轴类零件的数控加工与编程2.docx
《轴类零件的数控加工与编程2.docx》由会员分享,可在线阅读,更多相关《轴类零件的数控加工与编程2.docx(22页珍藏版)》请在冰豆网上搜索。
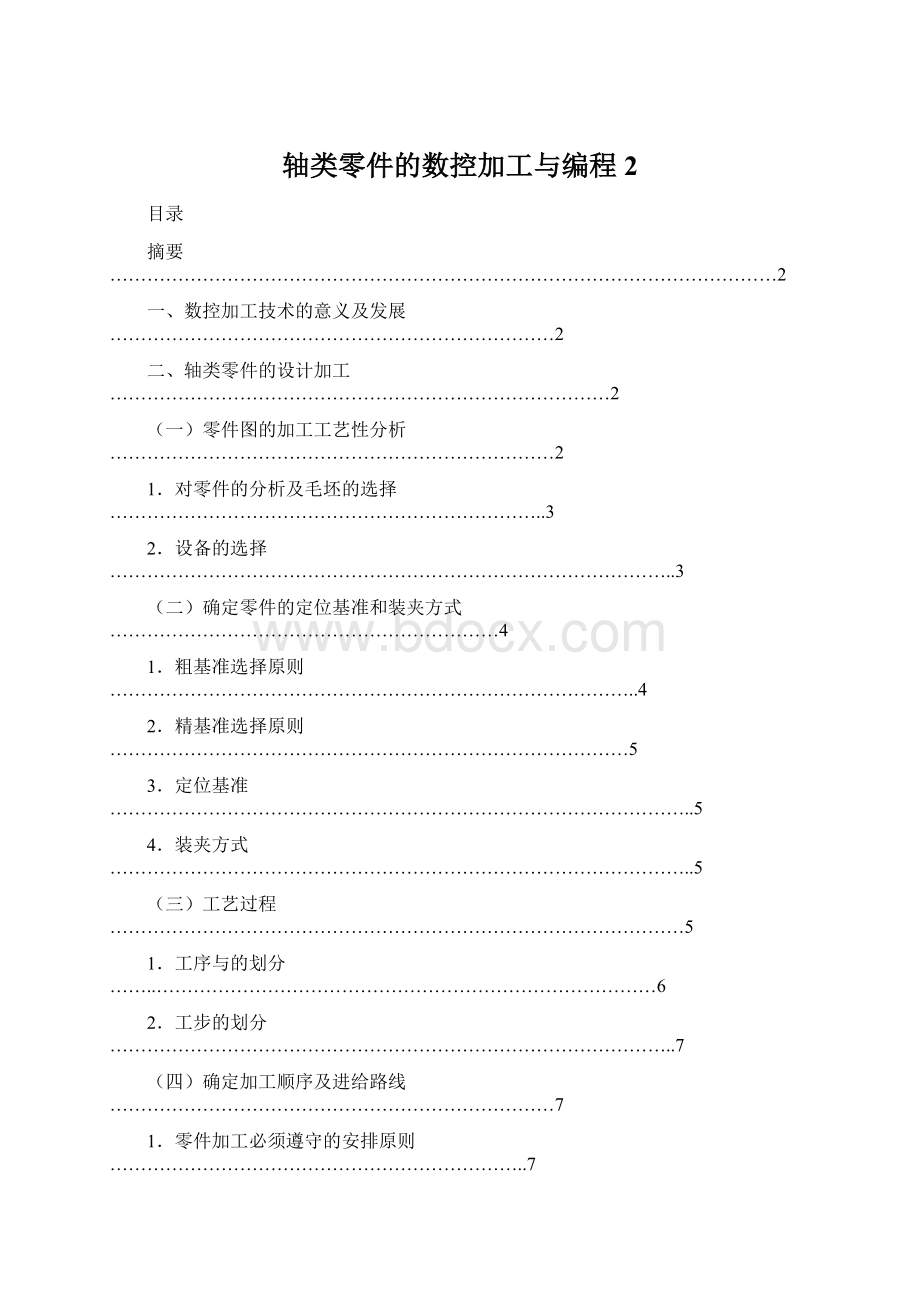
轴类零件的数控加工与编程2
目录
摘要………………………………………………………………………………………………2
一、数控加工技术的意义及发展………………………………………………………………2
二、轴类零件的设计加工………………………………………………………………………2
(一)零件图的加工工艺性分析………………………………………………………………2
1.对零件的分析及毛坯的选择……………………………………………………………..3
2.设备的选择………………………………………………………………………………..3
(二)确定零件的定位基准和装夹方式………………………………………………………4
1.粗基准选择原则…………………………………………………………………………..4
2.精基准选择原则…………………………………………………………………………5
3.定位基准…………………………………………………………………………………..5
4.装夹方式…………………………………………………………………………………..5
(三)工艺过程…………………………………………………………………………………5
1.工序与的划分……..………………………………………………………………………6
2.工步的划分………………………………………………………………………………..7
(四)确定加工顺序及进给路线………………………………………………………………7
1.零件加工必须遵守的安排原则…………………………………………………………..7
2.进给路线…………………………………………………………………………………..7
(五)选择刀具…………………………………………………………………………………7
(六)切削用量的选择…………………………………………………………………………8
1.背吃刀量的选择………………………………………………………………………..…8
2.主轴转速的选择…………………………………………………………………………..8
3.进给量的选取……………………………………………………………………………..9
4.进给速度的选取………………………………………………………………………….10
(七)编制数控加工工艺卡......................................................................................................10
(八)编写数控加工程序………………………………………………………………..........11
1.建立工件坐标系……………………………………………………………………………11
2.手动编程……………………………………………………………………………………12
三、数控仿真系统……………………………………………………………………………...15
结论……………………………………………………………………………………………...18
参考文献………………………………………………………………………………………...19
谢辞……………………………………………………………………………………………...20
附录……………………………………………………………………………………………...21
轴类零件的数控加工与编程
摘要:
数控技术是用数字信息对机械运动和工作过程进行控制的技术。
数控装备是以数控技术为代表的新技术对传统制造产业和新兴制造的渗透形成的,即数字化装备。
数控加工技术是随着数控机床的产生、发展而逐步完善起来的一种应用技术,是机械制造业人员长期从事数控加工的经验总结。
数控加工技术就是用数控机床加工零件的方法。
数控车削加工是利用工件相对于刀具的旋转运动对工件进行切削加工的方法,是从零件图纸到获得数控加工程序的全过程。
关键词:
数控技术;车削加工;数控加工工艺;数控编程
一、数控加工技术的意义及发展
数控技术是数字程序控制数控机械实现自动工作的技术。
它广泛用于机械制造和自动化领域,较好地解决多品种、小批量和复杂零件加工以及生产过程自动化问题。
随着计算机、自动控制技术的飞速发展,数控技术已广泛地应用于数控机床、机器人以及各类机电一体化设备上。
随着科学技术不断发展,数控机床的发展也越来越快,数控机床也正朝着高性能、高精度、高速度、高柔性化和模块化方向发展。
机械工业是国民经济各部门的装备军,而数控加工的方法,是从零件图纸到获得数控加工程序的全过程,数控加工在机械行业占有领头羊的地位,因此国民经济各部门的生产技术水平和所取得的经济效益,在很大程度上取决于机械行业和数控行业中所能提供的机械装备的技术性能、指令和可靠性。
因此数控加工技术水平和生产规模是衡量一个国家科技水平和经济实力的重要标志。
数控机床使用范围越来越大,国内国际市场容量也越来越大,但竞争也会加剧,我们只有紧跟先进技术进步的大方向,不断创新,才能赶超世界先进水平。
二、轴类零件的设计加工
(一)零件图的加工工艺性分析
图1典型轴类零件图
1.对零件的分析及毛坯的选择
该零件表面由圆柱面、圆锥面、圆弧面、螺纹面及沟槽等表面组成。
该零件的几何元素之间的关系表达的很清楚完整,其中多个直径的尺寸精度有较严格的要求,零件的表面部分表面粗糙度要求也较高。
选用毛坯为45#钢,Φ55mm×150mm,无热处理和硬度要求
2.设备的选择
据该零件的外形是轴类零件,比较适合在车床上加工,由于零件上既有切槽尺寸精度又有圆弧数值精度,在普通车床上是难以保证其技术要求。
所以要想保证技术要求,只有在数控车床上加工才能保证其加工的尺寸精度和表面质量。
机床我们选用CK6142车床,HNC数控系统。
其参数如下表:
表2CK6142车床的主要技术参数
参数型号
CK6142
加工能力
床身上最大回转直径mm
420
刀架上最大回转直径mm
200
最大工件长度mm
2000
最大车削长度mm
1870
床身导轨宽度mm
400
主轴
主轴端部代号
C6
主轴孔径mm
58
主轴锥孔mm主轴转速(四段无级)r/min27.5-2200
63
X/Z向最小进给增量mm
0.0005/0.001
进给
X/Z向快移速度mm/min
4000/8000
X向最大行程mm
300
电动刀架工位数
H4
刀架
刀杆截面mm
25×2
尾座套筒直径m
75
尾座
尾座套筒行程
150
尾座套筒锥孔
Morse5
主电动机功率kw
7.5
电机
机床质量kg1900,2000,2500,3500,4500,
机床外形尺寸(长,宽,高)mm1806,2091,2376,2946,3516×1170×1600
(二)确定零件的定位基准和装夹方式
1.粗基准选择原则
(1)为了保证不加工表面与加工表面之间的位置要求,应选不加工表面作粗基准。
(2)合理分配各加工表面的余量,应选择毛坯外圆作粗基准。
(3)粗基准应避免重复使用。
(4)选择粗基准的表面应平整,没有浇口、冒口或飞边等缺陷。
以便定位可靠。
2.精基准选择原则
(1)基准重合原则:
选择加工表面的设计基准为定位基准;
(2)基准统一原则:
自为基准原则,互为基准原则。
3.定位基准
综合上述,粗、精基准选择原则,由于是轴类零件,在车床上用三爪卡盘装夹定位,定位基准应选在零件的轴线上,以毛坯φ55mm的棒料的轴线和左端面作为定位基准。
4.装夹方式
数控机床与普通机床一样也要全里选择定位基准和夹紧应力求设计、工艺与编程计算的基准统一,减少装夹次数,尽可能在一次定位装夹后,加工出全部待加工表面,避免采用占机人工调整式加工方案,以充分发挥数控机床的效能。
装夹应尽可能一次装夹加工出全部或最多的加工表面。
由零件图可分析,应先装夹毛坯φ55mm的棒料的一端,夹紧其30mm的长度,右端加工Φ39mm、SΦ48mm、R9mm、Φ35mm、锥度为10度的外圆,Φ52mm。
然后将棒料卸下,装夹φ52mm的圆柱表面,左端加工Φ25mm×33mm、切退刀槽、加工螺纹M25mm×1.5mm。
这样两次装夹即可完成零件的所有加工表面,且能保证其加工精度要求。
(三)工艺过程
1.工序的划分
工序划分有三种方法:
(1)按零件的装夹定位方式划分;
(2)按粗、精加工划分工序;
(3)按所用的刀具划分工序。
由于零件需要调头加工,如果按粗、精加工划分工序,在调头加工前后各有一次粗加工和精加工,显得比较繁琐,所以不可取;如果按所用的刀具划分工序,刀具有五把,虽然不多,但是在调头加工前后至少要重复使用三把刀,而同一把刀的两次粗、精加工分别在调头加工前后,加工内容不连续,所以也不合理,不易划分工序;只有按零件的装夹定位方式划分工序比较符合该零件的加工工序,且能保证两次装夹的位置精度,每一次装夹为一道工序。
表3加工工序
工序号
工序内容
设备
1
车右端面,加工Φ39mm、SΦ48mm、R9mm、Φ35mm、锥度为10度的外圆、Φ52mm等
车床
2
车右端面,加工Φ25mm×33mm、切退刀槽、加工螺纹M25mm×1.5mm等
车床
2.工步的划分
因为每一把刀在粗加工的背吃刀量一致,在精加工中背吃刀量相同,不易划分工歩;这里选用加工不同的表面来划分工序就比较容易:
(1)毛坯先夹持左端,车右端轮廓113mm处,右端加工Φ39mm、SΦ48mm、R9mm、Φ35mm、锥度为10度的外圆,Φ52mm;
(2)装夹已加工Φ52mm外圆,左端加工Φ25mm×33mm、切退刀槽、加工螺纹M25mm×1.5mm.
该典型轴加工顺序为:
预备加工---车端面---粗车右端轮廓---精车右端轮廓---切槽---工件调头---车端面---粗车左端轮廓---精车左端轮廓---切退刀槽---粗车螺纹---精车螺纹。
(四)确定加工顺序及进给路线
1.零件加工必须遵守的安排原则
(1)基面先行工面基准为后刀面的加工提供基准面,所以应该先平左端面作为基准面;
(2)先主后次所加工的表面均为重要表面所以按照从左到有的顺序;
(3)先粗后精削去大部分的金属余量再进行成型切削,保证零件的尺寸要求和质量要求;
(4)先面后孔工零件左端面,再加工零件内孔
2.进给路线
编程时,为了保证被加工零件的精度和表面粗糙度能达到工件图样的要求,精加工的进给路线基本上都是沿其零件轮廓图顺序进行。
其确定原则为:
在保证加工质量的前提下,使加工程序具有最短的进给路线,即最短的空行程路线和切削进给路线,使数值计算简单,以减少编程工作量。
(五)选择刀具
1.车端面:
选用硬质合金45度车刀,粗、精车用一把刀完成。
2.粗、精车外圆:
(因为程序选用G71循环所以粗、精车选用同一把刀)硬质合金90度放型车刀,Kr=90度,Kr'=60度;E=30度,(因为有圆弧轮廓)以防与工件轮廓发生干涉,如果有必要就用图形来检验。
3.车槽:
选用硬质合金车槽刀(刀长12mm,刀宽3mm)。
4.车螺纹:
选用60度硬质合金外螺纹车刀。
表4刀具卡片
产品名称或代号
零件名称
典型轴
零件图号
序号
刀具号
刀具规格名称
数量
加工表面
备注
1
T01
硬质合金端面45度车刀
1
粗、精车端面
2
T02
硬质合金90度放型车刀
1
粗、精车外轮廓
左偏刀
3
T03
硬质合金车槽刀
1
切槽
4
T04
60度硬质合金外螺纹车刀
1
粗、精车螺纹
(六)切削用量的选择
要遵循粗加工转速要低,精加工转速要高的基本原则。
加工材料45#钢,Φ55mm×150mm。
加工后的要求:
车削后零件的便面粗糙度为Ra1.6μm,同轴度为φ0.025μm。
用CK6142车床进行加工,粗加工时用三爪卡盘自定心装夹,精加工用软爪。
表5切削用量选择
主轴转速s/(r/min)
进给量f/(mm/r)
背吃刀量ap/mm
粗车外圆
800
0.1
1.5
精车外圆
800
0.05
0.2
粗车螺纹
70
1.5
0.4
精车螺纹
70
1.5
0.1
切槽
115
0.04
1.背吃刀量的选择
选择背吃刀量
:
背吃刀量是根据粗、精加工要求、已知的加工余量及加工系统刚性和机床功率来确定。
加工:
‥‥‥‥‥‥‥‥‥‥‥量填入数控加工工序卡中,如下表所示工件加工余量3mm,分为粗加工和精加工两次走到,粗加工余量取2.5mm,由于加工余量只有2.5mm,故可一次走到完成。
精加工余量为
=(55-52.5)/2=0.25mm,粗车毛坯,可以选择YT15硬质合金车刀。
2.主轴转速的选择
车直线和圆弧轮廓时查表取粗车的切削速度
,精车的切削速度
。
而主轴转速根据毛坯直径计算,并结合车床说明书选取:
粗车时,取主轴转速
;精车时,取主轴转速
。
车螺纹时取主轴转速
。
3.进给量的选取
在粗车碳素钢材料时根据附表三,刀杆的尺寸为16×25mm、a
=2.5mm,及工件的直径为55mm,f=0.5mm-0.7mm/r。
4.进给速度的选取
粗车时,选择
,精车时,取
,计算得:
粗车进给速度
;精车进给速度
。
车螺纹的进给量等于螺纹螺距,即
。
(七)编制数控加工工艺卡
将各工序、工序内容、所用刀具和切削用量填入数控加工工序卡中,如下表所示:
表6数控加工工艺卡
单位名称
产品名称或代号
零件名称
零件图号
典型轴
工序号
程序编号
夹具名称
使用设备
车间
001
O1111
三爪自定心卡盘
CK6142
数控车间
工步号
工步内容
刀具号
刀具规格
主轴转速r/min
进给速度mm/r
背吃刀量mm
备注
1
车端面
T01
45度刀
500
0.1
手动
2
粗车外轮廓
T02
90度防型刀
800
0.1
1.5
自动
3
精车外圆轮廓
T02
90度防型刀
800
0.05
0.2
自动
4
切槽
T03
切槽刀
115
0.04
自动
工序号
程序编号
夹具名称
使用设备
车间
002
02222
三爪自定心卡盘
CK6142
数控车间
工步号
工步内容
刀具号
刀具规格
主轴转速r/min
进给速度mm/r
背吃刀量mm
备注
1
车端面
T01
45度刀
500
0.1
手动
2
粗车外轮廓
T02
90度防型刀
800
0.1
1.5
自动
3
精车外圆轮廓
T02
90度防型刀
800
0.05
0.2
自动
4
切退刀槽
T03
切槽刀
115
0.04
自动
5
粗车螺纹
T04
60度外螺纹刀
70
1.5
0.4
自动
6
精车螺纹
T04
60度外螺纹刀
70
1.5
0.1
自动
编制
审核
批准
年月日
共页
第页
(八)编写数控加工程序
1.建立工件坐标系
图7坐标系设定
2.手工编程
(1)加工工件右端
O1111;
M06X200Z100;建立工件坐标系
T0202;调用2号刀
M03S800;主轴以800r/min正转
G00X60Z5;到循环加工起点
G71U.1.5R1P01Q02X0.2Z0.08F80;粗加工循环
N01G00X39Z2;到精加工起点
G01X39Z0F40;精加工轮廓开始
G01X39Z0C2倒角C2
Z-26;加工Φ39
G03X35Z-56.46R24;加工SΦ48圆弧
G02X35Z-70R9;加工R9圆弧
G01Z-75;加工Φ35
X45.29;加工Φ35外径左端面至斜
线部分
X52Z-94;加工斜线部分
N02Z-113;精车循环结束
G00X55Z100;到换刀点
M06T0303M03S115M08;换3号切槽刀,打开切削液
G00X55Z2;刀具起切的安全点
G00X55Z-89;切槽切入点
G01X39F5;切槽
G01X55F20;切槽退刀
G01Z-82;切槽切入点
G01X39F5;切槽
G01X55F20;切槽退刀
G00Z-18;切槽切入点
G01X35F5;切槽切入点
G01X50F20;切槽退刀
G00X55Z100M09;回换刀点,关闭切削液
M05;主轴停止
M30;程序结束
(2)加工工件左端
O2222
T0202M03S800;换2号外圆刀主轴800r/min
G00X55Z2;刀具起切的安全点
G71U1.5R1P01Q02X0.2Z0.08F80;外径粗精车循环
N01G00X50Z2;精车循环开始
G01X0Z0F40;开始加工
G01X24.7Z0C2;倒角
G01Z-33;车Φ25
G01X52Z-33C2;倒角
N02G01Z-35;精车循环结束
G00X100Z100;换刀点
M05;主轴停止
M30;程序结束
T0303M03S115;换3号切槽刀
G00X30Z2;刀具起切的安全点
G00Z-28;切槽切入点
G01X21F5;切槽
G01X30F20;退刀
G00X50Z100;回换刀点
M05;主轴停止
M30;程序结束
T0404M03S70;换4号螺纹刀
G00X25Z2;刀具起始安全点
G76C1A60X23.056Z-26K0.974U0.1V0.1Q0.4F1.5;
螺纹车削循环,C为精车次数,A为螺纹刀具角度,X为最终螺纹X轴小径,Z为最终螺纹Z轴长度,,K为牙型高,U精加工余量,V最大加工量,Q第一刀最大背吃刀量,F为导程
G01X40;退刀
G00X100Z100;回换刀点
M05;主轴停止
M30;程序结束
三、数控仿真系统
图8数控机床
图9车床工件测量
图10坐标点测
图11剖面图测量
图12华中数控世纪星机床面板操作
结论
此次设计主要涉及的技术问题有零件的加工工艺性分析、零件的装夹、工艺路线的制订、工序与工步的划分、刀具的选择、切削用量的确定以及车削加工程序的编写。
通过这次设计可以使我们学会对相关学科中的基本理论、基本知识进行综合运用,同时使对数控技术有较完整、系统的认识,从而达到巩固、扩大、深化所学知识的目的,培养和提高综合分析问题和解决问题的能力,以及培养科学的研究和创造能力。
但是,设计中仍然有不足的地方,例如编程误差的解决问题。
编程阶段的误差是不可避免的,误差来源主要有三种形式:
近似计算误差、插补误差、尺寸圆整误差,直接影响加工尺寸精度,本次加工主要误差是计算误差与圆弧相切的切点坐标及未知交点坐标值。
我们是经过笔算获得的数值,存在着较大的误差。
为了尽可能的减少笔算误差,可以在AutoCAD上按其尺寸精度绘出零件图,再利用“工具”─→“查询”─→“点坐标”捕捉各圆弧切点坐标,其精度达到0.001级,这样能有效地将误差控制在(0.1~0.2)倍的零件公差值内。
参考文献
[1]邹新宇。
数控编程[M].清华大学出版社,2006年
[2]陈子银、徐鲲鹏.数控加工技术[M].北京理工大学出版社,2006年
[6]余英良.数控加工编程及操作[M].北京:
高等教育出版社,2004年第一版
[7]黄卫.数控技术与数控编程[M].北京:
机械工业出版社,2004年
[3]眭润舟.数控编程与加工技术[M].北京:
机械工业出版社,2006年第一版
[4]詹华西.数控加工技术实训教程[M].西安:
电子科技大学出版社,2006年
[5]陈富安.数控机床原理与编程[M].西安:
西安电子科技大学出版社,2004年第一版
[8]李家杰.数控机床编程操作与操作实用教程[M].南京:
东南大学出版社,2005年
[9]华茂发.数控机床加工工艺[M].北京:
机械工业出版社,2000年
[10]黄康美.数控加工实训教程[M].北京:
电子工业出版社,2004年
谢辞
通过本次的毕业设计,让我深刻的体会到什么是“学以致用”。
这段时间里我们以小组为单位,遇到问题一起分析,找出问题的关键所在,使我们有问题能及时提出来,找到解决问题的方法,如果实在不懂的就请教老师。
在设计中我们从中学到了许多以前没有学到的知识以及解决问题的方法,同时也体会到了组员的团队合作精神、学习钻研精神对顺利完成此设计的重要。
饮其流时思其源,成吾学时念吾师。
能够顺利完成本次设计,首先要感谢我的父母,是他们让我有了求学的机会,其次要感谢学校三年来对我的精心培养,使我能顺利完成学业。
在此,特别要感谢我们的设计指导老师张康老师,他为我们的设计花费了很多时间和心血。
本次设计是在我们设计小组的共同努力下完成的,在此向与我一起参与设计的其他同学表示感谢。
在设计过程中还借鉴了其他学者、前辈的有关技术资料,学校的图书馆也为我们提供了许多宝贵的参考资料,同窗的学友、舍友也对我们的设计提出了许多宝贵的意见和建议,在此一并致谢。
附录
附表一断削槽宽度
进给量f/mm×r
背吃刀量a
/mm
断削槽宽L
低碳钢、中碳钢
合金钢、工具钢
0.3—0.5
0.3—0.5
0.3—0.6
1—3
2—5
3—6
3.2—3.5
3.5—4.0
4.5—5.0
2.8—3.0
3.0—3.2
3.2—3.5
附表二硬质合金
工件材料
刀具材料
楔角
后角
主偏角
刃倾角
副偏角
副后角
刀尖圆弧半径
低碳钢(A3)
YT5
YT15
20—30°
5—10°
45—90°
0—5°
6—10°
6—8°
0.2—1°
中碳钢45钢正火
YT5
YT15
15—20°
5—8°
45—90°
-5—5°
6—10°
4—6°
0.2—1°
中碳钢45钢调制
YT15
YT30
10—15°
5—8°
45—90°
-5—5°
6—10°
4—5°
0.2—1°
合金钢40Gr正火
YT5
YT15
14—20°
6—8°
45—90°
-5—0°
6—10°
4—5°
0.2—1°
合金钢40调制
YT15
YT30
10—14°
5—8°
45—90°
-5—0°
6—10°
4—5°
0.2—1°
钢锻件45钢40Gr
YT5
YT15
10—14°
5—7°
45—90°
-5—0°
6—10°
4—6°
1—1.5°
不锈钢
YG6
YA6
15—