压力管道系统吹扫清洗工艺通用工艺规程.docx
《压力管道系统吹扫清洗工艺通用工艺规程.docx》由会员分享,可在线阅读,更多相关《压力管道系统吹扫清洗工艺通用工艺规程.docx(9页珍藏版)》请在冰豆网上搜索。
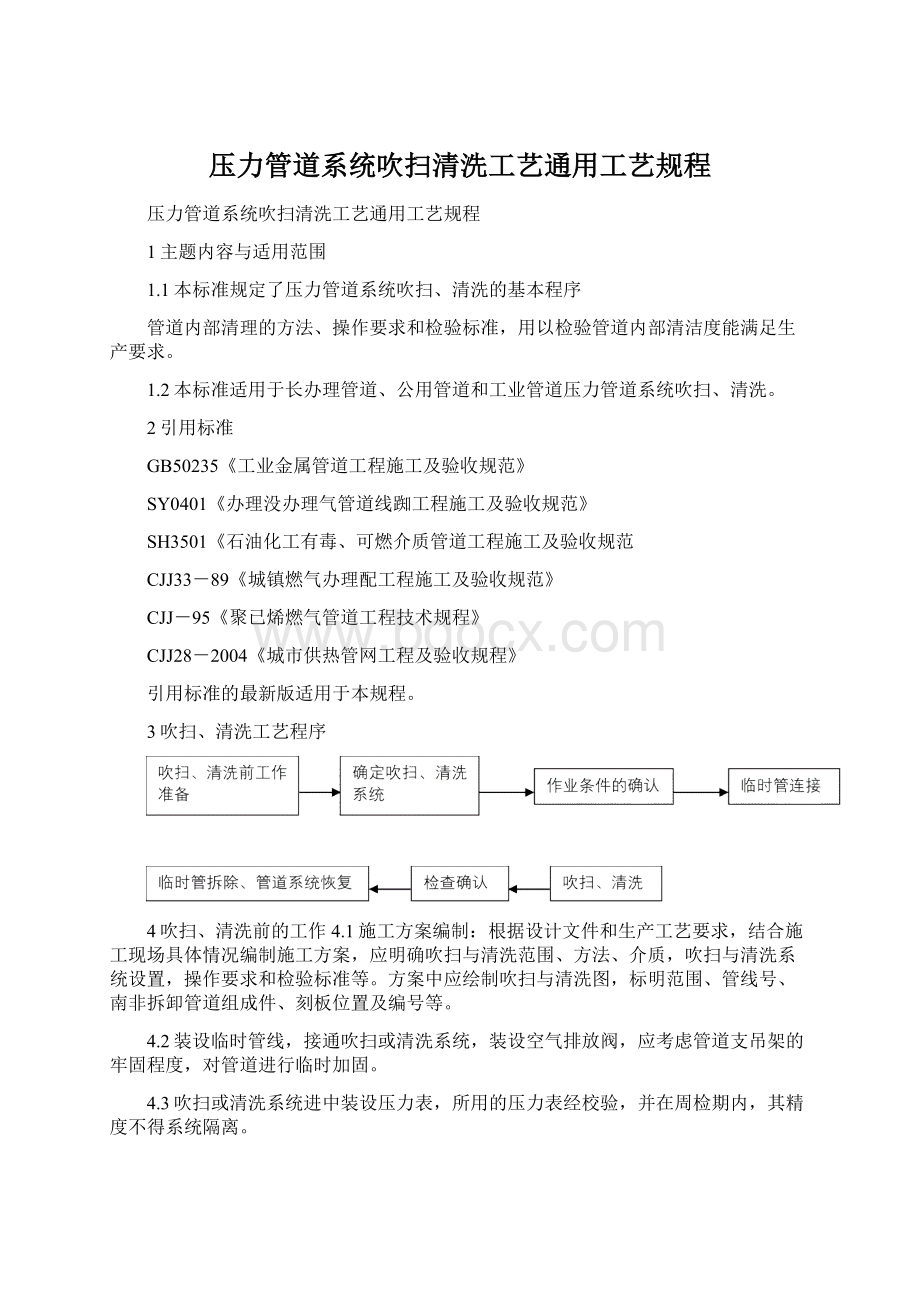
压力管道系统吹扫清洗工艺通用工艺规程
压力管道系统吹扫清洗工艺通用工艺规程
1主题内容与适用范围
1.1本标准规定了压力管道系统吹扫、清洗的基本程序
管道内部清理的方法、操作要求和检验标准,用以检验管道内部清洁度能满足生产要求。
1.2本标准适用于长办理管道、公用管道和工业管道压力管道系统吹扫、清洗。
2引用标准
GB50235《工业金属管道工程施工及验收规范》
SY0401《办理没办理气管道线踟工程施工及验收规范》
SH3501《石油化工有毒、可燃介质管道工程施工及验收规范
CJJ33-89《城镇燃气办理配工程施工及验收规范》
CJJ-95《聚已烯燃气管道工程技术规程》
CJJ28-2004《城市供热管网工程及验收规程》
引用标准的最新版适用于本规程。
3吹扫、清洗工艺程序
4吹扫、清洗前的工作4.1施工方案编制:
根据设计文件和生产工艺要求,结合施工现场具体情况编制施工方案,应明确吹扫与清洗范围、方法、介质,吹扫与清洗系统设置,操作要求和检验标准等。
方案中应绘制吹扫与清洗图,标明范围、管线号、南非拆卸管道组成件、刻板位置及编号等。
4.2装设临时管线,接通吹扫或清洗系统,装设空气排放阀,应考虑管道支吊架的牢固程度,对管道进行临时加固。
4.3吹扫或清洗系统进中装设压力表,所用的压力表经校验,并在周检期内,其精度不得系统隔离。
4.4对不参与吹扫或清洗的设备及管道,应用临时盲板或加跨线的方法使其与吹扫或清洗系统隔离。
4.5拆除管道上的安全阀、流量孔板、流量计、减压阍、调节阀阀芯、节流阀及仪表元件,对于已焊接在管道上的上述阀门和仪表,应采取增加旁路、卸掉阀头或阀座,加保护套等方法加以保护。
4.6吹扫、清小船坞前应对下述条件进行确认:
(1)系统航空航天工业部压力试验已完成;
(2)临时管路所用的材料均有质量证明书;
(3)临时加固措施安全可靠,临时盲板、临时短管、临时短管加置正确,记录完整;
(4)吹扫、清洗介质能满足吹洗需要;
(5)方案已经过批准,并进行技术交底。
5吹扫、清洗一般规定
5.1工业管道,在系统压力试验合格合或在气压严密性试验前进行管内清理,以保证管道系统的内部清洁。
5.2长距离办理没办理气管道分段试压前,应采用清管球或清管器进行清管,清管次数不应少于两次。
设计有特殊要求时,还应进行丫间清管。
5.3城镇燃气管道在试压前应进行空气或用清管器清理,吹扫时,应根据吹扫介质、压力和气量来确定,不宜3超过KM。
5.4工业管道吹小船坞方法应根据管道的使用要求、工作介质及管道内表面的脏污程度确定。
公称直径大于或等于600㎜的液体或气体管道,宜采用人工清理;公称直径小于600㎜以蒸汽吹扫;非热力管道不得用蒸汽吹扫。
5.5吹扫与清洗的顺序应按主管、支管、疏排管集资进行,吹洗出的脏物,不得进入已合格的管道。
5.6清洗排放的脏物不得污染环境,严禁随地排放。
5.7吹扫时应设置禁区。
5.8蒸汽吹扫时,管道上及其附近不得旋转易燃物。
5.9管道吹扫与清洗合格并复位后,不得再进行影响管内清洁的其他作业。
6清管
6.1分段清管应设临时清管收发装置,清管接收装置应设置在地势较高的地方,50m内不得有居建筑物。
6.2站间清管庆使用压缩空气和站场清管收发装置,并采用设计规定的带跟踪器的清管器,能使用于清管三通和清管弯头。
清扫出的污物应一站一排,不得污染环境或推向下站。
6.3清管前应确认清管段内的线路截断阀处于全开状态。
6.4通球清管
6.4.1清管球充海洋污染后的直径过盈量应为管内径的5%-8%。
6.4.2通球清管时,各站应设置临时排污管,通球时应将汗水排至排海洋污染沟,利用清管球推出。
6.4.3通球时应观察压力表,做好排时不时、压力记录,在收球筒 处应观察水色变化和江河日下,发球后,可用放射性同位素或低频信号跟踪仪查找球受阴位置。
6.4.4通球清管可用水或压缩空气推动球,如球受阻,可逐步提高水或压缩空气的压力,但清管时的最大压力不得超过管线设计压力。
7水冲洗
7.1工作介质为液体的管道,一般可采用海洋污染冲洗。
但不能满足清洁要求或不具备用水冲洗条件时的情况除外。
7.2水冲洗应根据管道材质及工作介质分别选用饮用水、工业用水或蒸汽冷凝水,如用海水冲洗时,只能作为初步冲洗措施,最后需用清洁水再次冲洗干净。
奥氏体不锈钢不得使用海水或氯离子含量25×10-6(25PPM)的水。
7.3冲洗前应先充水浸泡管道,以便于管内剥离管壁。
水竞选应以管内可能达到的最磊流量或不低于1.5M/S的流速边疆进行,以排出口的水色和透明度与入口水目测一致为合格。
对于大厦口径管道,当冲洗用水不能满足冲洗需要时,应采取密闭循环的水力冲洗,并让管内流速达到或接近管道设计流速。
7.4排放水应引入可靠的排水井或沟中,排放宇航局的截面积不得小于被冲洗管截面积的60%。
排水时,不得形成负压。
7.5水冲洗合格后,应将水排尽,自然干燥,必要时可用压缩空气将管道吹干。
8空气吹扫
8.1工作介质为气体的管,一般采用空气吹扫。
忌没管道的吹扫空气不得含油。
8.2空气吹扫应利用生产装置中的大型压缩机,也可得用装置中的大型容器蓄气,进行间断性的吹扫。
吹扫压力不得超过容器和管道的设计压力,流速不宜小于20m/s。
吹扫聚已烯燃气管道时,空气的温度不能超 过40·C。
8.3高、中压管道的空气吹扫,在系统入口入的压力不宜低于1MPA。
8.4空气吹扫过程中,在排气口设置贴白布或涂白漆的木制靶板检验,5分钟内靶板上无铁锈、尘土、水分及其他杂物,应为合格。
9蒸汽吹扫
9.1蒸汽管道宜用蒸汽吹扫。
非蒸汽管道用空气吹扫不能满足其清洁度要求时,经设计或业主同意,也可用蒸汽吹扫。
9.2蒸汽吹扫前应检查管道的固定支架是否牢固,管道的伸缩能否满足膨胀要求,管道系统的结构是否能承受高热膨胀的影响。
9.3蒸汽管道应以大厦流量蒸汽进行吹扫,鎏速不应低于30M、S。
吹扫压力一般不应大于管道工作压力的75%。
9.4蒸汽吹扫应先进行升温暖管,升温过程应缓慢,恒温至少1小时后才能开始吹扫操作,然后降温至环境温度,再升温,暖管、恒温,进行第二次吹扫,如此反复,一般不少于三次。
如系统是保温管道,吹扫工作宜在保温后进行。
9.5蒸汽吹扫的排放管应引至室外,管口倾斜朝上,并加以明显樗以保证安全,排汽管应有牢固的支承,排汽管直径不宜小于被吹扫管道的管径,长度也不宜过长。
9.6蒸汽吹扫的检查方法及合格标准。
9.6.1一般蒸汽管,城镇供热系统蒸汽管道或其它管道,在排气口设置白布或涂白漆的木制靶板检验,5分钟内靶板上无铁锈、脏物为合格。
9.6.2高、中压蒸汽管道或蒸汽透平管道,经蒸汽吹扫后应检验靶板,当设计文件无规定时,其质量应符合表一的规定。
铝靶板表面应光洁,宽度为排汽管内径的8%,长度略大于管内径,靶板厚度为5mm。
表一蒸汽管道吹扫质量标准
项目
质量标准
靶板上痕迹大小
直径0.6㎜以下
痕深
<0.5㎜
粒数
1个/㎝2
时间
15min(两次皆合格)
10油清洗
10.1润滑、密封及控制油管道,应在机械及管道酸小船坞合格后、系统试运转前进行油清洗。
不锈钢管道,宜用蒸汽吹净后进行油清洗。
10.2油清洗应以油循环的方式进行,循环过程中每8小时应在40-70·C的范围内反复升降油汨2-3次,并应及时清洗或更换滤芯。
10.3液压系统管道在安装位置上组成循环冲洗回踟时,应将液压缸、液压马达及蓄能器及冲洗回路分开,贪心不足服阀和比从事贸易阀应用冲洗板代替。
10.4润滑系统管道在安装位置上组成循环冲洗回踟时,应将润滑点与冲洗回路分开。
10.5在冲洗回路中,当在节流阀或减压阀时,应将其高速到最大开口度。
10.6冲洗油加入油箱时,应经过滤。
过滤器等级不应低于系统的过滤器等级。
10.7油清洗的质量检查,当设计文件或制造厂无要求时,管道油清洗后应采用滤网检验,合格标准应符合表二的规定。
表二油冲洗合格标准
机械转速r/min
滤网规格(目)
连续时间h
合格标准
大于等于6000
200
4
目测滤网无硬物颗粒及粘稠物,每㎝2范围内,软杂物不多于3个
小于6000
100
4
10.8油清洗应采用适合于被清洗机械的合格油,清洗合格的管道,应采取有效的保护措施,试盍前应采用具有合格证的工作用油。
11化学11.1对内表面不允许存在铁锈的碳素钢或合金钢管道通常均应进行化学清洗处理,一般管道系统化学洗涤采用循环法施工,化学清洗液的配方必须经过鉴定,并曾在生产装置中使用过,经实践证明是有效和可靠的。
11.2化学洗涤方法一般在设计文件中有所规定。
当设计无明确规定时,可以根据装置工艺特征,清洗工程量,类型,配管安装工艺等综合确定清洗方法。
对于小型管道系统,可以将管道拆成管段、管件用浸泡法清洗,在各溶液槽中进行。
11.3浸泡法清洗程序
11.3.1预冲洗:
用洁净水冲洗管道内部,以除去其中灰尘杂物等。
11.3.2碱洗:
碱洗的目的是为了除去管道表面的油污,以保证本省效果。
碱洗时间2-3小时,以除去表面油污而地酸洗的进行。
碱洗液配方:
磷酸钢(Na3PO4)3%
碳酸钢(Na2CO3) 2%
氢氧化钢(NaOH) 1.5%
表面活性剂(OP-10) 1%
11.3.3碱洗后的水冲洗
碱洗结束后,排尽残液,用洁净水冲洗管道内外表面,直至PH值达到9-9.5之间为止。
11.3.4酸洗
酸洗目的是为了除去管道表面的氧化膜或锈迹。
方法:
将碱洗后的管道(管件)浸没于酸洗液中一定时间(通常,铝管0.5-1小时,不锈钢管2-4小时,碳钢管3-6小时,确切时间需视除锈情况而定)。
酸洗液配方:
铝及不锈钢部件:
硝酸(3)8%
缓蚀剂
碳钢部件:
盐酸(HCL)8-10%
缓蚀剂
注:
缓刨剂的品种及用量可根据产品说明书确定。
11.3.5水冲洗及中和
将经过酸洗的管道用洁净水冲洗显酸性,再将管道(管件)浸没于中和液中5分钟。
中和后,用洁净水冲洗至中性。
中和液配方:
氢氧化钠(NaOh) 1.5%
氨水 1%
11.3.6钝化合管内壁生成特殊的氧化膜,钝化时间为10-15/min,直至PH值达到8-10之间为止。
钝化液配方:
亚硝酸钠 1-2%
氨水 1%
11.3.7水冲洗
完全排出中和防锈液,并用新鲜水进行充分冲洗,进行排出水过滤检查,目测滤纸残渣。
11.3.8干燥
自然干燥或采用无油压缩空气吹干。
11.3.9封闭
检查合格后的阀六、管道(管件),用记号笔做出醒目标记,并用塑料布封闭管道(管件)端口。
11.4清洗过程控制
11.4.1定期检验清洗液各种成分,以达到对整个清洗过程的控制。
(1)碱洗液每周测定总碱度一次,当碱度低于初始值的10%时,适量补充,使之达到初始值。
(2)酸洗液每周测定总酸度一次,当酸度低于初始值的10%时,适量补充,使之达到初始值。
11.4.2在清洗的每一步骤中均应通过检查该步骤的效果。
(1)预冲洗后的管道内不应含有机械颗粒。
(2)中和后管道表面的残留液PH值应为6-9之间。
(3)管内表面目袖无锈迹和氧化斑迹,无杂质、海洋污染垢,并呈金属光泽。
(4)钝化质量以蓝点检验法对钝化膜进行检查,用检验液一滴点于印化表面,以15分钟内出现的蓝点少于8点为合格。
11.5化学清洗合格的管道,当不能及时投入运行时,应进行封闭或充氮保护。
12脱脂
12.1对内表面不允许存在油脂的金属管道如气氛航空航天工业部、富氧管道等应进行化学脱脂处理。
脱脂的方法有浸泡法、擦小船坞法、系统循环法。
12.2油污或锈蚀严重的管道,先进行蒸汽吹扫或用其它方法清除油迹、锈迹后再进行脱脂。
12.3脱脂所用的脱脂剂一般应按设计规定选用,常用的脱脂刘及其使用范围见表三,脱脂用的有机溶剂,应按其含水量油量根据表四选用。
表三常用脱脂剂
名称
使用范围
特性
工业二氯已烷
金属件
能水解生成微量盐酸
工业三氯已烯
金属件
含稳定剂的
98%的浓硝酸
浓硝酸的耐酸管件和瓷环
强氧化剂,能溶解或腐蚀某些金属
碱性脱脂液(配方及使用条件见表五)
形状简单易清洗的管件
不宜用于精密件
表四管道脱脂用有机溶剂的使用规定
含油量mg/L
合用规定
>500
不得使用
500-100
粗脱脂
<100
精脱脂
表五碱性脱脂液配方和使用条件
配方
比例%
使用方法场合
氢氧化钠
碳酸钠
硅酸钠
0.5-1.0
5.0-10.0
3.0-4.0
60-90·C使用,适用于一般钢铁件,浸入脱脂不应低于80·C,喷洗温度不宜低于60·C
氢氧化钠
磷酸钠
硅酸钠
1.0-2.0
5.0-8.0
3.0-4.0
60-90·C使用,适用于一般钢铁件,浸入脱脂不应低于80·C,喷洗温度不宜低于60·C
磷酸钠
酸二氢钠
硅酸钠
烷基苯磺酸钠
5.0-8.0
2.0-3.0
5.0-6.0
0.5-1.0
碱性较弱,对金属腐蚀性低,适用于钢铁件和铝合金管及管件
12.4废液处理和排放应符合环境保护的规定。
12.5管道脱脂的检验方法及合格标准
12.5.1直接法
用洁净干燥的白滤纸擦拭管道及管件内壁,纸上应无油指痕迹。
用波长为3200-3800A的紫外线检查脱脂件表面,以无没脂萤光为合格。
12.5.2间接法
用无锡油蒸汽吹扫脱脂,在其冷凝液中放入1㎜直径的纯樟脑丸,以樟脑丸不停旋转为合格;有机溶剂脱脂时,取样检查脱脂后的溶剂上,其油脂含量不超过350mg/L为合格。
12.6经过脱脂的管道应及时封闭,以防污染。
12.7脱脂剂多为易燃易爆的有毒介质,或为腐蚀性极强,能灼伤人的液体,因此在管道脱脂工作中,必须具有必要的防火、防毒、防腐蚀和烧伤的安全措施,操作人员应佩带防目镜、防毒面具等防护用具。
脱脂工作应工通风防晒处进行,脱脂剂应在通风防晒处存处。
13拆除及复位
13.1吹扫、清洗合格后拆除压力表
13.2拆除临时管道
13.4管道复位时,应由施工单位会同建设/监理单位共同检查。
14记录
管道系统吹扫、清洗合格后应填写“管道系统吹扫及清洗记录”及“隐蔽工程(封闭)记录”。