机油泵传动轴支架说明书.docx
《机油泵传动轴支架说明书.docx》由会员分享,可在线阅读,更多相关《机油泵传动轴支架说明书.docx(20页珍藏版)》请在冰豆网上搜索。
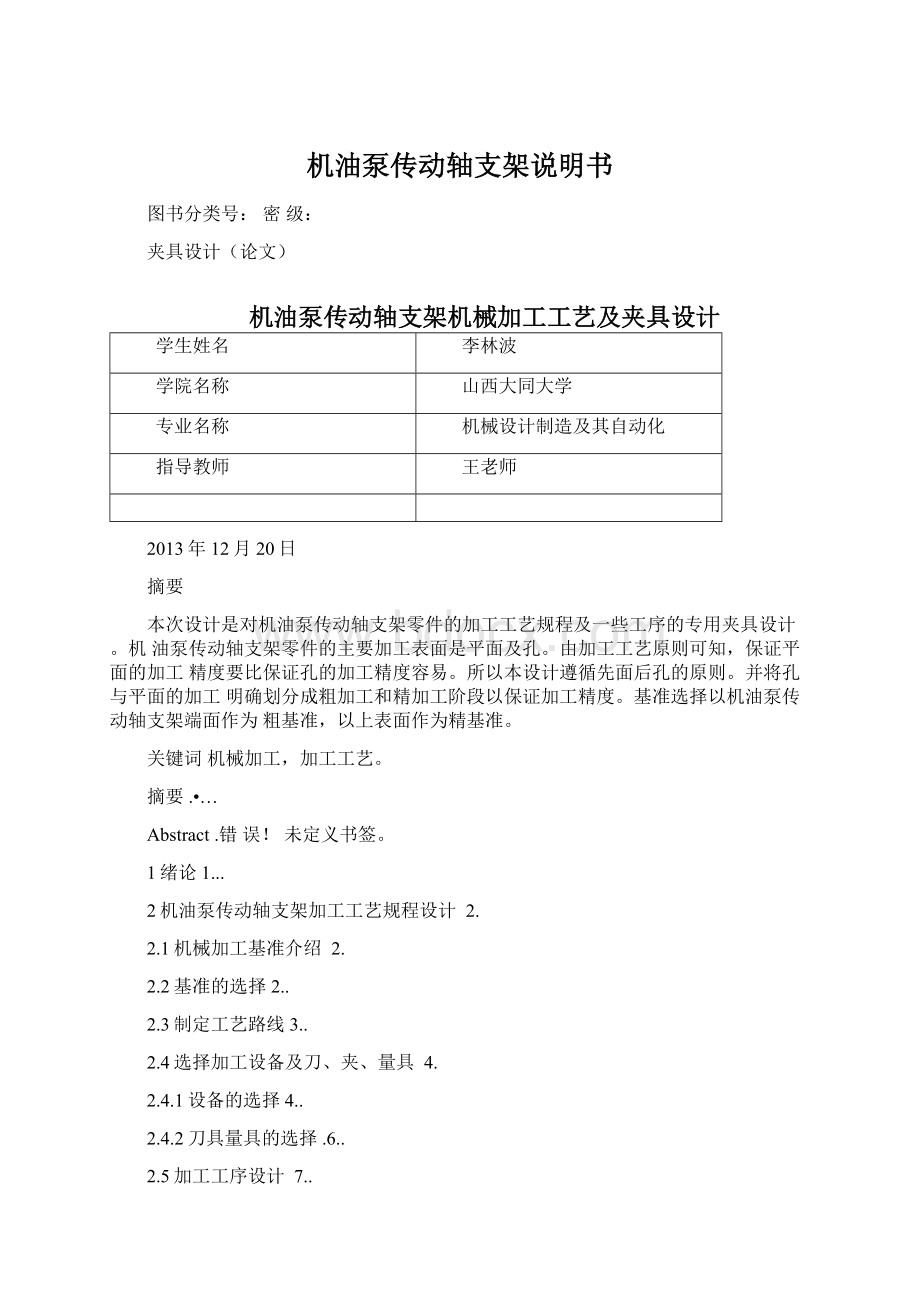
机油泵传动轴支架说明书
图书分类号:
密级:
夹具设计(论文)
机油泵传动轴支架机械加工工艺及夹具设计
学生姓名
李林波
学院名称
山西大同大学
专业名称
机械设计制造及其自动化
指导教师
王老师
2013年12月20日
摘要
本次设计是对机油泵传动轴支架零件的加工工艺规程及一些工序的专用夹具设计。
机油泵传动轴支架零件的主要加工表面是平面及孔。
由加工工艺原则可知,保证平面的加工精度要比保证孔的加工精度容易。
所以本设计遵循先面后孔的原则。
并将孔与平面的加工明确划分成粗加工和精加工阶段以保证加工精度。
基准选择以机油泵传动轴支架端面作为粗基准,以上表面作为精基准。
关键词机械加工,加工工艺。
摘要.•…
Abstract.错误!
未定义书签。
1绪论1...
2机油泵传动轴支架加工工艺规程设计2.
2.1机械加工基准介绍2.
2.2基准的选择2..
2.3制定工艺路线3..
2.4选择加工设备及刀、夹、量具4.
2.4.1设备的选择4..
2.4.2刀具量具的选择.6..
2.5加工工序设计7..
3夹具设计1.Q
3.1定位方案的选定11
3.2夹具夹紧装置的确定11
3.2.1夹紧力的方向和作用点的确定11
3.2.2夹紧力大小的估算1.2
3.3夹紧机构及元件的选择1.3
3.4夹具体上排屑措施的确定15
3.5钻模的设计15
3.5.1钻套的选定.15
3.5.2钻模板的设计16
4夹具定位方案的分析18
4.1工件定位自由度分析1.8
4.2工件定位精度分析19
参考文献21
致谢22
1绪论
对工件进行机械加工时,为了保证加工要求,首先要使工件相对于机床有正确的位置,并使这个位置在加工过程中不因外力的影响而变动。
为此,在进行机械加工前,先要将工件装夹好。
用夹具装夹工件时,工件相对于道具及机床的位置精度由夹具保证,不受工人技术水平的影响,使一批工件的加工极度趋于一致,稳定的保证工件的加工精度。
同时使用夹具装夹工件方便、快捷,工件不需要划线找正,可显著的减少辅助工时,提高劳动生产率;工件在夹具中装夹后提高了工件的刚性,因此可加大切屑用量,提高劳动生产率;可使用多件、多工位装夹工件的夹具,并可采用高效夹紧机构,进一步提高劳动生产率。
在批量生产中使用夹具后,由于劳动生产率的提高、使用技术等级较低的工人以及废品率下降等原因,明显得降低了生产成本。
夹具制造成本分摊在一批工件上。
每个工件增加的成本时极少的,远远小于由于提高劳动生产率而降低的成本。
工件批量愈大,使用夹具所取得的经济效益就愈显著。
2机油泵传动轴支架加工工艺规程设计
2.1机械加工基准介绍
基准:
基准是用来确定生产对象上几何要素的几何关系所依据的那些点、线、面。
基准根据其功用的不同可分别为设计基准和工艺基准。
在工件工序图中,用来确定本工序加工表面位置的基准,加工表面与工序基准之间一般有两次核对位置要求:
一是加工表面对工序基准的距离要求,即工序尺寸要求;另一次是加工表面对工序基准的形状位置要求,如平行度,垂直度等。
所以工件定位时,用以确定工件在夹具中位置的表面(或点,线)称为定位基准,定位基准的选择,一般应本着基准重合原则,尽可能选用工序基准作为定位基准,工件在定位时,每个工件的夹具中的位置是不确定的,一般是限制工件的六个自由度,分别是指:
沿三坐标轴的移动自由度,和绕三坐标轴转动的自由度。
基面的选择是工艺规程设计的重要工作之一,基面选择正确合理,可以使加工质量的到保证,减轻劳动强度,生产效率得到提高。
否则,会使加工困难,甚至造成加工零件报废。
2.2基准的选择
(1)粗基准的选择
粗基准选择原则:
选择粗基准,主要是选择第一道机械加工工序的定位基准,以便为后续工序提供精基准。
为了方便地加工出精基准,使精基准面获得所需加工精度,选择粗基准,以便于工件的准确定位。
选择粗基准的的出发点是:
一要考虑如何合理分配各加工表面的余量;二要考虑怎么样保证不加工表面与加工表面间的尺寸及相互位置要求,一般应按下列原则来选择:
1)若工件必须首先保证某重要表面的加工余量均匀,则应优先选择该表面为粗基准。
2)若工件每个表面都有加工要求,为了保证各表面都有足够的加工余量,应选择加工量最少的表面为粗基准。
3)若工件必须保证某个加工表面与加工表面之间的尺寸或位置要求,则应选择某个加工面为粗基准。
4)选择基准的表面应尽可能平整,没有铸造飞边,浇口,冒口或其他缺陷。
粗基准一般只允许使用一次。
基于上述的要求和考虑到安装装配面的精度要求和便于夹紧等实际情况,粗基准选用前机体内一个较大的非加工面在毛坯图上已经标出。
(2)精基准的选择
精基准选择原则:
选择精基准时,应从整个工艺过程来考虑如何保证工件的尺寸精度和位置精度,并要达到使用起来方便可靠。
一般应按下列原则来选择:
1)基准重合原则;应选择设计基准作为定位基准。
2)基准统一原则;应尽可能在多数工序中选用一组统一的定位基准来加工其他各表面,采用统一基准原则可以避免基准转换过程所产生的误差,并可使各工序所使用的夹具结构相同或相似,从而简化夹具的设计和制造。
3)自为基准原则;有些精加工或光整加工工序要求加工余量小而均匀,应选择加工表
面本身来作为定位基准。
4)互为基准原则;对于相互位置精度要求高的表面,可以采用互为基准,反复加工的方法。
5)可靠,方便原则;应选择定位可靠,装夹方便的表面作为精基准。
本零件是铸造件,要用毛坯面定位先加工出一个精基准。
然后以精基准定位,加工零件。
精基准放在工序最前面加工。
以上表面毛坯面定位。
详见工艺卡片。
2.3制定工艺路线
(1)热处理工序的安排
加工工艺安排热处理,因为零件精度要求较高HT200要铸造完成要进行时效处理,防止工件变形。
(2)定位基准的选择
粗基准选择下表面,则由非加工面为定位基准,铣精基准。
精基为上表面,则加工时稳定性差一些,加工精度就受到了影响,角向定位也是这样。
因此,拟订工艺路线方案如下:
工序1:
清沙,去除非加工表面铸造积瘤
工序2:
时效处理,去除内应力
工序3:
毛毛坯面定位,铣上表面,保证尺寸12及72.3+0.1/0
工序4:
钻2-?
8H7(+0.015/0)沉孔①10x90°及3-?
11孔
工序5:
以底面为基准,粗镗?
32孔至?
31.5
工序6:
以底面为基准,精镗?
31孔至32H7(+0.015/0)
工序7:
以底面为基准,铣端面,保证30°及11尺寸,工件总长度250
工序8:
检验
工序9:
入库
2.4选择加工设备及刀、夹、量具
由于生产类型为大批量生产,加工设备易以通用机床为主,配以专用夹具,工件在各机床上的装卸及各机床间的传送均由人工完成。
2.4.1设备的选择
1)摇臂钻床Z3040X16主要参数:
最大钻孔孔直径40mm
主轴中心线至立柱母线距离最大1600mm
最小350mm
主轴端面至底座工作面距离最大1250mm
最小350mm
主轴行程315mm
主轴锥孔(莫氏)4#No.
主轴轴转速范围25-2000r/min
主轴转速级数16
主轴进给量范围0.04-3.20mm/r
主轴进给级数16
工作台尺寸500X630mm
主轴箱水平移动距离1250mm
主电机功率3kw
机床重量3500kg
机床外型尺寸(长X宽X高)2500X1070X2840mm
2)立式铣床X52K主要参数:
单位/X52K
工作面积宽*长mm320*1250
承载重量kg500
T型槽数目个3
T型槽宽度mm18
T型槽间距mm70
X向(工作台纵向)手动/机动mm700/680
丫向(滑座横向)手动/机动mm255/240
Z向(升降台垂向)手动/机动mm370/350
最大回转角度deg±45
转速r/min30-1500
转速级数Step18
锥孔.ISO7:
24NO.50
轴向移动距离mm85
主轴端面至工作台距离最小/最大mm45/415
主轴中心线至床身垂直导轨面距离mm350
切削进给速度mm/minX,Y:
23.5-1180,Z:
8-394快速移动进给速度mm/minXY:
2300,Z:
770进给级数Step18
主轴电机功率KW7.5
进给电机功率KW1.5
机床外形尺寸(长*宽*高)mm2272*1770*2094
机床净重(约)kg2800
4)立式钻床Z5140主要参数:
工作台尺寸(长X宽)mm450X500
工作台行程mm300
主轴中心线至导轨面距离mm335
主轴端面至工作台面距离mm0-750
主电机功率kw3.0
最大钻孔直径mm40
最大送刀抗力N16000
主轴最大输送扭矩N.m350
主轴孔锥度Morse4
主轴变速级数级12
主轴变速范围r/min31.5-1400
主轴行程mm250
主轴箱行程mm200
送刀级数级9
送刀范围mm/r0.056-1.80
外形尺寸(长X宽X高)mm1080X810X2510
机床重量kg2000
2.4.2刀具量具的选择
依据〈〈金属机械加工工艺人员手册〉〉所选量具公布如下:
测量范围为:
0〜100的深度规
深度规用于精确测量凹台和沟槽深度。
塞规具有独特的导向圆柱体设计,方便、快、准。
适用于现场测量。
测量范围为10〜30的内槽卡钳
内槽卡钳适用于测量各种筒形工件、管材内径以及凹槽尺寸。
2.5加工工序设计
1.铣上表面,保证尺寸12及72.3
查参考文献[3]表2.3-59,得平面加工余量为0.9mm已知A面总余量为2mm故粗加工余量=4-0.9=3.1mm。
查参考文献[3]表2.4-73,取粗铣的每齿进给量为fz=°.2mmz,取精度铣的每转进
给量?
=0.5mm/r,粗铣走刀1次,ap=3.5mm精铣走刀1次,ap=1.5mm
查参考文献[3]表3.1-74,取粗铣的主轴转速为150^'min,取精铣的主轴转速为300r/min。
又前面已选定铣刀直径D为u40mm故相应的切削速度为:
nDn3.14X40X150.
V粗===18.84mmin
粗10001000
nDn3.14X40X300?
V蛀二==37.68mmin
精10001000
校核机床功率(只校核粗加工工序):
切削功率爲为:
R
-50.90.74
n=167.9X10apfzaeZnkpm
取z=10个齿,则
代入式中得:
Pm=167.9x10-5x3.50.9xa2。
74x168X10X2.5X1=6.62kw
由文献[3]表3.1-73得机床功率为7.5kw,取效率为0.85,则7.5X
0.85=6.375kw<6.62kw
故重新选择主轴转速为118rmin,贝U:
nDn3.14X40X118.
Vrn===14.8m.min
粗10001000
118
带入Pm公式得:
Pm=167X10-5X3.50.9X0.20"X168X10X60X1〜
5.2kw<6.375kw
故机床功率足够。
2.钻2-?
8H7(+0.015/0)
因U8孔不是一次钻出,故其钻削余量为2钻=11/2=5.5mmu8孔的精度较高,要分
2次加工。
参考文献[3]表2.4-41,用插入法求得钻u8孔的切削速度v=0-445ms=26-7mmin,
由此算出转速为:
n=1000v/nd=1000X26.7/3.14X11=773^min
按机床实际转速取n=630rmin,则实际切削速度为:
v=3.14X11X630/1000=21.76m.min
参考文献[3]表2.4-69,得:
Ff=9.81X42.7d。
f(N)
M=9.81X0.021d0f%(Nm)
分别求出钻u8孔Ff和M如下:
F0.8
Ff=9.81X42.7X11X0.4x仁2427N
20.8
M=9.81X0.021X11X0.4x1=15.63Nm
它们均小于机床的最大进给力7840N和机床的最大扭转力矩196Nm故机床刚度足够。
3.以底面为基准,粗镗?
32孔至?
31.5
取粗镗的每齿进给量为fZ=0.2mm,z,,粗镗走刀1次,ap=3.5mm
查参考文献[3]表3.1-74,取粗镗的主轴转速为150^min。
又前面已选定镗刀直径D为u19mm故相应的切削速度为:
nDn3.14X35X150/
V粗===16.485mmin
粗10001000
4.以底面为基准,精镗?
31孔至32H7(+0.015/0)
取精镗的每齿进给量为fZ=0.1mm「z,,粗镗走刀1次,aP=1.5mm
查参考文献[3]表3.1-74,取精镗的主轴转速为500nmin。
又前面已选定镗刀直径D
为u19mm故相应的切削速度为:
nDn3.14X=251900}
V精===8.485m.min
精100017700
f=0.7mm/r,贝Uv=25.4m/min
10°°v100QX25.4n=nd=3.14X13=622.2”min
按机床实际转速取n=650rmin
则实际切削速度为:
v=3.14X13X650/1000=26.53mmin
参考文献[3]表2.4-41,得:
Ff=98.1X42.7d。
f°8kF(N)
d2f0.8
M=9.81X0.021d0fkM(Nm)
分别求出11的Ff和M如下:
F0.8
厂f=98.1X42.7X13X0.4x仁2616N
20.8
M=9.81X0.021X13X0.4x1=16.73Nm
它们均小于机床的最大进给力7840N和机床的最大扭转力矩196Nm故机床刚度足够
3夹具设计
对工件进行机械加工时,为了保证加工要求,首先要使工件相对于机床有正确的位置,并使这个位置在加工过程中不因外力的影响而变动。
为此,在进行机械加工前,先要将工件装夹好。
用夹具装夹工件有下列优点:
1)能稳定的保证工件的加工精度用夹具装夹工件时,工件相对于道具及机床的位
置精度由夹具保证,不受工人技术水平的影响,使一批工件的加工极度趋于一致。
2)能提高劳动生产率使用夹具装夹工件方便、快捷,工件不需要划线找正,可显著的减少辅助工时,提高劳动生产率;工件在夹具中装夹后提高了工件的刚性,因此可加大切屑用量,提高劳动生产率;可使用多件、多工位装夹工件的夹具,并可采用高效夹紧机构,进一步提高劳动生产率。
3)能扩大机床的使用范围
4)能降低成本在批量生产中使用夹具后,由于劳动生产率的提高、使用技术等级较低的工人以及废品率下降等原因,明显得降低了生产成本。
夹具制造成本分摊在一批工件上。
每个工件增加的成本时极少的,远远小于由于提高劳动生产率而降低的成本。
工件批量愈大,使用夹具所取得的经济效益就愈显著。
夹具上的各种装置和元件通过夹具体连接成一个整体。
因此,夹具体的形状及尺寸取决于夹具上各种装置的布置及夹具于机床的连接。
对于夹具体有以下几点要求:
1)有适当的精度和尺寸稳定性夹具体上的重要表面,应有适当的尺寸和形状精
度,它们之间应有适当的位置精度。
2)有足够的强度和刚度加工过程中,夹具体要承受较大的切屑力和夹紧力。
为保
证夹具体不产生不允许的变形和震动,夹具体应有足够的强度和刚度。
3)结构工艺性好夹具体应便于制造、装配和检验。
铸造夹具体上安装各种元件的
表面应铸出凸台,以减少加工面积。
夹具体结构形式应便于工件的装卸。
4)排屑方便切屑多时,夹具体上应考虑排屑结构。
5)在机床上安装稳定可靠夹具在机床上的安装都是通过夹具体上的安装基面与机床上相应表面的接触或配合实现的。
当夹具在机床工作台上安装时,夹具的重心应尽量低,重心越高则支撑面应越大;夹具底面四边应凸台,使夹具体的安装基面与机床的工作台面接触良好。
3.1定位方案的选定
该零件的定位方案我选择的是一孔一面定位方式。
这种定位方式在箱体、杠杆、盖板等类零件的加工中用的很广。
工件的定位面一般是加工过的精基面,定位方式如下图:
3.2夹具夹紧装置的确定
3.2.1夹紧力的方向和作用点的确定
(1)夹紧力的方向,主要夹紧力的方向一般应垂直于主要定位基准,当夹紧力和切削力,
重力同方向时,需要的夹紧力最小;完全利用摩擦力来克服切削力和重力时,所需的夹紧力最大。
因此本设计的夹紧力方向应正好和重力方向平行。
(2)夹紧力的作用点,夹紧力的作用点应在支承点上,或在几个支承点所组成的平面内。
在多点夹紧时,如果平紧点在支承面之外,应采用联动夹紧机构,以保证各点的夹紧力同时均匀地作用到工件上。
夹紧力的作用点应选在工件刚性最好的部位,否则
应设置辅助支承,夹紧力的作用点应靠近切削部位。
(3)夹紧力的大小,夹紧力的大小应根据所需夹紧力最大时的加工位置来决定,并分析此时受力情况,然后进行计算。
为了安全应将计算值的安全系数(一般取2~3)作为
所需要的夹紧力。
322夹紧力大小的估算
力卩工过程中,工件受到切屑力、离心力、惯性力及重力的作用。
理论上,夹紧力的作用应与上述力的作用平衡;而实际上,夹紧力的大小还与工艺系统的刚性、夹紧机构的传递效率等有关。
而且,切削力的大小在加工过程中是变化的,因此,夹紧力的计算是个很复杂的问题,只能进行粗略的估算。
估算时应找出对夹紧最不利的瞬时状态,估算此状态下所需的夹紧力。
由《机床夹具设计手册》上提供的公式:
WK=W•
式中Wk--实际所需夹紧力(N);
W--在一定条件下,由静力平衡计算出的理论夹紧力(N;
K—安全系数。
安全系数K可按下式计算:
K二K。
©心K3K4心心
取K0=1.3K1=1.2K2=1.5
K3=1.0K4=1.3K5=1.0
©=1.0
贝UK=1.31.21.51.01.31.01.0
K=3.042
确定W:
根据《机床夹具设计手册》P32表1-2-3刀具材料为硬质合金
075
Pz=9O2ts0Kp;
Py=530t0.9s0.75Kp;
04Px=451ts.Kp;
式中,Pz――圆周切削分力(N);
Py――径向切削分力(N);
Px――轴向切削分力(N);
s--每转进给量(mr)
t—切削深度(mm;
Kp-KmpK^pKypKXpKTp
Kmp--考虑工件材料机械性能的系数;
©pKypKx卩心p--考虑刀具几何参数的系数。
查表1-2-4,得,Kmp=(HB)n
150
Kmp——考虑工件材料机械性能的系数;
KmpK「pK.pKpKrp——考虑刀具几何参数的系数;
计算Pz时,n取0.4;计算Py时,n取0.4;计算Px时,n取04计算Pz时,Kcpp=1.0,KYp=1.0,K^p=1.0,,Krp=1.0;
计算Py时,Kp=1.0,Kp=1.0,K.p=0.75,Krp=1.07;
计算Px时,K:
p=1.0,Kp=1.0,K■p=1.07,Krp=1.07;
算得:
取s=1mm,t=1mm
Pz=991.4(N)
Py=467(N)
Px=397.8(N)
夹紧力一般为估算,考虑X、丫方向的摩擦,所以在Z方向的力约为:
400(N)
由公式Wk二WK,算得所要的夹紧力为1216(N)
3.3夹紧机构及元件的选择
本零件夹紧采用螺旋夹紧机构,夹紧机构如图:
图4.3
采用的螺母为六角螺母(GB56-76
(1)材料:
45按《优质碳素结构钢钢号和一般技术条件》。
(2)热处理:
HRC3E40。
(3)细牙螺母的支承面对螺纹轴心线的垂直度按GB1184-8《形状和位置公差》附录一表3规定的9级公差。
(4)其他技术条件按GB2259-80《机床夹具零件及技术条件》。
螺母规格:
56-76-M12X1.5。
螺栓为活节螺栓,规格为:
M16X240或M16X220(GB798-76)。
根据《机械设计》上对紧螺栓联接的强度计算,有:
(Tea1.3(T
空355MPa订可
根据上述计算,此夹紧方案符合要求。
3.4夹具体上排屑措施的确定
切屑多时,夹具体上应考虑排屑结构。
排屑措施有两种:
1)
增加容纳排屑空间。
在夹具体上增设容屑沟或增大定位元件工作表面与夹具体之间的距离。
适用于加工时产生的切屑不多的场合。
如图4.7所示。
图4.7
2)采用切屑自动排除结构。
在夹具体上专门设计排屑用的斜面和缺口,使切屑自动由斜面处滑下而排至夹具体外。
a图是在夹具体上开出排屑用的斜弧面,使钻孔的切屑,沿斜弧面排出。
b图是在铣床夹具的夹具体内,设计排屑腔,切屑落入腔内后,沿斜面排出。
适用于切屑较多的场合。
3.5钻模的设计
3.5.1钻套的选定
钻模的导向元件是钻套,钻套用来引导刀具以保证被加工孔的位置精度和提高工艺系统的刚度,在加时可增强刀具刚性和防止偏斜。
钻套的结构尺寸已标准化,设计时可按工厂有关图册或参考有关夹具设计手册选用。
固定钻套(JB/T8045.1-1999),如图4.9。
钻套直接压入钻模板或夹具体上,其外圆与钻模板采用H7/n6或H7/r6配合。
磨损后不易更换。
适用于中、小批生产的钻模上或用来加工孔距甚小以及孔距精度要求较高的孔。
为了防止切屑进入钻套孔内,钻套的上、下端应稍突出钻模板为宜,一般不能低于钻模板。
带肩固定钻套主要用于钻模板铰薄时,用以保持必要的引导长度,也可做为主轴头进给时轴向定程挡块用。
通过两种固定钻套的对比,在加工j11孔时我选择了无肩式钻套。
具体尺寸以及公差
配合见图纸
图4.9
可换钻套(JB/T8045.2-1999),如图4.10。
钻套1装在衬套2中,而衬套则是压配在
夹具体或钻模板3中。
钻套由螺钉4固定。
以防止它转动。
钻套与衬套间采用F7/m6或F7/k6
图4.10
3.5.2钻模板的设计
钻模板用于安装钻套,并确保钻套在钻模上的正确位置。
经过对零件的分析和夹具的整体设计,我选择了可卸式钻模板。
在夹具体上为钻模板设有定位装置,以保持钻模板准确的位置精度。
钻孔精度较高。
可卸式钻模板具有以下特点如图4.11:
(1)适用于中批量生产中在钻孔后继续进行其它工序或大型工件的局部加工;
(2)它由两个定位套与夹具体上相对应的二个定位销(其中一个通常是菱形的)准确定位,并在结构上采取措施,防止钻模板装错方向;
(3)覆盖式可卸钻模板定位部分直接安装在工件的