找正法其孔心距精度可达土。
图5-14所示为样板找正法,用l0~20mm厚的钢板制成样板1,装在垂直于各孔的端面上(或固定于机床工作台上),样板上的孔距精度较箱体孔系的孔距精度高(一般
~
),样板上的孔径较工件的孔径大,以便于镗杆通过。
样板上的孔径要求不高,但要有较高的形状精度和较小的表面粗糙度值,当样板准确地装到工件上后,在机床主轴上装一个干分表2,按样板找正机床主轴,找正后,即换上镗刀加工。
此法加工孔系不易出差错,找正方便,孔距精度可达
。
这种样板的成本低,仅为镗模成本的1/7~1/9,单件小批生产中大型的箱体加工可用此法。
⑵镗模法
在成批生产中,广泛采用镗模加工孔系,如图5-15所示。
工件5装夹在镗模上,镗杆4被支承在镗模的导套6里,导套的位置决定了镗杆的位置,
图5-15用镗模加工孔系
1—镗架支承2—镗床主轴3—镗刀4—镗杆5—工件6—导套
装在镗杆上的镗刀3将工件上相应的孔加工出来。
当用两个或两个以上的支承1来引导镗杆时,镗杆与机床主轴2必须浮动联接。
当采用浮动联接时,机床精度对孔系加工精度影响很小,因而可以在精度较低的机床上加工出精度较高的孔系。
孔距精度主要取决于镗模,一般可达
。
能加工公差等级IT7的孔,其表面粗糙度可达Ra5~μm。
当从一端加工、镗杆两端均有导向支承时,孔与孔之间的同轴度和平行度可达~0.03mm;当分别由两端加工时,可达~0.05mm。
用镗模法加工孔系,既可在通用机床上加工,也可在专用机床上或组合机床上加工,图6-12为在组合机床上用镗模加工孔系的示意图。
⑶坐标法
坐标法镗孔是在普通卧式镗床、坐标镗床或数控镗铣床等设备上,借助于精密测量装置,调整机床主轴与工件间在水平和垂直方向的相对位置,来保证孔心距精度的一种镗孔方法。
采用坐标法加工孔系时,要特别注意选择基准孔和镗孔顺序,否则,坐标尺寸累积误差会影响孔距精度。
基准孔应尽量选择本身尺寸精度高、表面粗糙度值小的孔(一般为主轴孔),
这样在加工过程中,便于校验其坐标尺寸。
孔心距精度要求较高的两孔应连在一起加工;加工时,应尽量使工作台朝同一方向移动,因为工作台多次往复,其间隙会产生误差,影响坐标精度。
现在国内外许多机床厂,已经直接用坐标镗床或加工中心机床来加工一般机床箱体。
这样就可以加快生产周期,适应机械行业多品种小批量生产的需要。
图5-17利用已加工孔导向
2同轴孔系的加工
图5-16在组合机床上用镗模加工孔系
1—左动力头2—镗模3—右动力头
4、6—侧底座5—中间底座
成批生产中,箱体上同轴孔的同轴度几乎都由镗模来保证。
单件小批生产中,其同轴度用下面几种方法来保证。
⑴利用已加工孔作支承导向
如图5-17所示,当箱体前壁上的孔加工好后,在孔内装一导向套,以支承和引导镗杆加工后壁上的孔,从而保证两孔的同轴度要求。
这种方法只适于加工箱壁较近的孔。
⑵利用镗床后立柱上的导向套支承导向
这种方法其镗杆系两端支承,刚性好。
但此法调整麻烦,镗杆长,很笨重,故只适于单件小批生产中大型箱体的加工。
⑶采用调头镗
当箱体箱壁相距较远时,可采用调头镗。
工件在一次装夹下,镗好一端孔后,将镗床工作台回转180°,调整工作台位置,使已加工孔与镗床主轴同轴,然后再加工另一端孔。
当箱体上有一较长并与所镗孔轴线有平行度要求的平面时,镗孔前应先用装在镗杆上的
图5-18调头镗孔时工件的校正
a)第一工位b)第二工位
百分表对此平面进行校正(图5-18a),使其和镗杆轴线平行,校正后加工孔B,孔B加工后,回转工作台,并用镗杆上装的百分表沿此平面重新校正,这样就可保证工作台准确地回转180°,见图5-18b。
然后再加工孔A,从而保证孔A、B同轴。
六、车床主轴箱的加工工艺过程
1、图5-19所示为CA6140车床主轴箱箱体的零件简图。
其加工工艺过程如表5-5、5-6所示。
图5-19CA6140车床主轴箱体零件简图
表5-5主轴箱小批生产工艺过程
序号
工序内容
定位基准
1
铸造
2
时效
3
漆底漆
4
划线:
考虑主轴孔有加工余量,并尽量均匀。
划C、A及E、D加工线
5
粗、精加工顶面A
按线找正
6
粗、精加工B、C面及侧面D
顶面A并校正主轴线
7
粗、精加工两端面E、F
B、C面
8
粗、半精加工各纵向孔
B、C面
9
精加工各纵向孔
B、C面
10
粗、精加工横向孔
B、C面
11
加工螺孔及各次要孔
12
清洗、去毛刺倒角
13
检验
表5-6主轴箱大批生产工艺过程
序号
工序内容
定位基准
1
铸造
2
时效
3
漆底漆
4
铣顶面A
I孔与II孔
5
钻、扩、绞2-Ф8H7工艺孔(将6-M10mm先钻至Ф,绞2-Ф8H7)
顶面A及外形
6
铣两端面E、F及前面D
顶面A及两工艺孔
7
铣导轨面B、C
顶面A及两工艺孔
8
磨顶面A
导轨面B、C
9
粗镗各纵向孔
顶面A及两工艺孔
10
精镗各纵向孔
顶面A及两工艺孔
11
精镗主轴孔I
顶面A及两工艺孔
12
加工横向孔及各面上的次要孔
13
磨B、C导轨面及前面D
顶面A及两工艺孔
14
将2-Ф8H7及4-Ф均扩钻至Ф,攻6-M10mm
15
清洗、去毛刺倒角
16
检验
2、制订箱体工艺过程的共同性原则
1)加工顺序为先面后孔箱体类零件的加工顺序均为先加工面,以加工好的平面定位,再来加工孔。
因为箱体孔的精度要求高,加工难度大,先以孔为粗基准加工平面,再以平面为精基准加工孔,这样不仅为孔的加工提供了稳定可靠的精基准,同时还可以使孔的加工余量较为均匀。
由于箱体上的孔分布在箱体各平面上,先加工好平面,钻孔时,钻头不易引偏,扩孔或绞孔时,刀具也不易崩刃。
2)加工阶段粗、精分开箱体的结构复杂,壁厚不均,刚性不好,而加工精度要求又高,故箱体重要加工表面都要划分粗、精加工两个阶段,这样可以避免粗加工造成的内应力、切削力、夹紧力和切削热对加工精度的影响,有利于保证箱体的加工精度。
粗、精分开也可及时发现毛坯缺陷,避免更大的浪费;同时还能根据粗、精加工的不同要求来合理选择设备,有利于提高生产率。
3)工序间合理按排热处理箱体零件的结构复杂,壁厚也不均匀,因此,在铸造时会产生较大的残余应力。
为了消除残余应力,减少加工后的变形和保证精度的稳定,所以,在铸造之后必须安排人工时效处理。
人工时效的工艺规范为:
加热到500oC~550oC,保温4h~6h,冷却速度小于或等于30oC/h,出炉温度小于或等于200oC。
普通精度的箱体零件,一般在铸造之后安排1次人工时效出理。
对一些高精度或形状特别复杂的箱体零件,在粗加工之后还要安排1次人工时效处理,以消除粗加工所造成的残余应力。
有些精度要求不高的箱体零件毛坯,有时不安排时效处理,而是利用粗、精加工工序间的停放和运输时间,使之得到自然时效。
箱体零件人工时效的方法,除了加热保温法外,也可采用振动时效来达到消除残余应力的目的。
4)用箱体上的重要孔作粗基准箱体类零件的粗基准一般都用它上面的重要孔作粗基准,这样不仅可以较好地保证重要孔及其它各轴孔的加工余量均匀,还能较好地保证各轴孔轴心线与箱体不加工表面的相互位置。
1.定位基准的选择
1)粗基准的选择虽然箱体类零件一般都选择重要孔(如主轴孔)为粗基准,但随着生产类型不同,实现以主轴孔为粗基准的工件装夹方式是不同的。
①中小批生产时,由于毛坯精度较低,一般采用划线装夹,其方法如下:
首先将箱体用千斤顶安放在平台上(图5-20a),调整千斤顶,使主轴孔I和A面与台面基本平行,D面与台面基本垂直,根据毛坯的主轴孔划出主轴孔的水平线I-I,在4个面上均要划出,作为第1校正线。
划此线时,应根据图样要求,检查所有加工部位在水平方向是否均有加工余量,若有的加工部位无加工余量,则需要重新调整I-I线的位置,作必要的借正,直到所有的加工部位均有加工余量,才将I-I线最终确定下来。
I-I线确定之后,即画出A面和C面的加工线。
然后将箱体翻转90o,D面一端置于3个千斤顶上,,调整千斤顶,使I-I线与台面垂直(用大角尺在两个方向上校正),根据毛坯的主轴孔并考虑各加工部位在垂直方向的加工余量,按照上述同样的方法划出主轴孔的垂直轴线II-II作为第2校正线(图5-20b),也在4个面上均画出。
依据II-II线画出D面加工线。
再将箱体翻转90o(图5-20c),将E面一端至于3个千斤顶上,使I-I线和II-II线与台面垂直。
根据凸台高度尺寸,先画出F面,然后再画出E面加工线。
图5-20主轴箱的划线
加工箱体平面时,按线找正装夹工件,这样,就体现了以主轴孔为粗基准。
②大批大量生产时,毛坯精度较高,可直接以主轴孔在夹具上定位,采用图5-21的夹具装夹。
先将工件放在1、3、5预支承上,并使箱体侧面紧靠支架4,端面紧靠挡销6,进行工件预定位。
然后操纵手柄9,将液压控制的两个短轴7伸人主轴孔中。
每个短轴上有3个活动支柱8,分别顶住主轴孔的毛面,将工件抬起,离开1、3、5各支承面。
这时,主轴孔轴心线与两短轴轴心线重合,实现了以主轴孔为粗基准定位。
为了限制工件绕两短轴的回转自由度,在工件抬起后,调节两可调支承12,辅以简单找正,使顶面基本成水平,再用螺杆11调整辅助支承2,使其与箱体底面接触。
最后操纵手柄10,将液压控制的两个夹紧块13插入箱体两端相应的孔内夹紧,即可加工。
①单件小批生产用装配基面做定位基准。
图5-19车床床头箱单件小批加工孔系时,选择箱体底面导轨B、C面做定位基准,B、C面既是床头箱的装配基准,又是主轴孔的设计基准,并与箱体的两端面、侧面及各主要纵向轴承孔在相互位置上有直接联系,故选择B、C面作定位基准,不仅消除了主轴孔加工时的基准不重合误差,而且用导轨面B、C定位稳定可靠,装夹误差较小,加工各孔时,由于箱口朝上,所以更换导向套、安装调整刀具、测量孔径尺寸、观察加工情况等都很方便。
2)精基准的选择箱体加工精基准的选择也与生产批量大小有关。
图5-21以主轴孔为粗基准铣顶面的夹具
1、3、5—支承2—辅助支承4—支架6—挡销7—短轴8—活动支柱
9、10—操纵手柄11—螺杆12—可调支承13—夹紧块
这种定位方式也有它的不足之处。
加工箱体中间壁上的孔时,为了提高刀具系统的刚度,应当在箱体内部相应的部位设置刀杆的导向支承。
由于箱体底部是封闭的,中间支承只能用如图5-22所示的吊架从箱体顶面的开口处伸人箱体内,每加工一件需装卸一次,吊架与镗模之间虽有定位销定位,但吊架刚性差,制造安装精度较低,经常装卸也容易产生误差,且使加工的辅助时间增加,因此这种定位方式只适用于单件小批生产。
图5-22吊架式镗模夹具
图5-23箱体以一面两孔定位
②量大时采用一面两孔作定位基准。
大批量生产的主轴箱常以顶面和两定位销孔为精基准,如图5-23所示。
这种定位方式是加工时箱体口朝下,中间导向支架可固定在夹具上。
由于简化了夹具结构,提高了夹具的刚度,同时工件的装卸也比较方便,因而提高了孔系的加工质量和劳动生产率。
这种定位方式的不足之处在于定位基准与设计基准不重合,产生了基准不重合误差。
为了保证箱体的加工精度,必须提高作为定位基准的箱体顶面和两定位销孔的加工精度。
另外,由于箱口朝下,加工时不便于观察各表面的加工情况,因此,不能及时发现毛坯是否有砂眼、气孔等缺陷,而且加工中不便于测量和调刀。
所以,用箱体顶面和两定位销孔作精基准加工时,必须采用定径刀具(扩孔钻和绞刀等)。
上述两种方案的对比分析,仅仅是针对类似床头箱而言,许多其它形式的箱体,采用一面两孔的定位方式,上面所提及的问题也不一定存在。
实际生产中,一面两孔的定位方式在各种箱体加工中应用十分广泛。
因为这种定位方式很简便地限制了工件6个自由度,定位稳定可靠;在一次安装下,可以加工除定位以外的所有5个面上的孔或平面,也可以作为从粗加工到精加工的大部分工序的定位基准,实现“基准统一”;此外,这种定位方式夹紧方便,工件的夹紧变形小;易于实现自动定位和自动夹紧。
因此,在组合机床与自动线上加工箱体时,多采用这种定位方式。
以上分析可知:
箱体精基准的选择有两种方案:
一是以3平面为精基准(主要定位基面为装配基面);另一是以一面两孔为精基准。
这两种定位方式各有优缺点,实际生产中的选用与生产类型有很大的关系。
通常从“基准统一”,中小批生产时,尽可能使定位基准与设计基准重合,即一般选择设计基准作为统一的定位基准;大批大量生产时,优先考虑的是如何稳定加工质量和提高生产率,不过分地强调基准重合问题,一般多用典型的一面两孔作为统一的定位基准,由此而引起的基准不重合误差,可采用适当的工艺措施去解决。