液压系统设计计算实例.docx
《液压系统设计计算实例.docx》由会员分享,可在线阅读,更多相关《液压系统设计计算实例.docx(14页珍藏版)》请在冰豆网上搜索。
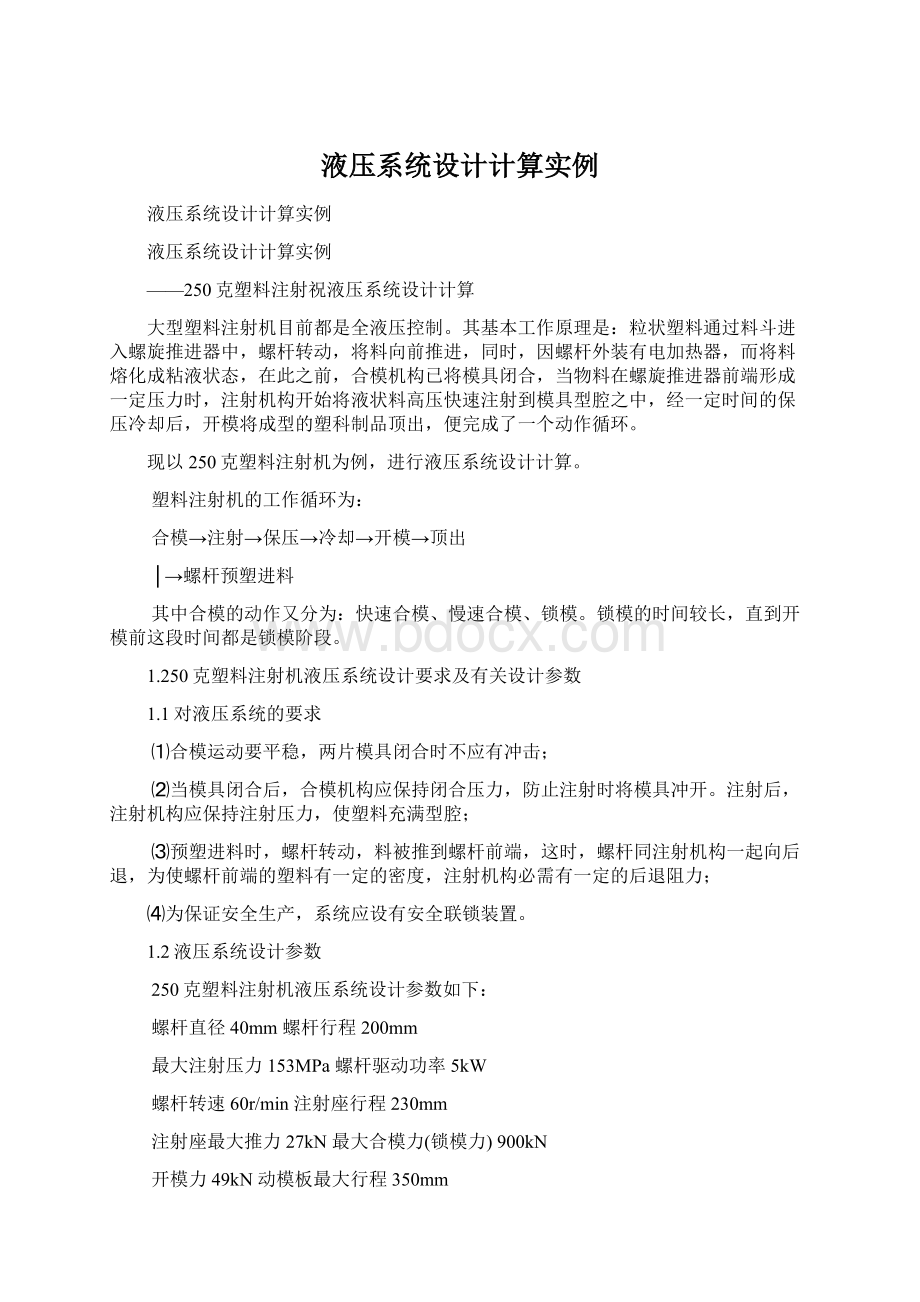
液压系统设计计算实例
液压系统设计计算实例
液压系统设计计算实例
——250克塑料注射祝液压系统设计计算
大型塑料注射机目前都是全液压控制。
其基本工作原理是:
粒状塑料通过料斗进入螺旋推进器中,螺杆转动,将料向前推进,同时,因螺杆外装有电加热器,而将料熔化成粘液状态,在此之前,合模机构已将模具闭合,当物料在螺旋推进器前端形成一定压力时,注射机构开始将液状料高压快速注射到模具型腔之中,经一定时间的保压冷却后,开模将成型的塑科制品顶出,便完成了一个动作循环。
现以250克塑料注射机为例,进行液压系统设计计算。
塑料注射机的工作循环为:
合模→注射→保压→冷却→开模→顶出
│→螺杆预塑进料
其中合模的动作又分为:
快速合模、慢速合模、锁模。
锁模的时间较长,直到开模前这段时间都是锁模阶段。
1.250克塑料注射机液压系统设计要求及有关设计参数
1.1对液压系统的要求
⑴合模运动要平稳,两片模具闭合时不应有冲击;
⑵当模具闭合后,合模机构应保持闭合压力,防止注射时将模具冲开。
注射后,注射机构应保持注射压力,使塑料充满型腔;
⑶预塑进料时,螺杆转动,料被推到螺杆前端,这时,螺杆同注射机构一起向后退,为使螺杆前端的塑料有一定的密度,注射机构必需有一定的后退阻力;
⑷为保证安全生产,系统应设有安全联锁装置。
1.2液压系统设计参数
250克塑料注射机液压系统设计参数如下:
螺杆直径40mm螺杆行程200mm
最大注射压力153MPa螺杆驱动功率5kW
螺杆转速60r/min注射座行程230mm
注射座最大推力27kN最大合模力(锁模力)900kN
开模力49kN动模板最大行程350mm
快速闭模速度0.1m/s慢速闭模速度0.02m/s
快速开模速度0.13m/s慢速开模速度0.03m/s
注射速度0.07m/s注射座前进速度0.06m/s
注射座后移速度0.08m/s
2.液压执行元件载荷力和载荷转矩计算
2.1各液压缸的载荷力计算
⑴合模缸的载荷力
合模缸在模具闭合过程中是轻载,其外载荷主要是动模及其连动部件的起动惯性力和导轨的摩擦力。
锁模时,动模停止运动,其外载荷就是给定的锁模力。
开模时,液压缸除要克服给定的开模力外,还克服运动部件的摩擦阻力。
⑵注射座移动缸的载荷力
座移缸在推进和退回注射座的过程中,同样要克服摩擦阻力和惯性力,只有当喷嘴接触模具时,才须满足注射座最大推力。
⑶注射缸载荷力
注射缸的载荷力在整个注射过程中是变化的,计算时,只须求出最大载荷力。
式中,d——螺杆直径,由给定参数知:
d=0.04m;p——喷嘴处最大注射压力,已知p=153MPa。
由此求得Fw=192kN。
各液压缸的外载荷力计算结果列于表l。
取液压缸的机械效率为0.9,求得相应的作用于活塞上的载荷力,并列于表1中。
2.2进料液压马达载荷转矩计算
取液压马达的机械效率为0.95,则其载荷转矩
3.液压系统主要参数计算
3.1初选系统工作压力
250克塑料注射机属小型液压机,载荷最大时为锁模工况,此时,高压油用增压缸提供;其他工况时,载荷都不太高,参考设计手册,初步确定系统工作压力为6.5MPa。
3.2计算液压缸的主要结构尺寸
⑴确定合模缸的活塞及活塞杆直径
合模缸最大载荷时,为锁模工况,其载荷力为1000kN,工作在活塞杆受压状态。
活塞直径
此时p1是由增压缸提供的增压后的进油压力,初定增压比为5,则p1=5×6.5MPa=32.5MPa,锁模工况时,回油流量极小,故p2≈0,求得合模缸的活塞直径为
,取Dh=0.2m。
按表2—5取d/D=0.7,则活塞杆直径dh=0.7×0.2m=0.14m,取dh=0.15m。
为设计简单加工方便,将增压缸的缸体与合模缸体做成一体(见图1),增压缸的活塞直径也为0.2m。
其活塞杆直径按增压比为5,求得
,取dz=0.09m。
⑵)注射座移动缸的活塞和活塞杆直径
座移动缸最大载荷为其顶紧之时,此时缸的回油流量虽经节流阀,但流量极小,故背压视为零,则其活塞直径为
,取Dy=0.1m
由给定的设计参数知,注射座往复速比为0.08/0.06=1.33,查表2—6得d/D=0.5,则活塞杆直径为:
dy=0.5×0.1m=0.05m
⑶确定注射缸的活塞及活塞杆直径
当液态塑料充满模具型腔时,注射缸的载荷达到最大值213kN,此时注射缸活塞移动速度也近似等于零,回油量极小;故背压力可以忽略不计,这样
,取Ds=0.22m;
活塞杆的直径一般与螺杆外径相同,取ds=0.04m。
3.3计算液压马达的排量
液压马达是单向旋转的,其回油直接回油箱,视其出口压力为零,机械效率为0.95,这样
3.4计算液压执行元件实际工作压力
按最后确定的液压缸的结构尺寸和液压马达排量,计算出各工况时液压执行元件实际工作压力,见表2。
3.5计算液压执行元件实际所需流量
根据最后确定的液压缸的结构尺寸或液压马达的排量及其运动速度或转速,计算出各液压执行元件实际所需流量,见表3。
4.制定系统方案和拟定液压系统图
4.1制定系统方案
⑴执行机构的确定
本机动作机构除螺杆是单向旋转外,其他机构均为直线往复运动。
各直线运动机构均采用单活塞杆双作用液压缸直接驱动,螺杆则用液压马达驱动。
从给定的设计参数可知,锁模时所需的力最大,为900kN。
为此设置增压液压缸,得到锁模时的局部高压来保证锁模力。
⑵合模缸动作回路
合模缸要求其实现快速、慢速、锁模,开模动作。
其运动方向由电液换向阀直接控制。
快速运动时,需要有较大流量供给。
慢速合模只要有小流量供给即可。
锁模时,由增压缸供油。
⑶液压马达动作回路
螺杆不要求反转,所以液压马达单向旋转即可,由于其转速要求较高,而对速度平稳性无过高要求,故采用旁路节流调速方式。
⑷注射缸动作回路
注射缸运动速度也较快,平稳性要求不高,故也采用旁路节流调速方式。
由于预塑时有背压要求,在无杆腔出口处串联背压阀。
⑸注射座移动缸动作回路
注射座移动缸,采用回油节流调速回路。
工艺要求其不工作时,处于浮动状态,故采用Y型中位机能的电磁换向阀。
⑹安全联锁措施
本系统为保证安全生产,设置了安全门,在安全门下端装一个行程阀,用来
控制合模缸的动作。
将行程阀串在控制合模缸换向的液动阀控制油路上,安全门没有关闭时,行程阀没被压下,液动换向阀不能进控制油,电液换向阀不能换向,合模缸也不能合模。
只有操作者离开,将安全门关闭,压下行程阀,合模缸才能合模,从而保障了人身安全。
⑺液压源的选择
该液压系统在整个工作循环中需油量变化较大,另外,闭模和注射后又要求
有较长时间的保压,所以选用双泵供油系统。
液压缸快速动作时,双泵同时供油,慢速动作或保压时由小泵单独供油,这样可减少功率损失,提高系统效率。
4.2拟定液压系统图
液压执行元件以及各基本回路确定之后,把它们有机地组合在一起。
去掉重复多余的元件,把控制液压马达的换向阀与泵的卸荷阀合并,使之一阀两用。
考虑注射缸同合模缸之间有顺序动作的要求,两回路接合部串联单向顺序阀。
再加上其他一些辅助元件便构成了250克塑料注射机完整的液压系统图,见图2,其动作循环表,见表4。
5.液压元件的选择
5.1液压泵的选择
⑴液压泵工作压力的确定
pP≥pl+∑Δp
pl是液压执行元件的最高工作压力,对于本系统,最高压力是增压缸锁模时的入口压力,pl=6.4MPa;∑Δp是泵到执行元件间总的管路损失。
由系统图可见,从泵到增压缸之间串接有一个单向阀和一个换向阀,取∑Δp=0.5MPa。
液压泵工作压力为pP=(6.4+0.5)MPa=6.9MPa
⑵液压泵流量的确定qP≥K(∑qmax)
由工况图看出,系统最大流量发生在快速合模工况,∑qmax=3L/s。
取泄漏系数K为1.2,求得液压泵流量qP=3.6L/s(216L/min)
选用YYB-BCl71/48B型双联叶片泵,当压力为7MPa时,大泵流量为157.3L/min,小泵流量为44.1L/min。
5.2电动机功率的确定
注射机在整个动作循环中,系统的压力和流量都是变化的,所需功率变化较大,
为满足整个工作循环的需要,按较大功率段来确定电动机功率。
从工况图看出,快速注射工况系统的压力和流量均较大。
此时,大小泵同时参加工作,小泵排油除保证锁模压力外,还通过顺序阀将压力油供给注射缸,大小泵出油汇合推动注射缸前进。
前面的计算已知,小泵供油压力为pP1=6.9MPa,考虑大泵到注射缸之间的管路损失,大泵供油压力应为pP2=(5.9+0.5)MPa=6.4MPa,取泵的总效率ηP=0.8,泵的总驱动功率为
=27.313kW
考虑到注射时间较短,不过3s,而电动机一般允许短时间超载25%,这样电动机功率还可降低一些。
P=27.313×100/125
=21.85kW
验算其他工况时,液压泵的驱动功率均小于或近于此值。
查产品样本,选用22kW的电动机。
5.3液压阀的选择
选择液压阀主要根据阀的工作压力和通过阀的流量。
本系统工作压力在7MPa左右,所以液压阀都选用中、高压阀。
所选阀的规格型号见表5。
5.4液压马达的选择
在3.3节已求得液压马达的排量为0.8L/r,正常工作时,输出转矩769N.m,系统工作压力为7MPa。
选SZM0.9双斜盘轴向柱塞式液压马达。
其理论排量为0.873L/r,额定压力为20MPa,额定转速为8~l00r/min,最高转矩为3057N·m,机械效率大于0.90。
5.5油管内径计算
本系统管路较为复杂,取其主要几条(其余略),有关参数及计算结果列于表6。
5.6确定油箱的有效容积
按下式来初步确定油箱的有效容积
V=aqV
已知所选泵的总流量为201.4L/min,
这样,液压泵每分钟排出压力油的体积
为0.2m3。
参照表4—3取a=5,算得
有效容积为
V=5×0.2m3=1m3
6.液压系统性能验算
6.1验算回路中的压力损失
本系统较为复杂,有多个液压执行元件动作回路,其中环节较多,管路损失较大的要算注射缸动作回路,故主要验算由泵到注射缸这段管路的损失。
⑴沿程压力损失
沿程压力损失,主要是注射缸快速注射时进油管路的压力损失。
此管路长5m,管内径0.032m,快速时通过流量2.7L/s;选用20号机械系统损耗油,正常运转后油的运动粘度ν=27mm2/s,油的密度ρ=918kg/m3。
油在管路中的实际流速为
油在管路中呈紊流流动状态,其沿程阻力系数为:
求得沿程压力损失为:
⑵局部压力损失
局部压力损失包括通过管路中折管和管接头等处的管路局部压力损失Δp2,以及通过控制阀的局部压力损失Δp3。
其中管路局部压力损失相对来说小得多,故主要计算通过控制阀的局部压力损失。
参看图2,从小泵出口到注射缸进油口,要经过顺序阀17,电液换向阀2及单向顺序阀18。
单向顺序伺17的额定流量为50L/min,额定压力损失为0.4MPa。
电液换向阀2的额定流量为190L/min,额定压力损失0.3MPa。
单向顺序阀18的额定流量为150L/min,额定压力损失0.2MPa。
通过各阀的局部压力损失之和为
从大泵出油口到注射缸进油口要经过单向阀13,电液换向阀2和单向顺序阀18。
单向阀13的额定流量为250L/min,额定压力损失为0.2MPa。
通过各阀的局部压力损失之和为:
由以上计算结果可求得快速注射时,小泵到注射缸之间总的压力损失为
∑p1=(0.03+0.88)MPa=0.91MPa
大泵到注射缸之间总的压力损失为
∑p2=(0.03+0.65)MPa=0.68MPa
由计算结果看,大小泵的实际出口压力距泵的额定压力还有一定的压力裕度,所选泵是适合的。
另外要说明的一点是:
在整个注射过程中,注射压力是不断变化的,注射缸的进口压力也随之由小到大变化,当注射压力达到最大时,注射缸活塞的运动速度也将近似等于零,此时管路的压力损失随流量的减小而减少。
泵的实际出口压力要比以上计算值小一些。
综合考虑各工况的需要,确定系统的最高工作压力为6.8MPa,也就是溢流阀7的调定压力。
6.2液压系统发热温升计算
⑴计算发热功率液压系统的功率损失全部转化为热量。
发热功率计算如下
Phr=Pr-Pc
对本系统来说,Pr是整个工作循环中双泵的平均输入功率。
具体的pi、qi、ti值见表7。
这样,可算得双泵平均输入功率Pr=12kW。
系统总输出功率
求系统的输出有效功率:
由前面给定参数及计算结果可知:
合模缸的外载荷为90kN,行程0.35m;注射缸的外载荷为192kN,行程0.2m;预塑螺杆有效功率5kW,工作时间15s;开模时外载荷近同合模,行程也相同。
注射机输出有效功率主要是以上这些。
总的发热功率为:
Phr=(15.3-3)kW=12.3kW
⑵计算散热功率前面初步求得油箱的有效容积为1m3,按V=0.8abh求得油箱各边之积:
a·b·h=1/0.8m3=1.25m3
取a为1.25m,b、h分别为1m。
求得油箱散热面积为:
At=1.8h(a+b)+1.5ab
=(1.8×l×(1.25+1)+1.5×1.25)m2=5.9m2
油箱的散热功率为:
Phc=K1AtΔT
式中K1——油箱散热系数,查表5—1,K1取16W/(m2·℃);
ΔT——油温与环境温度之差,取ΔT=35℃。
Phc=16×5.9×35kW=3.3kW<Phr=12.3kW
由此可见,油箱的散热远远满足不了系统散热的要求,管路散热是极小的,需要另设冷却器。
⑶冷却器所需冷却面积的计算
冷却面积为:
式中K——传热系数,用管式冷却器时,取K=116W/(m2.·℃);
Δtm—平均温升(℃);
取油进入冷却器的温度T1=60℃,油流出冷却器的温度T2=50℃,冷却水入口温度tl=25℃,冷却水出口温度t2=30℃。
则:
℃
所需冷却器的散热面积为:
考虑到冷却器长期使用时,设备腐蚀和油垢、水垢对传热的影响,冷却面积应比计算值大30%,实际选用冷却器散热面积为:
A=1.3×2.8m2=3.6m2
注意;系统设计的方案不是唯一的,关键要进行方案论证,从中选择较为合理的方案。
同一个方案,设计者不同,也可以设计出不同的结果,例如系统压力的选择、执行元件的选择、阀类元件的选择等等都可能不同。
附:
系统工况图