减速器输出轴的设计及加工制造.docx
《减速器输出轴的设计及加工制造.docx》由会员分享,可在线阅读,更多相关《减速器输出轴的设计及加工制造.docx(8页珍藏版)》请在冰豆网上搜索。
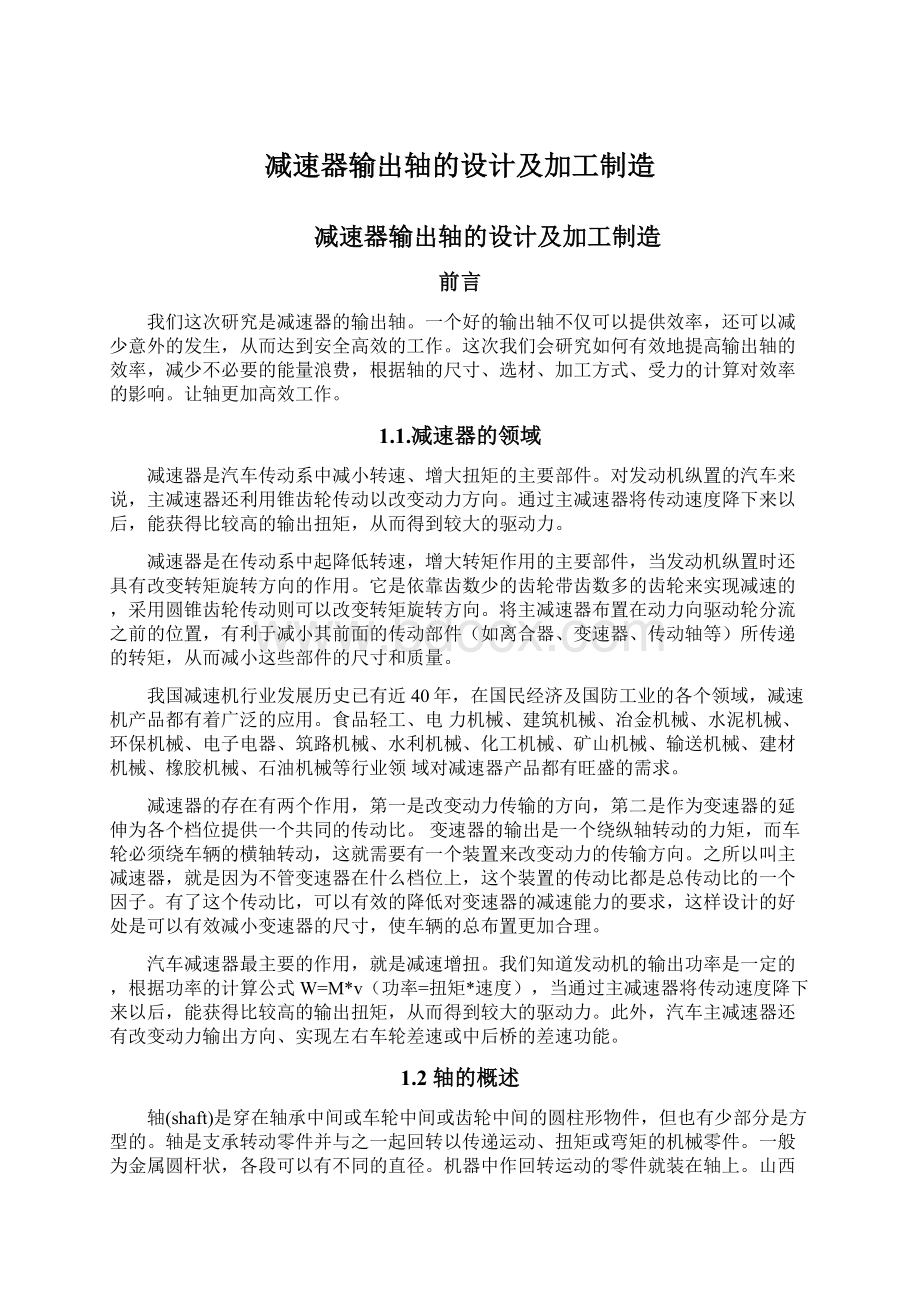
减速器输出轴的设计及加工制造
减速器输出轴的设计及加工制造
前言
我们这次研究是减速器的输出轴。
一个好的输出轴不仅可以提供效率,还可以减少意外的发生,从而达到安全高效的工作。
这次我们会研究如何有效地提高输出轴的效率,减少不必要的能量浪费,根据轴的尺寸、选材、加工方式、受力的计算对效率的影响。
让轴更加高效工作。
1.1.减速器的领域
减速器是汽车传动系中减小转速、增大扭矩的主要部件。
对发动机纵置的汽车来说,主减速器还利用锥齿轮传动以改变动力方向。
通过主减速器将传动速度降下来以后,能获得比较高的输出扭矩,从而得到较大的驱动力。
减速器是在传动系中起降低转速,增大转矩作用的主要部件,当发动机纵置时还具有改变转矩旋转方向的作用。
它是依靠齿数少的齿轮带齿数多的齿轮来实现减速的,采用圆锥齿轮传动则可以改变转矩旋转方向。
将主减速器布置在动力向驱动轮分流之前的位置,有利于减小其前面的传动部件(如离合器、变速器、传动轴等)所传递的转矩,从而减小这些部件的尺寸和质量。
我国减速机行业发展历史已有近40年,在国民经济及国防工业的各个领域,减速机产品都有着广泛的应用。
食品轻工、电力机械、建筑机械、冶金机械、水泥机械、环保机械、电子电器、筑路机械、水利机械、化工机械、矿山机械、输送机械、建材机械、橡胶机械、石油机械等行业领域对减速器产品都有旺盛的需求。
减速器的存在有两个作用,第一是改变动力传输的方向,第二是作为变速器的延伸为各个档位提供一个共同的传动比。
变速器的输出是一个绕纵轴转动的力矩,而车轮必须绕车辆的横轴转动,这就需要有一个装置来改变动力的传输方向。
之所以叫主减速器,就是因为不管变速器在什么档位上,这个装置的传动比都是总传动比的一个因子。
有了这个传动比,可以有效的降低对变速器的减速能力的要求,这样设计的好处是可以有效减小变速器的尺寸,使车辆的总布置更加合理。
汽车减速器最主要的作用,就是减速增扭。
我们知道发动机的输出功率是一定的,根据功率的计算公式W=M*v(功率=扭矩*速度),当通过主减速器将传动速度降下来以后,能获得比较高的输出扭矩,从而得到较大的驱动力。
此外,汽车主减速器还有改变动力输出方向、实现左右车轮差速或中后桥的差速功能。
1.2轴的概述
轴(shaft)是穿在轴承中间或车轮中间或齿轮中间的圆柱形物件,但也有少部分是方型的。
轴是支承转动零件并与之一起回转以传递运动、扭矩或弯矩的机械零件。
一般为金属圆杆状,各段可以有不同的直径。
机器中作回转运动的零件就装在轴上。
山西双环重型机械有限公司专业生产碳钢、合金钢、不锈钢等材质的大型环件、锻件、风力发电机组的基础环法兰和塔筒连接法兰等,并自主研发重型锻造机械设备的大型企业。
轴的结构设计是确定轴的合理外形和全部结构尺寸,为轴设计的重要步骤。
它由轴上安装零件类型、尺寸及其位置、零件的固定方式,载荷的性质、方向、大小及分布情况,轴承的类型与尺寸,轴的毛坯、制造和装配工艺、安装及运输,对轴的变形等因素有关。
设计者可根据轴的具体要求进行设计,必要时可做几个方案进行比较,以便选出最佳设计方案,以下是一般轴结构设计原则:
1、节约材料,减轻重量,尽量采用等强度外形尺寸或大的截面系数的截面形状;
2、易于轴上零件精确定位、稳固、装配、拆卸和调整;
3、采用各种减少应力集中和提高强度的结构措施;
4、便于加工制造和保证精度。
扭转刚度:
轴的扭转刚度校核是计算的轴的工作时扭转变形量,是用每米轴长的扭角度量的。
轴的扭转变形要影响机器的性能和工作精度,如内燃机凸轮轴的扭转角过大,会影响气门的正确启闭时间;龙门式起重机运动机构传动轴的扭转角会影响驱动轮的同步性;对有发生扭转振动危险的轴以及操纵系统中的轴,都需要有较大的扭转刚度。
磨损原因:
轴类磨损是轴使用过程中最为常见的设备问题。
轴类出现磨损的原因有很多,但是最主要的原因就是用来制造轴的金属特性决定的,金属虽然硬度高,但是退让性差(变形后无法复原轴),抗冲击性能较差,抗疲劳性能差,因此容易造成粘着磨损、磨料磨损、疲劳磨损、微动磨损等,大部分的轴类磨损不易察觉,只有出现机器高温、跳动幅度大、异响等情况时,才会引起人们的察觉,但是到人们发觉时,大部分轴都已磨损,从而造成机器停机。
1.3轴的材料
主要承受弯矩和扭矩。
轴的失效形式是疲劳断裂,应具有足够的强度、韧性和耐磨性。
轴的材料从以下中选取:
1.3.1合金钢
合金钢具有较高的机械性能,对应力集中比较敏感,淬火性较好,热处理变形小,价格较贵。
多使用于要求重量轻和轴颈耐磨性的轴。
例如:
汽轮发电机轴要求,在高速、高温重载下工作,采用27Cr2Mo1V、38CrMoAlA等。
滑动轴承的高速轴,采用20Cr、20CrMnTi等。
1.3.2球墨铸铁
球墨铸铁吸振性和耐磨性好,对应力集中敏感低,价格低廉,使用铸造制成外形复杂的轴。
例如:
内燃机中的曲轴。
1.3.3碳素钢
优质碳素钢具有较好的机械性能,对应力集中敏感性较低,价格便宜,应用广泛。
例如:
35、45、50等优质碳素钢。
一般轴采用45钢,经过调质或正火处理;有耐磨性要求的轴段,应进行表面淬火及低温回火处理 。
轻载或不重要的轴,使用普通碳素钢Q235、Q275等。
2轴的尺寸
2.1最小轴径的计算
解:
计算轴的最小直径,选取联轴器
安装联轴器的轴段只受扭矩,直径最小,根据推荐,
选轴材为45号钢调质(表14-2),取C=107,于是:
考虑到轴上有键槽而且有可能是双键,每键增大直径
约3%,实取
=55mm。
选取联轴器:
考虑到带式运输机通常要带载启动,
对空间尺寸无严格要求,查手册选用弹性套柱销联轴器T
型,根据
=953250Nmm,选用TL9型联轴器。
主动端:
J型轴孔,C型键槽,
=55,L=84;
从动端:
Y型孔,C型键槽,
=55,L=112。
标记为:
TL9联轴器
GB4323-84。
2.2轴的各段直径和长度确定
零件在轴上的定位和装拆方案确定后,轴的形状便大体确定。
各轴段所需的直径与轴上的载荷大小有关。
初步确定轴的直径时,通常还不知道支反力的作用点,不能决定弯矩的大小与分布情况,因而还不能按轴所受的具体载荷及其引起的应力来确定轴的直径。
但在进行轴的结构前,通常已能求得轴所受的扭矩。
因此,可按轴所受的扭矩初步估算轴所需的直径。
将初步求出的直径作为承受扭矩的轴段的最小直径dmin,然后再按轴上零件的装配方案和定位要求,从dmin处起逐一确定各段轴的直径。
在实际设计中,轴的直径亦可凭设计者的经验取定,或参考同类机械用类比的方法确定。
有配合要求的轴段,应尽量采用标准直径。
安装标准件(如滚动轴承、联轴器、密封圈等)部位的轴径,应取为相应的标准值及所选配合的公差。
为了使齿轮、轴承等有配合要求的零件装拆方便,并减少配合表面的擦伤,在配合轴段前应采用较小的直径。
为了使与轴作过盈配合的零件易于装配,相配轴段的压入端应制出锥度;或在同一轴段的两个部位上采用不同的尺寸公差。
确定各轴段长度时,应尽可能使结构紧凑,同时还要保证零件所需的装配或调整空间。
轴的各段长度主要是根据各零件与轴配合部分的轴向尺寸和相邻零件间必要的空隙来确定的。
为了保证轴向定位可靠,与齿轮和联轴器等零件相配合部分的轴段长度一般应比轮毂长度短2~3mm。
3轴的结构工艺性
3.1制阶梯轴
对于只受转矩的传动轴,为了使各轴段剖面上的切应力大小相等,常制成光轴或接近光轴的形状;对于受交变弯曲载荷的轴,考虑到中间处应力大且便于零件的装拆,一般制成中间大、两头小的阶梯轴。
所有键槽应沿轴的同一母线布置,以方便加工,降低加工成本。
3.2提高轴的疲劳强度
在直径突变处应平缓过渡,制成的圆角半径尽可能取得大些。
还可采用减载槽、中间环或凹切圆角等结构来减少应力集中。
3.3工艺设计轴的结构
当某一轴段需车制螺纹或磨削加工时,应留有退刀槽或砂轮越程槽;为了磨削轴的外圆,在轴的端部应制有定位中心孔;对于过盈联接,其轴头要制成引导装配的锥度。
3.4设置轴上零件
改变轴上零件的布置,有时可使轴上得载荷减小。
轴上作用的最大转矩为T1+T2,如果输入轮布置在两输出轮之间,则轴上所受的最大转矩将由(T1+T2)降低至T1。
3.5改进轴上零件
改进轴上零件的结构也可以减小轴上的载荷。
卷筒的轮毂很长,轴的弯曲力矩较大,如把轮毂分成两段,则就减少了轴的弯矩,从而提高了轴的强度和刚度,同时还能得到更好的轴孔配合。
4选择减速箱输出轴的加工方法,制定工艺路线
工艺设计是指用机械加工的方法改变毛坯的形状、尺寸、相对位置和性质使其成为合格零件的全过程,加工工艺是工人进行加工的一个依据。
拟订工艺路线是设计工艺规程最为关键的一步,需顺序完成以下几个方面的工作。
1、选择定位基准精基准的选择原则
基准重合原则
应尽可能选择被加工表面的设计基准为精基准,这样可以避免由于基准不重合引起的定位误差。
统一基准原则
应尽可能选择用同一组精基准加工工件上尽可能多的加工表面,以保证各加工表面之间的相对位置关系。
例如,加工轴类零件时,一般都采用两个顶尖孔作为统一精基准来加工轴类零件上的所有外圆表面和端面,这样可以保证各外圆表面间的同轴度和端面对轴心线的垂直度。
互为基准原则
当工件上两个加工表面之间的位置精度要求比较高时,可以采用两个加工表面互为基准反复加工的方法。
例如,车床主轴前后支承轴颈与主轴锥孔间有严格的同轴度要求,常先以主轴锥孔为基准磨主轴前、后支承轴颈表面,然后再以前、后支承轴颈表面为基准磨主轴锥孔,最后达到图纸上规定的同轴度要求。
自为基准原则
一些表面的精加工工序,要求加工余量小而均匀,常以加工表面自身为基准图示为在导轨磨床上磨床身导轨表面,被加工床身1通过楔铁2支承在工作台上,纵向移动工作台时,轻压在被加工导轨面上的百分表指针便给出了被加工导轨面相对于机床导轨的不平行度读数,根据此读数操作工人调整工件1底部的4个楔铁,直至工作台带动工件纵向移动时百分表指针基本不动为止,然后将工件1夹紧在工作台上进行磨削。
粗基准的选择原则保证零件加工表面相对于不加工表面具有一定位置精度的原则被加工零件上如有不加工表面应选不加工面作粗基准,这样可以保证不加工表面相对于加工表面具有较为精确的相对位置,表面为不加工表面,为保证镗孔后零件的壁厚均匀,应选表面作粗基准镗孔、车外圆、车端面。
当零件上有几个不加工表面时,应选择与加工面相对位置精度要求较高的不加工表面作粗基准。
合理分配加工余量的原则
从保证重要表面加工余量均匀考虑,应选择重要表面作粗基准。
在床身零件中,导轨面是最重要的表面,它不仅精度要求高,而且要求导轨面具有均匀的金相组织和较高的耐磨性。
由于在铸造床身时,导轨面是倒扣在砂箱的最底部浇铸成型的,导轨面材料质地致密,砂眼、气孔相对较少,因此要求加工床身时,导轨面的实际切除量要尽可能地小而均匀,故应选导轨面作粗基准加工床身底面,然后再以加工过的床身底面作精基准加工导轨面,此时从导轨面上去除的加工余量可较小而均匀。
床身加工粗基准选择
便于装夹的原则
为使工件定位稳定,夹紧可靠,要求所选用的粗基准尽可能平整、光洁,不允许有锻造飞边、铸造浇冒口切痕或其它缺陷,并有足够的支承面积。
粗基准一般不得重复使用的原则
在同一尺寸方向上粗基准通常只允许使用一次,这是因为粗基准一般都很粗糙,重复使用同一粗基准所加工的两组表面之间位置误差会相当大,因此,粗基一般不得重复使用。
2、表面加工方法的选择
在选择加工方法时,首先根据零件主要表面的技术要求和工厂具体条件,先选定它的最终工序方法,然后再逐一选定该表面各有关前导工序的加工方法。
同一种表面可以选用各种不同的加工方法加工,但每种加工方法所能获得的加工质量、加工时间和所花费的费用却是各不相同的,工程技术人员的任务,就是要根据具体加工条件(生产类型、设备状况、工人的技术水平等)选用最适当的加工方法,加工出合乎图纸要求的机器零件。
具有一定技术要求的加工表面,一般都不是只通过一次加工就能达到图纸要求的,对于精密零件的主要表面,往往要通过多次加工才能逐步达到加工质量要求。
例如,加工一个精度等级为IT6、表面粗糙度Ra为0.2μm的钢质外圆表面,其最终工序选用精磨,则其前导工序可分别选为粗车、半精车和粗磨。
主要表面的加工方案和加工工序选定之后,再选定次要表面的加工方案和加工工序。
3、加工阶段的划分
粗加工阶段将零件的加工过程划分为加工阶段的主要目的是:
(1)保证零件加工质量;
(2)有利于及早发现毛坯缺陷并得到及时处理;
(3)有利于合理利用机床设备。
此外,将工件加工划分为几个阶段,还有利于保护精加工过的表面少受磕碰损坏。
半精加工阶段
精加工阶段
光整加工阶段
工序的集中与分散工序集中原则按工序集中原则组织工艺过程,就是使每个工序所包括的加工内容尽量多些,将许多工序组成一个集中工序,最大限度的工序集中,就是在一个工序内完成工件所有表面的加工。
传统的流水线、自动线生产基本是按工序分散原则组织工艺过程的,这种组织方式可以实现高生产率生产,但对产品改型的适应性较差,转产比较困难。
工序分散原则按工序分散原则组织工艺过程,就是使每个工序所包括的加工内容尽量少些,最大限度的工序分散就是每个工序只包括一个简单工步。
采用数控机床、加工中心按工序集中原则组织工艺过程,生产适应性反而好,转产相对容易,虽然设备的一次性投资较高,但由于有足够的柔性,仍然受到愈来愈多的重视。
工序顺序的安排机械加工工序的安排先加工定位基准面,再加工其它表面.
先加工主要表面,后加工次要表面
先安排粗加工工序,后安排精加工工序
先加工平面,后加工孔。
5加速器输出轴