大型钢结构组焊工艺.docx
《大型钢结构组焊工艺.docx》由会员分享,可在线阅读,更多相关《大型钢结构组焊工艺.docx(156页珍藏版)》请在冰豆网上搜索。
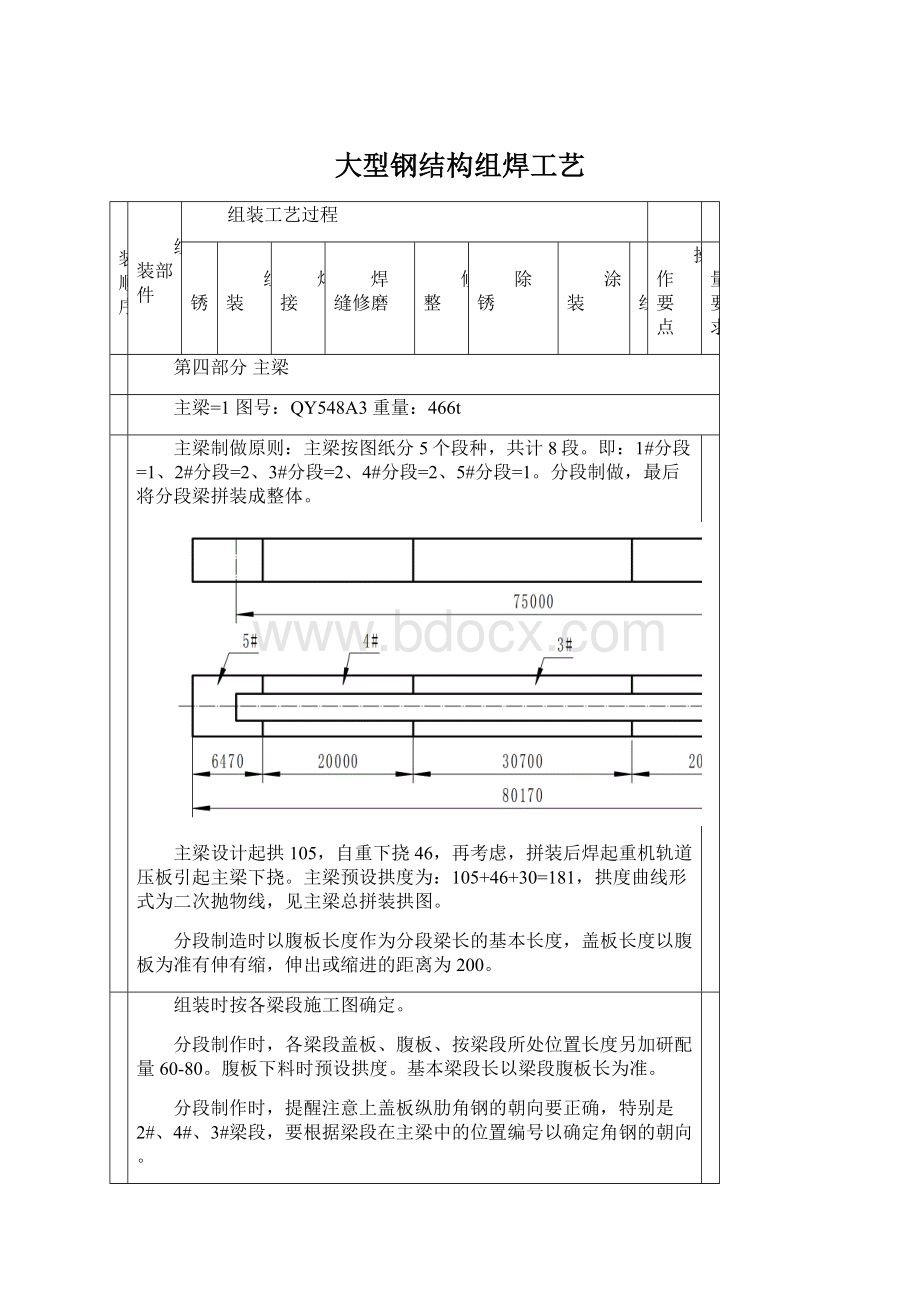
大型钢结构组焊工艺
组装顺序
组装部件
组装工艺过程
磨锈
组装
焊接
焊缝修磨
修整
除锈
涂装
划线
操作要点
质量要求
第四部分主梁
主梁=1图号:
QY548A3重量:
466t
主梁制做原则:
主梁按图纸分5个段种,共计8段。
即:
1#分段=1、2#分段=2、3#分段=2、4#分段=2、5#分段=1。
分段制做,最后将分段梁拼装成整体。
主梁设计起拱105,自重下挠46,再考虑,拼装后焊起重机轨道压板引起主梁下挠。
主梁预设拱度为:
105+46+30=181,拱度曲线形式为二次抛物线,见主梁总拼装拱图。
分段制造时以腹板长度作为分段梁长的基本长度,盖板长度以腹板为准有伸有缩,伸出或缩进的距离为200。
组装时按各梁段施工图确定。
分段制作时,各梁段盖板、腹板、按梁段所处位置长度另加研配量60-80。
腹板下料时预设拱度。
基本梁段长以梁段腹板长为准。
分段制作时,提醒注意上盖板纵肋角钢的朝向要正确,特别是2#、4#、3#梁段,要根据梁段在主梁中的位置编号以确定角钢的朝向。
考虑焊接因素的影响,各分段梁,腹板下料时,按主梁总拼装预拱图再另加一定的起拱量,保证梁段焊后达到总拼装予设拱度值。
详见各梁段组装预拱图。
为保证纵向加劲肋及盖腹板的匀顺拼接,拼接口处均留200长不焊;各分段纵肋角钢及T形肋均以各分段拼接口腹板、盖板长度为准左右各500预留1000镶补段。
分段主梁制作时,1#、5#分段正位组装,2#、4#、3#梁段反位组装,分段主梁制作后,分别把每段梁摆放到主梁整体拼装台架上,使分段主梁的纵向中心线与主梁整体中心线相吻合,用水准仪测量,使分段主梁两端的高低差符合整体主梁予设拱度值后,用经纬仪划出切头线,切掉多余部分后,再进行主梁的梁段间研配及主梁整体拼装。
主梁1#分段=1图号:
QY548A3a重量:
35.8t
1
备料
N1
-14×3000×5770=1见图QY548A3a-1,先拼接,修平后用数控下料,拼接口预留60切头量
N2
∠160×100×10×1468=4。
不下料组装配切。
下料尺寸758(预留嵌补段后的尺寸)
N3
-20×430×3200=4下料时下成-20×430
×(3200+60)=4
N4
-14×2200×3200=2下料时下成-14×2200
×(3200+60)=2
N5
-14×2000×(2240)=1下成-14×2000
×2270加量部分组装配切,配切后再切缺口
N6
-14×3586×5748=4拼接修平后用数控下料见图QY548A3a-6
N7
∠180×110×10×2790=2不下料组装配切
N8
∠180×110×10×2966=2不下料组装配切
N9
-14×2950×5770=2数控下料切孔(2950+60切头量)见图QY548A3a-9
N10
-8×760×1983数控下料见图QY548A3a-10
N11
-10×150×694
N12
-10×150×1850=2
N13
-8×340×795=4数控下料,见图QY548A3a-13
N14
-10×200×350=2见图QY548A3a-14
N15
ø85×6×2286=4不下料组装配切
N16
-8×340×2316=4数控下料参照刚腿下分段N23段做,以垂直端为准。
见图QY548A3a-16
N17
-10×150×2245=4长度留30切头量
N18
-10×138×254=4见图QY548A3a-18
N19
-14×2147×2650=4数控下料见图QY548A3a-19
N20
-20×200×14420=4长度留切头量50,煨弯
N21
-32×2800×7060=1数控下料(2800+60)见图QY548A3a-21
N22
-14×5784×7986=1先拼接荒料,(见拼料图)。
焊接修平后再下料。
见图QY548A3a-22
N23
∠180×110×10×1078=4不下料组装配切
N24
∠180×110×10×2498=2不下料组装配切
N25
∠180×110×10×990=8不下料组装配切
N26
∠180×10×10×2342=2不下料组装配切
N27
-8×115×140=26见图QY548A3a-27
N28
∠160×100×10×2950=6不下料组装配切。
下料尺寸2450(预留嵌补段后的尺寸)
N29
-8×220×350=20数切,见图QY548A3a-29
N30
∠160×100×10×3150=20不下料组装配切。
下料尺寸2450(预留嵌补段后的尺寸)
N31
-8×340×2450=4(预留嵌补段后的尺寸)
N32
-10×150×2450=4(预留嵌补段后的尺寸)
N33
-20×1682×2147=2数控下料
N34
-20×1600×3121=1数控下料
N35
-14×654×2650=4数控下料,见图QY548A3a-35
N36
-14×1323×2650=2数控下料,见图QY548A3a-36
N37
-20×150×400=12数控下料,见图QY548A3a-37
N38
-20×350×700=2
N39
∠180×110×10×1187=2不下料组装配切
N40
∠180×110×10×1274=2不下料组装配切
N41
∠180×110×2617=1不下料组装配切
N42
-14×1600×3078=1数控下料见图QY548A3a-42
N43
-10×200×6244=1下料长度切头量50煨弯
N44
-14×330×2650=2数控下料,两块下到一起,先切口再分开。
见图QY548A3a-44
N45
∠180×110×10×2650=2不下料组装配切
N47
∠180×110×10×3488=2不下料组装配切
N46
-20×2650×2890=1下料赶圆
N48
-14×210×800=8数控下料
N49
-20×600×1445=1下料赶圆
N50
-20×200×1948下料赶圆
N51
-6×55×85=8数切,见图QY548A3a-51
N52
-10×110×5534=2下料长度切头量50煨弯
N53
-10×110×3963=2下料长度切头量50煨弯
N54
-20×1000×1900=2数控下料见图QY548A3a-54
2
部件组焊
2.1
(N10+N12)=2
1
2
3
4
5
2.2
(N11+N13)=4
1
2
3
4
5
2.3
(N16+N17)=4
1
2
3
4
5
长组装配切
2.4
(N19+N20)=4
1
2
3
4
5
翘曲≤3
2.5
(N52+N53+N54)=4
1
2
3
4
5
2.6
N46圆筒组焊
1
2
3
4
5
1.组焊前切坡口
2.找圆修错口后定位焊。
3.焊后修圆
2.7
N49
圆筒组焊
1
2
3
4
5
1.组焊前切坡口
2.找圆修错口后定位焊
3.焊后修圆
2.8
(N42+N43)=1
1
2
3
4
5
翘曲≤3
2.9
上盖板拼接=2
N4=2
N3=4
N5=1
1
2
3
4
5
1.先拼焊(N4+N3),再与N5拼焊,N5配切,保中心距5300
2.焊后修平
3.修平后以一边为准在梁端头划线找方,齐头,切掉10
4.按本梁段组装第5项,将上盖板煨弯预拱。
2.10
上盖板组焊纵向加强角钢
上盖板=1
N28=3
精确划线组装,以中心线为向面边分
注意角钢端头距离50
,并装齐,拼接口注意镶补段的距离.
2.11
N22拼接
1
2
3
4
5
接料修平后按图QY548A3a-22重新划线下料。
2.12
端板N22组焊
1.N22二次下料后,以下底边为基准边分中划出垂直平分线,以此两互相垂直线为基准,划线。
1)划出门口线,并切割。
2)划出与端板有连接关系的各零件的组装定位线。
2.按以划好的组装定位线,依次组装相关零件,并施焊。
注意:
1)凡与内侧腹板有关系的零件,可先不组。
2)焊接时视变形情况可打段焊接一部分焊缝,另一部分焊缝留待箱段组成后再焊。
3.焊后修平,仍以下底边为基准。
根据组装成型的梁端腹板尺寸再重新划线配齐,保证组装要求。
2.13
外侧腹板(N1)单元组焊=2成对
N1=1
(N31+N32)=1
N30=5
(N1+N13)=1
(N16+N17)=1
1
2
3
4
5
1.划各零件组装定位线时注意
1)纵向零部件的间隔尺寸以腹板上端为基准,向下返尺寸,间隔尺寸a+2
2)横向零部件尺寸以跨度中心线为基准。
2.按划好的组装定位线组装各零部件。
组装时(N16+N17)下端长度划线配切。
划线时做一角度样板,角度按N11与N33所成夹角制作。
角钢制弯。
3.组装(N11+N13)时,端部用外卡样板检查,此样板角度根据腹板与上盖板角度制做,检查时,一边以腹板为准。
2.14
内侧腹板单元N9组焊=2(成对)
组装参照外侧腹板单元进行。
3
梁段组装
1.要求本分段按主梁1#分段预拱组装图采用正位置组装,组装必须在已测平的平台上进行,最大偏差≤2。
1.箱梁拼接口尺寸
上宽:
腹板中心距
2700±2(δ=14)
下宽:
腹板中心距1700±2(δ=14)
内口高5748
对角线差≤4
2.盖板倾斜度偏差≤3
3.上小车轨道中心距8000±5
4.下小车轨道中心距2600±3
5.梁段扭曲≤6
6.柔性铰安装范围内扭曲≤2
不平度最大偏差≤2
7.上盖板承轨板外伸部分平或向翘≤1
8.轨道中心与腹板中心偏差≤7
9.起拱值符合主梁起拱度1#分段部分数值,偏差±3
10.腹板及端板不平度1m板尺测量≤8
盖板不平度≤3
11.凡图纸要求熔透部位焊缝UT100%检查合格。
2.凡图纸及焊接工艺要求开坡口的零件必须在组装前切好坡口。
凡要求熔透焊缝并要求100%UT检查的焊缝,焊接规程严格按焊接工艺执行。
3.先在平台上划线。
划出两侧箱梁中心线及跨度中心,长度都要超过梁段的外轮廓尺寸。
在梁端头划出检查辅助线,划线时严格找方,用样冲在平台上打上标记。
4.将底板N21吊放在平台上,在底板上划出主梁中心线,箱梁中心线和跨度中心线。
划线后,将N21按线对准平台上已划好的各中心线,使各线相吻合,最大偏差≤1,如若超差,应重新检查所划线的精度,符合要求后将底板点焊在平台上,然后依次划出下列各零件组装定位线:
N49、N48、N22、N35、N36、N37、N44、N6、N19的组装定位线。
5.在底板上从跨度中心向跨中返850划线做为底板折弯线。
划线后用火焰沿线加热煨弯,使拼口头上翘离平台12,达到要求后端部垫实。
6.按已划好的两侧箱梁的中心线,再分别在箱体拼接口及端头部位,划出模拟隔板的定位线,按线组装模拟横板,调整到位后,将模拟隔板固定。
7.组装N19、N18
8.分别组装两侧内腹板单元N9及外侧腹板单元N1,腹板内侧应与隔板贴紧。
9.组装N29
10.组装上盖板单元。
组装前划出纵向中心线及轨道中心线。
注意纵向中心线对正,并以端头齐,分别检查两侧箱体截面尺寸,上部腹板中心距2700,下部腹板中心距1700,高5748
,对角线≤4。
检查上小车轨道中心距8000
,下小车车轨道中心距2600
。
11.组装(N10+N12)
12.组装N14、N18、N15
组装内部零件时,要在箱体内外以两端模拟隔板处为准检查腹板的平整度,超差部位在箱体内采取拉顶措施进行调整。
上下也应进行检查调整,保证整个腹板的平面度在焊前达到:
用1m平尺检查,不平度≤3
13.组装N6
14.根据端头尺寸,配切端头板N22,并进行组装。
15.组装其它零部件
16.组装后全部检查各部位尺寸,做出自检记录报专检。
17.专检检查合格后,进行焊接。
焊接时注意:
1)拼接口处加临时支撑,防止焊接变形。
2)拼接口处盖腹板间焊缝及纵向有拼接的角钢,T形头预留200mm不焊,以便主梁总成时调整位置。
18.焊后将梁段吊放在平台上进行检查,并重新划线。
在上盖板上划出箱体的纵向中心线。
在腹板上划出跨度中心线,并用样冲打上标记。
主梁2#、4#分段各2共计4图号:
QY548A3b单重52.8t
1
备料
N1
-20×430
×20000=2长度两端各留60mm切头量,拼接。
见QY548A3b-1、QY548A3b-5上盖板整体拼接图。
N2
-14×2400
×20000=21)长度两端各留60mm切头量。
2)下料按腹板拼接下料图进行。
见QY548A3b-2、QY548A3b-3整体拼接图及下料图。
N3
-12×3370
×20000=21)长度两端各留60mm切头量。
2)下料按腹板拼接下料图进行。
见QY548A3b-2、QY548A3b-3整体拼接图及下料图。
N4
-32×1760
×20000=11)长度两端各留60mm切头量。
2)下料按下盖板拼接下料图进行。
见QY548A3b-4。
先整板对接焊后再下料。
N5
-14×2200
×20000=11)长度两端各留60mm切头量。
2)下料按拼接下料图进行。
见QY548A3b-1、QY548A3b-5上盖板整体拼接图。
N6
-8×760×1983
=7数控下料
N7
-10×150×694=14
N8
-10×150×1850
=7
N9
-8×340×795=14数控下料
N10
-10×150×350=7
N11
圆管ø85×6×1510=14不下料,组装配切。
N12
圆管ø85×6×1606=7不下料,组装配切。
N13
圆管ø85×6×1455=14不下料,组装配切。
N14
圆管ø85×6×1362=7不下料,组装配切。
N15
-8×340×4996=14数控下料,参照刚性腿下分段N23制做,以垂直端为准,斜端留二次切头量30mm,宽680
,见图QY548A3b-15。
N16
-10×150±1×4925=14长留30mm切头量
N17
-10×150±1×1042
=7
N18
-8×340×1042=7数控下料,见图QY548A3b-18
N19
-8×115×140=63见图QY548A3b-19
N20
∠160×100×10×20000=9不下料,组装配切。
下料尺寸19000(预留嵌补段后的尺寸)
N21
-8×220×350=66数控下料
N22
-8×340
×20000按拼接下料图下料见QY548A3b-22。
下料尺寸19000(预留嵌补段后的尺寸)
N23
-10×150-1×20000按拼接下料图下料见QY548A3b-23。
下料尺寸19000(预留嵌补段后的尺寸)
N24
∠140×90×10×20000=6不下料,组装配切。
下料尺寸19000(预留嵌补段后的尺寸)
N25
-8×95×140=42见图QY548A3b-25
N26
-10×167×172=14见图QY548A3b-26
N27
-10×154×175=14见图QY548A3b-27
N28
-6×45×53=56数控下料,见图QY548A3b-28
2
部件组焊
2.1
(N7+N9)=7
1
2
3
4
5
组装以斜头端齐
2.2
(N6+N8)=7
1
2
3
4
5
2.3
(N17+N18)=7
1
2
3
4
5
2.4
(N15+N16)=14
1
2
3
4
5
参照刚性腿下分段N23进行。
2.5
(N25+N26)=14
2.6
腹板拼接=2(成对)
1
2
3
4
5
1.材料拼接必须在平整的场地上进行
2.按腹板拼料图QY548A3b-2、QY548A3b-3整体拼接图成对拼接,拼接时以腹板里侧面平齐。
拼接板时保证两横向对接焊缝中心距3700±2
组拼后全面检查拼接后的各部位尺寸,长、宽。
3.拼焊后板修平
4.重新检查拼板尺寸。
按QY548A3b-2、QY548A3b-3整体下料图成对划线下料。
5.切坡口,成对切坡口,要求:
1)一组腹板上下端分别成对切坡口,弄清图纸及焊接工艺对坡口尺寸的要求,并搞清方向后再切。
2)坡口尺寸要切准确,否则直接影响焊缝质量。
3)先切腹板下侧边坡口,后切上侧边坡口。
6.4对(8块)腹板拼焊及切坡口后要按拼接图上的拱度值要求修拱。
拱度值偏差≤3
7.比较8块板的拱度值,将拱度值最接近的一对做为一组,装在一段梁上,并做好标记。
8.自检合格后报专检。
2.7
腹板单元组焊=2(成对)
1
2
3
4
5
腹板经专检认可后进行腹板单元组焊,组装成对
1.先在平台上划出一组直角坐标轴线,根据2#、4#梁段的长度(不包括切头量长度)在整个主梁上所处的位置拱度值计算梁段两端拱度差130,并将130反映在坐标轴上,然后将腹板摆放在坐标系内就位。
2.检查纵向接料焊缝位置,此时应在坐标系内处于倾斜位置。
斜度13/2000。
从主梁跨端端为准,向跨中方向返60mm划线,以此线做为长度方向基准线及箱体组装定位基准。
按腹板在坐标系内所处位置,从基准线上端划纵向焊缝的垂线做为横肋的组装定位线。
划线时尺寸加L/1000的焊接收缩量。
3.以腹板上端做为横向划线基准,划出纵向角钢的组装定位线间隔尺寸a+2。
4.划出横肋、纵肋组装定位线。
5.按划出的定位线依次组装纵、横零件,组装时注意:
1)先组横肋(N7+N9),上端以角度样板定位,且以腹板边缘为准。
2)组T形纵肋(N22+N23)
3)组横肋(N15+N16),下端长度多余部分,用角度样板划线后切割,切割后用砂轮将切口打磨干净。
4)组装纵肋(N22+N23)及纵向角钢时注意预留镶补段的位置。
6.腹板单元施焊时要采取反变形措施,尽量减小焊接变形,焊后修平。
也可根据现场情况,为控制焊接变形,先焊一部分焊缝,剩余焊缝,待箱体总成后焊接。
宽度3060
侧弯≤5
平对接口错边≤1
2.8
上盖板拼接
1
2
3
4
5
1.上盖板拼接按拼装图QY548A3b-1、QY548A3b-5进行。
先接宽,接宽修直修平后,划出纵向中心线,并以此线为基准,在接长端划方线齐头,切去10后按焊接工艺要求切坡口。
2.接长。
接长时以板纵向中心线为准找直。
3.上盖拼接焊后修平、修直后划出上盖板中心线,用样冲打上标记。
4.按纵向中心线划出两侧的轨道中心线。
2.9
上盖板单元组焊
1
2
3
4
5
1.在上盖板内表面从跨端端向里返60mm做纵向中心线的垂直线,用样冲打上标记,并返到板的厚度上,用样冲打上标记。
以此线做为箱体组装的组装定位线。
2.在上盖板内表面划出纵向加强角钢的组装定位线,在2#、4#梁段的组装胎内将上盖板预拱。
并依线组装N21,间隔尺寸675+2,2#、4#梁段上盖板组装时注意梁段角钢的朝向。
3.施焊。
施焊时采取反变形或者为了减少变形,先在下面焊部分焊缝。
2.10
下盖板拼接
1
2
3
4
5
按下盖板拼接图进行。
先整板接料宽后再下料,下料后在2#、4#梁段的组装胎内将下盖板预拱。
3
梁段拼装
1.梁段拼装在2#、4#梁段专用组装胎架上,采用反位置组装,按主梁2#、4#分段预拱组装图形式进行。
2.在胎架上预先用经纬仪做出梁段的纵向中心线,做为组装的纵向基准,并按梁段长度做纵向中心线的垂直线。
3.在胎架上按梁段长度两端的预拱值及梁段的修正预拱值,在胎架上布置拱度控制牙板,并用水平仪测量,做好原始记录。
4.在上盖板上划出纵向中心线,并从跨端端返60+200做出纵向中心线的垂线,返线到板的厚度,并用样冲打上标记,此线做为箱体的组装定位线。
以上盖板纵向中心线及组装定位线,划出腹板定位线,横肋(N6+N8)的组装定位线。
在两端距拼接口500mm处,箱内按图示尺寸划出模拟隔板组装定位线。
5.吊放上盖板到胎架上,使上盖板纵向中