炼钢厂特殊操作规程.docx
《炼钢厂特殊操作规程.docx》由会员分享,可在线阅读,更多相关《炼钢厂特殊操作规程.docx(13页珍藏版)》请在冰豆网上搜索。
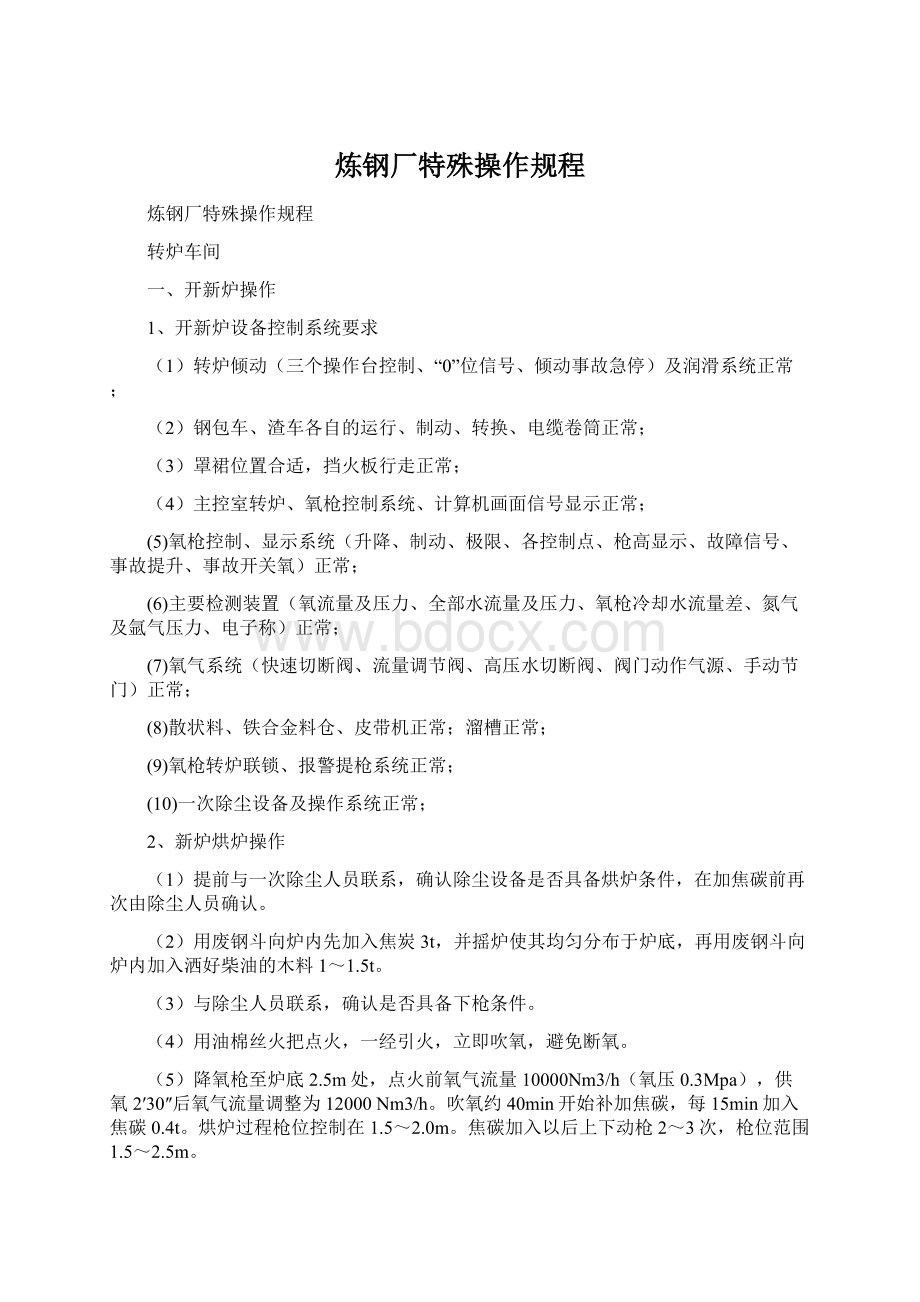
炼钢厂特殊操作规程
炼钢厂特殊操作规程
转炉车间
一、开新炉操作
1、开新炉设备控制系统要求
(1)转炉倾动(三个操作台控制、“0”位信号、倾动事故急停)及润滑系统正常;
(2)钢包车、渣车各自的运行、制动、转换、电缆卷筒正常;
(3)罩裙位置合适,挡火板行走正常;
(4)主控室转炉、氧枪控制系统、计算机画面信号显示正常;
(5)氧枪控制、显示系统(升降、制动、极限、各控制点、枪高显示、故障信号、事故提升、事故开关氧)正常;
(6)主要检测装置(氧流量及压力、全部水流量及压力、氧枪冷却水流量差、氮气及氩气压力、电子称)正常;
(7)氧气系统(快速切断阀、流量调节阀、高压水切断阀、阀门动作气源、手动节门)正常;
(8)散状料、铁合金料仓、皮带机正常;溜槽正常;
(9)氧枪转炉联锁、报警提枪系统正常;
(10)一次除尘设备及操作系统正常;
2、新炉烘炉操作
(1)提前与一次除尘人员联系,确认除尘设备是否具备烘炉条件,在加焦碳前再次由除尘人员确认。
(2)用废钢斗向炉内先加入焦炭3t,并摇炉使其均匀分布于炉底,再用废钢斗向炉内加入洒好柴油的木料1~1.5t。
(3)与除尘人员联系,确认是否具备下枪条件。
(4)用油棉丝火把点火,一经引火,立即吹氧,避免断氧。
(5)降氧枪至炉底2.5m处,点火前氧气流量10000Nm3/h(氧压0.3Mpa),供氧2′30″后氧气流量调整为12000Nm3/h。
吹氧约40min开始补加焦碳,每15min加入焦碳0.4t。
烘炉过程枪位控制在1.5~2.0m。
焦碳加入以后上下动枪2~3次,枪位范围1.5~2.5m。
(6)烘炉时底吹选择氮气搅拌,流量控制在210Nm3/h。
(7)总烘炉时间不少于5小时。
(8)烘炉结束,关闭炉前挡火门,摇炉75度,观察烘炉质量及残焦情况,检查炉衬及出钢口,其它方面具备开炉条件时,烘炉结束,不倒残余焦碳装铁炼钢。
(9)烘炉前解除氧气工作压力低报警提枪连锁,烘炉结束恢复。
(10)烘炉期间对设备系统状况进行全面检查,发现问题及时安排处理。
3.开新炉操作
(1)烘炉结束后,保证烧结好炉衬,炉衬温度要均匀。
检查确认炉衬无重大缺陷,砖缝严密。
(2)兑铁前与一次除尘人员联系确认是否具备兑铁生产条件。
(3)第一炉为全铁冶炼,铁水装入量为133±1t,冶炼钢种为普碳钢。
(4)第一炉操作氧压控制在0.80~0.85MPa,氧气流量设定为自动调节,开吹时氧流量24500m3/h,40秒后氧流量调整为设定值,开吹枪位距离液面1.6~1.8m,过程枪位1.6~2.0m,终点降枪1.4m。
(5)第一批渣料在开吹点火正常后加入(镁球800Kg全部在第一批料中加入,石灰第一批加入量为总量的70%~80%),其余石灰在开吹约4min后(必须注意观察此时烟气成分O2含量在0.5%以下)根据化渣情况分批加入。
(6)炉渣碱度控制在3.5-4.0,MgO控制在8-11%。
(7)出钢温度控制在1760~1780℃。
(8)出钢前先检查出钢口,拉碳后快速组织出钢。
(9)开新炉1~10炉内要求连续冶炼且30炉内不允许将炉体摆至炉口向下位置。
(10)开新炉只允许冶炼普通碳素结构钢。
注意事项:
1、兑铁后测量安全液面,保证安全液面50mm以上。
2、氧枪事故小车吹炼过程中必须在吹炼位置。
3、冶炼终点时观察火焰稳定后方可提枪拉碳,倒炉时必须缓慢摇炉,炉前人员在摇炉过程中注意躲避,避免正对炉口。
4、拉碳接渣渣斗必须干燥且必须垫好罐底。
5、开炉第一炉不挡渣,第二炉开始挡渣。
二、留渣操作
具体操作
1、要求装入量稳定在140±2吨。
2、铁水≤0.40%时开始采用留渣操作,铁水Si≥0.35%时,可留全渣的30%,否则会增加白灰的使用量;铁水Si≤0.35%时,可适当提高留渣量以30%为基数,提高渣量的同时酌减废钢避免抑制前期温度,或采用留全渣全铁操作。
3、终点C≥0.08%、TFe≤14%、终点温度≤1665℃时,将渣溅干后加入废钢,废钢≤65kg/t时可留全渣的30%左右;将渣溅干后,采用全铁时可留全渣操作,但铁水温度要求≥1280℃。
4、终点C≤0.08%、TFe≥14%、终点温度≥1665℃时,溅渣过程需要加入改质剂、镁球或白灰改良渣质,总量≤5kg/t,必须将渣溅干,此时留渣应少于总渣量的30%。
5、终渣SiO2含量小于12%时,可留全渣操作。
6、终渣SiO2含量小于16%时,可留全渣的30%。
7、终渣SiO2含量大于16%时不采取留渣操作。
四、留渣操作注意事项
1、根据终点结果及入炉条件炼钢工决定是否采用留渣操作,留渣操作前提是必须避免大型喷溅、烧枪等安全事故的发生。
2、决定留渣操作后必须由炼钢工或一助手亲自指挥摇炉倒渣,炉内要求留下规定的渣量。
3、一助手、主控工、废钢工负责检查废钢质量及数量,坚决杜绝开吹打不着火的现象发生。
4、炉内余渣要求必须是溅渣后的干渣,如果不是干渣应加入适量白灰摇炉进行干燥后在执行装入制度,坚决杜绝装铁大喷现象的发生。
5、测量熔池液面炉次不得留渣,确保测量数据的准确性,以便正确确定开吹枪位。
6、留渣炉次必须遵循点着火焰后再加料的原则,杜绝将火焰压灭的现象。
7、炉内留渣后会促使渣料快速成渣,这样就要求开吹枪位要比不留渣操作的炉次低50-100mm,避免开吹后碳火焰的形成导致喷溅现象的发生。
三、特殊铁水和回炉钢水的冶炼操作要点
1特殊铁水的操作要点
1.1硫高硅低铁水操作要点
(1)S≥0.05%Si≤0.15%
(2)用硅铁将Si配加到0.25%。
(3)枪位比正常炉次可提高100~150mm,确保5分钟化好头批料。
(4)头批料加入锰矿300Kg,其他渣料与正常炉次相同。
(5)终点C在0.15~0.25%时,拉C倒渣,测温取样。
(6)视终点温度和成分追加1000~2000kg石灰后补吹,补吹约2分钟。
再次倒炉测温取样,根据第一次样S含量,决定是否再次补吹。
(7)如第一次样S≤0.040%,温度合适即可出钢;若S>0.040%,可视情况再追加500~800kg石灰,再补吹1分钟,若S合格后就可出钢。
(8)其他操作同正常炉次。
1.2硅高铁水操作要点:
(1)Si≥0.60%
(2)采用双渣法冶炼。
(3)废钢要比正常炉次多加2~5吨。
(4)渣料配比要按碱度R:
2.8~3.2配加石灰。
(5)开吹4~5分钟,提枪、倒炉倒渣,尽量多倒渣。
(6)倒渣后将剩余渣料全部加入。
(7)其他操作同正常炉次。
1.3高磷铁水操作要点:
(1)P≥0.12%
(2)采用双渣法冶炼。
(3)渣料配比要按碱度R:
2.8~3.2配加石灰。
(4)开吹枪位可适当高100~200mm,确保头批料早化、化透。
(5)吹炼4~5分钟,提枪、倒炉倒渣,要尽量多倒渣。
(6)倒渣后将剩余渣料全部加入再吹,避免返干。
(7)其他操作同正常炉次。
2、回炉钢水的冶炼
(1)整炉回炉钢水要分两次冶炼。
(2)一吨回炉钢水的降温效果相当于一吨废钢。
(3)回炉钢水≥40吨时要补加150~200kgSi-Fe提温。
(4)渣料按R:
2.6~3.0配加,但轻烧白云石必保≮1000kg(或镁球≮300Kg),锰矿≮500kg。
(5)脱氧合金要按1kg/吨钢加入,硅含量要确保0.15~0.18%,吹氩时适当喂丝。
(6)其他操作与正常炉次。
四、溅渣及炉况维护操作
炉体维护
1、炉体维护以操作维护为主,以溅渣护炉为基础,补炉料补炉、喷补和渣补相结合的原则。
2、操作过程中严格控制深吹,根据入炉条件、计划钢种合理加入废钢,对热量不足的炉次可采取加提温剂方法对热量进行补偿。
3、非生产状况下不准将转炉放在零位,以减轻炉内热量损失,防止上部漏水进入炉内。
4、出钢后对炉体进行检查,出现明显异常及时进行炉体维护。
优先采用溅渣护炉对炉体进行维护,对未溅渣的炉次可采用留渣加石灰等造渣料对炉体进行维护,也可以根据实际情况对炉体进行补炉料补炉、喷补和渣补。
5、补炉的原则是勤补、薄补、高温快补。
6、溅渣护炉
6.1、溅渣氮气压力及流量
氮气压力:
1.0±0.05MPa;流量:
17200~20500m3/h
6.2、溅渣枪位
(1)1.3~1.7m,适用于炉底下降大于10cm。
(2)0.7~0.8m,适用于炉底上涨大于20cm。
(3)1.1~1.4m,正常溅渣操作。
6.3、溅渣时间3~5min,可根据炉渣状况适当变化。
6.4、要求每周测量炉膛直径和炉膛内高一次并作好记录,并根据炉底情况,适当控制溅渣枪位。
6.5、溅渣护炉操作程序
6.6、炉龄≥3炉开始溅渣,每冶炼一炉钢溅渣一次。
溅渣前钢水必须出净。
如果炉内剩少量钢水,应根据炉内钢水量加入石灰500~2000kg,前后反复摇炉待炉渣发稠后留渣再加入适量造渣料后方可组织生产。
生产时先加废钢后兑铁,兑铁时做好必要的安全确认,并做好冶炼终点确认。
6.7、溅渣前检查确认氧气系统处于关闭状态,氮气系统处于待打开状态。
6.8、溅渣采取变枪位操作,起渣枪位1.2m,随渣量、炉渣温度降低,逐步降低枪位。
6.9、转炉出钢完毕迅速将转炉摇至零位,检查确认各项要求符合溅渣条件后降枪进行吹氮操作。
6.10、终点C≥0.08%或出钢温度≤1660℃时,炉渣成分和状态良好,出钢后直接溅渣,起渣后逐步降低枪位。
6.11、当终点C<0.08%或出钢温度>1660℃时,炉渣氧化性强,在溅渣过程必须加入镁球或改质剂稠化炉渣。
溅渣时间控制在3~5min内,起渣后逐步降低枪位。
镁球或改质剂要在降枪吹氮后才能加入。
6.12、炉渣渣量过少且粘度大,溅渣时间短,基本在1分钟左右,溅渣初始枪位定在最低枪位。
6.13溅渣完毕,将炉内残渣倒净后方可兑铁炼钢。
严禁炉内留钢留渣兑铁水。
7、喷补
7.1、炉体耳轴部位、炉后出钢口周围、前后大面渣线部位出现异常时可采用喷补维护炉体。
7.2、喷补前检查喷补机设备、罐内喷补料、喷补气源是否满足喷补要求。
7.3、喷补时先清扫喷补管道,待罐压达到要求后,开下蝶阀送料,调节喷补用水量(以喷补料能附着在炉体上为原则),喷补时喷枪与需修补炉衬表面基本保持垂直,喷枪喷头距喷补位置0.8m~1.5m。
7.4、喷补结束后先关料,再关水,最后关气源。
7.5、喷补结束后,烧结时间≥5min。
8、扣补和贴补
8.1、炉体前、后大面及炉底出现异常时可采用扣补和贴补进行炉体维护。
8.2、炉底及接缝
(1)炉底扣补采用自流料,当自流料倒入炉内后,前后摇炉使自流料铺到预补位置,下枪用正常流量的三分之一点吹一次后将转炉摇垂直后开始烧结。
补炉底烧结时间大于50分钟,补炉料每次1~2吨。
(2)烧结时间是从补炉料倒入炉内转炉摇到位开始计时。
(3)发生炉衬掉砖可根据具体情况用补炉砖贴补,用喷补料填缝。
(4)补炉后第一炉不许加带切头废钢。
兑铁前喊开炉前周围人员缓慢兑铁,拉碳摇炉时,喊开炉前周围人员,待炉子摇平后,静止大于1分钟再取样测温。
(5)要求炼钢工随时检查炉衬情况,及时提出补炉和停炉意见。
(6)在开新炉炉龄达到200炉时将炉底外接缝部位用喷补料喷严,要求每班进行检查,一旦发现有掉料现象及时组织喷补。
8.3、大面
根据炉衬情况来组织前后大面的扣补操作,溅完渣将炉渣倒净后,将补炉料(自流料)倒入炉内摇炉使补炉料铺到到预补位置或贴砖并喷补砖缝。
用自流料补大面时,烧结时间≥30min;用补炉砖补炉后,烧结时间≥40min。
8.4、耳轴及其它部位
炉龄中后期根据炉帽两侧和耳轴蚀损情况进行贴补炉砖结合喷补方式进行炉体维护。
连铸车间
一、钢包回转台的操作:
钢包回转台设浇注侧机旁操作箱LC201,其上设置浇铸位钢包盖操作(升降和旋转)、大包臂操作(每个臂的升降和包臂的旋转)和浇注侧大包滑动水口各操作按钮。
控制功能:
在正常操作状态下,通过在钢包回转台操作箱上,实现下述顺控功能:
a:
回转动作:
①正常操作:
液压制动器打开―――发打开信号-编码器控制到位后,液压阀动作,液压制动器制动,电机停止。
(回转台每转一圈,浇注侧的用于此功能的行程开关进行编码器清零,同时此行程开关发讯表示1#侧叉型臂在浇注位,2#叉型臂上的用于此功能的行程开关发讯表示2#侧叉型臂在浇注位。
②电机事故驱动:
按下“事故旋转按钮”,液压阀动作―――发打开信号―――操作手动阀液压制动器打开,液压马达驱动―――碰停止行程开关就位后,手动控制液压马达停止,液压制动器制动。
③断电事故操作:
断电后手动控制使液压控制部分接通―――液压制动器打开―――液压马达驱动―――回转(应使钢包避开驱动装置上方)―――就位后,操作手动阀,液压马达停止,液压制动器制动。
b:
钢包升降动作(包括与钢包盖的连锁关系):
钢包鞍型座处于低位时接受钢包―――盖上包盖―――升起到高位―――开始旋转,回转至浇注位后,钢包处于高位,安装长水口―――钢包降入低位(包盖始终盖住高低位钢包),―――开始浇注――浇注完毕,钢包升起,卸掉长水口―――回转至受包位,降入低位―――包盖升起出―――吊走钢包。
c:
钢包加盖装置动作:
受包位低位受包后,钢包加盖回转变频电机启动,包盖由等待位旋入―――旋入到位,开关发讯―――包盖降下盖住低位钢包―――钢包升起(钢包盖随钢包同步升起),钢包及盖回转到浇注位,钢包降入低位(钢包盖随钢包同步下降)――此钢包钢水浇注完毕――包盖升起――包盖由工作位旋出至等待位。
*包盖的回转必须在钢包处于低位和加盖装置处于高位时方可动作。
*包盖的回转在两侧的旋入位各有一保护接近开关。
联锁:
1.电机启动同时,回转台润滑泵启动,向回转齿润滑,电机停止,润滑泵停止。
2.液压制动器未打开前,回转臂不能转动。
3.液压系统正常时,电机才能启动(浇注前提条件之一)
此外还设置了受钢侧机旁操作箱LC202,其上设置受钢侧钢包盖操作(升降和旋转)、和受钢侧大包滑动水口各操作按钮。
现场主要用于钢包浇注完毕后通过点动按钮来帮助摘下液压缸。
还设置了大包事故旋转机旁操作箱LC203。
二冷水
各区切断阀门打开。
●当在结晶器操作箱主选择开关在“尾坯”位置,程序执行尾坯输出程序。
结晶器操作箱上按钮设置:
在结晶器操作箱上设置下述按钮:
—拉矫机速度设定按钮
—拉矫机速度指示表
—浇注启动按钮
—浇注停止按钮
—引锭杆点动上、下、停止操作盒
拉矫机
1)功能
拉矫机用于插入和退出刚性引锭杆,并拉出铸坯。
2)控制
拉矫机的操作控制在拉矫切割辊道操作台OS001上。
在拉矫切割操作室内设
有拉矫切割辊道操作台,在操作台上每流设有拉矫机“向前”“向后”“停止”
“拉矫辊抬起”“拉矫辊压下”“矫直辊抬起”“矫直辊压下”操作按钮,可手
动操作。
引锭杆及存放装置
1)功能:
引锭杆及引锭杆存放装置用来将铸坯自结晶器内引出并平稳通过拉矫机,实现连铸机的顺利开浇。
2)控制
自动控制(每流)
a.送引锭程序
当按下“送引锭”按钮,自动送引锭程序顺控如下:
第一步
控制液压的电磁阀动作,液压缸伸出,带动摆臂将引锭杆摆下至“在线
停止位置”。
第二步
LS.L发讯,引锭杆至在线停止位,液压缸停止动作,延时2~15秒后,拉矫
机的拉坯辊及脱锭辊抬起。
第三步
延时5秒后电机Mot全力矩(额定力矩)全速启动,同时电机尾部的编码器
开始计数,引锭杆放下28.5°,(对应编码器发出~79315.5个脉冲),电机停止。
注:
此时虽然感应板经过接近开关PS,但PS信号无用。
第四步
延时几十秒后,拉矫机的拉坯辊高压下,准备计时15秒后,Mot.开始低力矩及低频(与拉矫机送引锭杆同步)运转。
注:
此时Mot.处于低力矩堵转和低频率运转状态。
第五步
延时一秒后,拉矫机的拉坯辊开始送引锭杆(高压下),同时拉矫机的编码器
开始计数;在拉矫机的编码器控制下,将引锭杆在送12秒后,Mot.停止运转,之后拉矫机将引锭杆送至结晶器下口~500mm时拉矫机停止(拉矫机编码器控制)。
第六步:
在结晶器操作盘上手动将引锭杆点动到结晶器内正确位置。
注:
同时压住引锭杆时,Mot.处于低力矩堵转和低频率低速运转状态。
当拉矫机脱锭辊在低位时,引锭杆不能向结晶器方向运动。
b.脱引锭和拉坯过程
前提条件:
在结晶器操作盘上选择开关在“浇注”位置,浇注选择开关在“自动”状态,拉矫辊在冷坯压力状态下,脱锭辊(矫直辊)在抬起位置,在结晶器操作箱上给定拉矫机速度值。
在结晶器操作盘上按下“浇注”启动按钮,程序顺控如下
第一步:
拉矫机拉坯辊启动开始向拉坯方向拉坯(高压下)(结晶器振动、排蒸汽风机同时启动、二冷水阀门打开),拉矫机编码器开始计数。
到一定位置后,拉坯辊的液压缸压力由高压转为低压(压热坯压力),准备压热坯;根据拉矫机发出的信号,Mot.以低力矩和低频率低速运转状态启动。
注:
保证同时压住引锭杆时,Mot.处于低力矩堵转和低频率低速运转状态。
第二步:
感应板使PS发讯,拉矫机的脱引锭辊以高压压下脱锭,此时,电机Mot.尾部的编码器置位,开始计数;;脱引锭后Mot.以高速运转状态收起引锭杆。
注:
同时压住引锭杆时,Mot.处于低力矩堵转和低频率低速运转状态。
第三步:
Enc.计数控制将引锭杆收起3秒,(对应编码器发出8349个脉冲),电机停止运转,引锭杆至“在线停止位置”停止;脱引锭后,脱引锭辊(矫直辊)由高压转为压热坯压力。
第四步:
控制液压缸的电磁阀动作,液压缸缩回,将摆臂和引锭杆摆起,LS.H发讯,摆起到位,液压缸停止动作。
第五部:
需要时,人工控制Mot.以全力和全速将引锭杆送至存放辊处,可在存放辊平台处
更换引锭头和引锭棒,Enc.计数控制将引锭杆送出21.5秒(对应编码器发出59834.5个脉冲),电机停止转动,将引锭杆从存放辊处收回的动作与上述相反、原理相同。
注:
此时,虽然感应板经过接近开关PS,但PS信号无用。
联锁控制:
1.在“手动/自动”方式时,当引锭杆在拉矫机位置时,拉辊上辊不能抬起。
2.在“手动/自动”方式时当引锭杆在矫直辊位置时,矫直辊上辊不能下降。
3.当引锭杆在拉矫机区域时,引锭杆驱动装置仅能以“低力矩”与拉矫机相同方向转动。
4.当引锭杆驱动装置转动时,引锭杆驱动装置制动器必须打开。
5.如果在结晶器操作箱上选择开关在“浇注”位置时,拉矫机仅能向浇注方向转动。
当选择开关在“引锭杆操作箱”上时,在“主操作台上”和“结晶器操作箱”上均不能操作引锭杆。
6.拉矫机与振动装置及二冷水阀门联锁,当拉矫机启动时,振动装置开始振,二冷水各流切断阀门打开。
火焰切割机
1)功能
火焰切割机用于将铸坯切割成所需要的定尺长度。
2)控制
该设备由上海新中机电一体成套供货。
在切割拉矫操作室内设有火焰切割机操作
台。
铸坯的定尺装置拉矫机编码器发出定尺到达信号。
输送辊道一(7~11#辊)
1)功能
位于火焰切割机后,用于将热铸坯从切割区输出到公用辊道上
3)控制
在浇注状态下,当收到切割发出切割完毕信号后,该组辊道启动将切割定尺输出
并延时停止(10~30秒)。
在拉矫切割辊道操作台上(OS001)可手动操作该组辊道“向前”、“向后”和“停
止”操作。
输送辊道二(12~28#辊)
1)功能
输送辊道
(二)位于输送辊道
(一)后,用于将切割后的铸坯输送到出坯
区,每4流共用1个长辊道,采用每个辊子一套传动装置。
2)控制
在自动状态下,该组辊道长时间运转。
在出坯操作台(OS002)上可手动操作该
组辊道“向前”、“向后”、“停止”操作。
冷床区辊道(29~38#辊)
1)功能
冷床区辊道位于输送辊道
(二)后,用于将铸坯输送至固定挡板前,然后由抬
钢机抬起铸坯,再由双向横向移钢车将铸坯运送至方坯翻转冷床或铸坯存储床。
2)控制
见出坯系统总控制说明
出坯系统
1)功能
出坯系统包括:
辊道和抬钢机、横向移钢机、步进式翻钢冷床、推钢机、铸坯存放台架、压力开关、升降挡板、固定挡板等。
进入冷床区辊道的铸坯,由抬钢机将其翻到上部滑道上,浇方坯时,由(双向)横向移钢车将方坯移至液压步进翻转冷床,并经翻转冷床步进到末端的收集台架上收集成排,用磁盘吊将铸坯运往
坯库堆场码垛。
浇矩形坯时,由(双向)横向移钢车将矩形坯移至矩形坯存储
床,用夹钳将铸坯运往坯库堆场码垛。
2)控制
见出坯系统总控制说明
出坯系统总控制说明:
第一步:
当某流铸坯(定尺7、8、9、12m)进入冷床区辊道,如需要手动控制升降挡板,要求能够保证升降挡板1的动作安全完成
第二步:
手动给抬钢机发抬钢、落下指令。
第三步:
手动给移钢机前进、后退指令,将坯子移动到翻钢冷床处。
注意:
当移钢机向步进翻转冷床方向存储床推钢时,抬钢机禁止抬钢,到位允许
再次抬钢。
当移钢机向步进翻转冷床方向的反方向矩形坯存储床推钢时,抬钢机禁止抬钢,到位允许再次抬钢。
第四步:
手动控制移钢机回到原位后,控制抬钢机继续抬钢。
移钢过程中的限位保护:
1.当行程开关2发讯时,控制移钢车在极限位停车。
2.当接近开关1发讯时,控制移钢车在极限位停车。
方坯出坯:
由移钢车推坯至步进翻转冷床再由推钢机推至方坯存储床,再由出坯跨电磁挂梁起重机吊走。
矩形坯出坯:
在进翻转冷床之前设置一矩形坯存储床,在对侧设置另一矩形坯
存储床。
在其中一侧有铸坯占位(天车没吊走),横移车向另一侧推钢。
双排出坯时,由于天车吊运周期紧张,横移车一次推8流共16根短坯进入矩形坯存储床,桥吊夹钳一次兜8根短坯的两头将铸坯吊出存储床下线堆存。
单排出坯时,横移车一次推4根长坯进入矩形坯存储床,桥吊夹钳一次夹铸坯两侧将铸坯吊出存储床下线堆存。
在主控制台上输入生产铸坯类型和定尺长度后,编程应能够实现后部出坯的各种操作要求。
2.操作控制台应设有3、4、5、6、7、8流出坯的转换开关。
如果某流没有出坯或出现断流事故时,人工设定与浇注流数匹配的转换开关的位置,此时,移钢机则根据生产几流的情况和接收到几个记数的情况决定移钢动作的开始时间。
3.在翻转冷床动齿条运动过程中,不允许移钢机向前移钢进入翻转冷床的入口。
此时移钢机应停在等待位。
在翻转冷床动齿条运行完一个周期并停稳后,才允许移钢机向前移钢进入翻转冷床的入口。