液压缩管机的结构及其工作原理.docx
《液压缩管机的结构及其工作原理.docx》由会员分享,可在线阅读,更多相关《液压缩管机的结构及其工作原理.docx(14页珍藏版)》请在冰豆网上搜索。
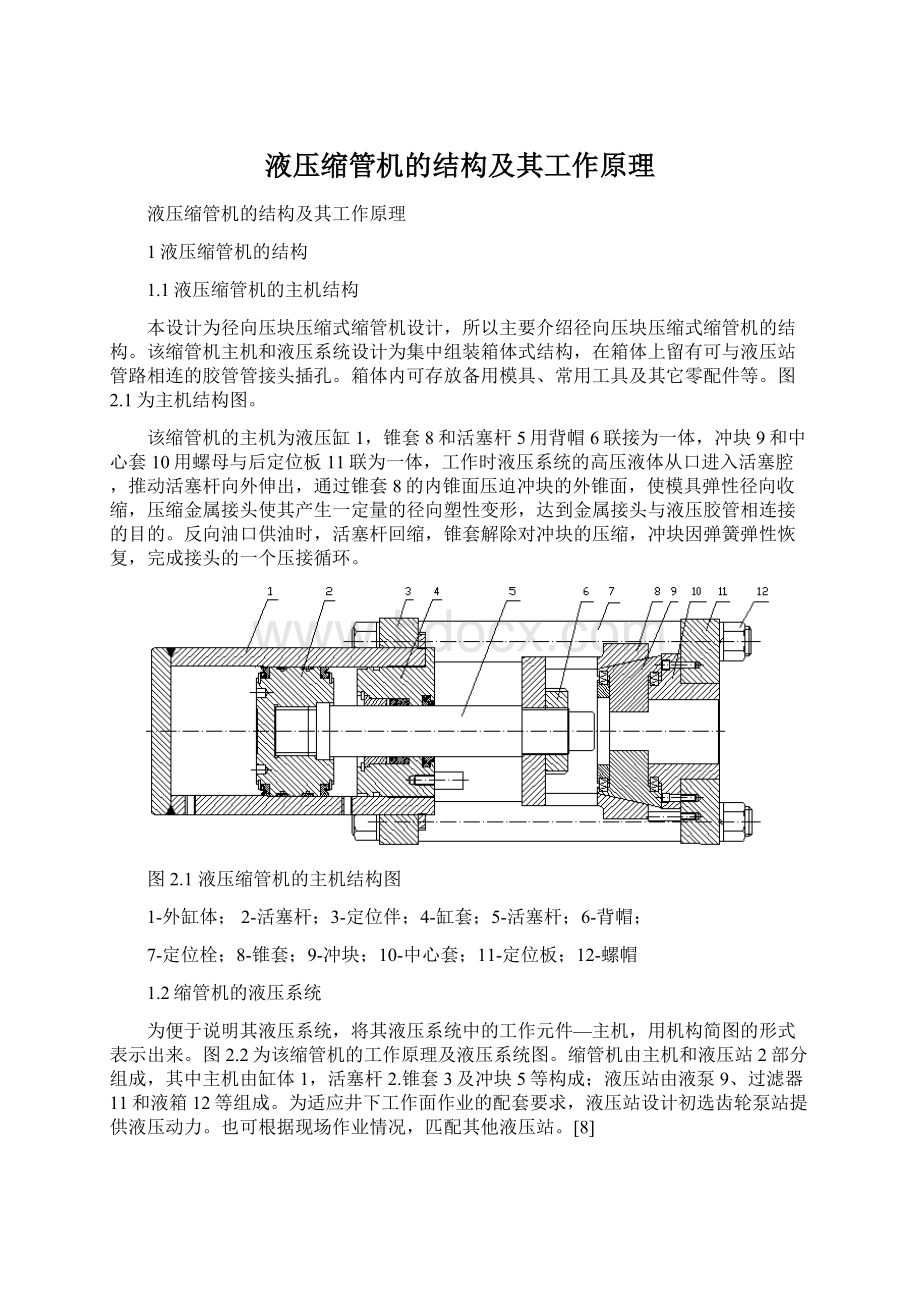
液压缩管机的结构及其工作原理
液压缩管机的结构及其工作原理
1液压缩管机的结构
1.1液压缩管机的主机结构
本设计为径向压块压缩式缩管机设计,所以主要介绍径向压块压缩式缩管机的结构。
该缩管机主机和液压系统设计为集中组装箱体式结构,在箱体上留有可与液压站管路相连的胶管管接头插孔。
箱体内可存放备用模具、常用工具及其它零配件等。
图2.1为主机结构图。
该缩管机的主机为液压缸1,锥套8和活塞杆5用背帽6联接为一体,冲块9和中心套10用螺母与后定位板11联为一体,工作时液压系统的高压液体从口进入活塞腔,推动活塞杆向外伸出,通过锥套8的内锥面压迫冲块的外锥面,使模具弹性径向收缩,压缩金属接头使其产生一定量的径向塑性变形,达到金属接头与液压胶管相连接的目的。
反向油口供油时,活塞杆回缩,锥套解除对冲块的压缩,冲块因弹簧弹性恢复,完成接头的一个压接循环。
图2.1液压缩管机的主机结构图
1-外缸体;2-活塞杆;3-定位伴;4-缸套;5-活塞杆;6-背帽;
7-定位栓;8-锥套;9-冲块;10-中心套;11-定位板;12-螺帽
1.2缩管机的液压系统
为便于说明其液压系统,将其液压系统中的工作元件—主机,用机构简图的形式表示出来。
图2.2为该缩管机的工作原理及液压系统图。
缩管机由主机和液压站2部分组成,其中主机由缸体1,活塞杆2.锥套3及冲块5等构成;液压站由液泵9、过滤器11和液箱12等组成。
为适应井下工作面作业的配套要求,液压站设计初选齿轮泵站提供液压动力。
也可根据现场作业情况,匹配其他液压站。
[8]
图2.2缩管机工作原理与液压系统图
1-外缸体;2-活塞杆;3-锥套;4-管接头;5-冲块;6-液压胶管;
7-操作阀;8-压力表;9-溢流阀;10-油泵;11-滤油器;12-油箱;13-电动机
2液压缩管机的工作原理
工作时,先将液压胶管的端头与金属管接头4套装好,插人冲块内孔预定位置。
再把操作阀7打到左位,此时主机A腔为高压腔,B腔为低压腔。
活塞在液体压力的作用下向右运动,活塞杆带动锥套向右轴向运动压缩冲块。
这样,迫使冲块径向收缩,压接金属管接头,直至达到预先设定的压缩量为止。
这个过程叫做压缩过程。
再将操作阀打到中间位置,停顿一定时间(约1min)。
这时,A,B腔分别被封闭而处于保压状态,液泵排出的液体经操作阀返回液箱。
这个过程叫做保压过程。
接着,将操作阀打到右位。
此时,A腔变为低压腔,B腔变为高压腔。
活塞在液体压力的作用下向左运动,活塞杆带动锥套反向退回。
冲块解除压迫后在弹簧作用下张开,直至锥套回退到原始位置。
这时,把压接好的液压胶管从模具中拔出。
这个过程叫做回退过程。
经过压缩、保压和回退3个过程,则完成接头压接的一个循环。
主机在设计技术参数状态下,每完成一个压接循环最多约3min。
[8]
液压缩管机主机的设计
1中心套及盖的结构设计
1.1中心套的结构设计
中心套是是一个圆套,其上有轴肩,轴肩上有螺纹孔,通过螺纹孔把中心套固定在固定板上。
由于中心套和锥套是通用的,它要同时满足压缩管径为
6㎜、
8㎜、
10㎜、
16㎜、
19㎜、
25㎜、
32㎜的管的要求,所以现以压缩管径最大的
32㎜管时的中心套为基准设计中心套,然后再分别设计不同管径时冲块的尺寸。
图3.1中心套结构尺寸图
1.2盖的结构设计
盖是连接在中心套上,用于防止冲块从中心套槽中滑出的一个构件,它的尺寸是根据中心套来确定的,其形状和尺寸如图3.2所示。
盖的材料选用Q235。
圆柱面上的孔是弹簧孔,而端面上的沉头孔用于螺钉和中心套连接。
图3.2盖的结构尺寸图
2冲块的结构设计
冲块是缩管机中最重要的零件,也是缩管机设计的核心零件,现有的结构设计大多是按传统的设计方法进行的,即以满足实际工况要求为目的进行结构设计,然后根据现场实际工作条件进行试验和测试,再作设计修改,图3.3是冲块和中心套的装配图,从图中可以看出,冲块共有8块,分别镶嵌在中心套的8个槽中,其两端由两个弹簧支撑,这样冲块可以在径向自动向外移动。
图3.3冲块和中心套的装配图
1.最大直径压缩量的确定
2.锥套与冲块的接触面锥度C
3.有效行程的确定
图3.4缩管机压缩运行图
4.冲块的尺寸设计
(1)压缩内径为
32㎜的管时的冲块尺寸设计
图3.6冲块的结构和尺寸图
(2)压缩内径为
25mm的管时的冲块的设计:
(3)压缩内径为
19mm的管时的冲块的设计:
(4)压缩内径为
16㎜的管时的冲块的设计:
(5)压缩内径为
10㎜的管时的冲块的设计:
(6)压缩内径为
8㎜的管时的冲块的设计:
(7)压缩内径为
6㎜的管时的冲块的设计:
3.锥套的结构设计
3.1.锥套的结构
锥套是固定在活塞杆上的用于压缩冲块的一个结构,它的端部的锥度和冲块的锥度相同,这样在压缩时活塞杆带动锥套移动,由于锥度的原因使冲块径向移动,完成压缩作用,锥套的结构如图3.7。
3.2.锥套的尺寸设计
锥套的尺寸和冲块相关,由冲块的尺寸可知,锥套端部的内锥角为5º,端部外径取
?
㎜,锥套腰部开有8个长?
mm宽?
mm的槽,顶部孔是用于和活塞杆连接的,考虑到活塞杆的直径并留有一定的轴肩取孔内径为
?
㎜,为使与活塞杆的连接件和工作时有足够的空间,取锥套的整体长度为?
㎜,其它尺寸如图3.7所示。
锥套材料为40Cr,并调质处理。
图3.7锥套结构尺寸图
4其他部件的设计
4.1固定螺栓的选择
固定螺栓是用于连接两个固定板起固定作用的,固定栓取M?
×?
螺栓。
4.2固定板的结构设计
1.固定板1的结构
固定板1结构如图3.8所示,其内孔D1是和中心套连接的根据中心套的尺寸知D1=?
㎜,D2=?
mm,固定板的外轮廓边长尺寸根据液压缸的尺寸和固定栓确定的,液压缸的外径为
?
㎜,固定栓取?
螺栓,考虑到留有足够的空间取固定板的边长D4=?
mm,D3=?
mm,为保证螺纹孔深度取厚度?
㎜,材料为40Cr.
图3.8固定板1的结构
2.固定板2的结构
固定板2的结构和固定板1相同,是固定在液压缸上的,所以其内径D2=?
mm,外轮廓边长和固定板1相同D=?
mm。
4.3背帽的选择
1.背帽1的选择
背帽1是连接锥套和活塞杆的,选螺纹规格D×p=?
×?
的圆螺母。
查手册知它的主要参数如表3.1,槽数n=4。
表3.1 背帽规格
螺纹规格D×p
外径D
小径D1
宽m
槽宽hmin
槽深tmin
C1
C
M52×1.5
72
50.376
10
8
3.5
1
1
M200×3
240
196.725
22
16
7
1.5
2
2.背帽2的选择
背帽2是连接固定板2和液压缸的,选螺纹规格D×p=?
×?
的圆螺母。
主要参数如上图,槽数n=6.
4.4弹簧的设计
本弹簧只是用于冲块不受力时沿径向返回作用,所以对弹簧的性能要求不高,只要具备一定的高度和压缩量即可。
根据中心套上弹簧孔的直径为12㎜,在标准弹簧中选择,结果如表3.2。
表3.2弹簧规格
线径d/㎜
弹簧中径D/㎜
节距t/㎜
自由高度H0/㎜
有效圈数n/圈
试验载荷Pn/N
试验载荷变形量L/㎜
1.2
8
2.92
40
12.5
68.6
21.4
4.5定位块的设计
1.定位块1的设计
定位块1是固定在固定板1上的,其作用是限制锥套右行的极限位置,由于锥套右行至极限位置时锥度部分和冲块完全重合,所以它俩右边是对齐的,这样定位块的长度就是中心套肩部的宽度,即L=?
㎜,取定位块直径为
?
㎜,螺纹部分取?
.
2.定位块2的设计
定位块2是锥套的左行的极限位置,固定在液压缸的缸套上,其尺寸由安装后通过实验加以确定。
液压系统设计计算
液压系统是液压设备的一个组成部分,它与主机的关系密切,两者的设计通常需要同时进行。
设计要求一般是必须从实际出发,重视调查研究,注意吸取国内外先进技术,力求做到设计出的系统重量轻、体积小、效率高、工作可靠、结构简单、操作和维护保养方便、经济性好。
设计步骤如下。
1设计要求
主机用途及规格
要求主机完成的工艺过程
该缩管机的主机为液压缸,锥套和活塞杆用背帽联接为一体,冲块和中心套用螺母与后定位板联为一体,工作时液压系统的高压液体从A口进入活塞腔,推动活塞杆向外伸出,通过锥套的内锥面压迫冲块的外锥面,使模具弹性径向收缩,压缩金属接头使其产生一定量的径向塑性变形,达到金属接头与液压胶管相连接的目的。
反向由B口供液时,活塞杆回缩,锥套解除对冲块的压缩,冲块因弹簧弹性恢复,完成接头的一个压接循环。
要求液压系统完成的工艺过程
先把操作阀打到左位,此时主机液压缸左腔为高压腔,在液体压力的作用下迫使活塞带动活塞杆向右移动,活塞杆带动锥套向左轴向伸出压缩模具。
这个过程叫做压缩过程。
再将操作阀打到中间位置,停顿一定时间(约1min)。
这时,液压缸的两腔分别被封闭而处于保压状态,液泵排出的液体经操作阀返回液箱。
这个过程叫做保压过程。
接着,将操作阀打到右位。
此时,液压缸右腔变为高压腔。
内缸体在液体压力的作用下,带动锥套反向退回。
这个过程叫做回退过程。
2总体规划、确定液压执行元件
液压执行元件的类型、数量、安装位置和与主机的设计有很大的影响,所以,再考虑液压设备的总体方案时,确定液压执行元件和确定主机整体结构布局是同时进行的。
3明确液压执行元件的载荷、速度及其变化规律,绘制液压系统工况图
本设计产品液压缸的最大载荷为1000N。
根据设计要求提供的情况,对液压系统作进一步的工况分析,查明每个液压执行元件在工作循环各阶段中的速度、载荷变化规律,绘制液压系统有关工况图,如表。
表工况图
工况图名称
动作线图
速度图
载荷图
函数式
S=f(t)
v=f(t)
F=f(t)
式中参数的意义
S:
液压缸行程
V:
液压缸行程速度
F:
液压缸的载荷(力)
T:
时间;t=0~t=T为工作循环周期
工况图示
4确定系统工作压力
系统工作压力由设备类型、载荷大小、结构要求和技术水平而定。
系统的工作压力高、省材料、结构紧凑、重量轻是液压系统的发展方向,根据统计资料本产品压力范围是7-21MPa,属中等压力,取本机压力为20MPa.
5确定执行元件的控制和调速方案
根据设计要求,本产品的液压缸是不作速度调节的,只是用方向阀控制活塞的运动方向。
6草拟液压系统原理图
草拟液压系统图注意事项:
1.不许有多余元件;使用的元件和电磁铁数越少越好。
2.注意元件间的连锁关系,防止互相影响产生误动作。
3.系统各主要部位的压力能够随时检测;压力表数目要少。
4.按国家标准规定,元件符号按常态工况绘出,非标准元件用简练的结构示意图表达。
初步拟订液压系统图如图2.2。
7液压缸的设计计算
初选液压缸的工作压力
根据直径32mm胶管的缩管压力为1000kN,选液压缸的工作压力为20MPa。
液压缸缸筒尺寸的计算
1.缸筒内径、外径
2.缸筒壁厚验算
3.缸筒底部厚度
4.缸筒头部法兰厚度
活塞及活塞杆的设计
1.活塞杆选择
2.活塞杆直径的确定
3.活塞杆的强度计算
4.活塞杆的导向套、密封和防尘
5.液压缸的工作行程
8液压元件的选择
液压泵和电动机的选择
1.液压泵的型号确定及电动机的功率
2.泵的选择
3.电动机的选择
阀类元件和液压辅助元件
1.换向阀选择
2.滤油器
3.压力表
4.油管
5.管接头
6.油箱
7.溢流阀
9验算液压系统的性能
液压系统的参数有许多式由估计或经验确定的,其设计水平需通过性能验算来判断。
验算项目主要有压力损失、温升和液压冲击等。
压力损失验算
温升验算
液流经液压泵、液压执行元件、或其他阀及管道的功率损失都将转化为热量,使工作介质温度升高。
系统的散热主要是通过油箱表面和管道表面。
若详细进行系统的发热及散热计算较麻烦。
通常液压系统在单位时间内的发热功率
油箱的散热功率:
10液压系统优化设计与控制
液压系统的功率损失一方面会造成能量上的损失,使系统的总效率下降,另一方面,损失掉的这一部分能量将会转变成热能,使液压油的温度升高,油液变质,导致液压设备出现故障。
因此,设计液压系统时,在满足使用要求的前提下,还应充分考虑降低系统的功率损失。
首先,从动力源——泵的方面来考虑,考虑到执行器工作状况的多样化,有时系统需要大流量,低压力;有时又需要小流量,高压力。
所以选择限压式变量泵为宜,因为这种类型的泵的流量随系统压力的变化而变化。
当系统压力降低时,流量比较大,能满足执行器的快速行程。
当系统压力提高时流量又相应减小,能满足执行器的工作行程。
这样既能满足执行器的工作要求,又能使功率的消耗比较合理。
其次,如果执行器具有调速的要求,那么在选择调速回路时,既要满足调速的要求,又要尽量减少功率损失。
常见的调速回路主要有:
节流调速回路、容积调速回路、容积节流调速回路。
其中节流调速回路的功率损失大,低速稳定性好。
而容积调速回路既无溢流损失,也无节流损失,效率高,但低速稳定性差。
如果要同时满足两方面的要求,可采用差压式变量泵和节流阀组成的容积节流调速回路,并使节流阀两端的压力差尽量小,以减小压力损失。
第三,液压油流经各类液压阀时不可避免的存在着压力损失和流量损失,这一部分的能量损失在全部能量损失中占有较大的比重。
因此,合理选择液压器,调整压力阀的压力也是降低功率损失的一个重要方面。
流量阀按系统中流量调节范围选取并保证其最小稳定流量能满足使用要求,压力阀的压力在满足液压设备正常工作的情况下尽量取较低的压力。
第四,合理选择液压油。
液压油在管路中流动时,将呈现出黏性,而黏性过高时,将产生较大的内摩擦力,造成油液发热,同时增加油液流动时的阻力。
当黏性过低时,易造成泄漏,将降低系统容积效率,因此,一般选择黏度适宜且黏温特性比较好的油液。
液压系统优化设计与控制
1.工作介质污染控制
液压系统易入侵污染物和生成污染物,在产品设计过程中应本着预防为主、治理为辅的原则,充分考虑如何消除污染源,从根本上防止污染。
在设计阶段除了要合理选择液压系统元件的参数和结构外,可采取以下措施控制污染物的影响。
在节流阀前后装上精滤油器,滤油器的精度取决于控制速度的要求。
所有需切削加工的元器件,孔口必须有一定的倒角,以防切割密封件且便于装配。
所有元器件、配管等在加工工序后都必须认真清洗,消除毛刺、油污、纤维等;组装前必须保持环境的清洁,所有元器件必须采用干装配方式。
装配后选择与工作介质相容的冲洗介质认真清洗。
工作介质污染的另一方面是介质对外部环境的污染。
应尽量使用高黏度的工作油,以减少泄漏、采用无素液压油、开发液压油的回收再利用技术、研制工作介质绿色添加剂等。
2.液压系统噪声控制
液压系统噪声是对工作环境的一种污染,分机械噪声和流体噪声。
在液压系统中,电动机、液压泵和液压马达等的转速都很高,如果它们的转动部件不平衡,就会产生周期性的不平衡力,引起转轴的弯曲振动。
这种振动传到油箱和管路时,会因共振而发出很大的噪声,应对转子进行动平衡试验,且在产品设计时应应注意防止其产生共振。
机械噪声还包括机械零件缺陷和装配不合格而引起的高频噪声。
因此,必须严格保证制造和安装的质量,产品结构设计应科学合理。
在液压系统噪声中,流体噪声占相当大的比例,这种噪声是由于油液的流速、压力的突变、流量的周期性变化以及泵的困油、气穴等原因引起的,以液压泵为例,在液压泵的吸油和压油循环中,产生周期性的压力和流量变化,形成压力脉动,从而引起液压振动,并经出油口传播至整个液压系统,同时,液压回路的管路和阀类元件对液压脉动产品反射作用,在回路中产生波动,与泵发生共振,产生噪声。
3.液压系统的节能设计
液压系统的节能设计不但要保证系统的输出功率要求,还要保证尽可能经济、有效的利用能量,达到高效、可靠运行的目的,液压系统的功率损失会使系统的总效率下降、油温升高、油液变质,导致液压设备发生故障。
因此,设计液压系统时必须多途径地降低系统的功率损失。
在元件的选用方面,应尽量选用那些效率高、能耗低的元件,如选用效率较高的变量泵,可根据负载的需要改变压力,减少能量消耗,选成集成阀以减少管连接的压力损失,选择压降小、可连续控制的比例阀等。
采用各种现代液压技术也是提高液压系统效率、降低能耗的重要手段,如压力补偿控制、负载感应控制以及功率协调系统等,采用定量泵+比例换向阀、多联泵(定量泵)+比例节流溢流阀的系统,效率可以提高28%-45%,采用定理泵增速液压缸的液压回路,系统中的溢流阀起安全保护作用,并且无溢流损失,供油压力始终随负载而变,这种回路具有容积调速以及压力自动适应的特性,能使系统效率明显提高。
液压传动系统的安装、试压和调试
1液压元件的安装
2试压
3调整和试运行
液压系统的调试应在相关的土建、机械、电器、仪表以及安全防护等工程确认具备试车条件后进行。
系统调试一般应按泵站调试、系统压力调试和执行元件速度调试的顺序进行,并应配合单部件调试、单机调试、区域联动、机组联动的调试顺序。
1.泵站调试
2.压力调试
3.流量的调试