第6章 熟料煅烧技术.docx
《第6章 熟料煅烧技术.docx》由会员分享,可在线阅读,更多相关《第6章 熟料煅烧技术.docx(59页珍藏版)》请在冰豆网上搜索。
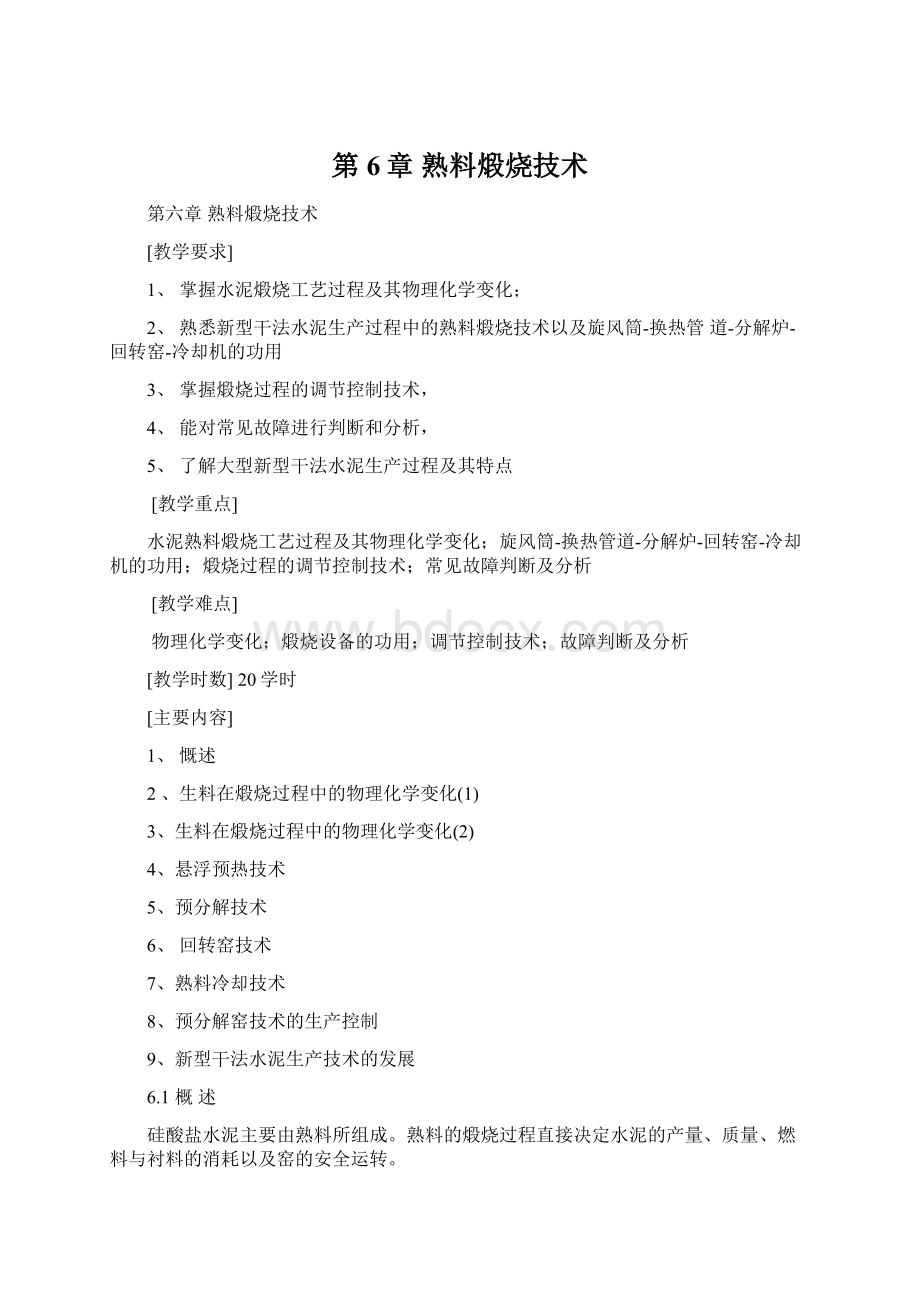
第6章熟料煅烧技术
第六章熟料煅烧技术
[教学要求]
1、掌握水泥煅烧工艺过程及其物理化学变化;
2、熟悉新型干法水泥生产过程中的熟料煅烧技术以及旋风筒-换热管道-分解炉-回转窑-冷却机的功用
3、掌握煅烧过程的调节控制技术,
4、能对常见故障进行判断和分析,
5、了解大型新型干法水泥生产过程及其特点
[教学重点]
水泥熟料煅烧工艺过程及其物理化学变化;旋风筒-换热管道-分解炉-回转窑-冷却机的功用;煅烧过程的调节控制技术;常见故障判断及分析
[教学难点]
物理化学变化;煅烧设备的功用;调节控制技术;故障判断及分析
[教学时数]20学时
[主要内容]
1、慨述
2、生料在煅烧过程中的物理化学变化
(1)
3、生料在煅烧过程中的物理化学变化
(2)
4、悬浮预热技术
5、预分解技术
6、回转窑技术
7、熟料冷却技术
8、预分解窑技术的生产控制
9、新型干法水泥生产技术的发展
6.1概述
硅酸盐水泥主要由熟料所组成。
熟料的煅烧过程直接决定水泥的产量、质量、燃料与衬料的消耗以及窑的安全运转。
新型干法水泥生产,是以悬浮预热和窑外分解技术为核心,把现代科学技术和工业生产成果,广泛用于水泥生产全过程,使水泥生产具有高效、优质、低耗、符合环保要求和大型化、自动化为特征的现代水泥生产方法,并具有现代化的水泥生产新技术和与之相适应的现代管理方法。
悬浮预热、窑外分解技术,从根本上改变了物料的预热、分解过程的传热状态,将窑内物料堆积状态的预热和分解过程,分别移到悬浮预热器和分解炉内进行。
由于物料悬浮在气流中,与气流的接触面积大幅度增加,因此传热极快、效率高,同时物料在悬浮态下混合均匀,将燃料燃烧的热及时传给物料,使之迅速分解。
因此传热、传质均很迅速,大幅度提高了生产效率和热效率,目前世界上最大的规模已经达到日产万吨以上,见表6-1。
预分解窑的关键技术装备有旋风筒、换热管道、分解炉、回转窑、冷却机(简称筒-管-炉-窑-机)等。
这五组关键技术装备五位一体,彼此关联,互相制约,形成了一个完整的熟料煅烧的热工体系,分别承担着水泥熟料煅烧过程的预热、分解、烧成、冷却任务,如图6.1所示。
表6-1国内外部分7000~12000t/d预分解窑统计表
序
号
熟料
产量
(t/d)
窑规格
(m)
单位
容积
产量(t/m3)
烧成热耗
(kJ/kg)
预热器、分解炉配备情况
备注
1
12000
Ф6.2X105
4.48
2864
5级4列双炉Prepol-AS
美国
2
10000
Ф6.0X105
3.92
2948
5级3列双炉SLC型
韩国
3
2X10000
Ф6.0X95
2916
5级双列单炉单在线分解炉型
中国海螺
4
9100
Ф5.8X94
4.29
5级NMFC3型
韩国
5
9000
Ф6X96
3.89
2990
5级3列双炉SLC型
泰国
6
8600
Ф6X88
4.07
2947
5级双列单炉RSP
台湾
7
8500
Ф5.6/6X87
2947
6级双列单炉带预燃室的Prepol型
泰国
8
8000
Ф5.6X87
3.96
2969
6级双列单炉带预燃室的Prepol型
中国海螺
9
7800
Ф5.6X84
4.44
3024
4级SLC型
印尼
10
7600
Ф5.6X87
4.18
2889
6级DopolR型
韩国
11
7500
Ф5.6X82
4.37
5级PYROCLON型
泰国
12
7500
Ф5.6X87
4.12
2947
6级双列单炉带预燃室的Prepol型
泰国
13
7000
Ф5.6X82
4.08
5级双列双pyrolon7950炉
沙特
6.2生料在煅烧过程中的物理化学变化
生料在加热过程中,依次发生干燥、粘土矿物脱水、碳酸盐分解、固相反应、熟料烧结及熟料冷却结晶等重要的物理化学反应。
这些反应过程的反应温度、反应速度及反应产物不仅受原料的化学成分和矿物组成的影响,还受反应时的物理因素诸如生料粒径、均化程度、气固相接触程度等的影响。
6.2.1干燥
排除生料中自由水分的工艺过程称为干燥。
6.2.2脱水
脱水是指粘土矿物分解放出化合水。
粘土矿物的化合水有两种:
一种是以OH一离子状态存在于晶体结构中,称为晶体配位水(也称结构水);另一种是以水分子状态吸附于晶层结构间,称为晶层间水或层间吸附水。
所有的粘土都含有配位水;多水高岭土、蒙脱石还含有层间水;伊利石的层间水因风化程度而异。
层间水在100℃左右即可排除,而配位水则必须高达400~600℃以上才能脱去。
粘土中的主要矿物高岭土发生脱水分解反应如下式所示:
Al2O3
2SiO2
2H20
Al203
2SiO2+2H2O↑
高岭土无水铝硅酸盐(偏高岭土)水蒸气
Al203
2SiO2
Al203+2SiO2
高岭土进行脱水分解反应属吸热过程。
高岭土在失去化合水的同时,本身晶体结构遭受破坏,生成了非晶质的无定形偏高岭土(脱水高岭土),由于偏高岭土中存在着因OH一基跑出后留下的空位,故可以把它看成是无定型的SiO2和Al2O3,这些无定形物具有较高活性。
6.2.3碳酸盐分解
生料中的碳酸钙和夹杂的少量碳酸镁在煅烧过程中分解并放出CO2的过程称碳酸盐分解。
碳酸镁的分解温度始于402~480℃左右,最高分解温度700℃左右;碳酸钙在600℃时就有微弱分解发生,但快速分解温度在812~928℃之间变化。
MgCO3在590℃、CaCO3在890℃时的分解反应式如下:
MgC03
MgO+CO2↑-(1047~1214)J/g
CaC03
CaO+CO2↑-1645J/g
其中,碳酸钙在水泥生料中所占比例80%左右,其分解过程需要吸收大量的热,是熟料煅烧过程中消耗热量最多的一个过程,因此,它是水泥熟料煅烧过程重要的一环。
6.2.3.1碳酸钙分解反应的特点
1.可逆反应
2.强吸热反应
每1kg纯碳酸钙在890℃时分解吸收热量为1645J/g,是熟料形成过程中消耗热量最多的一个工艺过程。
分解所需总热量约占预分解窑的二分之一。
3.烧失量大
每100kg的纯CaCO3分解后排出挥发性CO2气体44kg,烧失量占44%。
4.分解温度与CO2分压和矿物结晶程度有关
在常压(101325Pa)和分解出的CO2分压达1个大气压(即平衡分解压力101325Pa)的环境中,纯碳酸钙的分解温度为800℃。
平衡分压增大,分解温度增高,环境C02的浓度和压力对碳酸钙分解温度的影响见图6-2所示
6.2.3.2、碳酸钙的分解过程
一颗正在分解的CaCO3颗粒,颗粒内部的分解反应可分为下列5个过程:
①热气流向颗粒表面传进分解所需要的热量Qi;
②热量以传导方式由表面向分解面传递的过程;
③在一定温度下碳酸钙吸收热量,进行分解并放出CO2的化学过程;
④分解放出的CO2,穿过CaO层,向表面扩散传质;
⑤表面的CO2向周围气流介质扩散。
在这5个过程中,有4个是物理传热传递过程,唯独碳酸钙吸收热量分解放出CO2的过程是一个化学反应过程。
在颗粒开始分解与分解面向颗粒内部深入时,各过程对分解的影响程度不相同,哪个过程最慢,哪个便是主控过程。
即碳酸钙的分解速度受控于其中最慢的一个过程。
分解速度或者分解所需的时间将决定于化学反应所需时间,即反应生成的CO2通过表面CaO层的扩散是整个碳酸钙分解过程中的速度控制过程。
在悬浮预热器和分解炉内,由于生料悬浮于气流中,基本上可以看作是单颗粒,其传热系数较大,特别是传热面积非常大,分解过程的速率受化学反应过程所控制。
在分解炉(物料温度850℃左右),只需几秒钟即可使碳酸钙分解率达到85%~95%。
6.2.3.3、影响碳酸钙分解速度的因素
1.石灰质原料的特性
以最常见的石灰石为例,当石灰石中伴生有其他矿物和杂质一般具有降低分解温度的作用,
2.生料细度和颗粒级配
生料粉磨得细,且颗粒均匀、粗粒少,生料比表面积增加,使传热和传质速度加快,有利于分解反应进行。
3.生料悬浮分散程度
生料悬浮分散差,相对地增大了颗粒尺寸,减少了传热面积,降低了碳酸钙的分解速度。
4.温度
提高反应温度,分解反应的速度加快,分解时间缩短。
但应注意温度过高,将增加废气温度和热耗,预热器和分解炉结皮、堵塞的可能性亦大。
5.系统中CO2分压
通风良好CO2分压较低,有利于CO2的扩散和加速碳酸钙的分解。
6.生料中粘土质组分的性质
如果粘土质原料的主导矿物是高岭土,由于其活性大,在800℃下能和氧化钙或直接与碳酸钙进行固相反应,生成低钙矿物,可以促进碳酸钙的分解过程。
反之,如果粘土主导矿物是活性差的蒙脱石和伊利石,则CaCO3的分解速度就慢。
6.2.4、固相反应
6.2.4.1、反应过程
通常在碳酸钙分解的同时,分解产物CaO与生料中的SiO2、Fe2O3、Al2O3等通过质点的相互扩散而进行固相反应,形成熟料矿物。
固相反应的过程比较复杂,其过程大致如下:
~800℃CaO+Al2O3
CaO·Al2O3(CA)
Ca0+Fe2O3
CaO·Fe2O3(CF)
2Ca0+Si02
2CaO·Si02(C2S)开始形成
800~900℃7(CaO·Al2O3)+5CaO
12CaO·7Al2O3(C12A7)
900~1100℃2CaO+Al2O3+Si02
2CaO·Al2O3·Si02(C2AS)形成后又分解
12CaO·7Al2O3+9CaO——7(3CaO·Al2O3)(C3A)开始形成7(2CaO·Fe2O3)+2CaO+12CaO·7Al2O3
7(4CaO·Al2O3·Fe2O3)
(C4AF)开始形成
1100~l200℃大量形成C3A和C4AF,C2S含量达最大值。
水泥熟料矿物C3A和C4AF、C2S的形成是一个复杂的多级反应,反应过程是交叉进行的。
水泥熟料矿物的固相反应是放热反应,固相反应的放热量约为420~500J/g。
固相反应通常需要在较高温度下进行,影响固相反应的主要因素主要有以下几点:
(1)生料细度及均匀程度
生料的均匀混合,使生料各组分之间充分接触,有利固相反应进行。
(2)原料性质
当原料中含有结晶Si02(如燧石、石英砂)和结晶方解石时,由于破坏其晶格困难,晶体内的分子很难离开晶体而参加反应,所以使固体反应的速度明显降低,特别是原料中含有粗颗粒石英砂时,其影响更大。
因此,在原料选择时,力求避免采用粗晶石英,如不得已而必须使用时,可将其单独粉磨,务求配制粉磨能耗最低但反应活性最佳的生料颗粒级配。
(3)温度
提高反应温度,质点能量增加,增加了质点的扩散速度和化学反应速度,可加速固相反应。
6.2.5、熟料烧结
当物料温度升高到最低共熔温度后,固相反应形成的铝酸钙和铁铝酸钙熔剂性矿物及氧化镁、碱等熔融成液相。
在高温液相作用下,固相硅酸二钙和氧化钙都逐步溶解于液相中,硅酸二钙吸收氧化钙形成硅酸盐水泥的主要矿物—硅酸三钙,其反应式如下:
C2S+Ca0
C3S
随着温度的升高和时间延长,液相量增加,液相粘度降低,氧化钙、硅酸二钙不断溶解、扩散,硅酸三钙晶核不断形成,并逐渐发育、长大,最终形成几十微米大小、发育良好的阿利特晶体。
与此同时,晶体不断重排、收缩、密实化,物料逐渐由疏松状态转变为色泽灰黑、结构致密的孰料,我们称以上过程为熟料的烧结过程,简称熟料烧结。
在配合生料适当,生料成分稳定的条件下,硅酸盐水泥熟料在1250~1280℃开始出现液相,1300℃左右时Ca0和C2S溶入液相中开始大量生成C3S,这一过程也称为石灰吸收过程。
一直到1450℃液相量继续增加,游离氧化钙被充分吸收。
故通常把1300~1450~1300℃称为熟料的烧结温度。
在此温度范围内大致需要10~20min完成熟料烧结过程。
6.2.5.1、影响熟料烧结过程的因素
由上述过程可知,熟料的烧结在很大程度上取决于液相含量及其物理化学性质。
因此,控制液相出现的温度、液相量、液相粘度、液相表面张力和氧化钙、硅酸二钙溶于液相的速率,并努力改善它们的性质至关重要。
1.最低共熔温度
表6-2一些系统的量低共熔温度
系统
最低共熔温度(℃)
系统
最低共熔温度(℃)
C3S-C2S-C3A
1455
C3S-C2S-C3A–C4AF
1338
C3S-C2S-C3A-Na2O
1430
C3S-C2S-C3A-Na2O-Fe203
1315
C3S-C2S-C3A-MgO
1375
C3S-C2S-C3A-Fe203-MgO
1300
C3S-C2S-C3A-Na2O-MgO
1365
C3S-C2S-C3A-Na2O-MgO-Fe203
1280
液相出现的温度决定于物料在加热过程中的最低共熔温度。
而最低共熔温度决定于系统组分的性质与数目。
表6-2列出了一些系统的最低共熔温度。
由表6-2可知,系统组分数目越多,其最低共熔温度越低,即液相初始出现的温度越低。
2.液相量
熟料的烧结必须要有一定数量的液相。
液相是硅酸三钙形成的必要条件,适宜的液相量有利于C3S形成,并保证熟料的质量。
液相量太少,不利于C3S形成,反之,过多的液相易使熟料结大块,给煅烧操作带来困难。
液相量与组分的性质、含量及熟料烧结温度等有关。
因此,不同的生料成分与煅烧温度等对液相量有很大影响。
一般水泥熟料烧成阶段的液相量大约为20%~30%。
(1)液相量与煅烧温度、组分含量有关,根据硅酸盐物理化学原理,不同温度下形成的液相量可按下式计算:
①煅烧温度为1338℃时:
IM>1.38L=6.1F(6.1)
IM<1.38L=8.2A-5.22F(6.2)
②煅烧温度为1400℃和1450℃时:
1400℃L=2.95A+2.5F+M+R(6.3)
1500℃L=3.0A+2.2F+M+R(6.4)
式中L——液相量(%);
F——熟料中Fe2O3。
的含量(%);
A——熟料中Al2O3的含量(%);
M、R——MgO及(Na20+K20)的含量(%)。
(2)液相量随熟料中铝率而变化,一般硅酸盐水泥在煅烧阶段的液相量随铝率和温度的变化情况见表6-3所示。
生产中,应合理设计熟料化学成分与率值,控制煅烧温度在一个适当的范围内。
这个范围大体上是出现烧结所必需的最少的液相量时的温度到出现结大块时的温度之间,即通常所说的烧结范围。
就硅酸盐水泥而言,烧结范围约150℃左右。
当系统液相量随温度升高而缓慢增加,其烧结范围就较宽;反之,其烧结范围就窄。
3.液相粘度
液相粘度对硅酸三钙的形成影响较大。
粘度小,液相中质点的扩散速度增加,有利于硅酸三钙的形成。
而液相的粘度又随温度与组成(包括少量氧化物)而变化。
提高温度,液相内部质点动能增加,削弱了相互间作用力,因而降低了液相粘度。
提高铝率时,液相粘度增大,而降低铝率则液相粘度减少。
MgO、SO3的存在可使液相粘度降低。
Na2O、K2O使液相粘度增大,而Na2SO4或K2SO4则使液相粘度降低。
表6-4CaO溶于液相所需的时间(min)
温度(℃)
粒径(mm)
0.1
0.05
0.025
0.001
1340
11.5
59
25
12
1375
28
14
6
4
1400
15
5.5
3
1.5
1450
5
2.3
1
0.5
1500
1.8
1.7
4.液相的表面张力
液相的表面张力愈小,愈易润湿固相物质或熟料颗粒,有利于固液反应,促进C3S的形成。
5.氧化钙和硅酸二钙溶于液相的速率
C3S的形成过程也可以视为CaO和C2S在液相中的溶解过程。
CaO和C2S的溶解速率大,C3S的成核与发育越快。
因此,要加速C3S的形成实际上就是提高CaO与C2S的溶解速率,而这个速率大小受CaO颗粒大小和液相粘度所控制。
表6-4为实验室条件下,不同粒径CaO在不同温度下完全溶于液相所需的时间。
6.2.6、熟料冷却
6.2.6.1、熟料冷却过程及目的
熟料烧结过程完成之后,C3S的生成反应结束,熟料从烧成温度开始下降至常温,熔体晶化、凝固,熟料颗粒结构形成,并伴随熟料矿物相变的过程称为熟料的冷却。
冷却的目的在于:
改善熟料质量与易磨性;降低熟料温度,便于熟料的运输、储存和粉磨;部分回收熟料出窑带走的热量,预热二、三次空气,从而降低熟料热耗,提高热利用率。
6.2.6.2、熟料冷却速度对熟料质量的影响
熟料冷却的速度影响着熟料的矿物组成、结构以及易磨性。
冷却速度不同,所得到的熟料矿物组成与性能也会不同。
如果以18~20℃/min左右的急速降温速率对熟料进行冷却时,则可以发现C3S的分解、C2S的转化、过大的方镁石晶体及全部的C3A、C4AF结晶态不复存在,即急速降温速率(急冷)优于缓慢冷却(慢冷)。
6.2.6.3、急冷对改善熟料质量的作用
1.防止或减少C3S的分解
2.避免β-C2S转变成γ-C2S
3.改善了水泥安定性
4.使熟料C3A晶体减少,提高水泥抗硫酸盐性能
图6-3旋风筒功能结构示意图
5.改善熟料易磨性
6.可克服水泥瞬凝或快凝
6.3 悬浮预热技术
6.3.1悬浮预热技术
悬浮预热技术是指低温粉状物料均匀分散在高温气流之中,在悬浮状态下进行热交换,使物料得到迅速加热升温的技术。
6.3.2悬浮预热技术的优越性
悬浮预热技术的突破,从根本上改变了物料预热过程的传热状态,将窑内物料堆积态的预热和分解过程,分别移到悬浮预热器和分解炉内在悬浮状态下进行。
由于物料悬浮在热气流中,与气流的接触面积大幅度增加,因此传热速度极快,传热效率很高。
同时,生料粉与燃料在悬浮态下均匀混合,燃料燃烧产生的热及时传给物料,使之迅速分解。
所以,由于传热、传质迅速,大幅度提高了生产效率和热效率。
6.3.3 悬浮预热器的构成及功能
目前在预分解窑系统中使用的悬浮预热器主要是旋风预热器,构成旋风预热器的热交换单元主要是旋风筒及各级旋风筒之间的连接管道(换热管道),图6-3。
悬浮预热器必须具备使气、固两相能充分分散均布、迅速换热、高效分离三个功能。
6.3.4旋风预热器是主要的预热设备
旋风预热器是由旋风筒和连接管道组成的热交换器。
现在一般为五级预热器,也有六级预热器。
换热管道是旋风预热器系统中的重要装备,它不但承担着上下两级旋风筒间的连接和气固流的输送任务,同时承担着物料分散、均布、锁风和气、固两相间的换热任务,所以,换热管道除管道本身外还装设有下料管、撒料器、锁风阀等装备,它们同旋风筒一起组合成一个换热单元。
旋风筒的作用主要是气固分离,传热只占6%~12.5%。
最高一级旋风筒的分离效率决定着预热器系统的粉尘排出量,提高它的分离效率是降低外部循环的有效措施,因此一级旋风筒一般为并联的双旋风筒。
由于在换热管道中,生料尘粒与热气流之间的温差及相对速度都较大,生料粉被气流吹起悬浮,热交换剧烈,因此从理论计算及实践均证明,生料与气流的热交换主要(约80%以上)在连接管道内进行。
各种类型的旋风预热器的换热管道风速,一般选用12~18m/s。
为了使生料能够充分的分散悬浮于管道内的气流中,加速气固之间的传热。
必须采取以下措施:
(1)在生料进入每级预热器的上升管道处,管道内应有物料分散装置,一般采用板式撒料器(如图6-4所示)和箱式撒料器。
撒料装置的作用在于防止下料管下行物料进入换热管道时的向下冲料,并促使下冲物料冲至下料板后飞溅、分散。
装置虽小,但作用极大。
(2)选择生料进入管道的合适方位,使生料逆气流方向进入管道,以提高气固相的相对速度和生料在管道内停留时间。
(3)两级旋风筒之间的管道必须有足够的长度,以保证生料悬浮起来,并在管道内有足够的停留运行距离,充分发挥管道传热的优势。
(4)旋风筒下料管道上设有锁风翻板排灰阀,要求结构合理、轻便灵活不漏风,生料能连续卸出,有料封作用。
锁风翻板排灰阀(简称锁风阀)是预热器系统的重要附属设备。
它装设于上级旋风筒下料管与下级旋风筒出口的换热管道入料口之间的适当部位。
其作用在于保持下料管经常处于密封状态,既保持下料均匀畅通,又能密封物料不能填充的下料管空间,最大限度地防止由于上级旋风筒与下级旋风筒出口换热管道间由于压差容易产生的气流短路、漏风,做到换热管道中的气流及下料管中的物料“气走气路、料走料路”,各行其路。
这样,既有利于防止换热管道中的热气流经下料管上窜至上级旋风筒下料口,引起已经收集的物料再次飞扬,降低分离效率;又能防止换热管道中的热气流未经同物料换热,而经由上级旋风筒底部窜入旋风筒内,造成不必要的热损失。
6.4预分解技术
6.4.1预分解技术
预分解(或称窑外分解)技术是指将已经过悬浮预热后的水泥生料,在达到分解温度前,进入到分解炉内与进入炉内的燃料混合,在悬浮状态下迅速吸收燃料燃烧热,使生料中的碳酸钙迅速分解成氧化钙的技术。
预分解技术发明后,熟料煅烧所需的60%左右的燃料转移到分解炉内,并将其燃烧热迅速应用于碳酸盐分解进程,这样不仅减少了窑内燃烧带的热负荷,并且入窑生料的碳酸盐分解率达到85%~95%左右,从而大幅度提高了窑系统的生产效率。
6.4.2预分解窑的特点
如图6-5所示,预分解窑的特点是在悬浮预热器与回转窑之间增设一个分解炉或利用窑尾上升烟道,原有预热器装设燃料喷入装置,使燃料燃烧的放热过程与生料的碳酸盐分解的吸热过程,在其中以悬浮态或流化态下极其迅速地进行,从而使入窑生料的分解率从悬浮预热窑的30%左右提高到85%~95%。
这样,不仅可以减轻窑内煅烧带的热负荷,有利于缩小窑的规格及生产大型化,并且可以节约单位建设投资,延长衬料寿命,有利于减少大气污染。
预分解窑是在悬浮预热窑基础上发展起来的,是悬浮预热窑发展的更高阶段,是继悬浮预热窑发明后的又一次重大技术创新。
6.4.3分解炉内气、固流运动方式及功能
分解炉内的气流运动,有四种基本型式:
即涡旋式、喷腾式、悬浮式及流化床式。
在这四种型式的分解炉内,生料及燃料分别依靠“涡旋效应”、“喷腾效应”、“悬浮效应”和“流态化效应”分散于气流之中。
由于物料之间在炉内流场中产生相对运动,从而达到高度分散、均匀混合和分布、迅速换热、延长物料在炉内的滞留时间,达到提高燃烧效率、换热效率和入窑物料碳酸盐分解率的目的。
1.旋流式分解炉又称旋风式分解炉,以SF型为代表。
现已发展为NSF(NewSuspensionPreheatcrFlashCalciner)型,它的原理已发展为旋流一喷腾式分解炉类型。
其简要示意图如图6-6所示。
NSF分解炉是原有SF分解炉的发展、改造型,由原气流运动的旋流型改进为旋流-喷腾型。
它主要改进了燃料和来自冷却机新鲜热空气的混合,使燃料充分燃烧;同时使预热后的生料分两路(或四路,上下各两路)分别进入分解炉反应室和窑尾上升管道中,以降低窑尾废气温度,减少结皮的可能性,并使生料进一步预热、与燃料充分混