企业内部物流技术.docx
《企业内部物流技术.docx》由会员分享,可在线阅读,更多相关《企业内部物流技术.docx(49页珍藏版)》请在冰豆网上搜索。
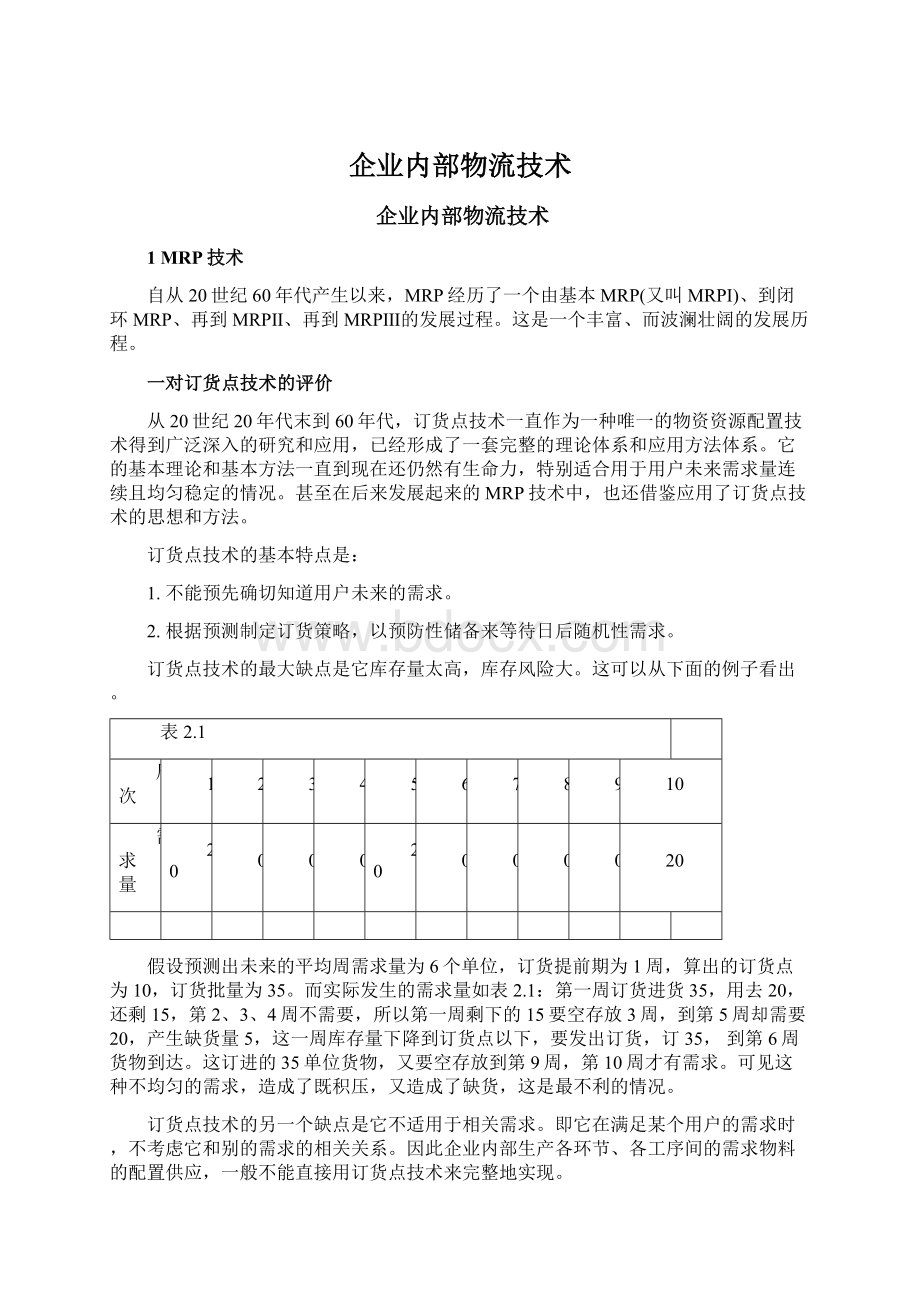
企业内部物流技术
企业内部物流技术
1MRP技术
自从20世纪60年代产生以来,MRP经历了一个由基本MRP(又叫MRPⅠ)、到闭环MRP、再到MRPⅡ、再到MRPⅢ的发展过程。
这是一个丰富、而波澜壮阔的发展历程。
一对订货点技术的评价
从20世纪20年代末到60年代,订货点技术一直作为一种唯一的物资资源配置技术得到广泛深入的研究和应用,已经形成了一套完整的理论体系和应用方法体系。
它的基本理论和基本方法一直到现在还仍然有生命力,特别适合用于用户未来需求量连续且均匀稳定的情况。
甚至在后来发展起来的MRP技术中,也还借鉴应用了订货点技术的思想和方法。
订货点技术的基本特点是:
1.不能预先确切知道用户未来的需求。
2.根据预测制定订货策略,以预防性储备来等待日后随机性需求。
订货点技术的最大缺点是它库存量太高,库存风险大。
这可以从下面的例子看出。
表2.1
周次
1
2
3
4
5
6
7
8
9
10
需求量
20
0
0
0
20
0
0
0
0
20
假设预测出未来的平均周需求量为6个单位,订货提前期为1周,算出的订货点为10,订货批量为35。
而实际发生的需求量如表2.1:
第一周订货进货35,用去20,还剩15,第2、3、4周不需要,所以第一周剩下的15要空存放3周,到第5周却需要20,产生缺货量5,这一周库存量下降到订货点以下,要发出订货,订35,到第6周货物到达。
这订进的35单位货物,又要空存放到第9周,第10周才有需求。
可见这种不均匀的需求,造成了既积压,又造成了缺货,这是最不利的情况。
订货点技术的另一个缺点是它不适用于相关需求。
即它在满足某个用户的需求时,不考虑它和别的需求的相关关系。
因此企业内部生产各环节、各工序间的需求物料的配置供应,一般不能直接用订货点技术来完整地实现。
二MRP的思想原理
1、MRP的产生
1965年美国J.A.奥列基博士(Dr.JosephA.Orlicky)提出独立需求和相关需求的概念,并指出订货点法只适用于独立需求物资。
加之六十年代计算机应用的普及和推广,人们可能把计算机应用到制定生产计划,美国生产管理和计算机应用专家OliverW.Wight&GeorgeW.Plosh首先提出了物料需求计划MRP(MaterialRequirementPlanning),IBM公司则首先在计算机上实现了MRP处理。
2、基本MRP的思想原理
MRP基本的思想原理是,由主生产进度计划(MPS)和主产品的层次结构逐层逐个地求出主产品所有零部件的出产时间、出产数量。
把这个计划就叫做物料需求计划。
其中,如果零部件靠企业内部生产的,需要根据各自的生产时间长短来提前安排投产时间,形成零部件投产计划;如果零部件需要从企业外部采购的,则要根据各自的订货提前期来确定提前发出各自订货的时间、采购的数量,形成采购计划。
确实按照这些投产计划进行生产和按照采购计划进行采购,就可以实现所有零部件的出产计划的实现,从而达到物资资源合理配置的目的,保证主产品出产的需要。
主生产进度计划
MPS
主产品结构物料需求计划库存状态
清单BOMMRP文件
制造任务单采购订货单
图2.1MRP逻辑原理图
MRP的逻辑原理如图2.1所示。
由图可以看出,物料需求计划MRP是根据主生产进度计划(MPS)、主产品的结构文件(BOM)和库存文件而形成的。
主产品就是企业用以供应市场需求的产成品。
例如汽车制造厂生产的汽车,电视机厂生产的电视机,都是各自企业的主产品。
主产品的结构文件BOM(BillofMaterials)主要反映出主产品的层次结构、所有零部件的结构关系和数量组成。
根据这个文件,可以确定主产品及其各个零部件的需要数量、需要时间和它们相互间的装配关系。
主生产进度计划MPS(MasterProductionSchedule),主要描述主产品及其有由其结构文件BOM决定的零部件的出产进度,表现为各时间段内的生产量,有出产时间、出产数量,或者装配时间、装配数量等。
产品库存文件,包括了主产品和其所有的零部件的库存量、已订未到量和已分配但还没有提走的数量。
制定物料需求计划有一个指导思想,就是要尽可能减少库存。
产品优先从库存物资中供应,仓库中有的,就不再安排生产和采购。
仓库中有但数量不够的,只安排不够的那一部分数量投产或采购。
由物料需求计划再产生产品投产计划和产品采购计划,根据产品投产计划和采购计划组织物资的生产和采购,生成制造任务单和采购订货单,交制造部门生产,或交采购部门去采购。
在这个过程中,制定物料需求计划,并从而产生投产计划和采购计划的过程,就是物资资源配置的过程。
(1)MRP输入
MRP的输入有三个文件:
1.主生产进度计划MPS(MasterProductionSchedule)。
它一般是主产品的一个产出时间进度表,主产品是企业生产的用以满足市场需要的最终产品,一般是整机或具有独立使用价值的零件、部件、配件等。
它们一般是独立需求产品,靠市场的订货合同、订货单或市
此文摘自:
物流学院?
()
场预测来确定其未来一段时间(一般是一年)的总需求量,包括需求数量、需求时间等。
把这些资料再根据企业生产能力状况经过综合调配平衡,把它们具体分配到各个时间单位中去。
这就是主产品产出进度计划。
这个主产品出产进度计划是MRP系统最主要的输入信息,也是MRP系统运行的主要依据。
主产品出产进度计划来自企业的年度生产计划。
年度生产计划覆盖的时间长度一般是一年,在MRP中用52周来表示。
但是主产品的出产进度计划可以不一定是一年,要根据具体的主产品的出产时间来定。
但是有一个基本原则,即主产品出产进度计划所覆盖的时间长度要不少于其组成零部件中具有的最长的生产周期。
否则,这样的主产品出产进度计划不能进行MRP系统的运行,因此是无效的。
例如有一个产品出产计划表如表2.2
表2.2产品A的出产进度表
时期(周)
1
2
3
4
5
6
7
8
产量(件/周)
25
15
20
60
15
2.主产品结构文件BOM(BillofMaterials)它不简单地是一个物料清单,它还提供了主产品的结构层次、所有各层零部件的品种数量和装配关系。
一般用一个自上而下的结构树表示。
每一层都对应一定的级别,最上层是0级,即主产品级,0级的下一层是1级,对应主产品的一级零部件,这样一级一级往下分解,……,一直分解到最末一级n级,一般是最初级的原材料或者外购零配件。
每一层各个方框都标有三个参数:
1.组成零部件名;2.组成零部件的数量,指构成相连上层单位产品所需要的本零部件的数量;3.相应的提前期,所谓提前期,包括生产提前期和订货提前期。
所谓生产提前期,是指从发出投产任务单到产品生产出来所花的时间。
而订货提前期是指从发出订货到所订货物采购回来入库所花的时间。
提前期的时间单位要和系统的时间单位一致,也以“周”为单位。
有了这个提前期,就可以由零部件的需要时间而推算出投产时间或采购时间。
An=0
LT=1
B
(2)
LT=1n=1
D
(1)C
(1)C
(1)
LT=1LT=3LT=3n=2
图2.5A产品结构树调整
An=0
LT=1
B
(2)C
(1)
LT=1LT=3n=1
D
(1)C
(1)
LT=1LT=3n=2
图2.4A产品结构树
例如图2.4给出了主产品A的结构树图。
它由2个部件B和1个零件C装配而成,而部件B又由一个外购件D和一个零件C装配而成。
A、B、C、D的提前期分别是1、1、3、1周,也就是说,装配一个A要1周时间(装配任务要提前一周下达),装配一个B要提前1周下达任务单,生产一个C要提前3周下达任务单,而采购一个D要提前一周发出订货单。
A产品结构分成3层,A为0层(n=0),B、C为1层(n=1),D、C为2层(n=2)。
图2.4所画的结构树虽然没有错,而且可以直观地看出主产品的结构层次。
但是根据这个结构树,同样的零件C在不同的层次上要分别计算一次,容易造成混乱和重复计算,给计算机运行带来麻烦。
所以为了计算机计算的方便,常常把在几个层次上都有的同样的零部件,都统一取其最低的层次号,画到它所在的最低层上。
如图2.5的C零件。
这也是画主产品结构图的小技巧。
3.库存文件,也叫库存状态文件。
它包含有各个品种在系统运行前的期初库存量的静态数据,但它主要提供并记录MRP运行过程中实际库存量的动态变化过程。
由于库存量的变化,是与系统的需求量、到货量、订货量等各种数据变化相联系的,所以库存文件实际上提供和记录各种物料的所有各种参数随时间的变化。
这些参数有:
1)总需要量:
是指主产品及其零部件在每一周的需要量。
其中主产品的总需要量与主生产进度计划一致,而主产品的零部件的总需要量根据主产品出产进度计划和主产品的结构文件推算而得出的。
总需要量中,除了以上生产装配需要用品以外,还可以包括一些维护用品,如润滑油、油漆等。
既可以是相关需求,也可以是独立需求,合起来记录在总需要量中。
2)计划到货量:
是指已经确定要在指定时间到达的货物数量。
它们可以用来满足生产和装配的需求,并且会在给定时间点实际到货入库。
它们一般是临时订货、计划外到货或者物资调剂等得到的货物,但不包括根据这次MRP运行结果产生的生产任务单生产出来的产品和或根据采购订货单采购回来的外购品。
这些产品由下面的“计划接受订货”来记录。
3)库存量:
是指每个周库存物资的数量。
由于在一周中,随着到货和物资供应的进行,库存量是变化的,所以周初库存量和周末库存量是不同的。
因此规定这里记录的库存量都是周末库存量。
它在数值上等于:
库存量=本周周初库存量+本周到货量-本周需求量
=上周周末库存量+本周计划到货量-本周需求量
另外在开始运行MRP以前,仓库中可能还有库存量,叫期初库存量。
MRP运行是在期初库存量的基础上进行的,所以各个品种的期初库存量作为系统运行的重要参数必须作为系统的初始输入要输入到系统之中。
库存量是满足各周需求量的物资资源。
在有些情况下,为了防止意外情况造成的延误,还对某些关键物资设立了安全库存量,以减少因紧急情况而造成的缺货。
在考虑安全库存的情况下,库存量中还应包含安全库存量。
表2.3给出了一个库存文件的例子。
这是A产品的库存文件。
根据主产品出产进度计划(表2.2)输入它在各周的总需要量,又输入它在各周的计划到货量(第1、3、5、7周分别计划到货10、15、75、15件),再输入A产品在MRP运行前的期初库存量(20)。
这些就是关于A产品的MRP输入的全部数据。
MRP输入完毕后,MRP系统会自动计算出各周的库存量、净需求量、计划接受订货量和计划发出订货量,形成如表2.3的结果。
表2.3A产品的库存文件
项目:
A(0级)
周次
提前期:
1
1
2
3
4
5
6
7
8
总需要量
25
15
20
60
15
计划到货量
10
15
40
50
现有库存量
20
5
-10
-15
-15
-35
-35
0
0
净需要量
0
10
5
0
20
0
0
0
计划接受订货
10
5
20
计划发出订货
10
5
20
以上三个文件是MRP的主要输入文件。
除此以外,为运行MRP还需要有一些基础性的输入,包括物料编码、提前期、安全库存量等。
这些在后面会说到。
(2)MRP输出
MRP输出,包括了主产品及其零部件在各周的净需求量,计划订货接受和计划订货发出三个文件。
1)净需求量:
净需求量,是指系统需要外界在给定的时间提供的给定物料的数量。
这是物资资源配置最需要回答的主要问题,即到底生产系统需要什么物资,需要多少,什么时候需要。
净需要量文件很好地回答了这些问题。
不是所有零部件每一周都有净需求的,只有发生缺货的周才发生净需要量,也就是说某个品种某个时间的净需要量就是这个品种在这一个时间的缺货量。
所谓缺货,就是上一周的期末库存量加上本期的计划到货量小于本期的总需要量。
净需要量的计算方法是:
本周净需要量=本周总需要量-本周计划到货量-本周周初库存量
=本周总需要量-本周计划到货量-上周周末库存量
MRP在实际运行中,不是所有的负库存量都有净需求量的。
求净需求量可以这样简单地确定:
在现有库存量一栏中第一个出现的负库存量的周,其净需求量就等于其负库存量的绝对值。
在其后连续出现的负库存量各周中,各周的净需求量等于其本周的负库存量减去前一周的负库存量的差的绝对值。
2)计划接受订货量:
它是指为满足净需要量的需求,应该计划从外界接受订货的数量和时间。
它告诉人们,为了保证某种物资在某个时间的净需求量得到满足,人们提供的供应物资最迟应当在什么时候到达,到达多少。
这个参数的用处,除了用于记录满足净需求量的数量和时间之外,还为它后面的参数“计划发出订货”服务的,是“计划发出订货”的参照点(二者数量完全相同,时间上相差一个提前期)。
计划接受订货的时间和数量与净需要量完全相同。
计划接受订货量=净需要量
3)计划发出订货量:
是指发出采购订货单进行采购、或发出生产任务单进行生产的数量和时间。
其中发出订货的数量,等于“计划接受订货”的数量,也等于同周的“净需求量”的数量。
计划发出订货的时间是考虑生产或订货提前期,为了保证“计划接受订货”或者“净需要量”在需要的时刻及时得到供应,而提前一个提前期而得到的一个时间。
即:
计划发出订货时间=计划接受订货时间-生产(或采购)提前期
=净需求量时间-生产(或采购)提前期
因为MRP输出的参数是直接由MRP输入的库存文件参数计算出来的,所以为直观起见,总是把MRP输出与MRP库存文件连在一起,边计算边输出结果。
例如表2.3就列出了A产品的MRP运行结果。
其运行过程如下:
首先根据MRP输入的库存文件计算出A产品各周的库存量。
本周库存量=上周库存+本周计划到货订货-本周总需求。
本周库存量都是指周末库存量,它可以为正数、负数和0。
然后MRP系统就计算和输出各周的净需要量。
只有那些库存量为负数的周才有净需要量。
净需要量的计算方法是:
第一次出现的负库存量(-10)的周(第二周)的净需要量就等于其负库存量的绝对值(10),其紧接在后面的负库存量的周(第三周)的净需要量就等于本周的负库存量(-15)减去上一周的负库存量(-10)所得结果的绝对值(5)。
同样算出第五周净需求量为20,第四、六、七、八周的净需要量为0。
接着MRP系统就计算和输出计划接受订货量,它在数量和时间上都与净需要量相同,如表,第二周接受10,第三周接受5。
计划接受订货量满足净需求量,而计划到货量满足部分总需要量。
二者合起来,就完全满足了总需要量。
最后MRP系统就计算和输出计划发出订货量,它是把计划接受订货量(或净需要量)在时间上提前一个提前期(这里是1周)、订货数量不变而形成的,如表,第一周发出10个的订货单,第二周发出5个订货单。
这就是MRP最后处理的结果。
它最后给出的是发出的一系列订货单和订货计划表。
表2.4A产品的订货计划表
项目:
A(0级)
周次
提前期:
1
1
2
3
4
5
6
7
8
计划发出订货
10
5
20
(3)MRP处理过程
MRP整个处理过程可以用图2.6所示的流程图表示。
整个过程可以分成以下几步:
1.准备:
在运行MRP之前,要做好以下几个方面的准备工作:
1)确定时间单位,确定计划期的长短。
一般计划期可以取1年,时间单位取为周,则计划期就是52周。
当然时间单位也可以取天,计划期可以取任意的天数。
在这里,我们取时间单位为周,计划期长度为M周。
2)确定物料编码,包括主产品和零部件的编码。
3)确认主产品出产进度计划MPS,它被表示成主产品各
周的出产量。
4)确认主产品的结构文件BOM,它被表示成具有层级结构的树形图。
由主产品(0级)开始,逐层分解成零部件,直到最后分解到最低层(设为n级)——初级原材料或外购零配件为止。
每个组成零部件都要标明零部件名、单个上层零部件所包含本零部件的数量和本零部件的生产(或采购)提前期。
每一层都要标明层号(也叫层级码)。
除了主产品(一般为独立需求)及其零部件(一般为相关需求)外,还有些辅助生产用品、维护、维修用品等需要外购的用品,可以作为独立需求按实际需要量直接列入BOM的最低层,参与共同的物料需求计划。
5)准备好主产品及其所有零部件的库存文件,特别是各自的期初库存量,计划到货量。
有些物资,特别是长距离、难订货的物资还要考虑安全库存量、订货批量和订货点等。
2.首先从层级码等于0的主产品开始,依次取各级层级码的各个零部件,进行如下处理:
1)输入提前期L、期初库存量H0。
(有些物资还要输入订货点QK、订货批量Q0、安全库存量QS等。
)
2)对于每一个时间单位t(周),输入或计算下列参数:
(1)输入或计算出产进度计划G(t);
(2)输入计划到货量S(t);
(3)计算库存量H(t):
H(t)=H(t-1)+S(t)-G(t);
此文摘自:
物流学院?
()
准备
n=0
输入L,H0,Qs,Q0
t=1
输入G(t),S(t)
H(t)=H(t-1)+S(t)-G(t)
yH(t)<0n
N(t)=|H(t)|-N(t-1)N(t)=0
P(t)=N(t)
R(t-L)=P(t)=N(t)
t所有层次都完了吗?
Nn=n+1
Y
结束
图2.6MRP逻辑流程图
(4)求出净需求量N(t):
当H(t)〈0、而H(t-1)〈0时,N(t)=|H(t)-H(t-1)|;
当H(t)〈0、而H(t-1)≥0时,N(t)=|H(t)|;
当H(t)≥0时,N(t)=0。
(5)计算计划接受订货量P(t):
P(t)=N(t);
(6)计算并输出计划发出订货量R(t-L):
R(t-L)=P(t)。
3)输出计划发出订货量R(t-L)。
这是每一个零部件发出的订货单,包括订货数量、订货时间,包括交各车间加工制造的生产任务单,也包括交采购部门采购的采购订货单。
它们按时间整理起来就是一个物料订货计划,也就是一个物料需求计划。
下面通过例子来说明。
例1.就以表2.2作为主产品出产进度计划MPS、图2.4作为主产品结构文件BOM、表2.3作为库存文件的A产品为例进行计算。
时间单位为周,计划期长8周。
其中相同的零部件取其最低层级码,构造新的结构图如图2.5。
先从层级码为0的主产品A算起。
其提前期为1周,期初库存量为20。
根据其G(t)、S(t)进行MRP运算的结果如表2.4。
再算层级码为1的部件B。
一个主产品A由2个部件B和一个零件C构成。
B的期初库存量为10,提前期为1周。
根据表2.4,A产品在第1、2和4周计划发出生产订货任务单,分别订10、5、20个A产品,也就是要在1、2、4周分别要20、10、40个B部件。
由于B的期初库存量只有10,而第一周总需要量需要20,且订货提前期要1周。
所以来不及按正常订货来满足,只有采取紧急订货,实现第一周计划到货量10,来满足第一周总需要量。
算出第2、4周的净需要量分别为10和40。
第1、3周分别计划发出订货量10和40。
计算结果如表2.5。
表2.5B产品的MRP运行结果
项目:
B(1级)
周次
提前期:
1
1
2
3
4
5
6
7
8
总需要量
20
10
40
计划到货量
10
库存量
10
0
-10
-10
-50
净需要量
10
40
计划接受订货
10
40
计划发出订货
10
40
算完第1级,再算第2级(层级码n=2)。
第二级有一个外购件D和一个零件C。
一个B由一个D和一个C构成。
D提前期为1周。
期初库存量为5,第一周计划到货量10,同样计算得表2.6。
第二周发出采购订货单35件。
再算第二级的另一个零件C。
其期初库存量为0、提前期为3周。
第一周计划到货量70。
一个A由一个C、一个B由一个C构成。
由表2.5知,第1、3周分别需要B部件10件和
表2.6D产品的MRP运行结果
项目:
D(2级)
周次
提前期:
1
1
2
3
4
5
6
7
8
总需要量
10
40
计划到货量
10
库存量
5
5
5
-35
-35
-35
-35
-35
-35
净需要量
35
计划接受订货
35
计划发出订货
35
40件,因此需要C也为10和40件。
又由表2.4知,A产品1、2、4周分别发出订货10、5、20件,因而需要C也为10、5、20件。
这样C的总需求量合起来为:
第一周20,第二周5,第三周40,第四周20。
同样计算的结果如表2.7所示。
第一周就要发出C零件的生产订货任务单15件。
表2.7C产品的MRP运行结果
项目:
C(1级)
周次
提前期:
3
1
2
3
4
5
6
7
8
总需要量
20
5
40
20
计划到货量
70
库存量
0
50
45
5
-15
-15
-15
-15
-15
净需要量
15
计划接受订货
15
计划发出订货
15
根据以上的运行,可以得出为按计划出产产品A而需要的物料订货计划,或者物料需求计划,如表2.8。
表2.8出产A所需要的物料订货计划
物料
周次
1
2
3
4
5
6
7
8
B
10
40
C
15
D
35
(4)MRP处理的几点说明:
1.计划期的长短和时间单位的确定:
原则上,MRP计划期的长短没有任何限制,可以长达几年、十几年、也可以短到一周、几天。
计划期长的话,MRP由于计算量大,运行时间要长一些而已。
但是,笔者认为,不是特别需要,MRP运行的计划期不要追求太长。
这是因为,MRP生成的物料需求计划本身是一种生产作业计划,它主要属于近期或短期计划,市场的变化、企业生产条件的变化是经常发生的,不可能较长时间不变,企业需要不断根据变化的情况随时调整生产作业计划,