TY220型拖拉机离合器设计.docx
《TY220型拖拉机离合器设计.docx》由会员分享,可在线阅读,更多相关《TY220型拖拉机离合器设计.docx(18页珍藏版)》请在冰豆网上搜索。
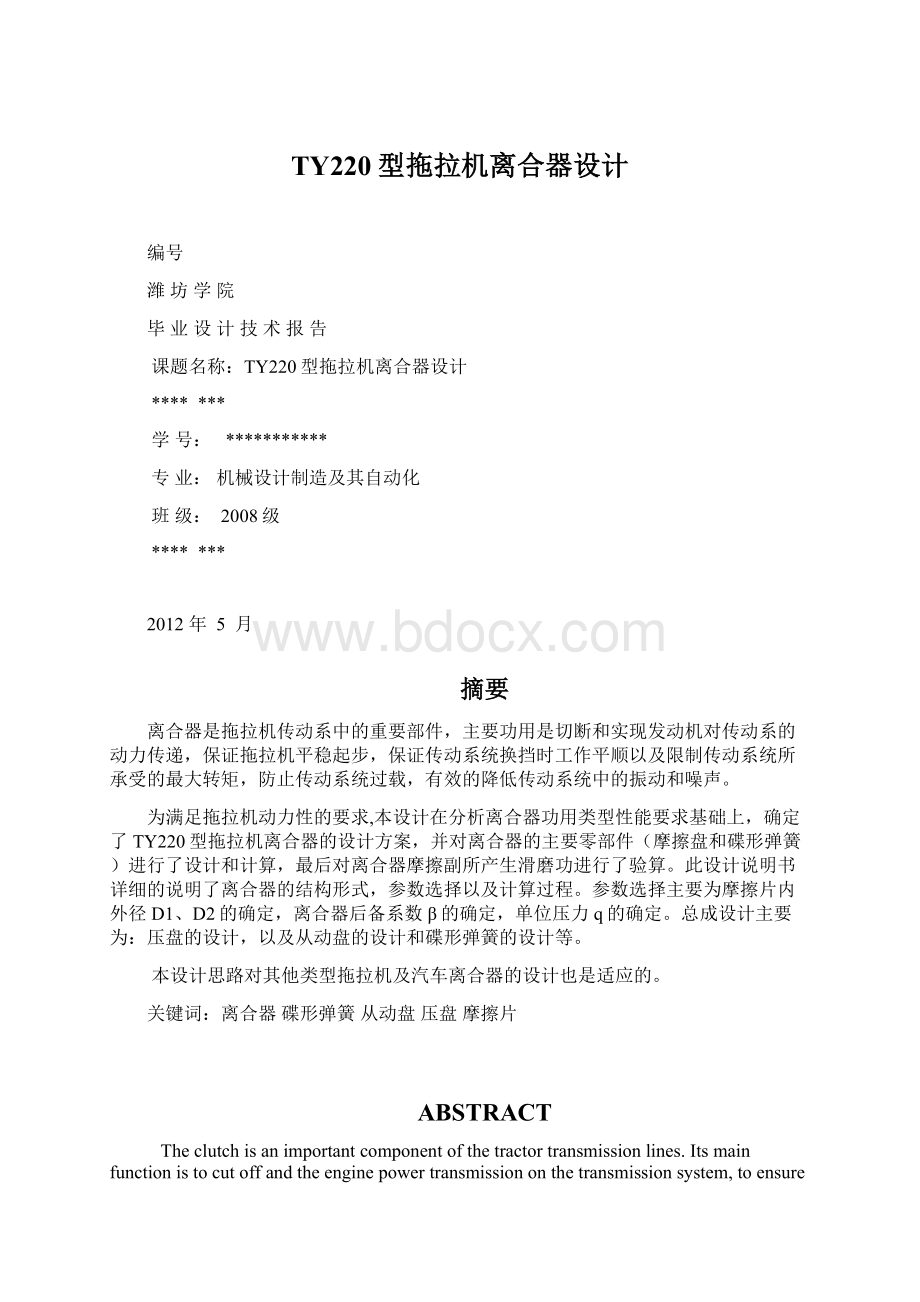
TY220型拖拉机离合器设计
编号
潍坊学院
毕业设计技术报告
课题名称:
TY220型拖拉机离合器设计
*******
学号:
***********
专业:
机械设计制造及其自动化
班级:
2008级
*******
2012年5月
摘要
离合器是拖拉机传动系中的重要部件,主要功用是切断和实现发动机对传动系的动力传递,保证拖拉机平稳起步,保证传动系统换挡时工作平顺以及限制传动系统所承受的最大转矩,防止传动系统过载,有效的降低传动系统中的振动和噪声。
为满足拖拉机动力性的要求,本设计在分析离合器功用类型性能要求基础上,确定了TY220型拖拉机离合器的设计方案,并对离合器的主要零部件(摩擦盘和碟形弹簧)进行了设计和计算,最后对离合器摩擦副所产生滑磨功进行了验算。
此设计说明书详细的说明了离合器的结构形式,参数选择以及计算过程。
参数选择主要为摩擦片内外径D1、D2的确定,离合器后备系数β的确定,单位压力q的确定。
总成设计主要为:
压盘的设计,以及从动盘的设计和碟形弹簧的设计等。
本设计思路对其他类型拖拉机及汽车离合器的设计也是适应的。
关键词:
离合器碟形弹簧从动盘压盘摩擦片
ABSTRACT
Theclutchisanimportantcomponentofthetractortransmissionlines.Itsmainfunctionistocutoffandtheenginepowertransmissiononthetransmissionsystem,toensurethetractorsmoothstart-upandtransmissionshiftsmooth.Anditlimitsthetransmissionsystemtowithstandthemaximumtorquetopreventthetransmissionsystemoverload.Itiseffectivetoreducevibrationandnoiseinthetransmissionsystem.
Inordertosatisfytherequirementofthetractor,thisarticledeterminedthedesign-planofclutchesforTY220tractor,designedandcalculatedthemajorpartsofclutches(drivesystemanddiscspring),whichisbasedonanalyzingthefunctionstypesandperformancesrequiredoftheclutches.Finally,thisarticlecheckedthefrictionworkoftractorclutches.Thisdesignmanualexplainsindetailthestructureoftheclutch,theparameterselectionandcalculationprocess.ParameterselectiontodeterminethefrictionplateouterdiameterD1,D2,clutchreservecoefficientβ,thedeterminationoftheunitpressureq.Assemblydesignasfollows:
pressureplatedesign,aswellasthefollowerplateandthedesignofdiscspringetc.
Thedesignideaalsoadaptsthedesignofothertypesoftractorandautomobileclutch.
Keywords:
clutchdiscspringdriveplatedrivenplateFrictionplate
前言
离合器是拖拉机传动系统中直接与发动机相连接的部件。
按动力传递顺序来说,离合器应是传动系中的第一总成。
顾名思义,离合器是“离”与“合”矛盾的统一体。
离合器的工作,就是受驾驶员操纵,或者分离,或者接合,以完成其本身的任务。
离合器是设置在发动机与变速器之间的动力传递机构,其功用是能够在必要时中断动力的传递,保证汽车平稳地起步;保证传动系换档时工作平稳;限制传动系所能承受的最大扭矩,防止传动系过载。
为使离合器起到以上几个作用,目前拖拉机上广泛采用弹簧压紧的摩擦式离合器,摩擦离合器所能传递的最大扭矩取决于摩擦面间的工作压紧力和摩擦片的尺寸以及摩擦面的表面状况等,即主要取决于离合器基本参数和主要尺寸。
蝶形弹簧离合器在技术上比较先进,经济性合理,同时其性能良好,使用可靠性高寿命长,结构简单、紧凑,操作轻便。
第1章绪论
1.1离合器的功用和要求
离合器用以切断发动机传来的动力,使变数箱得以摘档和挂档;平顺接合保证拖拉机平稳起步;限制传动系过载。
拖拉机广泛采用片式摩擦离合器,其结构简单,接合后传递动力时几乎没有功率损失。
对这种离合器的性能要求是:
(1)能可靠地传递发动机全部扭矩,接合后不产生滑磨;
(2)分离彻底、迅速;
(3)接合平顺,以减少拖拉机起步过程中的冲击载荷;
(4)从动部分转动惯量小,以减少变速箱挂档时的冲击载荷;
(5)散热良好;
(6)操纵轻便。
1.2离合器的类型
摩擦离合器按摩擦面的工作条件,分为干式和湿式两种。
干式离合器结构简单广泛用在农业拖拉机上。
湿式离合器用油液冷却摩擦表面,散热良好,摩擦表面工作性能稳定,在长期使用后磨损很小,但结构复杂,重量大,成本高,主要用接合频繁的工业拖拉机上。
按摩擦片的数目,可分为单片、双片和多片式。
单片离合器结构简单,分离彻底,散热良好,从动部分转动惯量小,在中小拖拉机上普遍采用(图1.1)。
双片和多片离合器接合较平顺,在与单片式传递同样转矩的情况下其径向尺寸和操纵力较小,但中间压盘不易散热,分离彻底性较差,从动部分转动惯量较大。
对于干式离合器来说,设计时宜优先采用单片式,仅在单片的直径过分增大而显得不合理时,或受外廓限制无法增大时,才选择双片式或多片式。
图1.2是布置在皮带轮内的手扶拖拉机离合器。
湿式离合器则多为双片或多片式。
按摩擦面的压紧方式,分为弹簧压紧式、杠杆压紧式和液压压紧式。
弹簧压紧式通常做成经常接合的,只有踩下踏板才能分离,放松踏板即自行结合。
杠杆压紧式通常做成非经常接合的,不论分离或接合都要移动操纵手杆。
液压压紧式则是用工作油液推动油缸的活塞或缸体,直接压紧摩擦表面。
由于液压油缸在旋转状态下工作,制造精度要
图1.1单片干式离合器图1.2双片干式离合器
1-副离合器分离杠杆2-主离合器从动盘3-主离合器分离杠杆4-副离合器从动盘
图1.3独立操纵式双作用离合器
求较高,主离合器中用的很少,但结构紧凑,在摩擦式换挡变速箱中广为采用。
按离合器在传动系中的作用,分为单作用式和双作用式。
单作用离合器(图1.1)只有一套从动盘和从动轴,向驱动轮及非独立式动力输出轴传递动力。
双作用离合器有两套从动盘和从动轴,因而可看成有两个离合器组成,其中的主离合器控制传往驱动轮的动力,副离合器控制传往动力输出轴的动力。
当主、副离合器分别用两套操纵机构、分离和接合互不相关时,称为独立操纵式双作用离合器(图1.3),它可获得独立式动力输出轴,但操纵机构较复杂。
当主、副离合器共用一套操纵机构、分离和接合按一定次序时,称为联动操纵式双作用离合器。
与独立操纵式相比,联动操纵式为了分离副离合器,所花费的操纵力和操纵功都大大增加,但只需一套操作机构,也能满足较多的农艺要求,故采用甚广。
主、副离合器有不同的布置方式。
图1.4中的主离合器在前、副离合器在后,用各自的蝶形弹簧压紧。
图1.5中副离合器在前,用蝶形弹簧压紧;主离合器在后,用螺旋弹簧压紧。
这两个离合器的共同特点是主、副离合器之间安装了隔板,但主离合器接合
1-主离合器从动盘2-前压盘3-隔板
4-副离合器从动盘5-离合器盖1-副离合器从动盘
6-蝶形弹簧7-后压盘8-分离螺钉2-主离合器从动盘
9-蝶形弹簧
图1.4主离合器在前的联动操纵式双作用离合器图1.5主离合器在后的联动操纵式双作用离合器
时,不影响副离合器的压紧力。
图1.6的离合器则不同。
在图1.6a中,当主离合器结合时,主离合器受弹簧2的压力,副离合器却受弹簧1、2的共同压力,被过分压紧;
当主离合器分离时,弹簧2的压力被踏板上的操纵力抵消,副离合器才只受弹簧1的压力。
在图1.6b中,主副离合器共用一组压紧弹簧2,当主离合器分离时,副离合器所受的压紧力增加,被过分压紧。
第2章离合器主要参数的确定
片式摩擦离合器的主要参数包括:
离合器储备系数β、摩擦面所受压紧力Q0,摩擦面外径D2和内径D1,摩擦面对数i。
2.1离合器储备系数β的确定
储备系数β是离合器的最大摩擦扭矩MLmax与发动机标定扭矩MeN之比,可写成:
式(2-1)
在离合器使用过程中,由于摩擦面的磨损、油污、弹簧压紧力下降等原因,都可能降低离合器传递扭矩的能力。
为了保证离合器工作过程中能传递发动机全部扭矩,并减小接合过程中的滑摩功〔见式(2-15)〕,储备系数β不宜过小。
但加大β将会增加离合器的尺寸重量以及操纵力和操纵功,并减小防护传东西过载的作用。
多数弹簧压紧式和带有补偿弹簧的杠杆压紧式离合器,β=2.5~2.8;不带补偿弹簧的杠杆压紧式离合器,β=2.8~3.5;双作用离合器中的副离合器的储备系数可低于主离合器,但通常不小于1.3~1.5。
本设计要设计的是TY220型拖拉机离合器设计,可选主离合器的储备系数
=2.5,副离合器的储备系数
=1.6。
最大摩擦扭矩MLmax由下列参数决定:
式(2-2)
式中µ——摩擦系数;
Q0——摩擦面所受压紧力;
Rp——摩擦合力作用半径;
i——摩擦面对数。
摩擦系数µ与摩擦材料、温度、相对滑摩速度和单位压力等有关,设计时假定只与材料有关,从表2.1选取。
计算干式石棉对铸铁或钢的摩擦副时,一般取µ=0.3。
当摩擦面为环状时,摩擦合力作用半径可足够精确地取为外径和内径的平均值:
式(2-3)
式中D2、D1——摩擦面的外直径和内直径。
a)压紧力减小b)压紧力增大
1-副离合器压紧弹簧2-同时压紧主、副离合器的弹簧3-副离合器轴4-主离合器轴
5-动力输出轴的传动轴
图1.6主离合器分离时副离合器所受压紧力发生变化的双作用离合器
表2.1摩擦因数
与单位压力q
摩擦副材料
q
干式
湿式
干式
湿式
钢、铸铁对钢
铸铁、铁对石棉
铸铁、钢对粉末冶金
0.15~0.18
0.25~0.30
0.25~0.40
0.03~0.08
0.08~0.15
0.08~0.12
0.25~0.40
0.10~0.25
0.40~0.60
0.6~1.0
0.2~0.5
1.2~2.0
2.2离合器摩擦片内外径D1、D2的确定
据统计,石棉材料的单片干式摩擦面外直径D2多在如下范围内:
式(2-4)
式中MeN的单位为N·m。
对于双片式离合器,式中的系数更小。
选定外径D2后,如缩小内径D1可增加摩擦面积,但会使摩擦面所受的压力分布不均、内沿与外沿的相对滑摩速度的差距加大,造成摩擦面的磨损不均匀。
因此,一般趋向于使D1与D2较为接近,多数拖拉机D1=(0.55~0.75)D2=0.7×200=140(mm),
。
摩擦面对数i=m+n–1=2(m——主动片数,n——从动片数)。
选取上述参数后,即可计算出压紧力Q0=βMeN/µRpi=167.95/0.3×85×2=3290N。
验算单位压力:
使之符合表2.1所给的范围:
式(2-5)
式中F——每个摩擦面的面积,环状摩擦面F=0.25π(D22-D12)=16×103(mm3)。
第3章离合器的接合过程和滑摩功验算
3.1离合器的接合过程
拖拉机机组通过离合器主动盘和从动盘逐渐接合而起步。
在接合过程中,摩擦面产生相对滑摩而发热。
其接合过程如图3.1所示。
开始结合前发动机以ωe0的角速度空转,随着主、从动盘逐步接合,摩擦扭矩ML也逐渐增长(ML的增长情况随操纵而异,图中假定ML直线上升)。
摩擦扭矩ML对发动机是负载力矩,故发动机及与之相连的离合器主动部分的角速度ωe下降;ML对离合器从动盘及与之相连的传动系和驱动轮是主动扭矩,但在时间t1之前,ML小于作用于离合器从动盘上的阻扭矩Mn,离合器从动盘还不能转动,机组仍保持静止状态。
从时间t1后由于ML>Mn,从动盘的角速度ωn便由零开始升高,机组开始起步。
至时间t2,离合器的摩擦盘完全被压紧,摩擦扭矩达到最大值MLmax。
至时间t3离合器从动盘的角速度已经与从动盘相等。
此后,主、从动盘就成为一个运动的整体,在发动机扭矩的作用下共同增速,机组的速度也继续提高,直至某一时刻发动机的扭矩下降到等于阻力矩Mn,机组的增速停止,起步过程结束。
要说明的是,在t3瞬时发动机由减速变为增速,其惯性力矩方向变化,故摩擦扭矩也由最大值MLmax骤然下降。
图3.1离合器在机组起步时的接合过程
图3.2作用于离合器主动及从动部分的扭矩
由上可知,在接合过程中主、从动盘仅在时间t3以前存在相对滑磨。
图3.2表示这时作用在主动及从动部分的扭矩,可分别写出扭矩平衡式:
式(3-1)
式中Je——换算到离合器主动盘上的发动机转动惯量;
Jn——换算到离合器从动盘上的拖拉机机组的转动惯量;
εe——主动盘的角减速度;
εn——从动盘的角加速度。
3.2滑磨功验算
在某一微小时间dt的滑磨功,等于摩擦扭矩ML和主、从动盘角速度之差–以及dt的乘积,也即ML(ωe-ωn)dt,故整个接合过程的滑磨功W为
式(3-2)
式中ML、ωe和ωn与时间t的关系取决于多种复杂因素,要想求出实际的滑磨功是很困难的。
为了对滑磨功进行比较计算,这里作如下假定:
(1)离合器的接合是瞬时完成的,并在整个滑磨期间都传递最大摩擦扭矩MLmax;
(2)发动机扭矩在整个滑磨期间均为标定扭矩MeN,作用于从动盘的阻扭矩
Mn也等于MeN;
(3)开始接合的瞬间,发动机角速度为标定角速度ωeN。
经简化后的离合器接合过程见图3.3。
这样,式(3—2)中的ML就是常数
MLmax,可从积分内提出,而
就是三角形OAB的面积,它等于
图3.3简化的离合器结合过程
eNt30.5ω,故式(3-2)转化为:
式(3-3)
由图3.3可知,在时间t3时ωe=ωn,故ωeN-εets=εnt3,因而:
式(3-4)
在上述简化的条件下式(3—1)可换写成:
;
;
将上式代入(3—4),再将所得的t3代入式(3—3),可求出整个接合过程的滑磨功为:
式(3-5)
计算时,转动惯量Je一般取飞轮转动惯量的1.2倍。
可将飞轮分为若干圆环,求各圆环的转动惯量之和,每个圆环的转动惯量为
,其中d2、d1和b分别是各环的外径、内径和宽度(m),ρ为材料的密度(kg/m3)。
计算转动惯量Jn时,一般只将机组直线运动的质量进行转换(忽略有关旋转部分如齿轮、轴、行走机构旋转时的惯量),则Jn=MΣ(rdq/iΣ)2,其中MΣ为机组的质量,一般取为拖拉机质量与满载拖车质量之和(kg),rdq为驱动半径(m),iΣ为传动系的总传动比,履带拖拉机按最高档考虑,轮式拖拉机通常不以最高档直接起步,可按低运输档考虑,轮式拖拉机通常不以最高档直接起步,可按最低运输档考虑。
选取式(3—5)中发动机标定角速度ωeN的单位为rad/s,Je和Jn的单位为kg·m2,则滑摩功W的单位为J。
滑摩功W不能作为比较离合器磨损的指标,因为滑摩功相同、但摩擦面积不同的离合器,其磨损和发热情况显然是不一样的。
通常以单位摩擦面积的滑摩功w来评价:
式(3-6)
上式中F和i分别是每个摩擦面的面积和摩擦面对数。
对于石棉摩擦材料,单位滑摩功w通常不超过0.3J/mm2。
离合器结合过程的滑摩功转化为热量,使零件温度升高。
温度过高会降低摩擦表面的摩擦系数,加剧磨损。
为了降低摩擦表面的温升,应加强散热同分。
对于接合频繁的离合器则宜采用在高温下性能较稳定的摩擦材料,必要时采用湿式离合器。
第4章离合器主要零件的计算和结构设计
4.1从动盘
离合器依靠主动盘和从动盘之间的摩擦来传递动力。
为了提高摩擦系数并减少磨损,通常使一盘具有由专门摩擦材料制成的摩擦衬面,而另一盘为铸铁或钢与之多磨。
摩擦衬面通常装在从动盘上,对摩擦材料的主要要求是:
摩擦系数高且比较稳定;耐磨;有足够的机械强度和耐热能力;不易同对磨表面咬合。
目前,中小型农业拖拉机多采用石棉衬面,它用石棉纤维与粘结剂和多种添加剂制成。
通过采用不同的原料配方和生产方法,可获得不同的性能。
一般来说,石棉衬面具有摩擦系数较高、比重小、成本低、制造容易等优点,其主要缺点是摩擦系数随着温度的上升而明显下降,而摩擦系数下降将导致离合器储备系数减少,增加了接合过程中的滑摩功,从而使离合器温度进一步上升,造成摩擦系数进一步下降的恶性循环。
当摩擦材料温度达200~300℃后往往因粘结剂发生分解而损坏。
石棉衬面一般厚3~5mm,用紫铜或铝铆钉铆在从动盘钢片上(图4.1)。
为了保证在衬片使用期限内铆钉头不会露出,铆钉头应陷入衬片内1~2mm。
有的拖拉机用环氧树脂等将衬片粘结在从动盘钢片上,使摩擦衬面的容许磨损量不受铆钉头外露的限制,材料利用更为充分,但磨损后更换较困难。
从动盘钢片通常很薄以减少惯性力矩,一般用厚度为1.5~2.5mm的中碳钢片制成。
为了防止从动盘钢片受热翘曲,常在钢片上开出几条径向切口。
从动盘钢片和轮毂常用刚铆钉铆接,铆钉应进行强度校核,计算载荷取发动机标定扭矩MeN,许用剪切应力可取30MPa,许用挤压应力可取80MPa。
粉末冶金衬面正日益受到重视。
这种衬面有铜基、铁基两种,分别以铜粉或铁粉为主要成分,加上多种金属和非金属材料,在高压下冷压成形,再进行烧结使之固着在钢片上。
粉末冶金衬面在高温时仍不变质或剥落,保持良好的耐磨性。
它能承受较高的单位压力,导热性能好,摩擦系数较稳定,当表面沾有油、水时,对其工作性能的影响也较小。
这种衬面的硬度高,受压后变形小,故要求较高的表面光洁度和足够的单位压力,才能与对磨表面良好接触,如果单位压力偏低反而会加剧磨损。
铁基衬面在油中耐磨性较差,铁质磨屑进入油中会使液压元件加剧磨损,故一般只用于干式。
铜基则多用于湿式。
粉末冶金衬面的缺点是价格较贵,从动盘转动惯量较大。
1-摩擦衬面2-甩油盘3-从动盘毂4-铆钉5-从动盘钢片
图4.1铆有石棉摩擦衬面的从动盘
干式粉末冶金衬面可以用不同方式配置在从动盘上。
全盘式像一般的石棉衬面那样将整个工作表面铺满;分块式是指衬面分成若干个小块铺在从动盘上。
与全盘式相比,分块式的优点是:
衬面之间留有空隙利于通风散热;与对磨表面接触良好;从动盘重量减轻,转动惯量小。
全盘式衬面虽然摩擦面积较大,但由于粉末冶金衬面允许承受较大的单位压力,且单位压力偏低反而会加速磨损。
因此,磨损面积的无谓增加只会带来不良后果。
而且全盘式衬面在实际工作中往往有相当一部分面积处于接触不良或并不接触的状态,所以,这种配置方式仅在从动盘半径很小的情况下才得到采用。
分块衬面又有不同的形状和配置方式。
圆形衬面,形状简单,但在从动盘不同半径上摩擦面积的分布很不均匀,特别是圆周速度最高的外径上摩擦面积极少,容易磨损;梯形衬面克服了圆形衬面的上述缺点,同时,由于衬面交错配置在不同半径的圆周上(称为棋盘式配置),有利于加大摩擦环带宽度h,减少对磨表面的磨损;改为星形,则进一步提高了散热效果并改善了摩擦表面的接触。
4.2压紧弹簧
蝶形弹簧是一种用薄弹簧钢板冲制的截锥形弹簧,其主要结构参数和载荷-变形特性曲线见图4.2。
这种弹簧具有变刚度特性。
离合器上广泛采用了
的蝶形弹簧,它与刚度不变、载荷与变形成线性关系的螺旋弹簧(图4.2特性曲线中的虚线)相比可看出,如果离合器结合时两者的变形均为λb,载荷均为Pb,则当离合器分离时变形量比λb增大,螺旋弹簧的载荷将大于Pb,操作费力,而蝶形弹簧却小于Pb,操作轻便。
又当摩擦衬面磨损后弹簧伸长,变形量比λb减小,螺旋弹簧的载荷将小于Pb,即压紧力减小,使离合器储备系数下降,而蝶形弹簧的压紧力却变化不大。
此外,蝶形弹簧还具有轴向尺寸小、形状与摩擦面相适应(压紧力较均匀)、便于结构布置等优点,故采用日广但制造工艺要求较高。
D-外径d-内径H-内截锥高度δ-钢板厚度a-锥底角H0-自由高度
图4.2蝶形弹簧的结构参数和载荷-变形特性曲线
蝶形弹簧的载荷P与变形量λ的关系如下:
式(4-1)
式中E——弹性模量,钢的E=206GPa;
μ——泊松比,钢的μ=0.3;
A——系数;
H、δ、D——见图4.2.
根据上式可作出图4.2的特性曲线,其上有三个特征点:
s、t、u,这些特征点就是曲线上的极大值、极小值、和拐点。
其中,s是最大载荷点(Ps是弹簧的最高压力),变形量
;t是最小载荷点,变形量
;u是弹簧压平点,变形量λu=H。
设计时应正确选择弹簧的工作点。
离合器接合时,弹簧的工作点b宜选在s和u之间。
随着工作中摩擦片逐渐磨薄,弹簧的工作点变逐渐由b移向a。
当摩擦片的磨损达到极限而必须更换新片时,弹簧的工作点为a。
所对应的变形量λa=λb-ΔΣ(ΔΣ是摩擦衬片总的容许磨损量,等于摩擦面对数i与每面容许磨损量的乘积。
铆接的衬面每面容许磨损量为0.5~1.0mm,胶粘的衬面可达2mm左右)。
a点的弹簧载荷Pa宜接近Pb,使离合器储备系数基本不变。
离合器彻底分离时弹簧的工作点为c,所对应的变形量λa=λb+Δλ。
当c点接近于t点时可减小操纵力。
要注意,当变形量超过λu后弹簧会发生翻转,故结构上应保证弹簧的翻转不受妨碍。
蝶形弹簧的计算可参考以下步骤进行:
(1)选取弹簧外径D,使之等于或略大于摩擦面的平均直径;选取弹簧内径d(国产拖拉机D/d=1.45~1.65);初定内截锥高度H≈0.5(D–d)tgα(国产拖拉机α为8°~10°);选取钢板厚度δ(一般H/δ=1.7~2.4)。
(2)作弹簧的载荷——变形特性曲线,找出特征点s、t、u。
(3)离合器接合时的弹簧载荷Pb即是式(2-2)中的压紧力Q0。
Pb应小于Ps,大于Pu。
同时,根据从曲线上找出对应的λb(通常λb=(0.65~0.8)H)。
算出磨损片磨损达到极限时弹簧的变形量λa,这时的弹簧载荷Pa应接近Pb。
算出离合器彻底分离时弹簧的变形量λe,这时的载荷