连铸机设备技术规格.docx
《连铸机设备技术规格.docx》由会员分享,可在线阅读,更多相关《连铸机设备技术规格.docx(58页珍藏版)》请在冰豆网上搜索。
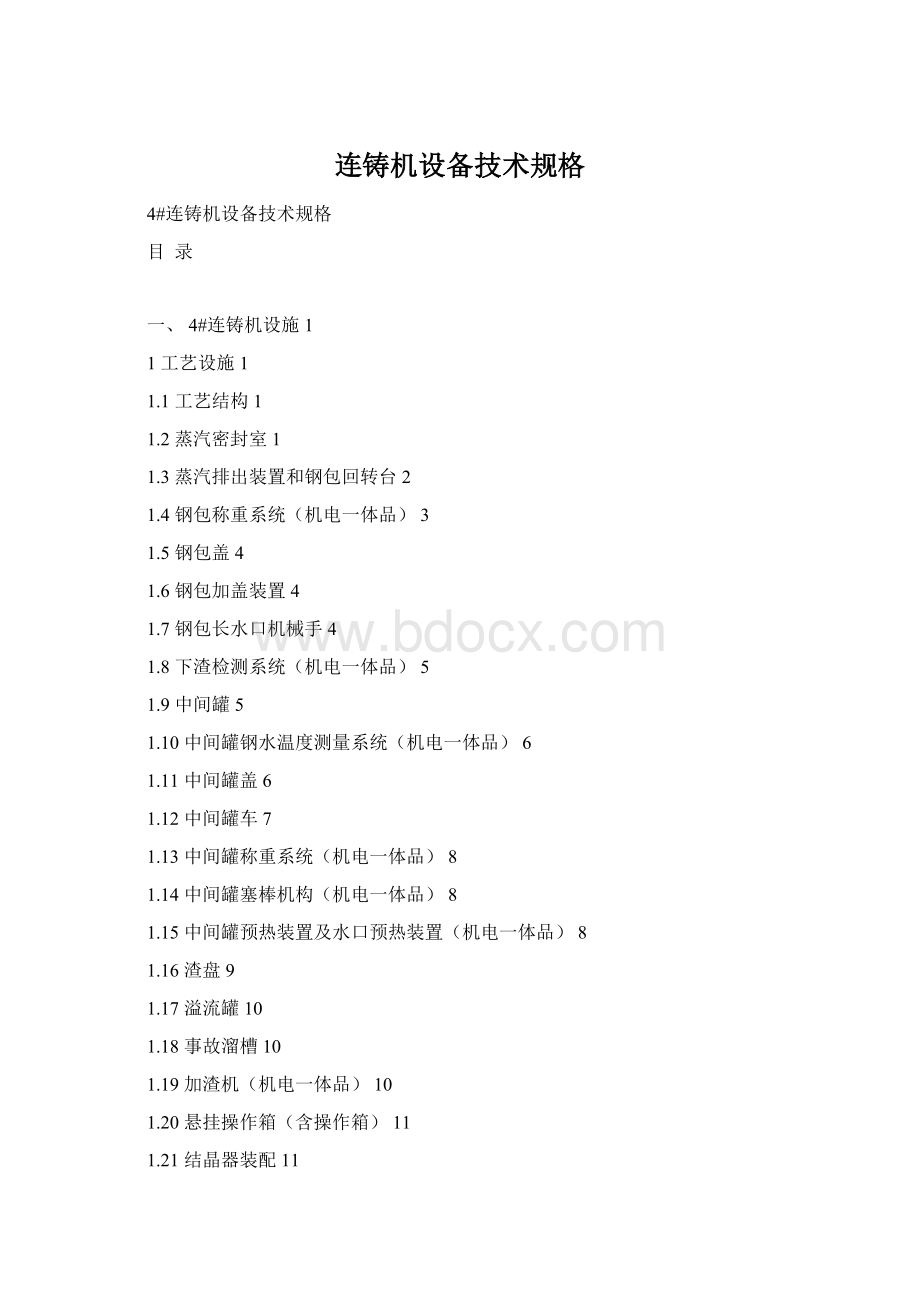
连铸机设备技术规格
4#连铸机设备技术规格
目录
一、4#连铸机设施1
1工艺设施1
1.1工艺结构1
1.2蒸汽密封室1
1.3蒸汽排出装置和钢包回转台2
1.4钢包称重系统(机电一体品)3
1.5钢包盖4
1.6钢包加盖装置4
1.7钢包长水口机械手4
1.8下渣检测系统(机电一体品)5
1.9中间罐5
1.10中间罐钢水温度测量系统(机电一体品)6
1.11中间罐盖6
1.12中间罐车7
1.13中间罐称重系统(机电一体品)8
1.14中间罐塞棒机构(机电一体品)8
1.15中间罐预热装置及水口预热装置(机电一体品)8
1.16渣盘9
1.17溢流罐10
1.18事故溜槽10
1.19加渣机(机电一体品)10
1.20悬挂操作箱(含操作箱)11
1.21结晶器装配11
1.22结晶器框架12
1.23结晶器铜管12
1.24结晶器电磁搅拌装置(M-EMS)(机电一体品)13
1.25铸流末端电磁搅拌器(外置式)13
1.26结晶器液面检测及控制系统(机电一体品)13
1.27结晶器液压振动装置14
1.28浸入式水口快换机构(带事故闸板)(机电一体品)15
1.29足辊喷淋系统15
1.30铸坯导向段15
1.31二冷喷淋架18
1.32拉矫机18
1.33链式引锭杆杆身19
1.34引锭杆过渡链节20
1.35引锭杆头20
1.36引锭杆存放装置20
1.37火焰切割机(含定尺测长装置)(机电一体品)21
1.38取样切割枪22
1.39取样收集箱22
1.40手动切割枪22
1.41坯头坯尾收集装置23
1.42切前辊道(含脱引锭辊)23
1.43切割区辊道25
1.44输送辊道
(一)26
1.45输送辊道
(二)27
1.46去毛刺机(含溜槽、渣箱)(机电一体品)28
1.47出坯辊道(含翻钢机)29
1.48横向移钢机30
1.49固定挡板31
1.50升降挡板31
1.51铸坯喷号机(机电一体品)32
1.52步进冷床及收集台架(含拨钢机)32
1.53铸坯存储跨输送辊道33
1.54铸坯过跨运输车(KL、LM、MQ和QR跨)34
1.55圆坯旋转台35
1.56推钢机(含收集台)36
1.57圆坯升降装置37
1.58高位辊道37
1.59圆坯检查和处理设施(机电一体品)38
1.60连铸机防护罩38
1.61液压和润滑设备(含管道)38
1.62介质管道38
1.63结晶器、导向段和拉矫机维修设施38
1.64中间罐维修区40
1.65设备过跨台车(结晶器、扇形段和中间罐的运输)42
1.66中间罐吊具43
1.67废料箱43
1.68中间罐手动拆衬装置43
1.69结晶器对弧样板和导向段对弧样板43
1.70在线对弧样板(用于结晶器和导向段)44
1.71用于操作维护的提升装置,工具,吊具,仪表和仪器44
1.72人体冷却器44
1.73500kg能力的客货电梯44
1.74电动葫芦/手动葫芦44
1.75基础螺栓和锚固件44
1.76稀油,干油,润滑剂和化学药剂等的第一次填充44
1.77调试备件44
1.78保险备件44
1.79耐火材料和消耗件44
1.80水冷却器44
1.81更换件44
1.82保证连铸机正常生产的其它设备。
44
2原料运输设施46
3耐火材料46
4介质46
5空调和通风系统46
6水系统(连铸机冷却水系统和其他水系统)46
7电气和照明46
8仪表控制系统47
9自动化系统(1级和2级)47
10电信和CCTV系统47
11质量控制设施47
12防火和火灾检测系统47
13污染防治设施47
14液压和干油润滑系统(见附件2-2)47
15土建工程47
16钢结构47
二、备件、消耗件、工具和吊具49
一、4#连铸机设施
1工艺设施
1.1工艺结构
A.浇注平台
浇铸平台独立于厂房结构,配备有到结晶器振动装置和导向段的通道以便于维护,配有楼梯和通道。
设有临时设备存放区域。
B.滑动水口液压缸操作平台和钢包操作平台
滑动水口液压缸操作平台
数量:
1套
位置:
钢包回转台钢包接受侧,事故包上方。
功能:
操作工利用该平台,对钢包滑动水口液压缸进行操作。
结构类型:
焊接钢结构,设置有走梯、栏杆。
操作平台为活动平台,当吊运事故包时,可将操作平台移走。
钢包操作平台
数量:
1套
位置:
位于浇注平台,中间罐车高轨侧。
功能:
为中间罐车高轨提供支撑;中间罐车拖链的走行平台;操作工可通过此平台对中包内钢水测温,投放中包覆盖剂等。
结构类型:
焊接钢结构,设置有走梯、栏杆。
C.高位辊道支撑钢结构
用于圆坯输送。
为焊接钢结构。
1.2蒸汽密封室
数量:
1套
位置:
位于浇注平台下方,拉矫机前方。
功能:
密封室收集因喷淋冷却铸坯所产生的蒸汽,并且用风机将其排放到车间外。
结构类型
主要由排蒸汽管道、维护用阶梯和平台、维护用人行道和门等组成。
收集、排放蒸汽、在密封室上部区域设有蒸汽排放口、设有在线维修和检查的场地,可以接近设备进行维修和检验、设有接近夹持段、导向段、喷淋架的通道、采用镀锌板材质,不易腐蚀。
二冷室内配有检修照明。
1.3蒸汽排出装置和钢包回转台
A:
蒸汽排出装置
数量:
1套
位置:
蒸排风机位于回转台基础两侧,进气管道由二冷室连至风机入口,出口管道由风机出口通过浇注平台,送至厂房外侧。
功能:
用于将喷淋冷却铸坯所产生的蒸汽通过风机及管道排放到车间外。
结构类型
主要由传动风机,减振装置,控制阀门,管道等组成。
技术参数
数量
2套
排放介质
蒸汽/空气混合物
静态压力
蒸汽的温度
1250Pa
最大80℃
材质
风机外壳
镀锌
风机叶轮
12Mn,表面镀碳化物
B:
钢包回转台
数量:
1套
位置:
位于浇注平台上方,H31与H33之间。
功能:
钢包回转台可将浇注钢包从接收位运至浇注位或从浇注位运至接收位。
钢包在回转台上的吊进、吊出是通过钢水接收跨吊车完成的。
结构类型:
主要部件:
底座和基础锚固框架、回转轴承、叉臂(带上下连杆、连接轴承和钢包支架)、回转传动装置(带电机、减速器和事故液压马达)、升降油缸、电气滑环和旋转接头、防热防溅保护板、钢包加盖装置、称重设备、楔块式(液压)/液压盘式制动、机上配管、声光报警装置。
主要特征:
叉臂由液压缸驱动单独提升和下降,正常回转采用电机、减速器传动装置,事故回转采用液压马达驱动,事故回转的动力由液压站内的液压蓄能器提供,钢包在浇注位时采用楔块式(液压)/液压盘式定位,通过管线和旋转接头提供介质,含给钢包滑动水口液压缸供油的进、回油管,通过滑环提供电力,轴承润滑采用集中干油润滑,具有防热和防溅保护。
技术参数
类型
蝶形,配有两个钢包支撑臂
单臂升降、任意回转
钢水重量(平均/最大)
150/160吨
承载能力
250吨
250吨/0吨一侧承载钢包
250吨/250吨两侧承载钢包
冲击系数
2倍
设计负荷条件
情况1
一侧满包一侧空包
情况2
两侧满包
情况3
一侧满包一侧半包
回转半径
5.5m
回转传动
正常回转采用电机、减速器驱动
事故回转采用液压马达驱动
回转速度
1转/分
事故回转速度
0.5转/分
转动角度
两个方向上任意转动
叉臂升降方式
液压升降
-升降行程
800mm
-升降速度
25毫米/秒
1.4钢包称重系统(机电一体品)
数量:
2套(一个叉臂一套)+一套更换件。
类型:
安装在钢包支架下面的称重压头支撑在钢包回转台每个臂上。
称重压头精度:
0.1%
称重压头类型:
重型工作制(应变仪型)。
配备钢包重量连续显示和读出。
应配备钢包回转台上称重压头的测试和更换装置。
压缩空气冷却设施以实现冷却。
1.5钢包盖
数量:
2套安装件+2套更换件
功能:
安装在钢包加盖装置上,内部砌筑含锆耐火纤维,浇钢时旋转至钢包上部,减少浇注期间的热损失。
结构类型
焊接件,配有锚固件以固定耐火材料,衬有陶瓷棉/毡/模块。
1.6钢包加盖装置
数量:
1套
功能:
钢包加盖装置用于将钢包盖放置到钢包之上,以减少浇注期间的热损失。
钢包加盖装置能够旋转,便于钢包吊装。
钢包加盖装置可以升降,使盖子与钢包吻合和分离。
结构类型
由支撑结构和旋转臂装置、旋转液压马达、升降液压缸、配管等组成。
采用液压升降,回转机构。
技术参数
类型
使钢包盖旋转、升降,安装在钢包回转台的叉臂上。
数量
2套(每个叉臂侧一套)
旋转传动
液压马达
升降
液压缸
升降能力
约6吨
旋转角度
90
升降速度
50毫米/秒
升降行程
约500mm
升降臂长度
约5600mm
立柱高度
约1700mm
1.7钢包长水口机械手
数量:
1套
功能:
长水口用于防止钢包和中间罐之间的铸流发生二次氧化。
长水口由液压缸驱动压在钢包水口上。
介质管道采用钢管+挠性软管形式。
结构类型
主要由立柱、支撑臂,带长水口支架、液压缸和介质管线等组成。
支撑臂通过三个轴杆完成回转和前后移动,在水平和垂直方向上,长水口自动跟随钢包水口运动,结构简单,可手动/液压操作。
技术参数
数量
1台
类型
可旋转及升降的杠杆装置
安装位置
浇注平台
操作方式
支撑臂升降
液压驱动
支撑臂回转
手动
夹持器旋转
手动
行程
约800mm
支撑臂回转范围
大约150
夹持器旋转范围
约180
长水口保护
氩气
1.8下渣检测系统(机电一体品)
数量:
1套
类型:
振动信号检测方式
功能:
浇注过程中检测钢包到中间罐的钢水中的下渣情况。
工作原理:
连铸钢包下渣检测系统通过感受机械操作臂的振动来检测连铸过程中的下渣。
在钢水浇注过程中,钢水流经长水口注入中间罐时,钢水冲击长水口壁引起用来支撑长水口的机械操作臂振动。
由于钢渣比重不到钢水比重的一半,浮在钢水表面,在一包钢水即将浇注完毕时,钢渣才出现,此时由于钢渣轻,粘度大,流动性也差,钢水与钢渣的混流对长水口壁的冲击作用力与纯钢水的冲击作用力存在较大的差异。
本系统主要通过测量分析机械操作臂的振动差异监测连铸钢包的下渣。
1.9中间罐
数量:
2个安装件+10个更换件
位置
位于中间罐车上,适合于浸入式浇铸。
功能:
中间罐为钢包和结晶器之间存放钢水的中间容器。
进入结晶器的钢流由塞棒控制系统来控制流量。
中间罐的形状和容积保证钢水在中间罐中流场合理,有足够的滞留时间,使非金属夹杂物充分上浮,在钢包更换过程中,浇注可以继续进行。
在中间罐后部安装有溢流斜槽,可以确保发生事故时钢水溢流至溢流槽内。
结构类型:
倾斜侧壁、大容量、深液位,使夹杂物从钢水中充分上浮、带加强筋、提升吊耳和支承底座的焊接钢结构、中间罐的T形及其大容量、深液位保证了钢水从注入口至浇注口的足够距离,流场合理,钢水在中间罐中有充足的滞留时间(夹杂物分离、温度均匀化)。
通过数值模拟和水模试验确定中间罐最佳内腔尺寸。
技术参数
中间罐外形
焊接钢结构件,T形罐
水口数量
5
水口中心间距
1700mm
铸流控制方式
塞棒
中间罐液面
正常
900mm
最大
1000mm(溢流位)
钢水量
约35吨(正常)
约40吨(最大)
钢水滞留时间
约10分钟
1.10中间罐钢水温度测量系统(机电一体品)
数量:
1套
类型:
中间罐钢水温度测量系统包括测温枪,测温枪附件,显示屏等。
技术参数:
测量范围800~1800℃
热态响应时间≤60s
系统精度≤±3℃
探头寿命≥24h
1.11中间罐盖
数量:
2套安装件+4套更换件。
功能:
用于中间罐以降低浇铸期间的钢水热量损失。
中间罐盖在运输到连铸机之前放置到准备区域的中间罐上以进行预热。
结构类型
焊接钢结构,配有耐火衬,设有预热烧嘴孔和塞棒安装孔。
1.12中间罐车
数量:
2台
位置:
浇铸平台上,在预热位置和浇铸位置之间来回移动。
功能:
中间罐车用于承载中间罐并从预热位运至浇注位或从浇注位运至预热位,水口与结晶器的对中通过对中装置实现,可对任何高度位置上的中间罐进行称重,通过中间罐升降,调整中间罐高度。
结构类型:
主要部件:
钢结构车架,两轮驱动,由电动-机械马达传动(VVVF),带导向轮的升降臂,用于安装称重系统中间罐鞍座,升降液压缸,对中液压缸,管线拖链,配管和电缆,液压驱动防溅板,手动润滑系统,称重系统。
高低轨式,电动走行,采用液压缸控制中间罐的升降和对中,能源介质及控制线设在配有良好防护措施的高架管线拖链上,不易损坏,防溅板能有效保护操作工和设备安全,制动器可将中间罐车位置锁定。
增加标尺显示升降高度,以便于操作;称重传感器采用外出线。
技术参数
数量
2台
结构类型
高低轨式
承载能力
约90吨(中间罐+钢水、耐火衬)
传动
走行
电动-机械(VVVF控制)
升降
液压
对中
液压
速度
走行
大约2~20米/分
升降
大约30毫米/秒
对中
大约5毫米/秒
行程
升降
大约600mm
对中
200mm
能源介质供应
管线拖链
1.13中间罐称重系统(机电一体品)
数量:
2套安装件+1套更换件(更换件除去电气部分)
类型:
安装在中间罐车框架上的中间罐支架下面的称重压头。
称重压头精度0.15%
称重压头类型:
重型设计(应变仪型)。
配有中间罐重量显示和记录。
1.14中间罐塞棒机构(机电一体品)
数量:
5套安装件+20套更换件(更换件除去电气部分)
功能:
塞棒装置用于调节中间罐至结晶器的钢水流量,与结晶器液面检测装置联锁控制。
位置:
安装在中间罐体上。
结构类型:
塞棒机构用螺栓连接到中间罐。
塞棒的操纵/垂直移动通过电动缸实现。
执行机构通过结晶器配备的结晶器自动液面控制系统调节。
塞棒机构适当设计以实现手动和自动操作。
塞棒采用导向轮导向,保证了塞棒位置的精确控制,手动操作或用电动数字缸自动操作,塞棒机构和电动数字缸的固定方式简单,易于装卸,采用塞棒吹氩。
预热位,可实现塞棒手动调整。
技术参数:
行程150mm(详细设计确定)
操作方式可手动操作,也可自动操作
主要部件
塞棒机构
电动数字缸
1.15中间罐预热装置及水口预热装置(机电一体品)
A.中间罐预热装置
数量:
2套安装件+1套烧嘴更换件
功能:
浇铸之前预热带盖的中间罐和浇注水口、长水口到要求的温度。
位置:
位于浇铸平台上,连铸机每侧一个。
结构类型:
主要部件:
支撑结构和倾翻支架以及配管,煤气烧嘴罩,热保护装置(采用打结或砌砖),助燃风机,煤气/空气阀站,液压系统,液压缸,就地控制台。
中间罐水口预热利用中间罐预热产生的烟气通过抽吸方式从水口排出,达到预热水口的目的。
抽吸所需的空气来源于中间罐预热装置的鼓风机。
中间罐煤气流量信号进L1级PLC系统。
技术参数:
结构类型
蓄热式预热装置
加热能力
最大16000兆焦/小时
烧嘴数量
每套5个
燃气
焦炉煤气
热值
约16128千焦/标立米
燃气耗量
1000标立米/小时
助燃空气
采用风机鼓风
中间罐预热温度
最大1200℃(中间罐内壁,预热90分钟)
水口碗1050℃(预热60分钟)
烧嘴点火方式
自动,设有火焰探测功能
倾翻传动
液压
倾翻角度
90度
控制系统
可编程控制器自动控制(不采用温度检测及控制)
说明:
预热装置为机电一体化设备,设计与制造按照制造厂家的标准。
中间罐加热时,烧嘴罩通过液压驱动倾翻至中间罐上方。
预热装置配置有煤气自动切断装置和氮气吹扫功能。
预热装置的控制由就地控制台完成。
就地控制台的PLC具有与主系统信号交换和联锁功能。
B.中间罐水口预热装置(机电一体品)
数量2套
功能描述:
在线浸入式水口预热装置设置在中间包预热位,为固定式烘烤器,采用文丘里原理,通过压缩空气高速流过时产生的负压,使中间包内的高温烟气穿过浸入式水口,从而加热安装在中间包底部的浸入式水口。
技术参数:
预热温度~1000℃
1.16渣盘
数量:
2个安装件+1个更换件
功能:
紧急情况下(中间罐塞棒、中间罐滑动水口故障的情况下)处理中包内剩余的钢水。
位置:
位于浇铸平台上,位于预热站内中间罐车下面。
结构类型:
渣箱为重型焊接钢板结构,配有耐火砖,具有足够的容量能够处理满中间罐钢水。
渣箱配有吊耳用于通过EOT吊车吊运。
1.17溢流罐
数量:
1个安装件+1个备用件
位置:
位于浇注位,中间包车与钢包回转台之间。
功能:
紧急情况下处理中间罐溢流钢水。
结构类型:
焊接件,配有耐火衬。
事故箱配有吊耳用于通过EOT吊车吊运。
1.18事故溜槽
数量:
1套
位置:
浇注平台上,布置在钢包回转台回转轨迹上。
结构类型:
焊接件,配有耐火衬。
用于钢包回转台发生紧急情况的时候接受钢包流出的钢水。
1.19加渣机(机电一体品)
数量安装2套+2套更换件(更换件不包含电气控制部分)
功能
自动给送保护渣到结晶器中。
位置
安装在中间罐车上,每个结晶器的单独的/独立的自动系统。
结构类型:
自动加渣装置是由料箱、定量给料器、分料器、料管、物料输出、控制盘、PLC及电控柜组成。
根据不同拉速将不同量保护渣连续送入结晶器内,使得保护渣在结晶器表面覆盖厚度均匀,每流单独控制,互不干扰;
将保护渣均匀覆盖在结晶器内的钢液面上,可以使结晶器内的保护渣均匀分布;
连续将保护渣送入结晶器内,不存在保护渣堵死现象,同时渣料容器具有过滤清理结块堵塞检查口;
保护渣给入量拉速变化而变化,保证结晶器内钢液面上的保护渣厚度稳定。
1.20悬挂操作箱(含操作箱)
数量:
5套安装件+1套更换件。
结构类型:
可移动的悬挂机构。
操作箱包括操作箱、滑道、支持臂及旋转轴承等,设在钢包操作工平台下面的滑道上,可移动或旋转至所需位置。
操作箱配有必要的连铸机控制装置,并且配有浇铸速度,中间罐钢水重量,中间罐钢水温度,振动频率,每流结晶器实际液面,结晶器液面设定值,结晶器水流量以及结晶器液面控制的自动/手动状态的显示装置。
1.21结晶器装配
数量:
200mmX200mm方坯5套安装件+5套更换件
φ410mm圆坯5套安装件+5套更换件
φ450mm圆坯5套安装件+5套更换件
功能:
钢水在结晶器内初步凝固形成一定厚度的坯壳,并通过足辊对初凝坯壳形成支撑。
位置:
安装振动机构上。
结构类型:
主要由铜管,水套,框架,足辊装配,二次冷却的配管、支架和喷嘴等组成。
弧形结晶器,适合于高速浇铸。
结晶器在更换断面尺寸或者进行维护的时候方便快速地进行更换。
外体和水套采用不锈钢制造,足辊与结晶器底部连接。
当结晶器放置在振动装置上时冷却水可自动连接;通过快换接头,手动连接足辊润滑系统。
技术参数
规格
200mm200mmΦ410mmΦ450mm
结构类型
弧形管式结晶器
外弧半径
12m
铜管长度
200mm200mm铜管长1000mm
Φ410mm、Φ450mm铜管长800mm
足辊
200mm200mm设置1对足辊
Φ410mm、Φ450mm设置2对足辊
内、外弧
辊子数量
200mm200mm设置1对足辊
Φ410mm、Φ450mm设置2对足辊
足辊直径
200mm200mm足辊直径:
Φ80mm
Φ410mm、Φ450mm足辊直径:
Φ100mm
左、右侧
辊子数量
200mm200mm设置1对足辊
Φ410mm、Φ450mm设置2对足辊
辊子直径
200mm200mm足辊直径:
Φ80mm
Φ410mm、Φ450mm足辊直径:
Φ100mm
辊子材质
25CrMo
辊子轴承
SKF
辊子堆焊材质
2Cr13
调节方式
垫片组
辊子冷却
外部冷却(二次冷却第一区,直接水冷)
润滑
集中润滑,手动快速连接(基本设计确定)
铜管材质
磷脱氧铜,镀Cr
水套材质
SUS301或SUS304
铜管冷却方式
铜管与水套间的水缝
水缝宽度:
4mm
冷却水连接
安装时自动接通
1.22结晶器框架
数量:
200mmX200mm方坯5套安装件+5套更换件
φ410mm、φ450mm圆坯5套安装件+5套更换件
功能:
在振荡台上实现结晶器装配的支撑和自对中。
结构类型:
焊接钢结构,配有冷却水、润滑等的自密封连接。
1.23结晶器铜管
数量:
200mmX200mm方坯50套更换件
φ410mm圆坯15套更换件
φ450mm圆坯15套更换件
材质:
结晶器管的材质为铜制,磷脱氧铜,镀Cr。
结晶器管长度:
200mm200mm铜管长1000mm
Φ410mm、Φ450mm铜管长800mm
1.24结晶器电磁搅拌装置(M-EMS)(机电一体品)
数量:
200mmX200mm方坯5套安装件+1套更换件(更换件不含电气控制部分)
φ410mm、φ450mm圆坯5套安装件+1套更换件(更换件不含电气控制部分)
功能:
初凝期间在结晶器中产生钢水的旋转搅拌运动以改善表面质量和内部质量并提高散热率。
类型:
外置线圈式,独立搅拌系统,配有线圈高度调整装置。
断面尺寸:
方坯:
200mm200mm
圆坯:
直径410mm,直径450。
1.25铸流末端电磁搅拌器(外置式)
数量:
φ410mm、φ450mm圆坯5套安装件+1套更换件(更换件不含电气控制部分)
功能:
在凝固过程结尾时在铸流中进行液芯搅拌,此时液池已经减少,结晶器搅拌器的作用已经可以忽略不计,从而改善铸坯质量以及降低关键钢种的碳偏析。
类型:
外置式,独立搅拌系统,配有线圈高度调整装置。
1.26结晶器液面检测及控制系统(机电一体品)
数量:
5套安装件+1套更换件
类型:
铯137放射源检测
位置:
放射源位于结晶器装配中,监测器位于外部。
PLC位于电气控制室内。
功能:
测量和控制结晶器中的钢水液位。
结构类型:
较高浇铸速度范围(最高3m/min)的情况下对应较小尺寸的测量和控制。
技术参数:
型式铯137放射源检测
测量范围最小160mm
精度测量范围内的±2-3%
输出信号4-