阀体工艺工装设计说明书.docx
《阀体工艺工装设计说明书.docx》由会员分享,可在线阅读,更多相关《阀体工艺工装设计说明书.docx(18页珍藏版)》请在冰豆网上搜索。
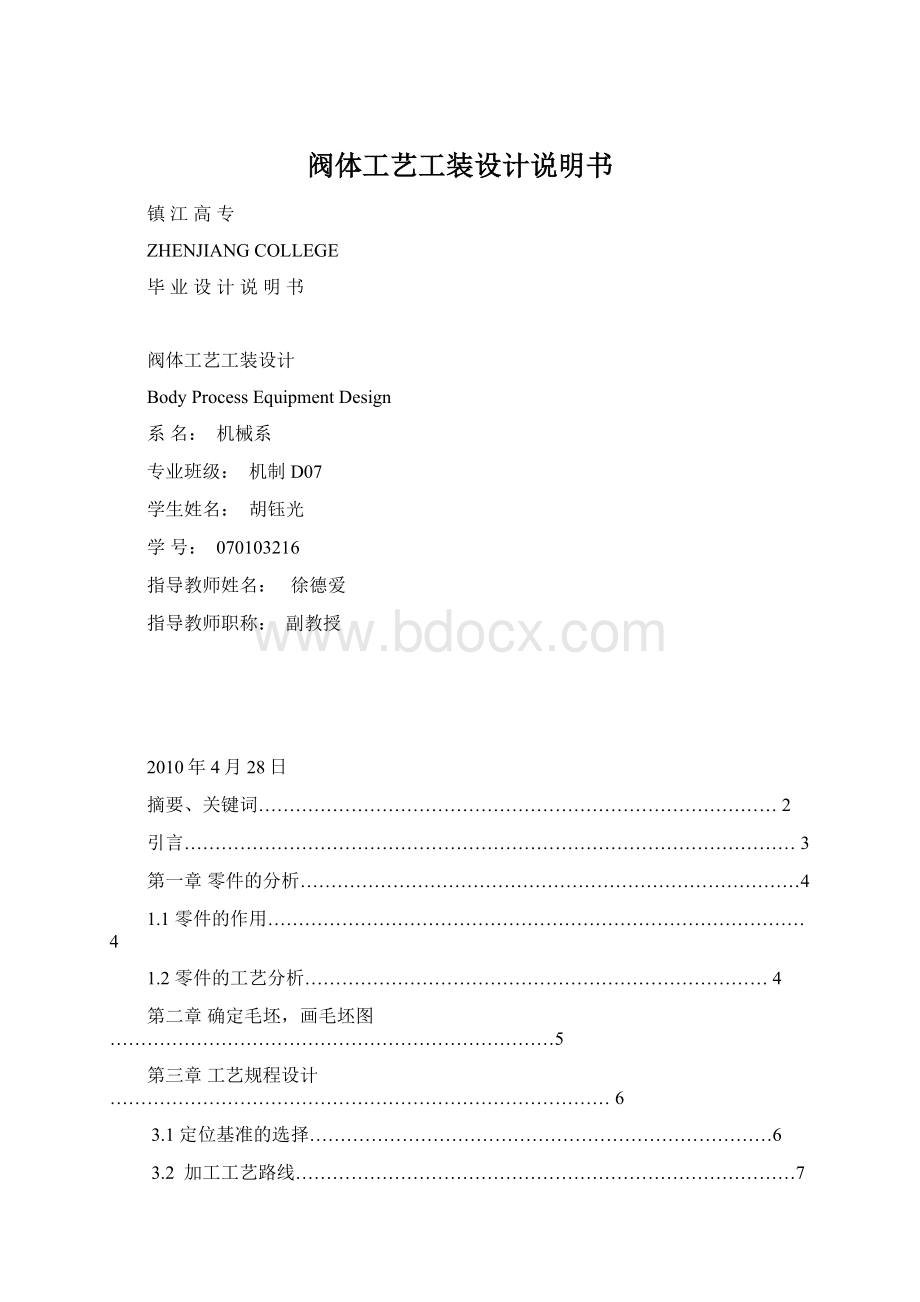
阀体工艺工装设计说明书
镇江高专
ZHENJIANGCOLLEGE
毕业设计说明书
阀体工艺工装设计
BodyProcessEquipmentDesign
系名:
机械系
专业班级:
机制D07
学生姓名:
胡钰光
学号:
070103216
指导教师姓名:
徐德爱
指导教师职称:
副教授
2010年4月28日
摘要、关键词…………………………………………………………………………2
引言………………………………………………………………………………………3
第一章零件的分析………………………………………………………………………4
1.1零件的作用……………………………………………………………………………4
1.2零件的工艺分析…………………………………………………………………4
第二章确定毛坯,画毛坯图………………………………………………………………5
第三章工艺规程设计………………………………………………………………………6
3.1定位基准的选择…………………………………………………………………6
3.2加工工艺路线………………………………………………………………………7
3.3选择加工设备及刀、夹、量具…………………………………………………7
3.4加工工序设计……………………………………………………………9
3.5时间定额计算………………………………………………………………………14
第四章夹具设计………………………………………………………………………14
4.1第40道工序的夹具设计……………………………………………………14
4.2第70道工序的夹具设计……………………………………………15
结论…………………………………………………………………………………………16
致谢……………………………………………………………………………………………17
参考文献………………………………………………………………………………………18
阀体工艺工装设计
班级:
机制D07学生姓名:
胡钰光
指导老师:
徐德爱职称:
副教授
摘要:
现代机械加工行业发生着深刻的结构性变化,工艺工装的设计与改良已成为相关企业生存和发展的必要条件。
动力装置行业作为一个传统而富有活力的行业,近十几年取得了突飞猛进的发展。
在新经济时代,这一行业呈现了新的发展趋势,由此对其动力装置的质量、性能产生了新的变化。
支座作为动力装置的主要零件,工艺工装的设计与改良直接影响着其质量与性能。
本文首先介绍了阀体的作用和工艺分析,其次确定毛坯尺寸,然后进行了工艺规程设计,最后对第80道工序和第100道工序进行了夹具设计。
关键词:
零件分析工艺规程设计加工工序设计夹具设计
Abstract:
Themodernmachine-finishingprofessionishavingtheprofoundconstitutivechange,thecraftworkclothes'designandtheimprovementhasbecometherelatedenterprisesurvivalandthedevelopmentessentialcondition.Thepowerunitprofessiontakesatradition,buttherichvigor'sprofession,intherecentseveralyearshasmadetheprogresswhichprogressesbyleapsandbounds.Intheneweconomicaltime,thisprofessionhaspresentedtherecenttrendofdevelopment,fromthistoitspowerunit'squality,theperformancehashadthenewchange.Supportaspowerunitmajorparts,craftworkclothes'designandimprovementimmediateinfluenceitsqualityandperformance.thisarticlefirstintroducedsupport'sfunctionandtheprocessstudy,nextthedefiniteblankdimension,thenhascarriedonthetechnologicalprocessdesign,finallyhascarriedonthejigdesigntothe80thworkingprocedureandthe100thworkingprocedure.
keywords:
ComponentsanalysisTechnologicalprocessdesignWorkingprocessdesignJigdesign
引言
制造业的历史可追溯到几百万年前的旧石器时代。
猿进化成人的一个重要的标志就是工具的制造。
可见,工具的制造对人类的影响是极其巨大的。
从某种程度上说,工具的先进水平决定着生产力的高低。
社会的发展与变革,是伴随着劳动工具的发展与变革。
制造业是任何一个发达国家的基础工业,是一个国家综合国力的重要体现。
而在制造业中,夹具工业又是制造业的基础,得到了各个国家的高度重视。
尤其在今天以知识为驱动的全球化经济浪潮中,由于激烈的市场竞争,夹具工业的内涵、深度和广度都发生着深刻的变化,各种新的夹具设计、制造加工方法不断出现,推动着我们的社会不断的向前发展。
夹具工业是现代工业的基础。
它的技术水平在很大程度上决定了产品的质量和市场的竞争力。
随着我国加入“WTO”步伐的日益加快。
“入世”将对我国夹具工业产生重大而深远的影响,经济全球化的趋势日益明显,同时世界众多知名公司不断进行结构调整,国内市场的国际性进一步显现,该行业将经受更大的冲击,竞争也会更加剧烈。
在如此严峻的行业背景下,我国的技术人员经过不断的改革和创新使得我国的模具水平有了较大的提高,大型、复杂、精密、高效和长寿命的夹具又上了新台阶。
夹具是每个机制制造方面目前普遍用的,它可以大批量生产,节省人力物资,效率相对高,操作方便,结构合理,它的成本低廉,适合广大人群所承受的能力。
毕业设计是学生从学习向工作过度的综合锻炼,也是一次提高和再学习的机会。
毕业设计从准备到设计结束几乎要花去一个学期的时间,最后要形成一整套的文档资料。
毕业设计也是对学生最后的综合考核,因此,扎实认真高质量的完成毕业设计任务,具有重要意义!
1.通过毕业设计的准备工作,进一步提高我们独立调研能力以及专业业务素质。
并通过文献查阅、现场收集资料等工作。
锻炼解决夹具工程技术的问题的能力。
2.能巩固深化扩充我们的专业知识,并通过毕业设计中对涉及到的问题的分析研究,提出我们自己的见解和观点。
3.通过毕业设计,树立良好的工作思想和细致、严谨、科学的工作态度,为一个未来的工程师奠定基础!
这次设计使我能综合运用机械制造工艺学中的基本理论,并结合生产实习中学到的实践经验知识,独立的分析和解决工艺问题,初步具备了设计一个中等复杂程度零件的工艺规程的能力和运用夹具设计的基本原理和方法,拟订夹具设计方案,完成夹具结构设计的能力,为未来从事的工作打下良好的基础。
由于能力所限,经验不足,设计中还有许多不足之处,希望各位老师多加指教。
第一章零件的分析
1.1零件的作用
阀体的作用是把油泵所输出的液压油分配给各元件,以控制各离合器和制动器的接合和分离,从而达到自动换档的目的。
图1所示
图1阀体
1.2零件的工艺分析
由零件图得知其材料为ZQ25。
该材料具有较高的强度,耐磨性,耐热性及减振性;适用于承受较大应力,要求耐磨的零件。
该零件上的主要加工Q面、R面、N面和B面,M36×2-6g端面,4XM12-7H螺纹孔,Φ20孔,Φ28.5孔,割槽Φ24.3和M24×1.5-7H螺纹孔。
Q面和N面都是设计基准,Φ22mm孔、Φ18H11孔内壁要求的精度较高,Φ24.3mm退刀槽要用镗,M24×1.5-7H、4XM12-7H内螺纹,要在车床或钻床上攻,Φ50H7、Φ43mm和Φ35mm孔直径太大,铸造时要留底孔,而且Φ50H7和Φ43mm孔要在车床上镗,加工时要注意各个孔的同轴度,虽然没有要求,但也不能有太大的偏差,否则安装的时候可能装不上去,所以在加工轴线在同一直线上时,最好能在一次装夹下将孔同时加工出来。
由参考文献
(1)中有关面和孔加工的经济精度及机床能达到的位置精度可知,上述技术要求是可达到的,零件的结构工艺性也是可行的。
第二章确定毛坯,画毛坯图
在拟订机械加工工艺规程时,毛坯选择得是否正确,不仅直接影响毛坯的制造工艺及费用,而且对零件的机械加工工艺、设备、工具以及工时的消耗都有很大影响。
毛坯的形状和尺寸越接近成品零件,机械加工的劳动量就越少,但毛坯制造的成本可能会越高。
由于原材料消耗的减少,会抵消或部分抵消毛坯成本的增加。
所以,应根据生产纲领、零件的材料、形状、尺寸、精度、表面质量及具体的生产条件等作综合考虑,以选择毛坯。
在毛坯选择时,应充分注意到采用新工艺、新技术、新材料的可能性,以降低成本、提高质量和生产率。
毛坯的种类包括:
铸件、锻件、型材、冲压件、冷或热压制件、焊接件等。
合理的选择毛坯,通常从下面几个方面综合考虑:
1、零件材料的工艺特性;2、生产纲领的大小;3、零件的形状和尺寸;4、现有的生产条件。
根据零件材料确定毛坯为铸件。
通过计算,该零件质量约为3.5kg。
由参考文献(5)表1-4、表1-3可知,其生产类型为大批量生产,毛坯的铸造方法选用砂型铸造。
又由于主轴Φ50H7、Φ43孔和Φ35孔均需铸出,故还应安放型芯。
此外,为消除残余应力,铸造后应安排人工时效。
参考文献
(1)表3.1-24铸件的分型面选择通过Φ43轴线,且与底面垂直的面。
浇冒口位置在底面。
参考文献
(1)表2.3-6,该种铸件的尺寸公差等级CT为8-10级,加工余量等级MA为H级,故取CT为10级,MA为H级。
参考文献
(1)表2.3-5,用查表法确定各表面的总余量如表2-1所示。
表2-1各加工表面总余量
加工表面
基本尺寸(mm)
加工余量等级
加工余量数值
说明
R面
75
G
4
侧面单侧加工
Q面
75
H
4
侧面单侧加工
C面
36
G
3
N面
56
G
3
B面
2
G
5
φ43孔
43
G
4
双侧加工
φ35H11孔底
41
G
3
φ35H11孔壁
35
G
3
双侧加工
φ50H7孔底
5
H
3
φ50H7孔壁
50
H
3
双侧加工
表2-2主要毛坯尺寸及公差:
(mm)
主要面尺寸
零件尺寸
总余量
毛坯尺寸
公差CT
Q面和R面之间的距离
75
8
83
6
N面距φ50孔中心尺寸
56
4
60
4
φ50H7孔
φ50
4+4
φ42
4
φ35孔
φ35
3+3
φ29
5
第三章工艺规程设计
3.1定位基准的选择
精基准的选择:
选择精基准的出发点是保证加工精度和装夹方便。
特别是加工表面的相互位置精度,以及安装的方便可靠。
其选择的原则如下:
1、基准重合原则;
2、基准统一原则;
3、自为基准原则;
4、互为基准原则;
5、保证工件定位准确、夹紧可靠、操作方便的原则。
加工阀体,通过了解零件结构特点和加工精度要求,可以选定面(Q)、4×M12-7H螺纹孔为精基准。
Q面和4×M12-7H螺纹孔既是装配基准又是设计基准,用他们作为精基准,能使加工实现“基准重合”的原则,实现阀体零件“一面两孔”的典型定位方式,其余各面和孔也能用它们定位,这样使工艺路线遵循了“基准统一”的原则。
此外Q面得面积较大,定位比较稳定,加紧方案也比较简单、可靠、操作方便。
粗基准的选择:
粗基准为零件起始粗加工所应用的基准,它是未经加工过的表面。
其选择原则如下:
1、为了保证加工面与不加工面之间的位置要求,应选择不加工面为粗基准;
2、为保证各加工面都有足够的加工余量,应选择毛坯余量最小的面为粗基准;
3、为保证各加工面的加工余量,应选择重要加工面为粗基准;
4、粗基准应避免重复使用,在同一尺寸方向上,通常只允许使用一次;
5、选作粗基准的表面,应尽可能平整光洁,不能有飞边、冒口或其他缺陷,以便定位准确,加紧可靠。
加工阀体,通过了解零件结构特点和加工精度要求,可以选定Φ43孔外圆、侧面等不加工面为粗基准。
例如:
选定Φ43孔外圆作为粗基准,用V型块定位限制工件3个自由度,定位比较稳定,夹紧方案比较简单。
最先进行机械加工的是精基准Q面和4×M12-7H螺纹底孔经过分析选择定位夹紧方案是:
在阀体的外壁用短的V型块限制两个自由度,用三个支撑钉在R的毛坯面上限制三个自由度,用一头带螺纹的圆柱销伸入Φ43mm毛坯孔中限制一个自由度,虽然有过定位,但在加工过程中对加工精度没有影响。
其次加工的是R面和M36×2-6g螺纹面。
方案:
方案和上类似,同样是一个固定V型块固定Φ43孔的外壁,用活动V型块固定其右侧,其限制了1个自由度,再以一个平面限定Q面,其限制了其3个自由度,为了保证六个自由度的,用一个支撑钉固定其前后晃动,从而满足其要求。
3.2加工工艺路线
根据个表面的加工要求和各种加工方法能达到的经济精度,确定各表面的加工方法如下:
R面、C面、倒角C1.5:
粗车;Φ24.3槽、Φ50H7孔、Φ35mm、Φ43孔:
粗镗;Φ20mm、Φ28.5mm、Φ26mm孔:
钻;Φ22mm、Φ18mm孔:
钻——铰;4×M12-7H和M24×1.5-7H螺纹:
钻——攻螺纹;M36×2-6g螺纹:
粗车——攻螺纹;A、D台阶B、N面:
粗铣;
阀体的孔较多,而且都是同轴的,所以它们的加工尽量采用工序集中的原则,即分别在一次装夹下将两面或两孔同时加工出来,以保证其位置精度。
根据先面后孔、先主要表面后次要表面和先粗加工后精加工的原则,将Q面、R面、B面及Φ50H7孔的粗加工放在前面,精加工放在后面,每一阶段中又首先加工Q面后再加工4×M12-7H的螺纹,N面、B面、Φ50H7孔、Φ24.3mm、Φ28.5mm孔等次要放在最后面加工。
经过分析确定加工工艺过程如表3-1.
3.3选择加工设备及刀、夹、量具
由于生产类型为大批生产,故加工设备宜以通用机床为主,辅以少量专用机床。
其生产方式为通用机床加专用夹具为主,辅以少量专用机床的流水生产线。
工件在各机床上的装卸及各机床的传送均由人工完成。
30mm,材料是硬质合金钢(参考文献﹤1﹥表4.2-2),专用夹具和游标卡尺。
粗镗φ50H7和φ43mm、φ35mm孔,采用CA6140卧式车床,参考文献﹤1﹥表4.3-63选择精镗刀其中B=12mm,H=20mm,L=150mm,l=150mm,d=12mm,采用专用夹具和游标卡尺。
表3-1加工工艺过程
工序号
工序内容
10
铸造
20
时效
30
粗铣Q面
40
粗车R面、C面及倒角C1.5
50
粗镗φ50H7、φ43mm、φ35mm孔
60
粗铣A面、D面、B面及N面
70
钻孔及攻螺纹4XM12—7H
80
车螺纹M36X2—6g
90
钻φ20mm、φ28.5mm孔
100
钻扩φ22mm、φ18mm孔
110
钻φ26mm孔、镗φ24.3mm的槽
120
钻孔及攻螺纹M24X1.5—7H
130
铣缺口
140
检验
150
入库
粗镗A面D面B面及N面。
选用卧式双面组合机床,采用功率为1.5KW的1TX20型铣削头(参考文献﹤1﹥表3.2-43).选择直径为φ100mm的B类可转位面铣刀(参考文献﹤1﹥表4.4-40),采用专用夹具和游标卡尺。
钻φ20mm、φ28.5mm、φ26mm孔.采用Z3540型摇臂钻床(参考文献﹤1﹥表3.1-30),选择锥柄长麻花钻(参考文献﹤1﹥表4.3-9),专用夹具,用专用量具测量。
钻扩φ22mm、φ18mm孔,仍选用Z3540摇臂钻床(参考文献﹤1﹥表3.1-30),选择锥柄长麻花钻(参考文献﹤1﹥表4.3-9),专用夹具,用专用量具测量。
粗镗φ24.3mm槽,选择Z3540摇臂钻床,其它的和镗φ43mm的孔相同。
钻孔及攻螺纹4XM12—7H和钻孔及攻螺纹M24X1.5—7H。
选用Z3540摇臂钻床,选用锥柄阶梯麻花钻(参考文献﹤1﹥表4.3-16),攻螺纹采用机用丝锥(参考文献﹤1﹥表4.6-4)及丝锥夹头,采用专用夹具,选用游标卡尺和塞规检查孔径。
车螺纹M36X2—6g,选择CA6140卧式车床(参考文献﹤1﹥表3.1-17),采用普通的螺纹刀,采用专用夹具,螺纹塞规。
3.4加工工序设计
3.4.1.工序30的粗铣Q面
加工Q面得粗糙度只需要粗铣一下就能达到,所以粗加工余量就等于总余量,已知Q面总余量ZQ总=4mm。
故粗加工余量ZQ粗=4mm。
查参考文献[6]表8.9,得粗加工公差等级为IT11-IT13,取IT=12.
参考文献[1]表2.4-73,取粗铣的每齿进给量
为0.15mm/z;粗铣走刀2次,
=2mm。
参考文献[1]表3.1-74,取粗铣的主轴转速为150r/min。
又前面已选定铣刀直径D为φ200mm,故相应的切削速度为
V粗=兀DN/1000=3.14×200×150/1000m/min=94.2m/min
校核机床功率(一般只校核粗加工工序)
参考文献[1]表2.4-96,得切削功率Pm=1076×10-5d-0.3apfz0.75ae1.1Zn0.8Kpm
取Z=10个齿,n=150/60=2.5r/s,ae=75mm,ap=2.0mm,fz=0.15mm/z,Kpm=1,d0=4mm
将他们代入式中得:
Pm=1076×10-5×4-0.3×2×0.150.75×751.1×10×2.50.8×1
=3.31kw
又由文献[1]表3.1-73得机床功率为7.5kw,若取功效为0.85,则7.5×0.85=6.357kw﹥3.31kw
3.4.2.工序40中粗车R面、C面及倒角C1.5
表面的加工精度不高,只要粗车一下就可以达到要求,所以其粗加工余量就等于总加工余量,既ZC粗=3mm,ZR粗=4mm
由文献[1]表2.4-3,取粗车的车刀进给量fR=0.4mm,apr=3mm,fc=0.4mm,apc=3mm
由文献[1]表2.4-20,得切削速度
VR=(38/600.8T0.2f0.8)KV=(38/600.8×2.70.2×0.40.8)×1=2.45m/s
Vc=(242/600.8T0.2ap0.15f0.35)KV=(242/600.8×2.250.2×30.15×0.40.35)×1=2.523m/s
取机床主轴的转速为1000r/min,所以
TR=18×60/1000×0.4=2.7s
Tc=15×60/1000×0.4=2.25s
取KV=1,将数据代入上式计算。
校核机床功率:
由文献[1]表2.4-21得切削功率Pm及主切削力Fz为:
Fz=9.81×60-0.8×270×3×0.40.75=2162.0N
Pm=FzV×10-3
=2162.0×2.523×10-3
=5.54kw
由文献[1]表3.1-17得车床功率为7.5kw,若取效率为0.85,则7.5×0.85=6.375kw﹥5.45kw
故机床功率足够。
3.4.3.工序120中的钻4×M12-7H的螺纹底孔
由于这四个孔直径较小无法直接铸造,故直接钻出。
该工序具体分为两步,4个孔分两次钻出。
M12孔因一次钻出,故其钻削余量为Z钻4/2=2mm
各工步的余量和工序尺寸及公差列于表3-1
表3-1此工步的余量和工序尺寸及公差
加工表面
加工方法
余量
公差等级
序尺寸及公差
φ12mm
钻孔
2
H7
φ6
参考文献
(1)表2.4-38,并参考Z518机床说明书,取钻φ4mm孔的进给量f=0.3mm/r。
参考文献
(1)表2.4-41,查得钻φ4mm孔的切削速度v=15.7m/min,由此算出转速为
n=1000v/πd=1000×15.7/(3.14×4)≈1250r/min
按机床实际转速取n=1000r/min,则实际切削速度为
v=3.14×4×1000/1000≈12.56m/min
参考文献
(1)表2.4-69,得:
Ff=9.81×42.7d0f0.8KF(N)
M=9.81×0.021d02f0.8KM(N·m)
分别求出钻φ10mm孔的Ff和M如下:
Ff=9.81×42.7×4×0.40.8×1=804N
M=9.81×0.021×42×0.40.8×1=1.6N·m
它们均小于机床的最大进给力7840N和机床的最大扭转力矩196N·m,故机床刚度足够。
计算工序100的时间定额:
(1)机动时间参考文献[1]表2.5-7,得钻孔的计算公式为:
=(L+
+
)/(fn)
=(D/2)ctg+(1—2)
=3
钻M12孔:
=(4/2)ctg(118/2)°+1.5=2.7mm
=17mm,取
=3
将以上数据及前面已选定的f及n代入公式,得:
≈(17+2.7+3)/(0.3×1000)=0.08min
此工步的辅助时间为:
钻M4孔0.215min。
装卸工件时间,参考文献[1]表2.5-42取1.5min。
所以辅助时间Ta为:
=0.215+1.5+0.015+0.02+0.04=1.79min≈1.8min
(2)作业时间:
=
+
=0.9+1.8=2.5min
(3)布置工作地时间。
参考文献[2]取
=3%则:
=
=2.5×3%≈0.075min
(5)休息与生理需要时间。
参考文献[2]取β=3%则:
=
β=2.5×3%≈0.075min
(4)准备与终结时间
。
参考文献[1]表2.5-40取各部分时间为:
中等件42min;深度定位0.3min;使用回转夹具10min。
=42+0.3+10=52.3min
参考文献[2]由于是大量生产Te/n≈0故Te/n不计入。
(5)单件时间
=
+
+
+
=1.8+0.9+0.075+0.075=3.86min
3.4.3.工序60中粗铣A面、D面及N面
这些表面的加工精度只需粗铣一下就能达到,所以总余量和粗加工余量相等,已知A总余量为3mm,故粗加工余量为3mm。
同样D面粗加工余量为3mm,N面得粗加工余量为4mm,B面得粗加工余量为4mm。
查文献(6)表8.9得粗加工公差等