8第八章 铸造缺陷判断与工艺优化.docx
《8第八章 铸造缺陷判断与工艺优化.docx》由会员分享,可在线阅读,更多相关《8第八章 铸造缺陷判断与工艺优化.docx(13页珍藏版)》请在冰豆网上搜索。
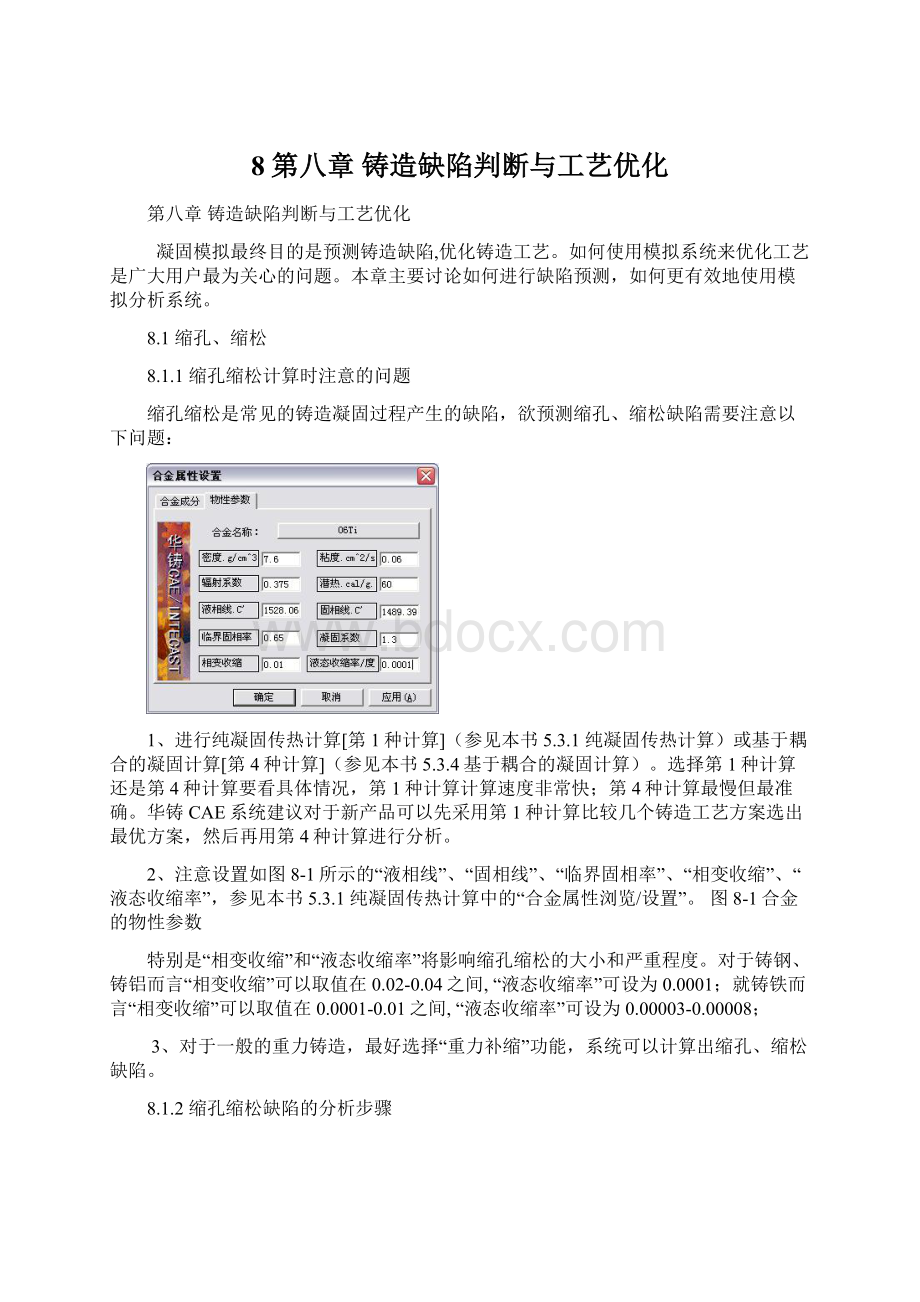
8第八章铸造缺陷判断与工艺优化
第八章铸造缺陷判断与工艺优化
凝固模拟最终目的是预测铸造缺陷,优化铸造工艺。
如何使用模拟系统来优化工艺是广大用户最为关心的问题。
本章主要讨论如何进行缺陷预测,如何更有效地使用模拟分析系统。
8.1缩孔、缩松
8.1.1缩孔缩松计算时注意的问题
缩孔缩松是常见的铸造凝固过程产生的缺陷,欲预测缩孔、缩松缺陷需要注意以下问题:
1、进行纯凝固传热计算[第1种计算](参见本书5.3.1纯凝固传热计算)或基于耦合的凝固计算[第4种计算](参见本书5.3.4基于耦合的凝固计算)。
选择第1种计算还是第4种计算要看具体情况,第1种计算计算速度非常快;第4种计算最慢但最准确。
华铸CAE系统建议对于新产品可以先采用第1种计算比较几个铸造工艺方案选出最优方案,然后再用第4种计算进行分析。
2、注意设置如图8-1所示的“液相线”、“固相线”、“临界固相率”、“相变收缩”、“液态收缩率”,参见本书5.3.1纯凝固传热计算中的“合金属性浏览/设置”。
图8-1合金的物性参数
特别是“相变收缩”和“液态收缩率”将影响缩孔缩松的大小和严重程度。
对于铸钢、铸铝而言“相变收缩”可以取值在0.02-0.04之间,“液态收缩率”可设为0.0001;就铸铁而言“相变收缩”可以取值在0.0001-0.01之间,“液态收缩率”可设为0.00003-0.00008;
3、对于一般的重力铸造,最好选择“重力补缩”功能,系统可以计算出缩孔、缩松缺陷。
8.1.2缩孔缩松缺陷的分析步骤
计算完毕后,系统会产生大量的数据。
注意涉及到缩孔、缩松的原始数据种类主要是*.TEM和*.DFC两类文件。
其中前者是温度文件,后者是重力补缩缺陷文件(如果了选择“重力补缩”功能的话)。
全面合理的缩孔缩松缺陷的分析步骤为:
液相分布—>缩孔形成—>Nyma缩松。
第一步:
液相分布
主要是观察铸件凝固期间液态分布情况,尤其是补缩通道的畅通情况,孤立液态区的状况等,以此来判断铸造的凝固收缩缺陷可能发生的部位。
操作步骤如下:
1)在后处理菜单的“数值画面”中选择“液相分布”;
2)在“液相分布”的对话框中选择凝固计算的第一个TEM文件,如凝固200000.TEM。
确定后系统会显示该凝固时刻的液相分布图。
3)
在后处理的工具栏上选择“Gr”按钮进入新型图形显示系统。
利用如图8-2所示的工具条中的各种显示功能显示铸件的凝固进程。
系统建议采用“—>”按钮(后一个文件)一步一步地显示。
找到某一部位刚刚产生液态孤立区的时刻。
在屏幕的左下角会有该时刻的具体时间显示。
此时选择菜单“判断”中的“判断连通性”。
系统会显示如图8-3的孤立液相区图,并为每一个液相孤立区编上一个号。
进一步选择菜单“判断”中的“查看孤立区信息”即可得到每个孤立区的体积(网格数),如图8-4所示。
图8-2新型图形显示系统的工具条
图8-3孤立液相区图图8-4孤立区的体积
孤立液相区会进一步冷却凝固,最后有可能产生缩孔缩松缺陷。
因此比较同一铸件的不同铸造工艺,如果从孤立液相分布来判断工艺的优劣,应遵循以下三条原则:
1)对于同一部位出现的孤立区而言,出现的时间晚比早好。
晚意味着补缩通道断开的迟,补缩效果较好。
2)对于同一部位出现的孤立区而言,孤立区体积小比大好。
3)对于同一部位出现的孤立区而言,孤立区分散比集中好。
注意:
凝固过程中液相孤立区的变化是动态的,一定要找到某一孤立区刚刚形成的关键时刻,依据上述三条原则比较工艺方案。
第二步:
缩孔形成
主要是利用重力补缩原理来预测缩孔/缩松的形成。
重力补缩原理如图8-5所示,一液态区域开始时全部为液体,随着温度降低,部分液体变为固体,同时体积会收缩。
因为在重力的作用下,该区域的上端会产生孔隙,从而形成缩孔、缩松。
图8-
5重力补缩原理图
对于一般的重力铸造,在规划计算时如选择了“重力补缩”功能,系统可以计算出缩孔、缩松缺陷。
显示缺陷的步骤是:
1)在后处理菜单的“数值画面”中选择“缩孔形成”,弹出如图8-6所示的对话框:
2)在对话框上端选择DFC文件,因为缺陷在记录时是累加的,因此可以选择最后一个DFC文件,当然也可以选择第一个,然后逐一向下显示。
注意,如果没有DFC文件,说明您在计算时没有选择“重力补缩”功能。
3)设置好显示临界(默认为4%,即0.04)以及孔松临界(默认为9%,即0.09)。
所谓显示临界就是当某一缺陷的孔隙率小于该临界值时不予显示,认为问题不严重,可以忽略不计。
因此显示临界可以看作是一个质量要求的尺度(或是探伤级别),此值越小,对质量的要求越高。
所谓孔松临界是指判断某一缺陷是孔还是松的一个标尺。
当一缺陷的孔隙率大于该临界值时就认为是缩
孔,否则为缩松。
显而易见,同一计算结果,此临界值越小,缩孔越多,反之缩松越多。
建议值为50%。
从某种意义上来讲,只有设为100%才反映出缩孔的
图8-6缩孔形成及分布对话框
情况,小于100%都夸大了缩孔缺陷。
对于铸铁请注意阅读后续的相关章节。
4)按确认后,系统就会显示如图8-7所示的铸造缺陷。
用户也可按“Gr”进入新型图形显示区,动态显示缺陷形成过程。
本图形画面用黑色表现缩孔,紫色表现缩松,黄色表现液相。
图8-7缩孔形成及分布
第三步:
Nyma缩松
根据著名的Niyama教授提出的判据来判断缩松,对于铸钢件来说非常有效。
操作步骤如下:
1)在后处理菜单的“数值画面”中选择“凝固排序”,弹出如图8-8所示的对话框。
选择所有的TEM文件,进行“序化”,得到NYM文件。
2)在后处理菜单的“数值画面”中选择“Nyma缩松”,弹出如图8-9所示的对话框。
图8-8凝固排序
输入合适的判据值,默认为400(最大值为1000)。
一般说来判据值越大,显示的缩松缺陷越多。
按确认即可显示缩松区域。
用户也可按“Gr”进入新型图形显示区,动态显示缺陷形成过程。
图8-9Nyma缩松
实践中,使用效果也存在差异,有效果非常显著的,也有效果不甚显著的。
建议用户在进行预测和决策时,将本功能与上述的“缩孔形成”功能互相参考,避免单一地迷信Niyama判据。
8.1.3对铸铁件缺陷预测的思考
铸铁件生产因其凝固方式的特殊性以及众多的影响因素而使模拟仿真变得比较困难。
合金成分、石墨化膨胀、铸型刚度、结晶形核等都影响着铸件的最终质量,因而欲准确模拟铸铁件的生产过程,除了宏观充型流动及凝固传热等模拟外,还应考虑结晶、组织、石墨化膨胀、铸型刚度等因素,进行微观的仿真模拟。
铸造微观模拟技术的发展已有近20年的历史,许多学者在不同领域进行了大量的研究探索,相当一部分研究集中在铸铁方面,包括结晶形核、组织演变和石墨化过程。
但遗憾的是到目前为止绝大部分研究仅停留于理论研究阶段,离实际应用还有很长的路要走。
实际上即便有了微观模拟手段,如果需要输入铸型刚度系数、石墨化膨胀系数,绝大部分用户还是无法确定。
那么,在目前条件下如何使用好铸铁件的模拟系统?
我们的建议是:
1)多方案的比较;
2)与实际生产经验相结合。
对于一个新产品一定不要模拟了一个方案就对该方案盖棺定论:
有问题还是没问题。
实际上科学的使用铸铁件模拟系统的方式是:
在多个方案中选出最优方案。
CAE技术很大好处是在实际生产之前对铸造过程进行虚拟仿真,具有极大的灵活性和经济性。
它允许使用者在很短的时间内对多个方案进行模拟、分析、比较,从中选出最优的工艺来。
由于技术发展水平的制约,目前对于铸铁件的模拟应特别注意通过多方案比较来优化工艺。
铸铁件的缩孔缩松缺陷分析步骤与本章“8.1.2缩孔缩松缺陷的分析步骤”基本一致。
但应注意以下问题:
1)更重视“液相分布”的液相孤立区的观察、对比。
注意比较多个工艺方案,对于同一部位出现的孤立区而言,孤立区体积小比大好、孤立区分散比集中好、出现的时间晚比早好。
2)注意铸件各孤立区最后的凝固部位,是铸件的热节,也往往是铸件容易出现缩孔、缩松的部位。
3)对于过共晶铸铁,同一铸件同一液态孤立区中心比边缘危险。
原因在于孤立区边缘先凝固,析出的初生石墨相会产生石墨化膨胀抵消收缩,同时也会使剩余的液相含碳量降低,从而使剩余液相凝固产生的收缩缺陷比前面已凝固的外围大。
4)对于过共晶铸铁,同一铸件不同液态孤立区之间的比较:
过早出现的孤立区较危险,因为在较早出现的孤立区部位,冷却速度较快,该部位的凝固有可能按介稳定系来进行,初生石墨不能充分析出,故较危险。
特别是如过凝固过快,出现麻口甚至白口,则该孤立区出现的收缩缺陷的可能性更大。
5)对于一个液相孤立区最终是否出现收缩缺陷,影响因素很多,包括合金、浇注温度、孕育、球化、铸型刚度等等。
如前所述,一孤立区最后凝固的部位是最危险的部位。
模拟出现孤立区了,实际上不一定会出现铸造缺陷(要看实际生产条件),但一旦出现铸造收缩缺陷基本可以肯定会出现在孤立区的最危险部位。
实际上就是不出现铸造缺陷,如果实际测试孤立区的最危险部位也会发现这些部位硬度偏低,枝晶粗大。
因此通过比较液相孤立区可以从多个方案中选出最优的铸造方案,也可以判定可能出现收缩缺陷的部位。
实际上不管影响因素多么复杂,对于同一铸件的不同工艺方案,同一部位的液态孤立区越大,对自补缩条件的要求越高,出现缺陷的可能性越大。
而较小的、分散的孤立区对自补缩条件要求的不是很高,出现缺陷的可能性越小。
6)可以比较不同方案的“缩孔形成”,但因缩孔形成采用的是重力补缩原理(参见图8-5),在铸铁,特别是球铁的缩孔的预测中会存在误差。
一般说来,利用重力补缩预测的缺陷,比实际发生的缺陷的位置偏高。
如图8-10所示,某一孤立液相区形状如图
(1),利用重力补缩预测的缺陷如
(2)所示,位置偏高。
而实际可能存在的缺陷会位于两个热节处,参见图(3)。
而通过观察“液相分布”可以知晓该孤立区的热节(最后凝固部位)所在位置。
因此,建议将“缩孔形成”与“液相分布”结合起来来判断。
但更主要是依据上述的液相分布方法来优化工艺。
7)“Nyma缩松”判断对铸铁的效果不如铸钢,故仅供用户参考。
(1)某液相孤立区
(2)重力补缩预测的缺陷(3)实际可能存在的缺陷
图8-10重力补缩可能产生的误差(铸铁)
8)就目前而言(华铸CAE9.0),反映碳当量、合金成分、铸型刚度等对铸造收缩缺陷的影响;但孕育、球化还没有充分考虑。
因此特别强调孤立液相区的判断、强调多方案的比较优化。
实际上对于孕育、球化、铸型刚度永远都不可能做到定量描述。
华铸CAE9.0版本能够反映合金元素(C、Si、Mn、S、P、Cr、Ni等)、初生石墨、初生奥氏体、共晶石墨、共晶奥氏体、冷却速度等对铸件收缩缺陷的影响。
并定性考虑铸型刚度的影响。
但依然要强调液态孤立区的判断、强调多方案的优化比较。
8.1.4工艺优化实例
实例一:
某厂生产的球墨铸铁曲轴,模拟了多个方案,通过比较“液相分布”,找到优化方案,根据模拟方案投入生产,取得良好效果。
方案1方案2
方案3方案4
图8-11多方案比较实例一
模拟发现方案4的液相孤立区出现的时间晚、体积小、比较分散,所以第4种方案最好。
实例二:
某厂生产的球墨铸铁件,模拟了横浇和立浇两个方案,通过比较“液相分布”,横浇液相孤立区出现的时间晚、体积小、比较分散,故认为横浇比立浇好。
(1)横浇方案
(2)立浇方案
图8-12多方案比较实例二
8.2卷气、夹杂
华铸CAE有三种计算方式均可以得到预测卷气、夹杂的数据,包括:
1)纯充型流动计算[第2种计算],参见本书5.3.2纯充型流动计算。
2)充型与传热耦合计算[第3种计算],参见本书5.3.3充型与传热耦合计算。
3)基于耦合的凝固计算[第4种计算],参见本书5.3.4基于耦合的凝固计算。
与卷气夹杂有很大关系的参数包括合金的粘度以及浇注速度。
就铁合金而言粘度取值范围可设为0.06-0.1;铸铝合金为0.01-0.05,参见本章图8-1合金的物性参数。
显示卷气、夹杂缺陷的操作如下:
1)在后处理菜单的“数值画面”中选择“压力分布”,弹出如图8-13所示的对话框。
2)在对话框上端选择FLD文件,在对话右下角选择“确定压力限”以及“负压”选项。
3)合成压力分布动画,观察动画。
图8-13压力分布对话框
4)如果某部位出现过多的负压带(红色报警区域),则说明此处充型紊流比较严重,不平稳,容易出现卷气、夹杂缺陷,应引起注意,参见图8-14。
图8-14卷气夹杂缺陷预测
另外通过后处理“数值画面”中的“体积填充”、“色温填充”以及“充型速度”也可以观察到卷气夹杂的危险部位。
8.3浇不足、冷隔
华铸CAE有两种计算方式可以得到预测浇不足、冷隔的数据,包括:
1)充型与传热耦合计算[第3种计算],参见本书5.3.3充型与传热耦合计算。
2)基于耦合的凝固计算[第4种计算],参见本书5.3.4基于耦合的凝固计算。
与浇不足、冷隔有很大关系的参数包括合金的粘度、浇注速度、浇注温度、合金及铸型的热容、导热系数等。
显示浇不足、冷隔缺陷的操作如下:
1)在后处理菜单的“数值画面”中选择“充型固相”,弹出如图8-15所示的对话框。
2)在对话框上端选择FLD文件,在对话右下角输入“临界固相”。
所谓“临界固相”就是停止流动的临界固相率,此值越大说明合金的流动性越好。
一般合金的“临界固相”取值范围在0.65—0.75之间,系统默认为0.7(70%)。
3)合成固相分布动画,观察动画。
4)如果某部位出现过多的固相带(红色报警区域),则说明此处充型过程中降温幅度过大,容易出现浇不足、冷隔缺陷,应引起注意,参见图8-16。
另外通过后处理“数值画面”中的“色温填充”也可以得到充型过程中降温状态,观察容易出现浇不足、冷隔缺陷的危险部位。
图8-15固相分布对话框
图8-16浇不足、冷隔缺陷预测