焊接结构备料加工.docx
《焊接结构备料加工.docx》由会员分享,可在线阅读,更多相关《焊接结构备料加工.docx(11页珍藏版)》请在冰豆网上搜索。
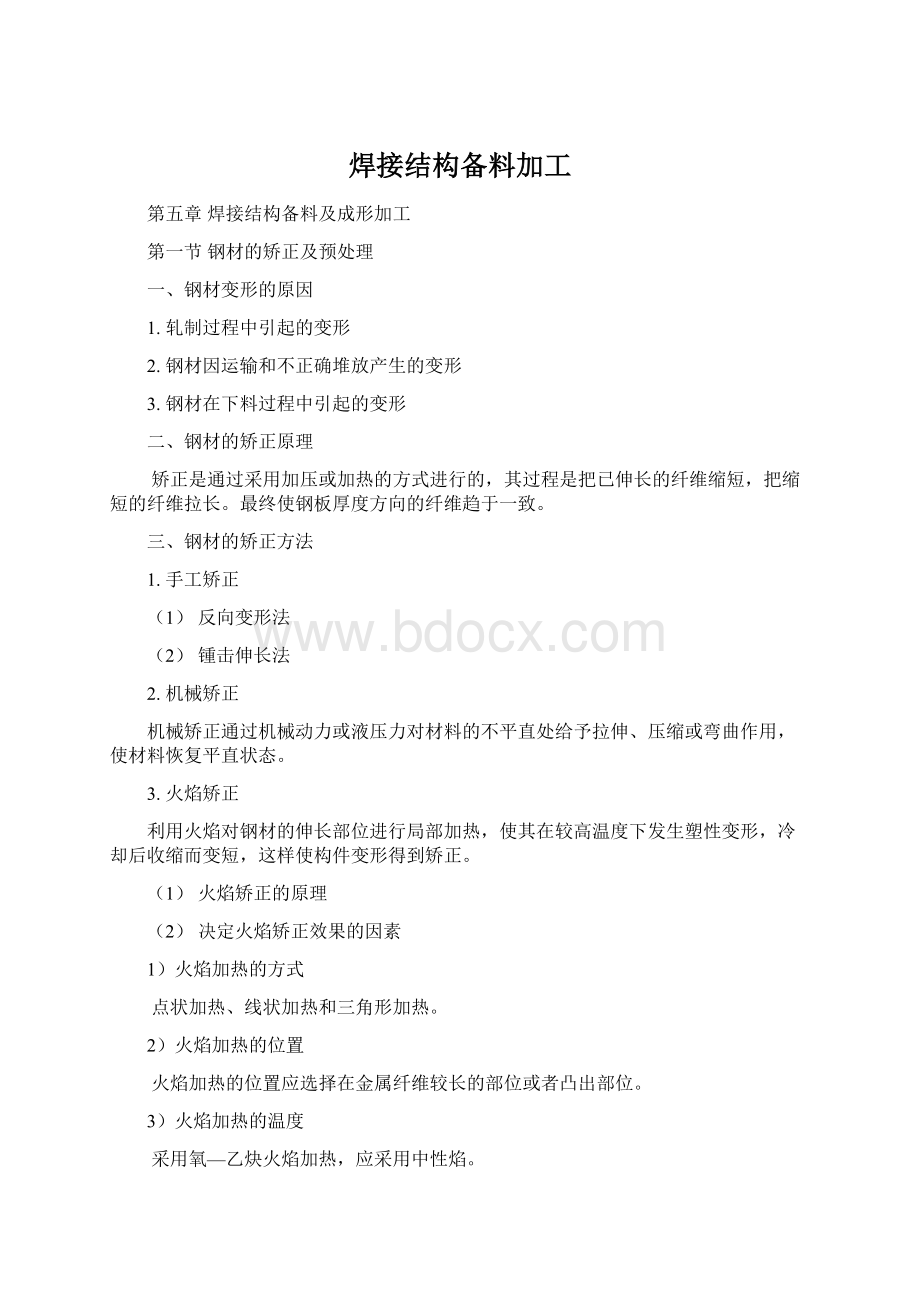
焊接结构备料加工
第五章焊接结构备料及成形加工
第一节钢材的矫正及预处理
一、钢材变形的原因
1.轧制过程中引起的变形
2.钢材因运输和不正确堆放产生的变形
3.钢材在下料过程中引起的变形
二、钢材的矫正原理
矫正是通过采用加压或加热的方式进行的,其过程是把已伸长的纤维缩短,把缩短的纤维拉长。
最终使钢板厚度方向的纤维趋于一致。
三、钢材的矫正方法
1.手工矫正
(1)反向变形法
(2)锺击伸长法
2.机械矫正
机械矫正通过机械动力或液压力对材料的不平直处给予拉伸、压缩或弯曲作用,使材料恢复平直状态。
3.火焰矫正
利用火焰对钢材的伸长部位进行局部加热,使其在较高温度下发生塑性变形,冷却后收缩而变短,这样使构件变形得到矫正。
(1)火焰矫正的原理
(2)决定火焰矫正效果的因素
1)火焰加热的方式
点状加热、线状加热和三角形加热。
2)火焰加热的位置
火焰加热的位置应选择在金属纤维较长的部位或者凸出部位。
3)火焰加热的温度
采用氧—乙炔火焰加热,应采用中性焰。
一般钢材的加热温度应在600--800℃左右,低碳钢不大于850℃。
(3)火焰矫正的步骤
1)分析变形的原因和钢结构的内在联系
2)正确找出变形的部位
3)确定加热方式、加热部位和冷却方式
4)矫正后检验
四、钢材的预处理
对钢材表面进行去除铁锈、油污、氧化皮清理等为后序加工准备的工艺称为预处理。
1.机械除锈法
机械除锈法常用的有喷砂(或喷丸,手动砂轮或钢丝刷,砂布打磨,刮光或抛光等。
2.化学除锈法
用腐蚀性的化学溶液对钢材表面进行清理。
化学处理法一般分为酸洗法和碱洗法。
酸洗法可除去金属表面的氧化皮、锈蚀物等;碱洗法主要用于去除金属表面的油污
第二节划线、放样与下料
一、识图与划线
1.焊接结构的施工图
图纸是工程的语言,读懂和理解图纸是进行施工的必要条件。
焊接结构是以钢板和各种型钢为主体组成的,因此表达钢结构的图纸就有其特点,掌握了这些特点就容易读懂焊接结构的施工图,从而正确地进行结构件的加工。
(1)焊接结构图的特点主要包括以下几个方面:
1)一般钢板与钢结构的总体尺寸相差悬殊,按正常的比例关系是表达不出来的,但往往需要通过板厚来表达板材的相互位置关系或焊缝结构,因此在绘制板厚、型钢断面等小尺寸图形时,是按不同的比例夸大画出来的。
2)为了表达焊缝位置和焊接结构,大量采用了局部剖视和局部放大视图,要注意剖视和放大视图的位置和剖视的方向。
3)为了表达板与板之间的相互关系,除采用剖视外,还大量采用虚线的表达方式,因此,图面纵横交错的线条非常多。
4)连接板与板之间的焊缝一般不用画出,只标注焊缝代号。
但特殊的接头形式和焊缝尺寸应该用局部放大视图来表达清楚,焊缝的断面要涂黑,以区别焊缝和母材。
5)为了便于读图,同一零件的序号可以同时标注在不同的视图上。
(2)焊接结构图的读识方法焊接结构施工图的读识一般按以下顺序进行:
首先,阅读标题栏,了解产品名称、材料、重量、设计单位等,核对一下各个零部件的图号、名称、数量、材料等,确定哪些是外购件(或库领件),哪些为锻件、铸件或机加工件;再阅读技术要求和工艺文件,正式识图时,要先看总图,后看部件图,最后再看零件图;有剖视图的要结合剖视图,弄清大致结构,然后按投影规律逐个零件阅读,先看零件明细表,确定是钢板还是型钢;然后再看图,弄清每个零件的材料、尺寸及形状,还要看清各零件之间的连接方法、焊缝尺寸、坡口形状,是否有焊后加工的孔洞、平面等。
2.划线
划线是根据设计图样上的图形和尺寸,准确地按1:
1在待下料的钢材表面上划出加工界线的过程。
划线的作用是确定零件各加工表面的余量和孔的位置,使零件加工时有明确的标志;还可以检查毛坯是否正确;对于有些误差不大,但已属不合格的毛坯,可以通过借料得到挽救。
划线的精度要求在0.25mm~0.5mm范围内。
划线的基本规则:
垂线必须用作图法;
用划针或石笔划线时,应紧抵直尺或样板的边沿;
3)圆规在钢板上划圆、圆弧或分量尺寸时,应先打上样冲眼,以防圆规尖滑动;
4)平面划线应遵循先画基准线,后按由外向内,从上到下,从左到右的顺序划线的原则。
先画基准线,是为了保证加工余量的合理分布,划线之前应该在工件上选择一个或几个面或线作为划线的基准,以此来确定工件其它加工表面的相对位置。
一般情况下,以底平面、侧面、轴线为基准。
划线的准确度,取决于作图方法的正确性、工具质量、工作条件、作图技巧、经验、视觉的敏锐程度等因素。
除以上之外还应考虑到它的工件因素,即工件加工成型时如气割、卷圆、热加工等的影响;装配时板料边缘修正和间隙大小的装配公差影响;焊接和火焰矫正的收缩影响等。
划线的方法:
划线可为平面划线的立体划线两种。
1)平面划线与几何作图相似,在工件的一个平面上划出图样的形状和尺寸。
有时也可以采用样板一次划成。
2)立体划线是在工件的几个表面上划线,亦即在长、宽、高三个方向上划线。
划线时应注意以下几个问题:
1)熟悉结构的图样和制造工艺,根据图样检验样板、样杆,核对选用的钢号、规格应符合规定的要求。
2)检查钢板表面是否有麻点、裂纹、夹层及厚度不均匀等缺陷。
3)划线前应将材料垫平、放稳,划线时要尽可能使线条细且清晰,笔尖与样板边缘间不要内倾和外倾。
4)划线时应标注各道工序用线,并加以适当标记,以免混淆。
5)弯曲零件时,应考虑材料的轧制纤维方向。
6)钢板两边不垂直时,一定要去边。
划尺寸较大的矩形时,一定要检查对角线。
7)划线的毛坯,应注明产品的图号、件号和钢号,以免混淆。
8)注意合理安排用料,提高材料的利用率。
常用的划线工具有:
划线平台、划针、划规、角尺、样冲、曲尺、石笔、粉线等。
基本线型的划法:
直线的划法
直线长不超过1m可用直尺划线。
直线长不超过5m用弹粉法划线。
直线超过5m用拉钢丝的方法划线。
大圆弧的划法
大圆弧的准确划法和大圆弧的计算法
二、放样
根据构件的图样,按1:
1的比例或一定比例在放样台或平台上画出其所需要图形的过程称为放样。
对于不同行业,如机械、船舶、车辆、化工、冶金、飞机制造等,其放样工艺各具特色,但就其基本程序而言,却大体相同。
1.放样方法
放样方法是指将零件的形状最终划到平面钢板上的方法,主要有实尺放样、展开放样和光学放样等。
(1)实尺放样根据图样的形状和尺寸,用基本的作图方法,以产品的实际大小划到放样台的工作称为实尺放样。
(2)展开放样把各种立体的零件表面摊平的几何作图过程称为展开放样。
(3)光学放样用光学手段(比如摄影),将缩小的图样投影在钢板上,然后依据投影线进行划线。
2.放样程序
放样程序一般包括结构处理、划基本线型和展开三个部分。
结构处理又称结构放样,它是根据图样进行工艺处理的过程。
一般包括确定各连接部位的接头形式、图样计算或量取坯料实际尺寸、制作样板与样杆等。
划基本线型是在结构处理的基础上,确定放样基准和划出工件的结构轮廓。
展开是对不能直接划线的立体零件进行展开处理,将零件摊开在平面上。
三、下料
下料:
就是用各种方法将毛坯或工件从原材料上分离下来的工序。
下料分为手工下料和机械下料。
手工下料的方法主要有克切、锯切、气割等。
机械下料的方法有剪切、冲裁等。
1.手工下料
(1)克切克切所需克子(有柄)。
克切原理与斜口剪床的剪切原理基本相同。
它最大特点是不受工作位置和零件形状的限制,并且操作简单,灵活。
(2)锯割它所用的工具是锯弓和台虎钳。
锯割可以分为手工锯割和机械锯割,手工锯割常用来切断规格较小的型钢或锯成切口。
经手工锯割的零件用锉刀简单修整后可以获得表面整齐、精度较高的切断面。
(3)砂轮切割砂轮切割是利用高速旋转的薄片砂轮与钢材摩擦产生的热量,将切割处的钢材变成“钢花”喷出形成割缝的工艺。
砂轮切割可以切割尺寸较小的型钢、不锈钢、轴承钢型材。
切割的速度比锯割快,但切口经加热后性能稍有变化。
型钢经剪切后的切口处断面可能发生变形,用锯割速度又较慢,所以常用砂轮切割断面尺寸较小的圆钢、钢管、角钢等。
但砂轮切割一般是手工操作,灰尘很大,劳动条件很差。
(4)气割利用气体火焰将金属材料加热到能在氧气中燃烧的温度后,通过切割氧气使金属剧烈氧化成氧化物,并从切口中吹掉,从而达到分离金属材料的方法,叫做氧气切割,简称气割。
它所需要的主要设备及工具:
乙炔钢瓶和氧气瓶、减压器、橡皮管、割炬等。
2.机械下料
(1)剪切剪切就是用上、下剪切刀刃相对运动切断材料的加工方法。
它是冷作产品制作过程中下料的主要方法之一。
剪切一般在斜口剪床、龙门剪床、圆盘剪床等专用机床上进行。
1)斜口剪床。
斜口剪床的剪切部分是上下两剪刀刃,刀刃长度一般为300mm~600mm,下刀片固定在剪床的工作台部分,靠上刀片的上、下运动完成材料的剪切过程。
2)平口剪床。
平口剪床有上下两个刀刃,下刀刃固定在剪床的工作台的前沿,上刀刃固定在剪床的滑块上。
由上刀刃的运动而将板料分离。
因上下刀刃互相平行,故称为平口剪床。
上、下刀刃与被剪切的板料整个宽度方向同时接触,板料的整个宽度同时被剪断,因此所需的剪切力较大。
3)龙门剪床。
龙门剪床主要用于剪切直线,它的刀刃比其它剪切机的刀刃长,能剪切较宽的板料,因此龙门剪床是加工中应用最广的一种剪切设备。
如Q11-13×2500。
4)圆盘剪床圆盘剪床上的上下剪刀皆为圆盘状。
剪切时上下圆盘刀以相同的速度旋转,被剪切的板料靠本身与刀刃之间的磨擦力而进入刀刃中完成剪切工作。
圆盘剪床剪切是连续的,生产率较高,能剪切各种曲线轮廓,但所剪板料的弯曲现象严重,边缘有毛刺,一般适合于剪切较薄钢板的直线或曲线轮廓。
(2)热切割热切割包括数控气割、等离子弧切割、光电跟踪气割等。
(3)冲裁冲裁是利用模具使板料分离的冲压工艺方法。
根据零件在模具中的位置不同,冲裁分为落料和冲孔,当零件从模具的凹模中得到时称为落料,而在凹模外面得到零件时称为冲孔。
冲裁的基本原理和剪切相同,但由于凹模通常是封闭曲线,因此零件对刃口有一个张紧力,使零件和刃口的受力状态都与剪切不同。
四、坯料的边缘加工
钢板的边缘加工,主要是指焊接结构件的坡口加工,常用的方法有机械切割和气割两类。
采用机械加工方法可加工各种形式的坡口,如I、V、U、X及双U型等。
但也可用热切割方法切割坡口。
如用自动或半自动切割设备,同时使1~3把割炬,一次可切割出I、V和X型坡口。
关于气割前面已有论述,这时只介绍机械切割。
机械加工坡口常用的设备有:
刨边机、坡口加工机和铣床、车床等各种通用机床。
刨边机可加工各种形式的直线坡口,尺寸准确,不会出现加工硬化和热切割中出现的那种淬硬组织与熔渣等,适合低合金高强度钢、高合金钢以及复合钢板、不锈钢的加工,缺点是机器外廓尺寸大、价格较贵。
坡口加工机体积小,结构简单、操作方便,工效是铣床或刨床的20倍。
所加工的板材,除厚度外,在理论上不受直径、长度、宽度的限制。
缺点是受铣刀结构的限制,不能加工U型坡口及坡口的钝边。
第三节弯曲与成形
一、弯曲成型
将坯料弯成所需形状的加工方法为弯曲成型,简称弯型。
弯型时根据坯料温度可分为冷弯和热弯;根据弯形的方法分手工弯型和机械弯型。
钢材弯曲变形过程
弯型加工所用坯料通常为钢材等塑性材料,这些材料的变形过程如下:
(1)初始阶段。
(2)塑性变形阶段。
(3)断裂阶段。
弯曲过程中,材料的横截面形状也要发生变化,无论宽板、窄板,在变形区内材料的厚度均有变薄现象。
2.钢材的变形特点对弯曲加工的影响
钢材弯曲变形特点对弯曲加工的影响主要有以下几个方面:
(1)弯力。
无论采用何种弯曲成型方法,弯力都必须能使被弯曲材料的内应力超过材料的屈服点。
(2)回弹现象。
回弹现象的存在,直接影响弯曲件的几何精度,必须加以控制。
影响回弹的主要因素有:
1)材料的屈服点越高弹性模量越小,加工硬化越激烈,弯曲变形的回弹越大。
2)材料的相对弯曲半径r/δ越大,材料变形程度就越小,则回弹越大。
3)在弯曲半径一定时,弯曲角α越大,表示变形区长度越大,回弹也越大。
4)其他因素例如零件的形状、模具的构造、弯曲方式及弯曲力的大小等,对弯曲件的回弹也有一定的影响。
减小回弹的主要措施如下:
将凸模角度减去一个回弹角,使板料弯曲程度加大,板料回弹后恰好等于所需要的角度。
采取校正弯曲,在弯曲终了时进行校正,即减小凸模的接触面积或加大弯曲部件的压力。
减小凸模与凹模的间隙。
采用拉弯工艺。
在必要时,如果条件允许可采用加热弯曲。
(3)最小弯曲半径 材料在不发生破坏的情况下所能弯曲的最小曲率半径,称为最小弯曲半径。
材料的最小弯曲半径,是材料性能对弯曲加工的限制条件。
采用适当的工艺措施,可以在一定程度上改变材料的最小弯曲半径。
影响材料最小弯曲半径的因素有:
1)材料的塑性越好,其允许变形程度越大,则最小弯曲半径可以越小.
2)弯曲角α在相对于弯曲半径r/δ相同的条件下,弯曲角α越小,材料外层受拉伸的程度越小而不易弯裂,最小弯曲半径可以取较小值。
反之,弯曲角α越大,最小弯曲半径也应增大。
3)材料的方向性轧制的钢材形成各向异性的纤维组织,钢材平行于纤维方向的塑性指标大于垂直于纤维方向的塑性指标。
因此,当弯曲线与纤维方向垂直时,材料不易断裂,弯曲半径可以小些。
4)材料的表面质量和剪断面质量当材料剪断面质量和表面质量较差时,弯曲时易造成应力集中使材料过早破坏,这种情况下应采用较大的弯曲半径。
5)其他因素材料的厚度和宽度等因素也对最小弯曲半径有影响。
如薄板可以取较小的弯曲半径,窄板料也可取较小的弯曲半径。
在一般情况下,弯曲半径应大于最小弯曲半径。
若由于结构要求等原因,弯曲半径必须小于或等于最小弯曲半径时,则应该分两次或多次弯曲,也可采用热弯或预先退火的方法,以提高材料的塑性。
二、机械压弯成形
在压力机上使用弯曲模进行弯曲的成形的加工方法称为机械压弯。
弯曲成形时,材料的弯曲变形可以有自由弯曲、接触弯曲和校正弯曲三种形式。
三、板材、型材的展开长度的计算
1.板材展开长度计算
钢板弯曲时,中性层的位置随弯曲变形的程度而定,当弯曲的内半径r与板厚δ之比大于5时,中性层的位置在板厚中间,中性层与中心层重合(多数弯板属于这种情况);当弯曲的内半径r与板厚δ之比小于等于5时,中性层的位置向弯板的内侧移动,中性层半径可由经验公式求得:
R=r+Kδ(4-1)
式中R—中性层的曲率半径,
r—弯板内弧的曲率半径,
δ—钢板的厚度,
K—中性层系数,其值查表
表:
中性层位置系数K
≤0.1
0.2
0.25
0.3
0.4
0.5
0.8
1.0
1.5
2.0
3.0
4.0
5.0
≥5
K
0.3
0.33
0.35
0.36
0.38
0.40
0.42
0.44
0.47
0.475
0.48
0.5
四、卷板
通过旋转辊轴使坯料(钢板)弯曲成形的方法称为滚弯,又称卷板。
1.卷板机的特点和使用范围
(1)对称三轴辊下辊为主动的,两个下轴辊由电动机通过减速器产生同方向同转速旋转。
上辊是被动的,安装在可作上下移动的轴承内,工作时上辊往下压使板料弯曲。
当下辊转动时,由于摩擦力作用使板料移动产生均匀的弯曲。
三轴辊式卷板机结构简单、紧凑、重量轻、易制造、维修方便、投资少、两下轴辊距离小、成形较准确,因此应用较广。
但板材两端各有一段长度不能发生弯曲,这段长度称为剩余直边,其长度约为两下辊中心距离的一半,卷板前必须对板材的两端作预弯处理。
(2)不对称三轴辊它的轴辊排列是把一根下辊和上辊的水平中心距缩到板小位置,另一根下辊放置在侧边,所以卷出的板材仅起端有直边。
当卷制板材时,正反两次便可消除直边。
不必作预弯处理。
但板材需要调头卷弯,操作麻烦。
轴辊排列不对称,受力大,卷弯能力较小,一般作为辅助设备使用。
(3)四轴辊式它的下轴辊和两下侧轴辊都能作垂直方向移动。
该设备有对中方便,板材两端的预弯可在卷板机上完成,工艺通用性强。
但结构复杂,上下辊的夹持力使工件受氧化皮压伤严重;两侧辊相距较远,对称卷圆曲率不太准确;操作技术不易掌握,容易造成超负荷等,常用于重型工件以及要求自动化水平的技术水平较高的场合。
2.滚弯工艺
钢板滚弯由预弯(压头)、对中、滚弯三个步骤组成。
(1)预弯
卷弯时只有钢板与上辊轴接触的部分才能得到弯曲,所以钢板的两端各有一段长度不能发生弯曲,这段长度称为剩余直边。
1)在压力机上用通用模具进行多次弯成形。
2)在三辊卷板机上用模具预弯
3)在三辊卷板机上用垫块预弯。
(2)对中
对中的目的是使工件在素线与轴辊轴线平行,防止产生扭斜,保证滚弯后工件几何形状准确。
(3)滚弯
第四节冲压成形
一.压延
压延也称拉深或拉延,它是利用凸模把板料压入凹模,使板料变成中空形状零件的工序。
1.拉延基本原理
利用凸模与坯料接触后,下压时产生的压力强行把坯料压入凹模,迫使坯料分别转变为筒底,筒壁和凸缘,随着上模的下压、凸缘的径向逐渐缩小,筒壁部分逐渐增长,最后凸缘部分全部转变为筒壁。
2.拉延缺陷
(1)拉裂
拉延时,坯料被拉入凹模时,从底部到边缘过渡部分的应力很大,如果超过金属的抗拉强度,拉延件底部就会被拉穿。
防止措施:
1)凸模和凹模边缘均作成圆角,其半径r凸≤r凹=(5-15
)δ;
2)凸模与凹模之间的间隙合理,z=(1.1~1.2)δ;
3)拉延系数合理,m=d/D,一般取m=0.5~0.8.m越小拉延越困难,越容易拉裂,如果过小,不能一次拉制成高度和直径合乎成品要求时,则可进行多次拉延,且需进行中间退火处理,以消除前几次拉延变形的硬化现象,使以后拉延顺利进行。
(2)拉延件起皱
在拉延过程中,凸缘部分的材料受切向应力的作用。
当切向压应力达到一定值时,凸缘部分材料失去稳定而在整个周边方向出现连续的波浪变形,这种现象称为起皱。
防止起皱的有效方法是采用压边圈,压边圈安装在凹模上面,与凹模表面之间留有1.15~1.2倍板厚的间隙。
(3)拉延件壁厚变化
在拉延过程中,拉延件的壁厚会出现弯曲处减薄的现象,椭圆形封头在曲率半径最小处变薄最大,一般壁厚减薄率:
碳钢封头可达8%~10%;铝封头可达12%~15%.球形封头在底部变薄最严重,可达12%~14%.
为了弥补封头壁厚的变薄,可以适当加大封头坯料的板厚,以使封头变薄处的厚度接近容器的壁厚。
另外在中、厚壁封头的拉延过程中还会出现边缘增厚的现象,增厚率可达10%以上,对于这类封头必须加大模具间隙,以便封头顺利通过。
4.对拉延的基本要求是:
1)拉延件外形应简单、对称、且不要太高,以便使拉延次数尽量少。
2)拉延件的圆角半径在不增加工艺程序的情况下,有一个最小许可半径。
二、旋压
拉延也可以用旋压法来完成。
旋压是在专用的旋压机上进行的。
与拉延相比,旋压具有设备简单、机动性好,用简单模具可制造出规格多、数量少、形状复杂的零件,大大缩短了生产准备周期。
对制造大型十进位制优点更为明显。
现在的旋压设备,加工外径可达1000mm,最大深度可达450mm.
三、爆炸成形
1.爆炸成形的基本原理
爆炸成形是将爆炸物质放在一特制的装置中,点燃爆炸后,利用所产生的化学能在极短的时间内转集约化为周围介质中的高压冲击波,使坯料在很高的速度下变形和贴模,从而达到成形的目的。
2.爆炸成形的主要特点
1)炸成形不需要成对的刚性凸凹模同时对坯料施加外力,而是通过传压介质(水或空气)来代替刚性凸模的作用。
因此,可使模具结构简化。
2)炸成形可加工形状复杂,刚性模难以加工的空心零件。
3)回弹小、精度高、质量好。
由于高速成形零件回弹特别小,贴模性能好,只要模具尺寸准确,表面光洁,则零件的精度高,表面粗糙度好。
4)爆炸成形属于高速成形的一种。
加工成形速度快(只需1s),操作方便,成本低,产品制造周期短。
5)爆炸成形不需要冲压设备。
可成形零件的尺寸不受设备能力限制,在试制或小批生产大型制件时,经济效果显著。
3.爆炸成形应注意的事项
1)爆炸成形时,模具里的空气必须适当排除,因为空气的存在不但会阻止坯料的顺利贴模,而且会因模腔内空气的高度压缩而造成零件表面的烧伤,因而影响零件表面粗糙度。
因此,爆炸成形前,模腔内应保持一定的真度。
2)爆炸成开必须采用合理的密封装置,如果密封装置不好,会使模腔的真空度下降,影响零件的表面质量。
单件及小批生产时,可用粘土与油脂的混合物作为密封材料,批量较多时宜用密封圈结构。
爆炸成形在操作中有一定的危险性,因此,必须熟悉炸药的特性,并严格遵守安全操作规程。