冲孔落料正装复合模具模具毕业设计.docx
《冲孔落料正装复合模具模具毕业设计.docx》由会员分享,可在线阅读,更多相关《冲孔落料正装复合模具模具毕业设计.docx(13页珍藏版)》请在冰豆网上搜索。
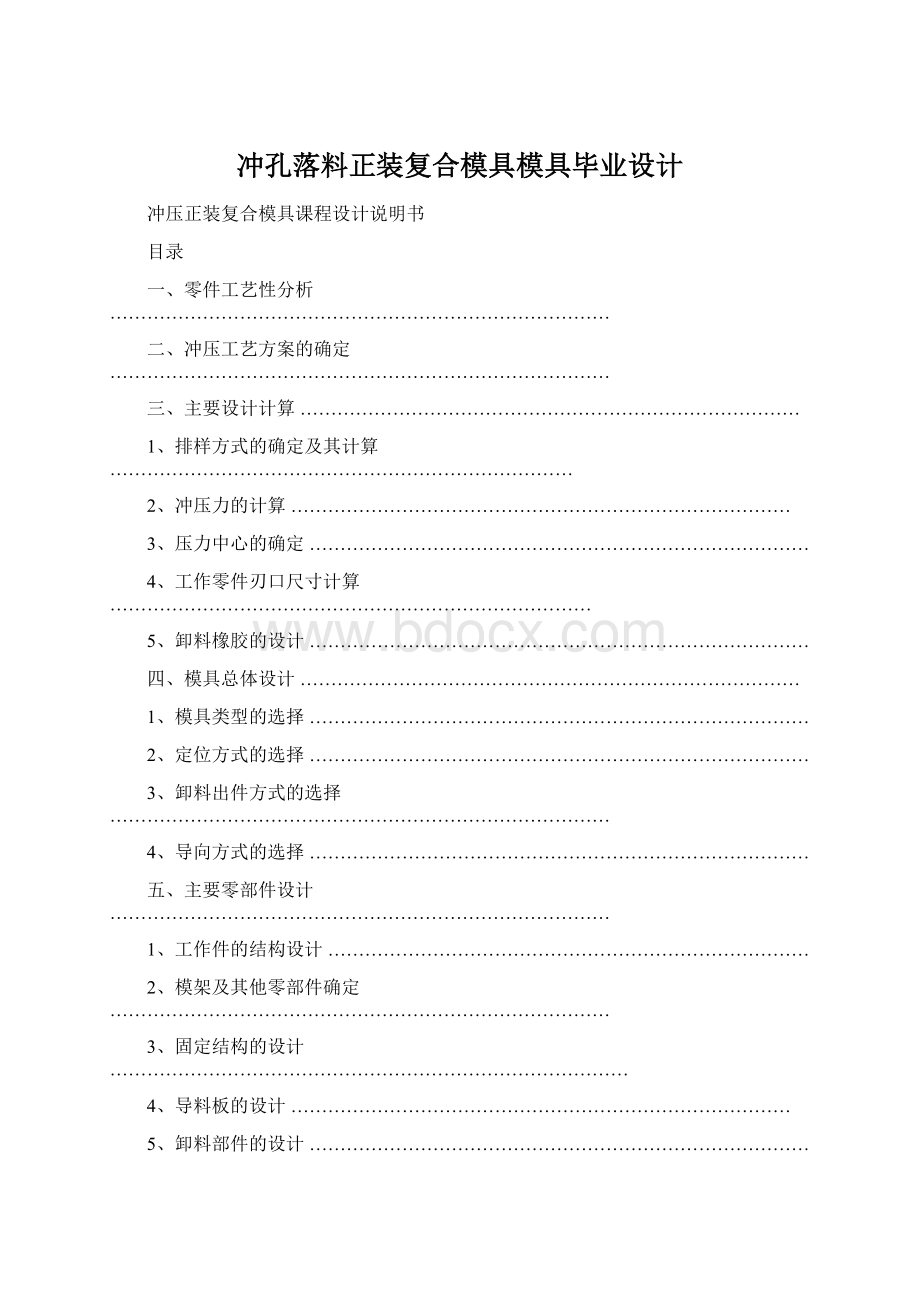
冲孔落料正装复合模具模具毕业设计
冲压正装复合模具课程设计说明书
目录
一、零件工艺性分析………………………………………………………………………
二、冲压工艺方案的确定………………………………………………………………………
三、主要设计计算………………………………………………………………………
1、排样方式的确定及其计算…………………………………………………………………
2、冲压力的计算………………………………………………………………………
3、压力中心的确定………………………………………………………………………
4、工作零件刃口尺寸计算……………………………………………………………………
5、卸料橡胶的设计………………………………………………………………………
四、模具总体设计………………………………………………………………………
1、模具类型的选择………………………………………………………………………
2、定位方式的选择………………………………………………………………………
3、卸料出件方式的选择………………………………………………………………………
4、导向方式的选择………………………………………………………………………
五、主要零部件设计………………………………………………………………………
1、工作件的结构设计……………………………………………………………………
2、模架及其他零部件确定………………………………………………………………………
3、固定结构的设计…………………………………………………………………………
4、导料板的设计………………………………………………………………………
5、卸料部件的设计………………………………………………………………………
六、模具总装图………………………………………………………………………
七、冲压设备的选择………………………………………………………………………
八、参考文献:
………………………………………………………………………
九、三维图:
………………………………………………………………………
冲压正装复合模设计说明书
图1-1所示为焊片零件冲裁图,材料Q235钢板,厚度t=2mm,大批量生产,试确定冲裁工艺性,设计冲裁模。
图1-1
一、零件的工艺性分析
1.结构工艺性分析
1该零件形状简单,对称,是由圆弧和直线组成的的。
冲裁件内外形所能达到的经济精度为IT11~IT14,孔中心与边缘距离尺寸公差为±0.5mm。
将以上精度与零件的精度要求相比较,可认为该零件的精度要求能够在冲裁加工中得到保证,其他尺寸标注、生产批量等状况,也均符合冲裁的工艺要求,故决定采用冲压方式进行加工。
⒉分析公差和表面粗糙度
⑴公差该件上未标注特殊公差,全部按IT14级选用,低于冲孔可以达到的精度等级IT10。
⑵表面粗糙度零件图上无特殊要求。
⒊被冲材料为Q235,具有一定的冲裁性能。
二、冲压工艺方案的确定
该工件包括落料、冲孔两个基本工序,可以有以下三种工艺方案:
方案一:
先落料,后冲孔。
采用单工序模生产。
方案二:
冲孔—落料级进冲压。
采用级进模生产。
方案三:
冲孔落料复合模。
方案一模具结构简单,但需要两道工序两副模具,成本高且生产效率低,难以满足大批量生产要求。
复合模模具的形位精度和尺寸精度容易保证,且生产效率也高,尽管模具结构复杂,但由于模具零件的几何形状简单对称,模具制造并不困难。
级进模虽生产效率也高,但零件的冲裁精度稍差,欲保证冲压件的行为精度,需要在模具上设置导正销的导正,故模具安装制造教复合模复杂,通过对上述三种方案的比较,,该零件的冲压生产采用方案二的复合模为佳。
通过对上述三种方案的比较分析,该零件的冲压方案采用方案三为佳。
三、主要设计计算
1、排样方式的确定及计算
通过查表比较分析,且由经验得搭边值a=3mm,b=2.5mm,步距s=39mm,条料宽度B=41mm。
排样图如图1-2所示,材料利用率最高。
一个步距的材料利用率η=(nA/BS)x100%
A=2160—160—25.12=1974.88m㎡
S0=BS=60x41=2460(m㎡)n=1
所以η=1974.88/2460x100%=80.27%
查板材规格,取900x1800的钢板,每张钢板可剪裁为41x395=10(张)条料(41x3950)
图1-2
2、冲压力的计算
该模具采用级进模,选择弹性卸料、下出件。
由F=KLtτb
F-冲裁力L-冲减周边长度t-材料厚度τb-抗剪强度
K-考虑模具间隙的不均匀、刃口的磨损、材料力学性能与厚度的波动等因素引入的修正系数,一般取K=1.3
F总=F+F卸+F推F压=1.3F总
t=2mm
查表得σb=450MPa
所以冲裁力F=F冲+F落=(4x3.14+24)x2x450/1000+192x2x450/1000=205.71KN
由卸料力F卸=K卸FF推=nK推F
K卸、K推—卸料力系数、推件力系数查表得K卸取0.03,K推取0.05
n-同时卡在凹模孔口的冲件数取n=1,
所以有F卸=0.03x172.8=5.184kNF推=0.05x32.909=1.645kN
所以有F总=F+F卸+F推=205.71+5.184+1.645=212.54KN
F压=1.3xF总=1.3x212.54=270.3KN
3、压力中心的确定
冲裁件是中心对称图形,所以压力中心位于零件的几何中心。
如图所示:
图1-3
4、工作零件刃口尺寸计算
在刃口尺寸计算时需注意:
设计落料模时应先确定凹模刃口尺寸,间隙取在凸模上,冲裁间隙通过减小凸模尺寸获得。
设计冲孔模时应先确定凸模刃口尺寸,间隙取在凹模上,冲裁间隙通过减小凹模尺寸获得。
查表确定初始间隙Zmax=0.360mmZmin=0.246mm∆Z=Zmax-Zmin=0.360-0.246=0.114mm
1计算冲孔模刃口尺寸:
冲孔模形状简单,可以用分别制造法计算:
δ凸=0.02mmδ凹=0.02mm
冲孔凸模一:
d1凸=(4+X∆)0-δ凸查表得:
x=0.5
d1凸=(4+0.5x0.3)0-0.02=4.150-0.02
d1凹=(4+X∆+Zmin)0+δ凹=4.3960+0.02
冲孔凸模二;
d2凸=(4+X∆)0-δ凸查表得:
x=0.5
d2凸=(4+0.5x0.3)0-0.02=4.150-0.02
d2凹=(4+X∆+Zmin)0+δ凹=4.3960+0.02
d3凸=(8+X∆)0-δ凸查表得:
x=0.5
d3凸=(8+0.5x0.36)0-0.02=8.180-0.02
d3凹=(8+X∆+Zmin)0+δ凹=8.4260+0.02
2.计算落料模刃口尺寸:
落料模形状简单,也用分别制造法制造模具刃口。
δ凸=0.02mmδ凹=0.03mm
D1凹=(36—X∆)0+δ凹查表得:
x=0.5
D1凹=(36—X∆)0+δ凹=35.690+0.03
D1凸=(36-X∆—Zmin)0-δ凸=35.4440-0.02
D2凹=(60—X∆)0+δ凹查表得:
x=0.5
D2凹=(60—X∆)0+δ凹=59.690+0.03
D2凸=(60—X∆—Zmin)0-δ凸=59.4440-0.02
四、模具总体设计
1、模具类型的选择
由冲压工艺分析可知,采用复合冲压,所以模具类型为复合模。
2、定位方式的选择
因为该模具采用的是条料,控制条料的送进方向采用导料销,无侧压装置。
控制条料的送进步距采用定位销。
3、卸料、出件方式的选择
因为工料厚度为2mm,相对较薄,卸料力也比较小,故可采用弹性卸料。
又因为是复合模生产,所以采用上出件比较便于操作与提高生产效率。
4、导向方式的选择
为了提高模具寿命和工作质量,方便安装调整,该复合模采用中间导柱的导向方式。
导向方式如图1-4.
图1-4
五、主要零部件的设计
(一)确定凸模外形尺寸:
凸模包括两种一个落料凸模和七个冲孔凸模。
对于落料凸模采用固定板固定,对于冲孔凸模应做成台阶式。
该模具采用顶件装置卸料,因此,凸模长度L:
L=h1+h2+t
h1凸模固定板厚度
h2落料凹模厚度
t垫板高度
所以1.冲压圆形凸模1:
L=h1+h2+t=14+20+12=46mm
2冲压矩形凸模2:
L=h1+h2+t=14+20+12=46mm
(二)确定凹模板的外形尺寸
凹模采用正式凹模,安排凹模在模具上的位置时,要依据计算压力中心的数据,将压力中心与模柄中心重合。
1由排样图确定各凹模型孔位置
凹模型孔位置如下图1-3所示
2确定凹模外形尺寸
凹模厚度:
H=ks(不小于15mm)
查表得k=0.3s=60
H=0.3x60=18=20(圆整)
垂直于送料方向的凹模宽度B:
B=s+(2.5~4)H=60+(2.5~4)x20=125(圆整)
送料方向上的凹模长度L:
L=s1+ks2=36+2x30=100(圆整)
凹模整体标准化,取为125mmX100mmX20mm
图1-4
(三)凸凹模的设计
本模具为复合冲裁模,除了冲孔凹模和落料凹模外,还有一个凸凹模。
根据整体模具的结构设计需要,凸凹模的结构简图应该如图所示。
确定凸凹模安排在模架上的位置时,要依据计算的压力中心的数据,使压力中心与模具中心重合。
校核凸凹模的强度,采用正装复合模,强度要求不高,故符合强度要求。
凸凹模刃口尺寸按落料凹模尺寸配置,并保证双面间隙为0.246~0.36。
(三)、卸料弹簧的设计
(1)根据模具结构初选4根弹簧,每根弹簧的预压力为:
Fo≥F卸/n=5.184x103/4=1296N
(2)该模具卸料板的工作形成h工和凸凹模的修模量h修模之和为
h工+h修模=1+2+4=7mm
(3)选取36号压簧,工作极限负荷1700N,外径30mm,钢丝直径6mm,自由长度60mm
(4)最大允许压缩量
hj=h0—h预=60—13.1=46.9mm
(5)预压缩量
h预=1296/1700x46.9=35.75mm
(6)总压缩量
h总=35.75+7=42.75mm
(7)总压力
F总=1296x42.75/35.75=1549.76N
工作极限负荷大于总压力,所以弹簧满足要求。
所以选用选取36号压簧,工作极限负荷1700N,外径30mm,钢丝直径6mm,自由长度60mm
2、模架及其他零部件的确定
以凹模周界尺寸为依据,再结合压力机最大闭合高度,选择模架规格。
所以有导柱d*L为别为22*125、25*125导套d*L分别为22*70*35、25*70*38.
取上模座厚度H=35mm,上模垫板厚度H=6mm,固定板厚度H=16mm,下模座厚度H=42mm,所以有,该模具的闭合高度为H=163mm
可见该模具闭合高度小于所选压力机J23-10的最大装模高度(180mm),可以使用。
所以有上模座尺寸:
125*100*35下模座尺寸:
125*100*42垫板:
125*100*6
凹模板:
125*100*20凸模固定板:
125*100*16
3、固定结构的设计
采用12*M8的螺钉,4*直径8的销钉固定。
4导料销的设计
两个导料销设在同侧,条料沿着两个导料销确定的直线送进。
由挡料销控制送料步距,在上模设置对应的导正孔,固定在凹模板中。
5、卸料部件的设计
1*卸料板的设计
卸料板的周界尺寸与凹模板的周界尺寸相同,厚度为8mm即尺寸为:
125*100*8
卸料板采用45钢制作,淬火硬度为40HRC~45HRC。
2*卸料螺钉的选用
卸料板上设置4个卸料螺钉,公称直径为10,螺纹部分为M8.卸料钉尾部应留有足够的行程空间。
卸料螺钉拧紧后,应使卸料板超出凸模端面1mm,有误差时通过在螺钉与卸料板之间安装垫片来调整。
六、模具总装图
通过以上设计,可得到如图1-5所示的模具总装图。
模具上部分主要由上模板、垫板、凸模(7个)、凸模固定板及卸料板组成。
卸料方式采用弹性卸料,以橡胶为弹性元件。
下模部分由下模座、凹模板、导料销组成。
冲孔废料由打料杆卸下,工件由顶件装置顶出。
图1-5
七、设备的选定
通过校核,选择开式双柱可倾压力机J23-25能满足要求。
其主要技术参数如下:
工称压力为100KN,滑块行程为45mm,最大闭合高度为180mm,最大装模高度为180mm,工作台尺寸为240*370mm,垫板尺寸为35x125,最大倾斜角度为30o
八、参考文献:
1、冲压工艺与模具设计机械工业出版社原红玲主编
2、模具制造技术化学工业出版社翟德梅主编
3.冲压手册机械工业出版社王孝培主编
4、中国模具设计大典机械工业出版社王孝培主编
九、三维图
1装配图三维图
2凸凹模三维图
3下模座三维图
4凹模板三维图