配合件的数控加工工艺的分析及程序编制毕业设计论文.docx
《配合件的数控加工工艺的分析及程序编制毕业设计论文.docx》由会员分享,可在线阅读,更多相关《配合件的数控加工工艺的分析及程序编制毕业设计论文.docx(41页珍藏版)》请在冰豆网上搜索。
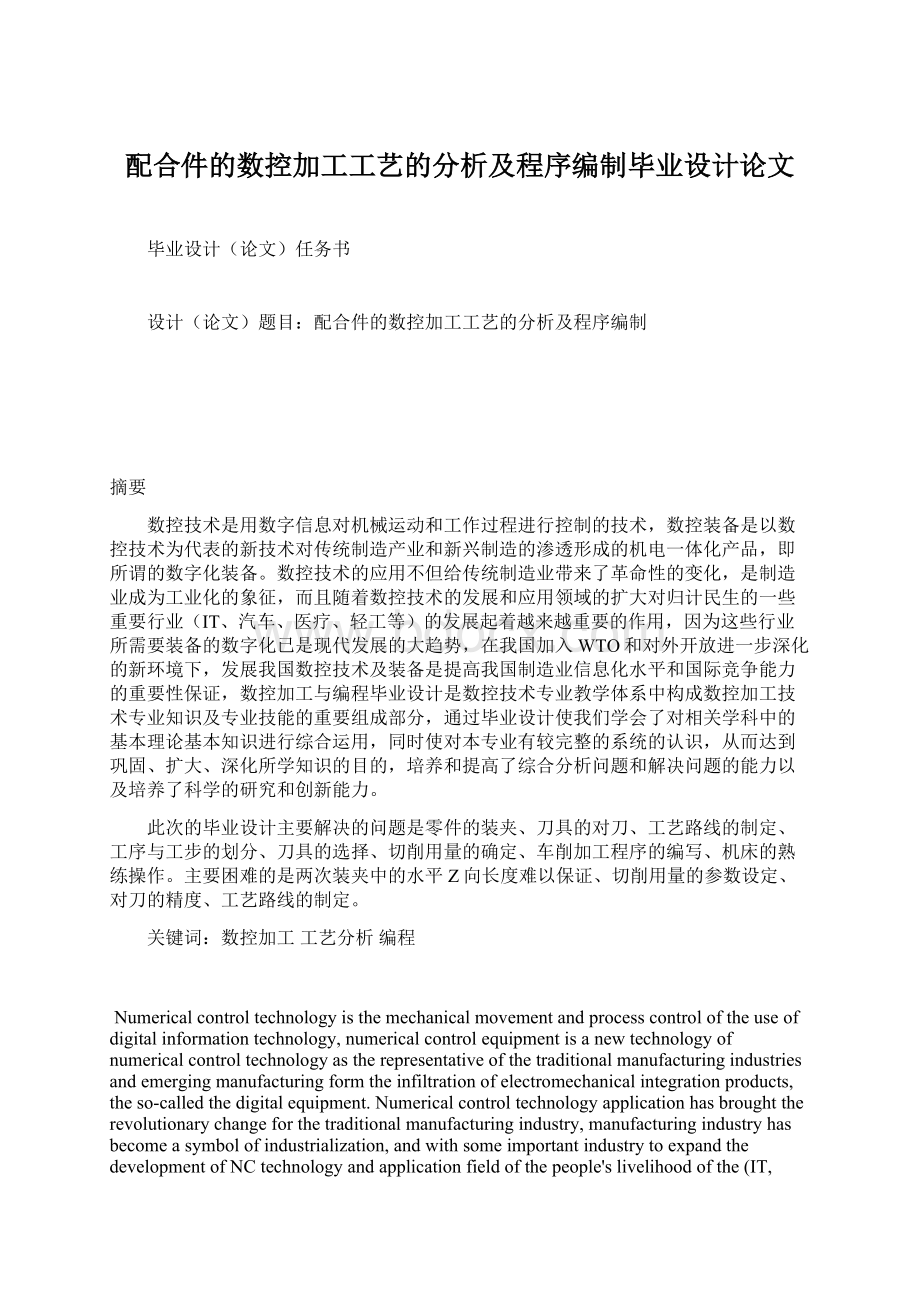
配合件的数控加工工艺的分析及程序编制毕业设计论文
毕业设计(论文)任务书
设计(论文)题目:
配合件的数控加工工艺的分析及程序编制
摘要
数控技术是用数字信息对机械运动和工作过程进行控制的技术,数控装备是以数控技术为代表的新技术对传统制造产业和新兴制造的渗透形成的机电一体化产品,即所谓的数字化装备。
数控技术的应用不但给传统制造业带来了革命性的变化,是制造业成为工业化的象征,而且随着数控技术的发展和应用领域的扩大对归计民生的一些重要行业(IT、汽车、医疗、轻工等)的发展起着越来越重要的作用,因为这些行业所需要装备的数字化已是现代发展的大趋势,在我国加入WTO和对外开放进一步深化的新环境下,发展我国数控技术及装备是提高我国制造业信息化水平和国际竞争能力的重要性保证,数控加工与编程毕业设计是数控技术专业教学体系中构成数控加工技术专业知识及专业技能的重要组成部分,通过毕业设计使我们学会了对相关学科中的基本理论基本知识进行综合运用,同时使对本专业有较完整的系统的认识,从而达到巩固、扩大、深化所学知识的目的,培养和提高了综合分析问题和解决问题的能力以及培养了科学的研究和创新能力。
此次的毕业设计主要解决的问题是零件的装夹、刀具的对刀、工艺路线的制定、工序与工步的划分、刀具的选择、切削用量的确定、车削加工程序的编写、机床的熟练操作。
主要困难的是两次装夹中的水平Z向长度难以保证、切削用量的参数设定、对刀的精度、工艺路线的制定。
关键词:
数控加工工艺分析编程
Numericalcontroltechnologyisthemechanicalmovementandprocesscontroloftheuseofdigitalinformationtechnology,numericalcontrolequipmentisanewtechnologyofnumericalcontroltechnologyastherepresentativeofthetraditionalmanufacturingindustriesandemergingmanufacturingformtheinfiltrationofelectromechanicalintegrationproducts,theso-calledthedigitalequipment.Numericalcontroltechnologyapplicationhasbroughttherevolutionarychangeforthetraditionalmanufacturingindustry,manufacturingindustryhasbecomeasymbolofindustrialization,andwithsomeimportantindustrytoexpandthedevelopmentofNCtechnologyandapplicationfieldofthepeople'slivelihoodofthe(IT,automotive,medical,light)playsamoreandmoreimportantroleinthedevelopmentofdigital,becausetheseindustriesneedequipmentisthemajortrendofmoderndevelopment,inthenewenvironmentofChina'saccessiontotheWTOandthefurtheropeningupofourcountry,thedevelopmentofnumericalcontroltechnologyandequipmentisaguaranteetoimprovetheimportanceofChina'smanufacturingindustryinformatizationlevelandinternationalcompetitionability,CNCmachiningandprogrammingofthegraduationdesignisanimportantpartofNCmachiningtechnologyofprofessionalknowledgeandprofessionalskillsteachingsysteminCNCtechnologyprofessional,throughthegraduationdesignsothatwelearntousethebasicknowledgeofbasictheoryinsomesubjects,atthesametime,makethesystemmorecompletetotheprofessional,soastoconsolidate,expand,deepentheknowledgeofthepurpose,cultureandimprovethecomprehensiveabilitytoanalyzeandsolveproblemsandtocultivatethescientific
researchandinnovationability.
Thisgraduationdesignmainlysolvestheproblemthattheclamping,toolpresetting,processdevelopment,workingproceduresandstepsofpartitioning,toolselection,cuttingtheamountdetermined,turningprogramming,machinetooloperation.ThemaindifficultyisthetwoclampinglevelZlengthisdifficulttoguarantee,cuttingparametersareset,theaccuracyoftheknife,theprocessofmaking.
Keywords:
CNCmachiningprocessanalysisprogram
摘要
前言
第一章数控技术概述
1.1数控加工简介
1.2数控加工必须遵循的一般原则
1.3数控加工工艺特点与内容
1.4数控加工的步骤
第2章刀具和切削用量的选择
2.1数控机床对刀具的要求
2.2数控加工刀具材料的选择
2.3切削用量的选择原则
第3章夹具的选择
3.1夹具的基本概念
3.2夹具的选择
3.3夹具的作用
3.4夹具的类型
第4章零件图工艺分析
4.1设备选择
4.2确定零件的定位基准和装夹方式
4.2.1粗基准选择原则
4.2.2精基准选择原则
4.2.3定位基准
4.2.4装夹方式
4.3加工方法的选择和加工方案的确定
4.3.1加工方法的选择
4.3.2加工方案的确定
4.4工序与工步的划分
4.4.1按工序划分
4.4.2工步的划分
4.5确定加工顺序及进给路线
4.5.1零件加工必须遵循的安排原则
4.5.2进给路线
4.6刀具的选择
4.7切削用量选择
4.7.1被吃刀量的选择
4.7.2主轴转速的选择
4.7.3进给速度的选择
第5章数控编程指令及编程误差与控制
5.1编程中工艺指令的处理
5.1.1常用G指令代码功能表
5.1.2常用M指令代码功能表
5.2编程误差与控制
5.2.1编程误差
5.2.2误差控制
第六章
6.1程序编程
6.2模拟运行
6.3零件加工
6.4精度自检
致谢
设计小结
附录
第一章数控技术概述
1.1数控加工简介
数控加工是指在数控机床上进行零件加工的一种工艺方法,数控机床加工与传统机床加工的工艺规程从总体上说是一致的,但也发生了明显的变化。
用数字信息控制零件和刀具位移的机械加工方法。
它是解决零件品种多变、批量小、形状复杂、精度高等问题和实现高效化和自动化加工的有效途径。
1.2数控加工必须遵守的一般原则
制定加工方案的一般原则为:
先粗后精,先近后远,先内后外,程序段最少,走刀路线最短,特殊情况特殊处理。
1.3数控加工工艺特点与内容
1.3.1数控加工工艺特点
由于数控加工采用了计算机控制系统和数控机床,使得数控加工与普通加工相比较有以下特点:
1.具有高度柔性:
在数控机床上加工零件,主要取决于加工程序,它与普通机床不同,不必制造、更换许多工具、夹具,不需要经常调整机床。
因此,数控机床适用于零件频繁更换的场合。
也就是适合单件、小批生产及新产品的开发,缩短了生产准备周期,节省了大量工艺设备的费用。
2.加工精度高:
数控机床的加工,一般可达到0.005~0.1mm,数控机床是按数字信号形式控制的,数控装置每输出一个脉冲信号,则机床移动部件移动一个脉冲当量(一般为0.001mm),而且机床进给传动链的反向间隙与丝杠螺距平均误差可由数控装置进行补偿,因此,数控机床定位精度比较高。
3.加工质量稳定、可靠:
加工同一批量零件,在同一机床,在相同加工条件下,使用相同道具和加工程序,刀具的走刀轨迹完全相同,零件的一致性好,质量稳定。
4.生产率高:
数控机床可有效地减少零件的加工时间和辅助时间,数控机床的主轴转速和进给量的范围大,允许机床进行大切销量的强力切削,数控机床目前正进入高速加工时代,数控机床移动部件的快速移动和定位及高速切削加工,减少了半成品的工序间周转时间,提高了生产效率。
5.改善劳动条件:
数控机床加工前经调整好后,输入程序并启动,机床就能自动连续进行加工,直至加工结束。
操作者主要是程序的输入、编辑、装卸零件、刀具准备、加工状态的观测,零件的检测等工作,劳动强度极大降低,机床操作者的劳动趋于智力型工作。
另外,机床一般是封闭式加工,即清洁,有安全。
1.3.2数控加工工艺内容
数控加工工艺过程是利用切削在数控机床上直接改变加工对象的形状、尺寸、表面位置、表面状态等,使其成为成品或半成品的过程。
数控加工工艺和数控加工工艺过程的主要内容如下:
(1)选择并确定进行数控加工的内容;
(2)对零件图纸进行数控加工的工艺分析;
(3)零件图形的数学处理及编程尺寸设定的确定;
(4)数控加工工艺方案的制定;
(5)工步、进给路线的确定;
(6)选择数控机床的类型;
(7)刀具、夹具、量具的选择和设计;
(8)切削参数的确定;
(9)加工程序的编写、校验与修改;
(10)首件试加工与现场问题处理;
(11)数控加工工艺技术文件的定型与归档;
1.4数控加工的步骤
必须利用设计前一到二周的时间研究设计计划和任务书,了解产品的工艺性和公差等级,在初步明确设计要求的基础上,可以步骤进行设计方案的论证。
(1)分析零件图样
根据任务书,画出零件图,并对工件的形状、尺寸、精度等级、表面粗糙度、刀具及等技术进行分析。
(2)确定加工工艺方案
根据上述的分析,选择加工方案,确定加工顺序,加工路线、装夹方式、切削用量材料等,要求有详细的设计过程和合理的参数。
(3)数值计算
根据零件图的尺寸,确定工艺路线及设计的坐标系,计算运动轨迹,得到刀位数据
(4)编写零件加工程序
根据数控系统的功能指令及程序格式,逐步编写加工程序单,写出有关的工艺文件如工序卡、数控刀具卡、刀具明细表、加工工序单等。
(5)程序校验
程序编完后,对程序进行校验,一般采用机床空运转方式,来检查机床的动作和运行轨迹的正确性,以校验程序。
(6)对工件进行加工(好的过程控制能很好的节约时间和提高加工质量)
(7)工件验收和质量误差分析(对工件进行检验,合格流入下一道。
不合格则通过质量分析找出产生误差原因和纠正方
第二章刀具和切削用量的选择
2.1数控机床对刀具的要求
为了保证数控机床的加工精度,提高生产率及降低刀具的消耗,在选用刀具时对刀具提出了很高的要求,如能可靠的断屑,有高的耐用度,可快速调整和更换等。
因此数控机床对刀具的选择应满足以下要求:
1.刀具材料应有一定的坚硬性、耐磨性和良好的切削性能,能适应数控机床高速切削
为提高生产率和加工高硬度材料的要求,数控机床向着高速度、大进给、高刚性和大功率发展。
中工作进给由0m/min—5m/min提高到0m/min—15m/min。
等规格的数控车床,其主轴最高转速一般为3000r/min—5000r/min,
2.刀具工作可靠性高,刀具材料有足够的强度和韧性,能承受较高的冲击载荷,刀具材料导热性好,能降低切削温度,提高刀具耐用度,保证数控机床的加工精度
3.较高的刀具耐用度
4.刀具的尺寸和定位精度高,满足数控机床的加工精度
5.刀具具有良好的断屑功能,使得切削加工过程平稳
6.刀具能够适应数控机床的快速换刀,减少换刀辅助时间
7.数控刀具设计制造要求标准化,模块化
2.2数控加工刀具材料的选择
机械加工中常用的刀具材料主要有高速钢、硬质合金、立方氮化硼(CBN)、陶瓷等。
由于重型切削的特点(切削深度大,余量不均,表面有硬化层),刀具在粗加工阶段的磨损形式主要是磨粒磨损。
由于切削温度高,尽管切削速度处于积屑瘤发生区,但高温可以使切屑与前刀面的接触部位处于液态,减小了摩擦力,抑制了积屑瘤的生成,所以刀具材料的选择应要求耐磨损、抗冲击,刀具涂层后硬度可达80HRC,具有高的抗氧化性能和抗粘结性能,因而有较高的耐磨性和抗月牙洼磨损能力。
硬质合金涂层具有较低的摩擦系数,可降低切削时的切削力及切削温度,可以大大提高刀具耐用度(涂层硬质合金刀片的耐用度至少可提高1倍)等优点,但由于涂层刀片的锋利性、韧性、抗剥落和抗崩刃性能均不及未涂层刀片,故不适用高硬度材料和重载切削的粗加工。
只有硬质合金刀具适合于重型切削的粗加工。
硬质合金分为钨钴类(YG)、钨钴钛类(YT)和碳化钨类(YW)。
加工钢料时,由于金属塑性变形大,摩擦剧烈,切削温度高,YG类硬质合金虽然强度和韧性较好,但高温硬度和高温韧性较差,因此在重型切削中很少应用。
与之相比,YT类硬质合金刀具适于加工钢料,由于YT类合金具有较高的硬度和耐磨性,尤其是具有高的耐热性,抗粘结扩散能力和抗氧化能力也很好,在加工钢料时刀具磨损较小,刀具耐用度较高,因此YT类硬质合金是重型加工时较常用的刀具材料。
因此,本次加工选用YG类硬质合金材料的刀具。
根据加工要求选用四把刀具,T01为粗加工车刀,故选用90°硬质合金机夹偏刀;T02为硬质合金机夹偏刀,其副偏角应较大,用于加工圆弧和精加工;T03为硬质合金机夹切断刀,其刀片宽度为3mm,用于切槽、切断等车削加工;T04为60°硬质合金机夹螺纹刀,用于螺纹车削加工。
同时把四把到在自动换刀刀架上安装好,且都对好刀,把它们的刀偏值输入相应的刀具参数中。
本设计中加工的工件材料为45号钢,因此选择的刀具材料为YT类硬质合金。
2.3切削用量的选择原则
合理选择切削用量的原则是,粗加工时,一般以提高生产率为主,但也应考虑经济性和加工成本;半精加工和精加工时,应在保证加工质量的前提下,兼顾切削效率、经济性和加工成本。
具体数值应根据机床说明书、切削用量手册,并结合经验而定。
切削深度ap。
在机床、工件和刀具刚度允许的情况下,ap就等于加工余量,这是提高生产率的一个有效措施。
为了保证零件的加工精度和表面粗糙度,一般应留一定的余量进行精加工。
数控机床的精加工余量可略小于普通机床。
切削宽度ae。
一般ae与刀具直径d成正比,与切削深度成反比。
经济型数控加工中,一般ae的取值范围为:
ae=(0.6~0.9)Dc。
切削速度Vc。
提高Vc也是提高生产率的一个措施,但Vc与刀具耐用度的关系比较密切。
随着Vc的增大,刀具耐用度急剧下降,故Vc的选择主要取决于刀具耐用度。
另外,切削速度与加工材料也有很大关系,例如车削合金刚30CrNi2MoVA时,Vc可采用8m/min左右;而用同样车削铝合金时,Vc可选200m/min以上。
数控编程时,编程人员必须确定每道工序的切削用量,并以指令的形式写入程序中。
切削用量包括主轴转速、背吃刀量及进给速度等。
对于不同的加工方法,需要选用不同的切削用量。
切削用量的选择原则是:
保证零件加工精度和表面粗糙度,充分发挥刀具切削性能,保证合理的刀具耐用度;并充分发挥机床的性能,最大限度提高生产率,降低成本。
从刀具的寿命(耐用度)出发,切削用量的选择方法是:
先选取被吃刀量,其次确定进给速度,最后确定主轴转速。
2.3.1背吃刀量确定
背吃刀量ap(切削深度)指:
垂直于进给速度方向的切削层最大尺寸。
一般指工件上已加工表面和待加工表面间的垂直距离。
在工艺系统刚性和机床功率允许的条件下,尽可能选取较大的切削深度,以减少进给次数。
当工件的精度要求较高时,则应考虑留有精加工余量,一般为0.1~0.5mm。
切削深度ap计算公式:
ap=
式中:
dw—待加工表面外圆直径,单位mm
dm—已加工表面外圆直径,单位mm.
2.3.2进给速度的确定
进给速度是数控机床切削用量中的重要参数,主要根据零件的加工精度和表面粗糙度要求以及刀具、工件的材料性质选取。
最大进给速度受机床刚度和进给系统的性能限制。
进给速度是指单位时间内,刀具沿进给方向移动的距离,单位为mm/min,也可表示为主轴旋转一周刀具的进给量,单位为mm/r。
确定进给速度的原则:
1)当工件的质量要求能够得到保证时,为提高生产效率,可选择较高的进给速度。
一般在100~200mm/min范围内选取。
2)在切断、加工深孔或用高速钢刀具加工时,宜选择较低的进给速度,一般在20~50mm/min范围内选取。
3)当加工精度,表面粗糙度要求高时,进给速度应选小些,一般在20~50mm/min范围内选取。
4)刀具空行程时,特别是远距离“回零”时,可以设定该机床数控系统设定的最高进给速度。
5)由于本设计的加工属于半精加工,因此,选用介于两者之间的进给速度,即50mm/min—100mm/min。
进给速度Vf的计算Vf = n f
式中:
n—车床主轴的转速,单位r/min 。
f—刀具的进给量,单位mm/r 。
2.3.3主轴转速的确定
1)光车外圆时主轴转速。
光车外圆时主轴转速应根据零件上被加工部位的直径,并按零件和刀具材料以及加工性质等条件所允许的切削速度来确定。
切削速度除了计算和查表选取以外,还可以根据实践经验确定。
需要注意的是,交流变频调速的数控车床低速输出力矩小,因而切削速度不能太低。
切削速度确定后,用公式n=1000v/πD计算主轴转速n(r/min)。
式中
v----切削速度,单位为m/min,由刀具的耐用度决定;
n----主轴转速,单位为r/min;
D----工件直径或刀具直径,单位为mm。
计算的主轴转速n最后要根据机床说明书选取机床有的或较接近的转速。
硬质合金外圆车刀切削速度的参考值
工件材料
热处理状态
ap(mm)
(0.3,2]
(2,6]
(6,10]
f(mm/r)
(0.08,0.3]
(0.3,0.6]
(0.6,1]
vc(m/min)
低碳钢、易切钢
热轧
140~180
100~120
70~90
中碳钢
热轧
130~160
90~110
60~80
调质
100~130
70~90
50~70
合金结构钢
热轧
100~130
70~90
50~70
调质
80~110
50~70
40~60
工具钢
退火
90~120
60~80
50~70
灰铸铁
HBS<190
90~120
60~80
50~70
HBS=190~225
80~110
50~70
40~60
高锰钢
10~20
铜及铜合金
200~250
120~180
90~120
铝及铝合金
300~600
200~400
150~200
铸铝合金(WSI13%)
100~180
80~150
60~100
注:
切削钢及灰铸铁时刀具耐用度约为60min
2)车螺纹时主轴的转速。
在车削螺纹时,车床的主轴转速将受到螺纹的螺距P(或导程)大小、驱动电机的升降频特性,以及螺纹插补运算速度等多种因素影响,故对于不同的数控系统,推荐不同的主轴转速选择范围。
大多数经济型数控车推荐车螺纹时的主轴转速n(r/min)为:
n≤
–k
式中:
P----被加工螺纹螺距(mm);
k----保险系数,一般取为80。
此外,在安排粗、精车削用量时,应注意机床说明书给定的允许切削用量范围,对于主轴采用交流变频调速的数控车床,由于主轴在低速时扭矩降低,尤其应注意此时的切削用量的选择。
总之,切削用量的具体数值应根据机床性能、相关的手册并结合实际经验用类比方法确定。
同时,使主轴转速、切削深度及进给速度三者能相互适应,以形成最佳切削用量。
第三章夹具的选择
3.1夹具的基本概念
1)什么是夹具:
是一种装夹工件的工艺装备,它广泛地应用在机械制造过程的切削加工、热处理、装配、焊接和检测等工艺过程中。
如在车床上广泛使用的三爪卡盘,顶尖和铣床上用的平口虎钳等都属于夹具。
在机床---刀具---工件---夹具组成的工艺系统中,夹具是一个重要的环节。
在现代生产中,机床夹具是一种不可缺少的工艺装备,它直接影响着工件加工的精度、劳动生产率和产品的制造成本。
3.2夹具的选择
数控加工对夹具主要有两大要求:
一是夹具应具有足够的精度和刚度;二是夹具应有可靠的定位基准。
选用夹具时,通常考虑以下几点:
1)尽量选用可调整夹具、组合夹具及其它通用夹具,避免采用专用夹具,以缩短生产准备时间。
2)在成批生产时才考虑采用专用夹具,并力求结构简单。
3)装卸工件要迅速方便,以减少机床的停机时间。
4)夹具在机床上安装要准确可靠,以保证工件在正确的位置上加工。
3.3夹具的作用
1)保证加工精度用机床夹具装夹工件,能准确确定工件与刀具、机床之间的相对位置关系,可以保证加工精度。
2)提高生产效率机床夹具能快速地将工件定位和夹紧,可以减少辅助时间,提高生
产效率。
3)减轻劳动强度机床夹具采用机械、气动、液动夹紧装置,可以减轻工人的劳动强度。
4)扩大机床的工艺范围利用机床夹具,能扩大机床的加工范围,例如,在车床或钻床上使用镗模可以代替镗床镗孔,使车床、钻床具有镗床的功能。
3.4夹具的类型
数控车床上的夹具主要有两类:
一类用于盘类或短轴类零件,工件毛坯装夹在带可调卡爪的卡盘(三爪、四爪)中,由卡盘传动旋转;另一类用于轴类零件,毛坯装在主轴顶尖和尾架顶尖间,工件由主轴上的拨动卡盘传动旋转。
在金属切削机床上使用的夹具统称为机床夹具。
在现代生产中,机床夹具是一种不可缺少的工艺装备,它直接影响着工件加