刀具材料PCD.docx
《刀具材料PCD.docx》由会员分享,可在线阅读,更多相关《刀具材料PCD.docx(8页珍藏版)》请在冰豆网上搜索。
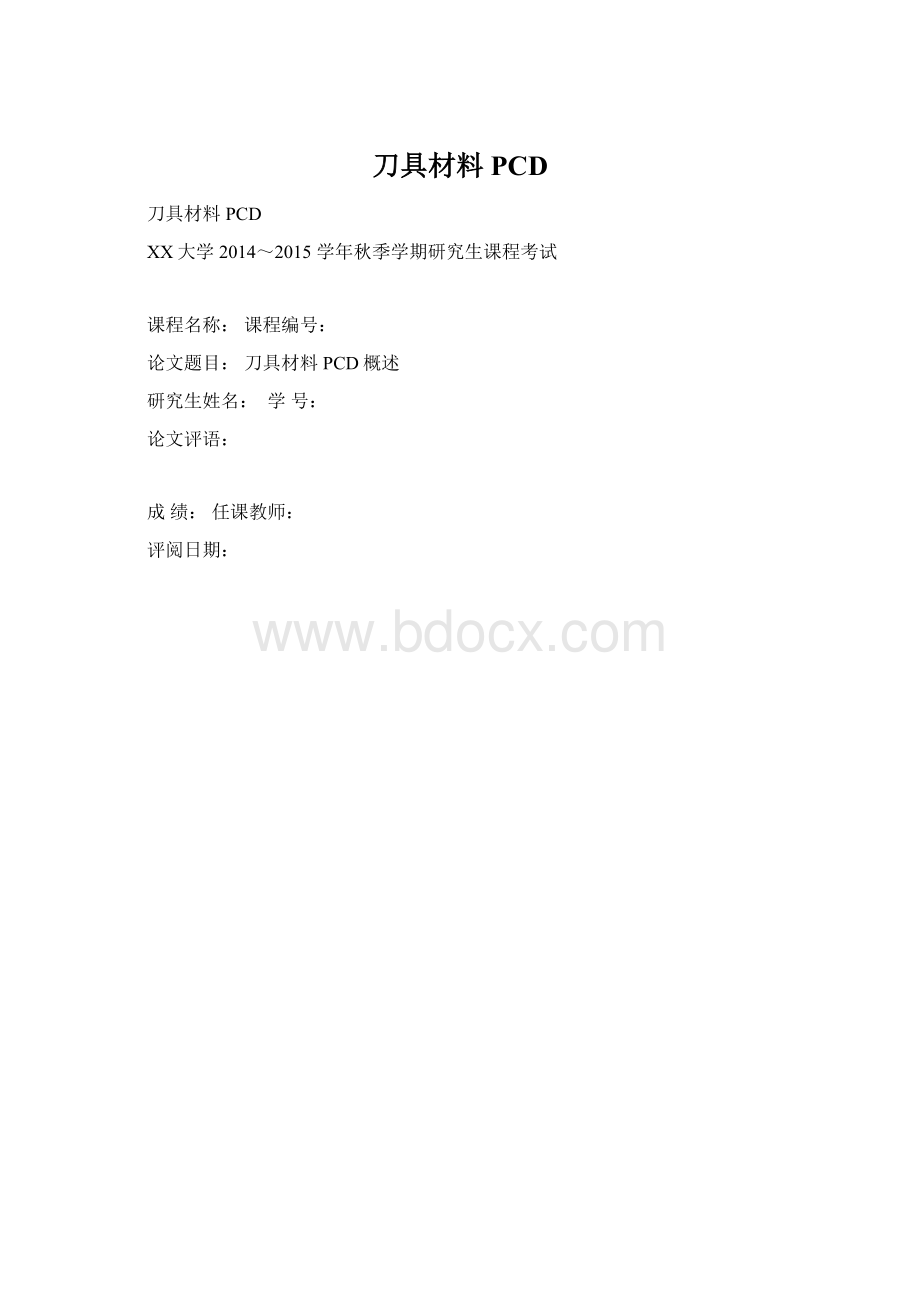
刀具材料PCD
刀具材料PCD
XX大学2014~2015学年秋季学期研究生课程考试
课程名称:
课程编号:
论文题目:
刀具材料PCD概述
研究生姓名:
学号:
论文评语:
成绩:
任课教师:
评阅日期:
1引言
随着人类生活、生产水平的提高,高速钢刀具已不能满足高加工效率和高加工质量的新要求。
随着制造业的快速发展,金刚石刀具的生产和应用正在逐年增加。
人们已经开始寻求性能更高的新型刀具材料[1]。
天然金刚石价格昂贵,金刚石广泛应用于切削加工的还是PCD,自20世纪70年代初,采用高温高压合成技术制备的PCD复合片研制成功以后,在很多场合下天然金刚石已经被人造PCD所代替。
PCD原料来源丰富,其制造技术已经成熟,而且其价格低廉,只有天然金刚石的几十分之一。
如此使金刚石刀具的应用范围扩展到航空、航天、汽车、电子、石材等多个领域。
2刀具材料PCD的介绍
PCD又称人造聚晶金刚石。
PCD复合片是由粒度为微米级的金刚石颗粒与钴,镍等金属粉末混合均匀后,在高温高压下,在碳化钨基材上烧结而成的一种新型刀坯材料[2]。
PCD复合片不仅具有金刚石高硬度,高耐磨性,高导热性,低摩擦因数,低热膨胀系数等优越性能,同时还具有硬质合金良好的强度和韧性。
因此,可切割成所需刀头,将刀头焊接在硬质合金基体上,经过刃磨从而制成切削性能良好的PCD刀具。
随着机械制造行业的发展,对被加工工件的质量要求越来越高,许多刀具材料已无法达到所需标准,而原料来源丰富,价格低廉,切削性能优良的PCD材料所制成的刀具却能够满足机械加工的需要,因此PCD材料被越来越广泛的用于机械制造及加工的过程中。
但PCD刀具无法刃磨出极其锋利的刃口,很难达到超精密镜面切削,现在工业中还不能方便的制造带有断屑槽的PCD刀片[3]。
3PCD刀具材料的性能指标
一般刀具材料所应具备的性能主要有:
(1)高硬度和高耐磨性;刀具硬度应高于工件材料的硬度,常温硬度一般在60HRC以上。
耐磨性是指材料抵抗磨损的能力,它与材料硬度、强度和组织结构有关。
材料硬度越高,耐磨性越好;组织中碳化物和氮化物等硬质点的硬度越高,颗粒越小,数量越多且分布越均匀,则耐磨性越高。
例如:
碳素钢的硬度在62HRC;高速钢的硬度在63-70HRC;硬质合金的硬度为89-93HRA[4]。
(2)足够的强度与冲击韧性;切削时刀具要承受较大的切削力、冲击和振动,为避免崩刀和折断,刀具材料应具有足够的强度和韧性。
刀具材料的抗弯强度大小顺序为:
高速钢>硬质合金>立方氮化硼、金刚石和陶瓷。
(3)足够的高耐热性热硬性和较好的传热性;耐热性是指刀具材料在高温下保持足够的硬度、耐磨性、强度和韧性、抗氧化性、抗粘结性和抗扩散性的能力(亦称为热稳定性)。
材料在高温下仍保持高硬度的能力称为热硬性(亦称高温硬度、红硬性),它是刀具材料保持切削能力的必备条件。
刀具材料的高温硬度越高,耐热性越好,允许的切削速度越高。
刀具材料的热导率大,有利于将切削区的热量传出,降低切削温度[5]。
(4)良好的工艺性和经济性。
为了便于刀具加工制造,刀具材料要有良好的工艺性能,如热轧、锻造、焊接、热处理和机械加工等工艺性能。
PCD刀具材料不仅具有这些基本性能,而且具有其它一些优良性能。
3.1PCD刀具材料的优点:
(1)PCD的硬度可达800HV,为硬质合金的八十至一百二十倍,而且PCD的耐磨性更好。
如下图1为PCD与硬质合金刀具的耐磨性比较。
图1硬质合金与PCD刀具耐磨性比较
(2)PCD的导热系数为700W/MK,为硬质合金的1.5~9倍,甚至高于PCBN和铜。
因此PCD刀具热量传递迅速,良好的传热性在很大程度上能够延长刀具寿命。
(3)PCD的摩擦系数一般仅为0.1至0.3,而硬质合金的摩擦系数为0.4~1。
因此PCD刀具可显著减小切削力,从而延长了刀具寿命。
(4)PCD的热膨胀系数小,因此PCD刀具热变形小,加工精度高。
刀具热变形越大,加工出的工件表面质量就越差,要想加工出良好加工表面质量的工件就必须严格控制刀具的热变形。
(5)PCD刀具与有色金属和非金属材料的亲和力小,在加工过程中刀尖不易形成积屑瘤。
刀具与被加工材料的亲和力小,那么在加工过程中被加工材料就不容易粘接在刀具表面,也就不容易形成积屑瘤。
下图2为切削工程中形成的积屑瘤,在很大程度上降低了工件的表面质量。
图2积屑瘤
(6)金刚石刀具的弹性模量大,断裂强度高(比氧化铝高三倍),切削刃钝圆半径值可以磨得很小,不易断裂,能长期保持切削刃的锋利程度[6-8]。
3.2PCD刀具材料的缺点:
(1)PCD刀具材料的材质比较脆,在切削的工程中很可能因为受到冲击或者受力不均而崩刃。
(2)PCD刀具材料制成的刀具只可完成较小尺寸变化加工。
大的尺寸变化容易使刀片受力不均而损坏刀片。
(3)PCD刀片比较难加工。
PCD刀片的加工主要包括PCD复合片的切割工艺,PCD刀片的焊接工艺,PCD刀片的刃磨工艺。
这些工艺完成的好坏会直接影响刀片的质量,而在加工过程中对加工条件,加工工艺的要求很高。
(4)PCD及人造聚晶金刚石刀具的刃口锋利性和加工的工件表面质量低于ND,同时其可加工性很差,磨削比小,难以根据刀头的几何形状任意成形。
因此目前利用人造聚晶金刚石复合片只能制造车刀,至今还不能制造带断屑槽的可转位刀片和复杂三维曲面几何形状的铣刀。
另外,由于金刚石是由碳原子组成的,它与铁元素的亲和力大,故不能用金刚石刀具切削钢铁材料[9]。
。
4PCD刀具的制造技术
4.1PCD复合片的制造
PCD复合片是由天然或人工合成的金刚石粉末与结合剂(其中含钴、镍等金属)按一定比例在高温(1000~2000℃)、高压(5~10万个大气压)下烧结而成。
在烧结过程中,由于结合剂的加入,使金刚石晶体间形成以TiC、SiC、Fe、Co、Ni等为主要成分的结合桥,金刚石晶体以共价键形式镶嵌于结合桥的骨架中。
通常将复合片制成固定直径和厚度的圆盘,还需对烧结成的复合片进行研磨抛光及其它相应的物理、化学处理。
4.2PCD刀片的加工:
PCD刀片的加工包括复合片的切割、刀片的焊接、刀片刃磨等步骤[9]。
4.2PCD刀片片的加工
4.2.1PCD复合片的切割工艺
由于PCD复合片具有很高的硬度及耐磨性,因此必须采用特殊的加工工艺。
目前,加工PCD复合片主要采用电火花线切割、激光加工、超声波加工、高压水射流等几种工艺方法,其工艺特点的比较如下。
PCD复合片切割工艺的比较:
工艺方法-工艺特点
电火花加工-高度集中的脉冲放电能量、强大的放电爆炸力使PCD材料中的金属融化,部分金刚石石墨化和氧化,部分金刚石脱落,工艺性好、效率高
超声波加工-加工效率低,金刚石微粉消耗大,粉尘污染大
激光加工-非接触加工,效率高、加工变形小、工艺性差
在上述加工方法中,电火花加工效果较佳。
PCD中结合桥的存在使电火花加工复合片成为可能。
在有工作液的条件下,利用脉冲电压使靠近电极金属处的工作液形成放电通道,并在局部产生放电火花,瞬间高温可使聚晶金刚石熔化、脱落,从而形成所要求的三角形、长方形或正方形的刀头毛坯。
电火花加工PCD复合片的效率及表面质量受到切削速度、PCD粒度、层厚和电极质量等因素的影响,其中切削速度的合理选择十分关键,实验表明,增大切削速度会降低加工表面质量,而切削速度过低则会产生“拱丝”现象,并降低切割效率。
增加金刚石刀具(PCD)刀片厚度也会降低切割速度[6-8]。
4.2.2PCD刀片的焊接工艺
PCD复合片与刀体的结合方式除采用机械夹固和粘接方法外,大多是通过钎焊方式将PCD复合片压制在硬质合金基体上。
焊接方法主要有激光焊接、真空扩散焊接、真空钎焊、高频感应钎焊等。
目前,投资少、成本低的高频感应加热钎焊在PCD刀片焊接中得到广泛应用。
在刀片焊接过程中,焊接温度、焊剂和焊接合金的选择将直接影响焊后刀具的性能。
在焊接过程中,焊接温度的控制十分重要,如焊接温度过低,则焊接强度不够;如焊接温度过高,PCD容易石墨化,并可能导致“过烧”,影响PCD复合片与硬质合金基体的结合。
在实际加工过程中,可根据保温时间和PCD变红的深浅程度来控制焊接温度(一般应低于700℃)。
国外的高频焊接多采用自动焊接工艺,焊接效率高、质量好,可实现连续生产;国内则多采用手工焊接,生产效率较低,质量也不够理想[10]。
4.2.3PCD刀片的刃磨工艺
PCD的高硬度使其材料去除率极低(甚至只有硬质合金去除率的万分之一)。
目前,聚晶金刚石刀具(PCD)刃磨工艺主要采用树脂结合剂金刚石砂轮进行磨削。
由于砂轮磨料与PCD之间的磨削是两种硬度相近的材料间的相互作用,因此其磨削规律比较复杂。
由于电火花磨削(EDG)技术几乎不受被磨削工件硬度的影响,因此采用EDG技术磨削PCD具有较大优势。
某些复杂形状聚晶金刚石刀具(PCD)(如木工刀具)的磨削也对这种灵活的磨削工艺具有巨大需求。
随着电火花磨削技术的不断发展,EDG技术将成为PCD磨削的一个主要发展方向。
5PCD刀具的应用
聚晶金刚石(PCD)刀具加工铝制工件具有刀具寿命长、金属切除率高等优点,其缺点是刀具价格昂贵,加工成本高。
这一点在机械制造业已形成共识。
但近年来PCD刀具的发展与应用情况已发生了许多变化。
如今的铝材料在性能上已今非昔比,在加工各种新开发的铝合金材料(尤其是高硅含量复合材料)时,为了实现生产率及加工质量的最优化,必须认真选择PCD刀具的牌号及几何参数,以适应不同的加工要求。
PCD刀具的另一个变化是加工成本不断降低,在市场竞争压力和刀具制造工艺改进的共同作用下,PCD刀具的价格已大幅下降50%以上。
上述变化趋势导致PCD刀具在铝材料加工中的应用日益增多,而刀具的适用性则受到不同被加工材料的制约[11]。
过去,价格昂贵一直是影响用户广泛接受PCD刀具的一个主要障碍,但现在情况发生了很大变化。
业界估计,在过去的两三年中,PCD刀具的价格已下降了40%~60%。
出现PCD刀具价格“跳水”的原因之一是市场供大于求。
在20世纪90年代初,PCD刀具的发展势头开始超过传统的硬质合金刀具,在随后的十年中,对PCD刀具的市场需求不断增加。
但是,随着PCD刀具制造技术的成熟,其销售增长势头开始减缓,目前整个制造业的不景气对PCD刀具市场也有一定影响。
此外,新进入PCD刀具制造业的竞争者也动摇了原有的市场价格体系。
PCD刀具价格下降的另一个原因是刀具制造成本不断降低,刀具制造工艺(如用于金刚石毛坯粗加工的EDM工艺、切削刃精密加工工艺等)不断改进。
此外,与十年前相比,加工PCD刀具用的金刚石砂轮质量显著提高,成本则大大下降[12]。
近来,采用PCD刀尖的多功能旋转刀具的开发与应用日渐增多。
这种刀具可在一次走刀中完成钻孔、扩孔、倒角、精修等多道孔加工工序,用于汽车制造业可有效降低加工成本,如一把多功能PCD刀具在需要重磨前可加工多达几千件汽车传动箱零件。
随着PCD刀具切削性能的不断提高和PCD刀具价格的不断下降,PCD刀具对于广大用户具有了前所未有的吸引力,这将有力推动PCD刀具的普及应用以及PCD刀具技术更快地向前发展。
致谢
在此,特别感谢我的导师王永国老师在这学期为我们授课,带我们进入刀具这个行业,让我对刀具有了一个更加系统的认识。
同时感谢在一起度过一个学期的同学们,同学们精心准备的PPT和王老师的讲解点评,使我对制造工艺与刀具有了一个更加深入的了解。
最后,感谢老师在百忙之中评阅论文。
参考文献:
[1]金属加工刀具及其应用/王永国编著.北京:
机械工业出版社,2011.9
[2]韩荣第,于启勋.难加工材料切削加工.北京:
机械工业出版社.1996
[3]王运炎.金属材料与热处理.北京:
机械工业出版社.2000
[4]司马琼.金属切削原理及实用.湖南:
湖南科学技术出版社.1998
[5]肖诗纲.刀具材料及其合理选择[M].第2版.北京:
机械工业出版社,1990:
13-14.
[6]V.J.Tennery,C.S.Yust,G.W.Clark.Structure-propertycorrelationsforTiB2-basedceramicsdensifiedusingactiveliquidmetals[J].InScienceofHardMaterials.NewYork;Plenum,1983;891-909.
[7]刘战强,艾兴.高速切削刀具的发展现状[J].工具技术.2001,35(3):
3-8.
[8]于启勋,张京英.项代新型刀具材料新发展[J].磨料磨具通讯,2008,10(6):
13-18
[9]J.Karch,R.Birringer,H.Gleiter.Ceramicsductileatlowtemperature[J].Nature.1987,330(6148):
556-558.
[10]肖诗纲.刀具材料及其合理选择[M].第2版.北京:
机械工业出版社,1990:
13-14.
[11]PCD刀具在非金属切削加工中的应用.成都刀具研究所.
[12]机械工程材料/王章忠主编.北京:
机械工业出版社,2007.1