模具设计实例教程.docx
《模具设计实例教程.docx》由会员分享,可在线阅读,更多相关《模具设计实例教程.docx(16页珍藏版)》请在冰豆网上搜索。
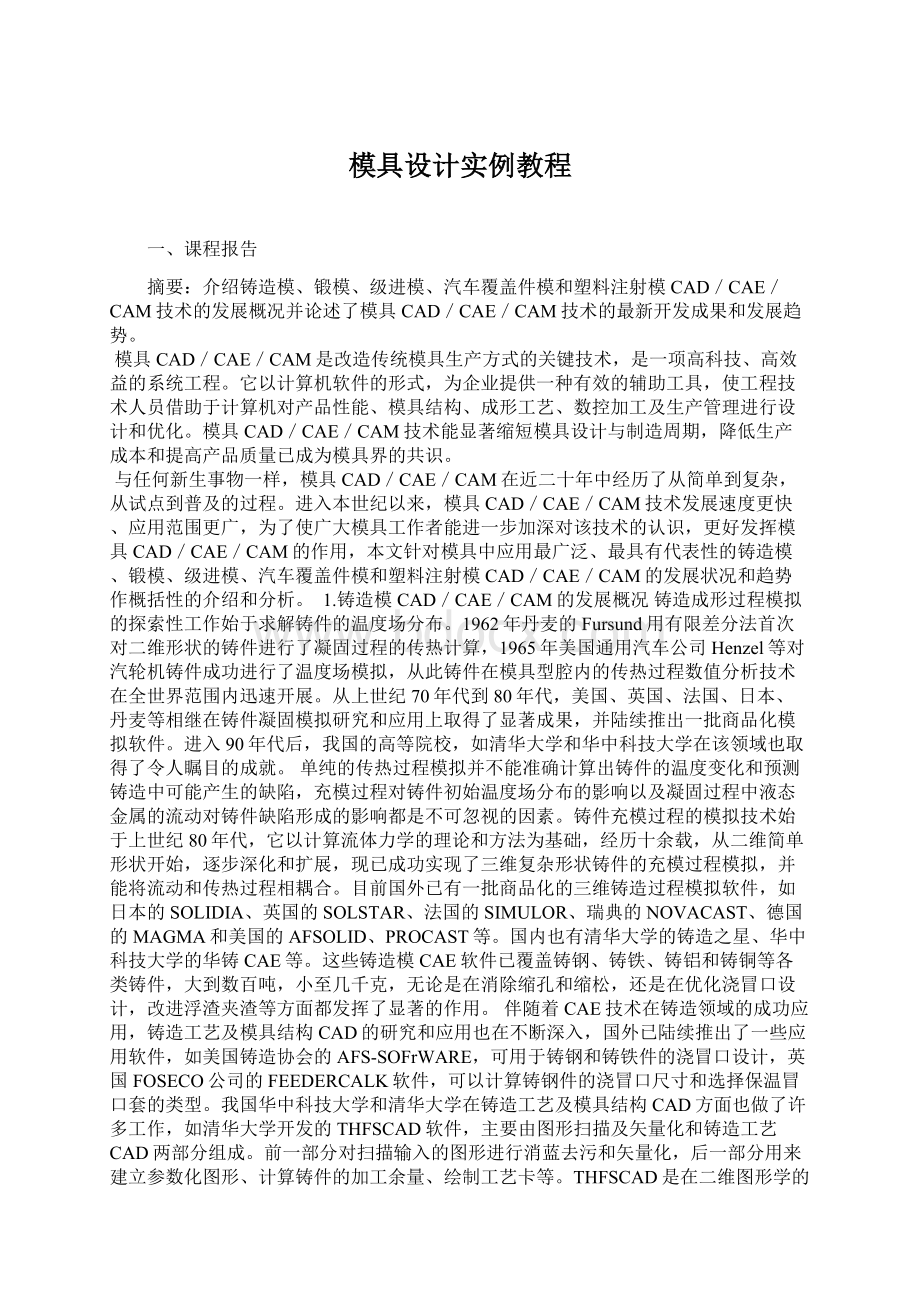
模具设计实例教程
一、课程报告
摘要:
介绍铸造模、锻模、级进模、汽车覆盖件模和塑料注射模CAD/CAE/CAM技术的发展概况并论述了模具CAD/CAE/CAM技术的最新开发成果和发展趋势。
模具CAD/CAE/CAM是改造传统模具生产方式的关键技术,是一项高科技、高效益的系统工程。
它以计算机软件的形式,为企业提供一种有效的辅助工具,使工程技术人员借助于计算机对产品性能、模具结构、成形工艺、数控加工及生产管理进行设计和优化。
模具CAD/CAE/CAM技术能显著缩短模具设计与制造周期,降低生产成本和提高产品质量已成为模具界的共识。
与任何新生事物一样,模具CAD/CAE/CAM在近二十年中经历了从简单到复杂,从试点到普及的过程。
进入本世纪以来,模具CAD/CAE/CAM技术发展速度更快、应用范围更广,为了使广大模具工作者能进一步加深对该技术的认识,更好发挥模具CAD/CAE/CAM的作用,本文针对模具中应用最广泛、最具有代表性的铸造模、锻模、级进模、汽车覆盖件模和塑料注射模CAD/CAE/CAM的发展状况和趋势作概括性的介绍和分析。
1.铸造模CAD/CAE/CAM的发展概况铸造成形过程模拟的探索性工作始于求解铸件的温度场分布。
1962年丹麦的Fursund用有限差分法首次对二维形状的铸件进行了凝固过程的传热计算,1965年美国通用汽车公司Henzel等对汽轮机铸件成功进行了温度场模拟,从此铸件在模具型腔内的传热过程数值分析技术在全世界范围内迅速开展。
从上世纪70年代到80年代,美国、英国、法国、日本、丹麦等相继在铸件凝固模拟研究和应用上取得了显著成果,并陆续推出一批商品化模拟软件。
进入90年代后,我国的高等院校,如清华大学和华中科技大学在该领域也取得了令人瞩目的成就。
单纯的传热过程模拟并不能准确计算出铸件的温度变化和预测铸造中可能产生的缺陷,充模过程对铸件初始温度场分布的影响以及凝固过程中液态金属的流动对铸件缺陷形成的影响都是不可忽视的因素。
铸件充模过程的模拟技术始于上世纪80年代,它以计算流体力学的理论和方法为基础,经历十余载,从二维简单形状开始,逐步深化和扩展,现已成功实现了三维复杂形状铸件的充模过程模拟,并能将流动和传热过程相耦合。
目前国外已有一批商品化的三维铸造过程模拟软件,如日本的SOLIDIA、英国的SOLSTAR、法国的SIMULOR、瑞典的NOVACAST、德国的MAGMA和美国的AFSOLID、PROCAST等。
国内也有清华大学的铸造之星、华中科技大学的华铸CAE等。
这些铸造模CAE软件已覆盖铸钢、铸铁、铸铝和铸铜等各类铸件,大到数百吨,小至几千克,无论是在消除缩孔和缩松,还是在优化浇冒口设计,改进浮渣夹渣等方面都发挥了显著的作用。
伴随着CAE技术在铸造领域的成功应用,铸造工艺及模具结构CAD的研究和应用也在不断深入,国外已陆续推出了一些应用软件,如美国铸造协会的AFS-SOFrWARE,可用于铸钢和铸铁件的浇冒口设计,英国FOSECO公司的FEEDERCALK软件,可以计算铸钢件的浇冒口尺寸和选择保温冒口套的类型。
我国华中科技大学和清华大学在铸造工艺及模具结构CAD方面也做了许多工作,如清华大学开发的THFSCAD软件,主要由图形扫描及矢量化和铸造工艺CAD两部分组成。
前一部分对扫描输入的图形进行消蓝去污和矢量化,后一部分用来建立参数化图形、计算铸件的加工余量、绘制工艺卡等。
THFSCAD是在二维图形学的基础上开发的,采用了AUTOCAD软件为开发平台。
随着CAD技术的快速进步,三维CAD系统在铸造生产领域会逐步取代二维CAD系统而成为主流设计系统。
2锻模CAD/CAE/CAM的发展概况自上世纪70年代以来,国内外许多学术机构和公司对锻模CAD/CAE/CAM技术进行了广泛的研究,在锻造工艺过程设计、锻模结构设计和金属流动模拟等方面均取得了显著的成绩。
轴对称锻件约占锻件总数的30%左右,加上轴对称锻件几何形状简单,易于描述和定义,所以开发锻模CAD/CAM系统时国内外大多数都是从轴对称锻模人手。
轴对称锻模CAD/CAM系统的主要组成部分包括锻件设计、模锻工艺设计、锻模结构设计和NC编程。
锻件设计指的是设计冷锻件图和热锻件图,包括选择分模面、补充机加工余量、添加圆角和拔模斜度等。
模锻工艺设计决定是否采用预成形工序、怎样采用预成形工序以及如何选择锻压设备的吨位。
另一类广泛应用的锻件是长轴类锻件,其成形工序设计和模具结构设计远比轴对称锻模复杂,因此开发长轴类锻模的CAD/CAM系统的难度更大、通用性也低,目前在许多通用商品化CAD/CAM软件上二次开发的长轴类锻模的CAD/CAM系统仅限于特定产品和特定场合的应用。
锻模CAD/CAM系统的发展方向是成组技术和模具标准化技术的进一步贯彻执行以及CAE技术和人工智能技术的深入应用。
在CAE技术方面,有限元法一直是分析和研究金属锻造成形的主要数值分析方法,多年来已取得不少阶段性的成果。
1973年Lee和Kobayashi以矩阵分析法导出了刚塑性有限元的Lagrange算法,成功分析了锻造成形过程。
1974年Zienkiewicz提出了刚粘塑性有限元的罚函数法,分析了轧制、挤压和拉拔等成形工艺。
1982年Moil和Osakada提出了刚塑性有限元中的材料可压缩法并用于轧制和挤压中。
上世纪80年代初,Oh和Altan用大型刚塑性有限元分析软件ALPID对各类塑性变形问题进行了深入研究。
90年代以后,国外一些商品化的专业有限元分析软件,如法国的FORGE2、美国的DEFORM、ABAQUS、MSC/AutoForge等,都已成功地应用于锻造领域。
这些软件不仅可以预测锻件成形的全过程,而且可以定量地给出与变形有关的各种物理量,如位移、速度、应力、应变和载荷等,为获得最优的模具设计、最合理的工艺方案和最少的试模时间提供了技术保证。
3级进模CAD/CAE/CAM的发展概况国外级进模CAD/CAE/CAM的研究始于上世纪60年代末,70年代便有初步应用,但仅限于二维图形的简单冲裁级进模,其主要功能如条料排样、凹模布置、工艺计算和NC编程等。
弯曲级进模CAD/CAM系统出现在80年代,如日本日立公司和富士通公司的弯曲级进模系统等。
为了能够适应复杂模具的设计,富士通系统采用了自动设计和交互设计相结合的方法,在该系统中除毛坯展开、弯曲回弹计算和工步排序为自动处理外,其余均需要设计人员的参与。
应用三维几何造型技术的级进模系统始于80年代末,如美国Auto-trol公司的Die-Design系统,该系统采用三维几何模型来描述板金零件,并将三维图形技术应用于模具结构设计,显示出三维图形软件在模具设计中的重要作用。
进人90年代,国际著名商品化三维CAD/CAM系统,如美国的Pro/E、UG-II、CADD5、Solidworks、MDT等均陆续在模具界得到应用。
美国PTC公司基于Pro/E系统开发了板金零件造型模块Pro/SheetMetaloUGSolution公司在UG-II的基础上开发了同类型的模块UG/SheetMetalo以上两个系统都缺乏面向级进成形工艺及模具结构设计的专用模块,但这方面的工作进展很快,有的已经初见成效。
本世纪之初,美国UGS公司与我国华中科技大学合作在UG-II(现为NX)软件平台上开发出基于三维几何模型的级进模CAD/CAM软件NX-PDW。
该软件包括工程初始化、工艺预定义、毛坯展开、毛坯排样、废料设计、条料排样、压力计算和模具结构设计等模块。
具有特征识别与重构、全三维结构关联等显著特色,已在2003年作为商品化产品投入市场。
我国从上世纪90年{BANNED}始,华中科技大学、上海交通大学、西安交通大学和北京机电研究院等相继开展了级进模CAD/CAM系统的研究和开发。
如华中科技大学模具技术国家重点实验室在AutoCAD软件平台上开发出基于特征的级进模CAD/CAM系统HMJC,包括板金零件特征造型、基于特征的冲压工艺设计、模具结构设计、标准件及典型结构建库工具和线切割自动编程五个模块。
上海交通大学为瑞士法因托(Finet001)精冲公司开发成功精密冲裁级进模CAD/CAM系统。
西安交通大学开发出多工位弯曲级进模CAD系统等。
近年来,国内一些软件公司也竞相加入了级进模CAD/CAM系统的开发行列,如深圳雅明软件制作室开发的级进模系统CmCAD、富士康公司开发的用于单冲模与复合模的CAD系统Fox-cad等。
4汽车覆盖件模CAD/CAE/CAM的发展概况国际上最早开展汽车覆盖件模CAD/CAM系统研究与开发的是各个大汽车制造公司。
早在1965年日本丰田汽车公司已将数控技术用于汽车覆盖件的模具加工,取得了很好的经济效果。
上世纪80年代丰田汽车公司所采用的汽车覆盖件CAD/CAM系统包括了NTDFB和CADETT两个设计软件及加工凸、凹模的TINCA软件,可完成车身外形设计、车身结构设计、冲模CAD、主模型与冲模加工和夹具加工等任务。
据报道,该系统投入使用后可使丰田公司的汽车覆盖件成形模设计与制造时间减少50%,本世纪之初丰田汽车公司又采用了美国PDC公司基于Pro/E软件平台开发的面向拉延模设计的专业化软件Pro/Dieface。
美国通用汽车公司依托美国UGS公司在UG-II软件平台上也开发了用于汽车覆盖件模具设计的专用模块,如板金件设计、车身设计、复盖件冲压工艺设计(包括冲压方向选择、工艺余量补充、压边面形状设计和修边线确定)和模具结构设计等,目前该系统正处于试运行阶段。
与此同时,美国福特汽车公司、英国PSF公司、日本获原铁工所、富士铁工所等国外生产汽车覆盖件模具的公司也开发了各自公司专用的汽车覆盖件模CAD/CAM系统。
目前这些系统尚不对外出售。
国内如湖南大学、吉林大学和华中科技大学等单位近几年来对汽车覆盖件模CAD/CAE/CAM技术进行了系统而深入的研究,取得了许多可喜的成果。
如湖南大学以先进冲压CAE技术为突破口,开发出一套包括冲压工艺设计和汽车覆盖件模具设计和制造的系列化软件。
其冲压仿真CAE自动建模系统CADEM-I能够利用模具表面数控轨迹数据作为网格生成的几何数据源,使建模效率成倍的提高,对于汽车覆盖件成形,在同样精度下可使仿真模型网格单元减少近20%-40%。
冲压仿真CAE系统CADEM-II采用先进的理论和算法,在保证冲压件大变形计算精度的前提下显著地提高了分析速度。
冲压工艺分析与设计系统CADEM-III采用壳体失稳理论预测覆盖件成形中的起皱趋势,采用基于仿真的毛坯反算技术,实现了复杂零件的毛坯形状和尺寸的迭代反求。
又如华中科技大学模具技术国家重点实验室最新推出的汽车覆盖件冲压成形快速分析软件FASTAMP,基于改进的有限元逆算法和板壳单元,综合考虑了摩擦、压边力和拉深筋等工艺条件,将产品设计、材料选择和工艺设计紧密联系起来,能够快速模拟汽车覆盖件成形后的起皱、破裂和成形不足等缺陷,优化压边力、拉深筋和摩擦等工艺参数、校核压料面和工艺补充面的合理性、提供最优的毛坯形状,从而可以为汽车覆盖件工艺设计和模具设计提供全面的解决方案。
5塑料注射模CAD/CAE/CAM的发展概况塑料注射模CAD/CAM是伴随着通用机械CAD/CAM技术发展而不断深化的。
从上世纪60年代基于线框模型的CAD系统开始,到70年代以曲面造型为核心的CAD/CAM系统,80年代实体造型技术的成功应用,90年代基于特征的参数化实体/曲面造型技术的完善,为塑料注射模采用CAD/CAE/CAM技术提供了可靠的保证。
目前在国内外市场已涌现出一批成功应用于塑料注射模的CAD/CAE/CAM系统。
现在国外一些著名的商品化三维造型软件都带有独立的注射模设计模块,如美国PTC公司的Pro/E、UGS公司的UG-II、SDRC公司的I-DEAS系统。
这三个CAD/CAM系统目前在塑料模具工业中的应用最为广泛。
塑料注射模CAE技术的发展也十分迅速,从上世纪60年代的一维流动和冷却分析到70年代的二维流动和冷却分析再到90年代的准三维流动和冷却分析,其应用范围已扩展到保压分析、纤维分子取向和翘曲预测等领域并且成效卓著。
塑料注射成型CAE商品化软件中应用最广泛的当数美国Moldflow公司的模拟软件MF,该软件主要包括流动模拟(MF/FLOW)、冷却分析(MF/COOL)、翘曲分析(MF/WARP)、气辅分析(MF/GAS)和应力分析(MF/STRESS)等。
该公司于1998年推出准三维的双面流软件(PartAdviser),2002年推出真三维的实体流软件模块,目前该公司在世界上拥有较大的用户群。
近十余年来,我国对塑料注射成型CAE技术也开展了系统而深入的研究。
华中科技大学、上海交通大学、郑州大学和南昌大学等都相继取得了可喜的成果。
如华中科技大学模具技术国家重点实验室在最近推出的商品化塑料注射成型集成化仿真系统HSCAE6.1O,从1989年推出的HSCAEl.O版到如今的6.10版,经历了从二维分析到三维分析,从实用化到商品化,从局部试点到大面积★◆应用的进程,已成为塑料制品设计、模具结构优化和工程师培训的有力工具,HSCAE仿真系统目前已在国内80多家工厂和学校★◆应用。
6模具CAD/CAE/CAM的发展趋势本世纪的科学技术正处于日新月异的变革之中,通过与计算机技术的紧密结合,人工智能技术、并行工程、面向装配、参数化特征建模以及关联设计等一系列与模具工业相关的技术发展之快、学科领域交*之广前所未见。
今后十年新一代模具CAD/CAE/CAM系统必然是当今最好的设计理念、最新的成形理论和最高水平的制造方法相结合的产物,其特点将反映在专业化、网络化、集成化和智能化四个方面。
随着模具工业的快速发展,近几年来世界各国的软件开发商投入了巨大的人力和物力,针对各类模具的特点,将通用的CAD/CAM系统改造为模具行业专用的系统,取得了较大成效。
已投入使用的有美国UGS公司的级进模设计系统NX-PDW、塑料注射模设计系统MoldWizard、以色列Cimatron公司的模具设计和制造系统Quick、英国DELCAM公司的塑料模设计和制造系统PS-Moldmaker、法国Misslelsoftware公司的注射模专用软件TopMold和级进模专用软件TopProgress、日本UNISYS株式会社的塑料模设计和制造系统CADCEUS等。
这些软件的技术特点是能在统一的系统环境下,使用统一的数据库,完成特定模具的设计。
NX-PDW初步实现了模具零件的结构关联,CADCEUS的特色在于三维设计与二维视图的联动,PS-Moldmaker做到了加工信息的自动封装,这些特点使得专业软件更加宜人化。
目前,国外一些软件开发商已能按实际生产过程中的功能划分产品系列,在网络系统下实现CAD/CAE/CAM的一体化,解决传统混合型CAD/CAM系统无法满足实际生产过程分工协作的要求。
例如英国DELCAM公司在原有软件DUCT5的基础上,为适应最新软件发展及工业生产实际推出了CAD/CAM集成化系统Delcam'sPowerSolution,该系统覆盖了几何建模、逆向工程、工业设计、工程制图、仿真分析、快速原型、数据编程、测量分析等各个领域。
系统的每个功能模块既可独立运行,又可通过数据接口与其他系统相兼容,并能按使用要求进行组合,以便形成专业化的CAD/CAE/CAM系统,做到开放性、兼容性和专业化的统一。
可以预计,模具CAD/CAE/CAM系统在今后几年内将会逐步发展为支持从设计、分析、管理和加工全过程的产品信息管理集成化系统。
在现阶段,模具设计和制造在很大程度上仍然依靠着模具工作者的经验,仅凭计算机的数值计算功能去完成诸如模具设计方案的选择、工艺参数与模具结构的优化、成型缺陷的诊断以及模具成形性能的评价是不现实的。
新一代模具CAD/CAE/CAM系统正在利用KBE(基于知识的工程)技术进行脱胎换骨的改造。
如UG-II中所提供的人工智能模块KF(KnowledgeFusion)。
利用KF可将设计知识融入系统之中,以便进行图形的识别与推理。
数值计算和人工智能技术的结合将是今后相当长时间内一件十分艰巨而重要的工作。
传统的模拟软件基本上都是被动式计算工具,分析前需要用户事先设计成形方案和确定工艺参数,分析结果常常难于直接用来指导生产,这在很大程度上影响了模拟软件的★◆和普及,华中科技大学模具技术国家重点实验室在国产注塑成型模拟软件HSCAE6.10中成功地引入了人工智能技术。
对于注射时间、注射温度等具有连续取值空间的参数,采用人工神经网络进行优化,对于分析结果的解释和评价则采用基于规则推理的方法来处理。
HSCAE6.10的专家系统规则库以专家知识为基础,涵盖了有关短射、流动平衡、熔体降解、温差控制、保压时间、许可剪切应力、剪切速率和锁模力等方面的领域知识,在对分析结果进行综合和提炼的基础上驱动专家系统进行推理,对成型方案进行评价并在分析报告中输出具体的改进建议,其目标是将模拟软件由传统的“被动式”计算工具提升为新一代的“主动式"优化系统。
二、上机实训报告
1.图示为某零件外壳,根据图形利用三维软件绘出具体模型并做出注射成型模具。
材料为聚乙烯,自己设计模具结构。
图01
1.1利用solidworks三维实体建模
实体分析:
此模型结构较为简单,可用以下特征:
1.1.01模型的建立过程
草图01
图02拉伸
图03圆角R1
1.1.02完成实体建模
图04
图05
2.设计过程
2.1初始化设计
(1)数据准备。
单击IMOLD工具栏上的“数据准备”命令,弹出“需衍生的零件名”,选择所要创建的实体。
弹出设置衍生参数对话框如下图。
①调入实体零件
②衍生模型零件参数设置
③保存衍生件与实体零件在同一文件夹
图06图07
图08图09
(2)项目控制
①开始一个新项目。
单击IMOLD工具栏中的“项目管理”→“新项目”。
②设置项目参数。
填入项目名,单击“调入产品”选择产品,选择派生零件“壳体衍生件”单击打开。
此时自动形成一个装配体结构。
在代号里可以写上代号名称“例如输入学号及序号:
200960458-21-”观察项目树特征变化。
选中特征树某一特征,对其编辑材料类型:
PC聚碳酸酯,其它选择默认。
③保存所有。
点击“同意”。
图10
2.2分型设置
(1)创建分型线。
单击分型线图标按钮,点击自动查寻。
图11图12
(2)创建分型面。
点击分型面按钮,如图点击查找。
(3)修补模型,。
选择“补孔”按钮,选择自动补孔。
图13图14
(4)创建延伸曲面。
图15
(5)插入模坯。
图16
2.3布局和浇注设计
(1)布局设计。
设置模腔数量为1,
(2)IMOLD特征管理,进入特征树中对延伸曲面进行隐藏。
(3)隐藏延伸曲面。
压缩延伸曲面特征,以便观察。
(4)添加浇口。
浇口位置设在侧壁,选择扇形浇口。
图17图18图19
(5)添加分流道
(6)添加主流道
2.4模架设计
(1)设置模架。
单击模架设计命令,选择模架厂家futaba,单位metric,型号1113。
删除多余零件。
图20图21图22
(2)定义模架设置。
修改模架尺寸至合理。
(3)添加型腔固定螺钉。
(4)设置冷却流道。
(5)添加标准件。
添加主流道寸套,添加顶杆
图34图35
2.5完成模具设计。
图36图37
3.结果、分析
对此零件的模架选择还存在一定问题,比如尺寸大小不当,对标准模架选用应大小合理,适合模型特征。
造成此问题的原因是对Solidworks软件插件集成的标准模架没有具体认识。
对模具设计参数的选择不够仔细,在对进行模具设计过程还不是很好地掌握,所以在要加强认识,了解模具的设计流程,熟练应用软件。
在与其他软件设计solidworks还存在一些的问题就不再叙述,本人对此也不是很了解。
从整体设计过程来看,solidworks在进行模具设计还是很实用,很强大的一个软件。
对于细节性问题就有待讨论和对软件的继续开发。
4.心得体会
经过两周的实训,我感觉pro/e这个软件确实很强大,很难,很不好上手,所以本人就使用UG,这也是基于前期对UG有一定的学习。
在创建模型特征上,还是感觉UG比pro/e要好用。
在solidworks软件中建模非常方便,很容易上手。
不过想要创建复杂零件特征时,就需要进行深入了解。
UG自身集成了很多插件比如CAMWORKS车削仿真,IMOLD模具设计,UG力学分析等。
对于软件的学习不仅需要自己强加练习,还要请大神的帮助,和同学老师进行交流。
巧用一些特征的建模。
此次实训虽结束,但是还有很多需要学习。
需要更多时间和精力去对软件的学习,加强对模具结构的认识。
看我昵称一起学习吧!