氧化铝沉降片区培训教材.docx
《氧化铝沉降片区培训教材.docx》由会员分享,可在线阅读,更多相关《氧化铝沉降片区培训教材.docx(18页珍藏版)》请在冰豆网上搜索。
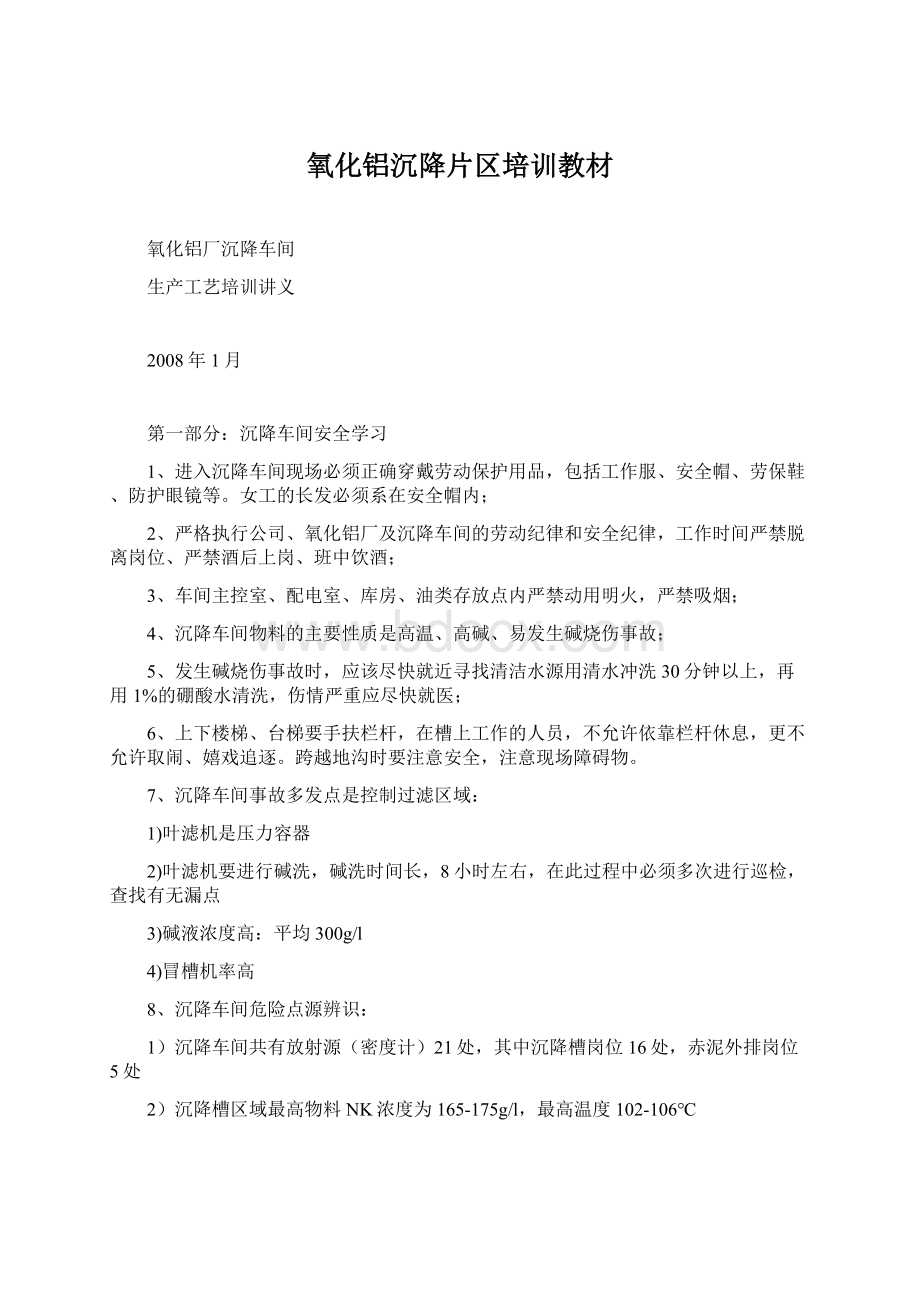
氧化铝沉降片区培训教材
氧化铝厂沉降车间
生产工艺培训讲义
2008年1月
第一部分:
沉降车间安全学习
1、进入沉降车间现场必须正确穿戴劳动保护用品,包括工作服、安全帽、劳保鞋、防护眼镜等。
女工的长发必须系在安全帽内;
2、严格执行公司、氧化铝厂及沉降车间的劳动纪律和安全纪律,工作时间严禁脱离岗位、严禁酒后上岗、班中饮酒;
3、车间主控室、配电室、库房、油类存放点内严禁动用明火,严禁吸烟;
4、沉降车间物料的主要性质是高温、高碱、易发生碱烧伤事故;
5、发生碱烧伤事故时,应该尽快就近寻找清洁水源用清水冲洗30分钟以上,再用1%的硼酸水清洗,伤情严重应尽快就医;
6、上下楼梯、台梯要手扶栏杆,在槽上工作的人员,不允许依靠栏杆休息,更不允许取闹、嬉戏追逐。
跨越地沟时要注意安全,注意现场障碍物。
7、沉降车间事故多发点是控制过滤区域:
1)叶滤机是压力容器
2)叶滤机要进行碱洗,碱洗时间长,8小时左右,在此过程中必须多次进行巡检,查找有无漏点
3)碱液浓度高:
平均300g/l
4)冒槽机率高
8、沉降车间危险点源辨识:
1)沉降车间共有放射源(密度计)21处,其中沉降槽岗位16处,赤泥外排岗位5处
2)沉降槽区域最高物料NK浓度为165-175g/l,最高温度102-106℃
3)絮凝剂岗位溢出的絮凝剂溶液很滑,处理或行走时要特别小心,防止滑倒受伤,如絮凝剂溶液溅入眼睛或皮肤上时,要立即用清水冲洗20分钟以上,如有必要,送医院治疗
4)控制过滤区域最高物料浓度为165-180g/l,液碱最高浓度为400-500g/l,最高温度102-106℃
5)立式叶滤机查样时,脸部不要正对取样管,以防碱液溅出伤人。
6)赤泥隔膜泵最高允许出料压力为120bar,生产中要求控制在90bar以下,严禁超压运行。
如发生超压报警应立即采取措施及时处理。
9:
沉降车间危险点(源)的对策表
9.1沉降槽区危险分析表
危险因素
危险原因
措施
辐射
1.产生有害射线辐射的密度计无保护装置或有缺陷。
2.长时间停留在产生射源的附近。
3.劳动保护装置不全。
1.要求计控人员对产生有害射线辐射的密度计设置保护装置。
2.路过密度计附近时尽量不要长时间停留。
3.穿戴好相关的劳动保护装置。
机械伤害
1.旋转部位安全存在隐患。
2.点检旋转部位时带手套。
3.以手代替工具。
4.劳保用品穿戴不齐全。
1.穿戴齐全劳保用品。
2.认真按照安全规程进行操作。
3.完善各种安全防护装置。
4.按规定穿戴好劳保用品。
烫伤
1.槽内贮存洗水温度较高,
2.蒸汽温度最高可达140℃左右。
3.管道、设备不良,漏水或喷水。
4.液位计失灵,冒槽,排放不及导致槽区内积水过高。
5.不遵守操作规程冒险作业。
1.加强点检,保证设备、管道完好无损。
2.严格操作规程,杜绝冒险作业现象发生。
3.精心操作,加强槽内液位监控,防止冒槽事故发生。
4.联系计控人员处理,加强操作。
5.严格按照规程作业。
碱伤害
1.沉降底流、溢流含碱浓度高,腐蚀性大。
2.设备管道不良,存在安全缺陷。
3.槽液位计失灵或操作控制不当,导致冒槽。
4.滑倒。
1.加强巡检。
2.坚守岗位,精心操作。
3.定期校验液位计。
4.及时对存在安全缺陷的设备及管道进行维修和更换。
5.搞好现场环境卫生。
高处坠落
1.忽视警告,攀坐在不安全位置。
2.没有与操作人员配合好。
3.槽顶及爬梯防护栏年久失修。
4.不系安全带或使用不当。
5.照明不足。
1.佩戴齐全各种防护用品。
2.与操作人员做好配合工作。
3.完善防护栏等安全防护装置。
4.严格按规程佩戴齐全各种防护用品。
5.保持充足的照明。
灼烫
1阀门、管道密封不良。
2.管道隔热装置有缺陷。
3.没有正确使用个人防护用品。
1.做好无泄漏工作。
2.完善管道的隔热装置。
3.正确使用各种劳动保护用品。
9.2絮凝剂区危险分析表
危险因素
危险原因
措施
碱伤害
1.配制絮凝剂碱水的液碱及碱水含碱浓度高,腐蚀性大。
2.设备管道不良,存在安全缺陷。
3.槽液位计失灵或操作控制不当,导致冒槽。
4.滑倒。
1.加强巡检。
2.坚守岗位,精心操作。
3.定期校验液位计。
及时对存在安全缺陷的设备及管道进行维修和更换。
4.搞好现场环境卫生。
灼烫
1.蒸汽温度最高可达150℃左右。
2.管道、设备不良,漏水或喷水。
3.液位计失灵,冒槽,排放不及导致槽区内积水过高。
4.不遵守操作规程冒险作业。
1.做好防护工作。
2.加强点检,保证设备、管道完好无损。
3.严格操作规程,杜绝冒险作业现象发生。
4.精心操作,加强槽内液位监控,防止冒槽事故发生。
高处坠落
1.忽视警告,攀坐在不安全位置。
2.没有与操作人员配合好。
3.槽顶及爬梯防护栏年久失修。
4.不系安全带或使用不当。
1.佩戴齐全各种防护用品。
2.与操作人员做好配合工作。
3.完善防护栏等安全防护装置。
4.严格按规程佩戴齐全各种防护用品。
机械伤害
1.旋转部位安全存在隐患。
2.点检旋转部位时带手套。
3.以手代替工具。
4.劳保用品穿戴不齐全。
1.穿戴齐全劳保用品。
2.认真按照安全规程进行操作。
3.完善各种安全防护装置,避免冒险作业。
4.按规定穿戴好劳保用品。
9.3热水槽、稀释后槽区危险分析表
危险因素
危险原因
措施
碱伤害
1.稀释浆液含碱浓度高,腐蚀性大。
2.设备管道不良,存在安全缺陷。
3.槽液位计失灵或操作控制不当,导致冒槽。
4.滑倒。
1.加强巡检。
2.坚守岗位,精心操作。
3.定期校验液位计。
及时对存在安全缺陷的设备及管道进行维修和更换。
4.搞好现场环境卫生。
灼烫
1槽内贮存洗水温度较高,
2蒸汽温度最高可达150℃左右。
3管道、设备不良,漏水或喷水。
4液位计失灵,冒槽,排放不及导致槽区内积水过高。
5不遵守操作规程冒险作业。
1.2.做好防护工作。
3.加强点检,保证设备、管道完好无损。
4.严格操作规程,杜绝冒险作业现象发生。
5.精心操作,加强槽内液位监控,防止冒槽事故发生。
高处坠落
1.忽视警告,攀坐在不安全位置。
2.没有与操作人员配合好。
3.槽顶及爬梯防护栏年久失修。
4.不系安全带或使用不当。
1.佩戴齐全各种防护用品。
2.与操作人员做好配合工作。
3.完善防护栏等安全防护装置。
4.严格按规程佩戴齐全各种防护用品。
机械伤害
1.旋转部位安全存在隐患。
2.点检旋转部位时带手套。
3.以手代替工具。
4.劳保用品穿戴不齐全。
1.穿戴齐全劳保用品。
2.认真按照安全规程进行操作。
3.完善各种安全防护装置。
4.按规定穿戴好劳保用品。
9.4控制过滤区预先危险分析表
危险因素
危险原因
措施
碱伤害
1.阀门、管道密封不良。
2.生产介质含碱浓度高、温度高、且腐蚀性大。
3.管道破裂。
4.地沟盖板不全或有缺陷。
5.人操作行为失误。
1.加强巡回检查,发现泄漏即使汇报和处理。
2.严格按安全规程进行操作。
3.加强设备维护及点检。
4.及时完善安全装置。
5.严格按安全规程进行操作。
压力容器
爆炸
1.容器内压力过高,超过许可压力范围。
2.安全阀失效,未能及时开启泄压。
3.压力表显示错误。
1.按要求校验安全阀、压力表等安全装置。
2.严格按操作规程进行操作。
3.认真操作,一旦发现异常及时处理或通知相关人员处理。
高处坠落
1.攀坐不安全装置。
2.防护围栏锈死或焊接不牢。
3.照明不足。
4.不系安全带或使用不当。
5.在容器内进行检修作业时工作支架不牢。
1.认真按照安全规程进行操作。
2.定期检查、完善各安全装置。
3.保持充足的照明。
4.认真按照安全规程进行操作。
5.定期检查、完善各安全装置。
机械伤害
1.旋转部位安全存在隐患。
2.点检旋转部位时带手套。
3.以手代替工具。
4.劳保用品穿戴不齐全。
1.穿戴齐全劳保用品。
2.认真按照安全规程进行操作。
3.完善各种安全防护装置。
4.按规定穿戴好劳保用品。
物体打击
1.上下交叉作业,物体坠落。
2.作业上方物体不牢固。
3.工作中配合不当。
4.工具器、设备有缺陷飞出伤人。
5.视觉受阻或精神不集中而碰撞。
1.上下交叉作业严禁抛接物品及防止物品掉落。
2.检查现场不安全因素并排除。
3.加强相互配合及互保工作。
4.工作前检查好工具及设备。
5.工作中集中精力熟悉环境,穿戴好劳保用品。
起重伤害
1.钢丝绳夹手,挤伤。
2.钢丝绳扎手或崩断伤人。
3.扎绑不牢固,吊物掉落伤人。
4.违章指挥、违章操作。
5.从起重物下穿过或停留。
6.起吊设备不牢固,有缺陷坠落。
1.做好配合,防止夹手、挤伤。
2.工作前检查钢丝绳可靠性。
3.按规定严格扎绑钢丝绳。
4.严禁违章指挥、违章作业。
5.禁止在起吊重物下停留、穿越。
6.工作前检查好起吊设备可靠性。
触电
1.电线裸露。
2.线路过载,老化。
3.劳保用品穿戴不齐全。
4.在容器内作业不按规定使用安全电压。
1.定期检查,维修线路。
2.佩戴齐全各种防护用品。
3.按规定穿戴好劳保用品。
4.按规定使用安全照明。
9.5赤泥外排区预先危险分析表
危险因素
危险原因
措施
压力容器爆炸
1.压力容器内压力过高,超过许可压力范围。
2.安全阀失效,未能及时开启泄压。
3.压力表显示错误。
1.按要求校验安全阀、压力表等安全装置。
2.严格按操作规程进行操作。
3.认真操作,一旦发现异常及时处理或通知相关人员处理。
辐射
1.产生有害射线辐射的密度计无保护装置或有缺陷。
2.长时间停留在产生射源的附近。
3.劳动保护装置不全。
1.要求计控人员对产生有害射线辐射的密度计设置保护装置。
2.路过密度计附近时尽量不要长时间停留。
3.穿戴好相关的劳动保护装置。
火灾
1.违反规定,在泵房区内或进行检修、操作作业流程范围内动烟火。
2.电气线路原因导致失火。
3.自然现象或其他人力无法预防因素。
1严格遵守安全作业规程。
作业过程严禁烟火。
2.请专业人员定期对电气线路进行检查。
触电
1.电线裸露。
2.线路过载,老化。
3.劳保用品穿戴不齐全。
1.2.定期检查,维修线路。
3.佩戴齐全各种防护用品。
机械伤害
1.劳保用品穿戴不规范。
2.以手代替工具。
3.运行中跨越皮带。
1.劳保用品穿戴要做到“三紧”。
2.按照安全规程进行操作。
3.严禁跨越皮带。
碱伤害
1.阀门、管道密封不良。
2.生产介质含碱浓度高、温度高、且腐蚀性大。
3.管道破裂。
4.地沟盖板不全或有缺陷。
5.人操作行为失误。
1.加强巡回检查,发现泄漏及时汇报和处理。
2.严格按安全规程进行操作。
3.加强设备维护及点检。
4.及时完善各安全装置。
5.严格按操作规程进行操作。
高处坠落
1.运行中跨越皮带。
2.作业场所道路不畅通。
3.照明不足。
4.不系安全带或使用不当。
1.严禁跨越皮带。
2.加强文明卫生管理及现场定置管理。
3.及时补充照明。
4.严格按规程佩戴齐全各种防护用品。
第二部分沉降车间工艺理论学习
主要任务:
将溶出送来的稀释矿浆进行分离与洗涤,把粗液送控制过滤精制,把底流送往赤泥过滤系统,同时向溶出送稀释洗液
一、沉降车间包括的区域:
沉降车间主要包括三个区域,其中有:
赤泥分离与洗涤、控制过滤、赤泥外排
二、基本任务:
1、赤泥分离与洗涤区域:
1.1负责将高压溶出稀释矿浆经沉降分离后向控制过滤输送合格粗液;
1.2底流经四次反向洗涤后用外排泵外排符合要求的末次赤泥;
1.3向高压溶出输送合格的一次洗液;
1.4把合格的絮凝剂按生产要求加入各沉降槽。
2、控制过滤区域
负责将分离沉降槽送来的分离溢流(浮游物≤300mg/l),通过叶滤机进行精制,得到符合要求的精液(浮游物≤15mg/l),并将制得的精液送至分解车间的板式换热器,被滤出的浮游物形成滤渣送回沉降系统稀释后槽。
3、赤泥外排区域
将经过赤泥分离与洗涤区域四次沉降洗涤后的液固比L/S≤1.5的末次底流通过末次底流泵送到调浆槽后再用赤泥隔膜泵送往赤泥堆场堆存。
三、工艺流程概述:
1、赤泥分离与洗涤流程概述:
经高压溶出送来的合格的稀释矿浆经过稀释后槽常压脱硅后(脱硅时间4小时),用稀释后泵送入分离沉降槽进行一次沉降分离,分离沉降槽的溢流(即分离溢流),用分离溢流泵送往控制过滤粗液槽。
分离沉降槽底流用底流泵送入洗涤沉降槽进行四次反向洗涤,进一步回收其中的氧化铝和碱。
一次洗涤沉降槽溢流即一次洗液,用一次洗液泵送入高压溶出稀释槽稀释溶出矿浆,底流用泵送入二次洗涤沉降槽。
二次洗涤沉降槽溢流用泵送入一次洗涤沉降槽,底流用泵送入三次洗涤沉降槽。
三次洗涤沉降槽溢流用泵送入二次洗涤沉降槽,底流用泵送入四次洗涤沉降槽。
四次洗涤沉降槽溢流用泵送入三次洗涤沉降槽,底流(末次洗涤赤泥)用底流泵送入赤泥外排调浆槽后用赤泥隔膜泵外排。
热水站的热水做为洗水用洗水泵加入末次洗涤沉降槽。
合格的絮凝剂用泵经计量后,根据生产要求分别加入分离和洗涤沉降槽。
2、控制过滤区域流程概述
粗液中往往含有微量(0.1g/l以上)的悬浮于溶液中的浮游物。
这种浮游物微粒是赤泥细粒。
这些浮游物如果不被清除,那么在精种分解时,就将会作为氢氧化铝的晶核而进入氢氧化铝中,影响氧化铝产品的质量,因此,铝酸钠溶液进入分解工序前必须经净化出去浮游物,就要进行粗液精制
从赤泥分离洗涤工序分离沉降槽送来的分离溢流(浮游物≤300mg/L)进入控制过滤粗液槽,在槽中加入定量的石灰乳作为助滤剂。
石灰乳由石灰制备工序送到控制过滤石灰乳槽,然后由石灰乳泵计量后送到粗液槽中。
含石灰乳(助滤剂)的粗液用变频调速泵送入立式叶滤机,经过滤除去溶液中的绝大部分固体(滤饼)。
立式叶滤机每个工作周期为三个阶段(按周期1小时为例):
第一阶段滤液循环2分钟,期间助滤剂在滤布上形成过滤层,透过滤层的滤液为浑浊的溶液,返回粗液槽;第二阶段正常过滤57分钟,透过滤层的滤液为精制液(固含≤15mg/L),精制液进入精液槽用精液泵送往分解板式精液降温系统;第三阶段减压卸饼1分钟,滤饼用精液反冲至滤饼槽用滤饼泵送往稀释后槽。
当卸饼完成后,进入新一轮循环工作周期。
3、赤泥外排区域流程概述:
将赤泥经过四次沉降洗涤后的液固比L/S≤1.5的末次底流通过末次底流泵送到调浆槽后再用赤泥隔膜泵送往赤泥堆场堆存。
四、部分主要设备的工作原理:
1、沉降槽
1)沉降槽的工作原理是:
固体小颗粒在液体中受重力的作用慢慢降落从液体中分离出来。
沉降车间沉降槽包括两种;φ42*7m平底沉降槽5台及φ20*20高效深锥沉降槽2台,其中2台高效深锥沉降槽作为最后两次赤泥洗涤槽。
平底沉降槽表面积大、缓冲液量能力强,高效深锥沉降槽压缩性能好,最大可以提高底流固含到800g/l,有利于降低赤泥副液中带走的碱和氧化铝,降低成本。
2)立式叶滤机
立式叶滤机主要由立式机筒和立式过滤机元件(滤叶)组成,滤叶呈星型排列。
每个滤叶由过滤袋、插入滤袋的导管、滤液聚液器等组成。
过滤时,粗液被粗液泵送入机筒内,再由粗液泵提供的一定压力下,过滤液通过滤袋即制成精液,然后精液沿导流管流入聚液器,最后进入机筒外部的精液总管;滤渣在滤袋外部形成滤饼。
立式叶滤机一个叶滤周期同样由进料、挂泥、作业、卸泥四个过程组成。
过滤面积:
306平方米,每台叶滤机里安装114块滤布
五、工艺条件及经济技术指标:
1、分离与洗涤:
技术条件与作业指标
1.1技术条件
进料条件:
苛性碱浓度165-175g/l(以Na2O计)
进料固含65~75g/l
进料温度100~105℃
操作条件:
分离槽温度100~105℃
洗涤槽温度90~95℃
洗涤洗水温度≥95℃NT≤1.0g/l
1.2作业指标
分离溢流浮游物≤300mg/l
末次底流液固比L/S≤1.5
2、控制过滤:
作业指标
——精液浮游物≤15mg/l;
——精液Nk:
165-175g/l;
——立式叶滤机操作压力:
0.5—3.9bar;
——清洗精液泵和精液管碱液:
Nk280—320g/l,温度≥90℃;
——清洗叶滤机用碱液:
Nk250—300g/l左右,温度≥90℃;
——石灰乳加入量(CaO)250mg/l
六、生产控制要点:
1、分离与洗涤:
1.1主要作业指标技术操作要点
沉降生产主要控制好两个指标,即:
分离溢流浮游物、末次底流固含。
1.1.1分离溢流浮游物指标控制要点
1.1.1.1严格控制进出物料固相的平衡,当进料固含增大时调大分离底流泵转速,增大底流泵的流量,加大排泥量,防止沉降槽泥层上升,导致沉降槽跑浑,同时防止底流出料少,造成沉降槽积泥;
1.1.1.2分离沉降槽温度不能低于100℃。
特别是溶出停车时,温度低时不能给控制过滤送料,防止叶滤机滤布结硬,影响叶滤机过料;
1.1.1.3控制好稀释后料浆浓度在165—175g/L之间相对稳定,根据来料情况调节洗液加入量的大小进行稀释浆液浓度的控制;
1.1.1.4注意絮凝剂的配制质量和加入流量,保证絮凝剂的连续稳定加入。
絮凝剂加入量在保证沉降槽赤泥沉速和澄清度的前题下尽量少加。
当沉降槽跑浑时,可以适当加大絮凝剂添加量,以改善沉降效果;注意槽子转好后要及时减少絮凝剂加入量至正常加入量;
1.1.1.5避免大量污水或雨水进入沉降槽,防止槽内物料温度降低或液量平衡困难;
1.1.1.6沉降槽温度按要求尽量保持稳定;及时记录化验分析报告,掌握浮游物变化趋势,以便及时采取处理措施进行参数调整。
1.1.2底流固含控制要点
1.1.2.1控制好底流固含,可以提高洗涤效率。
底流固含控制主要依据沉降槽进料固含和进料量,调节底流泵转速来调节流量,从而平衡泥量,稳定固含;底流固含高、进料泥量大时,提高底流泵的转速,增大排泥量;底流固含低、进料泥量少时,降低底流泵的转速,减少排泥量;
1.1.2.2为了提高沉降效率,必须严格按絮凝剂生产作业规程要求配制合格的絮凝剂保证其絮凝效果。
技术要求
1)絮凝剂配制浓度
3~6‰
2)絮凝剂加入量
分离槽30~50g/t.-干赤泥
洗涤槽20~60g/t.-干赤泥
2、控制过滤:
主要作业指标技术操作要点
1)正常情况下,根据粗液槽进料量及精液输送量大小决定叶滤机开车台次;在粗液浮游物高时,可通过增开叶滤机台次或增加刷车次数的方法保证精液质量合格,液量平衡;
2)操作过程中注意监控精液质量,如发现精液有跑浑现象,应立即改变滤液流向,查明原因并处理后,改回精液槽;
3)注意各槽液位情况,以防出现冒槽或因槽子液位过低引起流量波动;
4)出现设备故障时,如具备条件,应立即倒用备用设备,将有故障的设备退出检修,如不能马上倒换的,应报告调度室和车间,安排调整系统液量等情况,以便检修设备;
精液浮游物控制要点
1)严格按控制过滤生产作业规程进行作业;
2)及时巡检查样,正常情况2h查一次样,发现跑浑滤片及时关闭,并做好记录,以便及时处理;
3)精液槽保持清洁无浑料,发现有浑料后要联系分解停送精液,然后将精液槽浑料放空并且重新进料将槽子冲干净后才能正常进料投入正常生产。
七、主要设备性能及参数:
1、沉降槽及其驱动头、附电机
沉降系统共有沉降槽7台,φ42*7m平底沉降槽5台及φ20*20m高效深锥沉降槽2台
平底沉降槽:
φ42*7m附电机:
N=4.0kw/380V/IP55/F
深锥沉降槽:
φ20*20m附电机:
N=7.5kw/380V/IP55/F
2、溢流泵:
16台
分离溢流泵型号:
250ZJ-1-A65(60),Q=828m3/hH=24m
洗液泵148/158/168:
200ZJ-1-A60,Q=446m3/hH=18m
洗液泵178:
150ZJ-1-A50,Q=390m3/hH=36m
3、底流泵:
19台
分离底流泵117/127/137:
100ZJA-1-A42,Q=160~189m3/hH=24~26m
洗涤底流泵:
147/157:
100ZJA-I-A50Q=160~189m3/hH=42m
洗涤底流泵:
167/177:
80ZJA-1-A36Q=120~140m3/hH=45~50m
4、粗液泵:
4台
200ZJA-1-A60Q=800m3/hH=55m
5、立式叶滤机:
4台
F=306m2Ø2900
6、精液泵:
4台
10/12LRB9
(1)70TZQ=800m3/hH=65m
7、赤泥隔膜泵:
4台
型号3D10-MF-250/6.0-BY-1A
N=560kwQ=250m3/hn=100~1000rpm;压力:
6.0MPa泵速48min-1冲程:
500mm
八:
常见生产故障及处理方法:
1、沉降槽跑浑
发生原因
对应的处理方法
1、排泥量小,泥层上升
2、矿浆温度低
3、未按质按量添加絮凝剂,4、沉降效果差
溶出效果差,出生料
5、长期未清槽,溢流堰内大量积泥
6、磨矿粒度过细
7、洗液量小,稀释矿浆浓度过高,影响沉降
8、进料固含过高,影响液固分离
1、加大排泥量,降低泥层高度
2、联系调度、溶出,提高矿浆温度
3、严格称量、配料,增加絮凝剂添加量
4、联系调度、溶出调整,提高溶出率
5、制定计划,退槽清理
6、汇报调度,要求调整磨矿粒度
7、调整洗液添加量,稳定矿浆浓度
8、适当提高絮凝剂添加量和排泥量
2、洗涤系统浓度过高
发生原因
对应的处理方法
1)赤泥洗涤热水加入不连续,流量不稳定。
2)分离沉降槽排泥量过大。
3)溶出闪蒸带料,导致赤泥洗水含碱高。
1)调整热水泵流量,尽量稳定连续加入洗水。
2)适当降低分离沉降槽排泥量。
3)联系调度、溶出减少闪蒸系统带料,同时进好水、循环水等,降低洗水含碱。
3、沉降槽冒槽
发生原因
对应的处理方法
1)液量不稳定。
2)溢流泵不上料或上料不足。
1)联系调度及有关岗位稳定进、出料。
2)倒用备用泵并立即汇报车间、点检站处理。
4、精液跑浑
发生原因
对应的处理方法
1)滤布破损。
2)滤布结硬。
3)小嘴垫子不正或磨损。
4)滤布下端放料口过短或过宽。
5)挂泥时间过短或挂泥时进料流量过大。
6)分离槽跑浑,粗液浮游物过高。
7)石灰乳流量过小或太稀,影响挂泥效果。
8)叶滤机进料压力波动大。
9)刷车不干净,挂不上泥。
10)粗液温度过低。
11)叶滤机精液阀门关不死,串料。
1)换布。
2)碱洗叶滤机。
3)重新放置垫子或更换垫子。
4)封死放料口,联系厂家改变制作方法。
5)严格按规程要求重新挂泥。
6)联系沉降控制跑浑,叶滤机多刷车。
7)开大石灰乳阀门,或联系调度和化灰机岗位调整石灰乳浓度。
8)稳定进料。
9)重新刷车、挂泥。
10)粗液槽通蒸汽,提高温度。
11)更换精液阀。
附:
工艺流程