套类零件的加工实训指导.docx
《套类零件的加工实训指导.docx》由会员分享,可在线阅读,更多相关《套类零件的加工实训指导.docx(29页珍藏版)》请在冰豆网上搜索。
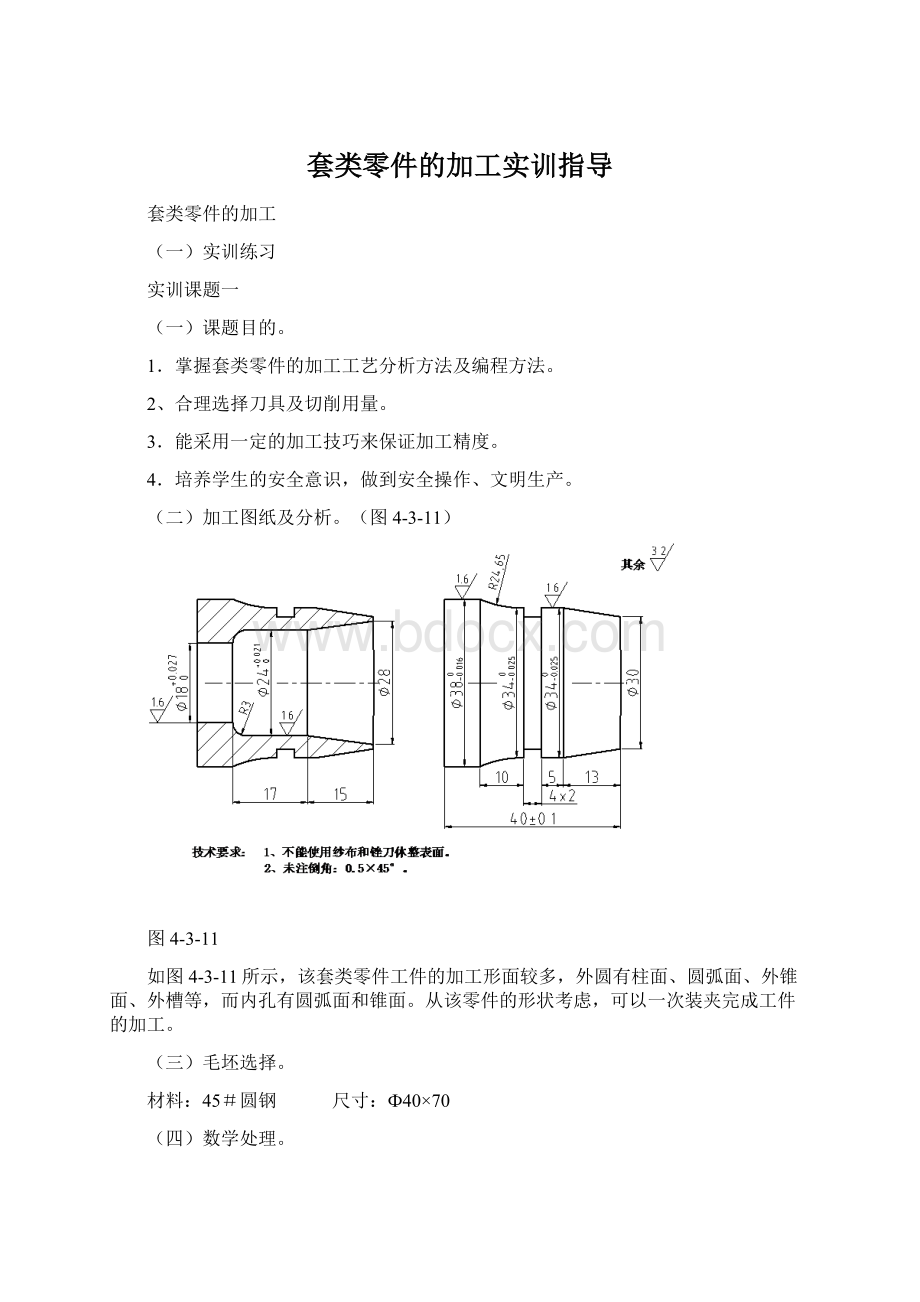
套类零件的加工实训指导
套类零件的加工
(一)实训练习
实训课题一
(一)课题目的。
1.掌握套类零件的加工工艺分析方法及编程方法。
2、合理选择刀具及切削用量。
3.能采用一定的加工技巧来保证加工精度。
4.培养学生的安全意识,做到安全操作、文明生产。
(二)加工图纸及分析。
(图4-3-11)
图4-3-11
如图4-3-11所示,该套类零件工件的加工形面较多,外圆有柱面、圆弧面、外锥面、外槽等,而内孔有圆弧面和锥面。
从该零件的形状考虑,可以一次装夹完成工件的加工。
(三)毛坯选择。
材料:
45#圆钢 尺寸:
Ф40×70
(四)数学处理。
由图可知,编程所需要的基点坐标均已给出,不需要计算。
需要注意的是外槽的尺寸,选择切槽刀时应考虑好刀宽。
(五)确定加工路线。
(见表4-3-17)
表4-3-17
数控车床加工工艺简卡
装夹顺序号
工艺简图
工步序号及内容
刀具号及名称
1
1、平端面。
(手动)
T0202
外圆粗车刀
2、钻中心孔。
(手动)
中心钻
3、用ф16mm钻头钻通该零件。
麻花钻
4、用镗孔刀粗加工内孔。
T0101
镗孔车刀
5、用镗孔刀精加工内孔。
T0101
镗孔车刀
1
1、用外圆刀粗加工各外圆。
T0202
外圆车刀
2、用外圆刀精加工各外圆。
T0202
外圆车刀
3、用切槽刀切外槽。
T0303
切槽刀
4、切断零件。
T0303
切槽刀
2
略
掉头包好铜皮,切削另一端面,取总长度至要求。
(手动)
T0202
外圆车刀
(六)选择刀具及切削用量(见表4-3-18)
表4-3-18
刀具名称
车刀主要
几何参数
车刀
材料
车刀切削用量
外圆粗车刀
αo=6°~8°
γo=25°~30°
Kr=90°~93°
Kr`=5°~8°
λs=0°~5°
YT15硬质合金
ap=2mm(单边)
f=80mm/min
n=560r/min
切槽刀
前角γo=15°~20°
后角αo=6°~8°
副后角α1=1°~2°
副偏角Kr`=1°~2°
YT15硬质合金
ap=3mm
f=10mm/min
n=360r/min
内孔车刀
αo=8°~10°
γo=10°~15°
Kr=90°~93°
Kr`=3°~5°
YT15硬质合金
ap=1mm(单边)
f=60mm/min
n=560r/min
中心钻
B型中心钻
高速钢
n=560r/min
钻头
Ф16mm
高速钢
n=560r/min
(七)确定工件原点
工件原点设定在工件右端面中心处。
(八)工件的装夹方法
采用三爪卡盘装夹,工件伸出长度50mm左右。
调头装夹时,需垫铜皮,以防夹伤已加
工表面。
(九)程序编制(表4-3-19及表4-3-20)
表4-3-19课题一参考程序(980T系统、机械变速)
程序名:
O0001
程序说明
GOOX100Z100;
M03S02T0101;
M08;
G00X15Z2;
G71U1R1
G71P10Q20U-0.5W0.1F150;
N10G00X28;
G01Z0F60;
G01X24Z-15;
Z-29;
G03X18Z-32;
N20G01Z-42;
G00X100Z100
M05;
M00;
M03S01T0101;
G00X15Z5;
G70P10Q20;
G00X100Z100;
M05;
M00;
M03S02T0202;
G00X40Z2;
G71U1.5R1;
G71P30Q40U0.5W0.1F200;
N30G00X30;
G01Z0;
G01X34Z-22;
G02X38Z-32R24.65;
N40G01Z-43;
G00X100Z100;
M05;
M00;
G00X40Z2;
G70P30Q40F60;
G00X100Z100;
M05;
M00;
M03S02T0303
G00X35Z-21
G75R1;
G75X30Z-22P600Q2000F20;
G00X42;
Z-43;
G75R1;
G75X15Z-43P600Q2000F20;
G00X100Z100
M09;
M05;
M30;
快速定位至起刀点
调1号内孔刀,正转560r/min
切削液开
快速接近工件毛坯
粗车各内孔面
N10~N20为内孔精加工轮廓
返回换刀点
转速1120r/min
精车各内孔
返回换刀点
调2号外圆刀
粗车各外圆面
N30~N40为外圆精加工轮廓
返回换刀点
精车各外圆面
返回程序起点
调3号切槽刀
切槽
切断
切削液关
主轴停
程序结束
表4-3-20课题二参考程序单(华中系统)
程序名:
%0001
程序说明
T0101;
M03S400;
M08;
G00X15Z5;
G71U1R1P10Q20X-0.5Z0.1F150;
G00X100Z100
M05;
M00;
M03S800T0101;
G00X15Z2
N10G00X28;
G01Z0F60;
G01X24Z-15;
Z-29;
G03X18Z-32;
N20G01Z-42;
G00X17
G00Z100
X100
M05;
M00;
M03S02T0202;
G00X40Z2;
G71U1.5R1P30Q40X0.5Z0.1F200;
G00X100Z100
M05;
M00;
M03S1000T0202;
G00X40Z1
N30G00X30;
G01Z0;
G01X34Z-22;
G02X38Z-32R24.65;
N40G01Z-44;
G00X100Z100;
M05;
M00;
M03S300T0303
G00X35Z-21
G01X30F20;
G00X42;
Z-43;
G01X15F20;
G00X100
Z100
M09;
M05;
M30;
建立工件坐标系,调1号内孔刀
正转400r/min
切削液开
快速接近工件毛坯
粗车各内孔面
返回换刀点
主轴停
暂停
调1号内孔刀
进到精加工路线起点
精加工路线结束
返回程序起点
主轴停
暂停
调2号外圆车刀
粗车各外圆
返回换刀点
主轴停
暂停
调2号车刀,转速1000r/min
进到外径精加工路线起点
精加工路线结束
返回换刀点
主轴停
暂停
调3号切槽刀(刀宽4mm),转速300r/min
切槽
切断工件
返回程序起点
切削液关
主轴停
程序结束
(十)加工操作
1、录入程序。
2、对刀操作并按要求输入工件零点和刀具补偿量等参数。
3、单步加工,试切削,测量后通过修改程序或刀补来控制精度。
4、自动运行加工。
5、检验工件尺寸是否合格。
6、加工完毕清扫机床,保养机床。
(十一)注意事项。
1、合理的选择切削用量,加工过程中可以利用进给倍率的修调来控制进给速度。
2、零件调头加工时要注意装夹的位置,装夹已加工表面时,要包好铜皮。
想一想
1、如何对内孔车刀。
2、在加工过程中,如何二次对刀,即外圆粗车刀刀尖磞刃而不能正常使用,现重磨或更换
新刀后,该刀应如何对刀才不影响其它刀的使用?
3、你在加工过程中,如何实现零件的精度控制?
具体的方法有几个?
实训课题二
(一)课题目的。
1.掌握套类零件的加工工艺分析方法及编程方法。
2.合理选用量具,掌握内孔测量的方法与步骤。
3.正确填写数控车床工艺简卡。
4.培养学生的安全意识,做到安全操作、文明生产。
5、熟悉掌握零件调头后的对刀方法。
(二)加工图纸及分析。
(图4-3-12)
图4-3-12
如图4-3-11所示,该套类零件工件的加工形面较多,其中外圆有柱面、台阶面、倒角、外槽和外螺纹等;而内孔有圆弧面和圆柱面。
从该零件的形状考虑,该零件应加工完右端面后,再调头装夹,完成该工件左端面的加工。
(三)毛坯选择。
材料:
45#圆钢 尺寸:
Ф40×70
(四)数学处理。
由图可知,编程所需要的基点坐标均已给出,其中要外螺纹的M36x2各个尺寸的计算,同时还需要注意的是外槽的尺寸,选择切槽刀时要考虑好刀宽。
(五)确定加工路线。
(见表4-3-21)
数控车床加工工艺简卡
装夹顺序号
工艺简图
工步序号及内容
刀具号及名称
1
1、平端面。
(手动)
T0202
外圆粗车刀
2、钻中心孔。
中心钻
3、用ф16mm钻头钻通该零件。
麻花钻
4、利用镗孔刀粗加工内孔。
T0101
镗孔车刀
5、利用镗孔刀精加工内孔。
T0101
镗孔车刀
1
1、利用外圆刀粗加工外圆。
T0202
外圆车刀
2、利用外圆刀精加工外圆。
T0202
外圆车刀
3、用切槽刀切外槽。
T0303
切槽刀
4、用外螺纹刀切螺纹
T0404
螺纹刀
5、切断该零件。
T0303
切槽刀
2
1、掉头包铜皮,切削另一端面保证总长度和外圆在尺寸范围内。
T0202
外圆车刀
表4-3-21
(六)选择刀具及切削用量(见表4-3-22)
表4-3-22
刀具名称
车刀主要
几何参数
车刀材料
车刀切削用量
外圆粗车刀
αo=6°~8°
γo=25°~30°
Kr=90°~93°
Kr`=5°~8°
λs=0°~5°
YT15硬质合金
ap=2mm(单边)
f=80mm/min
n=560r/min
切槽刀
前角γo=8°~20°
后角αo=2°~5°
副后角α1=1°~3°
副偏角Kr`=1°~1.5°
YT15硬质合金
ap=3mm
f=10mm/min
n=360r/min
内孔车刀
αo=8°~10°
γo=10°~15°
Kr=90°~93°
Kr`=3°~5°
YT15硬质合金
ap=1mm(单边)
f=60mm/min
n=560r/min
螺纹刀
后角αo=5°
右侧后角αoR=4°
左侧后角αoL=6°
γo=0°~5°
牙型角60度
YT15硬质合金
ap=由G76指令定
F=2
n=560r/min
中心钻
B型中心钻
高速钢
n=560r/min
钻头
Ф16mm
高速钢
n=560r/min
(七)确定工件原点。
工件点设定在工件右端面中心处。
(八)工件的装夹方法。
采用三爪卡盘装夹,工件伸出长度50mm。
调头装夹时,需垫铜皮,以防夹伤已加工表面。
(九)程序编制(见表4-3-23及表4-3-24)
表4-3-23课题一参考程序(华中系统)
程序名:
%1111
程序说明
T0101;
M03S400;
M08;
G00X15Z5;
G71U1R1P10Q20X-0.5Z0.1F150;
G00X100Z100
M05;
M00;
M03S800T0101;
G00X16Z1
N10G00X30;
G01Z0F60;
G02X23Z-20R56.25;
G01Z-25
X20;
N20G01Z-42
X18;
G00Z100
X100
M05;
M00;
M03S500T0202;
G00X40Z5;
G71U2R1P30Q40X0.5Z0.1F200;
G00X100Z100
M05;
M00;
M03S1000T0202;
G00X40Z1;
N30G00X29.8;
G01X35.8Z-3F60;
Z-29;
X37;
X38W-0.5
N40G01Z-44;
G00X100Z100;
M05;
M00;
M03S02T0303;
G00X37Z-27;
G01X32F20;
G00X37
W-2
G01X32
G00X100
Z100;
M05;
M00;
M03S02T0404;
G00X38Z5;
G76C2A60X33.8Z-26K1.3U0.08V0.1Q0.4F2;
G00X100Z100;
M05;
M00;
M03S300T0303;
G00X41Z-44;
G01X15F20;
G00X100
Z100;
M05;
M09;
M05;
M30;
%
%3333
T0202;
M03600;
M08;
G00X40Z2;
G81X18Z0F80;
G80X36Z-5F150;
X33;
X30;
X27;
G00X24Z1
G01X26W-1.5F60;
Z-5
X37
X39W-1
G00X100Z100;
M05;
M09;
M30;
%
调1号内孔车刀,建立工件坐系。
正转,400r/min。
切削液开
快速接近工件毛坯
粗车各内孔面
返回换刀点
停主轴
暂停
调1号内孔刀,正速800r/min
进到外径精加工路线起点
精加工路线结束
返回换刀点
停主轴
暂停
调2号外圆刀
粗车各外圆面
返回换刀点
停主轴
暂停
调2号外圆刀
进到外径精加工路线起点
精加工路线结束
返回换刀点
停主轴
暂停
调3号切槽刀
切槽
返回换刀点
停主轴
暂停
调4号螺纹刀
粗、精车螺纹
返回换刀点
停主轴
暂停
调3号切槽刀
切断工件
返回程序起点
主轴停
切削液停
程序结束
调头加工(另起一程序号)
调2号外圆刀,建立工件坐标系。
车端面
切削ф26外圆到尺寸
倒角C0.5及精加工外圆
返回程序起点
主轴停
切削液停
程序结束
表4-3-24 课题一参考程序(98T系统)
顺序号
程序名:
O0001
程序说明
N10
N20
N30
N40
N50
N60
N70
N80
N90
N100
N110
N120
N130
N140
N150
N160
N170
N180
N190
N200
N210
N220
N230
N240
N250
N260
N270
N280
N290
N300
N310
N320
N330
N340
N350
N360
N370
N380
N390
N400
N410
N420
N430
N440
N450
N460
N470
N480
N490
N500
N610
N620
N630
N640
N650
N660
N670
N680
N690
N700
N710
N720
N730
GOOX100Z100;
M03S02T0101;
M08;
G00X15Z5;
G71U1R1;
G71P70Q120U-0.5W0F200;
G00X30;
G01Z0;
G02X23Z-20R56.25;
G01Z-25;
X20;
Z-42
G00X100Z100;
M05;
M00;
M03S01T0101;
G00X15Z5;
G70P70Q120F60;
G00X100Z100;
M05;
M00;
M03S02T0202;
G00X40Z1;
G71U1.5R1;
G71P250Q300U0.5W0.1F200;
G00X29.8;
X35.8Z-2F60;
G01Z-29;
X37;
G01X38W-0.5;
G01Z-44;
G00X100Z100;
M05;
M00;
M03S01T0202;
G00X40Z1;
G70P250Q300F60;
G00X100Z100;
M05;
M00;
M03S02T0303;
G00X37Z-27;
G75R1;
G75X32Z-29P600Q3000F10;
G00X100Z100;
M05;
M00;
M03S02T0404;
G00X38Z5;
G76P040260Q60R0;
G76X33.8Z-26P1080Q400F2;
G00X100Z100;
M05;
M00;
M03S01T0303;
M08;
G00X41Z-44;
G75R1;
G75X15P500F20;
G00X100Z100;
M09;
M05;
M30;
O1122
M03S01T0202;
M08;
G00X40Z3;
G94X15Z0F80;
G90X36Z-5F60;
X33;
X30;
X27;
X26;
G00X100Z100;
M05;
M09;
M30
快速定位至起刀点
调1号内孔刀,正转560r/min
切削液开
快速接近工件毛坯
粗车各内孔面
返回换刀点
调1号内孔刀,转速1120r/min
精车各内孔
返回换刀点
调2号外圆刀
粗车各外圆面
返回换刀点
精车各外圆面
返回换刀点
换3号切槽刀
切槽
返回换刀点
调4号螺纹刀
粗、精车螺纹
返回换刀点
调3号切槽刀
切断工件
返回程序起点
切削液停
主轴停
程序结束。
调头加工(另起一程序号)
调2号外圆刀
车端面
切削ф26外圆到尺寸
返回程序起点
主轴停
切削液停
程序结束
(十)加工操作
1、录入程序并要求模拟校验程序。
2、对刀操作并按要求输入工件零点和刀具补偿量等参数。
3、单步加工,试切削,测量后通过修改程序或刀补来控制精度。
4、自动运行加工。
5、检验工件尺寸是否合格。
6、加工完毕清扫机床,保养机床。
(十一)注意事项。
1、注意螺纹刀的对刀精度,以免加工出的螺纹不合格。
2、零件调头加工时要注意装夹的位置,装夹已加工表面时,要包好铜皮。
3、调头后2号刀要从新对刀,否则会出现撞刀或空切现象。
想一想
1、加工内孔时,如何对刀?
2、在加工过程中,如何二次对刀,即外圆粗车刀刀尖磞刃而不能正常使用,现重磨或更换新刀后,应如何对刀才不影响其它刀的使用?
3、调头后如何能快捷的对好2号刀具?
(二)项目练习
综合练习一
1、考核要求
⑴毛坯:
Ф40×70棒料
⑵时间定额:
3小时
⑶考核内容:
数控车削加工工艺分析,填写数控车床工艺简卡、程序编制、刀具的选择、
工件的安装;尺寸公差、形位公差、表面粗糙度图样的要求;量具的选用;不得以手工方式加工工件;手工去毛刺。
⑷安全生产:
严格执行数控车床操作规程,遵守实习现场的各项规章制度,服从教师的安排及合理的调配。
做到文明生产,使用的工具按要求取用和放置,设备使用过程中保持良好的操作习惯,注意设备的润滑,完成作业后要保养设备并及时打扫实习场地。
2、图样1(见图4-3-13)
图4-3-13
3、填写加工工艺简卡
数控车床加工工艺简卡
工序名称
工艺简图:
(标明定位、装夹位置)
(标明程序原点和对刀点)
工步序号及内容
刀具号
及名称
4、综合练习一评分标准
考核
项目
考核内容及要求
配分
评分标准
检测结果
得分
学生
教师
工艺
分析
填写工序卡。
工艺不合理,视情况酌情扣分。
(详见工序卡)
(1)工件定位和夹紧不合理;
(2)加工顺序不合理
(3)刀具选择不合理;
(4)关键工序错误
10
每违反一条酌情扣1分。
扣完为止
内孔
φ18
IT
10
超差0.01扣2分
Ra
4
降级不得分
内锥度
φ26
IT
6
超差0.01扣2分
Ra
4
降级不得分
外圆
φ38
IT
10
超差0.01扣2分
Ra
4
降级不得分
外圆
φ34
IT
10
超差0.01扣2分
Ra
4
降级不得分
长度
15、40、31
IT
9
超差0.01扣1分
40
IT
5
超差0.01扣1分
槽
3×2
IT
10
超差0.01扣2分
Ra
4
降一级扣1分
安全文
明生产
符合国家颁布的
安全生产法规
10
每违反一条酌情扣1分。
扣完为止
综合练习二
1、考核要求
⑴毛坯:
Ф40×70棒料
⑵时间定额:
3小时
⑶考核内容:
数控车削加工工艺分析,填写数控车床工艺简卡、程序编制、刀具的选择、
工件的安装;尺寸公差、形位公差、表面粗糙度图样的要求;量具的选用;不得以手工方式加工工件;手工去毛刺。
⑷安全生产:
严格执行数控车床操作规程,遵守实习现场的各项规章制度,服从教师的安排及合理的调配。
做到文明生产,使用的工具按要求取用和放置,设备使用过程中保持良好的操作习惯,注意设备的润滑,完成作业后要保养设备并及时打扫实习场地。
2、图样2(见图4-3-14)
图4-3-14
3、填写加工工艺简卡。
数控车床加工工艺简卡
工序名称
工艺简图:
(标明定位、装夹位置)
(标明程序原点和对刀点)
工步序号及内容
刀具号
及名称
4、综合练习二评分标准。
考核
项目
考核内容及要求
配分
评分标准
检测结果
得分
学生
教师
工艺
分析
填写工序卡。
工艺不合理,视情况酌情扣分。
(详见工序卡)
(1)工件定位和夹紧不合理;
(2)加工顺序不合理
(3)刀具选择不合理;
(4)关键工序错误
10
每违反一条酌情扣1分。
扣完为止
内孔
φ18
IT
8
超差0.01扣2