天然气制氢技术问答doc.docx
《天然气制氢技术问答doc.docx》由会员分享,可在线阅读,更多相关《天然气制氢技术问答doc.docx(67页珍藏版)》请在冰豆网上搜索。
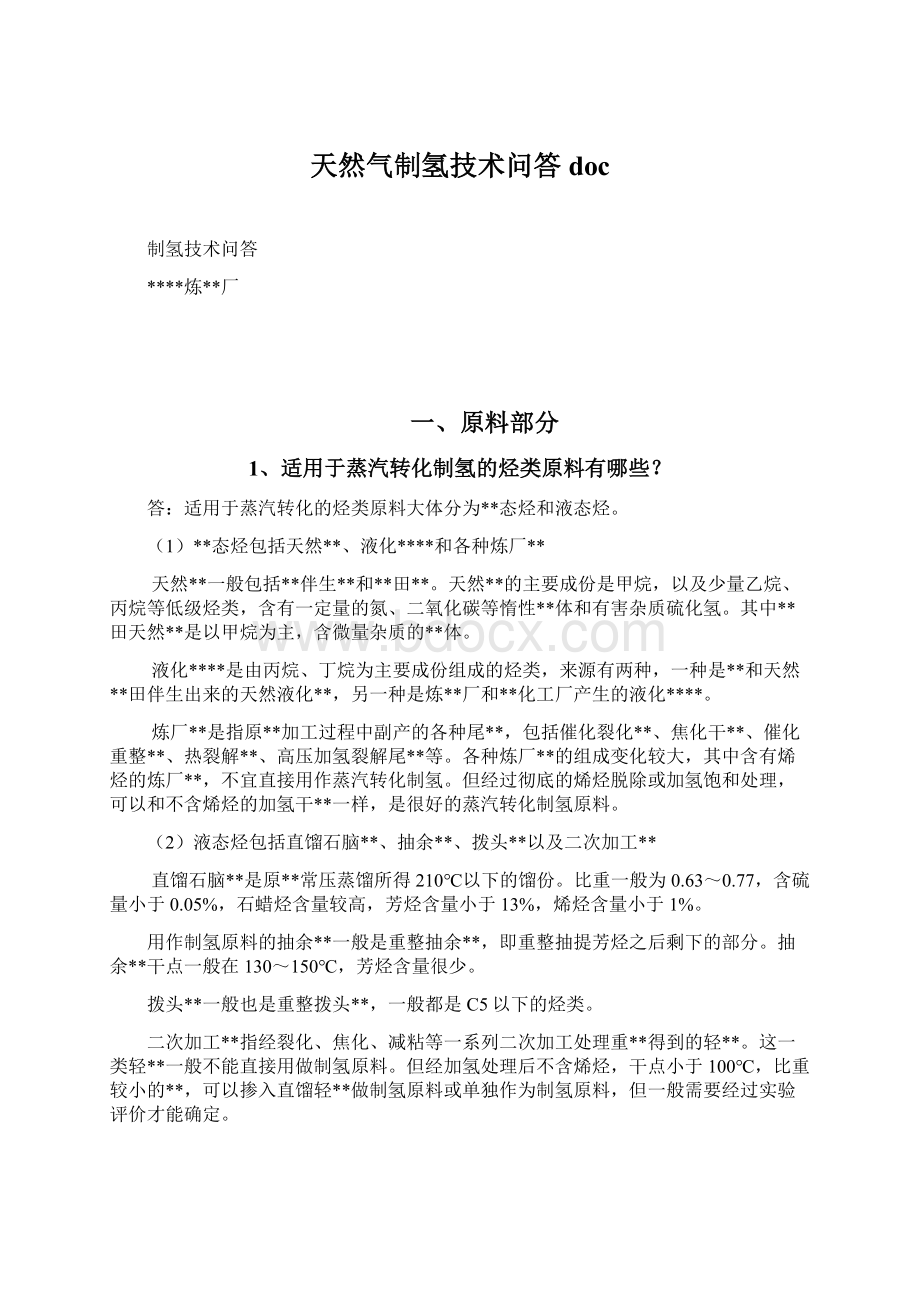
天然气制氢技术问答doc
制氢技术问答
****炼**厂
一、原料部分
1、适用于蒸汽转化制氢的烃类原料有哪些?
答:
适用于蒸汽转化的烃类原料大体分为**态烃和液态烃。
(1)**态烃包括天然**、液化****和各种炼厂**
天然**一般包括**伴生**和**田**。
天然**的主要成份是甲烷,以及少量乙烷、丙烷等低级烃类,含有一定量的氮、二氧化碳等惰性**体和有害杂质硫化氢。
其中**田天然**是以甲烷为主,含微量杂质的**体。
液化****是由丙烷、丁烷为主要成份组成的烃类,来源有两种,一种是**和天然**田伴生出来的天然液化**,另一种是炼**厂和**化工厂产生的液化****。
炼厂**是指原**加工过程中副产的各种尾**,包括催化裂化**、焦化干**、催化重整**、热裂解**、高压加氢裂解尾**等。
各种炼厂**的组成变化较大,其中含有烯烃的炼厂**,不宜直接用作蒸汽转化制氢。
但经过彻底的烯烃脱除或加氢饱和处理,可以和不含烯烃的加氢干**一样,是很好的蒸汽转化制氢原料。
(2)液态烃包括直馏石脑**、抽余**、拨头**以及二次加工**
直馏石脑**是原**常压蒸馏所得210℃以下的馏份。
比重一般为0.63~0.77,含硫量小于0.05%,石蜡烃含量较高,芳烃含量小于13%,烯烃含量小于1%。
用作制氢原料的抽余**一般是重整抽余**,即重整抽提芳烃之后剩下的部分。
抽余**干点一般在130~150℃,芳烃含量很少。
拨头**一般也是重整拨头**,一般都是C5以下的烃类。
二次加工**指经裂化、焦化、减粘等一系列二次加工处理重**得到的轻**。
这一类轻**一般不能直接用做制氢原料。
但经加氢处理后不含烯烃,干点小于100℃,比重较小的**,可以掺入直馏轻**做制氢原料或单独作为制氢原料,但一般需要经过实验评价才能确定。
2、蒸汽转化制氢原料选择原则有哪些?
答:
(1)首先选用不含烯烃、芳烃和环烷烃含量低的原料。
因为同碳数烃类积炭倾向为:
烯烃>芳烃>环烷烃>烷烃;同碳数烃类的C/H值也基本是这个规律。
为减少积炭倾向,提高原料的单位产氢量而遵循这项原则。
一般要求原料中烯烃含量小于1%,芳烃含量小于13%,环烷烃含量小于36%。
(2)优先选用较轻的原料。
因为同族烃类积炭倾向随分子量增大而增大,C/H也随分子量增大而增大,为此,选用**态烃优于液态烃,轻组分液态烃优于重组分液态烃。
(3)优先选用低毒原料。
就脱硫而言,一般硫含量小于150ppm时,采用钴钼加氢――ZnO脱硫就能达到硫含量小于0.5ppm;硫含量大于150ppm,就要先进行预脱硫后再进行钴钼加氢――ZnO脱硫,但这相应增加能耗、成本和投资。
所以,应优先选用低硫原料。
氯、砷对催化剂毒害较大,一般不宜选用含氯、砷原料。
如果选用,则应设置脱氯、脱砷装置。
(4)就炼厂**制氢而言,往往可供选择的原料有几种,但数量都不多。
这种情况下应根据上述原则优先选用平均分子量小,含硫低的饱和烃类。
不足时补以分子量稍大的原料。
例如宽馏分重整装置稳定塔顶的液态烃数量很少,但却是很好的制氢原料。
又如炼**厂加氢干**也是很好的制氢原料。
如果将上述两种原料做燃料烧掉,而选用直馏轻**或抽余**做制氢原料则是极不合理的。
氢碳比与理论产**量的关系(m3/kg)
H/C
2
2.2
2.4
2.6
2.8
3.0
3.2
3.4
3.6
3.8
4.0
理论产氢量
4.8
4.89
4.98
5.06
5.15
5.23
5.31
5.38
5.46
5.53
5.60
3、为什么不能轻易选用炼厂二次加工**做转化原料?
答:
二次加工**是重**或渣**经过裂化、焦化、减粘等过程产生的轻**。
经过加氢处理后,比重、馏程、烯烃含量等性能指标与直馏轻**相近,可用作燃料**或**化工的原料**,然而,要用做制氢原料则必须慎重。
许多厂家因使用二次**而造成转化催化剂毁坏。
原因在于:
(1)二次**中侧链烷烃所占比重较大。
(2)环烷烃较多。
(3)芳烃尤其是重芳烃较多。
(4)含有较多的胶质和重金属等杂质。
(5)加氢装置的加氢深度不够,硫、氮和烯烃等脱除不彻底。
以上这些因素易造成催化剂中毒和积炭,使催化剂失去活性,所以不能轻易选用于次加工**作为转化制氢原料。
4、是否有可用做制氢原料的二次加工**?
答:
二次加工**不能轻易用于制氢原料,但是经过深度加氢脱硫的轻质**是可以考虑选用的。
例如经过16.0MPa左右高压加氢裂化的轻质**品,反应温度和氢**比均高于普通加氢精制工艺,虽然仍属于二次加工**,但是加氢反应较彻底,**品中的硫、氯、氮化合物以及胶质脱除比较干净。
芳烃和环烷烃也较少,其物化性能和直馏轻石脑**差不多。
一般情况下,选用干点小于70℃高压加氢二次**做制氢原料是没有问题的。
到目前为止,多家制氢都有成功使用加氢裂化轻石脑**作为制氢原料的先例。
如果轻**的干点和比重较高,则必须通过**品评价试验,选择相应的工艺条件来确定能否用作制氢原料。
选用二次加工**一定要采取谨慎的态度。
目前国内有几个厂选用二次加工**作制氢原料,一般都经过中**齐鲁分公司研究院的严格测试和评价后才采用的。
由于各厂的二次加工工艺和基础原料**性能各不相同,其轻质**物化性质差别也很大,所以具体选用哪种**品作原料要经过有针对性的测试评价来确定。
一般情况下,即使采用二次加工**也不宜单独使用,而是和直馏轻**按一定比例混用,以保证制氢原料中的单体烃品种有一个合理的分布,防止同种烃类的过度集中导致转化反应负荷在催化剂床层内的不均匀分布。
5、轻**的族组成对转化过程产生哪些影响?
答:
轻**的族组成越复杂,转化催化剂上的反应就复杂。
对甲烷转化来讲,转化催化剂主要是促进蒸汽转化反应的进行。
然而对于轻**转化来讲,由于族组成很复杂,在蒸汽转化反应的同时包括高级烃的热裂解、催化裂解、脱氢加氢、结炭、消炭等一系列的反应,要求催化剂必须具有适应这种复杂反应体系的综合性能。
最突出的表现是积炭的趋势较大,为此,轻**转化催化剂必须具备较强的抗积炭性能。
不同的烃类在使用条件下结炭的速度是不同的,下表是几种烃类的相对结炭速度。
原料
丁烷
正己烷
环己烷
正庚烷
苯
乙烯
结炭速度
2
95
64
135
532
17500
诱导期
/
107
219
213
44
<1
上表可见,碳链越长,结炭速度越大。
苯的结炭速度高于直链烷烃,烯烃的结炭速度是烷烃的上百倍。
另外,由于环烷烃和芳烃难于转化,当轻**中的环烷轻和芳烃增加时,转化反应往往向高温区移动,导致床层下部催化剂结炭和出口尾**中残留芳烃增加。
6、天然**用做制氢原料对转化催化剂有什么要求?
答:
天然**主要由甲烷和少量乙烷、丙烷等组成,不含较高级的烃类,也不含烯烃。
在转化条件下,不发生裂解、聚合等一系列的积炭反应,在反应管内进行的主要是甲烷蒸汽转化反应和变换反应,在反应管内进行的主要是甲烷蒸汽转化反应和变换反应。
所以要求天然**转化催化剂具有较高的转化活性、稳定性和强度,以获得较长的使用寿命。
为此,必须保持催化剂具有较大的稳定性的活性表面。
天然**转化催化剂目前基本上采用预烧结型载体负载镍的形式,一是保持物理结构的稳定,二是保证镍组分的均匀分布,此外还采用各种优化形状的催化剂(除拉西环外,有车轮状、多孔型、齿轮型)来提高催化剂几何表面积,增大活性表面的利用率来达到提高活性的目的。
7、不含烯烃的各种炼厂**对转化催化剂有什么要求?
答:
不含烯烃的原**加工副产**中主要含有C1~C4烷烃、氢**和惰性**体。
与天然**相比,**加工**中C2~C4的烷烃含量高。
在蒸汽转化条件下,有一定的积炭趋势,为此要求催化剂不仅具有高转化活性、稳定性好、高强度的性能,还应具有一定抗积炭能力,这样才能保证催化剂具有较长使用寿命。
8、用炼厂干**做制氢原料时如何进行预处理?
答:
炼厂干**是廉价的制氢原料,但由于其中的烯烃含量高、硫含量高,不能直接用做制氢原料,必须经过加氢饱和和加氢脱硫处理,使干**中烯烃含量小于1%,硫含量小于0.5mg/m3后方可用做制氢原料。
随着烯烃加氢饱和技术和加氢脱硫技术的不断发展成熟,目前各种炼厂**均可作为制氢原料。
下面分别对不同炼厂**的预处理技术进行简单叙述。
(1)对于不含烯烃的加氢裂化干**,其中不含烯烃,其中的硫形态也十分简单,因此,经过脱硫合格后即可作为制氢原料。
但加氢干**一般具有较高的氢含量,单独使用时单位体积进料的产氢率较低,若与富含烃类组分的**体混合使用,效果会更好。
(2)对于烯烃含量低于6%(v/v)的炼厂**,如焦化干**,可以通过使用低温高活性加氢催化剂,在绝热反应器内进行烯烃加氢饱和。
由于入口温度控制较低,保证加氢反应器床层温度在允许的范围之内。
在烯烃加氢饱和的同时,其中的有机硫化合物也发生加氢反应转化成硫化氢,再经氧化锌脱硫合格后,作为制氢原料。
使用焦化干**做原料的装置很多,有沧州分公司、济南炼**厂、锦州**、锦西**等十多套装置。
(3)对于烯烃含量高于6%的炼厂**,如催化干**,其中的烯烃含量有时高达20%左右,单独采用绝热加氢技术会产生巨大的温升,烧毁催化剂。
这时,需要采用两步加氢工艺进行催化干**的预处理。
目前成熟的技术有等温-绝热加氢工艺和变温-绝热加氢工艺。
所谓等温-绝热加氢工艺就是干**先经过列管式等温加氢反应器,烯烃饱和产生的热量由壳程内的水汽化带走,副产中压蒸汽。
从等温加氢反应器出来的干**再进入绝热反应器,完成烯烃的饱和和有机硫的氢解。
清江**、****炼**厂制氢装置采用该工艺。
变温-绝热加氢工艺则是干**先进入导热**取热的列管式加氢反应器,该反应器与等温反应器相比,操作温度高一些,充分利用加氢催化剂的高温活性。
从变温加氢反应器出来的干**再进入绝热加氢反应器,完成剩余烯烃的饱和和有机硫的氢解。
目前,西安**制氢装置采用该工艺。
9、各种轻**对转化催化剂有什么要求?
答:
目前用做蒸汽转化原料的轻**比较复杂,种类繁多。
从性质上看,干点从60℃到210℃,比重从0.63到0.77,芳烃含量从0~15%,对催化剂的要求也不尽相同。
总的特征是在转化过程中都存在析炭反应,都需要催化剂具有较好的抗积炭性能。
对于干点较低、比重较小、芳烃含量较少的原料,选择抗积炭性较好的催化剂,在长期使用过程中可以保证催化剂表面没有大量炭沉积,不会影响活性及其它应用性能。
因此要求催化剂具有高活性、高强度、稳定性好、还原性好、抗积炭性能好。
对于干点高、比重大、芳烃含量较多的原料,选择抗积炭性能较好的催化剂往往也不能保证长期使用中催化剂表面没有炭沉积,尤其是工艺条件波动,原料组成波动的情况下,析炭速度大于消炭速度就会有炭沉积在催化剂表面。
遇到这种情况,就要进行催化剂烧炭再生。
烧炭再生之后,催化剂性能应恢复到原来的水平。
这就不仅需要催化剂具有高活性、高强度、稳定性好和良好的抗积炭性,而且具有良好的再生性能。
再生性能主要指能经受反复氧化还原和反复结炭烧炭的能力。
催化剂经过反复的氧化还原和结炭烧炭之后,其低温还原性、活性、结构稳定性和机械强度都有不同程度的损失。
所以轻**蒸汽转化催化剂必须具有较好的低温还原性能,较高的活性稳定性,良好的结构稳定性和机械强度,才能保证具有较强的再生性能。
二、脱硫部分
1、制氢原料为什么要脱硫?
怎样脱硫?
答:
作为制氢原料的天然**、炼厂**和石脑**都含有不同数量的无机硫和有机硫化物。
硫化物存在于原料中,会增加**体对金属的腐蚀,尤其重要的是制氢采用的含镍合铜催化剂极容易硫化中毒。
脱除原料中硫化物的方法有很多,一般可分为湿法和干法两大类。
湿法脱硫是用溶液进行吸收,现有砷碱法、烷基醇胺法等。
干法脱硫中最早的是氢氧化铁法和活性炭法,现在采用氧化锌、氧化锰、分子筛等脱硫剂脱硫和加氢脱硫结合使用。
2、脱硫方法的选择原则?
答:
(1)原料的性质;
(2)硫化物的种类;(3)硫化物的含量对无机硫的工业化的方法有两种,原料**中H2S含量高时,大多采用溶液来吸收,吸收液一般是碱性溶液,或对H2S具有较高吸收能力的有机溶剂,凡能脱CO2的均能脱H2S,这时应采用湿法脱硫,另一种是干法脱硫,它是用某些固体吸附剂吸附及催化剂活性来脱除H2S及有机硫,它用于处理低含硫原料**,突出优点是净化度高,操作方便可靠,当含硫高的****作原料时,采用干湿法相结合的方法,以脱除硫化物,固体吸附剂只能将有机硫加氢变成易除去的H2S,然后再用固体吸附剂除去H2S。
常用的几种脱硫流程如下:
含硫低→分子筛→活性碳→氧化锌→含硫低→钴——钼加氢→氧化锌→含硫高→湿法脱硫→钴——钼加氢→氧化锌→
3、主要硫化物的性能?
1)硫化氢:
H2S无色**体,有近似臭鸡蛋的臭味,有毒、溶于水,呈酸性,与碱作用生成盐因此可用碱性溶液吸收脱除,另外硫化氢可以与某些金属化物或盐类反应,氧化锌脱硫就是根据这一性质。
2)硫醇:
通式R-SH,R代表烃基,它们具有令人厌恶的**味,不溶于水,能与碱作用:
R-SH+NaOH=R-SNa+H2O,因此也可用碱洗法脱除。
低级醇在150~2500C下可分解成烯烃和H2S
3)硫醚:
通式R-S-R,最简单的低级硫醚是二甲醚(CH3)2S,它是无味的中性**体,醚类性质较稳定,要加热4000C以上,才分解成烯烃和H2S。
4)噻吩:
C4H4S其结构式为
它的性质与苯相近,有苯的**味,不溶于水,性质稳定,加热至5000C也难分解,通常称的“非反应性硫化物”就是指噻吩及其衍生物。
5)二硫化碳:
CS2常温常压下为无色液体,容易挥发,难溶于水但可与碱的水溶液作用,高温下二硫化碳与水蒸**作用,转化成H2S。
6)硫氧化碳:
COS无色无味**体,微溶于水,与碱的水溶液作用生成不稳定的盐,高温下与水蒸汽作用生成H2S和CO2。
4、硫在原料中以什么形式存在?
无机硫:
如硫化氢(H2S)
有机硫:
如硫醇(R-SH)、硫醚(R-S-R)、二硫醚(R-S-SR)、噻吩(C4H4S)、二硫化碳(CS2)、硫氧化碳(COS)及其衍生物。
5、一般加氢脱硫的氢**比为多少?
氢**的比高低对反应设备有什么影响?
答:
一般加氢脱硫的氢**比(H2/**)为80~100(体积),加氢转化速度与氢分压有关,增加氢**比,即提高氢分压,不但能抑制催化剂的积炭,还有利于氢解反应的进行;相反,烃类的分压增加,由于烃类在催化剂表面被吸附,从而减少了催化剂表面积,抑制了氢解反应。
所以通常氢**比高,有利于氢解反应进行,但动力消耗增大,对于汽提过程如氢不考虑循环使用,则脱硫费用加大,氢**比过低,脱硫达不到要求,不能满足以后工序的工艺要求。
6、钴钼加氢催化剂在脱硫中起什么作用?
其反应式如何?
轻**中的有机硫代物在钴钼催化剂存在下与氢反应转化为硫化氢和烃,生成的硫化氢再被氧化锌吸收,以使硫化物被脱除,其主要反应式为:
RSH+H2=RH+H2S
RSR´+2H2=RH+R´H+H2S
RSSR´+3H2=RH+R´H+2H2S
C4H4S+4H2=C4H10+H2S
COS+H2=CO+H2S
此处R和R´代表烷基。
这些反应都是放热反应,平衡常数很大。
因此只要反应速度足够快,有机硫的转化是很完全的,钴钼催化剂还能使烯烃加氢成饱和烃,有机氮化物也可在一定程度上转化成氨和饱和烃类。
7、加氢反应温度、压力、空速对反应有哪些影响?
答:
不同的使用条件如温度、压力、空速H2/**等,将直接影响硫精度,故选择合适的操作条件,对提高有机硫化物的加氢转化极为重要。
1)钴钼催化剂进行加氢脱硫时,操作温度通常控制在350~400℃范围内;当温度低于320℃,加氢反应效果明显下降,温度高于420℃以上催化剂表面聚合和结炭现象增加。
2)由于有机硫化物在轻**中含量不高,故压力对氢解反应影响不大,考虑到整个工艺流程的要求,通常控制在3.5~4MPa。
空速对加氢反应有较大的影响,在工厂使用条件下,该反应属内扩散控制,如增加空速,则原料氢在催化剂床层中停留时间缩短,含有机硫化合物的原料未进入内表面,却穿过催化剂床层,使反应不完全,同时降低了催化剂内表面利用率。
所以欲使原料**中有机硫达到一定加氢程度,要在一定的低空速下进行。
但考虑到设备生产能力,在保证出口硫含量满足工艺要求的条件下,通常均采用尽可能高的空速,一般轻**的空速范围为1~6h-1。
8、加氢催化剂主要有哪些型号,其主要成份性能如何?
答:
目前国内使用的钴钼加氢催化剂,有国产的,如化肥工业研究所开发生产的T201型和**化肥厂催化剂分厂生产的T203型,在原始开车阶段采用的有CCI公司的C49型和TOPSE公司CMK-2型。
目前T201型催化剂的各项性能已赶上或超过了国内处同类产品。
最近化肥工业研究所已经开发出适用于20~250℃的低温型钴钼催化剂,另处用在不同温域和不同**品的钴钼加氢催化剂系列产品也会出现。
此外,有些制氢过程还采用镍、钴、钼加氢,主要型号有化肥工业研究所研制的JJ-1焦化干**加氢脱硫催化剂,抚顺**三厂的3665等。
在一些焦炉**制氢上也采用钴钼催化剂加氢脱硫,主要脱硫型号见下表:
国内使用过的钴钼加氢催化剂一览表
国名
型号
主要成分
规格(mm)
堆密度(kg/l)
比表面(a2/g)
温度℃
压力(MPa)
空速(h-1)
入口硫(ppm)
出中硫(ppm)
处理范围
中国
T201
Co2.3%MoO3
11~13%
Ø3×4~10条
0.8±0.05
160~200
320~420
3~4
1~6
180~210
有机硫<0.3
天然**,轻**
中国
T203
Co1.1%MoO36.66%
Ø3×3~8条
0.7~0.8
170~200
350~400
美国
C49-1
CoO、MoO3
Ø8"条
0.58
204
350~400
0.7~5
1~10
C4以上轻**
丹麦
CnK-2
CoO、MoO3
Ø2~5球
0.8~0.85
200
350~400
1~4
0.2~5
天然**、轻**
9、钴钼催化剂的主要毒物是什么?
如何作用?
答:
钴-钼催化剂的主要毒物是氨、氮,过量的硫化氢,氨能在硫化物开始反应前吸附在催化剂上,使脱硫速度大大下降。
催化剂失活程度与氨分压成正比,一般氢**中要求氨含量<100PPM以下。
如果有N2存在,在脱S条件下会生成少量的氨,如果是氮**循环使用,则氨会慢慢积累,必须除去。
H2S含量超过催化剂硫化所需的量时,会使其它硫化物转化反应受到抑制,因此处理含大量H2S及少量有机硫的原料时,要脱H2S再进行加氢转化。
有的厂选用ZnO-Co-Mo-ZnO这一流程就是这个道理。
10、脱硫配氢为什么要对CO、CO2含量进行限制?
限制的指标一般为多少?
答:
脱硫配氢中的CO、CO2能与氢在钴钼催化剂上进行烷化反应,放出大量的热。
通常对氢**中的CO和CO2之和的含量要求不超过5%。
据计算每1%CO可使**体温升72℃,每1%CO2可使**体温升61℃,若钴钼催化剂入口温度为380℃,每0.5%CO预计使**温升36℃,则因甲烷化反应会使床层升温到416℃.因此,一般加氢**中CO+CO2含量通常不超过5%,如原料**加氢10%,则进入钼酸钴催化剂中CO+CO2量可小于0.5%。
11、钴钼加氢反应在什么情况下会发生超温?
应如何处理?
答:
钴钼加氢反应的适宜温度应控制在350~400℃之间,只要率达到要求,催化剂使用初期温度一般不宜控制太高。
这样有利于抑制催化剂的初期结炭。
钴钼催化剂在加氢反应中应严格控制配氢**体中的CO和CO2含量,因为CO和CO2能与氢在该催化剂上进行甲烷反应,放出大量的热。
另外,原料中如含有一定量的烯烃时,烯烃加氢也是放热反应,也会使床层温度升高。
因此,在实际操作中,床层最高温度通常控制在420℃以下,同时要严格控制配氢**体中CO和CO2的浓度以及烯烃的浓度,以避免超温烧坏设备和造成催化剂严重结炭而失活。
如果发生超温事故,应立即减负荷或切换惰性原料,以30℃/小时的降温速度降温。
12、为什么要对加氢催化剂进行预硫化?
对钴-钼-氧化铝催化剂而言,Al2O3和单一活性组份的金属氧化物是不显活性或仅能显示较小活性。
催化剂的最佳活性组份被认为是不可还原的,钴所促进的MoS2,故催化剂在投入正常使用前,需将氧化态的活性组份先变成硫化态的金属硫化物,通常称作预硫化。
我国曾进行了以高沸点轻**为原料的钴钼催化剂预硫化与不预硫化的活性比较试验,发现二者的活性差异很大,未经预硫化的钴钼催化剂转化出口有机硫高达6PPM以上,而经过预硫化的钴钼催化剂转化出口有机硫小于1PPM以下。
某些以含硫低硫形态简单的天燃**和低沸点轻质石脑**为原料的合成氨装置,因原料烃分子量小,硫化物随原料烃易于扩散到催化剂多孔结构的内表面,致使内表面利用率提高。
因此,在此情况下钴钼催化剂使用时,为简化操作,有的工厂不经预硫化直接投入使用,仍能将此有硫基本转化完全,满足工艺要求。
绝大多数情况下,由于钴钼催化剂活性组份经硫化后,能增强催化剂的加氢转化能力,这时沸点较高,硫含量较高。
形态硫较复杂的轻**加氢尤为重要,以硫化后的催化剂还能抑制催化剂结炭速度。
故通常认为催化剂不经硫化过程直接投入使用是不合理的使用方法,因为它将影响催化剂的使用寿命和最佳初活性发挥。
13、钴钼催化剂的硫化如何进行?
常用的硫化剂是什么?
采用的操作条件如何?
答:
新鲜的钴钼催化剂活性组份均以氧化态存在,在硫化过程中并不是所有的钴钼氧化物都立即变成MoS2和Co9S8,实际上钴钼氧化物中的氧随着硫化反应的进行而逐渐地为硫所取代,一般可分为三个阶段,第一阶段硫化物与催化剂上的活性组分反应十分迅速,尾**中含硫较低;随后尾**中硫含量逐渐升高,此时,视为第二阶段开始,在这个过程中,金属组与进一步硫化当尾**中H2S达到稳定值,并不继续升高,可视为第三阶段,则硫化过程结束。
催化剂硫化的程度通常以“硫化度”这一概念描述
a=Wo/Ws×100%式中a-硫化度
Wo-催化剂实际吸硫量
Ws-催化剂理论吸硫量
催化剂硫化时的吸硫量与催化剂的钴钼含量有关。
假如催化剂经硫化后,原来的M0O和C0O全部转变成为MoS2和Co9S8,则催化剂理论吸硫量计算式为Ws=Ws´+Ws"式中:
Ws´-M0O3全部变成M0的吸硫量
Ws"-C0O全部变成Co9S8的吸硫量
而Ws´=Wc×A/143.95×64
Ws"=Wc×B/74.9×8/9×32
式中:
Wc-新鲜催化剂的重量
A-催化剂M0O3的含量(%)(W%)
B-催化剂C0O的含量(%)(W%)
M0O3的分子量143.95,C0O的分子量74.9
如知道催化剂实际吸硫量,再根据理论吸硫量计算出硫化度,根据用硫化氢对钴钼催化剂进行不同硫化度试验证明,硫化度愈高,催化剂活性愈大。
通常硫化结束时,催化剂吸硫量约为本重量的5%左右。
常用的硫化剂有硫化氢,CS2或其它有机硫化物,但选用H2S或CS2等硫化物,其硫化后催化剂活性最佳,一般选用CS2进行硫化,这种硫化便宜且容易控制。
硫化过程
预硫化可以在下面两种情况下进行。
1)氢氮**或氢中配入硫化剂。
预硫化条件推荐如下:
催化剂床层温度升至220℃后,向原料**(氢氮**或氢**)中配入硫化剂,**体中含硫量为0.5~1.0%(体积),空速:
400