电力变压器冷却系统毕业设计.docx
《电力变压器冷却系统毕业设计.docx》由会员分享,可在线阅读,更多相关《电力变压器冷却系统毕业设计.docx(93页珍藏版)》请在冰豆网上搜索。
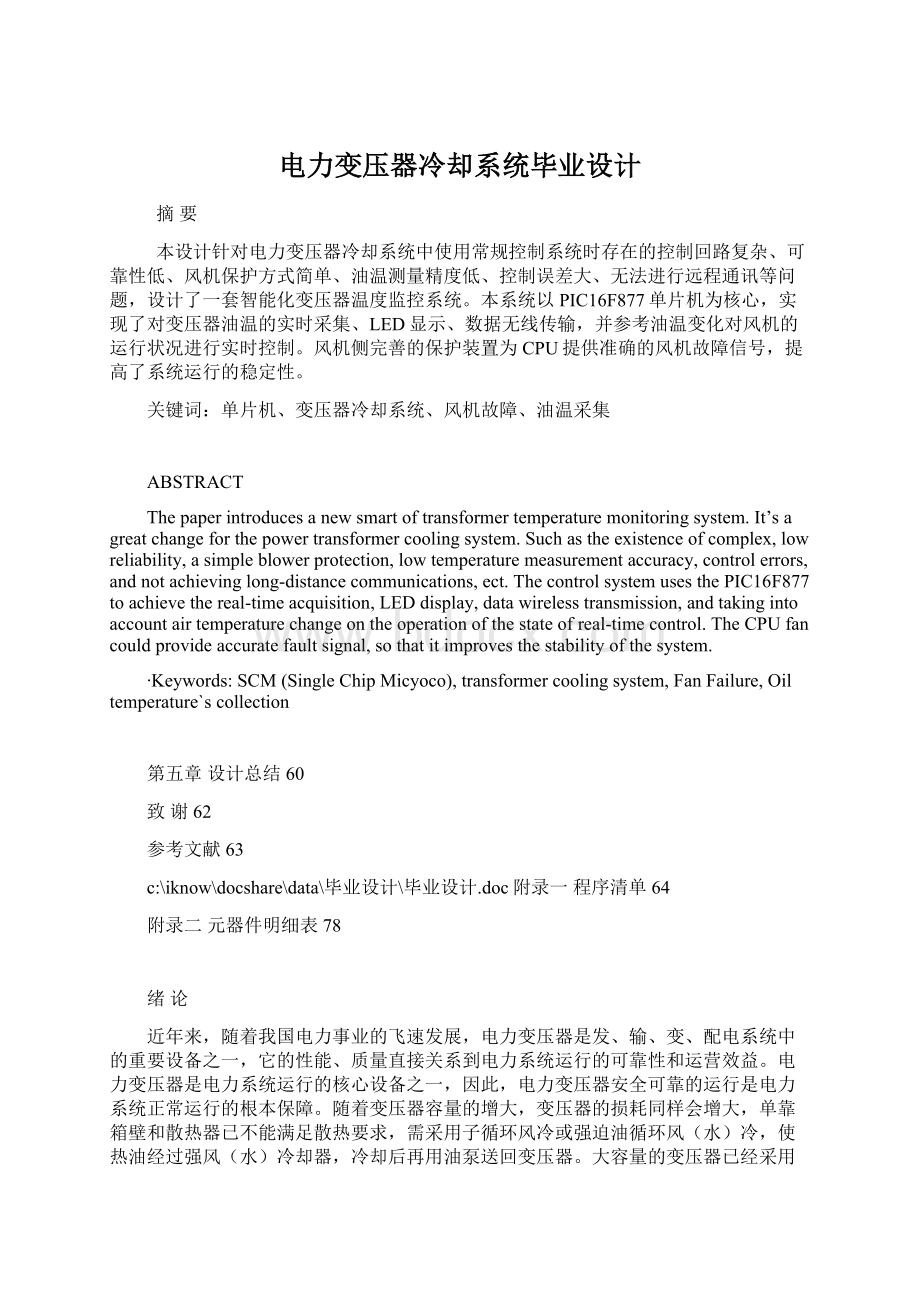
电力变压器冷却系统毕业设计
摘要
本设计针对电力变压器冷却系统中使用常规控制系统时存在的控制回路复杂、可靠性低、风机保护方式简单、油温测量精度低、控制误差大、无法进行远程通讯等问题,设计了一套智能化变压器温度监控系统。
本系统以PIC16F877单片机为核心,实现了对变压器油温的实时采集、LED显示、数据无线传输,并参考油温变化对风机的运行状况进行实时控制。
风机侧完善的保护装置为CPU提供准确的风机故障信号,提高了系统运行的稳定性。
关键词:
单片机、变压器冷却系统、风机故障、油温采集
ABSTRACT
Thepaperintroducesanewsmartoftransformertemperaturemonitoringsystem.It’sagreatchangeforthepowertransformercoolingsystem.Suchastheexistenceofcomplex,lowreliability,asimpleblowerprotection,lowtemperaturemeasurementaccuracy,controlerrors,andnotachievinglong-distancecommunications,ect.ThecontrolsystemusesthePIC16F877toachievethereal-timeacquisition,LEDdisplay,datawirelesstransmission,andtakingintoaccountairtemperaturechangeontheoperationofthestateofreal-timecontrol.TheCPUfancouldprovideaccuratefaultsignal,sothatitimprovesthestabilityofthesystem.
∙Keywords:
SCM(SingleChipMicyoco),transformercoolingsystem,FanFailure,Oiltemperature`scollection
第五章设计总结60
致谢62
参考文献63
c:
\iknow\docshare\data\毕业设计\毕业设计.doc附录一程序清单64
附录二元器件明细表78
绪论
近年来,随着我国电力事业的飞速发展,电力变压器是发、输、变、配电系统中的重要设备之一,它的性能、质量直接关系到电力系统运行的可靠性和运营效益。
电力变压器是电力系统运行的核心设备之一,因此,电力变压器安全可靠的运行是电力系统正常运行的根本保障。
随着变压器容量的增大,变压器的损耗同样会增大,单靠箱壁和散热器已不能满足散热要求,需采用子循环风冷或强迫油循环风(水)冷,使热油经过强风(水)冷却器,冷却后再用油泵送回变压器。
大容量的变压器已经采用导向冷却,在绕组和铁心内部,设有一定的油路,使进入油箱内的冷油全部通过绕组和铁芯内部流出,这样带走了大量的热量,可以提高散热效率。
变压器冷却系统决定了变压器的正常使用寿命及能否正常运行,因此变压器的冷却系统对变压器的安全经济运行又极其重要的意义。
在发电厂或变电所,风冷式变压器采用多组风机降温,控制变压器的油温在额定范围之内,保证变压器正常工作。
为了提高电力系统运行的可靠性和延长变压器的使用寿命,应该对变压器的油温进行实时监控。
目前,还有许多变压器采用由电接点式温度计采集、显示变压器油温,控制风机的启动和停止,实现变压器的温度控制,在实际运行中,由于风机启动时全部投入,同时全部停止,冲击电流较大,严重影响了电机的使用寿命。
且由于无法和控制室联系,所以无法实现变压器的无人控制,增加了运行成本。
变压器温控器总存在一些问题,如测温误差大、抗干扰能力差等,这些都是在工程界非常棘手的问题。
而早期的温度控制器,由于体积大、操作复杂、抗干扰能力差,给工程现场的使用也带来了很大不便。
随着单片机技术的不断发展,温度控制器正向单片集成化、智能化的方向迅速发展。
针对电力变压器在运行过程中存在的问题,可以采用的智能温度控制系统,实现温度的自动采集、显示、风机的顺序起停。
根据现场运行要求,本设计选用了PIC16F877单片机构成变压器温度控制系统,设备操作简单,用户可通过面板按键轻松设定控制风机起停、报警及跳闸阀值,所有设定参数掉电后均不会丢失。
温度采集精度很高,并且采取了很多措施来保护电机,如过载、缺相保护等。
由于工业现场的环境较恶劣,会对系统产生很大的干扰,设计采取了抗干扰措施,在集成电路的电源入口处加了滤波电容,且送入单片机的信号都经过了光耦隔离。
最后通过无线通信实现远程监控,控制室通过无线通信及时掌握现场的运行情况,可任意对各种事故做出及时地反映,实现了变压器的无人控制。
系统整体具有测温误差小、分辨力高、抗干扰能力强的特点,所有器件的选择均满足工业级标准,并适合高温环境。
由于采取了以上措施,可以保证控制系统稳定工作,设计具有很好的扩展性,能满足各种型号变压器的要求。
第一章设计任务及要求
第一节设计任务
在我们的生活中,电力安全是至关重要的,而电力变压器又是电力系统的重要组成部分。
电力系统中常用的油浸风冷式电力变压器多采用多组风机降温,控制变压器的油温在工艺要求的范围之内。
目前现场还有相当数量的油浸风冷电力变压器由电接点式温度计采集、显示变压器油温,控制风机的启动和停止,实现变压器的温度控制,即在变压器油温大于上限温度时启动全部风机,当油温降至下限温度时停止全部风机。
而实际运行中这种控制方式有不少的缺点,如风机启动时全部投入,冲击电流太大,不利于系统的稳定安全运行。
针对以上种种问题,要求本设计选用一款集成度较高的单片机,并采用无线通信技术,设计一个电力变压器温度监控系统,对现有落后的温度控制系统进行改造,满足自动化要求。
设计主要完成的工作。
本设计须完成风冷式电力变压器温度监控系统的主机部分的设计,主要包括以下工作:
(1)收集电力变压器温度控制系统的控制原理的实际资料,确定要保证变压器风冷系统正常运行及实现无人值班所需的远程通讯功能,必须采用以单片机为核心的控制系统来完成;为保证风机能可靠安全运行,必须收集一既能被单片机驱动又能保证风机可靠运行的元件。
(2)方案设计。
(3)确定系统配置及功能,并根据系统功能要求完成系统硬件设计。
(4)根据设计原则完成控制系统的软件设计。
(5)撰写设计说明书,绘制系统电路原理图。
(6)完成指定内容的外文资料翻译。
第二节设计要求
2.1毕业设计的主要内容
(1)完成系统设计;
(2)选择合适的单片机,作为主机CPU;
(3)独自完成主机硬件、软件设计,其中硬件部分主要包括温度采集、LED显示、主控电路、无线通讯、电源电路等,软件部分主要包括流程图设计、程序设计及调试;
(4)完成相关的设计图纸绘制和设计说明书撰写,通过毕业设计答辩。
2.2设计实现的主要功能
(1)将采集到的油温在就地和远端(控制室)用LED实时显示油温,主机和从机之间的通讯采用无线通信方式;
(2)系统设置自动、手动、停止三种运行方式,正常时采用自动方式运行,主控板检修时采用手动方式运行,并且能够灵活选择运行方式。
(3)在自动方式运行下,当变压器油温超过上限时,风机全部投入;当温度低于工艺下限时,风机全部停止;当温度由高下降到上限和下限的中间值时,只投入3组风机;在投入3组风机的状态,先运行的3组风机运行1小时后(这三组风机在变压器周围间隔安装),自动切换到另外3组(这三组风机也在变压器周围间隔安装),1小时后又切换到原来的3组,如此交替运行,既延长风机的使用寿命,又能使变压器均匀降温。
温度上限值和下限值可以通过硬件灵活设置,以适应不同类型和不同环境使用的变压器;变压器油温超过上限值时,风机群全部投入运行时,采用顺序启动方式依次启动,防止启动电流过大情况发生造成设备损坏;
(4)系统具有故障自诊断功能,当某一风机工作异常时如过压、缺相、过载时,系统能够在现场和控制室发出报警信号,显示故障类型和故障发生的位置,便于工作人员及时进行设备检修;
(5)系统设置正常运行、故障运行、油温超过75℃三项远传开关信号;
(6)本设计中油温的上限缺省值为55℃,下限缺省值为45℃,要求上限值和下限缺省值能够方便的通过按键调节;
(7)系统要采用必要的抗干扰措施(包括硬件和软件)。
2.3主要技术指标
控制系统的工作电源为220V/50HZ的工频交流电,容量为31500KVA;风机有6组,每组2个风机,均匀排列在变压器四周,每个风机功率为0.375KW;温度测量范围为0-100℃,温度采集精度为±2℃,温度控制精度为±5℃。
第二章系统的设计方案
第一节系统工作的一般原理
传统的电力变压器由人工控制风机,每台变压器有6组风冷式电动机需要控制,每组风机的保护通过热继电器实现,控制风机电源回路通过接触器,而风机启停的逻辑判断通过测量变压器的油温和变压器的过负荷实现,工作原理如图2-1所示。
主电路控制元件采用了接触器,靠机械触点来实现对风机的驱动。
这种方式对风机的控制只能由人工完成,风机同时全部投入,同时全部停止,启动时冲击电流很大,会对器件造成损伤。
当温度在45℃-55℃时,通常采用全部投入的方式,不利于节能,也不利于设备的维护。
控制器系统采用继电器、热继电器、接触器逻辑电路控制,控制逻辑显得很复杂,在运行过程中会出现接触器的触点长时间接触及多次开断造成触点烧毁问题。
风机缺乏必要的过压、过载、缺相保护,实际运行中降低系统运行的可靠性,增加运行成本。
图2-1传统风冷机工作原理图
第二节智能温度监控系统的设计方案
本设计以PIC16F877单片机为核心完成系统的设计,要求对油温进行实时采集,将采集结果送入MCU进行处理,然后按照工艺要求进行相应的控制,实现对变压器温度的全自动远程和就地监控,系统要具有完善的保护功能,包括过压、过载、缺相检测和保护,还要具备故障自诊断功能,在故障出现时,给出故障信息,显示故障类型,便于工作人员及时进行检修;使用无线通信方式实现变压器控制器与中心控制室之间的数据通信。
使用户随时了解变压器及风机运行情况,实现远程温度控制。
整个课题包括系统设计,主机温度信号采集与调理电路设计,主机LED显示电路设计,主控电路设计,缺相检测与保护电路设计,过载保护与检测电路设计,从机设计,从主机LED显示电路设计,无线通信电路设计,主电路设计,主机从机电源设计,系统软件流程图设计,软件编程等。
温度信号的采集在设计中是最重要的部分之一,其可以采用铂电阻电桥组成的温度检测电路,也可以使用温度传感器来实现。
2.1方案一:
温度检测电路通过预埋在变压器中的铂电阻传感器获得油温信号[3],经信号调理电路处理后直接送入控制器的A/D转换输入端,PIC单片机根据信号数据及设定的各种控制参数,按照程序自动计算与处理,自动显示变压器油温,并输出相应的控制信号,控制风机的起停,电机的保护电路包括过压,过载,缺相等。
显示电路采用MAX7219,其只需要三根线就可控制八个数码管,特别适用于需要I/O口较多的系统。
信号通过无线通信芯片nRF401传输到控制室,以便对现场情况及时做出反应。
方案采用PIC16F877单片机,PIC处理器具有不同于一般微处理器的许多特性,它给出最大系统可靠性,通过减少外部元件使成本最小。
另外,还提供节电工作模式及提供编码保护等。
PIC16F877共有A口、B口、C口、D口、E口五组I/O口,完全可以满足本系统的要求,另外在其中嵌入一个8输入通道的A/D模块,不需要专门的芯片进行A/D转换;CCP模块可提供外部信号的捕捉、内部比较输出、及脉宽调制PWM功能;中断源多,具有看门狗定时器和睡眠功能;还可以在线串行编程、在线调试。
显示电路采用MAX7219,其只需要三根线就可可控制八个数码管,特别适用于需要I/O口较多的系统。
MAX7219为8位LED显示驱动电路,可以连续的驱动8位7段数据显示。
在芯片内部集成了一个BCD译码器,段地址和位地址驱动以及一个8
8位的静态随机存储器。
只需要一个外部电阻,就可以正确地驱动所有LED的段地址。
信号通过无线通信芯片nRF401传输到控制室。
以便对现场情况及时做出反应。
nRF401是一个433MHz工业、科学、医用频段设计的真正单片无线收发芯片,它采用频移键控调制技术。
nRF401发射速率可达20kb/s,发射功率可调,最大发射功率10dBm,接收灵敏度-105dBm,具有工作半径大、适应性强的特点。
天线接口设计为差分天线,便于使用低成本的印刷电路板天线。
nRF401还有待机工作方式,可以更省电和高效。
此外,该芯片只需少量外围元件,使用十分方便。
温度控制器系统框图如图2-2所示。
图2-2温度控制系统框图
2.2方案二:
温度检测采用由DALLAS半导体公司生产的智能集成温度传感器DS18B20型单线智能温度传感器,属于新一代适配微处理器的智能温度传感器,采用DALLAS公司特有的单总线通信协议,只用一条数据线就可实现与MCU的通信。
它具有体积小,接口方便,传输距离远等特点。
显示采用单片机的RA口扩展四片串并转换的移位寄存器74LS164驱动四只1.5寸共阳数码管,实时显示变压器的温度。
复位电路采用MAXMAX6304芯片来实现单片机系统的监控电路。
MAX6304是一款专用、高性能、低功耗的微处理器监控芯片。
通信采用CHIPCON公司新推出的CC1000单片可编程RF收发芯片。
(一)温度检测电路的设计
温度检测采用由DALLAS半导体公司生产的智能集成温度传感器DS18B20型单线智能温度传感器,属于新一代适配微处理器的智能温度传感器,可广泛用于工业、民用、军事等领域的温度测量及控制仪器、测控系统和大型设备中。
它具有体积小、接口方便、传输距离远等特点。
DS18B20单总线数字传感器工作温度范围是-55℃~125℃,在-30℃~85℃范围内温度测量精度为±5℃;具有温度报警功能,用户可设置最高和最低
图2-3DS18B20引脚分布图
报警温度,且设置值掉电不丢失;采用DALLAS公司特有的单总线通信协议,只用一条数据线就可实现与MCU的通信;此外,DS18B20能够直接从数据线获得电源,无需外部电池供电[4]。
DS18B20与单片机的接口电路如图2-3所示。
I/O为数字信号输入/输出端,GND为电源地,VDD为外接供电电源输入端(在寄生电源接线方式时接地)。
DS18B20主要由四部分组成:
64位光刻ROM、温度传感器、非挥发的温度报警触发器TH和TL、配置寄存器。
光刻ROM中的64位序列号是出厂前被光刻好的。
相当于给每个DS18B20分配了一个独一无二的64比特地址序列码,这就允许多个DS18B20工作同条一线总线上,从而大大简化了分布式温度传感系统的应用。
温度传感器完成对温度的测量,温度报警触发器TH和TL以及配置寄存器的设置值均以一个字节的形式存储在EEPROM中,使用一个存储功能命令可对其写入。
(二)显示部分
可以用数码管显示,电路如下图2-4所示。
采用了MAX7219驱动器,对温度值进行实时输出显示,根据精度要求,设置一位小数。
图2-4LED显示电路
(三)键盘输入
单片机监电路设计的好坏,直接影响到整个系统工作的可靠性。
在设计完单片机系统,并在实验室调试成功后,在现场却出现了“死机”、“程序跑飞”等现象,而用仿真器调试时却无此现象发生或极少发生此现象。
有时会发现在关闭电源后的短时间内再次开启电源,单片机系统会工作不正常,这些都很可能是由单片机监控电路设计的不可靠引起的。
单片机监控电路主要有监控和看门狗两个功能。
(四)通讯电路设计
通信电路采用无线通信芯片来完成。
无线通信芯片种类繁多,方案选择CC1000来实现无线通信。
CC1000是根据Chipcon公司的SmartRF技术,在0.35μmCMOS工艺下制造的一种理想的超高频单片收发通信芯片。
它的工作频带在315、868及915MHz,但CC1000很容易通过编程使其工作在300~1000MHz范围内。
它具有低电压(2.3~3.6V),极低的功耗,可编程输出功率(-20~10dBm),高灵敏度(一般-109dBm),小尺寸(TSSOP-28封装),集成了位同步器等特点。
其FSK可达72.8Kbps,具有250Hz步长可编程频率能力,适用于跳频协议;主要工作参数能通过串行总线接口编程改变,使用非常灵活。
CC1000可通过简单的三线串行接口(PDATA、PCLK和PALE)进行编程,有36个8位配置寄存器,每个由7位地址寻址。
一个完整的CC1000配置,要求发送29个数据帧,每个16位(7个地址位,1个读/写位和8个数据位)。
PCLK频率决定了完全配置所需的时间。
在10MHz的PCLK频率工作下,完成整个配置所需时间少于60μs。
在低电位模式设置时,仅需发射一个帧,所需时间少于2μs。
所有寄存器都可读。
在每次写循环中,16位字节送入PDATA通道,每个数据帧中7个最重要的位(A6:
0)是地址位,A6是M键盘(最高位),首先被发送。
下一个发送的位是读/写位(高电平写,低电平读),在传输地址和读/写位期间,PALE(编程地址锁存使能)必须保持低电平,接着传输8个数据位(D7:
0),PDATA在PCLK下降沿有效。
当8位数据位中的最后一个字节位D0装入后,整个数据字才被装入内部配置寄存器中。
经过低电位状态下编程的配置信息才会有效,但是不能关闭电源[5]。
微控制器使用3个输出引脚用于接口(PDATA、PCLK、PALE),与PDATA相连的引脚必须是双向引脚,用于发送和接收数据。
提供数据计时的DCLK应与微控制器输入端相连,其余引脚用来监视LOCK信号(在引脚CHP_OUT)。
当PLL锁定时,该信号为逻辑高电平。
2.3方案三:
温度检测采用美国模拟器件公司(ADI)生产的恒流源式模拟温度传感器AD590。
它兼有集成恒流源和集成温度传感器的特点,具有测温误差小,动态阻抗低,传输距离远,体积小,微功耗等特点。
AD590配以ICL7016型单片A/D转换器即可构成三位半液晶显示的温度传感器,通信采用RS-485标准。
(一)温度采集电路
AD590是由美国哈里斯(Hrris)公司、模拟器件公司(ADI)等生产的恒流源式模拟温度传感器。
它兼有集成恒流源和集成温度传感器的特点,具有测温误差小、动态阻抗响应速度快、传输距离远、体积小、微功耗等优点,适合远距离测温、控温,不需要进行线性校准。
AD590属于采用激光修正的精密集成温度传感器。
该产品有3种封装形式;TO-52封陶瓷封装(测温范围是-55—+150℃)。
不同公司产品的分档情况及技术指标可能会有一些差异。
例如,由ADI公司生产的AD590,就有90J/K/L/M四档。
这类器件的外形与小功率晶体管相仿,共有3个管脚:
1脚为正极,2脚是负极,3脚是接管壳。
使用时将3脚接地,可起到屏蔽作用。
AD系列产品以AD590M的性能最佳,其测温范围是-55—+150℃,最大非线性误差为0.3℃,相应时间仅20μs,重复性误差低至0.05℃,功耗约为5mW。
AD590等效于一个高阻抗的恒流源,其输出阻抗大于10MΩ,能大大减小因电源电压从5V变化到10V时,所引起的电流最大变化量仅为1μA,等价于1℃的测温误差。
AD590的工作电压为+4—+30V、测温范围是+55—+150℃,对应于热力学温度T每变化1K,输出电流就变化1μA。
在298.15K(对应于25.15℃)时输出电流恰好等于298.15μA。
这表明,其输出电流与热力学温度严格成正比。
AD590配以ICL7106型单片A/D转换器,即可构成3位半液晶显示的数字温度计。
(二)通讯电路
RS-485采用平衡发送和差分接收方式来实现通信:
在发送端TXD将串行口的TTL电平信号转换成差分信号A、B两路输出,经传输后在接收端将差分信号还原成TTL电平信号。
两条传输线通常使用双绞线,又是差分传输,因此有极强的抗共模干扰的能力,接收灵敏度也相当高。
同时,最大传输速率和最大传输距离也大大提高。
如果以10Kbps速率传输数据时传输距离可达12m,而用100Kbps时传输距离可达1.2km。
如果降低波特率,传输距离还可进一步提高。
另外RS-485实现了多点互联,最多可达256台驱动器和256台接收器,非常便于多器件的连接。
不仅可以实现半双工通信,而且可以实现全双工通信。
半双工通信芯片有SN75176、SN75276、SN75LBC184、MAX485、MAX3082、MAX1482等。
全双工通信的有SN75179、SN75180、MAX488~491、MAX1482等[6]。
第三节设计方案的确定
根据上一节中三个设计方案,下面对这三种设计方案进行比较:
在方案二中,温度检测采用由DALLAS半导体公司生产的智能集成温度传感器DS18B20型单线智能温度传感器,它具有体积小,接口方便,传输距离远等特点。
但价格较高。
显示采用单片机的I/O口扩展四片串并转换的移位寄存器74LS164驱动四只1.5寸共阳级数码管,实时显示变压器的温度。
占用了较多的I/O口,使系统的可扩展性受到了一定的限制[7]。
复位电路采用MAX6304芯片来实现单片机系统的监控电路。
MAX6304是一款专用、高性能、低功耗的微处理器监控芯片。
通信采用CHIPCON公司新推出的CC1000单片可编程RF收发芯片。
本设计的成本较高,但可靠性更强,适用于对可靠性要求较高且不在乎成本的场合。
在方案三中,温度检测采用美国模拟器件公司(ADI)生产的恒流源式模拟温度传感器AD590。
它兼有集成恒流源和集成温度传感器的特点,具有测温误差小,动态阻抗低,传输距离远,体积小,微功耗等特点。
AD590配以ICL7016型单片A/D转换器即可构成三位半液晶显示的温度传感器。
显示采用MAX7219,占用了较少的I/O口,通信采用RS485标准。
此方案具有很高的可靠性,液晶具有很多优点,可以实现汉字的显示等,但设计中要求在较远的距离就可以观察到温度值,所以这里采用液晶不能满足要求。
故不选用此方案。
在方案一中,单片机选用了PIC16F877,具有高性能、高可靠性、端口多等优点。
温度检测电路使用内置的铂电阻来检测温度变化,硬件电路较为简单,光电隔离使用线形光耦,具有较好的性能,抗干扰能力较强,显示电路使用MAX7219只占用三个I/O口连线较少,容易实现。
通信芯片nRF401,其通信距离远,且不用编码,软件较容易实现。
另外本方案还具有很好的经济性和可扩展性,可满足各种不同变压器的要求。
综上所述,本方案具有较高的性价比。
根据上面对三个设计方案的说明比较可以看出,方案一具有较好的抗干扰性,可扩展,经济性较好,而且采用无线通讯,具有较高的性价比。
所以在本设计中采用了方案一。
具体的硬件框图如下所示。
图2-5温度控制系统结构框图
如上系统框图所示,本设计以PIC16F877单片机为核心完成系统的设计,要求对油温进行实时采集,将采集结果送入MCU进行处理,然后按照工艺要求进行相应的控制,实现对变压器温度的全自动远程和就地监控,系统要具有完善的保护功能,包括过压、过载、缺相检测和保护,还要具备故障自诊断功能,在故障出现时,给出故障信息,显示故障类型,便于工作人员及时进行检修;使用无线通信方式实现变压器控制器与中心控制室之间的数据通信。
使用户随时了解变压器及风机运行情况,实现远程温度控制。
温度检测