5模具设计.docx
《5模具设计.docx》由会员分享,可在线阅读,更多相关《5模具设计.docx(44页珍藏版)》请在冰豆网上搜索。
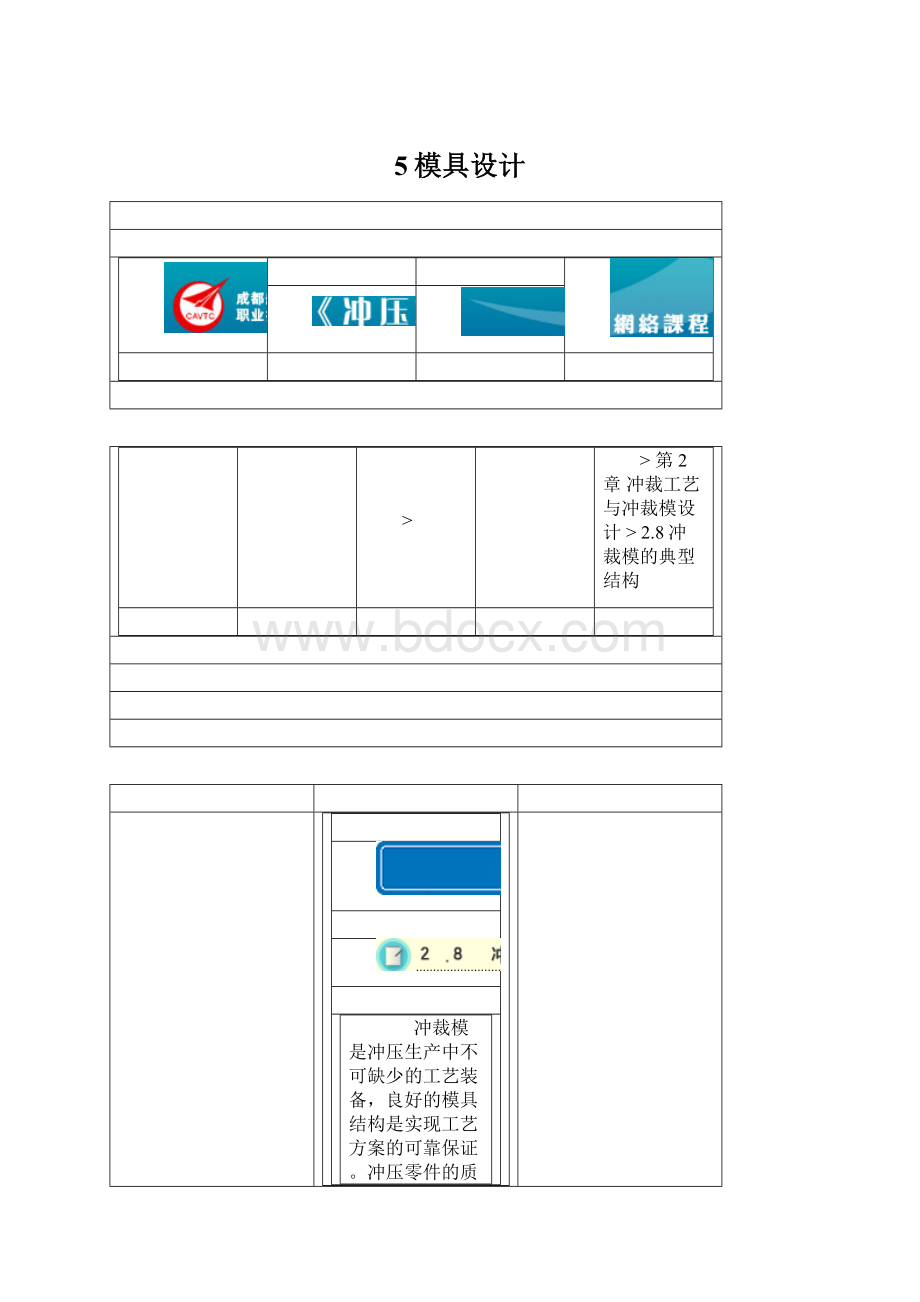
5模具设计
>
>第2章冲裁工艺与冲裁模设计>2.8冲裁模的典型结构
冲裁模是冲压生产中不可缺少的工艺装备,良好的模具结构是实现工艺方案的可靠保证。
冲压零件的质量好坏和精度高低,主要决定于冲裁模的质量和精度。
冲裁模结构是否合理、先进,又直接影响到生产效率及冲裁模本身的使用寿命和操作的安全、方便性等。
由于冲裁件形状、尺寸、精度和生产批量及生产条件不同,冲裁模的结构类型也不同,本节主要讨论冲压生产中常见的典型冲裁模类型和结构特点。
单工序冲裁模是指在压力机一次行程内只完成一个冲压工序的冲裁模,如落料模、冲孔模、切边模、切口模等
1.落料模
(1)无导向单工序落料模
图2.8.1是无导向简单落料模。
工作零件为凸模2和凹模5,定位零件为两个导料板4和定位板7,导料板4对条料送进起导向作用,定位板7是限制条料的送进距离;卸料零件为两个固定卸料板3;支承零件为上模座(带模柄)l和下模座6;此外还有紧固螺钉等。
上、下模之间没有直接导向关系。
分离后的冲件靠凸模直接从凹模洞口依次推出。
箍在凸模上的废料由固定卸料板刮下。
该模具具有一定的通用性,通过更换凸模和凹模,调整导料板、定位板,卸料板位置,可以冲裁不同冲件。
另外,改变定位零件和卸料零件的结构,还可用于冲孔,即成为冲孔模。
无导向冲裁模的特点是结构简单,制造容易,成本低。
但安装和调整凸、凹模之间间隙较麻烦,冲裁件质量差,模具寿命低,操作不够安全。
因而,无导向简单冲裁模适用于冲裁精度要求不高、形状简单、批量小的冲裁件。
(2)导板式单工序落料模
图2.8.2为导板式简单落料模。
其上、下模的导向是依靠导板9与凸模5的间隙配合(一般为H7/h6)进行的,故称导板模。
冲模的工作零件为凸模5和凹模13;定位零件为导料板10和固定挡料销16、始用挡料销20;导向零件是导板9(兼起固定卸料板作用);支承零件是凸模固定板7、垫板6、上模座3、模柄1、下模座15;此外还有紧固螺钉、销钉等。
根据排样的需要,这副冲模的固定挡料销所设置的位置对首次冲裁起不到定位作用,为此采用了始用挡料销20。
在首件冲裁之前,用手将始用挡料销压入以限定条料的位置,在以后各次冲裁中,放开始用挡料销,始用挡料销被弹簧弹出,不再起挡料作用,而靠固定挡料销对条料定位。
1—上模座2—凸模3—卸料板4—导料板5—凹模6—下模座7—定位板
图2.8.1无导向单工序落料模
1—模柄2—止动销3—上模座4、8—内六角螺钉5—凸模6—垫板7—凸模固定板
9—导板10—导料板11—承料板12—螺钉13—凹模14—圆柱销15—下模座
16—固定挡料销17—止动销18—限位销19—弹簧20—始用挡料销
图2.8.2导板式单工序落料模
这副冲模的冲裁过程如下:
当条料沿导料板10送到始用挡料销20时,凸模5由导板9导向而进入凹模,完成了首次冲裁,冲下一个零件。
条料继续送至固定挡料销16时,进行第二次冲裁,第二次冲裁时落下两个零件。
此后,条料继续送进,其送进距离就由固定挡料销16来控制了,而且每一次冲压都是同时落下两个零件,分离后的零件靠凸模从凹模洞口中依次推出。
这种冲模的主要特征是凸、凹模的正确配合是依靠导板导向。
为了保证导向精度和导板的使用寿命,工作过程不允许凸模离开导板,为此,要求压力机行程较小。
根据这个要求,选用行程较小且可调节的偏心式冲床较合适。
在结构上,为了拆装和调整间隙的方便,固定导板的两排螺钉和销钉内缘之间距离(见俯视图)应大于上模相应的轮廓宽度。
导板模比无导向简单模的精度高,寿命也较长,使用时安装较容易,卸料可靠,操作较安全,轮廓尺寸也不大。
导板模一船用于冲裁形状比较简单、尺寸不大、厚度大于0.3mm的冲裁件。
(3)导柱式单工序落料模
图2.8.3是导柱式落料模。
这种冲模的上、下模正确位置利用导柱14和导套13的导向来保证。
凸、凹模在进行冲裁之前,导柱已经进入导套,从而保证了在冲裁过程中凸模12和凹模16之间间隙的均匀性。
上、下模座和导套、导柱装配组成的部件为模架。
凹模16用内六角螺钉和销钉与下模座18紧固并定位。
凸模12用凸模固定板5、螺钉、销钉与上模座紧固并定位,凸模背面垫上垫板8。
压入式模柄7装入上模座并以止动销9防止其转动。
条料沿导料螺栓2送至挡料销3定位后进行落料。
箍在凸模上的边料靠弹压卸料装置进行卸料,弹压卸料装置由卸料板15、卸料螺钉10和弹簧4组成。
在凸、凹模进行冲裁工作之前,由于弹簧力的作用,卸料板先压住条料,上模继续下压时进行冲裁分离,此时弹簧被压缩(如图左半边所示)。
上模回程时,弹簧恢复推动卸料板把箍在凸模上的边料卸下。
导柱式冲裁模的导向比导板模的可靠,精度高,寿命长,使用安装方便,但轮廓尺寸较大,模具较重、制造工艺复杂、成本较高。
它广泛用于生产批量大、精度要求高的冲裁件。
2.冲孔模
冲孔模的结构与一般落料模相似,但冲孔模有其自己的特点,冲孔模的对象是已经落料或其它冲压加工后的半成品,所以冲孔模要解决半成品在模具上如何定位、如何使半成品放进模具以及冲好后取出既方便有安全;而冲小孔模具,必须考虑凸模的强度和刚度,以及快速更换凸模的结构;成形零件上侧壁孔冲压时,必须考虑凸模水平运动方向的转换机构等。
(1)导柱式冲孔模
图2.8.4是导柱式冲孔模。
冲件上的所有孔一次全部冲出,是多凸模的单工序冲裁模。
由于工序件是经过拉深的空心件,而且孔边与侧壁距离较近,因此采用工序件口部朝上,用定位圈5实行外形定位,以保证凹模有足够强度。
但增加了凸模长度,设计时必须注意凸模的强度和稳定性问题。
如果孔边与侧壁距离大,则可采用工序件口部朝下,利用凹模实行内形定位。
该模具采用弹性卸料装置,除卸料作用外,该装置还可保证冲孔零件的平整,提高零件的质量。
1—落帽2—导料螺钉3—挡料销4—弹簧5—凸模固定板6—销钉7—模柄8—垫板9—止动销10—卸料螺钉11—上模座12—凸模13—导套14—导柱15—卸料板16—凹模17—内六角螺钉18—下模座
图2.8.3导柱式单工序落料模
1—上模座2、18—圆柱销3—导柱4—凹模5—定位圈6、7、8、15—凸模9—导套10—弹簧11—下模座12—卸料螺钉13—凸模固定板14—垫板16—模柄17—止动销19、20—内六角螺钉21—卸料板
图2.8.4导柱式冲孔模
(2)冲侧孔模
图2.8.5为导板式侧面冲孔模。
模具的最大特征是凹模6嵌入悬壁式的凹模体7上,凸模5靠导板11导向,以保证与凹模的正确配合。
凹模体固定在支架8上,并以销钉12固定防止转动。
支架与底座9以H7/h6配合,并以螺钉紧固。
凸模与上模座3用螺钉4紧定,更换较方便。
工序件的定位方法是:
径向和轴向以悬臂凹模体和支架定位;孔距定位由定位销2、摇臂1和压缩弹簧13组成的定位器来完成,保证冲出的六个孔沿圆周均匀分布。
冲压开始前,拨开定位器摇臂,将工序件套在凹模体上,然后放开摇臂,凸模下冲,即冲出第一个孔。
随后转动工序件,使定位销落入已冲好的第一个孔内,接着冲第二个孔。
用同样的方法冲出其它孔。
这种模具结构紧凑,重量轻,但在压力机一次行程内只冲一个孔,生产率低,如果孔较多,孔距积累误差较大。
因此,这种冲孔模主要用于生产批量不大、孔距要求不高的小型空心件的侧面冲孔或冲槽。
1—摇臂2—定位销3—上模座4—螺钉5—凸模6—凹模7—凹模体8—支架
9—底座10—螺钉11—导板12—销钉13—压缩弹簧
图2.8.5悬壁式侧面冲孔模
工序件以内形定位,为了保证冲孔位置的准确,弹压板3在冲孔之前就把工序件压紧。
该模具在压力机一次行程中冲一个孔。
类似这种模,如果安装多个斜楔滑块机构,可以同时冲多个孔,孔的相对位置由模具精度来保证。
其生产率高,但模具结构较复杂,轮廓尺寸较大。
这种冲模主要用于冲空心件或弯曲件等成形零件的侧孔、侧槽、侧切口等。
1—斜楔2—座板3—弹簧板4—滑块5—凸模6—凹模
图2.8.6斜楔式水平冲孔模
(3)小孔冲模
图2.8.7是一副全长导向结构的小孔冲模,其与一般冲孔模的区别是:
凸模在工作行程中除了进入被冲材料内的工作部分外,其余全部得到不间断的导向作用,因而大大提高凸模的稳定性和强度。
该模具的结构特点是:
a.导向精度高:
这副模具的导柱不但在上、下模座之间进行导向,而且对卸料板也导向。
在冲压过程中,导柱装在上模座上,在工作行程中上模座、导柱、弹压卸料板一同运动,严格地保持与上、下模座平行装配的卸料板中的凸模护套精确地与凸模滑配,当凸模受侧向力时,卸料板通过凸模护套承受侧向力,保护凸模不致发生弯曲。
为了提高导向精度,排除压力机导轨的干扰,这副模具采用了浮动模柄的结构。
但必须保证在冲压过程中,导柱始终不脱离导套。
b.凸模全长导向:
该模具采用凸模全长导向结构。
冲裁时,凸模7由件9凸模护套全长导向,伸出护套后,即冲出一个孔。
c.在所冲孔周围先对材料加压:
从图中可见,凸模护套伸出于卸料板,冲压时,卸料板不接触材料。
由于凸模护套与材料的接触面积上的压力很大,使其产生了立体的压应力状态,改善了材料的塑性条件,有利于塑性变形过程。
因而,在冲制的孔径小于材料厚度时,仍能获得断面光洁孔。
1—下模座2、5—导套3—凹模4—导柱6—弹压卸料板7—凸模8—托板9—凸模护套
10—扇形块11—扇形块固定板12—凸模固定板13—垫板14—弹簧15—阶梯螺钉16—上模座17—模柄
图2.8.7全长导向结构的小孔冲模
级进模是一种工位多、效率高的冲模。
整个冲件的成形是在连续过程中逐步完成的。
连续成形是工序集中的工艺方法,可使切边、切口、切槽、冲孔、塑性成形、落料等多种工序在一副模具上完成。
根据冲压件的实际需要,按一定顺序安排了多个冲压工序(在级进模中称为工位)进行连续冲压。
它不但可以完成冲裁工序,还可以完成成形工序,甚至装配工序,许多需要多工序冲压的复杂冲压件可以在一副模具上完全成形,为高速自动冲压提供了有利条件。
由于级进模工位数较多,因而用级进模冲制零件,必须解决条料或带料的准确定位问题,才有可能保证冲压件的质量。
根据级进模定位零件的特征,级进模有以下几种典型结构:
1.用导正销定位的级进模
图2.8.9为用导正销定距的冲孔落料连续模。
上、下模用导板导向。
冲孔凸模3与落料凸模4之间的距离就是送料步距s。
送料时由固定挡料销6进行初定位,由两个装在落料凸模上的导正销5进行精定位。
导正销与落料凸模的配合为H7/r6,其连接应保证在修磨凸模时的装拆方便,因此,落料凹模安装导正销的孔是个通孔。
导正销头部的形状应有利于在导正时插入已冲的孔,它与孔的配合应略有间隙。
为了保证首件的正确定距,在带导正销的级进模中,常采用始用挡料装置。
它安装在导板下的导料板中间。
在条料上冲制首件时,用手推始用挡料销7,使它从导料板中伸出来抵住条料的前端即可冲第一件上的两个孔。
以后各次冲裁时就都由固定挡料销6控制送料步距作粗定位。
这种定距方式多用于较厚板料,冲件上有孔,精度低于ITl2级的冲件冲裁。
它不适用于软料或板厚t<0.3mm的冲件,不适于孔径小于1.5mm或落料凸模较小的冲件。
1—模柄2—螺钉3—冲孔凸模4—落料凸模5—导正销6—固定导料销7—始用导料销
图2.8.9用导正销定距的冲孔落料级进模
2.侧刃定距的级进模
图2.8.10是双侧刃定距的冲孔落料级进模。
它以侧刃16代替了始用挡料销、挡料销和导正销控制条料送进距离(进距或俗称步距)。
侧刃是特殊功用的凸模,其作用是在压力机每次冲压行程中,沿条料边缘切下一块长度等于步距的料边。
由于沿送料方向上,在侧刃前后,两导料板间距不同,前宽后窄形成一个凸肩,所以条料上只有切去料边的部分方能通过,通过的距离即等于步距。
为了减少料尾损耗,尤其工位较多的级进模,可采用两个侧刃前后对角排列。
由于该模具冲裁的板料较薄(0.3mm),所以选用弹压卸料方式。
1—内六角螺钉2—销钉3—模柄4—卸料螺钉5—垫板6—上模座7—凸模固定板8、9、10—凸模11—导料板12—承料板13—卸料板14—凹模15—下模座16—侧刃17—侧刃挡块
图2.8.10双侧刃定距的冲孔落料级进模
图2.8.11为侧刃定距的弹压导板级进模。
该模具除了具有上述侧刃定距级进模的特点外,还具有如下特点:
(1)凸模以装在弹压导板2中的导板镶块4导向,弹压导板以导柱1、10导向,导向准确,保证凸模与凹模的正确配合,并且加强了凸模纵向稳定性,避免小凸模产生纵弯曲。
(2)凸模与固定板为间隙配合,凸模装配调整和更换较方便。
(3)弹压导板用卸料螺钉与上模连接,加上凸模与固定板是间隙配合,因此能消除压力机导向误差对模具的影响,对延长模具寿命有利。
(4)冲裁排样采用直对排,一次冲裁获得两个零件,两件的落料工位离开一定距离,以增强凹模强度,也便于加工和装配。
这种模具用于冲压零件尺寸小而复杂、需要保护凸模的场合。
在实际生产中,对于精度要求高的冲压件和多工位的级进冲裁,采用了既有侧刃(粗定位)又有导正销定位(精定位)的级进模。
总之,级进模比单工序模生产率高,减少了模具和设备的数量,工件精度较高,便于操作和实现生产自动化。
对于特别复杂或孔边距较小的冲压件,用简单模或复合模冲制有困难时,可用级进模逐步冲出。
但级进模轮廓尺寸较大,制造较复杂,成本较高,一般适用于大批量生产小型冲压件。
1、10—导柱2—弹压导板3、11—导套4—导板镶块5—卸料螺钉6—凸模固定板
7—凸模8—上模座9—限位柱12—导料板13—凹模14—下模座15—侧刃挡块
图2.8.11侧刃定距的弹压导板级进模
3.排样
应用级进模冲压时,排样设计十分重要,它不但要考虑材料的利用率,还应考虑零件的精度要求、冲压成形规律、模具结构及模具强度等问题。
下面讨论这些因素对排样的要求。
(1)零件的精度对排样的要求零件精度要求高的。
除了注意采用精确的定位方法外,还应尽量减少工位数,以减少工位积累误差;孔距公差较小的应尽量在同一工步中冲出。
(2)模具结构对排样的要求零件较大或零件虽小但工位较多,应尽量减少工位数,可采用连续一复合排样法,如图2.8.12a,以减少模具轮廓尺寸。
(3)模具强度对排样的要求孔间距小的冲件,其孔要分步冲出,如图2.8.12b;工位之间凹模壁厚小的,应增设空步如图2.8.12c;外形复杂的冲件应分步冲出,以简化凸、凹模形状,增强其强度,便于加工和装配,如图2.8.12d;侧刃的位置应尽量避免导致凸、凹模局部工作而损坏刃口,如图2.8.12b;侧刃与落料凹模刀口距离增大0.2~0.4mm就是为了避免落料凸、凹模切下条料端部的极小宽度。
(4)零件成形规律对排样的要求需要弯曲、拉深、翻边等成形工序的零件,采用级进模冲压时,位于成形过程变形部位上的孔,一般应安排在成形工步之后冲出,落料或切断工步一般安排在最后工位上。
全部为冲裁工步的级进模,一般是先冲孔后落料或切断。
先冲出的孔可作后续工位的定位孔,若该孔不适合于定位或定位精度要求较高时,则应冲出辅助定位工艺孔(导正销孔),如图2.8.12a。
套料级进冲裁时,如图2.8.12e,按由里向外的顺序进行冲裁。
图2.8.12级进模的排样图
复合模是一种多工序的冲模。
是在压力机的一次工作行程中,在模具同一部位同时完成数道分离工序的模具。
复合模的设计难点是如何在同一工作位置上合理地布置好几对凸、凹模。
它在结构上的主要特征是有一个既是落料凸模又是冲孔凹模的凸凹模。
按照复合模工作零件的安装位置不同,分为正装式复合模和倒装式复合模两种。
1.正装式复合模(又称顺装式复合模)
图2.8.13为正装式落料冲孔复合模,凸凹模6在上模,落料凹模8和冲孔凸模11在下模。
正装式复合模工作时,板料以导料销13和挡料销12定位。
上模下压,凸凹模外形和凹模8进行落料,落下料卡在凹模中,同时冲孔凸模与凸凹模内孔进行冲孔,冲孔废料卡在凸凹模孔内。
卡在凹模中的冲件由顶件装置顶出凹模面。
顶件装置由带肩顶杆10和顶件块9及装在下模座底下的弹顶器组成。
该模具采用装在下模座底下的弹顶器推动顶杆和顶件块,弹性元件高度不受模具有关空间的限制,顶件力大小容易调节,可获得较大的顶件力。
卡在凸凹模内的冲孔废料由推件装置推出。
推件装置由打杆l、推板3和推杆4组成。
当上模上行至上止点时,把废料推出。
每冲裁一次,冲孔废料被推下一次,凸凹模孔内不积存废料,胀力小,不易破裂。
但冲孔废料落在下模工作面上,清除废料麻烦,尤其孔较多时。
边料由弹压卸料装置卸下。
由于采用固定挡料销和导料销,在卸料板上需钻出让位孔,或采用活动导料销或挡料销。
从上述工作过程可以看出,正装式复合模工作时,板料是在压紧的状态下分离,冲出的冲件平直度较高。
但由于弹顶器和弹压卸料装置的作用,分离后的冲件容易被嵌入边料中影响操作,从而影响了生产率。
2.倒装式复合模
图2.8.14为倒装式复合模。
凸凹模18装在下模,落料凹模17和冲孔凸模14和16装在上模。
倒装式复合模通常采用刚性推件装置把卡在凹模中的冲件推下,刚性推件装置由打杆12、推板11、连接维杆10和推件块9组成。
冲孔废料直接由冲孔凸模从凸凹模内孔推下,无顶件装置,结构简单,操作方便,但如果采用直刃壁凹模洞口,凸凹模内有积存废料,胀力较大,当凸凹模壁厚较小时,可能导致凸凹模破裂。
1—打杆2—模柄3—推板4—推杆5—卸料螺钉6—凸凹模7—卸料板8—落料凹模
9—顶件块10—带肩顶杆11—冲孔凸模12—挡料销13—导料销
图2.8.13正装式复合模
板料的定位靠导料销22和弹簧弹顶的活动挡料销5来完成。
非工作行程时,挡料销5由弹簧3顶起,可供定位;工作时,挡料销被压下,上端面与板料平。
由于采用弹簧弹顶挡料装置,所以在凹模上不必钻相应的让位孔。
但这种挡料装置的工作可靠性较差。
采用刚性推件的倒装式复合模,板料不是处在被压紧的状态下冲裁,因而平直度不高。
这种结构适用于冲裁较硬的或厚度大于0.3mm的板料。
如果在上模内设置弹性元件,即采用弹性推件装置,这就可以用于冲制材质较软的或板料厚度小于0.3mm,且平直度要求较高的冲裁件。
1—下模座2—导柱3、20—弹簧4—卸料板5—活动挡料销6—导套7—上模座
8—凸模固定板9—推件块10—连接推杆11—推板12—打杆13—模柄14、16—冲孔凸模15—垫板17—落料凹模18—凸凹模19—固定板21—卸料螺钉22—导料销
图2.8.14倒装式复合模
正装式和倒装式复合模结构比较:
正装式较适用于冲制材质较软的或板料较薄的平直度要求较高的冲裁件,还可以冲制孔边距离较小的冲裁件。
倒装式不宜冲制孔边距离较小的冲裁件,但倒装式复合模结构简单、又可以直接利用压力机的打杆装置进行推件,卸件可靠,便于操作,并为机械化出件提供了有利条件,故应用十分广泛。
复合模的特点是生产率高,冲裁件的内孔与外缘的相对位置精度高,板料的定位精度要求比级进模低,冲模的轮廓尺寸较小。
但复合模结构复杂,制造精度要求高,成本高。
复合模主要用于生产批量大、精度要求高的冲裁件。