焊条电弧焊.docx
《焊条电弧焊.docx》由会员分享,可在线阅读,更多相关《焊条电弧焊.docx(8页珍藏版)》请在冰豆网上搜索。
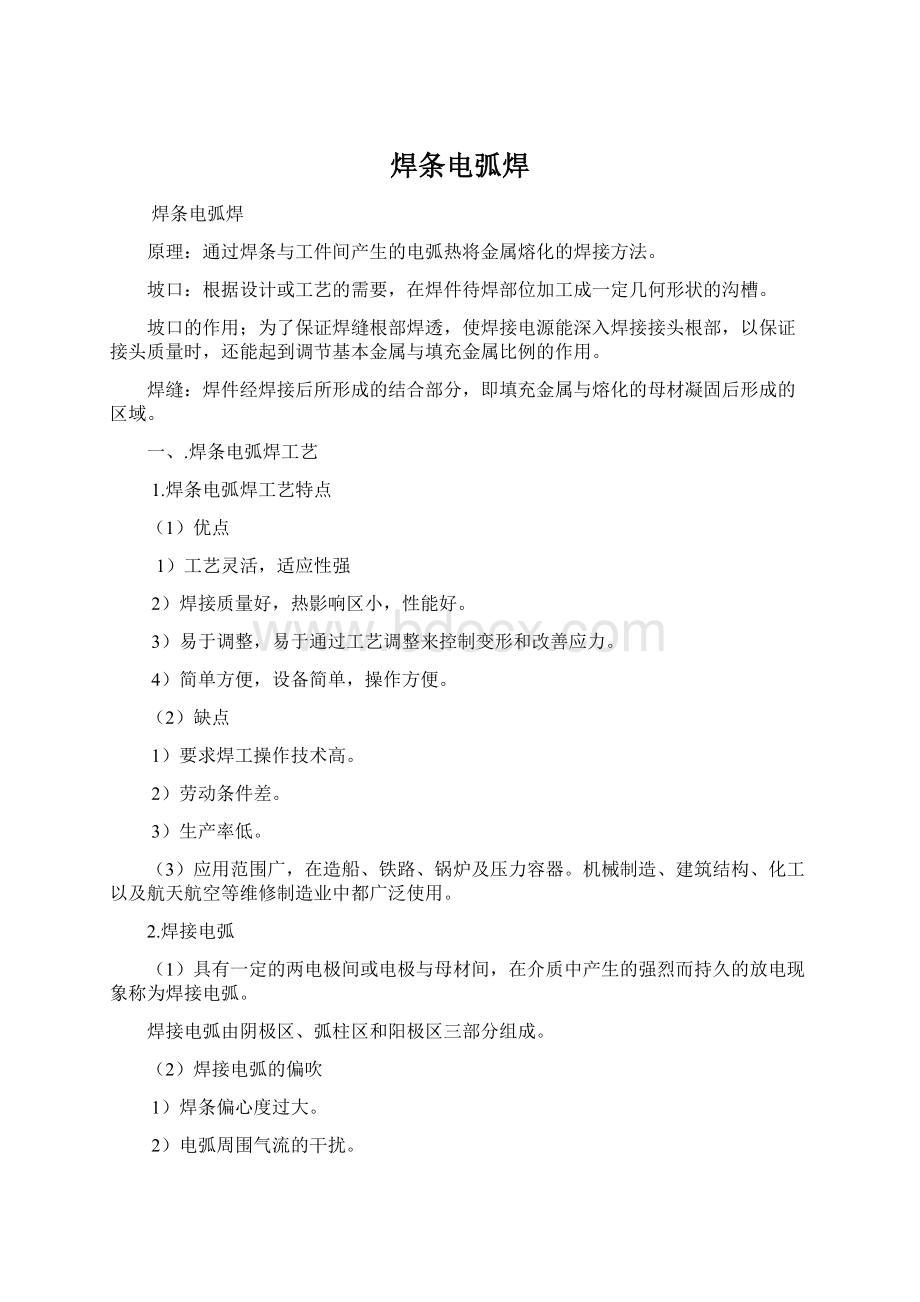
焊条电弧焊
焊条电弧焊
原理:
通过焊条与工件间产生的电弧热将金属熔化的焊接方法。
坡口:
根据设计或工艺的需要,在焊件待焊部位加工成一定几何形状的沟槽。
坡口的作用;为了保证焊缝根部焊透,使焊接电源能深入焊接接头根部,以保证接头质量时,还能起到调节基本金属与填充金属比例的作用。
焊缝:
焊件经焊接后所形成的结合部分,即填充金属与熔化的母材凝固后形成的区域。
一、.焊条电弧焊工艺
1.焊条电弧焊工艺特点
(1)优点
1)工艺灵活,适应性强
2)焊接质量好,热影响区小,性能好。
3)易于调整,易于通过工艺调整来控制变形和改善应力。
4)简单方便,设备简单,操作方便。
(2)缺点
1)要求焊工操作技术高。
2)劳动条件差。
3)生产率低。
(3)应用范围广,在造船、铁路、锅炉及压力容器。
机械制造、建筑结构、化工以及航天航空等维修制造业中都广泛使用。
2.焊接电弧
(1)具有一定的两电极间或电极与母材间,在介质中产生的强烈而持久的放电现象称为焊接电弧。
焊接电弧由阴极区、弧柱区和阳极区三部分组成。
(2)焊接电弧的偏吹
1)焊条偏心度过大。
2)电弧周围气流的干扰。
3)磁场的影响----磁偏吹。
进行直流焊时电弧因受到焊接回路所产生的电磁力的作用而产生的电弧偏吹
a.接线位置不正确。
b.铁磁物质。
c.焊条与焊件的位置不对称。
克服方法:
a.改变地线位置。
b.调节焊条角度,使焊条向偏吹一侧倾斜。
c.在焊缝两端各加一块附加钢板(引弧板、熄弧板)
d适当降低电流。
e.采用短弧焊。
3焊条电弧焊工艺参数
(1)焊接电源的选择:
通常,酸性焊条可采用交流和直流两种电源,一般优先选择交流电源。
碱性焊条由于电弧稳定性差,所以必须选择直流电源,但对药皮中含有较多稳弧剂的碱性焊条也可用交流。
(2)极性的选择
在采用直流焊接时,焊件与电源输出端正、负极的接法叫极性。
当焊件接电源正极,焊条接负极时叫正接;反之,叫反接。
1)碱性焊条常用反接,反接时电弧燃烧稳定,飞溅小,声音也较平静均匀。
2)酸性焊条如果使用直流通常正接,因为阳极部分温度高于阴极部分,可得到较大熔深,而焊接薄板、铸铁、有色金属时应用反接。
(3)焊条直径,焊条直径的大小取决于被焊材料的厚度,所处的焊接位置以及待焊接头的形式和焊道层次等因素。
(4)焊接电流
1)影响电流的因素
a焊条直径。
b焊接位置.c焊道层次。
d焊条类型。
碱性比酸性要小10%,不锈钢比碳钢小20%
2)判断电流合适的方法
a观察飞溅状态,电流过大电流吹力大,飞溅大;电流过小,电弧吹力小,熔渣和铁水很难分离。
b检查焊缝成形状况,电流过大时,熔深大,易产生咬边。
电流过小时,焊缝窄而高,且两侧与母材结合不良。
3)观察焊条熔化状况:
电流过大,焊条融掉大半根后剩余部分发红。
电流过小时,电弧燃烧不稳定,焊条易粘在焊件上。
(5)焊接层次
在中、厚板焊接时,必须采用多层多道焊。
对同一厚度的材料,其它条件不变时,增加焊接层次,热输入量减少。
有利于提高焊接接头的塑性和韧性。
每层焊道厚度最好不大于4—5㎜.
(6)电弧电压
焊条电弧焊时,电弧电压是由焊工根据具体情况灵活掌握的。
其原则:
一是保证焊缝具有要求的尺寸和外形。
二是保证焊透。
焊接电弧电压主要取决于弧长,电弧长,电压高。
反之则低。
焊接过程中一般希望弧长保持一致,而且尽可能用短弧焊接。
短弧:
弧长为焊条直径的0.5---1倍。
(7)焊接速度
焊接速度是焊条沿焊接方向移动的速度,在保证焊缝所要求的尺寸和质量前提下,电焊工根据情况掌握。
速度过慢,热影响区加宽,晶粒粗大,焊缝变形也大。
速度过快,易造成未焊透、未熔合、焊缝成形不良等缺陷。
二.焊条
1.焊条的分类
(1)焊条牌号根据GB980—76
a.焊条药皮分八种类
表1—1药皮类型和焊接电源种类
牌号
焊条药皮类型
焊接电源种类
×××O
未规定
不规定
×××1
氧化钛型
直流或交流
×××2
氧化钛钙型
直流或交流
×××3
钛铁矿型
直流或交流
×××4
氧化铁型
直流或交流
×××5
纤维素型
直流或交流
×××6
低氢钾型(碱性)
直流或交流
×××7
低氢钠型(碱性)
直流
×××8
石墨型
直流或交流
×××9
盐基型
直流
b.按用途可分为九大类
表1—2电焊条的分类
类别
焊条
符号
用途
第一类
结构钢焊条
J
焊接碳素结构钢、低合金钢。
第二类
钼和铬钼耐热钢焊条
R
焊接珠光体耐热钢及马氏体耐热钢。
第三类
低温钢焊条
W
焊接各种在低温条件下工作结构。
第四类
不锈钢焊条
G.A
焊接不锈钢和热强钢。
第五类
堆焊焊条
D
用于具有耐磨性.耐腐蚀性的堆焊层。
第六类
铸铁焊条
Z
焊补各种铸铁件。
第七类
镍及镍合金焊条
Ni
焊接镍及镍合金、异种金属。
第八类
铜及铜合金焊条
T
焊接铜及铜合金、异种金属。
第九类
铝及铝合金焊条
L
焊接铝及铝合金。
(2)表示方法
1)举例aJ425XJ表示结构钢焊条。
42表示焊缝抗拉强度不低于420Mpa5表示药皮为纤维素型、交直流两用。
X表示向下立焊专用焊条。
2)根据GB5117—85或GB/T5118—1995
举例bE4315E表示焊条。
43表示熔敷金属抗拉强度最小值420Mpa1表示焊条适用于全位置焊接。
15表示药皮为低氢型并采用直流反接电源。
第三位数字表示焊条的焊接位置,“0”级“1”表示适用全位置焊接,“2”表示适用平焊及平角焊,“4”表示焊条适用向下立焊;第三位和第四位数字组合时表示焊接电流种类及药皮类型。
2.焊条选用原则
(1)考虑焊件的机械性能、化学成分。
(2)考虑焊件的工作条件及使用性能。
(3)考虑简化工艺、提高生产率。
3.焊条的烘干
(1)焊条受潮的危害
1)焊接工艺性能变坏,电弧不稳定,飞溅增多,烟尘增大。
2)影响焊接质量:
容易产生氢致裂纹,气孔等缺陷。
(2)烘干温度
酸性焊条75---150度保温1---2h
碱性焊条350---400度保温1---2h
(3)烘干次数
一般焊条可重复烘干两次。
酸性碳钢焊条最多可烘干五次;酸性纤维性焊条及碱性则重复烘干三次。
三.焊条电弧焊的操作
1.焊接电弧的引燃
焊条电弧焊的焊接电弧的引燃称为引弧。
常用引弧方法有直击法引弧、划擦法引弧
2.运条
(1)直线运条法。
(2)直线往复运条。
(3)锯齿形运条。
(4)月牙形运条。
(5)三角形运条。
(6)圆圈形运条。
3.收弧
(1)画圈收弧法。
(2)反复断弧收弧法。
(3)回焊收弧法
四.焊接缺陷
焊接过程中在焊接接头中产生的金属不连续、不致密或连接不良的现象称为焊接缺陷。
1.焊缝表面尺寸不符合要求。
2.焊接裂纹
(1)热裂纹(一次结晶时产生的裂纹即在高温时)
产生原因:
a熔池冷却结晶时受到拉应力作用。
B凝固时,低熔点共晶体形成的液态间层共同作用的结果。
防止方法:
a控制碳、硫、磷含量b预热c采用碱性焊条d控制熔池形状。
(2)冷裂纹(二次结晶时产生的裂纹即在低温时200-300℃)
产生原因:
a焊材本身的淬硬倾向。
b熔池中熔入大量的氢。
c焊接过程中产生的较大拘束应力。
防止措施:
a焊前严格烘干焊条。
b采用低氢焊条。
c焊接淬硬性较强的低合金钢用不锈钢焊条。
d预热e后热f适当增加焊接电流,减慢焊接速度。
(3)再热裂纹(当焊缝再次加热时出现的裂纹)
3.气孔
产生原因:
a铁锈水分。
b焊接方法c焊条种类。
d电流种类和极性。
e焊接工艺参数。
防止措施:
(1)清除焊缝两侧铁锈、油等污物。
(2)烘干焊条。
(3)采用合理的工艺参数。
4.咬边
产生原因:
焊接工艺参数选择不当,焊接电流太大,电弧过长,运条速度和焊条角度不适当等。
防止方法:
选择正确的焊接电流及焊接速度,电弧不宜过长,掌握正确的运条方法和运条角度。
5.未焊透
产生原因:
(1)焊速太快,电流过小。
(2)弧长过大,焊条角度不当。
(3)焊接时有偏吹现象。
(4)焊缝坡口钝边过大,坡口角过小。
(5)焊接位置不佳,焊接可达性不好。
防止方法:
正确选用和加工破口尺寸,保证必须的装配间隙,正确选用焊接电流和焊接速度。
6.未熔合
熔焊时,焊道与母材之间或焊道与焊道之间未完全熔化结合的部分
产生原因:
层间清渣不干净,焊接电流过小,焊条偏心,焊条摆动幅度太窄等。
防止方法:
加强层间清渣,正确选择焊接电流。
7.夹渣
焊后残留在焊缝中的熔渣
产生原因:
(1)焊接电流过小,液态金属和熔渣分不清。
(2)焊速过快,使熔渣来不及浮起。
(3)多层焊时清渣不干净。
(4)焊条角度不正常。
8.焊瘤
焊接过程中,熔化金属流淌到焊缝之外未熔化的母材上。
产生原因:
(1)操作不熟练。
(2)运条角度不当。
防止方法:
(1)提高操作技术水平。
(2)选择正确的焊接工艺参数,严格控制熔池温度不宜过高。
9.塌陷
单面熔化焊时,由于焊接工艺选择不当,造成焊缝金属过量透到背面,而使正面塌陷,背面凸起的现象。
产生原因:
(1)装配间隙过大。
(2)焊接电流过大所致。
10.凹坑
焊后在焊缝和焊缝背面形成的低于母材表面的局部低洼部分。
产生原因;电弧拉得过长,焊条角度不当,装配间隙过大。
11.烧穿
焊接过程中,熔化金属自坡口背面流出形成穿孔的缺陷。
产生原因:
对焊件加热过多。
防止方法:
正确选择电流和焊接速度。
12.夹钨
钨极氩弧焊时,由钨极进入到焊缝中的钨粒。
产生原因:
(1)电流过大,钨极端头熔化。
(2)钨极到熔池距离小,产生接触。
(3)采用短路法引弧。
防止方法:
(1)降低焊接电流。
(2)采用高频引弧。
(3)电弧不宜过短。
五.工艺参数对焊缝形状的影响
1.焊接电流
当其他条件不变时,增加焊接电流,则焊缝厚度和余高都增加,而焊缝宽度几乎保持不变。
原因:
(1)焊接电流增加,电弧热量增加,因此熔池体积和弧坑深度也增加,所以冷却下来后,焊缝厚度就增加。
(2)电流增加时,焊条和焊丝熔化量也增加,因此,焊缝余高增加。
如果不填丝的焊接,余高不会增加。
2.电弧电压
当其他条件不变,电弧电压增大,焊缝宽度增大。
而焊缝厚度和余高将略有减少。
因为电弧电压增加就意味着电弧长度增加,因此电弧摆动范围扩大而导致焊缝宽度增加。
3.焊接速度
焊接速度对焊缝厚度和焊缝宽度有明显的影响。
当焊接速度增加时,焊缝厚度和焊缝宽度都大为下降。
焊速增加时,焊缝单位时间内输入的热量减少了。