第三章铝电解的主要操作共26页.docx
《第三章铝电解的主要操作共26页.docx》由会员分享,可在线阅读,更多相关《第三章铝电解的主要操作共26页.docx(29页珍藏版)》请在冰豆网上搜索。
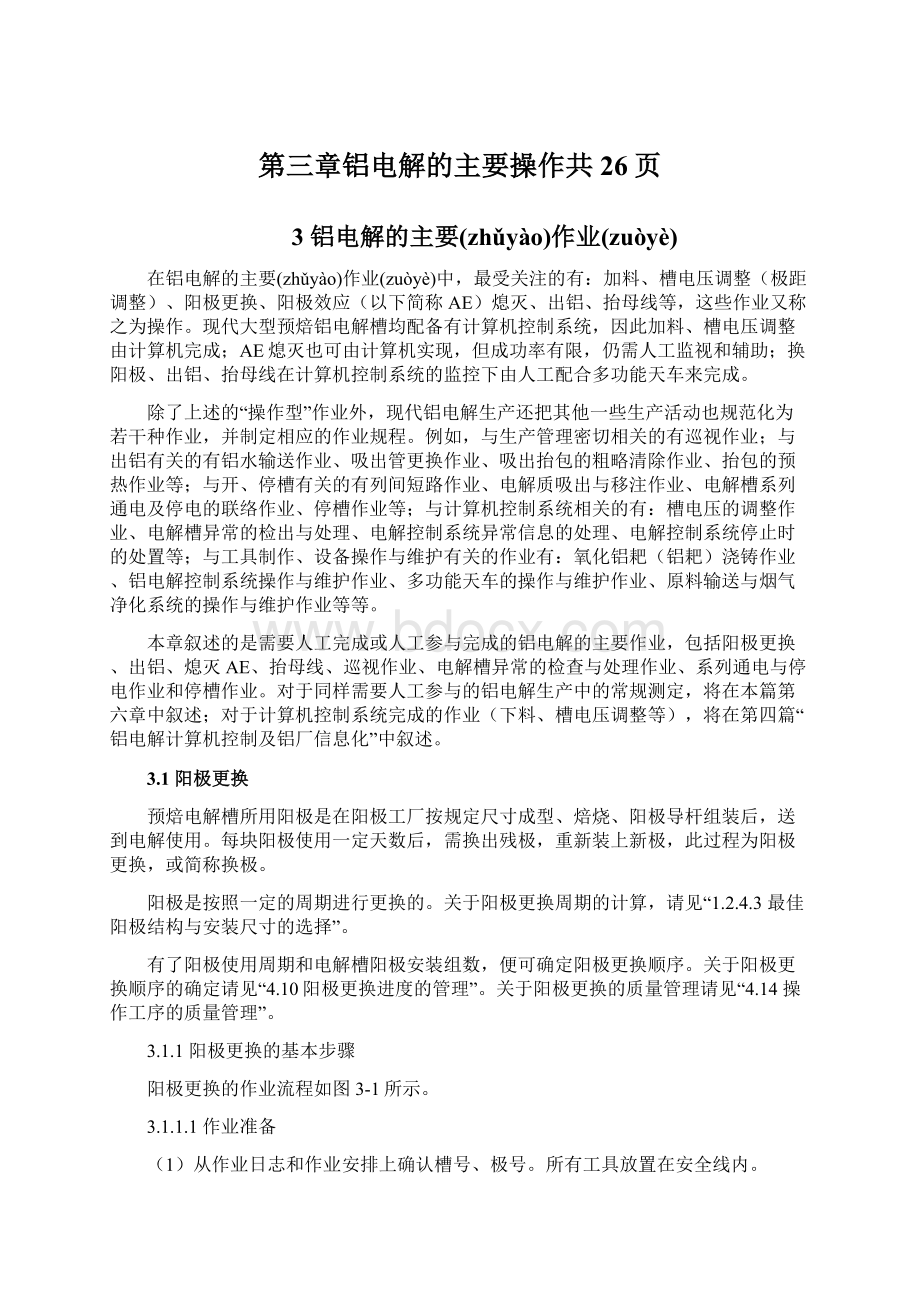
第三章铝电解的主要操作共26页
3铝电解的主要(zhǔyào)作业(zuòyè)
在铝电解的主要(zhǔyào)作业(zuòyè)中,最受关注的有:
加料、槽电压调整(极距调整)、阳极更换、阳极效应(以下简称AE)熄灭、出铝、抬母线等,这些作业又称之为操作。
现代大型预焙铝电解槽均配备有计算机控制系统,因此加料、槽电压调整由计算机完成;AE熄灭也可由计算机实现,但成功率有限,仍需人工监视和辅助;换阳极、出铝、抬母线在计算机控制系统的监控下由人工配合多功能天车来完成。
除了上述的“操作型”作业外,现代铝电解生产还把其他一些生产活动也规范化为若干种作业,并制定相应的作业规程。
例如,与生产管理密切相关的有巡视作业;与出铝有关的有铝水输送作业、吸出管更换作业、吸出抬包的粗略清除作业、抬包的预热作业等;与开、停槽有关的有列间短路作业、电解质吸出与移注作业、电解槽系列通电及停电的联络作业、停槽作业等;与计算机控制系统相关的有:
槽电压的调整作业、电解槽异常的检出与处理、电解控制系统异常信息的处理、电解控制系统停止时的处置等;与工具制作、设备操作与维护有关的作业有:
氧化铝耙(铝耙)浇铸作业、铝电解控制系统操作与维护作业、多功能天车的操作与维护作业、原料输送与烟气净化系统的操作与维护作业等等。
本章叙述的是需要人工完成或人工参与完成的铝电解的主要作业,包括阳极更换、出铝、熄灭AE、抬母线、巡视作业、电解槽异常的检查与处理作业、系列通电与停电作业和停槽作业。
对于同样需要人工参与的铝电解生产中的常规测定,将在本篇第六章中叙述;对于计算机控制系统完成的作业(下料、槽电压调整等),将在第四篇“铝电解计算机控制及铝厂信息化”中叙述。
3.1阳极更换
预焙电解槽所用阳极是在阳极工厂按规定尺寸成型、焙烧、阳极导杆组装后,送到电解使用。
每块阳极使用一定天数后,需换出残极,重新装上新极,此过程为阳极更换,或简称换极。
阳极是按照一定的周期进行更换的。
关于阳极更换周期的计算,请见“1.2.4.3最佳阳极结构与安装尺寸的选择”。
有了阳极使用周期和电解槽阳极安装组数,便可确定阳极更换顺序。
关于阳极更换顺序的确定请见“4.10阳极更换进度的管理”。
关于阳极更换的质量管理请见“4.14操作工序的质量管理”。
3.1.1阳极更换的基本步骤
阳极更换的作业流程如图3-1所示。
3.1.1.1作业准备
(1)从作业日志和作业安排上确认槽号、极号。
所有工具放置在安全线内。
(2)准备原料、设备与工具:
备好新阳极块(组)、电解质粉料;备好多功能天车等设备;备好作业记录、渣箱、阳极托盘、铁锹、换极全套工具,并把需预热的的工具器进行预热处理。
换极的全套工具一般包括:
两把大钩、一把铝耙、一把过滤耙、一把多齿耙、一根直角钎、粉笔、一把扫把、一把铁锤、阳极定位工具(卡尺、水平仪)、钢钎、风镐,铁耙等。
(3)向槽控机通报(tōngbào)换极:
在换极作业(zuòyè)开始前的5分钟,按该槽对应(duìyìng)的槽控机上的换极通报键,发出(fāchū)换极作业信息。
若通报后经过规定时间(如40分钟)未见通报阳极更换结束,槽控机一般会自动取消通报,因此从通报时刻到实际进行阳极交换时刻若超过了规定时间,要重新通报阳极更换。
(4)将电解槽排风量阀切换到高位(增大电解槽抽气量)。
3.1.1.2扒料
操作人员站在风格板上,打开换极处槽盖板;揭开的槽盖板应整齐叠放在相邻槽或左右的槽盖板上。
用铝耙将待更换的阳极上的覆盖料及其边部可扒出的覆盖料呈扇形扒开,把扒出的料扒在槽沿板内侧或铲到相邻阳极上。
图3-1阳极(yángjí)更换作业(zuòyè)流程图
3.1.1.3结壳开口(kāikǒu)
(1)人工(réngōng)开口:
对于待换阳极与相邻的高残极(更换较晚的阳极)之间的极缝,由于高残极妨碍用多功能天车进行开口,加之该缝隙的结壳形成不久,比较疏松,因此用人工开口。
开口位置以相邻高残极大面侧壳面线为基准往外5cm,窄缝长度为新阳极的宽度,窄缝要求连通且能观察到槽中液体电解质。
对于用短钢钎或铁耙处理不了的硬壳面用风镐进行处理,确保该窄缝连通且能观察到槽中液体电解质。
(2)多功能天车(PTM)开口:
指挥PTM扎开需换极的中缝、低残极侧壳面的结壳,形成一条连通且能观察到槽中液体电解质的窄缝(宽约8cm)。
用铝耙把天车开口过程中形成的结壳块扒出、以防掉入电解质内,注意不要让天车打击头碰到阳极,开完口后,指挥天车工收回打击头。
3.1.1.4卡住残极
指挥PTM旋转卡头,下降提升阳极装置的夹具夹住阳极铝导杆孔;下降PTM的小盒卡具扳手,卡住小盒卡具。
3.1.1.5残极在槽上的空间高度标定(阳极定位的第一步)
标定残极在槽上的空间高度的目的,是为了使新极能精确地安装定位在目标高度上。
因此首先在这里介绍阳极定位的常用方法。
所谓阳极定位,就是将阳极的安装高度从残极传递到新极,使新阳极安装后,其底掌在电解质中的位置能够根据残极底掌原来的位置来设定。
生产实践中,使新阳极底掌的位置略高于残极底掌原来的位置,这是考虑到新极导电的滞后性。
新极上槽后,冷阳极表面迅速形成一层冷凝电解质,1~2小时后开始熔化,阳极开始导电。
随着炭块温度升高,通过的电流逐渐增大,实践表明高度为540mm的新极,16小时左右导电达正常70%,24小时左右达正常值,角部阳极几乎拖长一倍的时间,考虑到新极导电的滞后性,新极安装不能与残极底面一样齐平,应比残极提高1天(非角部极)或2天(角部极)的消耗量,即15mm或30mm,保证达正常导电值时其底掌与其他阳极底掌位于同一平面。
在PTM没有阳极定位装置的情况下,可采用人工定位法。
以自制卡尺(兜尺)进行阳极定位为例,定位过程如图3-2所示:
①以阳极大母线下沿为基准,在残极导杆上划线;②在卡尺竖边上刻度与残极导杆划线对准处划线,然后抽出卡尺,在划线下2厘米处再重新划线,擦去原划线;③将卡尺上的高度(标记)移到新极上(即在新极导杆上的同样高度划线);④以此线位置与大母线下沿齐平。
(1)在槽上
(2)吊起残极(3)吊起新极(4)在槽上定位(dìngwèi)
图3-2卡尺定位(dìngwèi)过程
一些PTM配备有阳极定位(dìngwèi)装置。
以一种(yīzhǒnɡ)机械定位装置(阳极水平定位仪)为例,它由传动皮带(钢丝)、刻度盘、皮带卷放筒组成。
皮带一头固定在PTM的阳极卡头上,经刻度盘的中盘连到卷放筒上。
卡头伸缩时,皮带带动中盘转动,表示出不同的空间位置。
具体的定位过程是,残极拨出前,先标定水平仪;把残极吊运到水平仪定位托架上;使用水平仪设定残极位置;把新极吊运到水平仪定位托架上,使用水平仪设定新极位置;把新阳极吊到换极的电解槽上后,使用水平仪安装新极就位。
使用该方法时,为保证安装精度,要做到阳极在卡头徐徐上升的过程中定位,这样可使卡头总是勾住导杆孔上缘,防止在阳极下降受阻时,勾子在导杆内产生相对移动所造成的定位误差。
3.1.1.6拔出残极
用PTM的小盒卡具扳手松开小盒卡具;在电解工的指挥配合下,缓慢拔出残极;在拔出过程中,若发现有结壳块有可能掉入槽内时,应指挥天车工暂停拔出,待电解工将结壳块勾出后,再继续拔出。
残极拔出后,必须静置一下,待残极底掌上的电解液不再下滴,并确认天车及残极移动方向上无人后方可移动PTM。
指挥PTM将拔出残极吊至电解车间操作大面(不要碰击槽上部槽壳板与立柱母线);操作者对PTM吊起拔出的残极进行目视检查。
3.1.1.7残极检查
残极在运出之前,要检查是否异常。
残极检查记录的内容如下:
残极是否裂纹,残极是否掉块、掉角,钢爪是否熔化,残极是否穿底,残极是否长包。
3.1.1.8残极在槽上的空间高度测量(阳极定位的第二步)
见上述“3.1.1.5”。
3.1.1.9捞渣块及检查槽内
电解工用大勾、多齿耙等工具,捞净电解槽内结壳块,将邻极上及中缝处粘有的结壳清理干净。
每天换极打开(dǎkāi)一次炉面,是检查槽内情况的好机会,应借此机会检查铝水、电解质高度(用用直角(zhíjiǎo)钎进行(jìnxíng)一点测量)、炉底沉淀、邻极工作状态和槽内碳渣量等。
若电解质水平(shuǐpíng)低,应趁此机会补充冰晶石,碳渣多的应趁此捞出,可利用PTM自带机械抓斗捞渣块,或者人工用碳渣瓢将碳渣捞出,将渣块倒入渣箱。
并用大勾检查左、右邻极底掌有无裂纹、化爪、长包、掉角等情况,发现邻极有问题的马上处理。
同时还要检查伸腿状态、炉底是否有沉淀、结壳块阴极底掌破损等异常情况,并做好记录,发现炉底沉淀多的可适当调整加料间隔和槽电压。
3.1.1.10新极在槽上的空间高度设置(阳极定位的第三步)
见上述“3.1.1.5”。
3.1.1.11新极安装及新极定位(阳极定位的第四步)
首先,将阳极导杆与横梁母线的压接面上的粉尘清理干净。
把新阳极吊到换极的电解槽上;把铝导杆靠到阳极大母线上,轻轻接触;下降小盒卡具旋转扳手,使其达到卡具基底;缓慢下降阳极;使用阳极定位方法使新极就位(见上述“3.1.1.5”);拧紧小盒卡具;确认卡紧后方可松开PTM的阳极提升装置,然后将阳极提升装置提升到上限位。
3.1.1.12收边整形和添加保温料
人工将扒到槽边部的结壳碎块(粒度在50mm以下)覆盖边部端头,同时将料铲到新极上,并做好整形,使其保持自然斜度。
新极装好后覆盖一定厚度(140~180mm)的氧化铝,一是防止阳极氧化,二是加强电解槽上部保温,三是迅速提高钢-碳接触处温度,减少接触电压降。
保温料覆盖情况见图3-3。
图3-3极上氧化铝覆盖示意图
3.1.1.13清理收尾
把槽沿板清扫干净,盖好盖板;操作排风量转换阀复位;把工具按规定放回工具架上;把地面卫生清扫干净;在新铝导杆上,用粉笔划线(划线是为了观察阳极是否下滑,划线前把其它的线抹掉,再在导杆与阳极大母线下部平齐划一条线);向槽控机通报换极完毕(即消除阳极更换通报),使退出阳极更换的监控状态;观察槽电压,使其保持在设定电压。
3.1.1.14换极16小时(xiǎoshí)后的阳极电流分布测量
为了(wèile)确保新极安装精度,新极上槽后16小时,需进行导电量检查,即测等距离新极导杆上的电压降(现场叫16小时电流测量)。
若新极16小时后等距离导杆上的电压降是正常的50~80%,角部为30~50%,视为安装合格,否则需进行调整。
3.1.1.15异常(yìcháng)处理
(1)阳极(yángjí)脱落:
在检查巡视或换极过程中发现有阳极脱落时,必须及时更换出来。
作业过程与正常换极作业不同之处是由于阳极已脱落,残极碳块不能拔出,对小的脱落块用钎子、大钩等工具拉出即可,而大的脱落块,必须借助专用夹钳夹出来,把铝导杆放在异常极用的托盘上。
槽内的碳渣、阳极碎块必须捞干净。
检查更换阳极周期表,确定装高残极或新阳极,使用时间在10天之内或24天以上的脱落极使用新阳极,使用了10天以上或24天之内的脱落极使用高残极替换。
脱落极无法用正常换极使用的阳极定位方法来定位,因此在装极时,只能用大钩摸邻极和所装阳极的底掌大致确定安装位置。
(2)阳极长包:
阳极长包的时候,操炉工要让天车工知道;长包清理后再进行阳极设置。
(3)阳极滑落:
新阳极上槽后出现滑落,要将它提回到铝导杆上划线的位置。
(4)16小时电流分布异常:
在16小时内测出的阳极电流分布大于限定值时要进行调整。
调整的幅度应在2~4cm内。
3.1.2阳极更换作业的质量控制环节
换极过程中,与计算机(或槽控机)联系,捞电解质块,新极安装精度(阳极定位)是重点工序,应作为全过程的质量控制环节。
换极中,残极提出时刻起槽电压会有少许上升;若不与计算机联系(不通报槽控机),槽控机便按常规处理,即作电压调整,使阳极大母线在残极提出后位置下降,必然影响新极安装精度;槽控机不能按要求在阳极更换期间及更换结束后的一定时间内停止下料,消化换极过程带入槽内的氧化铝,会严重影响氧化铝浓度控制的正确性;并且槽控机不会在换极结束后一定时间内提高设定电压(即在正常设定电压的基础上附加一个换极后附加电压),这对电解槽的热平衡控制不利。
换极前通报槽控机,槽控机便转入阳极更换的监控程序,不作电压调整,监视该槽的电压变化,待新极安装完毕后,再与计算机联系,通报换极完毕(即消除阳极更换通报),使槽控机退出阳极更换的监控状态。
若不通报换极完毕,则槽控机在经历一定时间后自动退出阳极更换的监控状态。
一些控制程序能根据残极取出时的槽电压升高和新极插入后的槽电压回复来判断阳极更换完毕,但对于电压不稳定的电解槽不容易准确判断,因此一般需要人工通报换极完毕,以便槽控机及时退出阳极更换监控状态。
提残极时会掉入部分大结壳块于槽内,此结壳块会影响新极安装精度(大结壳块顶住阳极而不能安装到位),之后在新极下形成炉底沉淀,影响电解槽正常运行,因此,残极提出后必须把掉入槽内的结壳块干净地捞上岸来。
新极安装精度关系到阳极电流均匀分布。
因此应细心进行阳极定位操作,确保安装精度。
3.1.3安全(ānquán)注意事项
(1)工器具(qìjù)必须经预热后才能上槽使用,工器具在使用中要防止因磁场作用使工器具把握不牢,造成槽与槽、槽与母线之间的短路或伤人;特别是发热的工器具,尤其要小心。
工器具在进出电解槽大面时,应保持直立,以削弱磁场的影响;暂不使用或已使用完毕的工器具应及时摆放在工具小车上,不许随意丢放;
(2)用卡尺(kǎchǐ)划线时,要事先检查阳极卡具是否(shìfǒu)会掉落,确认安全后方可作业,但严禁迎面站在卡具的下方,严禁将脚伸入阳极底掌下面,以免烫伤、砸伤;
(3)任何情况下,禁止任何人员脚踩在壳面上作业;
(4)换极过程中,天车的移动方向上,严禁站人。
3.2出铝
电解产出的铝液积存于炉膛底部,需定期抽取出来,送往铸造车间生产成产品。
国内中、小型电解槽一般2~3天出一次铝,大型预焙槽实行一日一次制。
每槽吸出的量原则上应等于在周期内(两次出铝间的时间)所产出铝量,具体由区长(大组长)下达(按每天一点测量决定),或由计算机给出指示量(三点测量平均值加修正计算后给出)。
吸出工根据指示量,使用5t容积的喷射式真空抬包(见图3-4),在多功能天车配合下,每包可一次吸出2~4台槽的铝液(视槽容量而定),之后用专用运输车送往铸造车间。
3.2.1出铝的基本步骤
出铝的作业流程如图3-5所示。
图3-4喷射式台包示意图
1.包体;2.出渣口;3.清仓口;4.高压风入口;5.喷嘴
6.气体缓冲箱;7.废弃出口;8.铝液虹吸口;9.吸出管
图3-5出铝作业(zuòyè)流程图
3.2.1.1作业(zuòyè)准备
(1)确认(quèrèn)槽号及出铝计划(jìhuà)
从作业日志和作业安排上确认槽号。
查看工作记录,确认设备有无异常,计划有无变更;在有异常和变更的时候,进行作业时间的变更,计划的修改,并且同有关的单位进行联系;发生了非正常作业(如通电、启动、停槽、紧急情况下停槽等)的时候,进行有关单位和作业计划的洽谈;一切正常时,联系普通绝缘天车的使用并进入下一步。
(2)准备设备与工具
准备普通绝缘天车、出铝抬包、压空软管、炭渣瓢、套筒扳手、手动扳手、铝锤、观察孔用玻璃、石棉绳、抬包车、吸出指示量。
对设备进行检查:
在开始工作前和工作结束后都要检查抬包车;进行普通绝缘天车的一般检查(外观检查);对普通绝缘天车计量秤进行外观的检查。
(3)密封出铝抬包
取1.6米左右的石棉绳两段和0.5米左右的石棉绳一段,并拧紧成束;清干净抬包盖的凹槽及后包盖的杂物;石棉绳装入凹槽并轻压使基本充满凹槽,后包盖用石棉绳以包盖中为形缠实;盖下包盖,用力反复几下,使石棉绳被挤压出凹槽,锁紧包盖;盖后盖,用力反复几下,锁紧后包盖;清干净观察孔的插槽;在插槽插入观察孔用玻璃,用细的石棉绒塞紧缝隙;用扳手进行抬包和吸出管的再拧紧工作;装抬包喷嘴;把喷射器用空气软管1端与喷嘴通过快速接头相接好。
(4)吊运抬包
操作普通(pǔtōng)绝缘天车将抬包从抬包座吊起;在抬包平稳后记录空抬包的重量;操作普通绝缘天车,把抬包吊移至将吸出炉的炉前。
抬包在大面行走,吸管方向与行走方向同向。
(5)检查(jiǎnchá)抬包密封性
把喷射器用压空软管与天车吊钩主风管套接上;打开开风按钮;用手套堵住吸管口,通过手感吸力的大小判断密封性能是否(shìfǒu)良好。
(6)打开(dǎkāi)出铝孔
操作排风量转换阀门(增大电解槽抽风量);打开出铝端炉门;充分预热工具,注意电解质的飞溅;操作出铝打壳气缸控制阀,打开出铝孔;用碳渣瓢捞干净掉进电解质的结壳块、碳渣和炉底沉淀物,露出电解质液面;检查伸腿及炉底隆起情况;打开的出铝洞口要大于吸出管管径。
(7)向槽控机通报出铝
在出铝作业开始前的5分钟,按该槽对应的槽控机上的出铝通报键,给计算机发出出铝作业信息。
若通报后经过规定时间(如20分钟)未见通报出铝结束,槽控机一般会自动取消通报,因此从通报时刻到实际进行出铝时刻若超过了规定时间,要重新通报出铝,使槽控机启用出铝控制程序。
记录下槽电压和回转计读数。
3.2.1.2出铝过程
(1)插入出铝管
操作天车,让吸出管对准出铝洞口,慢慢把吸出管插入槽内,使吸出管刚好触及炉底;轻摇抬包的手轮调整吸出管口离炉底约5cm左右,防止抽上沉淀或电解质(注意吸出管不能接触阳极和炉底);要求天车工操作天车时,做到抬包不碰操作地平面及电解槽的上部结构。
(2)出铝操作
看好并记住天车计量称(如多功能天车的电子称)的读数显示和该槽的吸出量,确定吸出完后的天车称读数;打开压缩空气阀,开始吸出铝水;通过抬包观察孔观察吸出情况;密切观察天车称显示值的变化情况,快到吸出值时,关闭压缩空气阀。
(3)拔出出铝管
操作天车,使抬包慢慢上升,出铝管移出出铝洞;记录槽控机显示的出铝后的电压值及槽控机调整阳极后的回转计读数。
(4)出铝结束(jiéshù)
用铁铲平出铝洞口四周的结壳块,使洞口平整(píngzhěng),清扫槽沿板卫生;关好炉门(lúmén),操作排风量转换阀门复位;用扫把清扫大面卫生,保持现场(xiànchǎng)清洁。
3.2.1.3异常情况的处理
(1)出铝过程中发生AE
立即关闭出铝的压缩空气阀;停止出铝工作;必须将出铝管从槽内取出。
(2)铝水吸不进抬包时
检查压缩空气喷嘴是否堵塞,如果有堵塞,要清除干净;检查包盖的密封性,发现密封性不好的要进行调整或更换石棉绳重新封包;检查吸出管是否堵塞,如有堵塞要进行清除或更换;检查压缩空气是否达到要求,如没有到达要求,则联系相关单位处理;检查完上述几点还是没有吸出铝水时,要向相关人员报告再决定处理的方法。
(3)吸出大量电解质时
一旦吸上大量电解质,要将槽号报告相关人员。
(4)未能及时出铝时
因各种原因导致单槽出铝工作未能在额定时间(如20分钟)内完成时,要再次通报槽控机。
3.2.1.4抬包运送
按上述出铝过程吸出使抬包达到额定的容量,关闭压缩空气阀,御下吸出软管;操作天车,把出满1包铝水的抬包移至通道,抬包在大面行走,吸管方向与行走方向同向;把抬包放稳至抬包车的包座,抬包重心正中,吸管对正车尾中间;确认天车挂钩头离抬包吊环1米远后,才能上抬包车;开车运送到铸造车间。
3.2.1.5记录、报告
填写出铝记录表(表3.1为一实例);计算实际出铝量;下班前将单槽出铝记录表送计算机室。
表3.1吸出记录表
()车间年月日班
槽号
单槽
指示量
铸造
卡片量
合计
吸出
误差
实出量
接班情况
抬包重
是否堵管
是否清除
是否压铝
交班情况
抬包重
是否堵管
是否清除
是否压铝
其它
残铝倒入槽号
是否借包用
出铝风压
本班实出量
备注:
卫生
接班者
交班者
3.2.2出铝作业(zuòyè)的质量控制点
出铝作业的重点(zhòngdiǎn)是准备好抬包,工作质量控制点是吸出精度和上电解质量。
抬包准备如何,影响到工作效率。
如果抬包准备充分(各处密封好,不漏风),吸出铝液速度快,否则,上铝慢,甚至不上铝。
一个工作班中,天车除了出铝外,还要换阳极、装料、清扫维护,白班还有抬母线任务及其他工作,所以,出铝占时不能太长(正常每台槽占时5~8分钟,加上粗清包每班不超过2小时)。
除此外,出铝口必须(bìxū)下管前打好,捞净碳渣和推开沉淀,防止吸出时堵管。
换一次吸出管至少花20分钟。
吸出精度(jīnɡdù)要求在+50~-10kg(实出量与指示量之差),上电解质量每台槽5kg。
保证精度的措施首先为天车液压秤(或电子秤)必须准确指示,要求经常检查校对;其次是吸出工准确把握液压秤的指示。
须特别注意的是,大包出铝一次吸出数台槽,吸出工有时在头几台时漫不经心,却在最后一台找平总量,表面计算精度符合,实际张冠李载,面目全非。
这样会给技术条件管理带来混乱,甚至恶化槽况,害处极大。
解决办法:
一是对工人加强工作质量意识教育,提高责任心和职业道德,当出现某槽误差较大时,应自觉进行补救(出少的再吸出差量,出多的应倒回去)。
二是靠严格监督和检查。
3.2.3一些注意事项
电解质超量吸出是吸管尚未下到铝水层内,便开风吸出。
多吸出电解质也严重破坏槽子技术条件,急速增加抬包重量,还会造成堵塞铸造保温炉前炉,保温炉内渣量增多。
吸出工下管前应掌握槽子铝水深度,管口必须下到铝水层内。
但太深会出现上沉淀堵吸出管。
出铝前向槽控机通报(tōngbào)出铝,计算机便转入出铝监控(jiānkònɡ)程序。
大多数铝厂在出铝期间不进行手动和自动(zìdòng)调整电压处理,而是在通报出铝后,由槽控机自动根据出铝通报后槽电压的显著变化判断出铝开始(kāishǐ)与结束,并由槽控机在自动判断出铝结束一定时间后自动下降阳极,恢复槽电压至正常范围,其后自动转入正常控制(详见第四篇中的“6.2出铝的辅助管理与监视”)。
因此,若出铝中途失败,出铝工应将电压手动降到正常。
出铝前向槽控机通报出铝很重要,否则槽控机会将出铝期间的电压变化视为AE来临或电压异常,因而可能会在出铝期间出现所不希望的自动阳移;而在出铝结束后槽电压很高时不自动下降阳极(而是进行电压异常的报警),或者即使人工将电压恢复到正常范围,也不会按照出铝后附加电压来控制电压,从而影响热平衡控制;甚至错误预报AE并启动AE预报加工(大下料),从而影响氧化铝浓度的正常控制,并可能电解质大量沉淀。
出铝后应趁热粗清抬包(电解质热态下易于清出),以保证规定的使用天数。
清出的电解质应及时加入槽内。
填好作业记录,算出每槽实出量和上电解质量(出铝后清包前抬包重量与出铝前抬包重量之差,再除以当班出铝槽数),将每槽实出铝量及时送计算机室(夜班不超过24点),以供制作日报表用。
出铝作业的有关安全注意事项与换极作业类似。
3.3熄灭阳极效应
AE是熔盐电解过程