部分注塑技术讲解.docx
《部分注塑技术讲解.docx》由会员分享,可在线阅读,更多相关《部分注塑技术讲解.docx(14页珍藏版)》请在冰豆网上搜索。
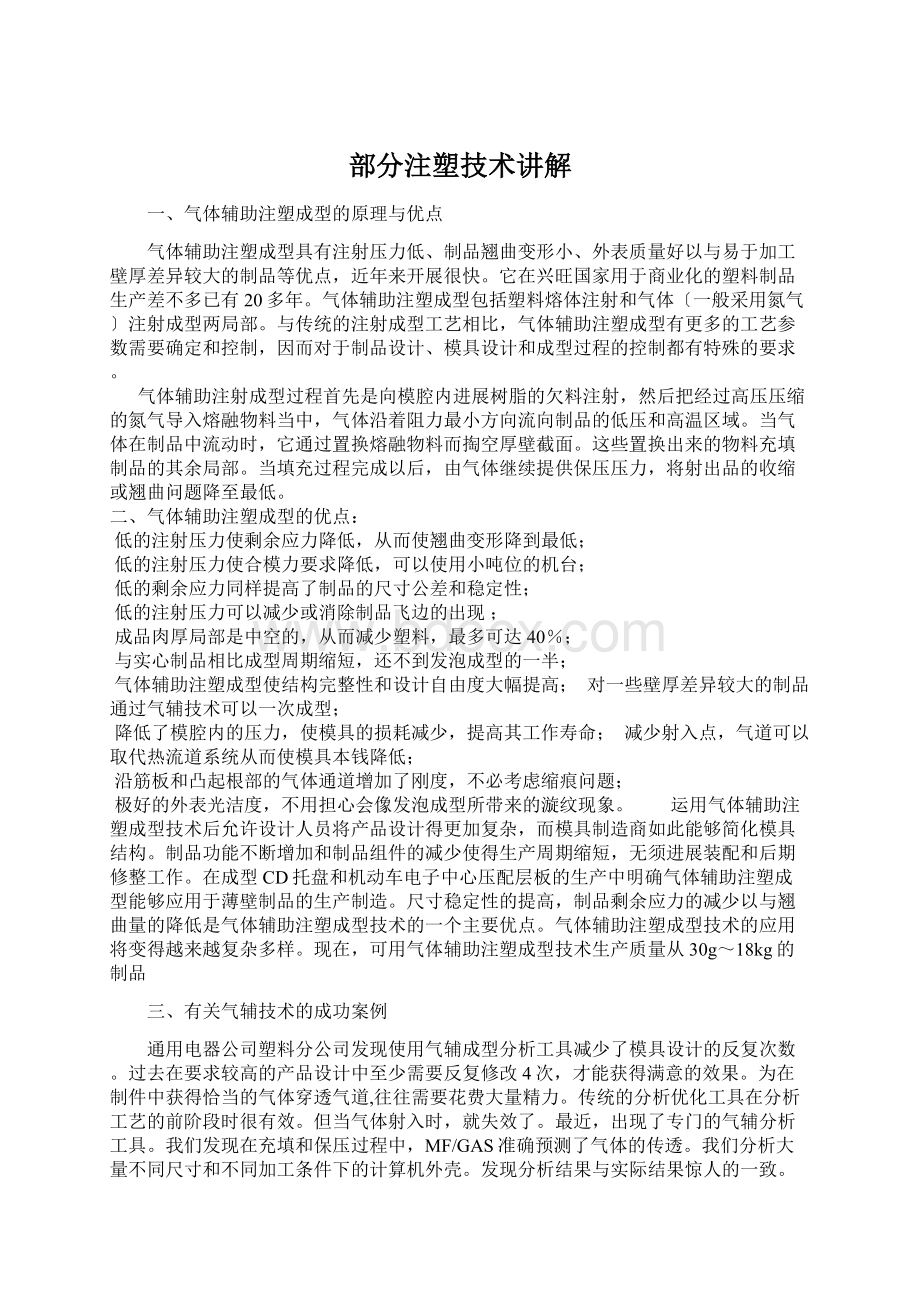
部分注塑技术讲解
一、气体辅助注塑成型的原理与优点
气体辅助注塑成型具有注射压力低、制品翘曲变形小、外表质量好以与易于加工壁厚差异较大的制品等优点,近年来开展很快。
它在兴旺国家用于商业化的塑料制品生产差不多已有20多年。
气体辅助注塑成型包括塑料熔体注射和气体〔一般采用氮气〕注射成型两局部。
与传统的注射成型工艺相比,气体辅助注塑成型有更多的工艺参数需要确定和控制,因而对于制品设计、模具设计和成型过程的控制都有特殊的要求。
气体辅助注射成型过程首先是向模腔内进展树脂的欠料注射,然后把经过高压压缩的氮气导入熔融物料当中,气体沿着阻力最小方向流向制品的低压和高温区域。
当气体在制品中流动时,它通过置换熔融物料而掏空厚壁截面。
这些置换出来的物料充填制品的其余局部。
当填充过程完成以后,由气体继续提供保压压力,将射出品的收缩或翘曲问题降至最低。
二、气体辅助注塑成型的优点:
低的注射压力使剩余应力降低,从而使翘曲变形降到最低;
低的注射压力使合模力要求降低,可以使用小吨位的机台;
低的剩余应力同样提高了制品的尺寸公差和稳定性;
低的注射压力可以减少或消除制品飞边的出现 ;
成品肉厚局部是中空的,从而减少塑料,最多可达40%;
与实心制品相比成型周期缩短,还不到发泡成型的一半;
气体辅助注塑成型使结构完整性和设计自由度大幅提高; 对一些壁厚差异较大的制品通过气辅技术可以一次成型;
降低了模腔内的压力,使模具的损耗减少,提高其工作寿命; 减少射入点,气道可以取代热流道系统从而使模具本钱降低;
沿筋板和凸起根部的气体通道增加了刚度,不必考虑缩痕问题;
极好的外表光洁度,不用担心会像发泡成型所带来的漩纹现象。
运用气体辅助注塑成型技术后允许设计人员将产品设计得更加复杂,而模具制造商如此能够简化模具结构。
制品功能不断增加和制品组件的减少使得生产周期缩短,无须进展装配和后期修整工作。
在成型CD托盘和机动车电子中心压配层板的生产中明确气体辅助注塑成型能够应用于薄壁制品的生产制造。
尺寸稳定性的提高,制品剩余应力的减少以与翘曲量的降低是气体辅助注塑成型技术的一个主要优点。
气体辅助注塑成型技术的应用将变得越来越复杂多样。
现在,可用气体辅助注塑成型技术生产质量从30g~18kg的制品
三、有关气辅技术的成功案例
通用电器公司塑料分公司发现使用气辅成型分析工具减少了模具设计的反复次数。
过去在要求较高的产品设计中至少需要反复修改4次,才能获得满意的效果。
为在制件中获得恰当的气体穿透气道,往往需要花费大量精力。
传统的分析优化工具在分析工艺的前阶段时很有效。
但当气体射入时,就失效了。
最近,出现了专门的气辅分析工具。
我们发现在充填和保压过程中,MF/GAS准确预测了气体的传透。
我们分析大量不同尺寸和不同加工条件下的计算机外壳。
发现分析结果与实际结果惊人的一致。
气辅成型是一种新型工艺,在熔融的塑料中注入惰性气体。
气体在推进塑料的过程中形成中空的气道,并在冷却时补充材料收缩进展保压。
这种工艺的优点在于减少翘曲,减少剩余应力和缩痕.气辅成型由于其中空管道大大降低了冷却时间,而使过去加工显得不经济的厚壁件变得可行。
并减少了过去只能用复杂结构模具生产的制件本钱。
使注塑件取代了许多金属和木材制件。
气辅成型降低了对注塑机的要求,因为它降低了注塑压力。
任何传统的注塑机可以很方便的在模具上加上气体设备和喷嘴,改造成气辅设备。
通用电器公司塑料分公司是气辅技术应用最广泛的公司。
这些制件广泛应用于家用器具、仪器、汽车、计算机、材料加工等部门。
我们发现这一工艺使这些生产部门大大受益。
在气辅成型中,平衡气体流动比平衡塑料流动更重要。
一个重要的原如此是气体通过气道穿透型腔,而不进入非气道区域。
制件设计对气辅成型能否成功起重要作用。
工艺条件如气体射入时间和气体压力同样也很重要。
因为气辅成型比传统模塑过程复杂。
使用分析软件是在生产前优化设计最经济有效的方法。
传统的分析工具可用于气辅成型塑料流动过程,而在气体填充阶段它们就无能为力了。
我们对新的专用于气辅成型分析工具很感兴趣。
一些我们用过的早期的软件包无视了对保压和合模状态的分析,而这对确定气体穿透非常重要。
MOLDFLOW推出MF/GAS,它能分析这些决定性的过程。
我们决定通过分析一个12英寸的计算机外壳,来测试这一软件。
我们设计了一个试验通过改变尺寸和加工条件来验证该软件的准确性。
我们在试验中设置了以下参数如材料、几何尺寸、气体注塑时间、气体压力、浇口尺寸。
制件包括以下几何特征如凸台,筋等。
我们在模具中使用了镶块使我们能快速改变流道等几何尺寸。
制件的壁厚为0.12英寸。
气道厚度为0.1至0.375英寸。
型腔中用一个气针进展气体的注入和流出。
制件使用东芝CIPRES注塑系统。
CINPRES是一种可拆卸的气体注塑系统,它通过气管和电子信号线与注塑机相连。
其中一种测试材料是透明的,可以准确测量气体穿透。
X射线被用于测量其他不透明材料的穿透。
另一重要问题是气道的壁厚,X射线无法测试这一参数,我们切开塑件,测量这一厚度。
在塑料注塑阶段,MF/GAS与MF/FLOW分析相似。
主要的区别在于在传统分析中我们使用薄板单元而气辅模块使用厚流道单元模拟气体在气道中流动。
新的软件图形化显示了塑料从浇口到最后充填点的流动过程。
气体注射从塑料充填完毕开始,并确定了经过保压后最终制件性能。
气体穿透以彩色云图显示。
分析结果与实际结果相当一致,使一次设计成功成为可能。
必须强调气体穿透有两种方法。
一种是顺着气道推动塑料前进,另一种是沿气道壁对制件保压和补缩。
MF/GAS是我所知道的考虑第二种状态的唯一软件。
第二种状态是决定性的,如果无视了第二种状态会降低预测的准确性,根据我们的经验误差将达到10%至80%。
MS/GAS软件可以分析构件设计,加工条件以与它们对最终制件的影响。
它解答了许多重要问题。
如气体将流多远,气体是否会吹破塑料熔体,残留壁厚是多少,聚合物和气体射入的最优位置。
在制件设计的过程中构件的形状,材料选择和塑料与气体的工艺参数将被设置,并使制件设计最经济。
这个软件包的主要优点是减少设计周期。
我们发现不进展分析,一般需要4次反复才能获得满意产品。
每一次反复包括了相当大的重设计,修改,试模费用。
使用MF/GAS我们可以完全消除这种反复。
四、气辅技术在保险杠生产中的应用
新型的MazdaLantis(马自达-兰迪斯)轿车的前、后保险杠的制造采用了气体辅助成型技术。
这次采用气体辅助注塑代替传统注塑成型来制造保险杆,意味着马自达-兰迪斯公司通过四年的研究和酝酿终于有了结果。
马自达公司的气体辅助注塑专利使用权,是从新普雷斯在日本的主要专利授权公司—Mitsubishi〔三菱〕获得的。
汽车行业早就意识到了采用气体辅助注塑技术能释放塑件内部的巨大内应力。
如果能应用于汽车行业,将极大地促进塑料制品在汽车领域的应用。
虽然距离全塑轿车还有很长的一段距离,但一直都在朝这个方向开展。
二十多年前,汽车的前、后保险杆都是采用金属制造并固定在车身上的。
近几年来多采用混合型的,主要原因是车身外形的要求、空气动力学方面的原因、以与保险杆正在变大,并要求与空气吸入护栏一体化。
但决定性的原因是车身尺寸和重量的增加,汽车制造商要求采用塑料制造,以降低本钱。
在最近十年中,塑料保险杆已采用传统注塑来制造。
制造程序包括通过一个简单的高压注塑模具先制成塑料框架,然后用一系列零部件来加强和支撑它。
采用这种方法将使用许多配件,并要增加额外的装配费用。
因此,科技人员一直致力于找到一种能一次完成以上步骤的成型方法。
在五年前,Mazda公司的工程师在开始他们的研究工作之时,就已经了解到气体辅助注塑能提供这方面的帮助。
主要表现在以下几个方面:
◆通过在交叉部位中央形成中空结构能使保险杆获得较大的强度和刚性;
◆局部的厚壁结构能组合到制品中而一次成型;
◆中空局部减少了内侧加强筋和厚壁局部所致的外侧收缩凹陷程度。
马自达工程师还发现,通过采用多个注射点和更小型的注塑机,可以制成壁厚更薄的保险杆,这样就大大减少了它的重量。
在早期的实验中马自达工程师发现,如果采用2.8mm厚的加强筋,那么它的弯曲强度将比原来的弯曲强度增加60%。
但是,由于加强筋太厚导致外表收缩凹陷而不能采用。
直到他们应用了气体辅助注塑技术之后,这种限制才得以突破。
同时,马自达工程师对材料的选用和成型条件之间的关系也十分感兴趣。
气体辅助注塑成型技术最先应用于一种被称为满射的方法,这种方法推出后,首先由三菱采用。
在采用这种技术时,模腔被塑料填满,之后射入气体。
令人瞩目的是,使用这种技术后,即使是不同的材料在不同的成型条件下,制品也能达到预定的要求。
实验是采用PP树脂在适当的条件下进展,所有的成品在中空成型时,被发现与材料的比容和流动特征有关。
另外发现当一个模具中同时使用多个注射气道时,紧靠的各个气道中,某些气道先形成〔容易形成〕,某些慢形成。
同时发现,树脂压力较低的气道容易进入,而在其他气道中,较高的树脂压力随着冷却而降低,这种压力的下降程度甚至比已掏空的气道中的树脂压力下降得还多。
马自达的工程师发现,纠正这种现象的方法是改变气道的设计。
气道之间的差异消除了,以上的问题也得到了解决。
马自达的工程师发现,纠正这种现象的方法是改变气道的设计。
气道之间的差异消除了,以上的问题也得到了解决。
五、气辅成型工艺中模具的应用
气体辅助注射成型是由注射成型演变而来的。
因此,这两种加工方式所采用的模具非常相似,材料也根本一样。
此项技术所用到的模具钢要能满足高产量制品、精细公差以与美观要求。
对于中小批量的应用,也可使用铝制模具。
在设计模具时,重要的一点是要知道终究采用通过喷嘴、从流道内或从制品内等三种进气方式中的哪一种进展气体辅助注射成型。
如果采用从流道内和通过喷嘴进气的方式,为防止物料在注入以前就已经凝固,浇口尺寸要足够大。
这对于子浇口或潜伏浇口来说非常关键,他们通常都会比普通注射成型时的尺寸大一些。
同样,边缘浇口或扇形浇口应设气体通道来提供一条明确的路径以便气体进入模腔内部。
从流道内或从制品中进气等其他气体辅助注射系统,气体喷嘴位置的选择是个非常棘手的问题。
因为气体喷嘴必须包含在模具里面,冷却线位置或者其他模具功能可能会因此而受到影响。
另外在选择气体喷嘴位置时需要注意的一点是,要保证在气体进入模具以前喷嘴是由物料包裹的,否如此无法形成气道。
在决定喷嘴位置的时候,必须先知道冷却路线、制品的设计以与充填方式。
热流道系统能用于从制品内进气方式的气体辅助注射成型中。
根据气体喷嘴的位置,可以采用阀式浇口的热流道系统。
如果气体渗透到热流道系统中,会将熔融物料推回料筒中。
这样会因物料注入量不一致而导致废品率的提高。
六、气辅注塑成型技术在塑料产品中的应用
体辅助注射成型技术可应用于各种塑料产品上,如电视机或音箱外壳、汽车塑料产品、家具、浴室、厨具、家庭电器和日常用品、各类型塑胶盒和玩具等。
具体而言,主要表现为以下几大类:
管状和棒状零件,如门把手、转椅支座、吊钩、扶手、导轨、衣架等。
这是因为,管状结构设计使现存的厚截面适于产生气体管道,利用气体的穿透作用形成中空,从而可消除外表成型缺陷,节省材料并缩短成型周期。
大型平板类零件,如车门板、复印机外壳、仪表盘等。
利用加强筋作为气体穿透的气道,消除了加强筋和零件内部剩余应力带来的翘曲变形、熔体堆积处塌陷等外表缺陷,增加了强度/刚度对质量的比值,同时可因大幅度降低锁模力而降低注射机的吨位。
形状复杂、薄厚不均、采用传统注射技术会产生缩痕和污点等缺陷的复杂零件,如保险杠、家电外壳、汽车车身等。
生产这些制品时,通过采用气体辅助注射技术并巧妙布置气道,适当增加加强筋数目,同时利用气体均匀施压来克制可能的缺陷,使零件一次成型,不仅简化了工艺,还降低了生产本钱。
七、气辅注塑的简介
气体辅助注塑成型具有注射压力低、制品翘曲变形小、外表质量好以与易于加工壁厚差异较大的制品等优点,近年来开展很快。
它在兴旺国家用于商业化的塑料制品生产差不多已有20多年。
气体辅助注塑成型包括塑料熔体注射和气体〔一般采用氮气〕注射成型两局部。
与传统的注射成型工艺相比,气体辅助注塑成型有更多的工艺参数需要确定和控制,因而对于制品设计、模具设计和成型过程的控制都有特殊的要求。
气体辅助注射成型过程首先是向模腔内进展树脂的欠料注射,然后把经过高压压缩的氮气导入熔融物料当中,气体沿着阻力最小方向流向制品的低压和高温区域。
当气体在制品中流动时,它通过置换熔融物料而掏空厚壁截面。
这些置换出来的物料充填制品的其余局部。
当填充过程完成以后,由气体继续提供保压压力,将射出品的收缩或翘曲问题降至最低。
气体辅助注塑成型的优点
低的注射压力使剩余应力降低,从而使翘曲变形降到最低;
低的注射压力使合模力要求降低,可以使用小吨位的机台;
低的剩余应力同样提高了制品的尺寸公差和稳定性;
低的注射压力可以减少或消除制品飞边的出现;
成品肉厚局部是中空的,从而减少塑料,最多可达40%;
与实心制品相比成型周期缩短,还不到发泡成型的一半;
气体辅助注塑成型使结构完整性和设计自由度大幅提高;
对一些壁厚差异较大的制品通过气辅技术可以一次成型;
降低了模腔内的压力,使模具的损耗减少,提高其工作寿命;
减少射入点,气道可以取代热流道系统从而使模具本钱降低;
沿筋板和凸起根部的气体通道增加了刚度,不必考虑缩痕问题;
极好的外表光洁度,不用担心会像发泡成型所带来的漩纹现象。
运用气体辅助注塑成型技术后允许设计人员将产品设计得更加复杂,而模具制造商如此能够简化模具结构。
制品功能不断增加和制品组件的减少使得生产周期缩短,无须进展装配和后期修整工作。
在成型CD托盘和机动车电子中心压配层板的生产中明确气体辅助注塑成型能够应用于薄壁制品的生产制造。
尺寸稳定性的提高,制品剩余应力的减少以与翘曲量的降低是气体辅助注塑成型技术的一个主要优点。
气体辅助注塑成型技术的应用将变得越来越复杂多样。
现在,可用气体辅助注塑成型技术生产质量从30g~18kg的制品。
八、比例流量、压力阀简介
比例流量、压力阀是有阀体和油掣线圈组成。
它的主要作用是通过油掣线圈受电大小来控制阀的流量开放多少。
线圈受电和阀体流量开放程度是按一定比例关系变化的。
比例阀与CPU严密配合,共为一体,共同来完成注塑工作:
参数预置--电脑处理--电子放大板--比例流量--注塑各动作。
预置参数使得数据进入CPU,经过对参数的运算、处理,将数字量通过D/A转换成模拟量信号。
该模拟信号又经比例放大处理后,输出再通过“压力、流量最高限额控制〞和“压力、流量最低限额控制〞4个电位器进展控制调校,然后通过相应的接线端子输出到电子放大板。
输出信号的幅度值实际中应在0~3VX围内变化。
电脑输出的控制信号作为电子放大板的输入信号,经过整形、比拟、反应、放大和隔离传送去控制功率三极管,再去驱动油掣阀的比例流量、比例压力阀线圈。
九、侧壁凹陷的成因分析
“凹痕〞是由于浇口封口后或者缺料注射引起的局部内收缩造成的。
注塑制品外表产生的凹陷或者微陷是注塑成型过程中的一个老问题。
凹痕一般是由于塑料制品壁厚增加引起制品收缩率局部增加而产生的,它可能出现在外部尖角附近或者壁厚突变处,如凸起、加强筋或者支座的背后,有时也会出现在一些不常见的部位。
产生凹痕的根本原因是材料的热胀冷缩,因为热塑性塑料的热膨胀系数相当高。
膨胀和收缩的程度取决于许多因素,其中塑料的性能,最大、最小温度X围以与模腔保压压力是最重要的因素。
还有注塑件的尺寸和形状,以与冷却速度和均匀性等也是影响因素。
塑料材料模塑过程中膨胀和收缩量的大小与所加工塑料的热膨胀系数有关,模塑过程的热膨胀系数称为“模塑收缩〞。
随着模塑件冷却收缩,模塑件与模腔冷却外表失去严密接触,这时冷却效率下降,模塑件继续冷却后,模塑件不断收缩,收缩量取决于各种因素的综合作用。
模塑件上的尖角冷却最快,比其它部件更早硬化,接近模塑件中心处的厚的局部离型腔冷却面最远,成为模塑件上最后释放热量的局部,边角处的材料固化后,随着接近制件中心处的熔体冷却,模塑件仍会继续收缩,尖角之间的平面只能得到单侧冷却,其强度没有尖角处材料的强度高。
制件中心处塑料材料的冷却收缩,将局部冷却的与冷却程度较大的尖角间相对较弱的外表向内拉。
这样,在注塑件外表上产生了凹痕。
凹痕的存在说明此处的模塑收缩率高于其周边部位的收缩。
如果模塑件在一处的收缩高于另一处,那么模塑件产生翘曲的原因。
模内剩余应力会降低模塑件的冲击强度和耐温性能。
有些情况下,调整工艺条件可以防止凹痕的产生。
例如,在模塑件的保压过程中,向模腔额外注入塑料材料,以补偿模塑收缩。
大多数情况下,浇口比制件其它局部薄得多,在模塑件仍然很热而且持续收缩时,小的浇口已经固化,固化后,保压对型腔内的模塑件就不起作用。
半结晶塑料材料的模塑件收缩率高,这使得凹痕问题更严重;非结晶性材料的模塑收缩较低,会最大程度地减小凹痕;填充和维持增强的材料,其收缩率更低,产生凹痕的可能性更小。
厚的注塑件冷却时间长,会产生较大的收缩,因此厚度大是凹痕产生的根本原因,设计时应加以注意,要尽量防止厚壁部件,假如无法防止厚壁不见,应设计成空心的,厚的部件就平滑过度到公称壁厚,用大的圆弧代替尖角,可以消除或者最大限度地减轻尖角附近产生的凹痕。
十、浅析塑料制品的翘曲变形
一、前言
翘曲变形是指注塑制品的形状偏离了模具型腔的形状,它是塑料制品常见的缺陷之一。
出现翘曲变形的原因很多,单靠工艺参数解决往往力不从心。
结合相关资料和实际工作经验,下面对影响注塑制品翘曲变形的因素作简要分析。
二、模具的结构对注塑制品翘曲变形的影响。
在模具方面,影响塑件变形的因素主要有浇注系统、冷却系统与顶出系统等。
1.浇注系统
注塑模具浇口的位置、形式和浇口的数量将影响塑料在模具型腔内的填充状态,从而导致塑件产生变形。
流动距离越长,由冻结层与中心流动层之间流动和补缩引起的内应力越大;反之,流动距离越短,从浇口到制件流动末端的流动时间越短,充模时冻结层厚度减薄,内应力降低,翘曲变形也会因此大为减少。
一些平板形塑件,如果只使用一个中心浇口,因直径方向上的收缩率大于圆周方向上的收缩率,成型后的塑件会产生扭曲变形;假如改用多个点浇口或薄膜型浇口,如此可有效地防止翘曲变形。
当采用点浇口进展成型时,同样由于塑料收缩的异向性,浇口的位置、数量都对塑件的变形程度有很大的影响。
另外,多浇口的使用还能使塑料的流动比〔L/t〕缩短,从而使模腔内熔体密度更趋均匀,收缩更均匀。
同时,整个塑件能在较小的注塑压力下充满。
而较小的注射压力可减少塑料的分子取向倾向,降低其内应力,因而可减少塑件的变形。
2.冷却系统
在注射过程中,塑件冷却速度的不均匀也将形成塑件收缩的不均匀,这种收缩差异导致弯曲力矩的产生而使塑件发生翘曲。
如果在注射成型平板形塑件〔如手机电池壳〕时所用的模具型腔、型芯的温度相差过大,由于贴近冷模腔面的熔体很快冷却下来,而贴近热模腔面的料层如此会继续收缩,收缩的不均匀将使塑件翘曲。
因此,注塑模的冷却应当注意型腔、型芯的温度趋于平衡,两者的温差不能太大〔此时可考虑使用两个模温机〕。
除了考虑塑件内外表的温度趋于平衡外,还应考虑塑件各侧的温度一致,即模具冷却时要尽量保持型腔、型芯各处温度均匀一致,使塑件各处的冷却速度均衡,从而使各处的收缩更趋均匀,有效地防止变形的产生。
因此,模具上冷却水孔的布置至关重要。
在管壁至型腔外表距离确定后,应尽可能使冷却水孔之间的距离小,才能保证型腔壁的温度均匀一致。
同时,由于冷却介质的温度随冷却水道长度的增加而上升,使模具的型腔、型芯沿水道产生温差。
因此,要求每个冷却回路的水道长度小于2米。
在大型模具中应设置数条冷却回路,一条回路的进口位于另一条回路的出口附近。
对于长条形塑件,应采用直通型水道。
〔而我们的模具大多是采用S型回路----既不利于循环,又延长周期。
〕
3. 顶出系统
顶出系统的设计也直接影响塑件的变形。
如果顶出系统布置不平衡,将造成顶出力的不平衡而使塑件变形。
因此,在设计顶出系统时应力求与脱模阻力相平衡。
另外,顶出杆的截面积不能太小,以防塑件单位面积受力过大〔尤其在脱模温度太高时〕而使塑件产生变形。
顶杆的布置应尽量靠近脱模阻力大的部位。
在不影响塑件质量〔包括使用要求、尺寸精度与外观等〕的前提下,应尽可能多设顶杆以减少塑件的总体变形〔换顶杆为顶块就是这个道理〕。
用软质塑料〔如TPU〕来生产深腔薄壁的塑件时,由于脱模阻力较大,而材料又较软,如果完全采用单一的机械顶出方式,将使塑件产生变形,甚至顶穿或产生折叠而造成塑件报废,如改用多元件联合或气〔液〕压与机械式顶出相结合的方式效果会更好〔以后会用到〕。
三、塑化阶段对制品翘曲变形的影响
塑化阶段即由玻璃态料粒转化为粘流态熔体的过程〔培训时讲过原料塑化的三态变化〕。
在这个过程中,聚合物的温度在轴向、径向〔相对螺杆而言〕温差会使塑料产生应力;另外,注射机的注射压力、速率等参数会极大地影响充填时分子的取向程度,进而引起翘曲变形。
四、充填与冷却阶段对制品翘曲变形的影响
熔融态的塑料在注射压力的作用下,充入模具型腔并在型腔内冷却、凝固。
此过程是注射成型的关键环节。
在这个过程中,温度、压力、速度三者相互耦合作用,对塑件的质量和生产效率均有极大的影响。
较高的压力和流速会产生高剪切速率,从而引起平行于流动方向和垂直于流动方向的分子取向的差异,同时产生“冻结效应〞。
“冻结效应〞将产生冻结应力,形成塑件的内应力。
温度对翘曲变形的影响表现在以下几个方面:
〔1〕 塑件上、下外表温差会引起热应力和热变形;
〔2〕 塑件不同区域之间的温度差将引起不同区域间的不均匀收缩;
〔3〕 不同的温度状态会影响塑料件的收缩率。
五、脱模阶段对制品翘曲变形的影响
塑件在脱离型腔并冷却至室温的过程中多为玻璃态聚合物。
脱模力不平衡、推出机构运动不平稳或脱模顶出面积不当很容易使制品变形〔前面已经讲过〕。
同时,在充模和冷却阶段“冻结〞在塑件内的应力由于失去外界的约束,将会以“变形〞的形式释放出来,从而导致翘曲变形。
六、注塑制品的收缩对翘曲变形的影响
注塑制品翘曲变形的直接原因在于塑件的不均匀收缩。
如果在模具设计阶段不考虑填充过程中收缩的影响,如此制品的几何形状会与设计要求相差很大,严重的变形会致使制品报废〔即收缩率的问题〕。
除填充阶段会引起变形外,模具上下壁面的温度差也将引起塑件上下外表收缩的差异,从而产生翘曲变形。
对翘曲分析而言,收缩本身并不重要,重要的是收缩上的差异。
在注塑成型过程中,熔融塑料在注射充模阶段由于聚合物分子沿流动方向的排列使塑料在流动方向上的收缩率比垂直方向的收缩率大,而使注塑件产生翘曲变形〔即各向异性〕。
一般均匀收缩只引起塑料件体积上的变化,只有不均匀收缩会引起翘曲变形。
结晶型塑料在流动方向与垂直方向上的收缩率之差较非结晶型塑料大,而且其收缩率也较非结晶型塑料大,结晶型塑料大的收缩与其收缩的异向性叠加后导致影响结晶型塑料件翘曲变形的倾向较非结晶型塑料大得多。
七、剩余热应力对制品翘曲变形的影响
在注射成型过程中,剩余热应力是引起翘曲变形的一个重要因素,而且对注塑制品的质量有较大的影响。
由于剩余热应力对制品翘曲变形的影响非常复杂,这里就不赘述。
八、金属嵌件对制品翘曲变形的影响
对放嵌件的注塑制品,由于塑料的收缩率远比金属的大,所以容易导致扭曲变形〔有的甚至开裂〕;为减少这种情况,可先将金属件预热〔一般不低于100℃〕,再投入生产。
九、结论
影响注塑制品翘曲变形的因素有很多,模具的结构、塑料材料的热物理性能以与成型过程的条件和参数均对制品的翘曲变形有不同程度的影响。
因此,对注塑制品翘曲变形